skärningslägen. Matningar vid grovsvarvning blev hårdmetallfräsar utan extra skäregg. Stort uppslagsverk om olja och gas
Svarvning kan utföras med mekanisk matning, eftersom generatrisen för den bearbetade konen är parallell med riktningen för skärarens längsgående matning.
Den kopieringsteknologiska cykeln används för att bearbeta stegvisa, koniska och krökta ytor som kräver en längsgående matning av fräsen. I slutet av ytbehandlingen dras skäraren tillbaka från delen och bromsoket återgår till sitt ursprungliga läge.
Allmänt index för en gängskärningsmaskin. |
Det längsgående stödet 7, monterat på bäddens styrningar, rör sig längs dessa och tillhandahåller en längsgående matning av skäraren. Tvärvagnen ger korsmatning till fräsen. Det övre roterande stödet kan ställas in i valfri vinkel mot arbetsstyckets rotationsaxel, vilket är nödvändigt vid bearbetning av koniska ytor på arbetsstycken.
Schema för att vända ett format arbetsstycke. |
Efter den tvärgående förskjutningen av bakstyckets kropp med en mängd h upp till 15 - 20 mm), är generatrisen för den bearbetade konen parallell med riktningen för skärarens längsgående matning, så svarvning kan utföras med mekanisk matning .
System för att vända matlagning. |
Efter den tvärgående förskjutningen av bakstyckets kropp med värdet h (upp till 15 - 20 mm), är generatrisen för den bearbetade konen parallell med riktningen för skärarens längsgående matning, så svarvning kan utföras med mekanisk utfodra.
För gängning på en svarv är det nödvändigt att spindelns rotationshastighet är strikt kopplad till bromsokets rörelsehastighet, eftersom skärarens längsgående matning i ett varv av spindeln måste exakt matcha gängans stigning skärs.
Tjockleken på det skurna metallskiktet påverkar i hög grad storleken på ojämnheterna. Tjockleken på det skurna lagret bestäms av skärmaskinens längsgående matning. Om det inte förekom några elastisk-plastiska deformationer under skärprocessen, skulle höjden på ojämnheterna lätt kunna beräknas från geometrisk form toppen av skäraren.
Efter 1 minut från början av arbetet, stäng av skärarens längsgående matning, flytta fräsen bort från arbetsstycket och vrid snabbt verktygshållaren 90 eller 180 tills knivens spets vidrör indikatorspetsen.
För diamanter i en ram bör de längsgående matningarna vara mindre än för pennor och ännu mindre för slipade diamanter. Till exempel, när man bearbetar flertrådiga gängslipskivor med diamantskärare, bör den längsgående matningen av fräsen inte vara mer än 0 05 m / min. I slutet av förbandsprocessen rekommenderas att göra en eller två pass utan korsmatning, vilket minskar mängden längsgående foder.
Fixturen är utformad för borrning av koniska hål med konstant vinkel a. Enheten är fixerad på det radiella stödet på maskinens frontplatta. Genom att vrida skruven 3 matas skäret i längdriktningen. I den andra änden av skruven är en asterisk 1 installerad, som hoppar med sin tand vid varje varv av bromsoket på det inställda stoppet och utför automatisk längsgående matning.
För att bearbeta arbetsstycket genom att skära och som ett resultat av detta erhålla de bearbetade ytorna på en viss del, arbetsstycket och det applicerade skärverktyg skulle göra vissa rörelser. Dessa rörelser är indelade i huvud (som tjänar för genomförandet av skärprocessen) och hjälpmedel (som tjänar till att förbereda för skärningsprocessen och för att slutföra operationen). Det finns två huvudrörelser:
- skärande rörelse (eller huvudrörelse);
- matningsrörelse.
Vid bearbetning på en svarv utförs skärrörelsen - roterande - av arbetsstycket, som är fäst på ett eller annat sätt till maskinspindeln, och matningsrörelsen - translationell - får ett skärverktyg (skär) stelt fast i verktyget hållare. Rörelsen möjliggör skärningsprocessen (spånbildning), rörelsen av matningen gör det möjligt att genomföra denna process (bearbetning) längs hela längden av arbetsstycket (Fig. Del 16).
Skärdjup (t)- värdet av det skurna lagret i en passage, mätt i riktningen vinkelrätt mot den bearbetade ytan. Skärdjupet är alltid vinkelrätt mot matningsriktningen (se även fig. 11-14). Med extern längsgående svarvning (fig. 16) är det en halv skillnad mellan diametern på arbetsstycket och diametern på den bearbetade ytan som erhålls efter en passage:
Skärhastighetυ - mängden punktrörelse allra senaste i förhållande till ytan per tidsenhet under genomförandet av skärrörelsen *.
Vid svarvning, när arbetsstycket roterar med en frekvens av n rpm, kommer skärhastigheten vid skäreggens MK-punkter att vara ett variabelt värde. Högsta hastighet:
där D är den största ytdiametern i mm.
* Skärhastigheten är en funktion av arbetsstyckets rotationshastighet och verktygets rörelsehastighet (matningshastighet).
Om hastigheten är känd är det lätt att bestämma rotationsfrekvensen:
Vid längsgående svarvning har skärhastigheten ett konstant värde under hela skärtiden (om diametern på arbetsstycket längs hela dess längd är densamma och rotationshastigheten är oförändrad). Vid trimning av änden, när fräsen rör sig från arbetsstyckets periferi till mitten, är skärhastigheten vid konstant hastighet variabel. Hon har högsta värde vid periferin och är lika med noll i mitten (fig. 17). Skärhastigheten kommer också att variera längs den bearbetade ytan under avstickning (se fig. 14). Men i dessa fall, överväg toppfart skärande.
Inlämning s(närmare bestämt matningshastighet) - storleken på skäreggens rörelse i förhållande till den bearbetade ytan per tidsenhet i matningsrörelsens riktning. Vid vändning kan det vara längsgående matning när fräsen rör sig i en riktning parallell med arbetsstyckets axel (se fig. 16); korsmatning när fräsen rör sig i en riktning vinkelrät mot arbetsstyckets axel (se fig. 17), och sned matning- i en vinkel mot arbetsstyckets axel (till exempel vid vridning av en konisk yta).
Särskilj tonhöjd i ett varv arbetsstycket, dvs. graden av relativ rörelse av fräsen under ett varv av arbetsstycket (från position I flyttade fräsen till position II, fig. 16), och minut matning, dvs. värdet på fräsens relativa rörelse under 1 min. Minutmatning indikeras med S m (mm / min), och matning per varv - s (mm / varv). Det finns följande förhållande mellan dem.
till hemmet
avsnitt tre
Grunderna i teorin om metallskärning.
Val av skärdata
Kapitel VI
Grunderna i teorin om metallskärning
Grundarna av teorin om skärande metaller var de framstående ryska forskarna I. A. Time (1838-1920), K. A. Zvorykin (1861-1928), Ya. G. Usachev (1873-1941) och andra. Dessa forskares verk, som fick världserkännande har ännu inte förlorat sitt värde. Men under förhållandena i det efterblivna tsariska Ryssland, hittade inte alla dessa verk praktisk applikation eftersom branschen var underutvecklad.
Vetenskapen om bearbetning av metall fick stor omfattning först efter den stora socialistiska oktoberrevolutionen, särskilt under de sovjetiska femårsplanerna, då vetenskapen ställdes i den socialistiska industrins tjänst.
Sovjetiska vetenskapsmän V.D. Kuznetsov, V.A. Krivoukhov, I.M. metaller, särdrag som är det nära samarbetet mellan vetenskap och produktion, forskare med innovatörer av produktion.
En viktig roll i utvecklingen av vetenskapen om att skära metaller spelades av rörelsen av innovatörer i produktionen. I ett försök att öka arbetsproduktiviteten började produktionsledare leta efter nya sätt att förbättra skärförhållandena: de skapade en ny skärverktygsgeometri, ändrade skärförhållanden, bemästrade nya skärmaterial. Varje arbetsplats Turner-innovator har blivit som ett litet laboratorium för att studera skärprocessen.
Ett brett erfarenhetsutbyte, endast möjligt under villkoren för en socialistisk ekonomi, och nära samarbete mellan ledande arbetare inom produktion och vetenskap säkerställde den snabba utvecklingen av vetenskapen om skärande metaller.
1. Kutterens arbete
Wedge och hans verk. Den arbetande delen av alla skärverktyg är kil(Fig. 44). Under verkan av den applicerade kraften skär spetsen av kilen in i metallen.
Ju skarpare kilen är, det vill säga ju mindre vinkeln som bildas av dess sidor, desto mindre kraft krävs för att skära den i metallen. Vinkeln som bildas av kilens sidor kallas avsmalnande vinkel och betecknas med den grekiska bokstaven β ( beta). Därför, ju mindre avsmalningsvinkeln β, desto lättare tränger kilen in i metallen, och omvänt, ju större avsmalningsvinkeln β är, desto större kraft måste anbringas för att skära metallen. Vid tilldelning av konvinkeln är det nödvändigt att ta hänsyn till de mekaniska egenskaperna hos metallen som bearbetas. Om du skär hårdmetall med en fräs som har en liten skärpningsvinkel β, kommer det tunna bladet inte att motstå och kommer att smulas sönder eller gå sönder. Därför, beroende på hårdheten hos metallen som bearbetas, tilldelas en lämplig skärpningsvinkel för kilen.
Metallskiktet som bearbetas, placerat direkt framför fräsen, komprimeras kontinuerligt av dess främre yta. När skärmaskinens kraft överstiger vidhäftningskrafterna för metallpartiklarna, klipps det komprimerade elementet av och förskjuts av kilens främre yta uppåt. Skäraren, som rör sig framåt under verkan av den applicerade kraften, kommer att fortsätta att komprimera, flisa och växla enskilda element av vilka chips bildas.
Grundläggande rörelser i svängning. Vid bearbetning på svarvar roterar arbetsstycket, och fräsen får rörelse i längsgående eller tvärgående riktning. Arbetsstyckets rotation kallas huvudrörelse, och skärarens rörelse i förhållande till delen - matningsrörelse(Fig. 45).
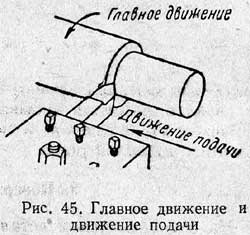
2. Huvuddelarna och delarna av svarvverktyget
Kuttern består av två huvuddelar: huvudet och kroppen (staven) (bild 46). Huvudär den arbetande (skärande) delen av skäraren; kropp tjänar till att säkra skäraren i verktygshållaren.

Huvudet består av följande delar: främre ytan, längs vilken markerna lossnar, och bakre ytor vänd mot arbetsstycket. En av de bakre ytorna som vetter mot skärytan kallas huvud; den andra, vänd mot den behandlade ytan, - extra.
Skärkanter erhålls från skärningspunkten mellan de främre och bakre ytorna. Skilja på Hem och extra skäregg. Det mesta av skärarbetet utförs av huvudskäret.
Skärningen mellan huvud- och sekundärskäreggarna kallas framtandsspets.
3. Ytbehandling
Tre typer av ytor urskiljs på arbetsstycket (bild 47): bearbetad, bearbetad och skäryta.

bearbetas yta är ytan på arbetsstycket från vilken spån avlägsnas.
Ytbehandlad kallas ytan på den del som erhålls efter spånborttagning.
skäryta kallas den yta som bildas på arbetsstycket av skärarens huvudskär.
Det är också nödvändigt att skilja mellan skärplanet och basplanet.
skärplan kallas planet som tangerar skärytan och passerar genom skäreggen på fräsen.
Huvudplan kallas ett plan parallellt med skärmaskinens längsgående och tvärgående matningar. För svarvar sammanfaller den med verktygshållarens horisontella stödyta.
4. Skärvinklar och deras syfte
Vinklarna på skärarens arbetsdel påverkar i hög grad flödet av skärprocessen.
Genom att välja rätt vinkel på skäraren kan du avsevärt öka varaktigheten av dess kontinuerliga drift fram till trubbighet (hållbarhet) och process per tidsenhet (per minut eller timme) stor kvantitet detaljer.
Skärkraften som verkar på fräsen, den erforderliga kraften, kvaliteten på den bearbetade ytan etc. beror också på valet av skärets vinklar. Det är därför varje vändare måste studera syftet med var och en av skärpningsvinklarna på fräsen. skäraren och kunna korrekt välja sitt mest fördelaktiga värde.
Fräsens vinklar (Fig. 48) kan delas in i huvudvinklarna, skärarens vinklar i planen och lutningsvinkeln för huvudskäreggen.
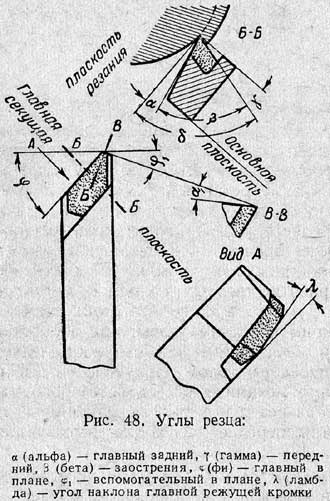
Huvudvinklarna inkluderar: ryggvinkel, frontvinkel och konvinkel; skärarens vinklar i planen inkluderar huvud och extra.
Skärarens huvudvinklar ska mätas i huvudskärplanet, som är vinkelrätt mot skärplanet och huvudplanet.
Den arbetande delen av fräsen är en kil (skuggad i fig. 48), vars form kännetecknas av vinkeln mellan främre och bakre huvudytor på fräsen. Detta hörn kallas avsmalnande vinkel och betecknas med den grekiska bokstaven β (beta).
ryggvinkel α ( alfa) är vinkeln mellan huvudflanken och skärplanet.
Frigångsvinkel α tjänar till att minska friktionen mellan fräsens baksida och arbetsstycket. Genom att minska friktionen minskar vi därmed uppvärmningen av fräsen, som på grund av detta sliter mindre. Men om avlastningsvinkeln ökas kraftigt, försvagas framtanden och förstörs snabbt.
främre vinkeln γ ( gamma) är vinkeln mellan fräsens främre yta och planet vinkelrätt mot skärplanet, ritad genom huvudskäreggen.
Spånvinkeln γ spelar en viktig roll i spånbildningsprocessen. Med en ökning av spånvinkeln är det lättare att skära skäraren i metallen, deformationen av det skurna lagret minskas, spånflödet förbättras, skärkraften och energiförbrukningen minskar och kvaliteten på den bearbetade ytan är förbättrad. Å andra sidan leder en överdriven ökning av spånvinkeln till en försvagning av skäreggen och en minskning av dess styrka, till ett ökat slitage på fräsen på grund av avflisning av skäreggen och till en försämring av värmeavlägsnandet. . Därför, vid bearbetning av hårda och spröda metaller, för att öka verktygets styrka, såväl som dess hållbarhet, bör fräsar med en mindre spånvinkel användas; vid bearbetning av mjuka och formbara metaller bör fräsar med stor spånvinkel användas för att underlätta borttagning av spån. I praktiken beror valet av frontvinkel, utöver mekaniska egenskaper material som bearbetas, från skärmaskinens material och formen på frontytan. Rekommenderade spånvinklar för hårdmetallfräsar anges i tabell. ett.
Plan vinklar. Ledande vinkel φ ( fi) kallas vinkeln mellan huvudskäreggen och matningsriktningen.
Vinkeln φ väljs vanligtvis i intervallet 30-90° beroende på typen av bearbetning, typen av fräs, styvheten hos arbetsstycket och fräsen och metoden för deras fastsättning. Vid bearbetning av de flesta metaller med genomgående avskalningsfräsar är det möjligt att ta vinkeln φ = 45°; vid bearbetning av tunn långa delar i mitten är det nödvändigt att använda fräsar med en blyvinkel på 60, 75 eller till och med 90 ° så att delarna inte böjs eller darrar.
Hjälpvinkel i planφ 1 är vinkeln mellan den sekundära skäreggen och matningsriktningen.

Vinkel λ ( lambda) huvudskärets lutning(Fig. 49) är vinkeln mellan huvudskäreggen och linjen som dras genom toppen av fräsen parallellt med huvudplanet.
bord 1
Rekommenderade spån- och släppningsvinklar för hårdmetallverktyg
Notera. Metallers mekaniska egenskaper bestäms på speciella maskiner och instrument och varje egenskap får sin egen beteckning. Beteckningen σ b som ges i denna och efterföljande tabeller uttrycker metallens draghållfasthet; värdet för denna gräns mäts i kg/mm². Bokstäverna HB betecknar metallens hårdhet, som bestäms på Brinell-anordningen genom att en härdad stålkula trycks in i metallens yta. Värdet på hårdhet mäts i kg / mm 2.
Fräsar vars spets är den lägsta punkten på skäreggen, dvs vinkeln λ positiv(Fig. 49, c), är mer hållbara och motståndskraftiga; med sådana fräsar är det bra att bearbeta hårdmetaller, såväl som intermittenta ytor som skapar en stötbelastning. Vid bearbetning av sådana ytor hårdmetallfräsar lutningsvinkeln för huvudskäreggen justeras till 20-30°. Fräsar vars spets är den högsta punkten på skäreggen, dvs vinkeln λ negativ(Fig. 49, a), rekommenderas att använda för bearbetning av delar av mjuka metaller.
5. Material som används för tillverkning av framtänder
Vid arbete på skärkanten uppstår högt tryck, såväl som hög temperatur (600-800 ° och högre). Friktionen av fräsens baksida på skärytan och spån på fräsens främre yta orsakar mer eller mindre snabb förslitning av dess arbetsytor. På grund av slitage ändras skärdelens form och fräsen blir efter en tid oanvändbar för vidare arbete; en sådan skärmaskin måste tas bort från maskinen och slipas igen. För att öka verktygets livslängd utan omslipning är det nödvändigt att dess material motstår slitage vid höga temperaturer. Dessutom måste materialet i skäraren vara tillräckligt starkt för att tåla höga tryck uppstår under skärning. Därför ställs följande grundläggande krav på skärarnas material - hårdhet vid hög temperatur, bra slitstyrka och styrka.
För närvarande finns det många verktygsstål och legeringar som uppfyller dessa krav. Dessa inkluderar: kolverktygsstål, höghastighetsstål, hårda legeringar och keramiska material.
Kolverktygsstål. För tillverkning av skärverktyg används stål med en kolhalt på 0,9 till 1,4 %. Efter härdning och härdning får skärverktyget av detta stål hög hårdhet. Men om under skärprocessen temperaturen på skärkanten når 200-250 °, sjunker stålets hårdhet kraftigt.
Av denna anledning är kolverktygsstål för närvarande av begränsad användning: det används för att tillverka skärverktyg som arbetar med en relativt låg skärhastighet när temperaturen i skärzonen når ett lågt värde. Sådana verktyg inkluderar: stansar, brotschar, kranar, filar, skrapor, etc. Fräsar tillverkas för närvarande inte av kolverktygsstål.
Höghastighetsstål. Höghastighetsstål innehåller Ett stort antal speciella, så kallade legeringselement - volfram, krom, vanadin och kobolt, som ger stål höga skäregenskaper - förmågan att bibehålla hårdhet och slitstyrka vid upphettning under skärning till 600-700 °. HSS-fräsar tillåter 2-3 gånger högre skärhastigheter än kolfräsar.
För närvarande tillverkas följande kvaliteter av höghastighetsstål (GOST 9373-60) i Sovjetunionen: R18, R9, R9F5, R14F14, R18F2, R9K5, R9KYU, R10K5F5 och R18K5F2.
Fräsar gjorda helt av höghastighetsstål är dyra, därför används främst fräsar med svetsade plåtar för att spara höghastighetsstål.
Hårda legeringar. Karbidlegeringar kännetecknas av mycket hög hårdhet och god slitstyrka.
Hårda legeringar tillverkas i form av plattor av volfram och titanpulver kombinerat med kol. Kombinationen av kol och volfram kallas volframkarbid och med titan, titankarbid. Kobolt tillsätts som bindemedel. Denna pulverformiga blandning pressas under högt tryck för att erhålla små plattor, som sedan sintras vid en temperatur av cirka 1500°. De färdiga plattorna kräver inga värmebehandling. Plåten är lödd med koppar till skärhållaren av kolstål eller fäst på den med hjälp av justeringar och skruvar (mekanisk fastsättning av plattorna).
Den största fördelen med hårda legeringar ligger i det faktum att de motstår nötning av fallande spån och arbetsstycket väl och inte förlorar sina skäregenskaper även när de värms upp till 900-1000 °. Tack vare dessa egenskaper är fräsar utrustade med hårdmetallskär mest lämpade för bearbetning fasta metaller(hårda stål, inklusive härdade) och icke-metalliska material (glas, porslin, plast) vid skärhastigheter som är 4-6 gånger eller mer högre än de skärhastigheter som tillåts av höghastighetsskärare.
Nackdelen med hårda legeringar är ökad sprödhet.
För närvarande produceras två grupper av hårda legeringar i Sovjetunionen. De viktigaste är - volfram(VK2, VKZ, VK4, VK6M, VK6, VK8 och VK8M) och titan-volfram(T30K4, T15K6, T14K8, T5K10). Var och en av dessa grupper har en specifik omfattning (tabell 2).
Alla volframlegeringar är avsedda för bearbetning av gjutjärn, icke-järnmetaller och deras legeringar, härdade stål, rostfria stål och icke-metalliska material (ebonit, porslin, glas, etc.). För bearbetning av stål används hårda legeringar av titan-volframgruppen.
Keramiska material. Nyligen har sovjetiska metallurger skapat billiga material med höga skäregenskaper, som i många fall ersätter hårda legeringar. Dessa är keramiska material termokorund), framställd i form av plattor vit färg, som påminner om marmor, som likt hårda legeringar antingen är fastlödda på skärhållarna eller mekaniskt fästa vid dem. Dessa plattor innehåller inte så dyra och knappa grundämnen som volfram, titan etc. Samtidigt har keramiska plattor en högre hårdhet än hårda legeringar och behåller sin hårdhet vid uppvärmning till 1200° vilket gör det möjligt att skära metaller med dem med höga hastigheter skärande.
Nackdelen med keramiska plattor är deras otillräckliga viskositet. Fräsar utrustade med keramiska skär kan användas för finbearbetning eller halvbearbetning av gjutjärn, brons, aluminiumlegeringar och mjukt stål.
6. Slipning och efterbehandling av fräsar
I fabriker utförs skärpning av fräsar vanligtvis på ett centraliserat sätt kl slipmaskiner specialarbetare. Men svarvaren måste själv kunna slipa och avsluta fräsen.
Tabell 2
Egenskaper och syfte för vissa kvaliteter av hårdlegering

Slipning och efterbehandling av höghastighetsskärare utförs i enlighet med följande regler:
1. Slipskivan ska inte träffa, dess yta ska vara jämn; om cirkelns arbetsyta har utvecklats bör den korrigeras.
2. Under skärpningen måste du använda ett handstycke och inte hålla skäraren på vikten. Handstycket bör installeras så nära slipskivan som möjligt, i önskad vinkel och ge ett tillförlitligt stöd till fräsen (fig. 50, a-d).
3. Skäraren som ska slipas måste flyttas längs cirkelns arbetsyta, annars kommer den att slitas ojämnt.
4. För att inte överhetta fräsen och därigenom undvika uppkomsten av sprickor i den, pressa inte skäraren kraftigt mot cirkeln.
5. Slipning måste utföras med kontinuerlig och riklig kylning av fräsen med vatten. Droppkylning, liksom periodisk nedsänkning av en starkt uppvärmd fräs i vatten, är inte tillåtet. Om kontinuerlig kylning inte är möjlig är det bättre att byta till torrslipning.
6. Slipning av fräsar av snabbstål bör göras med elektrokorundhjul med medelhårdhet och kornstorlek 25-16.
Ordningen för skärpning av skär är inställd enligt följande. Först slipas den bakre huvudytan (fig. 50, a). Därefter den bakre hjälpytan (fig. 50, b), sedan den främre ytan (fig. 50, c) och, slutligen, radien på toppen (fig. 50, d).
7. Det är strängt förbjudet att slipa fräsar på maskiner med skyddskåpan borttagen.
8. Var noga med att bära skyddsglasögon vid slipning.
Efter slipning av skäret finns små skåror, grader och risker kvar på skärkanterna. De elimineras genom efterbehandling på speciella efterbehandlingsmaskiner. Efterbehandling utförs också manuellt med en finkornig bryne fuktad med mineralolja. Först, med lätta rörelser av provstenen, justeras de bakre ytorna, och sedan framsidan och radien på toppen.
Slipning och efterbehandling av fräsar utrustade med hårdmetallskär. Slipning av fräsar med plattor av hårda legeringar utförs på slipmaskiner med cirklar av grön kiselkarbid. Slipning utförs både manuellt (fig. 50, a-d), och med fixering av framtänderna i verktygshållarna. Ordningen för skärpning av dessa fräsar är densamma som för fräsar gjorda av höghastighetsstål, d.v.s. först skärs fräsen längs huvudryggen (fig. 50, a), sedan längs de bakre hjälpytorna (fig. 50, b) ), sedan längs den främre ytan (fig. 50, c) och slutligen, runda av toppen av framtanden (fig. 50, d).
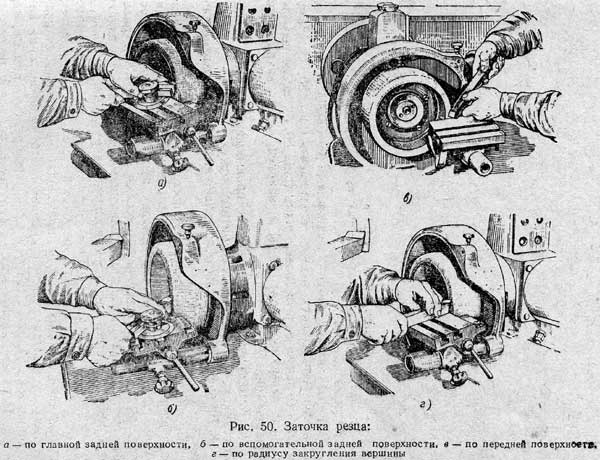
Preliminär skärpning utförs med gröna kiselkarbidhjul med kornstorlek 50-40, och slutslipning med kornstorlek 25-16.
Skäraren bör inte pressas hårt mot cirkelns arbetsyta för att undvika överhettning och sprickbildning av den hårda legeringsplattan. Dessutom måste den ständigt flyttas i förhållande till cirkeln; detta är nödvändigt för jämnt slitage av cirkeln.
Slipning kan utföras både torrt och med riklig kylning av fräsen med vatten.
Efter slipning av en hårdmetallfräs är det absolut nödvändigt att avsluta dess yta. Efterbehandling görs manuellt eller på en efterbearbetningsmaskin. Manuell efterbehandling utförs med en gjutjärns- eller kopparlapp, vars arbetsyta gnids med en speciell pasta eller borkarbidpulver blandat med maskinolja eller fotogen appliceras på ytan i ett jämnt lager. Efterbehandling utförs till en bredd av 2-4 mm från skärkanten.
Mer produktiv efterbehandling på en speciell efterbehandlingsmaskin med en gjutjärnsskiva med en diameter på 250-300 mm, roterande med en hastighet av 1,5-2 m / s; en pasta eller pulver av borkarbid blandat med motorolja eller fotogen appliceras på ytan av denna skiva.
7. Chipbildning
Typer av spån. Det lossnade spånet under verkan av skärets tryck ändrar kraftigt sin form eller, som de säger, deformeras: det förkortas i längd och ökar i tjocklek. Detta fenomen upptäcktes först av Prof. I. A. Tid och namngiven spånkrympning.
Utseendet på flisen beror på metallens mekaniska egenskaper och de förhållanden under vilka skärningen sker. Om viskösa metaller bearbetas (bly, tenn, koppar, mjukt stål, aluminium, etc.), så bildar de individuella elementen i spån, tätt vidhäftande till varandra, ett kontinuerligt spån som krullas till en tejp (fig. 51, en ). En sådan sträng kallas dränera. Vid bearbetning av mindre viskösa metaller, såsom hårt stål, bildas spån av individuella element (fig. 51, b), svagt förbundna med varandra. En sådan sträng kallas flisa chips.
Om metallen som bearbetas är spröd, såsom gjutjärn eller brons, går de enskilda spånelementen sönder och separeras från arbetsstycket och från varandra (fig. 51, c). Ett sådant chip, bestående av individuella vågar oregelbunden form, kallas trasiga chips.
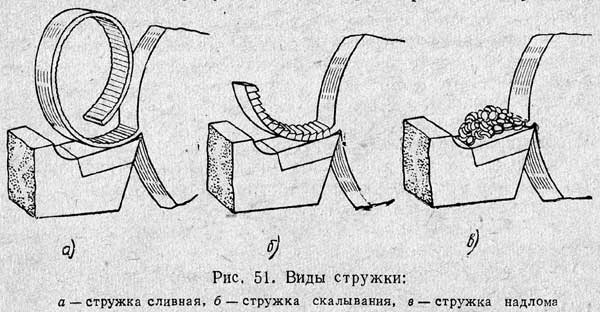
De övervägda typerna av spån förblir inte konstanta, de kan förändras med ändrade skärförhållanden. Ju mjukare metall som bearbetas och ju mindre spåntjocklek och skärvinkel, desto mer närmar sig spånformen avloppet. Detsamma kommer att observeras när skärhastigheten ökas och kylning appliceras. Med en minskning av skärhastigheten erhålls flisflis istället för ett dräneringsspån.
Utväxt. Om du undersöker främre ytan på fräsen som användes för att skära, så kan du vid skäreggen ibland hitta en liten metallklump svetsad till fräsen under hög temperatur och tryck. Detta är den så kallade utväxt(Fig. 52). Det uppträder under vissa skärförhållanden av sega metaller, men observeras inte vid bearbetning av spröda metaller. Hårdheten på uppbyggnaden är 2,5-3 gånger högre än hårdheten hos metallen som bearbetas; tack vare detta har själva tillväxten förmågan att skära metallen från vilken den bildades.
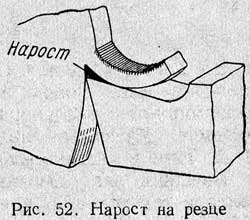
Den positiva rollen med uppbyggnaden är att den täcker skärbladet, skyddar det från slitage av nedåtgående spån och värmepåverkan, och detta ökar skärmaskinens hållbarhet något. Närvaron av en ansamling är användbar vid skalning, eftersom skärbladet värms upp mindre och dess slitage minskar. Men med uppbyggnaden försämras noggrannheten och renheten hos den bearbetade ytan, eftersom uppbyggnaden förvränger bladets form. Därför är bildandet av uppbyggnad ogynnsamt för efterarbete.
8. Konceptet för elementen i skärläget
För att utföra bearbetning mer effektivt i varje enskilt fall måste svarvaren känna till de grundläggande elementen i skärläget; dessa element är skärdjup, matning och skärhastighet.
Skärdjup kallas avståndet mellan de bearbetade och bearbetade ytorna, mätt vinkelrätt mot den senare. Skärdjupet anges med bokstaven t och mäts i millimeter (fig. 53).
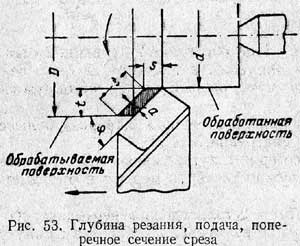
Vid svarvning av ett arbetsstycke på en svarv skärs bearbetningstillägget av i en eller flera omgångar.
För att bestämma skärdjupet t är det nödvändigt att mäta arbetsstyckets diameter före och efter att fräsen passerar, halva skillnaden i diametrar kommer att ge skärdjupet, med andra ord,
där D är delens diameter i mm innan fräsen passerar; d är delens diameter i mm efter att fräsen har passerat. Fräsens rörelse i ett varv av arbetsstycket (bild 53) kallas arkivering. Matningen betecknas med bokstaven s och mäts i millimeter per varv av detaljen; för korthetens skull är det vanligt att skriva mm / varv. Beroende på i vilken riktning fräsen rör sig i förhållande till ramstyrningarna, finns det:
a) längsgående matning- längs sängguiderna;
b) korsmatning- vinkelrätt mot sängguiderna;
i) sned matning- i vinkel mot sängens styrningar (till exempel när du vrider en konisk yta).
Snityta betecknas med bokstaven f (eff) och definieras som produkten av skärdjupet av matningen (se fig. 53):
Förutom skärdjupet och matningen särskiljer de också bredden och tjockleken på skärskiktet (bild 53).
Skärande lagerbredd, eller spånbredd, - avståndet mellan de bearbetade och bearbetade ytorna, mätt längs skärytan. Den mäts i millimeter och betecknas med bokstaven b (be).
Skär tjocklek, eller spåntjocklek, är avståndet mellan två på varandra följande positioner av skäreggen i ett varv av delen, mätt vinkelrätt mot spånbredden. Spåntjocklek mäts i millimeter och betecknas med bokstaven a.
Med samma matning och skärdjup, när huvudvinkeln φ minskar, minskar spåntjockleken och dess bredd ökar. Detta förbättrar värmeavledningen från skäreggen och ökar verktygets livslängd, vilket i sin tur gör att du kan öka skärhastigheten avsevärt och bearbeta fler delar per tidsenhet. En minskning av huvudvinkeln i planen φ leder dock till en ökning av den radiella (repulsiva) kraften, som vid bearbetning av otillräckligt styva delar kan få dem att böjas, förlust av noggrannhet och även starka vibrationer. Uppkomsten av vibrationer leder i sin tur till en försämring av renheten hos den bearbetade ytan och orsakar ofta flisning av skäreggen på fräsen.
Skärhastighet. Vid bearbetning på en svarv går punkt A, som ligger på en cirkel med diameter D (fig. 54), i ett varv av delen en bana lika med längden på denna cirkel.
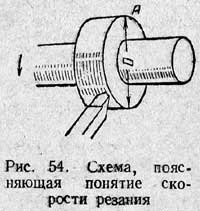
Längden på en cirkel är ungefär 3,14 gånger dess diameter, därför är den lika med 3,14 D.
Siffran 3,14, som visar hur många gånger en cirkels längd är större än dess diameter, betecknas vanligtvis med den grekiska bokstaven π (pi).
Punkt A i ett varv kommer att göra en bana lika med πD. Delens diameter D, såväl som dess omkrets πD, mäts i millimeter.
Antag att arbetsstycket kommer att göra flera varv per minut. Låt oss beteckna deras nummer med bokstaven n varv per minut, eller förkortat som rpm. Den väg som punkt A kommer att ta i detta fall kommer att vara lika med produkten av omkretsen och antalet varv per minut, d.v.s. πDn millimeter per minut eller förkortat mm/min, och kallas omkretshastighet.
Sätt, framkomlig punkt ytan som ska bearbetas vid svarvning i förhållande till fräsen på en minut kallas skärhastighet.
Eftersom detaljens diameter vanligtvis uttrycks i millimeter, för att hitta skärhastigheten i meter per minut, dividera πDn med 1000. Detta kan skrivas som följande formel:
där v är skärhastigheten i m/min;
D är arbetsstyckets diameter i mm;
n är antalet varv per minut.
Exempel 3 Bearbetad valsdiameter D = 100 = 150 rpm. Bestäm skärhastigheten.
Beslut: Spindelhastighetsräkning. Vid svarvning av en del med känd diameter kan det vara nödvändigt för en svarvar att justera maskinen till ett sådant antal spindelvarv för att erhålla erforderlig skärhastighet. För detta används följande formel: där D är arbetsstyckets diameter i mm;
Exempel 4 Vilket antal varv per minut ska en rulle med diametern D \u003d 50 mm ha vid en skärhastighet på v \u003d 25 m / min?
Beslut:
9. Grundläggande information om krafterna som verkar på fräsen och skärkraften
Krafter som verkar på fräsen. När du tar bort spån från arbetsstycket måste skäraren övervinna kraften av vidhäftning av metallpartiklar till varandra. När skäreggen på fräsen skär in i materialet som bearbetas och spånet separeras, utsätts skäret för tryck från metallen som separeras (fig. 55).

Från topp till botten pressar kraften P z på fräsen, som tenderar att pressa fräsen nedåt och böja delen uppåt. Denna kraft kallas skärkraft.
I horisontalplanet i motsatt riktning mot matningsrörelsen, pressas fräsen av kraften P x, kallad axiell kraft, eller matningskraft. Denna kraft under längsgående vändning tenderar att pressa fräsen mot ändstocken.
I horisontalplanet, vinkelrätt mot matningsriktningen, pressas fräsen av kraften P y, som kallas den radiella kraften. Denna kraft tenderar att trycka bort fräsen från arbetsstycket och böja den i horisontell riktning.
Alla angivna krafter mäts i kilogram.
Den största av de tre krafterna är den vertikala skärkraften: den är cirka 4 gånger matningskraften och 2,5 gånger den radiella kraften. Skärkraften belastar delarna av huvudmekanismen; det belastar också skäret, delen, vilket ofta orsakar stora påkänningar i dem.
Experiment har fastställt att skärkraften beror på egenskaperna hos materialet som bearbetas, storleken och formen på den del av spånet som tas bort, formen på skäraren, skärhastighet och kylning.
Att karakterisera motstånd olika material skärning etablerade begreppet skärkoefficient. Skärfaktorn K är skärtrycket i kilogram per kvadratmillimeter av skärsektionen, mätt under vissa skärförhållanden:
Skärdjup t......................5 mm
Matning s......................1 mm/varv
Kraftvinkel γ......................15°
Ledningsvinkel φ.......45°
Skärkanten på fräsen - rätlinjig, horisontell
Skärets spets är avrundad med en radie r = 1 mm
Arbetet utförs utan kylning
I tabell. 3 visar medelvärdena för skärfaktorn för vissa metaller.
Tabell 3
Medelvärden för skärfaktorn K vid vändning
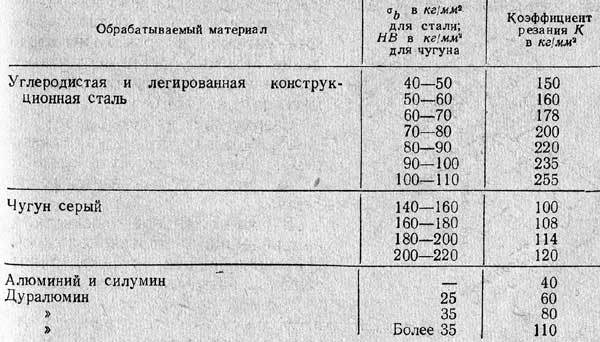
Om skärfaktorn K är känd kan du genom att multiplicera den med tvärsnittsarean för skärningen f i mm 2 hitta det ungefärliga värdet på skärkraften med hjälp av formeln
P z \u003d Kf kg. (åtta)
Exempel 5 En axel av maskintillverkat stål med σ b = 60 kg / mm 2 vrids på en svarv. Bestäm skärkraften om skärdjupet t = 5 mm och matningen s = 0,5 mm/varv.
Beslut. Enligt formel (8), skärkraft P z \u003d Kf kg. (åtta) Vi bestämmer värdet på f: f \u003d ts \u003d 5x0,5 \u003d 2,5 mm 2. Enligt tabellen 3 hittar vi värdet på K för maskintillverkat stål med σ b \u003d 60 kg / mm 2: K \u003d 160 kg / mm 2. Därför är z = Kf = 160x2,5 = 400 kg. skärkraft. Genom att känna till skärkraften och skärhastigheten kan du ta reda på hur mycket kraft som krävs för att skära spån av en viss sektion.
Skärkraften bestäms av formeln (9) där N res - skäreffekt i hk;
P z - skärkraft i kg;
v - skärhastighet i m/min.
Kraften hos verktygsmaskinens elmotor bör vara något större än skärkraften, eftersom en del av kraften hos elmotorn går åt till att övervinna friktion i mekanismerna som överför rörelse från elmotorn till maskinspindeln.
Exempel 6 Bestäm skärkraften för att vrida axeln, betraktad i föregående exempel, om bearbetningen utförs med en skärhastighet, υ = 60 m/min. Beslut . Enligt formel (9), skärkraft
Skärkraft uttrycks vanligtvis inte i hästkrafter, utan i kilowatt (kW). En kilowatt är 1,36 gånger hästkrafter, så för att uttrycka effekt i kilowatt måste du dividera hästkrafter med 1,36:
och vice versa,
10. Skärvärme och livslängd
Med en ökning av skärkraften ökar friktionskraften, vilket gör att mängden värme som frigörs under skärprocessen ökar. Skärvärmen ökar ännu mer när skärhastigheten ökar, eftersom detta påskyndar hela processen med spånbildning.
Den genererade skärvärmen med otillräcklig borttagning av den mjukar upp skäraren, vilket resulterar i att slitaget på dess skärande del sker mer intensivt. Detta gör det nödvändigt att byta eller vässa den och installera om den.
Tiden för skärarens kontinuerliga arbete före trubbning kallas verktygets livslängd (mätt i minuter). Orsaker till frekvent byte av fräs (kort livslängd). ytterligare utgifter för slipning och montering av fräsen, samt för att fylla på slitna fräsar.
Därför är verktygets livslängd en viktig faktor vid val av skärförhållanden, speciellt vid val av skärhastighet.
Skärarens hållbarhet beror främst på egenskaperna hos materialet som den är gjord av. Den mest motståndskraftiga kommer att vara skäraren, som är gjord av ett material som tillåter den högsta uppvärmningstemperaturen utan betydande förlust av hårdhet. Skärarna utrustade med hårdlegeringsplåtar, mineralkeramiska plåtar har störst motstånd; betydligt mindre motstånd - fräsar gjorda av höghastighetsstål, de minsta - fräsar gjorda av kolverktygsstål.
Skärarens motstånd beror också på egenskaperna hos materialet som bearbetas, skärsektionen, skärningsvinklarna och skärhastigheten. Att öka hårdheten på materialet som bearbetas minskar verktygets livslängd.
Genom att ändra skärpningsvinklarna och formen på den främre ytan är det möjligt att uppnå en betydande ökning av skärarnas hållbarhet och deras produktivitet.
Skärhastigheten har en särskilt stark effekt på verktygets livslängd. Ibland leder till och med den minsta hastighetsökningen till snabb avtrubbning av fräsen. Till exempel, om, vid bearbetning av stål med en höghastighetsfräs, skärhastigheten ökas med endast 10%, dvs. 1,1 gånger, kommer fräsen att bli matt dubbelt så snabbt och vice versa.
Med en ökning av skärets tvärsnittsarea minskar verktygslivslängden, men inte lika mycket som med samma ökning av skärhastigheten.
Verktygets livslängd beror också på verktygets storlek, formen på den skurna delen och kylning. Ju mer massiv skärmaskinen är, desto bättre tar den bort värme från skäreggen och, följaktligen, desto längre hållbarhet.
Experiment visar att med samma skärsektion ger ett stort skärdjup och en mindre matning längre verktygslivslängd än ett mindre skärdjup med en motsvarande större matning. Detta förklaras av det faktum att med ett större skärdjup kommer spånen i kontakt med en större längd av skäreggen, så att skärvärmen tas bort bättre. Därför är det mer lönsamt att arbeta med ett större djup med samma kapade sektion än med en större matning.
Skärarens hållbarhet ökar avsevärt när den kyls.
Kylvätska måste tillföras rikligt (emulsion 10-12 l/min, olja och sulfofresol 3-4 l/min); en liten mängd vätska gynnar inte bara, utan förstör till och med fräsen, vilket gör att små sprickor uppstår på ytan, vilket leder till flisning.
11. Val av skärhastighet
Arbetsproduktiviteten beror på valet av skärhastighet: ju högre skärhastighet, desto mindre tid spenderas på bearbetning. Men när skärhastigheten ökar minskar verktygslivslängden, så valet av skärhastighet påverkas av verktygets livslängd och alla faktorer som påverkar verktygets livslängd. Av dessa är de viktigaste egenskaperna hos materialet som bearbetas, kvaliteten på materialet i fräsen, skärdjupet, matningen, skärens dimensioner och skärpningsvinklar samt kylning.
1. Ju längre verktygslivslängden ska vara, desto lägre ska skärhastigheten väljas och vice versa.
2. Ju hårdare material som bearbetas, desto kortare livslängd, för att säkerställa det nödvändiga motståndet vid bearbetning av hårda material måste skärhastigheten minskas. Vid bearbetning av gjutna och smidda arbetsstycken, på vars yta det finns en hård skorpa, skal eller fjäll, är det nödvändigt att minska skärhastigheten mot vad som är möjligt vid bearbetning av material utan skorpa.
3. Materialegenskaperna hos skäraren bestämmer dess hållbarhet, därför beror valet av skärhastighet också på dessa egenskaper. Allt annat lika tillåter höghastighetstålskärare en betydligt högre skärhastighet än kolstålskärare; ännu högre skärhastigheter tillåter fräsar utrustade med hårda legeringar.
4. För att öka skärets motstånd vid bearbetning av trögflytande metaller är det fördelaktigt att använda kylning av fräsen. I det här fallet, med samma livslängd, är det möjligt att öka skärhastigheten med 15-25% jämfört med bearbetning utan kylning.
5. Skärmaskinens dimensioner och vinklarna på dess skärpning påverkar också den tillåtna skärhastigheten: ju mer massiv skäraren, speciellt dess huvud, desto bättre tar den bort värmen som genereras under skärningen. Felaktigt valda fräsvinklar som inte motsvarar materialet som bearbetas ökar skärkraften och bidrar till snabbare slitage på fräsen.
6. Med en ökning av skärsektionen minskar verktygslivslängden, därför är det med en större sektion nödvändigt att välja en skärhastighet som är lägre än med en mindre sektion.
Eftersom små spån avlägsnas under finbearbetningen kan skärhastigheten vid finbearbetning vara mycket högre än vid grovbearbetning.
Eftersom en ökning av skärsektionen har mindre effekt på verktygslivslängden än en ökning av skärhastigheten, är det fördelaktigt att öka skärsektionen på grund av en lätt minskning av skärhastigheten. Bearbetningsmetoden för innovatörsvarvaren i Kuibyshev Machine Tool Plant V. Kolesov är baserad på denna princip. T. Kolesov arbetar med en skärhastighet på 150 m/min och bearbetar ståldetaljer med en matningshastighet på upp till 3 mm/varv istället för 0,3 mm/varv, och detta leder till en minskning av maskintiden med 8-10 gånger.
Frågan uppstår: varför ökar avancerade svarvare ofta arbetsproduktiviteten genom att öka skärhastigheten? Motsäger inte detta de grundläggande lagarna för skärning? Nej, det motsäger inte. De ökar skärhastigheten endast i de fall där möjligheterna att öka snittet utnyttjas fullt ut.
När halvbearbetning eller efterbearbetning utförs, där skärdjupet begränsas av ett litet tillstånd för bearbetning, och matningen begränsas av kraven på hög renhet av bearbetning, är en ökning av skärläget möjlig genom att öka skärhastigheten . Detta är vad avancerade svarvare gör, som arbetar med halvfinish och finish. Om det går att jobba med stora sektioner skära (med stora mängder), då är det först och främst nödvändigt att välja största möjliga skärdjup, sedan största möjliga tekniskt tillåtna matning och slutligen motsvarande skärhastighet.
I de fall bearbetningstillägget är litet och det inte finns några särskilda krav på ytfinish, bör skärläget ökas genom att använda största möjliga matning.
12. Renlighet av den bearbetade ytan
Vid bearbetning med en fräs kvarstår alltid ojämnheter i form av fördjupningar och pilgrimsmusslor på delens bearbetade yta, även med den mest noggranna efterbehandlingen. Höjden på grovheten beror på bearbetningsmetoden.
Praxis har fastställt att ju renare ytan på delen behandlas, desto mindre utsätts den för slitage och korrosion, och delen är starkare.
Noggrann ytbehandling vid bearbetning av en detalj är alltid dyrare än en grov ytfinish. Därför bör renheten hos den bearbetade ytan tilldelas beroende på delens driftsförhållanden.
Beteckning på ytrenhet i ritningar. Enligt GOST 2789-59 tillhandahålls 14 klasser av ytrenhet. För att beteckna alla renhetsklasser upprättas ett tecken - en liksidig triangel, bredvid vilken klassnumret anges (till exempel 7; 8; 14). De renaste ytorna är graderade 14 och de grovaste klasserna 1.
Ytgrovheten enligt GOST 2789-59 bestäms av en av två parametrar: a) den aritmetiska medelavvikelsen för profilen Ra och b) höjden på oregelbundenheterna Rz .
För att mäta grovheten och tilldela den behandlade ytan till en viss klass, special mätinstrument baserad på metoden att känna av ytprofilen med en tunn diamantnål. Sådana enheter kallas profilometrar och profilografer.
För att bestämma grovheten och klassificera den behandlade ytan till en eller annan klass av renlighet i verkstadsförhållanden, används testade prover av olika klasser av renhet - de så kallade renhetsstandarderna, med vilka den bearbetade ytan på delen jämförs.
Faktorer som påverkar ytfinish. Det har fastställts genom praxis att renheten hos den bearbetade ytan beror på ett antal skäl: materialet som bearbetas, materialet i fräsen, skärpningsvinklarna och tillståndet hos skäreggarna på fräsen, matningen och skärhastigheten , vätskans smörjande och kylande egenskaper, styvheten hos systemets maskin - fräs - del, etc.
Framförallt betydelse för att få en yta Hög kvalitet vid svarvning har den skärhastighet, matning, ledningsvinklar och en krökningsradie för verktygsspetsen. Ju mindre matnings- och ingångsvinkel och ju större hörnradie, desto renare är den bearbetade ytan. Skärhastigheten påverkar ytfinheten i hög grad. Vid svarvning av stål med en skärhastighet på mer än 100 m/min är den bearbetade ytan renare än vid en hastighet på 25-30 m/min.
För att få en renare bearbetad yta bör man vara noggrann med skärpning och efterbehandling av skäreggarna.
testfrågor 1. Vilken form bildas spånet vid bearbetning av viskösa metaller? Vid bearbetning av spröda metaller?
2. Namnge huvudelementen i framtandens huvud.
3. Visa fram- och bakytorna på framtanden; främre och bakre hörn; skärpningsvinkel.
4. Vad är syftet med framtandens främre och bakre hörn?
5. Visa ledningsvinklar och ledningsvinkel.
6. Vilka material är fräsar gjorda av?
7. Vilka kvaliteter av hårda legeringar används vid stålbearbetning? Vid bearbetning av gjutjärn?
8. Lista skärlägeselementen.
9. Vilka krafter verkar på fräsen?
10. Vilka faktorer och hur påverkar de storleken på skärkraften?
11. Vad avgör skärmaskinens hållbarhet?
12. Vilka faktorer påverkar valet av skärhastighet?
De viktigaste skärverktygen som används i processen inkluderar en fräs, vars geometriska parametrar bestämmer dess tekniska kapacitet, noggrannhet och bearbetningseffektivitet. Varje specialist som bestämmer sig för att ägna sig åt svarvning, i den mån rätt val skäreggsvinklar ökar både verktygets livslängd och produktivitet.
Parametrar för svarvverktyg
Några svarvverktyg bilda en hållare som behövs för att fixera verktyget i hållaren svarv, och ett arbetshuvud som ger metallskärning. För att beakta de geometriska parametrarna för ett svarvverktyg är det bättre att ta ett genomgående verktyg som ett prov.
På den skärande delen av svarvverktyget av denna typ det finns tre ytor:
- framsidan (på den under bearbetningen av arbetsstycket kommer metallspån av);
- bak - huvud och hjälp (båda vända med sin främre del mot arbetsstycket).
Kanten på verktyget, kallad skäreggen (och direkt involverad i bearbetningen), bildas av skärningspunkten mellan dess främre och bakre huvudytor. I svarvverktygets geometri urskiljs också en extra skäregg. Den bildas av korsningen mellan den främre ytan och den extra baksidan.
Den punkt där huvud- och sekundärskäreggarna skär varandra kallas spetsen på fräsen. Den senare, när den skär metall, upplever enorma belastningar, vilket leder till att den går sönder. För att öka motståndet hos skärets spets skärs den inte under skärpningsprocessen, utan är något rundad. Detta kräver införandet av en parameter såsom vertexradien. Det finns ett annat sätt att öka motståndet hos spetsen på ett svarvverktyg - bildandet av en övergångsskäregg som har en rätlinjig form.
De viktigaste geometriska parametrarna för fräsar för svarvning är deras vinklar, som bestämmer ömsesidigt arrangemang verktygsytor. Vinkelparametrarna varierar beroende på typ av svarvverktyg och på ett antal andra faktorer:
- verktygsmaterial;
- hans arbetsvillkor;
- egenskaper hos det material som ska bearbetas.
Verktygsvinklar för svarvning
För att korrekt bestämma vinklarna svarvverktyg, dem exakta värden, betraktas de i de så kallade initiala planen.
- Huvudplanet är parallellt med svarvverktygets matningsriktningar (längsgående och tvärgående) och sammanfaller med dess stödyta.
- Skärplanet inkluderar huvudskäreggen och är tangentiellt mot bearbetningsytan. Detta plan är vinkelrät mot huvudplanet.
- Huvudskärplanet skär huvudskäreggen och är placerat vinkelrätt mot den projektion som denna egg lägger på huvudplanet. Det finns också ett hjälpplan av sekanttyp, som följaktligen är vinkelrät mot utsprånget som avsätts på huvudplanet av hjälpskäreggen.
Som nämnts ovan mäts de exakt i dessa plan, och de som mäts i ett plan som kallas huvudsekanten betecknas som de huvudsakliga. Dessa är i synnerhet de huvudsakliga främre, huvudsakliga bakre vinklarna, såväl som vinklarna för skärpning och skärning.
En av de viktigaste är den huvudsakliga frigångsvinkeln för svarvverktyget, som minimerar friktionen som uppstår när verktygets baksida samverkar med den del som för närvarande bearbetas (och därför minskar uppvärmningen av verktyget och förlänger dess livslängd ). Denna vinkel bildas av skärytan (huvudbaksidan) och skärplanet. När man väljer denna vinkel när man skärper ett verktyg, beaktas typen av bearbetning och arbetsstyckets material. I det här fallet bör du vara medveten om att en kraftig ökning av storleken på släppningsvinkeln leder till ett snabbt fel på svarvverktyget.
Styrkan och hållbarheten hos skärverktyget, krafterna som uppstår under bearbetningen, bestäms av parametrarna för spånvinkeln. Den är placerad mellan den främre ytan av svarvverktyget och det plan där huvudskäreggen är placerad (detta plan är vinkelrät mot skärplanet). Vid slipning av ett svarvverktyg tas ett antal faktorer i beaktande som påverkar värdet på denna vinkel:
- arbetsstyckets material och själva verktyget;
- formen på den främre ytan;
- förhållanden under vilka fräsen kommer att användas.
En ökning av spånvinkelns värde förbättrar å ena sidan finishen av bearbetningen, och å andra sidan provocerar det en minskning av styrkan och hållbarheten hos svarvverktyget. En sådan vinkel, erhållen som ett resultat av skärpning, kan ha en positiv och negativ betydelse.
Svarvfräsar med spånvinklar som har negativa värden är mycket hållbara, men bearbetning med sådana verktyg är svårt. Vanligtvis används slipning med spånvinkel, som har ett positivt värde, när arbetsstycket ska bearbetas av ett trögflytande material, och även när verktygsmaterialet är mycket hållbart.
Fräsar med negativa spånvinklar används vid bearbetning av material med hög hårdhet och styrka, vid avbruten skärning, när verktygsmaterialet inte har tillräcklig böjhållfasthet och inte absorberar stötbelastningar väl.
Parametrarna som kännetecknar skärarens geometri för svarvning är också skär- och pekvinklar. Skärvinkeln, vars värde kan variera inom 60–100 0, är placerad mellan verktygets yta, kallad fronten, och skärplanet.
Värdet på denna vinkel beror direkt på hårdheten hos metallen som bearbetas: ju högre den är, desto större är dess värde. Avsmalningsvinkeln överensstämmer helt med dess namn, den mäts mellan verktygets främre och bakre huvudytor och kännetecknar graden av skärpning av dess topp.
Karaktärisera svarvverktyget och vinklarna i planen. Detta är den huvudsakliga, mätt mellan riktningen för den längsgående matningen och den projektion som huvudskäreggen ligger på huvudplanet, och den extra, som bildas av projiceringen av den extra skäreggen på huvudplanet och riktningen för den längsgående matningen.
Vid skärpning väljs dessa vinklar inte godtyckligt, utan beroende på typen av svarvning och den styvhet som systemet "verktygsmaskin-arbetsstycke" har. Så bearbetningen av de flesta metaller kan utföras med verktyg med en huvudvinkel i planen lika med 45 0, men tunna och långa arbetsstycken bör bearbetas med fräsar, där värdet på denna vinkel är i intervallet 60– 90 0 . Detta är nödvändigt för att eliminera avböjning och darrning av delen.
Hjälpvinkeln i ledningen korrelerar samtidigt med finishen på bearbetningen och med verktygets livslängd. Med dess minskning ökar renheten i bearbetningen och livslängden ökar.
Utöver de som diskuterats ovan, i geometrin hos svarvverktyg, särskiljs vinklar.
Längsgående svarvning kallas svarvning, där matningens rörelseriktning är parallell med arbetsstyckets axel. På svarvar är skärrörelsen - rotation - fäst vid arbetsstycket och matningsrörelsen - translationsrörelse - till fräsen. På rundstavsmaskiner roterar skärverktyget och matningsrörelsen fästs på arbetsstycket. Den verkliga skärbanan är en spirallinje.
Skilj på fin- och grovsvarvning.
Finsvarvning (fig. 2, a) utförs med en fräs med plana arbetsytor och raka skäreggar - huvud- och extra. Skäreggarnas läge i förhållande till arbetsstyckets rotationsaxel kännetecknas av huvudvinkeln i ledningen och hjälpvinkeln i ledningen. Värdet på hjälpvinkeln i planen bestämmer djupet på de kinematiska oregelbundenheterna, så det kan inte vara större. Placeringen av ytorna som bildar huvudskäreggen kännetecknas av släppningsvinkeln, skärpningsvinkeln och spånvinkeln.
Huvudskäreggen producerar tvärskärning, kännetecknad av träfibrernas lutningsvinkel.
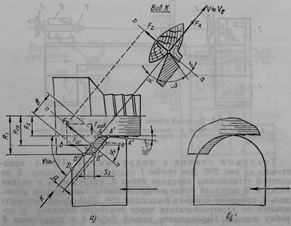
Ris. 2. Längssvarvning (a) och grovbearbetning (b)
Lutningsvinkeln mäts mellan fibrernas riktning och normalen.
Grovsvarvning (fig. 2, b) utförs med räfflade fräsar med en halvcirkelformad skäregg. Tvärsnitt spånen är halvmåneformade, tjockleken på spånen på arbetsstyckets periferi är maximal, och nära delens yta är den obetydlig även vid hög matning till skäraren. Detta gör att du kan applicera matningen per fräs upp till 2 mm, medan för finsvarvning - inte mer än 0,8 mm.
> Uppsättning av svarvar
Vid inställning av svarvar är det nödvändigt att: välja en fräs och fixera den i verktygshållaren (för maskiner med mekanisk matning); installera en frontplatta eller chuck; välj och fixera handstödet (för maskiner med manuell inmatning) eller en kopieringslinjal (för maskiner med mekanisk matning); installera och fixa arbetsstycket i maskinen; testa maskinen på tomgång; ställ in spindelhastigheten och matningshastigheten; bearbeta och inspektera provbitar.
Den nödvändiga skäraren väljs beroende på arten av det utförda arbetet. För den initiala grovbearbetningen används en skalfräs, för den sista en finbearbetning med rak skäregg. Med mekanisk matning fixeras fräsen i verktygshållaren med skruvar. För att minska omställningstiden används speciella roterande huvuden, där flera framtänder för olika ändamål samtidigt förstärks.
På manuellt arbete det är nödvändigt att kontrollera tillförlitligheten av att fästa skäraren på trähandtaget. Använd inte ett defekt skärverktyg.
Medlen för att fästa arbetsstycket väljs beroende på dess form och storlek. För fastsättning av långa arbetsstycken (fig. 3, a) används främre och bakre mittpunkter. Den främre mitten 2 är gjord i form av ett tredelat koppel med ett avsmalnande skaft, med vilket det förs in i det avsmalnande hålet på spindeln 1. Den bakre mitten 4 har en konisk och spetsig del och är fixerad i fjäderpennan. 5 av ändstocken 6. För att minska friktionen och öka tillförlitligheten av att fästa arbetsstycket, är den bakre mitten monterad på ett lager, vilket säkerställer dess rotation med arbetsstycket 3.

Ris. 3. Fastsättning av arbetsstycket i svarvar: a - i mitten, b - i chucken, c - på frontplattan; 1 - spindel, 2 - främre mitten, 3 - arbetsstycke, 4 - bakre mitten, 5 - fjäderpinne, 6 - bakaxel, 7 - chuck, 8 - plan
Beroende på längden på arbetsstycket som bearbetas, flyttas ändstocken längs bäddens styrningar och fixeras i ett förutbestämt läge. Arbetsstycket fixeras genom att trycka ut pennan ur huvudstocken tills mitten är inbäddade i ändarna av arbetsstycket och kommer att hålla fast det säkert under rotation. För att vrida koniska delar ska bakkroppen flyttas på tvären med en justerskruv och fixeras med en låsanordning. Chuckar är utformade för att fästa korta arbetsstycken (fig. 3, b). Chuck 7 har en gänga genom vilken den skruvas på spindeln. Arbetsstycket fixeras i chucken genom att dess ände fästs ordentligt i chuckhålet. Spännhylsor och chuckar med glidbackar används också.
För fastspänning av arbetsstycken med kort längd och stor diameter tjäna som frontplattor 8 (fig. 3, c), skruvas på spindeln. Arbetsstycket fästs på frontplattan med skruvar eller bultar 9.
Handstycket är installerat på ramen så att dess arbetskant är i nivå med mitten och är nära generatrisen för arbetsstycket som bearbetas, men inte rör det. När diametern minskar och vid bearbetning av långa arbetsstycken, omarrangeras handstycket sekventiellt till en ny position längs bäddstyrningarna. Vid bearbetning av formade produkter på baksidan av sängen fästs en kopieringslinjal på fästena, vars form liknar formen på den färdiga delen. När matningen är påslagen rör sig bromsoket längs en krökt bana och fräsen återger delens givna form.
Spindelhastigheten väljs beroende på arbetsstyckets diameter och dess styrka. För större diametrar bör minsta spindelhastighet ställas in. Vid montering av en frontplatta med en diameter på 400 mm bör spindelhastigheten inte överstiga 800 rpm. Rotationshastigheten minskas med växelspaken eller genom att ändra rotationshastigheten för den flerväxlade elmotorn. skärhastighet för trä mjuka stenar bör vara 10 ... 12 m / s, fast - 0,5 ... 3 m / s.
Längsmatning per ett varv av spindeln bör vara: för grovbearbetning 1,6 ... 2 mm, för efterbearbetning - inte mer än 0,8 mm. Ju högre krav på ytjämnhet är, desto lägre bör den längsgående matningen vara. Korsmatning per spindelvarv bör inte överstiga 1,2 mm. Innan du startar maskinen, se till att pålitlig infästningämnen och installera ett staket.
Efter grovbearbetning av delen byts fräsen och finsvarvning utförs vid låg matning. Spånen i detta fall bör vara så kontinuerliga som möjligt och av enhetlig tjocklek.
Under bearbetningen kontrolleras delens form periodiskt av en mall eller mätare. När du använder en kaliber eller mätinstrument med en våg stängs maskinen av och först efter att delen har stannat helt mäts den.
Efter att ha avslutat justeringen utförs en provbearbetning av delen och dess dimensioner kontrolleras med en kaliber eller ett mätverktyg med en skala.