Tests of heating systems: hydraulic, thermal, pneumatic. Manometric testing of pipelines for tightness
Heating system tests produced after completion installation work. But first, all plumbing pipes must be flushed.
Before testing, check compliance with the test heating systems project, produce an external inspection of pipelines, connections, equipment, instruments, fittings.
Put to the test heating systems in general and certain types equipment, as well as their regulation. According to the test results, acts are drawn up.
Testing of heating systems, heat supply perform hydrostatic and manometric (pneumatic) methods.
Hydrostatic testing of the heating system produced by filling all elements of the system with water (with complete removal of air), increasing the pressure to test pressure, keeping the system under test pressure for a certain time, reducing pressure and, if necessary, emptying the system. Hydrostatic testing is safe: the system is tested in conditions that are closest to the workers. However, such a test requires water to be supplied to the building to fill the plumbing system, which is unacceptable. If the tightness is violated, it is possible to flood the premises, soak building structures; in winter time possible freezing of water in the pipes and their “defrosting”.
So hydrostatic testing of heating systems, heat supply, boilers, water heaters are performed at a positive temperature in the premises of the building. The temperature of the water that fills the system must be at least 278°K (5°C).
Hydrostatic heating tests carried out before finishing the premises.
Gauge testing of the heating system in many respects they are devoid of the shortcomings of hydrostatic tests, but they are more dangerous, since if pipelines or system elements are accidentally destroyed under the action of compressed air, their pieces can get into the people conducting the tests.
Gauge heating tests spend, filling heating system compressed air at a pressure equal to the test pressure, and keeping it under this pressure for a certain period, then the pressure is reduced to atmospheric pressure.
For testing, a pneumohydraulic unit TsSTM-10 is used in the form of a two-axle trailer, on which a container with a volume of 2.5 m3 and all test equipment are mounted.
Testing of heating systems. Acceptance of heating boiler houses is carried out on the basis of the results of a hydrostatic or manometric test, and heating systems– based on the results of hydrostatic and thermal tests, as well as external inspection of the installed devices and equipment. Heating systems tested for tightness (but not for strength) by the manometric method under an excess air pressure of 0.15 MPa to detect mounting defects by ear and then with a pressure of 0.1 MPa for 5 minutes (in this case, the pressure should not decrease by more than 0.01 MPa ).
hydrostatic water heating system testing carried out after installation and inspection. To do this, the system is filled with water and air is completely removed from it by opening all air collectors, taps on the risers and at the heaters. Fill the system through the return line, connecting it to a permanent or temporary water supply. After filling the system, close all air collectors and turn on a manual or powered hydraulic press, which creates the required pressure.
Water heating systems tested with a hydrostatic pressure equal to 1.5 times the working pressure but not less than 0.2 MPa at the lowest point. During the test, the boilers and the expansion vessel are disconnected from the system. The pressure drop during the test shall not exceed 0.02 MPa for 5 min. The pressure is controlled by a checked and sealed pressure gauge with divisions on the scale through 0.01 MPa. Minor faults found that do not interfere with the hydrostatic test are marked with chalk and then corrected.
Installation and country house.
The act of hydraulic testing of the heating system and pipelines
Not a single heating structure can constantly function, and therefore provide reliable heat supply, without planned preventive measures. Among them are hydraulic tests of the heating system. Their goal is to find weak areas that can create a problem for property owners at the most inopportune moment.
Carrying out test activities (they are also called pressure testing) is a whole range of works aimed at detecting shortcomings not only in the strength of the pipeline, but also in all heating equipment.
Time of hydraulic testing
Hydraulic testing of pipelines of heating systems and their other elements is performed in the following cases:
- when preparing the heat supply design for heating season(read: "Rules for preparing a residential building for the heating season");
- if necessary, replace one of the sections;
- after completion of repair work;
- when the object is put into operation.
Successful completion of hydraulic tests is a confirmation of the tightness of the circuit.
The process itself consists of several stages:
- with the help of special equipment, air or water is supplied to the pipelines under a certain pressure;
- detection of weaknesses in the heating system;
- elimination of defects.
Hydraulic tests of pipelines and heating devices are carried out with a minimum number of specialists.
Regulations and rules
When carrying out these planned preventive measures, they use a specially developed SNiP, which describes the sequence and nuances of the work, for which the document has a standard instruction. It also contains technological schemes that take into account all the features of the implementation of actions according to safety regulations and the required equipment. Any hydraulic tests are carried out in strict accordance with this regulatory document.
When hydraulic tests of the heating system are carried out - SNiP regulates the mandatory flushing of the structure in order to remove from internal walls deposits and scale on pipelines and radiators (read also: “The act of flushing the heating system - a sample contract form“). There are several ways to carry it out, while using a compressor and special solutions.
Most often, oxides are collected in pipelines:
- copper;
- gland:
- sulfur;
- zinc;
- calcium;
- magnesium.
Experts recommend flushing the heating system at least once every five years. As a result, space heating will be more efficient and reliable. The fact is that during operation, the quality of heat supply decreases due to the formation of deposits and scale, which, gathering on the walls of pipes, reduce their cross section, after which the circulation of the coolant slows down.
Carry out periodic preventive measures for heating systems and engineering communications obligated operating companies serving buildings. AT residential buildings these works are performed by employees of ZhEKs or similar organizations and enterprises.
Crimping
All crimping work is carried out by specially trained personnel using necessary equipment. Do it yourself for the owners of houses or apartments this work Absolutely forbidden.
Pressure testing begins with filling the heating system with water, if before that it was empty. This is done through the return pipeline of the heating system, and more specifically through the elevator. With the help of valves located at the highest points, air is bled until a coolant appears from them.
If a water leak is detected, the system is emptied through the drain valves. The pump for crimping is connected through the control unit. The person responsible for carrying out the work has an empty form that he fills out during the event. Upon completion, they write out an act of hydraulic testing of the heating system, as it looks like in the photo.
What is the act for?
When the installation or repair of the heating structure is carried out, tests must be carried out at the end of the work in order to verify the high-quality functioning of the circuit. The pipeline and various elements of the system are checked for strength and reliability.
Further, an act of hydraulic testing of heat supply systems is drawn up. It reflects the results of the measures taken and makes a conclusion regarding the suitability of the heating structure with permission to commission.
Features of the crimping process
The system is checked for tightness under pressure, and its value exceeds the working pressure by 1.5 times.
Measures, including hydraulic tests of heat exchangers and other elements, are carried out under the following conditions:
- the pressure cannot be less than 0.6 bar;
- water temperature is constant;
- the system must be completely rid of air congestion;
- strength analysis is carried out using pressure gauges.
The sequence of hydraulic tests of the heating system
When pressing, work is carried out in stages:
- At the beginning of hydraulic tests, the pressure in the system is raised to the set value at least twice. This is usually done for half an hour, increasing it every 10 minutes. For the next 30 minutes, the pressure is maintained at a level of at least 0.6 bar.
- In the second stage, the pressure should be at least 0.2 bar. If a leak is detected in the flange or threaded assemblies of the heating system, they can be tightened. When deficiencies cannot be corrected, this connection must be replaced.
Hydraulic testing is complex and must be approached responsibly. It is not possible to do high-quality crimping on your own. It is advisable to resort to the services of special organizations that, after completion of work, will issue an act of hydraulic testing of the heating system and then, with the onset of cold weather, the house will be warm and comfortable. See also: "How to make pressure testing of the heating system with your own hands".
Detailed video about hydraulic test heating systems:
Pressure testing of the heating system: SNiP norms
The norms for pressure testing the heating system are described in documents such as SNiP 41-01-2003, and also 3.05.01-85.
Air conditioning, ventilation and heating - SNiP 41–01-2003
It is possible to carry out hydraulic checks of water heating systems only at a positive temperature in the premises of the house. In addition, they must withstand water pressure of at least 0.6 MPa without damage to the tightness and destruction.
During the test, the pressure value should not be higher than the limit for heating devices, pipelines and fittings mounted in the system.
Internal sanitary systems - 3.05.01–85
According to this SNiP rule, it is necessary to check the water heating and heating systems with the expansion vessels and boilers by hydrostatic pressure. equal to 1.5 working, but not less than 0.2 MPa in the lower part of the system.
It is considered that the heating network has passed the test if it lasts 5 minutes under test pressure and does not fall by more than 0.02 MPa. In addition, there should be no leakage in heating equipment, welds, fittings, threaded connections and pipes.
Crimping conditions
Test work is correctly carried out if all necessary requirements. For example, third-party work cannot be carried out at the test object, and the shift supervisor must supervise the testing.
Crimping is carried out only according to the program approved by the chief engineer of the company. It defines: employee procedures and technological sequence checks. They also set out safety measures for ongoing and current work performed at adjacent facilities.
There should be no strangers during the pressure testing of the heating system, turning on or off the test devices, only employees participating in the test remain in place.
When work is carried out in adjacent areas, it is imperative to provide for reliable fencing and shutdown of test equipment.
Inspection of heating devices and pipes is only allowed at working pressure values. When the pressure test of the heating system is completed, the acts are filled out to confirm the tightness.
Crimping procedure
This method of checking the heating system involves the implementation of hydraulic tests:
Thus, it is possible to identify leaks that indicate network depressurization.
Before testing the heating system with plugs, it is necessary to isolate the heating system from the water supply, visually evaluate the reliability of all connections. and check the functionality and status stop valves.
After that they turn off expansion tank and a boiler for flushing radiators, pipelines from various deposits, debris and dust.
During the hydraulic test, the heating system is filled with water, but this is not done when performing air tests, but simply a compressor is connected to the drain valve. Then increase the pressure to the required value, and monitor its performance with a pressure gauge. If there are no changes, then the tightness is good, therefore, the system can be put into operation.
When the pressure begins to decrease beyond the allowable value, means there are defects.. Leaks in a filled system are not difficult to find. But in order to identify damage during the air test, a soapy solution should be applied to all joints and joints.
It takes at least 20 hours to perform an air pressure test, and 1 hour to perform a hydraulic test.
Having corrected the identified defects, the procedure is repeated again, and this has to be done until good tightness achieved. After carrying out these works, they fill out the acts of pressure testing of heating systems.
Checking the heating network with air is usually carried out if it is impossible to fill it with water, or when working in conditions low temperatures because the liquid can just freeze.
Act of pressure testing of the heating system
This document displays the following information:
- What kind of crimping method was used;
- The project in accordance with which the circuit was installed;
- The date of the check, the address of its conduct, as well as the names of the citizens who sign the act. Basically, this is the owner of the house, representatives of the repair and maintenance organization and heating networks;
- How were the identified problems resolved?
- Check results;
- Are there signs of leakage or reliability of threaded and welded joints. In addition, it is indicated whether there are drops on the surface of fittings and pipes.
Permissible test pressure during pressure testing of water heating
Many developers are interested in under what pressure it is necessary to check the heating system. In accordance with the requirements of SNiP presented above, during pressure testing, a pressure higher than the working one by 1.5 times is allowed. but should not be less than 0.6 MPa.
There is another figure indicated in the "Rules technical operation thermal power plants. Of course, this method is “softer”, in it the pressure exceeds the working one by 1.25 times.
In private houses equipped independent heating, it does not rise above 2 atmospheres, and it is tuned artificially: if it appears overpressure . then the relief valve is immediately activated. Whereas in public and multi-apartment buildings, the working pressure is much higher than these values: five-story buildings - about 3-6 atmospheres, and tall buildings - about 7-10.
Heating system test equipment
Most often, a pressure tester is used to perform a hydraulic test. It is connected to the circuit to regulate the pressure in the pipes.
Great amount local networks heating in private buildings does not need high pressure, therefore a manual presser will suffice. In other cases, it is better to use an electric pump.
Hand-held devices for testing heating systems develop a force of up to 60 bar and more. Moreover, this is enough to check the integrity of the system even in a five-story building.
The main advantages of hand pumps:
- Acceptable cost, which makes them affordable for many consumers;
- Small weight and dimensions of manual presses. Such devices are convenient to use not only for personal purposes, but also for professional use;
- Long service life without failures and breakdowns. The device is so simply arranged that there is nothing to break in it;
- Suitable for medium and small heating equipment.
Branched and large circuits in large areas, multi-storey buildings and production facilities are only checked electrical appliances. They are capable of pumping water at very high pressure. which is unattainable for manual devices. They are equipped with a self-priming pump.
Electric pumps develop force up to 500 bar. These units, as a rule, are built into the main line or connected to any opening. Basically, the hose is connected to a tap through which the pipe was filled with coolant.
Pressure testing of heating is a very complex technological procedure. That is why you should not do it yourself, it is better to use the services of professional teams.
Hydraulic testing of pipelines of heating systems
February 28, 2016
Only proper and reliable functioning of the heating system is able to ensure a calm and normal life of the population in winter period of the year. Sometimes there are various kinds of extreme situations in which the performance of the system can differ significantly from civilian conditions. Hydraulic testing of pipelines and pressure testing are necessary to prevent situations that may arise during the heating season.
Purpose of hydraulic testing
As a rule, any heating system operates in standard mode. The working pressure of the coolant in low-rise buildings is mainly 2 atm, in nine-story buildings - 5-7 atm, in high-rise buildings- 7-10 atm. In a heat supply system laid underground, the pressure indicator can reach 12 atm.
Sometimes unexpected pressure surges occur, which leads to its increase in the network. The result is water hammer. Hydraulic testing of heating pipelines is necessary to check the system not only for the ability to function under standard normal conditions, but also for its ability to overcome hydraulic shocks.
If for some reason the heating system has not been tested, then serious accidents can occur subsequently due to hydraulic shocks, which will lead to the flooding of rooms, equipment, furniture, etc. with boiling water.
The sequence of work
Hydraulic testing of pipelines should be carried out in the following sequence.
- Pipeline cleaning.
- Installation of taps, plugs and manometers.
- Water and hydraulic press are connected.
- Pipelines are filled with water to the required value.
- The pipelines are inspected and the places where defects were found are marked.
- Elimination of defects.
- Carrying out the second test.
- Disconnection from the water supply and descent of water from pipelines.
- Removing the plug and gauges.
Preparatory work
Before performing hydraulic tests of pipelines of heating systems, it is necessary to revise all the valves, fill the seals on the valves. Insulation is being repaired and checked on pipelines. Herself heating system must be separated from the main pipeline by means of plugs.
After performing all the necessary manipulations, the heating system is filled with water. With the help of pumping equipment, excess pressure is created, its indicator is about 1.3-1.5 times higher than the working one. The resulting pressure in the heating system must be maintained for another 30 minutes. If it has not decreased, then the heating system is ready for operation. Acceptance of work on hydraulic tests is carried out by the inspection of thermal networks.
Strength and tightness tests
Preliminary and acceptance hydraulic tests of pipelines (SNiP 3.05.04-85) must be carried out in a certain sequence.
tightness
- The pressure in the pipeline increases to the test value for tightness (P g).
- The start time of the test is fixed (T n), in the measuring tank it is measured First level water (h n).
- After that, a decrease in the pressure indicator in the pipeline is monitored.
There are three options for the pressure drop, consider them.
If within 10 minutes the pressure indicator decreases by less than 2 marks on the pressure gauge scale, but does not fall below the calculated internal (P p), then the observation can be completed.
If, after 10 minutes, the pressure value drops by less than 2 marks on the pressure gauge scale, then in this case, monitoring the decrease in pressure to the internal (P p) calculated value must be continued until it drops by at least 2 marks on the pressure gauge scale.
The duration of observation for reinforced concrete pipes should not exceed 3 hours, for cast iron, steel and asbestos-cement pipes - 1 hour. After the specified time, the pressure should decrease to the calculated one (P p), otherwise, water is discharged from the pipelines into a measuring tank.
If within 10 minutes the pressure becomes less than the internal design pressure (P p), then further hydraulic tests of the pipelines of the heating systems must be suspended and measures should be taken to eliminate hidden defects by maintaining the pipes under the internal design pressure (P p) until, upon careful inspection defects will not be detected that will cause an unacceptable pressure drop in the pipeline.
Determining the additional volume of water
After completing the observation of the drop in the pressure indicator according to the first option and stopping the coolant discharge according to the second option, the following should be done.

Drawing up an act
The certificate of hydraulic testing of pipelines is evidence that all work has been carried out. This document is compiled by the inspector and confirms that the work was carried out in compliance with all norms and rules, and that the heating system withstood them successfully.
Hydraulic testing of pipelines can be carried out in two main ways:
- Manometric method - tests are carried out using pressure gauges, devices that record pressure indicators. During operation, these devices show the current pressure in the heating system. The ongoing hydraulic testing of pipelines using a pressure gauge allows the inspector to check what pressure was during testing. Thus, the service engineer and the inspector check how reliable the tests are.
- The hydrostatic method is considered the most effective, it allows you to check the heating system for performance at a pressure that exceeds the average operating rate by 50%.
During different times, various elements of the system are tested, while hydraulic tests of pipelines cannot last less than 10 minutes. In heating systems, the permissible pressure drop is 0.02 MPa.
The main condition for the beginning of the heating season is well-conducted and properly executed hydraulic tests of pipelines (SNiP 3.05.04-85), in accordance with the requirements of the current regulatory documentation.
How to cut onions and not cry - simple tips Chewing gum or lighting a candle? It's time to find out which of these myths about cutting onions without crying is true, and which one is you.
Never do this in a church! If you're not sure if you're doing the right thing in church or not, then you're probably not doing the right thing. Here is a list of the terrible ones.
15 Cancer Symptoms Women Most Often Ignore Many of the signs of cancer are similar to those of other illnesses or conditions and are often overlooked. Pay attention to your body. If you notice.
10 Adorable Celebrity Kids Who Look Very Different Today Time flies and one day little celebrities become unrecognizable adults Pretty boys and girls turn into s.
7 Body Parts You Shouldn't Touch Think of your body as a temple: you can use it, but there are some sacred places that you shouldn't touch. Display research.
Unforgivable Movie Mistakes You Probably Never Noticed There are probably very few people who don't like watching movies. However, even in the best cinema there are errors that the viewer can notice.
The act of hydraulic testing of the heating system - the result of pressure testing
The heat supply system is an engineering structure that allows you to comply with and maintain temperature parameters buildings during the winter months. A big misconception is that the heating system can work smoothly without various planned preventive measures. From the last great importance have hydraulic tests of the heating system.
These activities are carried out to find weak areas of the system that can let users down at the most inopportune time. You can see the crimping process in the photo below or in the video in our article.
Crimping of heat supply elements
Important. Testing heating systems is a set of measures that are aimed at checking, or rather, the location of weak sections of pipelines and other heating equipment during operation.
When work is done
All measures that relate to checking the heating for leaks are performed in such cases:
- During preparation for the heating season;
- When replacing circuit sections;
- After repair of heating devices;
- When putting the property into operation.
The test procedure itself is a confirmation of the tightness of the circuit .
This procedure includes the following components:
- Supply of air or water with a given pressure to the heating pipelines using special equipment;
- Finding deformations in the heating circuit;
- Elimination of violations.
Hand pump connection
It is worth noting that modern heating schemes allow such events to be carried out with a minimum number of personnel.
Regulatory rules
For proper conduct such works, a separate SNiP was specially developed, which discusses the subtleties and details of the process. In addition, it contains standard instructions for conducting such events. (See also the article Heating installation - important nuances)
SNiP itself contains technological schemes that take into account the features of work in accordance with safety regulations, as well as the necessary equipment. Any hydraulic test of the heating system must be carried out in accordance with this document.
Electric compressor connected to heating
Important. Before hydraulic testing, the system must be flushed.
It can be carried out different ways and its task is to remove deposits and scale from the inner walls of pipes.
It is produced by special solutions and a compressor.
Oxides can be observed as deposits in pipelines:
During the operation of any heat supply system, its efficiency decreases, this phenomenon occurs due to the deposits and raids described above. They lead to a decrease in the cross section of pipes and poor circulation of the coolant. (See also the article Heating and water supply systems - the benefits of civilization)
Sectional pipeline
Who does the pressing
Responsibilities for the prevention of these engineering networks are borne by institutions and organizations that operate buildings. That is, in residential buildings, these works are carried out by employees of housing departments and similar entities.
It must be clearly understood that these activities are carried out only by specially trained and tested personnel using the necessary equipment. Do-it-yourself work is strictly prohibited!
The work process begins with filling the system with water if it was empty. This is done through the return pipeline of heating networks, namely through the elevator. Thanks to the valves installed at the highest points, air is bled off until the coolant flows from the valves.
If a leak is found, the system is emptied through the drain valves. The pressure test pump is connected via the control unit. The person responsible for carrying out the work has an empty form, which is filled in during the work. Upon completion of the work, an act of testing the heating system is issued.
What is the act for?
Upon completion of installation or maintenance work, hydraulic tests are performed. These works show the condition of the entire heating system. The strength of pipelines and various components of the circuit is checked, and upon completion they draw up an act of hydrostatic testing of heating and heat supply systems.
It carries the results of all activities and a conclusion on the suitability of the heating system with permission to put it into operation.
Process
The heating system is tested for tightness by a pressure that exceeds the working one and a half times.
Work conditions:
- The pressure must not fall below 0.6 bar;
- The coolant temperature is constant;
- The system must be completely free of air pockets;
- Strength analysis is carried out through the use of pressure gauges.
Form for testing
Stages of work
- At the first stage of hydraulic testing, the pressure in the system rises at least twice to the set value. Usually do this for thirty minutes, stepping up every ten minutes. Over the next half hour, the pressure is maintained at a level of at least 0.6 bar;
- In the second stage, the pressure should not fall below 0.2 bar. If a leak is found in the threaded or flanged connections of the heating system, then they can be tightened. If the leak does not stop, then this connection must be replaced.
Conclusion
The process of hydraulic testing is very complex and responsible. (See also the article Heating project and the features of its preparation) It will not be possible to carry it out independently with high quality. Now you can easily find special organizations that are engaged in similar work, the price for their services is quite democratic. The reliability of work in the winter months will depend on the quality of these measures.
Hydraulic testing of heating systems
Hydraulic testing of heating systems real estate objects connected to the main heat supply are carried out after the installation or repair of the pipeline, precede the start of the heating season.
Goals and conditions of the test
The purpose of hydraulic testing is to determine the operability and degree of resistance of the heating system to water hammer from the inside.
For testing a system where the coolant is water, the term "pressure test" is also applicable.
The concept of hydraulic shock is defined as a sharp short-term increase in water pressure in pipes. Behind a short time it reaches a level, sometimes significantly exceeding the permissible parameters.
Photos of objects

SAO, st. Belomorskaya

SAO, st. Smolnaya

SVAO, st. Uglichskaya

SVAO, st. Pskovskaya
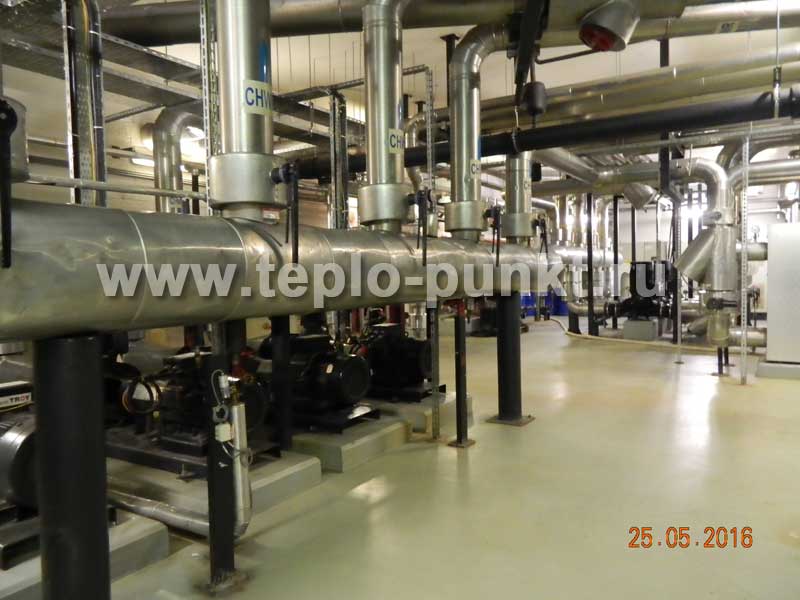
CAO, st. Earthworks
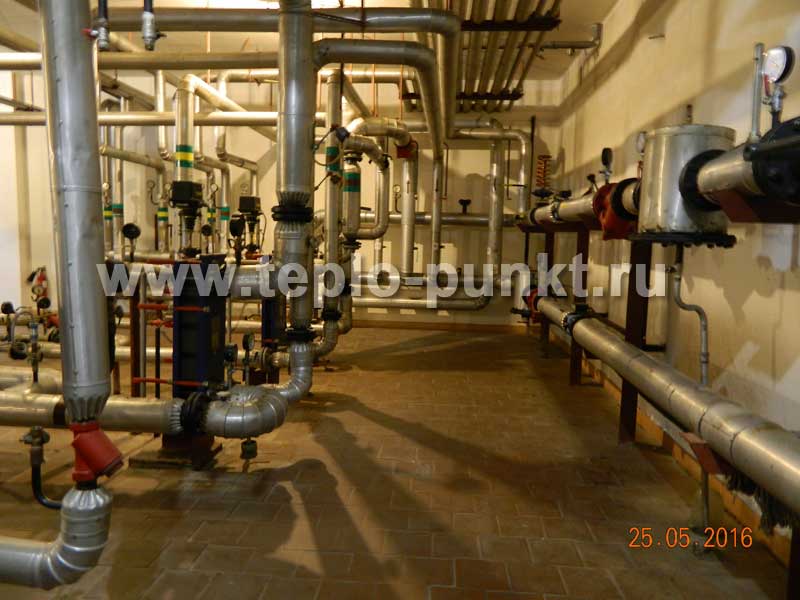
Sequencing
The algorithm for hydraulic testing is as follows:
Before starting pressing heating scheme, produced:
- visual inspection and repair (and, if necessary, replacement) of valves;
- inspection and restoration of pipe insulation;
- installation of additional seals (to improve the tightness of the system).
- clipping heating circuit from the main pipeline.
The first indicator is characterized by:
- pipe material, their diameter;
- technical condition of the pipeline;
- storey of the building.
Exact calculation of the test pressure is carried out by involved specialists.
The test takes at least 10 minutes. First, the heat supply scheme is tested for strength.
- If during the test period there is a decrease in pressure in the circuit, the water is completely drained.
Then, the identified defects are repaired, and the coolant is again supplied under pressure.
- If during the specified period of time the pressure gauges did not record a decrease in the pressure of the medium, then the pipeline is strong enough.
Only then can you proceed with the leak test.
The pressure in the pipes is again brought to the test pressure, and the system is monitored for 10 minutes.
Possible results:
- During the specified time, the pressure did not decrease - the circuit is tight.
- If P has decreased by 2 Pa or more, the observation continues in order to fix the time during which the pressure reaches the calculated values.
For pipes made of steel, cast iron, asbestos concrete, the maximum duration of observation should not exceed 1 hour, for reinforced concrete - 3 hours.
- If P test for 10 minutes fell to the worker, testing is stopped. The pipeline is being repaired, and the test is carried out according to the specified algorithm again.
If the system has successfully passed the tests, the inspector of the Gostekhnadzor service draws up an act on the basis of which the heating system is put into operation.
Qualitatively conducted tests of the heat supply scheme allow for uninterrupted heating of premises, without the risk of an accident.
Before testing, all plumbing pipes must be flushed. Prior to testing, the compliance of the tested ristem with the project is checked, an external inspection of pipelines, connections, equipment, instruments, fittings is carried out.
The system as a whole and individual types of equipment are subjected to testing, as well as their regulation. According to the test results, acts are drawn up.
Tests are performed by hydrostatic and manometric (pneumatic) methods.
Hydrostatic tests are carried out by filling all elements of the system with water (with complete removal of air), increasing the pressure to test pressure, keeping the system under test pressure for a certain time, reducing pressure and, if necessary, emptying the system.
Tests of heating systems, heat supply, boilers, water heaters are carried out before finishing the premises and at a positive temperature in the building. The temperature of the water that fills the system must be at least 278 K (5°C).
Gauge tests are largely devoid of the shortcomings of hydrostatic tests, but they are more dangerous, since if pipelines or system elements are accidentally destroyed under the action of compressed air, their pieces can get into the people conducting the tests.
Manometric tests are carried out by filling the system with compressed air at a pressure equal to the test pressure, and keeping it under this pressure for a certain period, then the pressure is reduced to atmospheric pressure. For testing, a pneumohydraulic unit TsSTM-10 is used, made in the form of a two-axle trailer, on which a container with a volume of 2.5 m3 and all the equipment necessary for testing are mounted.
Testing of heating systems. Hydrostatic tests of the water heating system are carried out at the end of its installation and inspection. To do this, the system is filled with water and air is completely removed from it by opening all air collectors, taps on the risers and at the heaters. Fill the system through the return line, connecting it to a permanent or temporary water supply. After filling the system, close all air collectors and turn on a manual or powered hydraulic press, which creates the required pressure.
Water heating systems are tested with a pressure equal to 1.5 working pressure, but not less than 0.2 MPa at the lowest point. During the test, the boilers and the expansion vessel are disconnected from the system. The pressure drop during the test shall not exceed 0.02 MPa for 5 min. The pressure is controlled by a checked and sealed pressure gauge with divisions on the scale through 0.01 MPa. Minor faults found that do not interfere with the hydrostatic test are marked with chalk and then corrected.
Hydrostatic testing of panel heating systems is carried out before sealing the installation windows with a pressure of 1 MPa for 15 minutes. In this case, the pressure drop should not exceed 0.01 MPa. At negative outside temperatures, a manometric test of these systems is allowed.
After the hydrostatic test, a thermal test of the system is carried out for 7 hours, checking the uniformity of heating of the heaters. If the outside air temperature is positive, then the water temperature in the supply lines must be at least 60°C, if negative, at least 50°C.
Steam heating systems with working pressure up to
0.07 MPa is tested with a pressure equal to 0.25 MPa at the lowest point of the system. After the hydrostatic test, the steam heating system is tested for the tightness of the heat pipe connections. To do this, steam is allowed into the system at operating pressure.
Water heaters are tested for density with a pressure of 1.25 times the working pressure plus 0.3 MPa for the steam part and 0.4 MPa for the water part.
Pumping units are tested first at idle, and then under load. Before testing, the installation is carefully inspected, the reliability of fastening, the absence of any objects inside (gaskets, parts) are checked. To do this, the pump shaft is turned manually and turned on for 3-5 minutes. When extraneous noises and knocks appear, the pump is turned off and disassembled. During normal operation, the pump is run in for 12-15 minutes, after which the rubbing parts are checked, there is no overheating. Causes of overheating can be inaccurate fit, misalignment, tight tightening, contamination of rubbing parts or lubricating oil. Then the pump is run in for 1 hour, then 6 hours, monitoring its condition. If no defects are found, the pump is switched on for trial operation and put under load.
The test results are documented in the act of acceptance of the heating system.
Heat pipelines of heat networks are subjected to a pressure test equal to the working one with a coefficient of 1.25, but not less than 1.6 MPa. During the test, the following requirements are observed: the valves in the test area must be fully open, the stuffing boxes are sealed. To disconnect the tested section of the heat pipeline from the existing networks, plugs must be installed.
After filling the line with water with a temperature of at least 5 ° C, a pressure equal to the working pressure is set in the heat pipes and maintained for 10 minutes. If no defects or leaks are found at the operating pressure, it is brought to the test pressure and kept for the time necessary to inspect the route, but not less than 10 min.
The results of testing heat pipelines are considered satisfactory if during the test the pressure did not drop, and there were no signs of rupture, leakage or fogging in the welded seams of pipes and valve bodies.
In the course of installation work, in some cases, the hydrostatic test of heat networks is replaced by a manometric test (usually by separate sections of the heat pipeline no longer than 200 m long).
To put the heating into operation, it is imperative to flush and pressure test the system. After completing this procedure, an act is filled out confirming that the installation of the heating network is done correctly. Employees authorized to perform this work are required to complete all relevant regulations.
Crimping rules SNiP
The norms for pressure testing the heating system are described in documents such as SNiP 41-01-2003, and also 3.05.01-85.
Air conditioning, ventilation and heating - SNiP 41–01-2003
It is possible to carry out hydraulic checks of water heating systems only at a positive temperature in the premises of the house. In addition, they must withstand water pressure of at least 0.6 MPa without damage to the tightness and destruction.
During the test, the pressure value should not be higher than the limit for heating devices, pipelines and fittings mounted in the system.
Internal sanitary systems - 3.05.01–85
According to this SNiP rule, it is necessary to check the water heating and heating systems with the expansion vessels and boilers by hydrostatic pressure equal to 1.5 working, but not less than 0.2 MPa in the lower part of the system.
It is considered that the heating network has passed the test if it lasts 5 minutes under test pressure and does not fall by more than 0.02 MPa. In addition, there should be no leakage in heating equipment, welds, fittings, threaded connections and pipes.
Crimping conditions
Test work is correctly carried out if all the necessary requirements are met. For example, third-party work cannot be carried out at the test object, and the shift supervisor must supervise the testing.
Crimping is carried out only according to the program approved by the chief engineer of the company. It defines: the procedure for the actions of employees and the technological sequence of verification. They also set out safety measures for ongoing and current work performed at adjacent facilities.
There should be no strangers during the pressure testing of the heating system, turning on or off the test devices, only employees participating in the test remain in place.
When work is carried out in adjacent areas, it is imperative to provide for reliable fencing and shutdown of test equipment.
Inspection of heating devices and pipes is only allowed at working pressure values. When the pressure test of the heating system is completed, the acts are filled out to confirm the tightness.
Crimping procedure
This method of checking the heating system involves the implementation of hydraulic tests:
- Heat exchangers;
- boilers;
- Pipes.
Thus, it is possible to identify leaks that indicate network depressurization.
Before testing the heating system with plugs, it is necessary to isolate the heating system from the water supply, visually evaluate the reliability of all connections, as well as check the operability and condition of the shut-off valves.
After that, the expansion tank and boiler are turned off to flush radiators, pipelines from various deposits, debris and dust.
During the hydraulic test, the heating system is filled with water, but this is not done when performing air tests, but simply a compressor is connected to the drain valve. Then increase the pressure to the required value, and monitor its performance with a pressure gauge. If there are no changes, then the tightness is good, therefore, the system can be put into operation.
When the pressure begins to decrease beyond the allowable value, means there are defects.. Leaks in a filled system are not difficult to find. But in order to identify damage during the air test, a soapy solution should be applied to all joints and joints.
It takes at least 20 hours to perform an air pressure test, and 1 hour to perform a hydraulic test.
Having corrected the identified defects, the procedure is repeated again, and this has to be done until good tightness achieved. After carrying out these works, they fill out the acts of pressure testing of heating systems.
Checking the heating network with air is usually carried out if it is impossible to fill it with water, or when working at low temperatures, because the liquid can simply freeze.
Act of pressure testing of the heating system
This document displays the following information:
- What kind of crimping method was used;
- The project in accordance with which the circuit was installed;
- The date of the check, the address of its conduct, as well as the names of the citizens who sign the act. Basically, this is the owner of the house, representatives of the repair and maintenance organization and heating networks;
- How were the identified problems resolved?
- Check results;
- Are there signs of leakage or reliability of threaded and welded joints. In addition, it is indicated whether there are drops on the surface of fittings and pipes.
Permissible test pressure during pressure testing of water heating
Many developers are interested in under what pressure it is necessary to check the heating system. In accordance with the requirements of SNiP presented above, during pressure testing, a pressure higher than the working one by 1.5 times is allowed, but should not be less than 0.6 MPa.
There is another figure indicated in the "Rules for the technical operation of thermal power plants." Of course, this method is “softer”, in it the pressure exceeds the working one by 1.25 times.
In private houses equipped with autonomous heating, it does not rise above 2 atmospheres, and it is adjusted artificially: if there is excess pressure, then the relief valve immediately turns on. Whereas in public and multi-apartment buildings, the working pressure is much higher than these values: five-story buildings - about 3-6 atmospheres, and tall buildings - about 7-10.
Heating system test equipment
Most often, a pressure tester is used to perform a hydraulic test. It is connected to the circuit to regulate the pressure in the pipes.
A huge number of local heating networks in private buildings do not need high pressure, therefore a manual presser will suffice. In other cases, it is better to use an electric pump.
To provide heat in the house in winter, you need a reliable and efficient heating system. After installing the boilers, installing pipes, replacing individual components, as well as in preparation for the new season, hydraulic tests of the heating system are carried out. These tests are aimed at identifying leaks, local damage, leaky connections and other problems that can cause the system to become inoperable during operation.
If in apartments hydraulic testing and pressure testing falls on the shoulders of housing and communal services workers, then owners of private houses should contact specialists or conduct hydraulic tests with their own hands.
Hydraulic testing of pipelines of heating systems
Hydraulic testing of the heating system is a prerequisite to ensure comfortable conditions in a private house. Over time, heating elements wear out and fail, testing the heating system helps prevent damage during the heating season.
Before installing heating elements and pipelines, a hydraulic calculation of the heating system is carried out, taking into account the material and inner diameter pipes, diameter of fittings and fittings, pipe wall thickness and other technical parameters. With incorrect calculations, the efficiency of the system can be significantly reduced, and the operating period can be reduced several times.
Consider how the calculation of the diameter of the pipeline of the heating system is carried out and the diameter of the pipes is determined depending on the nominal load on a single section.
Calculation of the section of the heating pipe
D = √354∙(0.86∙Q:∆t):V
where D- diameter of the heating pipe, cm;
Q- load on the calculated section of the system, kW;
∆t– temperature difference between the falling and return pipes, ᵒС;
V is the speed of movement of the coolant, m/s.
This calculation allows you to determine the average diameter of the pipe of the heating system. Professional calculations of the heating system use significantly more data. In this case, not only the size of an individual pipe is determined, but also the diameters of the narrowed sections, the distance between the pipelines, and so on.
Why is hydraulic testing of a heating system necessary?
Each individual heating system has its own operating pressure, which determines the degree of heating of the room, the quality of the circulation of the coolant, and the level of heat loss. The choice of working pressure is influenced by a number of factors, including the type of building, the number of storeys, the quality of the line, and so on.
While the coolant moves through the pipelines, various hydraulic processes occur, which lead to pressure drops in the system, called water hammer. It is these loads that usually cause the accelerated destruction of the heating system, therefore hydraulic tests are carried out at a pressure 40% higher than the nominal one.
Hydraulic testing of pipelines of heating systems is carried out after performing the following work:
- checking valves, serviceability of valves of shut-off type;
- strengthening the tightness of the system by means of additional glands (if necessary);
- restoration of pipeline insulation layers, replacement of worn materials;
- cutting off the house common system with a blind plug.
When carrying out pressure testing, as well as for further filling the system with coolant, a drain-type valve is used, which is installed on the return.
Technology for pressure testing of the heating system
In the process of filling the system, the liquid is supplied under moderate pressure, which makes it possible for it to gradually fill all the elements of the system. Air must be bled from the system from time to time.
In apartments multi-storey buildings leaks are detected by testing with a pressure of 20 - 30% higher than the working one. For this, a special press is used to pressure test the heating system, and the pressure is controlled by a pressure gauge. After reaching the required pressure, the system is left for 30 minutes. If the pressure subsequently decreases, then there are leaks or leaks in the system.
The most common cause of loss of tightness is damage to gaskets, valves, junctions or pipe bends, wear threaded connections or radiators. After troubleshooting and re-checking, a act of testing the heating system. A heating system that is ready for start-up without damage and leakage of the coolant is considered to be pressurized.
Crimping of a warm floor, features of carrying out
In addition to the heating system, the underfloor heating also needs to be checked regularly. Pressure testing of the warm floor is carried out until the pressure in the system stops dropping. Required pressure in the system is achieved by using a pressure test pump. In apartments of multi-storey buildings, medical and educational institutions pressure testing is carried out by special supervisory authorities. After the tests, a hydraulic test report is drawn up, which indicates the control parameters and the date of the test.
During the installation of the underfloor heating system, different links may become clogged with small debris, and the connections may be deprived of tightness. All this can interfere with the normal functioning of the warm floor, cause leaks or loss of efficiency. Crimping of the warm floor is carried out immediately after installation before pouring the screed or laying the finished floor.
During pressure testing, the underfloor heating system is filled with water from the central pipeline through the valve for filling and draining the coolant. Test pressure during a hydraulic test, it should be 2.5 - 2.8 atm. After filling the system, it must be left for 20 - 30 minutes, leaks should be identified and eliminated.
When pouring water into the underfloor heating system is difficult, pressure testing can be done by forcing air masses. To do this, you can use a compressor or a car pump with a pressure gauge, which must be connected to any valve in the system. Also, for crimping underfloor heating, you can use special crimping machines, the cost of which is usually quite high. The pressure during pressure testing with air should be 2 - 3 times higher than the working one. For example, at an operating pressure of 1.5 - 2 atm. It is necessary to achieve a pressure of about 5 atm.
After filling the system with water or air, check all connections for leaks. The filled underfloor heating system can be left under pressure for 24 hours to check the strength of the connections and detect leaks. It should be remembered that with temperature changes in the room, the pressure in the system also slightly decreases. After pressing the underfloor heating, you can lay the finishing floor or pour the screed.