Measuring tool for wood turning. Wood cutters
Currently, it is not difficult to buy turning tools for woodworking, but it is quite easy to make them yourself at little cost, and also adapt them to your own needs.
We offer you one of the options for manufacturing cutters for lathe with your own hands. To do this, it is necessary to select rasps and files of a suitable configuration, both for metal and for wood. Rasps can be used worn and old, which are no longer even suitable for their initial use, but they are quite suitable for making turning tools.
They need to be sharpened so as to get not very sharp corners. Most often they are sharpened at an angle of 50-60 degrees. Only an oblique flat cutter is sharpened differently: first you need to cut and make a bevel at a 40-degree angle, and then sharpen this bevel at the same angle on both sides.
We make six types of homemade turning tools for wood
1. Cut-off cutter, which is sharpened on both sides. Most often it is used for the initial alignment of the workpiece and rough removal.
2. The through cutter is semicircular. Such a cutter may be needed when there is a need to walk after the completion of rough processing, and also when it is necessary to make a semicircular recess, in the manufacture, for example, of the bottom of a salt shaker.
3. Flat cutter oblique. With it, you can round the edges, as well as trim the end or base of the part.
4. Straight cutter is flat.
5. There are also analogues of flat straight cutter, which are used most often in small details, where there is a need to earn them a little from the end.
6. Small turning tool semicircular. It is used quite rarely and mainly in order to make small figured parts.
The general classification of devices available today for working with wooden surfaces combines them into common group which are called incisors. This list includes cutting blades, saws, axes, chisels, special planers and other tools. main feature any tool from this list is to perform a specific type of wood processing.
Wood lathe cutters
Turning cutters for wood are necessary for the manual processing of a part that rotates in the machine. Such wood cutters consist of two main parts: a working (metal) and a handle (most often made of wood).
In the working part there are:
- cutting edge or blade. This is the part to be sharpened, it is she who interacts with the workpiece
- the body is the main part for which the turner holds the cutter with his “non-working” hand on the armrest of the machine
- the shank is the narrow part into which the body smoothly passes. A handle is attached to the shank.
The handle consists of two parts:
- the base, which is a large part that the master holds in the "working" hand
- the neck, which is a small cylindrical part with a metal fastening ring that prevents the handle from cracking when it is stuffed onto the shank of the working part.
Depending on the type of processing, turning tools come in different configurations. Note that with an increase in the complexity of the work, their design becomes more complicated, which also determines the specific sharpening of the blade. For a young master, two types of incisors are enough: reyer and meisel.
These two tools will help to carry out turning work of an average level of complexity. Basically, the processing of the outer surface is carried out. In some cases, you can work with internal surfaces products.
What other wood turning tools are there? The video below demonstrates the work various kinds turning cutters.
Work on a lathe
Today, wood lathes are often used to produce multifunctional furniture parts. In addition, this machine will help you create attractive and unusual decorative elements, for example, candlesticks, cups, toys, spinning tops and more.
Lathes are different sizes. First of all, you need to choose the most suitable machine. To date, there is a fairly wide range of desktop lathes, ideal for small project. Larger devices are used to create balusters, which are used to make furniture and railings.
Parameters by which lathes differ:
- bed length. It determines the maximum length of the processed bar
- turning diameter over bed is the maximum bar diameter
- horsepower - the power of the power unit, which determines the mass of the bar for turning without load on the cutter and machine
- engine revolutions per minute. Most machines have a constant speed. Devices with low speed mode can be used for workpiece processing irregular shape. And higher speeds help to polish the product.
When buying, pay attention to the weight and material from which the machine is made. Options with a cast-iron bed and a steel frame are quite durable, but not mobile. They cannot be transferred to another place of work.
Turning cutters are characterized by a long curved handle. It is designed to make it convenient for the master to hold the tool. As a result of the presence of such a handle, the master accurately controls the blade, but at the same time does not feel fatigue. Hand cutters are not suitable for machine work because they have a short handle.
Work with wood cutters
Woodcarving is a complex, but rather interesting technique for decorating products, which has been known since ancient times. At the beginning of work, it is necessary to create blanks, in other words, decks or blanks. After that, a rough surface treatment is carried out, during which the surface is leveled and all kinds of defects are eliminated.
After that, you can start artistic work, which is carried out using cutters for woodcarving. In fact, this is a selection of a piece of wood, which allows you to give the workpiece a relief and volume. it main stage because it depends appearance subject. Finishing decorative item consists in grinding the timber and impregnating it with antiseptic agents and paint and varnish coatings.
For implementation self made of this type, cutting devices having a different blade configuration are used. Their quality has a direct impact on the purity of the ornament, for this reason it is necessary to carefully monitor that the blade of the chisel is sharp and without notches.
Wood carving chisels are an indispensable tool in the arsenal of a craftsman who is engaged in the manufacture of decorative items from wood. These tools are various types and shapes, which affects the specifics of the processing of some parts.
Some believe that virtuoso masters work with one or two cutters, but in practice it turns out that only a complete set of special carpentry tools, which should contain chisels with blades of various shapes, will help to achieve the best result and ensure easy work.
Wood cutting tools include:
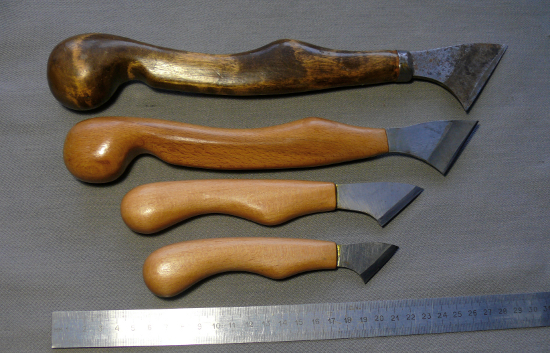
Sharpening wood cutters
in the process of wood processing, the used cutters and chisels remove the layer of wood. After some time, the tool becomes dull, which affects the quality of processing. For this reason, tool sharpening is a very important issue.
There are two ways to sharpen a tool:
- manual method. In this case, the mechanization of the process is completely absent, that is, everything is done manually from beginning to end. This method is characterized by low productivity. In addition, it is quite difficult to achieve the desired result.
- mechanical sharpening using special machines that have a stone for removing metal.
Both of these methods are used in production. Using the manual method, you can sharpen the tool in a short time. If the cutting edge is slightly worn and there are no mechanical damages. A special machine makes it possible to restore the cutting surface, to eliminate various defects.
The most popular sharpening machines are:
- a device with two grindstones. It allows you to install two different abrasives in order to speed up the processing procedure. To avoid the need to frequently rearrange the abrasive, these machines are equipped with two output shafts on which the wheel is mounted.
- device with a bath for cooling the surface of the abrasive. Such a system prevents the tool from burning metal during processing. Due to strong friction, the surface is very hot, the metal during heating can change its performance. Metal burning should be avoided by using a cooling bath of water.
Each master who works with wood has carpentry chisels in his arsenal. A wood chisel is very useful in works that are associated with the processing of wooden blanks. Perfectly sharpened blade various shapes apply implementation for carving of any complexity. AT construction stores you can buy both ready-made sets of devices, and chisels by the piece.
August 14Wood turning cutters are a tool designed for processing wooden parts using a special machine. The lathe that is used in this case is designed to obtain bodies of revolution.
What are cutters for?
Wooden blocks or blocks, which are initially rounded or close to rounded, are installed on such a machine using two clamps. One of the clamps, as a rule, is connected to an electric motor, which brings the part into a state of rotation, while the fixation on one side can only be axial, and on the motor side, the fixation is rigid so that rotation does not occur at idle.
The incisors, which are fixed on a special guide mechanism or held in the hand, process the rotation body itself and, depending on the shape of the incisor, its strength and sharpness, which traces remain on wood detail, and what form it will receive as a result of processing.
The most common standard part made from wood using a lathe is familiar things, such as an ordinary candlestick or a baseball bat. For their manufacture, not only incisors are used, but also other tools.
The use of a variety of cutters allows you to get more complex parts and thinner ones, so the number of possible forms of cutters for wood for a lathe is very large.
But when working with cutters, there are several problems that almost all turners have to solve:
- Firstly, the cutters are quite expensive, so if they break, then you need to be able to make them yourself. This also applies to situations where the tool needs to be obtained urgently.
- Secondly, incisors quickly become dull if they are used frequently. Therefore, they need to be sharpened correctly, because with the wrong approach to turning, you can disfigure the tool and be left with nothing.
DIY turning tools
Homemade cutters for a wood lathe can be obtained by having a certain set of tools at hand, as well as the source material or the original old tool. In both cases, they will have to be specially processed.
You can make a new turning tool from a rasp or file. One method also allows the use of reinforced steel, the rods of which also make good cutters. In this case, the shape of the rods must be taken into account. Another well-known homemade way to quickly create a woodworking tool in expert circles is to use an old car spring.
Each of these types of raw material must be processed differently in order to obtain a sufficiently high-quality tool for a lathe, but after that it is practically indistinguishable in functionality from the factory one.
Before you make a turning tool from improvised means, you should make sure that they do not have cracks, and that there are no chips on them. When processing reinforcement, it chooses the one that has square section rods.
The most difficult to process in this case is the automobile spring, which is treated with autogenous or welding before making a tool from it. Thus, the spring is given correct form- a rectangular body.
After the workpiece is received, it can already be sharpened for the first time. Sharpening methods are described below.
After sharpening, hardening follows cutting edge. It is heated to a state of incandescence, after which it is quickly cooled in engine oil. Also, sometimes they resort to the slow hardening technique, when the workpiece is allowed to cool without resorting to emergency cooling - it cools by itself to normal temperature.
Finished homemade cutters should be tested using in processing soft rocks tree. If they do not deviate from the guide mechanism clamps and do not vibrate in the hands during operation, and are also rigidly mounted on a lathe and retain their original shape, then they can be sharpened and used for hardwood and other more complex or precise work.
How to sharpen cutters for a lathe
Sharpening of turning tools on wood can be carried out both before hardening and after. If a we are talking about homemade cutters, they are pre-sharpened before hardening.
In the course of periodic work with cutters, it is also necessary to resort to sharpening. The fact is that in the process of processing wood, both factory and home-made wood cutters will certainly become dull. Thus, in order to keep them in a normal state of readiness for work, they should be constantly sharpened.
For primary sharpening homemade tool with your own hands, before hardening it, you can use a regular abrasive wheel. Sufficiently soft and malleable metal is processed easily and acquires any desired shape. After hardening, as well as when sharpening dull factory cutters, grinding skins should be used.
If the incisors are not only dull, but chips or irregularities have also formed on them, then the defects are removed with a corundum circle. At the same time, home-made tools are recommended to be processed with little effort, since hardened tools are characterized by the formation of chips during sharpening.
Professional turners who deal with homemade cutters for turning wood work recommend using a trick that many of them have tested in practice: when making a cutter, it’s worth making several copies of the same type - this allows you not only to always have at hand the right tools, but also solves the problem of waste in the manufacture of tools from improvised materials.
You can give the desired decoration to wooden cylindrical products using such a special hand tool, like a cutter for a wood lathe. To the attention of those who love to craft, a wide range of these cutting attachments. Anyone can purchase the turning chisel he needs.
However similar products expensive, and most craftsmen prefer to work with homemade cutters for a wood lathe. What is a tool? How to use it correctly? Can it be made at home? The answers to these questions are contained in the article.
Acquaintance
The cutter for a wood lathe is a special cutting tool, with the help of which the controlled removal of an unnecessary volume of material from the workpiece is carried out.
Chisels, depending on the work performed, come in various configurations. Many turners use their own exclusive, highly specialized cutting turning tools.
Design
Wood lathe cutters contain a metal working part and a wooden handle.
The working part consists of the following sections:
- Cutting, or blade. This section of the tool interacts with the workpiece. It sharpens as needed.
- The main site, or "body". While working with a cutter on a wood lathe, the master, holding the “body” with his second hand, securely fixes the cutter.
- Shank. This section of the chisel has a narrowed shape. It smoothly passes into the handle and is firmly attached there.
The wooden handle consists of two parts:
- Basics. The master holds this section of the tool in his hand.
- Neck - a small cylindrical part, for which a metal fastening ring is provided. Its presence prevents the formation of cracks when the handle is placed on the shank.
The main types of cutters for a wood lathe
Masters, working with wooden cylindrical products, use the following cutting tools:
- Reyers. These chisels perform rough, rough and initial processing of workpieces. The tool is equipped with a blade in the form of a semicircle. For his self-manufacturing you can use a thick plate or a groove with a semicircular section.
- Meisels. These chisels carry out the finishing of wooden products. With the help of this model, the workpiece is given the final shape. In addition, using a meisel, the master can cut off unnecessary remnants from the product. The shape of the chisel is the same as in the jamb knife: the plate is characterized by the presence of an oblique blade with double-sided sharpening.
Shaped tools
With the help of reyers and meisels, work of an average level of complexity is carried out. More subtle operations are possible with the following shaped cutters for a wood lathe:
- Chisel scraper. The tool is characterized by a straight shape and one-sided sharpening. With this cutter, you can level the cylindrical surface of the product.
- Combs. It applies carvings, decorative grooves and dashes.
- Hook and rings. These incisors wooden product cavities are drilled out.
- Triangle chisels. With the help of this shaped model, the workpiece can be given the desired cylindrical shape. According to the reviews of the masters, it is very safe to work with this chisel. This is due to the fact that the blade has a triangular shape, due to which the area of interaction between the cutter and the workpiece is negligible.
Preparation for tool making
It is not difficult to make a cutter for a wood lathe at home with your own hands if you have:
- Metal for the future chisel. Judging by the numerous reviews, good cutters are obtained from old files, rasps and car springs. You can also use various pipe trimmings and fittings. It is desirable that they have a square section.
- Wooden handle. She is considered obligatory element for the future cutter, because it provides a comfortable hold during operation. Some masters buy ready-made pens. However, it is not difficult to carve it yourself.
- As this device you can use any installation equipped with an emery wheel.
- Overalls: goggles, gloves and work overalls. During operation, hot sparks and metal crumbs are formed. The presence of protective special equipment will protect the master from injury.
Progress
To make high-quality wood chisels, it is important to follow the standard algorithm:
- Create a drawing of the future cutter. Attaching it to the metal, carefully cut out the desired shape.
- Carry out the initial sharpening of the product on the abrasive wheel.
- Harden the workpiece. To do this, heat the metal to the maximum temperature, and then place it in a container with used engine oil. Remove the product only after it has completely cooled down. Judging by the reviews, some craftsmen carry out hardening without oil, and they simply allow their homemade products to cool in the air. This procedure is mandatory, since it is hardened cutters that are suitable for working with wood of various hardness.
- Process the product using a sandpaper.
- Perform finishing sharpening on a metalworking machine.
- Slide the metal part onto the wooden handle.
How to sharpen cutters for a wood lathe
The quality of the surface of the workpiece processed by it will depend on how correctly the working tool is sharpened. The sharpness of the cutters is formed on electric metalworking machines equipped with circles of various grain sizes. At what angle to sharpen the tool, each master decides for himself. For beginners, the following optimal options are presented:
- Meisels should have a sharpening angle of about 40 degrees.
- The value of the standard sharpening angle for reyers can vary between 50-60 degrees.
Most turners reduce the angles to 20 degrees as they gain experience. Experienced craftsmen recommend having several incisors of the same type with different angles sharpening. This recommendation is due to the fact that a certain degree of sharpness of the cutter is intended for processing each type of wood. For example, with hardwood on initial stage it is more convenient to work with a tool with sharp ones, they are designed to remove a larger volume from a workpiece. Thus, a cutter with sharp corners can significantly speed up the process. However, in this case, the master is at great risk, since in this mode the blades are very often damaged, which leads to the formation of chips on the workpiece. It is recommended to start sharpening with coarse-grained circles. The fine-grained base is intended exclusively for finishing work.
The value of the sharpening angle that will be given to the cutter should be thought about already before hardening a home-made tool. It is at the initial stage that the molding of the working part is carried out. Finishing in the absence of a metalworking machine with a fine-grained emery wheel is easy to do with a velvet bar.
Finally
The process of making homemade incisors is not an easy task, but very exciting. Having the whole essential tool, high-quality raw materials and following the algorithm of actions, it will not be difficult to make a good cutter even at home.