Опресовування труб СНІП. ТТК. Гідравлічне випробування напірних поліетиленових трубопроводів
Після монтажу водопровідні мережі відчувають внутрішнім тиском на герметичність та міцність. Попереднє випробування водопроводу слід розпочинати лише після придбання стиками необхідної міцності.
Трубопроводи відчувають пневматичним або гідравлічним методом двічі. Вперше труби водопроводу випробовують до встановлення арматури та засипки траншеї. Це роблять для усунення нещільностей при карбуванні або інших з'єднаннях, а також для виявлення в трубах нориць. Вдруге трубопровід випробовують після засипки траншеї, а також закінчення всіх робіт на ділянці трубопроводу.
Коли здійснюють гідравлічне випробування, попередньо трубопровід заповнюють водою, коли пневматичне випробування- Повітрям. Випробування трубопроводу має здійснюватися окремими ділянками, довжина яких не перевищує 1 км.
При випробуванні водопроводу водою, ніж з'являлося зміщення труб, кінці трубопроводу треба закрити глухими фланцями, закріпити упорами. Потім трубопровід із тимчасового трубопроводу наповнюють водою. При цьому спостерігають за виходом повітря із труб через кран, який вмонтований у найвищій точці ділянки трубопроводу.
У трубопроводі за допомогою поршневий насосстворюють необхідний тиск. У результаті випробування трубопроводів необхідно зважати на ймовірність розриву труб, розкидання уламків, тобто. Необхідно вжити всіх заходів, ніж запобігти появі травм в людей.
Тиск повинен бути:
- для напірних чавунних та сталевих трубопроводів- рівним робочому тиску, тобто. встановленому цим проектом, з коефіцієнтом 1,25. Збільшення тиску випробуваного над тиском робітником має становити не менше 5кг/см2, величина тиску випробуваного повинна становити не менше 10кг/см2;
- для азбестоцементних напірних водопроводів- Більше робочого тиску на 5кг/см2;
- для трубопроводів полімерних – рівним тиску, що передбачено ТУ чи ГОСТом даного виду труб, але з менше робочого.
Вважають, що трубопровід попереднє випробуваннявитримав, якщо в ньому не виникло розривів фасонних частин і труб, не виникло порушень карбування з'єднань стикових, не виявлено витоків води. У процесі попереднього випробування водопроводу падіння тиску протягом 10 хвилин за манометром не повинно становити більше 0,5 кг/см2 для трубопроводів не сталевих. Якщо ж трубопровід сталевий, то падіння тиску не допускається.
Трубопровід після гідравлічного випробування відразу засипають землею і негайно проводять остаточне випробування. Трубопровід для цього треба промити чистою водою, випробувані ділянки відключити заглушками чи фланцями від діючого водопроводу.
Трубопровід з розтрубними та муфтовими з'єднаннями перед початком випробування треба наповнити водою та витримати у такому стані 24 години. Остаточне випробування водопроводу треба виконувати без запобіжних клапанів, гідрантів тощо. - замість них встановлюють заглушки, засувки ж відкривають повністю (перевіривши заздалегідь сальникове набивання). Використовувати засувки для відключення діючих мереж випробуваної ділянки не допускається.
Водопровід вважається придатним для прийняття його в експлуатацію, якщо в ньому в ході гідравлічного випробування не буде виявлено розривів фасонних частин, труб, стикових з'єднань, а також якщо витоку води фактичної не перевищуватиме допустимих. Найчастіше остаточне випробування водопроводу поєднують з його здаванням в експлуатацію.
Трубопровід перед введенням його в експлуатацію слід продезінфікувати. Для цього його на добу заповнюють водою, до складу якої входить 30-20мг/л активного хлору. Після цього трубопровід промивають. Коли бактеріологічний аналіз буде задовільним, воду дозволять використовуватиме господарсько-питних потреб.
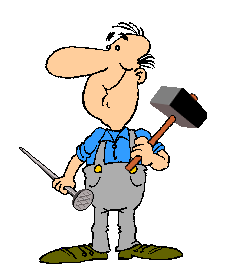
БНіП 3.05.04-85 *
БУДІВЕЛЬНІ НОРМИ І ПРАВИЛА
ЗОВНІШНІ МЕРЕЖІ І СПОРУДИ
ВОДОПОСТАЧАННЯ ТА КАНАЛІЗАЦІЇ
Дата введення 1986-07-01
РОЗРОБЛЕНІ ВНІЇ ВОДГЕО Держбуду СРСР (канд. техн. наук В.І. Готовцев - керівник теми, В.К. Андріаді), за участю Союзводоканалпроекту Держбуду СРСР (П.Г. Васильєв та А.С. Ігнатович), Донецького Промбудівництва проекту Держбуду СРСР (С.А. Світницький), НДІОСП ім. Н.М. Герсеванова Держбуду СРСР (канд. техн. наук В. Г. Галицький та Д.І. Федорович), Гіпроречтрансу Мінрічфлоту РРФСР (М.М. Доманевський), НДІ комунального водопостачання та очищення води АКХ ім. К.Д. Памфілова Мінжитлово-комунального господарства РРФСР (д-р техн. наук Н.А. Лукіних, канд. техн. наук В.П. Криштул), інституту Тульський Промбудпроект Мінтяжбуду СРСР.
ВНЕСЕН ВНІЇ ВОДГЕО Держбуду СРСР.
ПІДГОТОВЛЕНІ ДО ЗАТВЕРДЖЕННЯ Головтехнормуванням Держбуду СРСР (Н. А. Шишов).
ВЗАМЕН СНиП III-30-74 у частині вимог щодо виробництва та приймання робіт з будівництва та реконструкції зовнішніх мереж та споруд водопостачання та каналізації.
СНиП 3.05.04-85 є перевиданням СНиП 3.05.04-85 зі зміною № 1, затвердженим постановою Держбуду СРСР від 25 травня 1990 р. № 51.
Зміна розроблена ВНДІ ВОДГЕО Держбуду СРСР та ЦНДІЕП інженерного обладнання Держкомархітектури.
Розділи, пункти, таблиці, до яких внесено зміни, відмічені зірочкою.
Погоджено з Головним санітарно-епідеміологічним управлінням МОЗ СРСР листом від 10 листопада 1984 р. № 121212/1600-14.
Ці правила поширюються на будівництво нових, розширення та реконструкцію діючих зовнішніх мереж** та споруд водопостачання та каналізації населених пунктівта об'єктів народного господарства.
** Зовнішні мережі - в наступному тексті «трубопроводів».
1. ЗАГАЛЬНІ ПОЛОЖЕННЯ
1.1. При будівництві нових, розширення та реконструкції діючих трубопроводів та споруд водопостачання та каналізації крім вимог проектів (робочих проектів)** та цих правил повинні дотримуватися також вимоги СНиП 3.01.01-85*, СНиП 3.01.03-84, СНиП III-4- 80* та інших норм і правил, стандартів та відомчих нормативних документів, затверджених відповідно до СНиП 1.01.02-83.
** Проектів (робочих проектів) – у наступному тексті «проектів».
1.2. Закінчені будівництвом трубопроводи та споруди водопостачання та каналізації слід приймати в експлуатацію відповідно до вимог СНіП 3.01.04-87.
2. ЗЕМЛЯНІ РОБОТИ
2.1. Земляні роботита роботи з влаштування основ при будівництві трубопроводів та споруд водопостачання та каналізації повинні виконуватись відповідно до вимог СНіП 3.02.01-87.
3. МОНТАЖ ТРУБОПРОВІДІВ
загальні положення
3.1. При переміщенні труб і зібраних секцій, що мають антикорозійні покриття, слід застосовувати м'які кліщові захвати, гнучкі рушники та інші засоби, що унеможливлюють пошкодження цих покриттів.
3.2. При розкладанні труб, призначених для господарсько-питного водопостачання, не слід допускати попадання в них поверхневих або стічних вод. Труби та фасонні частини, арматура та готові вузли перед монтажем повинні бути оглянуті та очищені зсередини та зовні від бруду, снігу, льоду, масел та сторонніх предметів.
3.3. Монтаж трубопроводів повинен проводитися відповідно до проекту виконання робіт та технологічних карт після перевірки відповідності проекту розмірів траншеї, кріплення стінок, позначок дна і при надземному прокладанні - опорних конструкцій. Результати перевірки мають бути відображені у журналі виконання робіт.
3.4. Труби розтрубного типу без напірних трубдротів слід, як правило, укладати розтрубом вгору по ухилу.
3.5. Передбачену проектом прямолінійність ділянок безнапірних трубопроводів між суміжними колодязями слід контролювати переглядом "світло" за допомогою дзеркала до і після засипки траншеї. При перегляді трубопроводу круглого перерізу видиме в дзеркалі коло повинно мати правильну форму.
Допустима величина відхилення від форми кола по горизонталі повинна становити не більше 1/4 діаметра трубопроводу, але не більше 50 мм у кожну сторону. Відхилення від правильної формикола по вертикалі не допускаються.
3.6. Максимальні відхилення від проектного положення осей напірних трубопроводів не повинні перевищувати ±100 мм у плані, позначок лотків безнапірних трубопроводів – ±5 мм, а позначок верху напірних трубопроводів – ±30 мм, якщо інші норми не обґрунтовані проектом.
3.7. Прокладання напірних трубопроводів по пологій кривій без застосування фасонних частин допускається для розтрубних труб зі стиковими з'єднаннями на гумових ущільнювачах з кутом повороту в кожному стику не більше ніж на 2° для труб умовним діаметромдо 600 мм та не більше ніж на 1° для труб умовним діаметром понад 600 мм.
3.8. При монтажі трубопроводів водопостачання та каналізації в гірських умовах крім вимог цих правил слід дотримуватися також вимог розд. 9 БНіП III-42-80.
3.9. При прокладанні трубопроводів на прямолінійній ділянці траси сполучні кінці суміжних труб повинні бути відцентровані так, щоб ширина розтрубної щілини була однаковою по всьому колу.
3.10. Кінці труб, а також отвори у фланцях запірної та іншої арматури при перервах укладання слід закривати заглушками або дерев'яними пробками.
3.11. Гумові ущільнювачі для монтажу трубопроводів в умовах низьких температурзовнішнього повітря не допускається застосовувати у промороженому стані.
3.12. Для закладення (ущільнення) стикових з'єднань трубопроводів слід застосовувати ущільнювальні та "замкові" матеріали, а також герметики згідно з проектом.
3.13. Фланцеві з'єднання фасонних частин та арматури слід монтувати з дотриманням таких вимог:
фланцеві з'єднання повинні бути встановлені перпендикулярно до осі труби;
площини фланців, що з'єднуються, повинні бути рівними, гайки болтів повинні бути розташовані на одній стороні з'єднання; затяжку болтів слід виконувати рівномірно хрест-навхрест;
усунення перекосів фланців установкою скошених прокладок або підтягування болтів не допускається;
зварювання стиків суміжних із фланцевим з'єднанням слід виконувати лише після рівномірної затяжки всіх болтів на фланцях.
3.14. При використанні ґрунту для спорудження упору опорна стінкакотлована має бути з непорушеною структурою ґрунту.
3.15. Зазор між трубопроводом та збірною частиною бетонних або цегляних упорів має бути щільно заповнений бетонною сумішшюабо цементним розчином.
3.16. Захист сталевих та залізо бетонних трубпроводів від корозії слід здійснювати відповідно до проекту та вимог СНіП 3.04.03-85 та СНіП 2.03.11-85.
3.17. На трубопроводах, що споруджуються, підлягають прийманню зі складанням актів огляду прихованих робіт за формою, наведеною в СНиП 3.01.01-85* наступні етапи та елементи прихованих робіт: підготовка основи під трубопроводи, пристрій упорів, величина зазорів та виконання ущільнень стикових з'єднань, пристрій колодязів та камер , протикорозійний захист трубопроводів, герметизація місць проходу трубопроводів через стінки колодязів та камер, засипання трубопроводів з ущільненням та ін.
Сталеві трубопроводи
3.18. Способи зварювання, а також типи, конструктивні елементи та розміри зварних з'єднань сталевих трубопроводів повинні відповідати вимогам ГОСТ 16037-80.
3.19. Перед збиранням та зварюванням труб слід очистити їх від забруднень, перевірити геометричні розміри оброблення кромок, зачистити до металевого блиску кромки та прилеглі до них внутрішню та зовнішню поверхні труб на ширину не менше 10 мм.
3.20. По закінченню зварювальних робітзовнішня ізоляція труб у місцях зварних з'єднань має бути відновлена відповідно до проекту.
3.21. При складанні стиків труб без підкладного кільця зсув кромок не повинен перевищувати 20% товщини стінки, але не більше 3 мм. Для стикових з'єднань, що збираються і зварюються на циліндричному кільці, що залишається, зсув кромок зсередини труби не повинен перевищувати 1 мм.
3.22. Складання труб діаметром понад 100 мм, виготовлених із поздовжнім або спіральним зварним швом, слід проводити зі зміщенням швів суміжних труб не менше ніж на 100 мм. При збиранні стику труб, у яких заводський поздовжній або спіральний шов зварений з двох сторін, усунення цих швів можна не проводити.
3.23. Поперечні зварні з'єднання повинні бути розташовані на відстані не менше ніж:
0,2 м від краю конструкції опори трубопроводу;
0,3 м від зовнішньої та внутрішньої поверхонькамери або поверхні огороджувальної конструкції, через яку проходить трубопровід, а також краю футляра.
3.24. З'єднання кінців стикуючих труб і секцій трубопроводів при величині зазору між ними, що більше допускається, слід виконувати вставкою "котушки" довжиною не менше 200 мм.
3.25. Відстань між кільцевим зварним швом трубопроводу і швом патрубків, що приварюються до трубопроводу, повинна бути не менше 100 мм.
3.26. Складання труб для зварювання повинно виконуватись за допомогою центраторів; допускається виправлення плавних вм'ятин на кінцях труб глибиною до 3,5% діаметра труби та підгонка кромок за допомогою домкратів, роликових опор та інших засобів. Ділянки труб із вм'ятинами понад 3,5% діаметра труби або ті, що мають надриви, слід вирізати. Кінці труб із вибоїнами або задирками фасок глибиною понад 5 мм слід обрізати.
При накладенні кореневого шва прихватки мають бути повністю перетравлені. Електроди, що застосовуються для прихваток, або зварювальний дріт повинні бути тих же марок, що і для зварювання основного шва.
3.27. До зварювання стиків сталевих трубопроводів допускаються зварювальники за наявності документів на право виконання зварювальних робіт відповідно до Правил атестації зварювальників, затверджених Держгіртехнаглядом СРСР.
3.28. Перед допуском до роботи зі зварювання стиків трубопроводів кожен зварювальник повинен зварити допускний стик у виробничих умовах (на об'єкті будівництва) у випадках:
якщо він вперше приступив до зварювання трубопроводів або мав перерву у роботі понад 6 місяців;
якщо зварювання труб здійснюється з нових марок сталей, із застосуванням нових марок зварювальних матеріалів (електродів, зварювального дроту, флюсів) або з використанням нових типів зварювального обладнання.
На трубах діаметром 529 мм і більше дозволяється зварювати половину стику.
Допускний стик піддається:
зовнішньому огляду, у якому зварний шов повинен задовольняти вимогам цього розділу та ГОСТ 16037-80;
радіографічному контролю відповідно до вимог ГОСТ 7512-82;
механічним випробуванням на розрив та вигин відповідно до ГОСТ 6996-66.
У разі незадовільних результатів перевірки допускного стику здійснюються зварювання та повторний контроль двох інших допускових стиків. У разі отримання при повторному контролі незадовільних результатів хоча б на одному зі стиків зварювальник визнається таким, що не витримав випробувань і може бути допущений до зварювання трубопроводу тільки після додаткового навчання та повторних випробувань.
3.29. Кожен зварювальник повинен мати привласнене йому тавро. Зварювальник зобов'язаний вибивати або наплавляти тавро на відстані 30 - 50 мм від стику з боку, доступного для огляду.
3.30. Зварювання та прихватку стикових з'єднань труб допускається проводити при температурі зовнішнього повітря до мінус 50°С. При цьому зварювальні роботи без підігріву стиків, що зварюються, допускається виконувати:
при температурі зовнішнього повітря до мінус 20°С - при застосуванні труб з вуглецевої сталііз вмістом вуглецю не більше 0,24% (незалежно від товщини стінок труб), а також труб із низьколегованої сталі з товщиною стінок не більше 10 мм;
при температурі зовнішнього повітря до мінус 10°С - при застосуванні труб із вуглецевої сталі з вмістом вуглецю понад 0,24%, а також труб із низьколегованої сталі з товщиною стінок понад 10 мм.
При температурі зовнішнього повітря нижче за вищевказані межі зварювальні роботи слід проводити з підігрівом у спеціальних кабінах, в яких температуру повітря слід підтримувати не нижче за вищевказану, або здійснювати підігрів на відкритому повітрікінців труб, що зварюються на довжину не менше 200 мм до температури не нижче 200°С.
Після закінчення зварювання необхідно забезпечити поступове зниження температури стиків і прилеглих до них зон труб шляхом укриття їх після зварювання азбестовим рушником або іншим способом.
3.31. При багатошаровому зварюванні кожен шар шва перед накладенням наступного шва повинен бути очищений від шлаку та бризок металу. Ділянки металу шва з порами, раковинами та тріщинами мають бути вирубані до основного металу, а кратери швів заварені.
3.32. При ручному електродуговому зварюванні окремі шари шва повинні бути накладені так, щоб замикаючі ділянки їх у сусідніх шарах не співпадали один з одним.
3.33. При виконанні зварювальних робіт на відкритому повітрі під час опадів місця зварювання повинні бути захищені від вологи та вітру.
3.34. При контролі якості зварних з'єднань сталевих трубопроводів слід виконувати:
операційний контроль у процесі збирання та зварювання трубопроводу відповідно до вимог СНіП 3.01.01-85*;
перевірку суцільності зварних стиків з виявленням внутрішніх дефектів одним з неруйнівних (фізичних) методів контролю – радіографічним (рентгено- або гаммаграфічним) за ГОСТ 7512-82 або ультразвуковим за ГОСТ 14782-86.
Застосування ультразвукового методу допускається лише у поєднанні з радіографічним, яким має бути перевірено щонайменше 10% загальної кількостістиків, що підлягають контролю.
3.35. При операційному контроліякості зварних з'єднань сталевих трубопроводів слід перевірити відповідність стандартам конструктивних елементів та розмірів зварних з'єднань, способу зварювання, якості зварювальних матеріалів, підготовки кромок, величини зазорів, кількості прихваток, а також справності зварювального обладнання.
3.36. До зовнішнього огляду підлягають усі зварні стики. На трубопроводах діаметром 1020 мм і більше зварені стики, зварені без підкладного кільця, піддаються зовнішньому огляду та вимірюванню розмірів зовні та зсередини труби, в інших випадках – лише зовні. Перед оглядом зварний шов та прилеглі до нього поверхні труб на ширину не менше 20 мм (з обох боків шва) повинні бути очищені від шлаку, бризок розплавленого металу, окалини та інших забруднень.
Якість зварного шва за результатами зовнішнього огляду вважається задовільною, якщо не виявлено:
тріщин у шві та прилеглій зоні;
відступів від допустимих розмірів та форми шва;
підрізів, западань між валиками, напливів, пропалів, незаварених кратерів і пор, непроварів або провисань в корені шва (при огляді стику зсередини труби);
зсувів кромок труб, що перевищують допустимі розміри.
Стики, що не задовольняють переліченим вимогам, підлягають виправленню або видаленню та повторному контролю якості.
3.37. Перевірці якості зварних швів фізичними методами контролю піддаються трубопроводи водопостачання та каналізації з розрахунковим тиском: до 1 МПа (10 кгс/кв.см) обсягом не менше 2% (але не менше одного стику на кожного зварника); 1-2 МПа (10-20 кгс/кв.см) - обсягом щонайменше 5% (але щонайменше двох стиків кожного зварювальника); понад 2 МПа (20 кгс/кв.см) обсягом щонайменше 10% (але щонайменше трьох стиків кожного зварювальника).
3.38. Зварні стики для контролю фізичними методами відбираються в присутності представника замовника, який записує в журналі виконання робіт відомості про відібрані для контролю стики (місце розташування, тавро зварника та ін.).
3.39. Фізичним методам контролю слід піддавати 100% зварних з'єднань трубопроводів, що прокладаються на ділянках переходів під і над залізничними та трамвайними коліями, через водні перешкоди, під автомобільними дорогами, у міських колекторах для комунікацій при суміщеній прокладці з іншими інженерними комунікаціями. Довжину контрольованих ділянок трубопроводів на ділянках переходів слід приймати щонайменше наступних розмірів:
для залізниць- відстані між осями крайніх колій та по 40 м від них у кожний бік;
для автомобільних доріг - ширині насипу по підошві або виїмки по верху та по 25 м від них у кожний бік;
для водних перешкод - у межах підводного переходу, що визначаються розд. 6 БНіП 2.05.06-85;
для інших інженерних комунікацій- ширині споруди, що перетинається, включаючи її водовідвідні пристрої плюс не менше ніж по 4 м в кожну сторону від крайніх меж споруди, що перетинається.
3.40. Зварні шви слід бракувати, якщо під час перевірки фізичними методами контролю виявлено тріщини, незаварені кратери, пропалювання, нориці, а також непровари в корені шва, виконаного на підкладному кільці.
При перевірці зварних швів радіографічним методом допустимими дефектами вважаються:
пори та включення, розміри яких не перевищують максимально допустимих за ГОСТ 23055-78 для 7-го класу зварних з'єднань;
непровари, увігнутість та перевищення проплаву в корені шва, виконаного електродуговим зварюванням без підкладного кільця, висота (глибина) яких не перевищує 10% номінальної товщини стінки, а сумарна довжина – 1/3 внутрішнього периметра з'єднання.
3.41. При виявленні фізичними методами контролю неприпустимих дефектів у зварних швах ці дефекти слід усунути та провести повторний контроль якості подвоєної кількості швів порівняно із зазначеним у п. 3.37. У разі виявлення неприпустимих дефектів при повторному контролі мають бути проконтрольовані усі стики, виконані даним зварювальником.
3.42. Ділянки зварного шва з неприпустимими дефектами підлягають виправленню шляхом місцевої вибірки та наступного підварювання (як правило, без переварювання всього зварного з'єднання), якщо сумарна довжина вибірок після видалення дефектних ділянок не перевищує сумарної довжини, зазначеної в ГОСТ 23055-78 для 7-го класу.
Виправлення дефектів у стиках слід проводити дуговим зварюванням.
Підрізи повинні виправлятися наплавленням ниткових валиків заввишки не більше 2 – 3 мм. Тріщини довжиною менше 50 мм засвердлюються по кінцях, вирубуються, ретельно зачищаються та заварюються у кілька шарів.
3.43. Результати перевірки якості зварних стиків сталевих трубопроводів фізичними методами контролю слід оформляти актом (протоколом).
Чавунні трубопроводи
3.44. Монтаж чавунних труб, що випускаються відповідно до ГОСТ 9583-75, слід здійснювати з ущільненням розтрубних з'єднаньпрядив'яним смоляним або бітумінізованим пасмом та пристроєм азбестоцементного замку, або тільки герметиком, а труб, що випускаються відповідно до ТУ 14-3-12 47-83, гумовими манжетами, що поставляються комплектно з трубами без улаштування замка.
Склад азбестоцементної суміші для влаштування замка, а також герметика визначається проектом.
3.45. Величину зазору між упорною поверхнею розтруба і торцем труби, що з'єднується (незалежно від матеріалу закладення стику) слід приймати, мм: для труб діаметром до 300 мм - 5, понад 300 мм - 8-10.
3.46. Розміри елементів закладання стикового з'єднання чавунних напірних труб повинні відповідати величинам, наведеним у табл. 1.
Таблиця 1
Умовний діаметр |
Глибина загортання, мм |
||
труб Dy, мм |
при застосуванні прядив'яної прядки |
при влаштуванні замку |
при застосуванні лише герметика |
Азбестоцементні трубопроводи
3.47. Величину зазору між торцями труб, що з'єднуються, слід приймати, мм: для труб діаметром до 300 мм - 5, понад 300 мм - 10.
3.48. Перед початком монтажу трубопроводів на кінцях труб, що з'єднуються в залежності від довжини застосовуваних муфт, слід зробити позначки, що відповідають початковому положенню муфти до монтажу стику і кінцевому - в змонтованому стику.
3.49. З'єднання азбестоцементних труб з арматурою або металевими трубамислід здійснювати за допомогою чавунних фасонних частин або сталевих зварних патрубків та гумових ущільнювачів.
3.50. Після закінчення монтажу кожного з'єднання необхідно перевірити правильність розташування муфт і гумових ущільнювачів в них, а також рівномірність затягування фланцевих з'єднань чавунних муфт.
Залізобетонні
та бетонні трубопроводи
3.51. Величину зазору між упорною поверхнею розтруба і торцем труби, що з'єднується, слід приймати, мм:
для залізобетонних напірних труб діаметром до 1000 мм – 12-15, діаметром понад 1000 мм – 18-22;
для залізобетонних та бетонних безнапірних розтрубних труб діаметром до 700 мм – 8-12, понад 700 мм – 15-18;
для фальцевих труб – не більше 25.
3.52. Стикові з'єднання труб, що поставляються без гумових кілець, слід ущільнювати прядив'яним смоляним або бітумінізованим пасмом, або сизальським бітумінізованим пасмом із закладенням замку азбестоцементною сумішшю, а також полісульфідними (тіоколовими) герметиками. Глибина закладення наведена в табл. 2, при цьому відхилення по глибині загортання пасма та замка не повинні перевищувати ±5 мм.
Зазори між наполегливою поверхнею розтрубів і торцями труб у трубопроводах діаметром 1000 мм і більше слід зсередини закладати цементним розчином. Марка цементу визначається проектом.
Для водостічних трубопроводів допускається розтрубну робочу щілину на всю глибину закладати цементним розчином марки В7,5, якщо інші вимоги не передбачені проектом.
Таблиця 2
Глибина загортання, мм |
|||
Діаметр умовного проходу, мм |
при влаштуванні замку |
при застосуванні лише герметиків |
|
3.53. Герметизацію стикових з'єднань безнапірних фальцевих залізобетонних і бетонних труб з гладкими кінцями слід проводити відповідно до проекту.
3.54. З'єднання залізобетонних та бетонних труб з трубопровідною арматурою та металевими трубами слід здійснювати за допомогою сталевих вставок або залізобетонних фасонних з'єднувальних частин, виготовлених згідно з проектом.
Трубопроводи із керамічних труб
3.55. Величину зазору між торцями керамічних труб, що укладаються (незалежно від матеріалу закладення стиків) слід приймати, мм: для труб діаметром до 300 мм - 5 - 7, при великих діаметрах - 8 - 10.
3.56. Стикові з'єднання трубопроводів з керамічних труб слід ущільнювати прядив'яним або сизальським бітумінізованим пасмом з наступним пристроєм замку з цементного розчину марки В7,5, асфальтовою (бітумною) мастикою та полісульфідними (тіоколовими) герметиками, якщо інші матеріали не передбачені проектом. Застосування асфальтової мастики допускається при температурі стічної рідини, що транспортується, не більше 40°С і при відсутності в ній розчинників бітуму.
Основні розміри елементів з'єднання керамічних труб повинні відповідати величинам, наведеним у табл. 3.
Таблиця 3
Глибина загортання, мм |
|||
Діаметр умовного проходу, мм |
при застосуванні прядив'яної або сизальської пасма |
при влаштуванні замку |
при застосуванні тільки герметиків або бітумної мастики |
3.57. Закладка труб у стінках колодязів та камер повинна забезпечувати герметичність з'єднань та водонепроникність колодязів у мокрих ґрунтах.
Трубопроводи із пластмасових труб*
3.58. З'єднання труб із поліетилену високого тиску(ПВД) та поліетилену низького тиску(ПНД) між собою та з фасонними частинами слід здійснювати нагрітим інструментом методом контактно-стикового зварювання встик або врозтруб. Зварювання між собою труб та фасонних частин з поліетилену різних видів(ПНД та ПВД) не допускається.
3.59. Для зварювання слід використовувати установки (пристрою), що забезпечують підтримання параметрів технологічних режимів відповідно до ОСТ 6-19-505-79 та іншої нормативно-технічної документації, затвердженої в установленому порядку.
3.60. До зварювання трубопроводів із ПВД та ПНД допускаються зварювальники за наявності документів на право виконання робіт із зварювання пластмас.
3.61. Зварювання труб із ПВД та ПНД допускається проводити при температурі зовнішнього повітря не нижче мінус 10°С. За нижчої температури зовнішнього повітря зварювання слід проводити в утеплених приміщеннях.
При виконанні зварювальних робіт місце зварювання необхідно захищати від впливу атмосферних опадів та пилу.
3.62. З'єднання труб з полівінілхлориду (ПВХ) між собою та з фасонними частинами слід здійснювати методом склеювання враструб (із застосуванням клею марки ДІПК-127 відповідно до ТУ 6-05-251-95-79) та з використанням гумових манжет, що поставляються комплектно з трубами .
3.63. Склеєні стики протягом 15 хв не повинні піддаватися механічним впливам. Трубопроводи з клейовими з'єднаннями протягом 24 годин не повинні піддаватися гідравлічним випробуванням.
3.64. Роботи зі склеювання слід виконувати при температурі зовнішнього повітря від 5 до 35°С. Місце роботи має бути захищене від впливу атмосферних опадів та пилу.
4. ПЕРЕХОДИ ТРУБОПРОВІДІВ ЧЕРЕЗ ПРИРОДНІ
І ШТУЧНІ ПЕРЕГРАДИ
4.1. Будівництво переходів напірних трубопроводів водопостачання та каналізації через водні перешкоди (річки, озера, водосховища, канали), підводні трубопроводи водозаборів та каналізаційних випусків у межах русла водойм, а також підземних переходів через яри, дороги (автомобільні та залізні, включаючи лінії метрополітену та трамвайні шляхи) ) та міські проїзди мають бути здійснені спеціалізованими організаціями відповідно до вимог СНіП 3.02.01-87, СНіП III-42-80 (розд. 8) та цього розділу.
4.2. Способи прокладання трубопровідних переходів через природні та штучні перешкоди визначаються проектом.
4.3. Прокладання підземних трубопроводів під дорогами слід здійснювати при постійному маркшейдерсько-геодезичному контролі будівельної організаціїза дотриманням передбаченого проектом планового та висотного положень футлярів та трубопроводів.
4.4. Відхилення осі захисних футлярів переходів від проектного положення для самопливних безнапірних трубопроводів не повинні перевищувати:
по вертикалі – 0,6% довжини футляра за умови забезпечення проектного ухилу;
по горизонталі – 1% довжини футляра.
Для напірних трубопроводів ці відхилення не повинні перевищувати відповідно 1 та 1,5% довжини футляра.
5. СПОРУДИ ВОДОПОСТАЧАННЯ ТА КАНАЛІЗАЦІЇ
Споруди для паркану поверхневої води
5.1. Будівництво споруд для забору поверхневої води з річок, озер, водосховищ та каналів має здійснюватися, як правило, спеціалізованими будівельними та монтажними організаціями відповідно до проекту.
5.2. До початку пристрою основи під руслові водоприймачі повинні бути перевірені їх розбивні осі та позначки часових реперів.
Водозабірні свердловини
5.3. У процесі буріння свердловин усі види робіт та основні показники (прохідка, діаметр бурового інструменту, кріплення та вилучення труб із свердловини, цементація, виміри рівнів води та інші операції) слід відображати в журналі з виробництва бурових робіт. При цьому слід відзначати найменування пройдених порід, колір, щільність (фортеця), тріщинуватість, гранулометричний склад порід, водоносність, наявність і величину "пробки" при проходці плавунів, що з'явився і рівень води всіх зустрінутих водоносних горизонтів, що потрапив, поглинання промивної рідини. Вимір рівня води в свердловинах при бурінні слід проводити перед початком робіт кожної зміни. У фонтануючих свердловинах рівні води слід вимірювати шляхом нарощування труб або виміром тиску води.
5.4. У процесі буріння в залежності від фактичного геологічного розрізу допускається в межах встановленого проектом водоносного горизонту коригування буровою організацією глибини свердловини, діаметрів та глибини посадки технічних колон без зміни експлуатаційного діаметра свердловини та без збільшення вартості робіт. Внесення змін до конструкції свердловини не повинно погіршувати її санітарного стану та продуктивності.
5.5. Зразки слід відбирати по одному з кожного шару породи, а при однорідному шарі через 10 м.
За погодженням із проектною організацією зразки порід допускається відбирати не з усіх свердловин.
5.6. Ізолювання експлуатованого водоносного горизонту в свердловині від водоносних горизонтів, що не використовуються, слід виконувати при способі буріння:
обертальному - шляхом затрубної та міжтрубної цементації колон обсадних труб до позначок, передбачених проектом;
ударним - задавлюванням та забиванням обсадної колони у шар природної щільної глини на глибину не менше 1 м або проведенням підчеревної цементації шляхом створення каверни розширювачем або ексцентричним долотом.
5.7. Для забезпечення передбаченого проектом гранулометричного складу матеріалу обсипання фільтрів свердловин глинисті та дрібнопіщані фракції повинні бути видалені відмиванням, а перед засипанням відмитий матеріал слід продезінфікувати.
5.8. Відслонення фільтра в процесі його обсипання слід проводити шляхом підняття колони обсадних труб щоразу на 0,5 - 0,6 м після обсипання свердловини на 0,8 - 1 м за висотою. Верхня межа обсипки повинна бути вищою за робочу частину фільтра не менше ніж на 5 м.
5.9. Водозабірні свердловини після закінчення буріння та установки фільтра повинні бути випробувані відкачуванням, що проводяться безперервно протягом часу, передбаченого проектом.
Перед початком відкачування свердловина має бути очищена від шламу та прокачана, як правило, ерліфтом. У тріщинуватих скельних і гравійно-галечникових водоносних породах відкачування слід починати з максимального проектного зниження рівня води, а в піщаних породах - з мінімального проектного зниження. Величина мінімального фактичного зниження рівня води має бути не більше 0,4 - 0,6 максимального фактичного.
При вимушеній зупинці робіт з відкачування води, якщо сумарний час зупинки перевищує 10% загального проектного часу одне зниження рівня води, відкачування води цього зниження слід повторити. У разі відкачування зі свердловин, обладнаних фільтром з обсипанням, величину усадки матеріалу обсипання слід заміряти в процесі відкачування один раз на добу.
5.10. Дебіт (продуктивність) свердловин слід визначати мірною ємністю з часом заповнення не менше 45 с. Допускається визначати дебіт за допомогою водозливів та водомірів.
Рівень води у свердловині слід заміряти з точністю до 0,1% глибини рівня води, що замірюється.
Дебіт та рівні води в свердловині слід заміряти не рідше ніж через кожні 2 години протягом усього часу відкачування, визначеного проектом.
Контрольні проміри глибини свердловини слід проводити на початку та в кінці відкачування у присутності представника замовника.
5.11. У процесі відкачування бурова організація повинна проводити замір температури води та відбір проб води відповідно до ГОСТ 18963-73 та ГОСТ 4979-49 з доставкою їх до лабораторії для перевірки якості води згідно з ГОСТ 2874-82.
Якість цементації всіх обсадних колон, а також розташування робочої частини фільтра слід перевіряти геофізичними методами. Гирло свердловини, що самовиливається, після закінчення буріння необхідно обладнати засувкою і штуцером для манометра.
5.12. Після закінчення буріння водозабірної свердловини та випробування її відкачуванням води верх експлуатаційної труби повинен бути заварений металевою кришкою та мати отвір з різьбленням під болт-пробку для вимірювання рівня води. На трубі повинні бути нанесені проектний та буровий номери свердловини, найменування бурової організації та рік буріння.
Для експлуатації свердловина відповідно до проекту повинна бути обладнана приладами для вимірювання рівнів води та дебіту.
5.13. Після закінчення буріння та випробування відкачуванням водозабірної свердловини бурова організація повинна передати її замовнику відповідно до вимог СНиП 3.01.04-87, а також зразки пройдених порід та документацію (паспорт), що включає:
геолого-літологічний розріз із конструкцією свердловини, відкоригований за даними геофізичних досліджень;
акти на закладання свердловини, встановлення фільтра, цементацію обсадних колон;
зведену каротажну діаграму з результатами її розшифровки, підписану організацією, що виконала геофізичні роботи;
журнал спостережень за відкачуванням води з водозабірної свердловини;
дані про результати хімічних, бактеріологічних аналізів та органолептичних показників води за ГОСТ 2874-82 та висновок санітарно-епідеміологічної служби.
Документація до здачі замовнику має бути узгоджена з проектною організацією.
Ємнісні споруди
5.14. При монтажі бетонних та залізобетонних монолітних та збірних ємнісних споруд крім вимог проекту слід виконувати також вимоги СНиП 3.03.01-87 та цих правил.
5.15. Зворотне засипання ґрунту в пазухи та обсипання ємнісних споруд необхідно проводити, як правило, механізованим способом після прокладання комунікацій до ємнісних споруд, проведення гідравлічного випробування споруд, усунення виявлених дефектів, виконання гідроізоляції стін та перекриття.
5.16. Після закінчення всіх видів робіт та набору бетоном проектної міцності проводиться гідравлічне випробування ємнісних споруд відповідно до вимог розд. 7.
5.17. Монтаж дренажно-розподільних систем фільтрувальних споруд допускається проводити після проведення гідравлічного випробування ємності споруди на герметичність.
5.18. Круглі отвори в трубопроводах для розподілу води та повітря, а також для збирання води слід виконувати свердлінням відповідно до класу, що вказується у проекті.
Відхилення від проектної ширини щілинних отворів поліетиленових трубахне повинні перевищувати 0,1 мм, а від проектної довжини щілини у світлі ±3 мм.
5.19. Відхилення у відстанях між осями муфт ковпачків у розподільних та відвідних системах фільтрів не повинні перевищувати ±4 мм, а у відмітках верху ковпачків (по циліндричних виступах) – ±2 мм від проектного положення.
5.20. Позначки кромок водозливів у пристроях для розподілу та збирання води (жолоби, лотки та ін.) повинні відповідати проекту та повинні бути вирівняні за рівнем води.
При влаштуванні переливів із трикутними вирізами відхилення відміток низу вирізів від проектних не повинні перевищувати ±3 мм.
5.21. На внутрішній та зовнішній поверхнях жолобів та каналів для збору та розподілу води, а також для збору опадів не повинно бути раковин та наростів. Лотки ринв та каналів повинні мати заданий проектом ухил у бік руху води (або осаду). Наявність на них ділянок із зворотним ухилом не допускається.
5.22. Укладання фільтруючого завантаження в споруди для очищення води фільтруванням допускається проводити після гідравлічного випробування ємностей цих споруд, промивання та прочищення підключених до них трубопроводів, індивідуального випробування роботи кожної з розподільних та збірних систем, вимірювальних та запірних пристроїв.
5.23. Матеріали фільтруючого завантаження, що укладається в споруди для очищення води, у тому числі біофільтри, по гранулометричному складу повинні відповідати проекту або вимогам СНиП 2.04.02-84 і СНиП 2.04.03-85.
5.24. Відхилення товщини шару кожної фракції завантаження, що фільтрує, від проектної величини і товщини всього завантаження не повинно бути понад ±20 мм.
5.25. Після закінчення робіт з укладання завантаження фільтрувальної споруди питного водопостачання має бути проведена промивка та дезінфекція споруди, порядок проведення яких представлений у додатку 5, що рекомендується.
5.26. Монтаж займистих елементів конструкцій дерев'яних зрошувачів, водоуловлювальних ґрат, повітронапрямних щитів та перегородок вентиляторних градирень та бризкальних басейнів слід здійснювати після завершення зварювальних робіт.
6. ДОДАТКОВІ ВИМОГИ ДО БУДІВНИЦТВА
ТРУБОПРОВІДІВ І СПОРУД ВОДОПОСТАЧАННЯ
І КАНАЛІЗАЦІЇ У ОСОБЛИВИХ ПРИРОДНИХ
І КЛІМАТИЧНИХ УМОВАХ
6.1. При будівництві трубопроводів та споруд водопостачання та каналізації в особливих природних та кліматичних умовах слід дотримуватись вимог проекту та цього розділу.
6.2. Трубопроводи тимчасового водопостачання, як правило, необхідно укладати на поверхні землі з дотриманням вимог, що пред'являються до укладання трубопроводів постійного водопостачання.
6.3. Будівництво трубопроводів і споруд на вічномерзлих ґрунтах слід проводити, як правило, при негативних температурахзовнішнього повітря із збереженням мерзлих ґрунтів основ. У разі будівництва трубопроводів та споруд при позитивних температурах зовнішнього повітря слід зберігати ґрунти основи у мерзлому стані та не допускати порушень їх температурно-вологісного режиму, встановленого проектом.
Підготовку основи під трубопроводи та споруди на льодонасичених ґрунтах слід здійснювати шляхом відтавання їх на проектну глибину та ущільнення, а також шляхом заміни відповідно до проекту льодонасичених ґрунтів талими ущільненими ґрунтами.
Рух транспортних засобіві будівельних машину літній час має здійснюватися дорогами та під'їзними шляхами, спорудженими відповідно до проекту.
6.4. Будівництво трубопроводів та споруд у сейсмічних районах слід здійснювати тими самими способами та методами, як і у звичайних умовах будівництва, але з виконанням передбачених проектом заходів щодо забезпечення їхньої сейсмостійкості. Стики сталевих трубопроводів та фасонних частин слід зварювати лише електродуговими методами та перевіряти якість зварювання їх фізичними методами контролю в обсязі 100%.
При будівництві залізобетонних ємнісних споруд, трубопроводів, колодязів та камер слід застосовувати цементні розчиниз пластифікуючими добавками відповідно до проекту.
6.5. Усі роботи із забезпечення сейсмостійкості трубопроводів і споруд, виконані у процесі будівництва, слід відображати в журналі робіт та в актах огляду прихованих робіт.
6.6. При зворотному засипанні пазух ємнісних споруд, що будуються на територіях, що підробляються, слід забезпечувати збереження деформаційних швів.
Зазори деформаційних швів на всю їх висоту (від підошви фундаментів до верху надфундаментної частини споруд) повинні бути очищені від ґрунту, будівельного сміття, напливів бетону, розчину та відходів опалубки.
Актами огляду прихованих робіт мають бути оформлені всі основні спеціальні роботи, у тому числі: монтаж компенсаторів, влаштування швів ковзання у фундаментних конструкціях та деформаційних швів; анкерування та зварювання в місцях влаштування шарнірних з'єднань зв'язків-розпірок; будову пропусків труб через стіни колодязів, камер, ємнісних споруд.
6.7. Трубопроводи на болотах слід укладати в траншею після відведення з неї води або в залиту водою траншею за умови вжиття відповідно до проекту необхідних заходів проти їх спливу.
Плеті трубопроводу слід протягати вздовж траншеї або переміщати на плаву із заглушеними кінцями.
Укладання трубопроводів на повністю відсипані з ущільненням дамби необхідно проводити як у звичайних ґрунтових умовах.
6.8. При будівництві трубопроводів на просадних ґрунтах приямки під стикові з'єднання слід виконувати шляхом ущільнення ґрунту.
7. ВИПРОБУВАННЯ ТРУБОПРОВІДІВ І СПОРУД
Напірні трубопроводи
7.1. За відсутності в проекті вказівки про спосіб випробування напірні трубопроводи підлягають випробуванню на міцність та герметичність, як правило, гідравлічним способом. Залежно від кліматичних умову районі будівництва та за відсутності води може бути застосований пневматичний спосіб випробування для трубопроводів з внутрішнім розрахунковим тиском Рр, не більше:
підземних чавунних, азбестоцементних та залізобетонних - 0,5 МПа (5 кгс/кв.см);
підземних сталевих - 1,6 МПа (16 кгс/кв.см);
надземних сталевих – 0,3 МПа (3 кгс/кв.см).
7.2. Випробування напірних трубопроводів всіх класів має здійснюватися будівельно-монтажною організацією, як правило, у два етапи:
перший - попереднє випробування на міцність і герметичність, що виконується після засипки пазух з підбиванням ґрунту на половину вертикального діаметру та присипкою труб відповідно до вимог СНиП 3.02.01-87 з залишеними відкритими для огляду стиковими з'єднаннями; це випробування допускається виконувати без участі представників замовника та експлуатаційної організації зі складанням акта, що затверджується головним інженером будівельної організації;
другий - приймальне (остаточне) випробування на міцність та герметичність слід виконувати після повного засипання трубопроводу за участю представників замовника та експлуатаційної організації зі складанням акта про результати випробування за формою обов'язкових додатків 1 або 3.
Обидва етапи випробування повинні виконуватися до встановлення гідрантів, вантузів, запобіжних клапанів, замість яких на час випробування слід встановлювати фланцеві заглушки. Попереднє випробування трубопроводів, доступних для огляду в робочому стані або підлягаючих у процесі будівництва негайному засипанню (виконання робіт у зимовий час, у обмежених умовах), за відповідного обґрунтування в проектах допускається не виробляти.
7.3. Трубопроводи підводних переходів підлягають попередньому випробуванню двічі: на стапелі або майданчику після зварювання труб, але до нанесення антикорозійної ізоляції на зварні з'єднання, і вдруге - після укладання трубопроводу траншею в проектне положення, але до засипання грунтом.
Результати попереднього та приймального випробуваньслід оформляти актом формою обов'язкового докладання 1.
7.4. Трубопроводи, що прокладаються на переходах через залізні та автомобільні дорогиІ та ІІ категорій, що підлягають попередньому випробуванню після укладання робочого трубопроводу у футлярі (кожусі) до заповнення міжтрубного просторупорожнини футляра та до засипки робочого та приймального котлованів переходу.
7.5. Величини внутрішнього розрахункового тиску Рр та випробувального тиску Рі для проведення попереднього та приймального випробувань напірного трубопроводу на міцність повинні бути визначені проектом відповідно до вимог СНиП 2.04.02-84 та вказані у робочій документації.
Величина випробувального тиску на герметичність Рг для проведення як попереднього, так і приймального випробувань напірного трубопроводу повинна бути рівною величині внутрішнього розрахункового
межі вимірювання тиску, класу точності та ціни поділу шкали манометра. У цьому величина Рг має перевищувати величини приймального випробувального тиску трубопроводу на міцність Ри.
7.6* Трубопроводи із сталевих, чавунних, залізобетонних та азбестоцементних труб, незалежно від способу випробування, слід випробовувати при довжині менше 1 км - за один прийом; за більшої довжини - ділянками трохи більше 1 км. Довжину випробувальних ділянок цих трубопроводів при гідравлічному способі випробування дозволяється приймати понад 1 км.
Трубопроводи із труб ПВД, ПНД та ПВХ незалежно від способу випробування слід випробовувати при довжині не більше 0,5 км за один прийом, при більшій довжині – ділянками не більше 0,5 км. За відповідного обґрунтування у проекті допускається випробування зазначених трубопроводів за один прийом за довжини до 1 км за умови, що величина припустимої витрати підкачаної води повинна визначатися як для ділянки завдовжки 0,5 км.
Таблиця 4
для різних величин внутрішнього розрахункового тиску Рр у трубопроводі та характеристик використовуваних технічних манометрів |
||||||||||||||||||
Величина внутрішнього розрахункового тиску у трубопроводі Рр, МПа (кгс/кв.см) |
верхня межа вимірювання тиску, МПа (кгс/кв.см) |
ціна поділу, МПа (кгс/кв. см) |
верхня межа вимірювання тиску, МПа (кгс/кв.см) |
ціна поділу, МПа (кгс/кв. см) |
верхня межа вимірювання тиску, МПа (кгс/кв.см) |
ціна поділу, МПа (кгс/кв. см) |
МПа (кгс/кв. см) |
|||||||||||
Класи точності технічних манометрів |
||||||||||||||||||
Від 0,41 до 0,75 (від 4,1 до 7,5) |
||||||||||||||||||
Від 0,76 до 1,2 (від 7,6 до 12) |
||||||||||||||||||
Від 1,21 до 2,0 (від 12,1 до 20) |
||||||||||||||||||
Від 2,01 до 2,5 (від 20,1 до 25) |
||||||||||||||||||
Від 2,51 до 3,0 (від 25,1 до 30) |
||||||||||||||||||
Від 3,01 до 4,0 (від 30,1 до 40) |
||||||||||||||||||
Від 4,01 до 5,0 (від 40,1 до 50) |
7.7. За відсутності у проекті вказівок про величину гідравлічного випробувального тиску Ри для виконання попереднього випробування напірних трубопроводів на міцність величина приймається відповідно до табл. 5*.
Таблиця 5*
Характеристика трубопроводу |
Величина випробувального тиску при попередньому випробуванні, МПа (кгс/кв.см) |
|
1. Сталевий I класу* зі стиковими з'єднаннями на зварюванні (у тому числі підводний) з внутрішнім розрахунковим тиском Рр до 0,75 МПа (7,5кгс/кв.см) |
||
2. Те саме, від 0,75 до 2,5 МПа (від 7,5 до 25 кгс/кв.см) |
Внутрішній розрахунковий тиск з коефіцієнтом 2, але не більше заводського випробувального тиску труб |
|
3. Те саме, св. 2,5 МПа (25 кгс/кв.см) |
||
4. Сталевий, що складається з окремих секцій, що з'єднуються на фланцях, із внутрішнім розрахунковим тиском Рр до 0,5 МПа (5 кгс/см2) |
||
5. Сталевий 2- та 3-го класів зі стиковими з'єднаннями на зварюванні та з внутрішнім розрахунковим тиском Рр до 0,75 МПа (7,5 кгс/кв.см) |
||
6. Те саме, від 0,75 до 2,5 МПа (від 7,5 до 25 кгс/кв.см) |
Внутрішній розрахунковий тиск з коефіцієнтом 1,5, але не більше заводського випробувального тиску труб |
|
7. Те саме. св. 2,5 МПа (25 кгс/кв.см) |
Внутрішній розрахунковий тиск з коефіцієнтом 1,25, але не більше заводського випробувального тиску труб |
|
8. Сталевий самопливний водовід водозабору або каналізаційний випуск |
Встановлюється проектом |
|
9. Чавунний зі стиковими з'єднаннями під зачеканку (за ГОСТ 9583-75 для труб всіх класів) з внутрішнім розрахунковим тиском до 1 МПа (10 кгс/см2) |
Внутрішній розрахунковий тиск плюс 0,5 (5), але не менше 1 (10) та не більше 1,5 (15) |
|
10. Те саме, зі стиковими з'єднаннями на гумових манжетах для труб усіх класів |
Внутрішній розрахунковий тиск з коефіцієнтом 1,5, але не менше 1,5 (15) та не більше 0,6 заводського випробувального гідравлічного тиску |
|
11. Залізобетонний |
Внутрішній розрахунковий тиск із коефіцієнтом 1,3, але не більше заводського випробувального тиску на водонепроникність |
|
12. Азбестоцементний |
Внутрішній розрахунковий тиск з коефіцієнтом 1,3 але не більше 0,6 заводського випробувального тиску на водонепроникність |
|
13. Пластмасовий |
Внутрішній розрахунковий тиск із коефіцієнтом 1,3 |
* Класи трубопроводів приймаються за СНиП 2.04.02-84.
7.8. До проведення попереднього та приймального випробувань напірних трубопроводів мають бути:
закінчено всі роботи з закладення стикових з'єднань, влаштування упорів, монтажу з'єднувальних частин та арматури, отримано задовільні результати контролю якості зварювання та ізоляції сталевих трубопроводів;
встановлені фланцеві заглушки на відводах замість гідрантів, вантузів, запобіжних клапанів та в місцях приєднання до експлуатованих трубопроводів;
підготовлено засоби наповнення, опресування та спорожнення ділянки, що випробовується, змонтовано тимчасові комунікації та встановлено прилади та крани, необхідні для проведення випробувань;
осушені та провентильовані колодязі для виробництва підготовчих робіт, організовано чергування на межі ділянок охоронної зони;
заповнений водою ділянку трубопроводу (при гідравлічному способі випробування) і з нього видалено повітря.
Порядок проведення гідравлічного випробування напірних трубопроводів на міцність та герметичність викладено у додатку 2, що рекомендується.
7.9. Для проведення випробування трубопроводу відповідальному виконавцю робіт має бути виданий наряд-допуск на виконання робіт підвищеної небезпеки із зазначенням у ньому розмірів охоронної зони. Форма наряду-допуску та порядок його видачі повинні відповідати вимогам БНіП III-4-80*.
7.10. Для вимірювання гідравлічного тиску при проведенні попереднього та приймального випробувань трубопроводів на міцність та герметичність слід застосовувати атестовані в установленому порядку пружинні манометри класу точності не нижче 1,5 з діаметром корпусу не менше 160 мм та зі шкалою на номінальний тискблизько 4/3 випробувального Рі.
Для вимірювання об'єму води, що підкачується в трубопровід і що випускається з нього при проведенні випробування, слід застосовувати мірні бачки або лічильники холодної води(Водоміри) за ГОСТ 6019-83, атестовані в установленому порядку.
7.11. Заповнення трубопроводу водою, що випробовується, повинно проводитися, як правило, з інтенсивністю, куб.м/год, не більше: 4 - 5 - для трубопроводів діаметром до 400 мм; 6 -10 – для трубопроводів діаметром від 400 до 600 мм; 10 – 15 – для трубопроводів діаметром 700 – 1000 мм та 15 – 20 – для трубопроводів діаметром понад 1100 мм.
При заповненні трубопроводу водою повітря має бути видалене через відкриті крани та засувки.
7.12. Приймальний гідравлічний випробування напірного трубопроводу допускається починати після засипання його ґрунтом відповідно до вимог СНиП 3.02.01-87 та заповнення водою з метою водонасичення, і якщо при цьому він був витриманий у заповненому стані не менше: 72 год - для залізобетонних труб (у тому кількості 12 год під внутрішнім розрахунковим тиском Рр); азбестоцементних труб - 24 год (зокрема 12 год під внутрішнім розрахунковим тиском Рр); 24 год – для чавунних труб. Для сталевих та поліетиленових трубопроводіввитримка з метою водонасичення не провадиться.
Якщо трубопровід заповнений водою до засипки грунтом, то зазначена тривалість водонасичення встановлюється з моменту засипання трубопроводу.
7.13. Напірний трубопровід визнається таким, що витримав попереднє і приймальне гідравлічне випробування на герметичність, якщо величина витрати підкачаної води не перевищує величин допустимої витрати підкачаної води на ділянку, що випробовується, довжиною 1 км і більше зазначеного в табл. 6*.
Якщо витрата підкаченої води перевищує допустимий, то трубопровід визнається таким, що не витримав випробування і повинні бути вжиті заходи до виявлення та усунення прихованих дефектів трубопроводу, після чого має бути виконане повторне випробування трубопроводу.
ТИПОВА ТЕХНОЛОГІЧНА КАРТА (ТТК)
ГІДРАВЛІЧНЕ ВИПРОБУВАННЯ НАПІРНИХ ПОЛІЕТИЛЕНОВИХ ТРУБОПРОВІДІВ
I. ОБЛАСТЬ ЗАСТОСУВАННЯ
I. ОБЛАСТЬ ЗАСТОСУВАННЯ
1.1. Типова технологічна карта (далі ТТК) - комплексний нормативний документ, що встановлює за визначеною технологією організацію робочих процесів з будівництва споруди із застосуванням найбільш сучасних засобівмеханізації, прогресивних конструкцій та способів виконання робіт. Вони розраховані деякі середні умови виконання робіт. ТТК призначена для використання при розробці Проектів виконання робіт (ППР), іншої організаційно-технологічної документації, а також з метою ознайомлення (навчання) робітників та інженерно-технічних працівників з правилами виконання робіт з гідравлічного випробування на міцність та щільність (герметичність) ділянок напірних мереж .
1.2. У цій карті наведено вказівки щодо організації та технології виконання робіт з гідравлічного випробування на міцність та щільність (герметичність) ділянок напірних мереж раціональними засобами механізації, наведено дані щодо контролю якості та приймання робіт, вимоги промислової безпекита охорони праці під час виконання робіт.
1.3. Нормативною базою для розробки технологічних карток є:
- робочі креслення;
- будівельні норми та правила (СНіП, СН, СП);
- заводські інструкції та технічні умови(ТУ);
- норми та розцінки на будівельно-монтажні роботи (ГЕСН-2001 ЕНіР);
- виробничі норми витрат матеріалів (НПРМ);
- місцеві прогресивні норми та розцінки, норми витрат праці, норми витрат матеріально-технічних ресурсів.
1.4. Мета створення ТК - опис рішень з організації та технології виконання робіт з гідравлічного випробування на міцність та щільність (герметичність) ділянок напірних мереж з метою забезпечення їх високої якості, а також:
- Зниження собівартості робіт;
- скорочення тривалості будівництва;
- забезпечення безпеки виконуваних робіт;
- Організації ритмічної роботи;
- раціональне використання трудових ресурсів та машин;
- уніфікації технологічних рішень.
1.5. На базі ТТК у складі ППР (як обов'язкові складові Проекту виконання робіт) розробляються Робочі технологічні карти(РТК) на виконання окремих видівпо гідравлічному випробуванню на міцність та щільність (герметичність) ділянок напірних мереж. Робочі технологічні карти розробляються на основі типових карток для конкретних умов даної будівельної організації з урахуванням її проектних матеріалів, природних умов, наявного парку машин та будівельних матеріалів, прив'язаних до місцевих умов. Робочі технологічні карти регламентують засоби технологічного забезпечення та правила виконання технологічних процесів під час виконання робіт. Конструктивні особливостіпо гідравлічному випробуванню на міцність та щільність (герметичність) ділянок напірних мереж вирішуються у кожному конкретному випадку Робочим проектом. Склад та ступінь деталізації матеріалів, що розробляються в РТК, встановлюються відповідною підрядною будівельною організацією, виходячи зі специфіки та обсягу виконуваних робіт.
Робочі технологічні карти розглядаються та затверджуються у складі ППР керівником Генеральної підрядної будівельної організації, за погодженням з організацією Замовника, Технічного нагляду Замовника.
1.6. Технологічна карта призначена для виробників робіт, майстрів та бригадирів, що виконують роботи з гідравлічного випробування на міцність та щільність (герметичність) ділянок напірної каналізації та водопроводу з ПЕ труб 160 мм, змонтованих за допомогою зварювання, а також працівників технічного нагляду Замовника та розрахована на конкретні умови виконання робіт у III-й температурній зоні.
Технологічну карту слід застосовувати на такі обсяги робіт:
Напірна каналізація К1н |
- 195 м;
|
Водопровід В1 |
- 170 м. |
ІІ. ЗАГАЛЬНІ ПОЛОЖЕННЯ
2.1. Технологічна карта розроблена на комплекс робіт з гідравлічного випробування на міцність та щільність (герметичність) ділянок напірних мереж.
2.2. Роботи з гідравлічного випробування на міцність та щільність (герметичність) ділянок напірних мереж виконуються в одну зміну, тривалість робочого часу протягом зміни становить:
Де 0,06 - коефіцієнт зниження працездатності за рахунок збільшення тривалості робочої зміни з 8 годин до 10 годин, а також час, пов'язаний з підготовкою до роботи та проведення ЕТО, перерви, пов'язані з організацією та технологією виробничого процесу та відпочинку машиністів будівельних машин та робітників - 10 хв через кожну годину роботи.
2.3. До складу робіт, що послідовно виконуються при гідравлічному випробуванні на міцність та щільність (герметичність) ділянок напірних мереж, входять:
- очищення трубопроводу (промивання) від ґрунту;
- встановлення заглушок, манометрів, кранів, вентилів;
- Влаштування упорів;
- приєднання до трубопроводу випробувального обладнання;
- Наповнення трубопроводу водою до заданого тиску;
- огляд трубопроводу та усунення виявлених дефектів;
- випробування та здавання трубопроводу.
2.5. Технологічною картою передбачено виконання робіт комплексною механізованою ланкою у складі: комбінованої дорожньої машини КДМ-130В-03
(Місткість цистерни 6000 л); автомобільного крана КС-55713-1 "Галичанин"
(Вантажопідйомністю 25,0 т) та вакуумного насосу HUDING TYP-HC551/07
(Робочий тиск 10,0 МПа) як провідний механізм.
Рис.1. Комбінована дорожня маш
іна КДМ-130В-03
Рис.2. Вакуумний насос HUDING TYP-HC551/07
Рис.3. Вантажні характеристики автомобільного стрілового крана КС-55713-1
2.6. Роботи з гідравлічного випробування на міцність та щільність (герметичність) ділянок напірних мереж слід виконувати, керуючись вимогами наступних нормативних документів:
- СП 48.13330.2011. Організація будівництва;
- СНиП 3.01.03-84. Геодезичні роботи у будівництві;
- БНіП 3.05.04-85*. Зовнішні мережі та споруди водопроводу та каналізації;
- БНіП 12-03-2001. Безпека праці у будівництві. Частина 1. Загальні вимоги;
- БНіП 12-04-2002. Безпека праці у будівництві. 2. Будівельне виробництво;
- РД 11-02-2006. Вимоги до складу та порядку ведення виконавчої документації при будівництві, реконструкції, капітальному ремонтіоб'єктів капітального будівництва та вимоги до актів огляду робіт, конструкцій, ділянок мереж інженерно-технічного забезпечення;
- РД 11-05-2007. Порядок ведення загального та (або) спеціального журналу обліку виконання робіт під час будівництва, реконструкції, капітального ремонту об'єктів капітального будівництва.
ІІІ. ОРГАНІЗАЦІЯ ТА ТЕХНОЛОГІЯ ВИКОНАННЯ РОБОТ
3.1. Відповідно до СП 48.13330.2001 "Організація будівництва" до початку виконання будівельно-монтажних робіт на об'єкті Підрядник зобов'язаний в установленому порядку отримати у Замовника проектну документаціюта дозвіл на виконання будівельно-монтажних робіт. Виконання робіт без дозволу забороняється.
3.2. До початку виконання робіт з гідравлічного випробування на міцність і щільність (герметичність) ділянок напірних мереж необхідно провести комплекс організаційно-технічних заходів, у тому числі:
- призначити осіб, відповідальних за якісне та безпечне виконання будівельно-монтажних робіт, а також їх контроль та якість виконання;
- провести інструктаж членів бригади з техніки безпеки;
- розмістити у зоні виконання робіт необхідні машини, механізми та інвентар;
- влаштувати тимчасові проїзди та під'їзди до місця виконання робіт;
- забезпечити зв'язок для оперативно-диспетчерського управління виконанням робіт;
- встановити тимчасові інвентарні побутові приміщення для зберігання будівельних матеріалів, інструменту, інвентарю, обігріву робітників, прийому їжі, сушіння та зберігання робочого одягу, санвузлів тощо;
- забезпечити робочих інструментами та засобами індивідуального захисту;
- підготувати місця для складування матеріалів, інвентарю та іншого необхідного обладнання;
- захистити будівельний майданчикта виставити попереджувальні знаки, освітлені у нічний час;
- забезпечити будівельний майданчик протипожежним інвентарем та засобами сигналізації;
- Скласти акт готовності об'єкта до виконання робіт;
- отримати дозволи на виконання робіт у технагляду Замовника.
3.3. До початку виконання робіт з гідравлічного випробування ділянок напірних мереж повинні бути виконані наступні роботи:
- у траншею покладено трубопровід та прийнято Замовником;
- підземні комунікації, що перетинають покладений трубопровід, укладені в захисні короби і в місці перетину встановлені попереджувальні знаки;
- закінчено всі роботи із закриття кінців трубопроводу в колодязях заглушками та закріплення їх упорами;
- встановлені фланцеві заглушки на відводах замість гідрантів, запобіжних клапанів та у місцях приєднання до експлуатаційних трубопроводів;
- підготовлені засоби наповнення та випорожнення ділянки, що випробовується;
- Отримані задовільні результати контролю якості з'єднань трубопроводу.
Завершення підготовчих робіт фіксують у Загальному журналі робіт (Рекомендована форма наведена у РД 11-05-2007).
3.4. Трубопровідні мережі після монтажу відчувають внутрішнім тиском на міцність та герметичність. Випробування проводять після заповнення трубопроводу водою. Трубопроводи випробовують гідравлічним способом двічі.
Попереднє випробування водопровідних мереж потрібно починати після того, як стики набудуть необхідної міцності.
3.5. Гідравлічне випробування трубопроводу здійснюється у два етапи:
-
перший
- попереднє випробування на міцність і герметичність виконують для ліквідації нещільностей у зварних з'єднаннях та виявлення свищів у трубах, після засипання пазух з підбиванням ґрунту до 15 см з обох боків труб вібротрамбовками та присипкою ґрунтом на 20 см вище за верхи труб з залишеними відкритими для огляду. ;
-
другий
- приймальне (остаточне) випробування на міцність та герметичність виконують після повного засипання трубопроводу ґрунтом механізованим способом до проектних позначок та завершення всіх робіт на даній ділянці трубопроводу.
3.6. Попередні випробування
трубопроводів каналізації слід проводити ділянками між колодязями N 6 - N 5; N 5 - N 4; N 4 - N 1, а трубопроводів водопроводу відповідно між колодязями N - N; N-N; N - N 1 вибірково за вказівкою замовника (за однією із трьох ділянок). Якщо результати вибіркового випробування виявляться незадовільними, випробуванням підлягають всі ділянки трубопроводів.
3.6.1. Величина попереднього випробувального (надлишкового) гідравлічного тиску на міцність, що виконується до засипки траншеї та установки арматури (гідрантів, запобіжних клапанів, вантузів), повинна дорівнювати внутрішньому розрахунковому тиску ( 1,18 МПа
) для поліетиленових напірних труб ПЕ80 SDR13.6
160х9,5 мм із коефіцієнтом 1,5, тобто. 1,77 МПа
.
3.6.2. Попереднє гідравлічне випробування напірних поліетиленових трубопроводів слід проводити в наступному порядку:
- за схемою гідравлічних випробувань (див. мал.7) підключити ділянку випробуваного трубопроводу 1
через тимчасове підведення води 5
до цистерні комбінованої дорожньої машини КДМ-130В-03
, Виконати наповнення його водою з інтенсивністю не більше 4-5 м/год і витримати без тиску протягом 2 годин. При заповненні трубопроводу водою необхідно стежити за видаленням повітря із труб через відкритий кран 4
. При випробуванні, щоб не виникло зміщення труб, кінці трубопроводу закривають глухими фланцями та закріплюють упорами. 2
;
-
підняти тиск у трубопроводі до випробувального 1,77 МПа
, Визначаючи його пружинними манометрами (ГОСТ 8625-77) класу точності не нижче 1,5 7
і шляхом підкачування води підтримувати його протягом 10 хв, не допускаючи зниження тиску більш ніж на 0,1 МПа (1 кгс/см). Падіння тиску за манометром протягом 10 хв має бути не більше 0,5 кг/см. Підтримка тиску шляхом підкачування води в трубопровід проводиться, щоб уникнути деформації оболонки трубопроводу;
- далі випробувальний тиск знизити до внутрішнього розрахункового тиску 1,18 МПа
і, підтримуючи його шляхом підкачування води, провести огляд трубопроводу з метою виявлення дефектів на ньому. Витримка трубопроводу під робочим тиском провадиться не менше 0,5 години.
3.6.3. Напірний поліетиленовий трубопровід вважається таким, що витримав попереднє гідравлічне випробування, якщо під випробувальним тиском не виявлено розривів труб або стиків і фасонних деталей, а під робочим тиском - не виявлено видимих витоків води.
3.6.4. Виявлені при випробуванні трубопроводу дефекти усуваються, а трубопровід піддають повторному випробуванню. При незначних дефектах труб (відколи, тріщини емалі) на дефектне місце наносять шар епоксидної смоли, а при виявленні тріщин і нориці на трубах і на пошкоджених місцях встановлюють сіделки з гумовою прокладкою.
3.6.5. Виконані роботи пред'являють технагляду Замовника для огляду та підписання Акту попереднього випробування трубопроводу відповідно до Додатка 1, СНиП 3.05.04-85* та отримання дозволу на проведення остаточних випробувань на герметичність (щільність).
3.7. Після закінчення випробування трубопроводу на міцність приступають до випробування на герметичність (щільність). Проведення остаточних гідравлічних випробувань на щільність напірних поліетиленових трубопроводів необхідно починати не раніше ніж через 48 годин з моменту засипки траншеї і не раніше ніж через 2 години після заповнення трубопроводу водою. Для цього трубопроводи промивають чистою водою, а випробувані ділянки відключають від діючого водопроводу заглушками або фланцями.
3.8. Випробування ділянок трубопровідних мереж на герметичність (щільність) проводять у наступній послідовності (див. рис.4):
-
вакуумним насосом HUDING TYP-HC551/07
підняти тиск у трубопроводі до величини випробувального тиску на герметичність, що дорівнює величині внутрішнього розрахункового тиску плюс 0,5 МПа (5 кгс/см), враховуючи при цьому, що величина не повинна перевищувати величин випробувального тиску трубопроводу на міцність (у нашому випадку дана умова виконується МПа
);
- фіксуємо час початку випробування та замірюємо початковий рівеньводи у мірному бачку 10
;
- проводимо спостереження за падінням тиску в трубопроводі, при цьому можуть мати місце три варіанти падіння тиску.