tryby cięcia. Posuwy podczas toczenia zgrubnego stały się frezami z węglików spiekanych bez dodatkowej krawędzi skrawającej. Wielka encyklopedia ropy i gazu
Toczenie można przeprowadzić z posuwem mechanicznym, ponieważ tworząca obrobionego stożka jest równoległa do kierunku posuwu wzdłużnego noża.
Cykl technologiczny kopiowania służy do obróbki powierzchni schodkowych, stożkowych i zakrzywionych, które wymagają wzdłużnego posuwu noża. Pod koniec obróbki powierzchni frez jest wycofywany z części, a zacisk powraca do swojej pierwotnej pozycji.
Ogólny indeks maszyny do gwintowania. |
Wzdłużny wspornik 7, zamontowany na prowadnicach łoża, porusza się wzdłuż nich i zapewnia wzdłużny posuw noża. Wózek poprzeczny zapewnia posuw poprzeczny do plotera. Górna podpora obrotowa może być ustawiona pod dowolnym kątem do osi obrotu przedmiotu, co jest niezbędne przy obróbce powierzchni stożkowych przedmiotów.
Schemat toczenia ukształtowanego przedmiotu. |
Po poprzecznym przemieszczeniu korpusu konika o wielkość h do 15 - 20 mm) tworząca obrabianego stożka jest równoległa do kierunku posuwu wzdłużnego noża, dzięki czemu toczenie może odbywać się z posuwem mechanicznym .
Schemat obracania gotowania. |
Po poprzecznym przemieszczeniu korpusu konika o wartość h (do 15 - 20 mm) tworząca obrabianego stożka jest równoległa do kierunku posuwu wzdłużnego noża, dzięki czemu toczenie można wykonać mechanicznie karmić.
W przypadku gwintowania na tokarce konieczne jest, aby prędkość obrotowa wrzeciona była ściśle powiązana z prędkością ruchu suwmiarki, ponieważ posuw wzdłużny frezu w jednym obrocie wrzeciona musi dokładnie odpowiadać skokowi gwintu cięcie.
Grubość warstwy ciętego metalu ma duży wpływ na wielkość nierówności. Grubość ciętej warstwy zależy od posuwu wzdłużnego noża. Gdyby podczas procesu skrawania nie wystąpiły odkształcenia sprężysto-plastyczne, wysokość nierówności można łatwo obliczyć z kształt geometryczny górna część noża.
Po 1 minucie od rozpoczęcia pracy należy wyłączyć posuw wzdłużny frezu, odsunąć frez od obrabianego przedmiotu i szybko obrócić uchwyt narzędzia o 90 lub 180, aż końcówka frezu dotknie końcówki wskaźnika.
W przypadku diamentów w oprawie, podłużne posuwy powinny być mniejsze niż w przypadku ołówków, a w przypadku oszlifowanych diamentów nawet mniej. Np. przy obciąganiu ściernic wielowątkowych frezami diamentowymi posuw wzdłużny frezu nie powinien przekraczać 0,05 m/min. Pod koniec procesu obciągania zaleca się wykonanie jednego lub dwóch przejść bez posuwu poprzecznego, zmniejszając ilość posuwu wzdłużnego.
Oprawa przeznaczona jest do wiercenia otworów stożkowych o stałym kącie a. Urządzenie jest zamocowane na promieniowym wsporniku płyty czołowej maszyny. Obracając śrubę 3, nóż jest podawany wzdłużnie. Na drugim końcu śruby zainstalowana jest gwiazdka 1, która przeskakując zębem przy każdym obrocie zacisku na ustawiony ogranicznik, wykonuje automatyczny posuw wzdłużny.
W celu obróbki przedmiotu poprzez cięcie i uzyskania w wyniku tego obrobionej powierzchni danej części, przedmiotu obrabianego i zastosowanego narzędzie tnące powinien zrobić pewne ruchy. Ruchy te dzielą się na główne (służące do realizacji procesu krojenia) i pomocnicze (służące do przygotowania do procesu krojenia i zakończenia operacji). Istnieją dwa główne ruchy:
- ruch tnący (lub ruch główny);
- ruch paszy.
Podczas obróbki na tokarce ruch skrawający - obrotowy - jest wykonywany przez przedmiot obrabiany, który jest w taki czy inny sposób przymocowany do wrzeciona obrabiarki, a ruch posuwowy - translacyjny - odbiera narzędzie skrawające (frez) sztywno zamocowane w narzędziu uchwyt. Ruch umożliwia proces cięcia (tworzenie wiórów), ruch posuwu umożliwia przeprowadzenie tego procesu (obróbki) na całej długości przedmiotu obrabianego (rys. część 16).
Głębokość cięcia (t)- wartość ciętej warstwy w jednym przejściu, mierzona w kierunku prostopadłym do obrabianej powierzchni. Głębokość cięcia jest zawsze prostopadła do kierunku posuwu (patrz także rys. 11-14). Przy zewnętrznym toczeniu wzdłużnym (rys. 16) jest to połowa różnicy między średnicą przedmiotu obrabianego a średnicą obrabianej powierzchni uzyskaną po jednym przejściu:
Prędkość cięciaυ - ilość ruchu punktowego pionierski nowatorski względem powierzchni na jednostkę czasu podczas wykonywania ruchu skrawającego*.
Podczas toczenia, gdy obrabiany przedmiot obraca się z częstotliwością n obr/min, prędkość skrawania w punktach MK krawędzi skrawającej będzie wartością zmienną. Maksymalna prędkość:
gdzie D jest największą średnicą powierzchni w mm.
* Prędkość skrawania jest funkcją prędkości obrotowej przedmiotu obrabianego oraz prędkości przesuwu (posuwu) narzędzia.
Jeśli prędkość jest znana, łatwo jest określić częstotliwość obrotu:
Przy toczeniu wzdłużnym prędkość skrawania ma stałą wartość przez cały czas skrawania (jeśli średnica przedmiotu obrabianego na całej jego długości jest taka sama, a prędkość obrotowa niezmienna). Podczas przycinania końca, gdy frez przesuwa się z obrzeża przedmiotu obrabianego do środka, prędkość cięcia przy stałej prędkości jest zmienna. Ona ma najwyższa wartość na obrzeżach i jest równa zeru w środku (ryc. 17). Prędkość cięcia będzie również zmienna wzdłuż obrabianej powierzchni podczas przecinania (patrz rys. 14). Jednak w takich przypadkach należy rozważyć prędkość maksymalna ciąć.
Składanie s(dokładniej posuw) - wielkość ruchu krawędzi skrawającej względem obrabianej powierzchni na jednostkę czasu w kierunku ruchu posuwu. Podczas skręcania może być posuw wzdłużny gdy frez porusza się w kierunku równoległym do osi przedmiotu obrabianego (patrz ryc. 16); posuw krzyżowy gdy frez porusza się w kierunku prostopadłym do osi przedmiotu obrabianego (patrz rys. 17), oraz posuw ukośny- pod kątem do osi przedmiotu obrabianego (na przykład podczas toczenia powierzchni stożkowej).
Wyróżnij boisko za jednym zamachem detalu, czyli wielkość względnego ruchu frezu podczas jednego obrotu detalu (z pozycji I frez przesunął się do pozycji II, rys. 16), oraz pasza minutowa, czyli wartość względnego ruchu frezu przez 1 min. Posuw minutowy jest wskazywany przez S m (mm/min), a posuw na obrót - s (mm/obr). Istnieje między nimi następujący związek.
do domu
sekcja trzecia
Podstawy teorii skrawania metali.
Wybór danych skrawania
Rozdział VI
Podstawy teorii skrawania metali
Założycielami teorii cięcia metali byli wybitni rosyjscy naukowcy I. A. Time (1838-1920), K. A. Zvorykin (1861-1928), Ya. G. Usachev (1873-1941) i inni. Prace tych naukowców, które otrzymały uznanie na świecie nie straciło jeszcze na wartości. Jednak w warunkach zacofanej carskiej Rosji wszystkie te prace nie znalazły praktyczne zastosowanie ponieważ przemysł był słabo rozwinięty.
Nauka o cięciu metali nabrała szerokiego zakresu dopiero po Wielkiej Socjalistycznej Rewolucji Październikowej, zwłaszcza podczas sowieckich planów pięcioletnich, kiedy nauka została oddana na służbę socjalistycznemu przemysłowi.
Radzieccy naukowcy W.D. Kuzniecow, W.A. Kriwouchow, I.M. metale, osobliwość czyli ścisła współpraca nauki z produkcją, naukowców z innowatorami produkcji.
Ważną rolę w rozwoju nauki o cięciu metali odegrał ruch innowatorów w produkcji. W celu zwiększenia wydajności pracy liderzy produkcji zaczęli szukać nowych sposobów na poprawę warunków skrawania: stworzyli nową geometrię narzędzia skrawającego, zmienili warunki skrawania, opanowali nowe materiały do cięcia. Każdy Miejsce pracy Turner-innovator stał się jak małe laboratorium do badania procesu cięcia.
Szeroka wymiana doświadczeń, możliwa tylko w warunkach gospodarki socjalistycznej, oraz ścisła współpraca czołowych pracowników produkcji i nauki zapewniły szybki rozwój nauki o cięciu metali.
1. Praca noża
Klin i jego praca. Część robocza każdego narzędzia tnącego to klin(Rys. 44). Pod działaniem przyłożonej siły czubek klina wcina się w metal.
Im ostrzejszy klin, to znaczy im mniejszy kąt utworzony przez jego boki, tym mniej siły potrzeba do wcięcia go w metal. Nazywa się kąt utworzony przez boki klina kąt stożka i jest oznaczony grecką literą β ( beta). Dlatego im mniejszy kąt zbieżności β, tym łatwiej klin wnika w metal, i odwrotnie, im większy kąt zbieżności β, tym większa siła, którą należy przyłożyć, aby przeciąć metal. Przy przypisywaniu kąta stożka należy wziąć pod uwagę właściwości mechaniczne obrabianego metalu. Jeśli tniesz twardy metal nożem o małym kącie ostrzenia β, to cienkie ostrze nie wytrzyma i ulegnie kruszeniu lub pękaniu. Dlatego w zależności od twardości obrabianego metalu przypisywany jest odpowiedni kąt zaostrzenia klina.
Warstwa obrabianego metalu, znajdująca się bezpośrednio przed frezem, jest w sposób ciągły ściskana przez jego przednią powierzchnię. Gdy siła noża przekroczy siły adhezji cząstek metalu, ściśnięty element zostaje ścięty i przesunięty przez przednią powierzchnię klina do góry. Frez poruszający się do przodu pod działaniem przyłożonej siły będzie nadal ściskał, odpryskiwał i przesuwał się poszczególne elementy z którego powstają żetony.
Podstawowe ruchy w toczeniu. Podczas obróbki na tokarkach przedmiot obrabiany obraca się, a frez otrzymuje ruch w kierunku wzdłużnym lub poprzecznym. Nazywa się obrót przedmiotu obrabianego główny ruch i ruch noża względem części - ruch posuwu(Rys. 45).
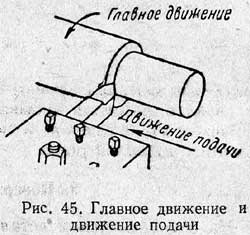
2. Główne części i elementy tokarki
Nóż składa się z dwóch głównych części: głowicy i korpusu (prętu) (ryc. 46). Głowa jest roboczą (tnącą) częścią noża; ciało służy do zabezpieczenia noża w uchwycie narzędzia.

Głowica składa się z następujących elementów: powierzchnia przednia, wzdłuż którego odpadają wióry, oraz tylne powierzchnie przodem do obrabianego przedmiotu. Jedna z tylnych powierzchni skierowanych w stronę powierzchni cięcia nazywa się Główny; druga, zwrócona w stronę obrabianej powierzchni, - pomocniczy.
Krawędzie tnące uzyskuje się z przecięcia przedniej i tylnej powierzchni. Wyróżnić Dom oraz pomocnicza krawędź tnąca. Większość prac związanych z cięciem wykonuje główna krawędź tnąca.
Nazywa się przecięcie głównej i dodatkowej krawędzi skrawającej końcówka siekacza.
3. Obróbka powierzchni
Na przedmiocie obrabianym wyróżnia się trzy rodzaje powierzchni (rys. 47): obrobioną, obrobioną i skrawaną.

obrobiony powierzchnia to powierzchnia przedmiotu obrabianego, z którego usuwane są wióry.
Obróbka powierzchni nazywana powierzchnią części uzyskanej po usunięciu wiórów.
powierzchnia cięcia zwana powierzchnią utworzoną na obrabianym przedmiocie przez główną krawędź tnącą noża.
Konieczne jest również rozróżnienie między płaszczyzną cięcia a płaszczyzną podstawy.
płaszczyzna cięcia nazywana płaszczyzną styczną do powierzchni tnącej i przechodzącą przez krawędź tnącą noża.
Główny samolot nazywana płaszczyzną równoległą do podłużnych i poprzecznych posuwów noża. W przypadku tokarek pokrywa się z poziomą powierzchnią podparcia uchwytu narzędziowego.
4. Kąty cięcia i ich przeznaczenie
Kąty części roboczej noża znacznie wpływają na przebieg procesu cięcia.
Dobierając odpowiednie kąty frezu można znacznie wydłużyć czas jego ciągłej pracy aż do stępienia (trwałość) oraz obróbki w jednostce czasu (na minutę lub godzinę) duża ilość Detale.
Siła skrawania działająca na frez, wymagana moc, jakość obrabianej powierzchni itp. zależą również od doboru kątów frezu, dlatego każdy tokarz musi dobrze przestudiować przeznaczenie każdego z kątów ostrzenia noża i umieć prawidłowo dobrać ich najkorzystniejszą wartość.
Kąty noża (ryc. 48) można podzielić na kąty główne, kąty noża w rzucie oraz kąt nachylenia głównej krawędzi skrawającej.
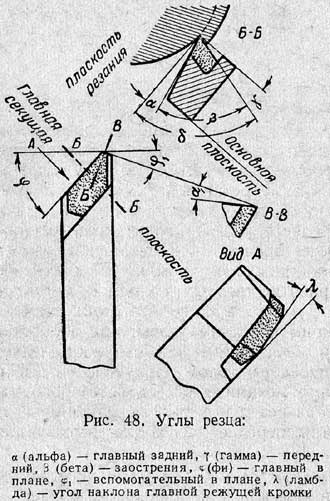
Główne kąty to: kąt tylny, kąt przedni i kąt stożka; kąty noża w planie obejmują główny i pomocniczy.
Główne kąty noża należy mierzyć w głównej płaszczyźnie cięcia, która jest prostopadła do płaszczyzny cięcia i płaszczyzny głównej.
Część roboczą noża stanowi klin (zacieniony na ryc. 48), którego kształt charakteryzuje kąt między przednią a główną tylną powierzchnią noża. Ten róg nazywa się kąt stożka i jest oznaczony grecką literą β (beta).
kąt pleców α ( alfa) to kąt między głównym bokiem a płaszczyzną cięcia.
Kąt przyłożenia α służy do zmniejszenia tarcia między tylną powierzchnią frezu a obrabianym przedmiotem. Zmniejszając tarcie, zmniejszamy w ten sposób nagrzewanie się noża, który dzięki temu zużywa się mniej. Jeśli jednak kąt przyłożenia zostanie znacznie zwiększony, siekacz jest osłabiony i szybko zniszczony.
kąt przedni γ ( gamma) to kąt między przednią powierzchnią noża a płaszczyzną prostopadłą do płaszczyzny cięcia, przeciągnięty przez główną krawędź tnącą.
Ważną rolę w procesie formowania wióra odgrywa kąt natarcia γ. Wraz ze wzrostem kąta natarcia łatwiej jest ciąć frez w metalu, zmniejsza się odkształcenie warstwy ciętej, poprawia się spływ wiórów, zmniejsza się siła skrawania i pobór mocy oraz jakość obrabianej powierzchni jest ulepszony. Z drugiej strony nadmierny wzrost kąta natarcia prowadzi do osłabienia krawędzi skrawającej i spadku jej wytrzymałości, do wzrostu zużycia frezu na skutek wykruszania się krawędzi skrawającej oraz do pogorszenia odprowadzania ciepła. Dlatego przy obróbce metali twardych i kruchych, aby zwiększyć wytrzymałość narzędzia, a także jego trwałość, należy stosować frezy o mniejszym kącie natarcia; przy obróbce metali miękkich i ciągliwych należy stosować frezy o dużym kącie natarcia, aby ułatwić usuwanie wiórów. W praktyce wybór kąta przedniego zależy, oprócz tego, właściwości mechaniczne obrabiany materiał, z materiału noża i kształtu powierzchni czołowej. Zalecane kąty natarcia dla frezów z węglików spiekanych podano w tabeli. jeden.
Planuj kąty. Kąt wiodący φ ( fi) nazywa się kątem między główną krawędzią skrawającą a kierunkiem posuwu.
Kąt φ dobierany jest zwykle w zakresie 30-90° w zależności od rodzaju obróbki, rodzaju frezu, sztywności obrabianego przedmiotu i frezu oraz sposobu ich mocowania. Przy obróbce większości metali przy pomocy nożyc przelotowych można przyjąć kąt φ = 45°; podczas przetwarzania cienkich długie części w kłach należy użyć frezów o kącie natarcia 60, 75 lub nawet 90 °, aby części nie wyginały się ani nie drżały.
Kąt pomocniczy w planieφ 1 to kąt między drugorzędną krawędzią skrawającą a kierunkiem posuwu.

Kąt λ ( lambda) nachylenie głównej krawędzi tnącej(Rys. 49) to kąt między główną krawędzią tnącą a linią poprowadzoną przez górną część noża równolegle do głównej płaszczyzny.
Tabela 1
Zalecane kąty natarcia i przyłożenia dla narzędzi z węglików
Notatka. Właściwości mechaniczne metali są określane na specjalnych maszynach i przyrządach, a każda właściwość ma swoje własne oznaczenie. Oznaczenie σ b podane w tej i kolejnych tabelach wyraża wytrzymałość metalu na rozciąganie; wartość tego limitu jest mierzona w kg/mm 2 . Litery HB oznaczają twardość metalu, którą określa się na urządzeniu Brinella poprzez wciśnięcie kulki z utwardzonej stali w powierzchnię metalu. Wartość twardości mierzy się w kg/mm2.
Frezy, których wierzchołkiem jest najniższy punkt krawędzi skrawającej, czyli kąt λ pozytywny(ryc. 49, c), są bardziej trwałe i odporne; za pomocą takich frezów dobrze jest obrabiać twarde metale, a także powierzchnie przerywane, które tworzą obciążenie udarowe. Podczas obróbki takich powierzchni frezy z węglików spiekanych kąt nachylenia głównej krawędzi skrawającej jest ustawiony na 20-30°. Frezy, których wierzchołkiem jest najwyższy punkt krawędzi skrawającej, czyli kąt λ negatywny(ryc. 49, a) zaleca się stosowanie do obróbki części wykonanych z miękkich metali.
5. Materiały użyte do produkcji siekaczy
Podczas pracy na krawędziach tnących noża występuje wysokie ciśnienie, a także wysoka temperatura (600-800 ° i więcej). Tarcie tylnej powierzchni noża o powierzchnię skrawającą oraz wióry o powierzchnię przednią noża powoduje mniej lub bardziej gwałtowne zużywanie się jego powierzchni roboczych. Z powodu zużycia zmienia się kształt części tnącej i frez po pewnym czasie staje się bezużyteczny do dalszej pracy; taki nóż należy wyjąć z maszyny i ponownie naostrzyć. Aby zwiększyć trwałość narzędzia bez konieczności ponownego szlifowania, ważne jest, aby materiał narzędzia był dobrze odporny na zużycie w wysokich temperaturach. Ponadto materiał noża musi być wystarczająco mocny, aby wytrzymać wysokie ciśnienia powstające podczas cięcia. Dlatego na materiał frezów nałożono następujące podstawowe wymagania - twardość w wysokiej temperaturze, dobrą odporność na zużycie i wytrzymałość.
Obecnie istnieje wiele stali narzędziowych i stopów, które spełniają te wymagania. Należą do nich: stale narzędziowe węglowe, stale szybkotnące, stopy twarde i materiały ceramiczne.
Stal narzędziowa węglowa. Do produkcji narzędzi skrawających używa się stali o zawartości węgla od 0,9 do 1,4%. Po hartowaniu i odpuszczaniu narzędzie skrawające wykonane z tej stali nabiera dużej twardości. Jeśli jednak podczas procesu cięcia temperatura krawędzi skrawającej osiągnie 200-250 °, twardość stali gwałtownie spada.
Z tego powodu węglowa stal narzędziowa ma obecnie ograniczone zastosowanie: jest wykorzystywana do wytwarzania narzędzi skrawających, które pracują ze stosunkowo niską prędkością skrawania, gdy temperatura w strefie skrawania osiąga niewielką wartość. Do takich narzędzi należą: matryce, rozwiertaki, gwintowniki, pilniki, skrobaki itp. Frezy nie są obecnie produkowane z węglowej stali narzędziowej.
Stale szybkotnące. Stale szybkotnące zawierają duża liczba specjalne, tzw. pierwiastki stopowe – wolfram, chrom, wanad i kobalt, które nadają stali wysokie właściwości skrawające – zdolność do zachowania twardości i odporności na zużycie po nagrzaniu podczas cięcia do 600-700 °. Frezy HSS pozwalają na 2-3 razy wyższe prędkości skrawania niż frezy węglowe.
Obecnie w ZSRR produkowane są następujące gatunki stali szybkotnącej (GOST 9373-60): R18, R9, R9F5, R14F14, R18F2, R9K5, R9KYU, R10K5F5 i R18K5F2.
Frezy wykonane w całości ze stali szybkotnącej są drogie, dlatego w celu zaoszczędzenia stali szybkotnącej stosuje się głównie frezy z blachami spawanymi.
Stopy twarde . Stopy węglikowe charakteryzują się bardzo dużą twardością i dobrą odpornością na zużycie.
Stopy twarde wykonywane są w postaci płyt z proszków wolframu i tytanu w połączeniu z węglem. Połączenie węgla i wolframu nazywa się węglik wolframu, a w przypadku tytanu węglik tytanu. Kobalt jest dodawany jako spoiwo. Ta sproszkowana mieszanina jest prasowana pod wysokim ciśnieniem w celu uzyskania małych płyt, które następnie są spiekane w temperaturze około 1500°. Gotowe płyty nie wymagają żadnych obróbka cieplna. Płytka jest przylutowana miedzią do uchwytu noża wykonanego z Stal węglowa lub przymocowane do niego za pomocą regulacji i śrub (mechaniczne mocowanie płytek).
Główną zaletą stopów twardych jest to, że są odporne na ścieranie przez spadające wióry i obrabiany przedmiot oraz nie tracą swoich właściwości skrawających nawet po podgrzaniu do 900-1000 °. Dzięki tym właściwościom frezy wyposażone w płytki węglikowe nadają się do obróbki najbardziej metale stałe(twarde stale, w tym hartowane) oraz materiały niemetaliczne (szkło, porcelana, tworzywa sztuczne) przy prędkościach skrawania 4-6 razy lub więcej niż prędkości skrawania dopuszczone przez frezy wysokoobrotowe.
Wadą twardych stopów jest zwiększona kruchość.
Obecnie w ZSRR produkowane są dwie grupy stopów twardych. Najważniejsze z nich to - wolfram(VK2, VKZ, VK4, VK6M, VK6, VK8 i VK8M) oraz tytanowo-wolframowy(T30K4, T15K6, T14K8, T5K10). Każda z tych grup ma określony zakres (tab. 2).
Wszystkie stopy wolframu przeznaczone są do obróbki żeliwa, metali kolorowych i ich stopów, stali hartowanych, stali nierdzewnych oraz materiałów niemetalicznych (ebonit, porcelana, szkło itp.). Do obróbki stali stosuje się twarde stopy z grupy tytan-wolfram.
Materiały ceramiczne. W ostatnim czasie radzieccy metalurdzy stworzyli tanie materiały o wysokich właściwościach skrawania, które w wielu przypadkach zastępują stopy twarde. Są to materiały ceramiczne termokorund), produkowane w postaci płyt biały kolor, przypominający marmur, który podobnie jak stopy twarde jest albo przylutowywany do oprawek noża, albo mocowany do nich mechanicznie. Płyty te nie zawierają tak drogich i rzadkich pierwiastków jak wolfram, tytan itp. Jednocześnie płyty ceramiczne mają wyższą twardość niż stopy twarde i zachowują swoją twardość po podgrzaniu do 1200 °, co umożliwia cięcie metali ich z wysokie prędkości ciąć.
Wadą płyt ceramicznych jest ich niewystarczająca lepkość. Frezy wyposażone w ceramiczne wkładki mogą być stosowane do wykańczania lub półwykańczania żeliwa, brązu, stopów aluminium i stali miękkich.
6. Ostrzenie i wykańczanie frezów
W fabrykach ostrzenie frezów odbywa się zwykle w sposób scentralizowany w Szlifierki pracownicy specjalni. Ale sam tokarz musi być w stanie naostrzyć i wykończyć noże.
Tabela 2
Właściwości i przeznaczenie niektórych gatunków stopów twardych

Ostrzenie i wykańczanie szybkich noży odbywa się zgodnie z następującymi zasadami:
1. Tarcza szlifierska nie powinna bić, jej powierzchnia powinna być równa; jeśli rozwinęła się powierzchnia robocza koła, należy to skorygować.
2. Podczas ostrzenia należy używać rękojeści, a nie obciążać noża. Rękojeść powinna być zamontowana jak najbliżej ściernicy, pod wymaganym kątem i zapewniać niezawodne podparcie przecinaka (rys. 50, a-d).
3. Nóż do ostrzenia należy przesuwać po powierzchni roboczej koła, w przeciwnym razie będzie się zużywał nierównomiernie.
4. Aby nie przegrzać noża i tym samym uniknąć pojawienia się w nim pęknięć, nie dociskaj mocno noża do koła.
5. Ostrzenie należy przeprowadzać przy ciągłym i obfitym chłodzeniu noża wodą. Chłodzenie kroplowe, a także okresowe zanurzanie mocno nagrzanego noża w wodzie, jest niedozwolone. Jeśli ciągłe chłodzenie nie jest możliwe, lepiej przejść na ostrzenie na sucho.
6. Ostrzenie frezów ze stali szybkotnącej powinno odbywać się przy użyciu ściernic elektrokorundowych o średniej twardości i uziarnieniu 25-16.
Kolejność ostrzenia noży ustala się następująco. Najpierw zaostrzona jest główna tylna powierzchnia (ryc. 50, a). Następnie pomocnicza powierzchnia tylna (ryc. 50, b), następnie przednia powierzchnia (ryc. 50, c) i wreszcie promień wierzchu (ryc. 50, d).
7. Surowo zabrania się ostrzenia noży na maszynach ze zdjętą osłoną ochronną.
8. Podczas ostrzenia należy nosić okulary ochronne.
Po naostrzeniu noża na jego krawędziach tnących pozostają niewielkie nacięcia, zadziory i zagrożenia. Eliminuje je obróbka wykańczająca na specjalnych maszynach wykończeniowych. Wykańczanie odbywa się również ręcznie za pomocą drobnoziarnistej osełki zwilżonej olejem mineralnym. Najpierw, przy lekkich ruchach probierza, reguluje się tylne powierzchnie, a następnie przód i promień blatu.
Ostrzenie i wykańczanie frezów wyposażonych w płytki węglikowe. Ostrzenie frezów płytkami z twardych stopów odbywa się na szlifierkach z kręgami z zielonego węglika krzemu. Ostrzenie odbywa się zarówno ręcznie (ryc. 50, a-d), jak i przy mocowaniu siekaczy w uchwytach narzędziowych. Kolejność ostrzenia tych frezów jest taka sama jak w przypadku frezów ze stali szybkotnącej, tj. najpierw frez ostrzy się wzdłuż głównego grzbietu (ryc. 50, a), a następnie wzdłuż pomocniczych powierzchni tylnych (ryc. 50, b ), następnie wzdłuż przedniej powierzchni (ryc. 50, c) i na koniec zaokrąglić górną część siekacza (ryc. 50, d).
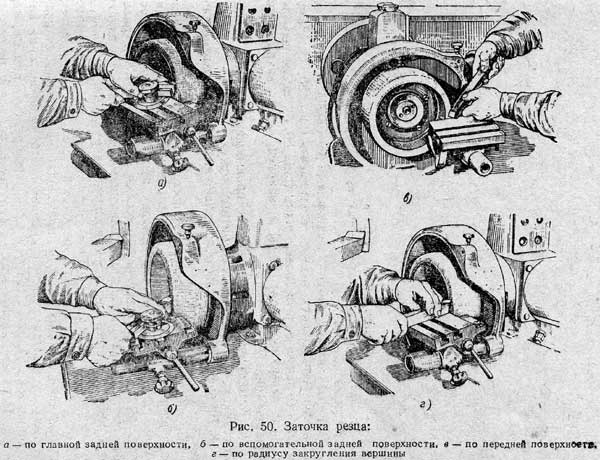
Ostrzenie wstępne wykonujemy zielonymi tarczami z węglika krzemu o ziarnistości 50-40, a końcowe o ziarnistości 25-16.
Nóż nie powinien być mocno dociskany do powierzchni roboczej koła, aby uniknąć przegrzania i pęknięcia płyty ze stopu twardego. Ponadto musi być stale przesuwany względem koła; jest to konieczne do równomiernego noszenia koła.
Ostrzenie można przeprowadzić zarówno na sucho, jak iz obfitym chłodzeniem noża wodą.
Po naostrzeniu frezu z węglików spiekanych konieczne jest wykończenie jego powierzchni. Wykańczanie odbywa się ręcznie lub na maszynie wykańczającej. Wykańczanie ręczne odbywa się za pomocą zakładki żeliwnej lub miedzianej, której powierzchnię roboczą pociera się specjalną pastą lub sproszkowanym węglikiem boru zmieszanym z olejem maszynowym lub naftą nakłada się na powierzchnię równomierną warstwę. Wykańczanie odbywa się na szerokość 2-4 mm od krawędzi tnącej.
Wydajniejsze wykończenie na specjalnej maszynie wykańczającej za pomocą żeliwnego dysku o średnicy 250-300 mm, obracającego się z prędkością 1,5-2 m / s; na powierzchnię tego dysku nakłada się pastę lub proszek z węglika boru zmieszanego z olejem silnikowym lub naftą.
7. Tworzenie wiórów
Rodzaje wiórów. Oderwany wiór pod wpływem nacisku noża znacznie zmienia swój kształt lub, jak mówią, odkształca się: skraca się długość i zwiększa się grubość. Zjawisko to po raz pierwszy odkrył prof. I. A. Czas i nazwany skurcz wióra.
Wygląd wiórów zależy od właściwości mechanicznych metalu i warunków, w jakich odbywa się cięcie. Jeśli obrabiane są lepkie metale (ołów, cyna, miedź, stal miękka, aluminium itp.), wówczas poszczególne elementy wiórów, ściśle przylegające do siebie, tworzą ciągły wiór, który zwija się w taśmę (ryc. 51, a ). Taka nić nazywa się odpływ. Podczas przetwarzania mniej lepkich metali, takich jak twarda stal, z poszczególnych elementów powstają wióry (ryc. 51, b), słabo ze sobą połączone. Taka nić nazywa się frytki.
Jeśli obrabiany metal jest kruchy, taki jak żeliwo lub brąz, wówczas poszczególne elementy wiórów pękają i oddzielają się od przedmiotu obrabianego oraz od siebie (ryc. 51, c). Taki chip, składający się z pojedynczych łusek nieregularny kształt, jest nazywany złamane wióry.
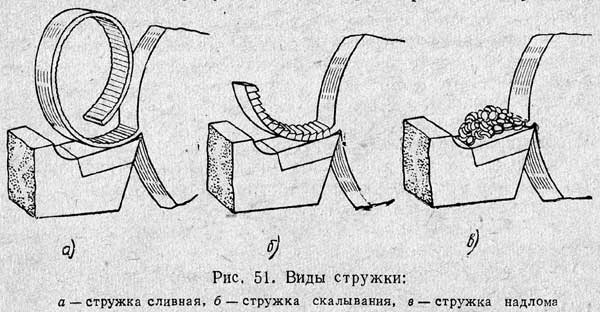
Rozważane rodzaje wiórów nie pozostają stałe, mogą się zmieniać wraz ze zmieniającymi się warunkami skrawania. Im bardziej miękki obrabiany metal i im mniejsza grubość wióra i kąt cięcia, tym bardziej kształt wióra zbliża się do odpływu. To samo będzie obserwowane przy zwiększeniu prędkości skrawania i zastosowaniu chłodzenia. Wraz ze spadkiem prędkości skrawania zamiast wióra drenażowego uzyskuje się wióry wiórowe.
Wyrostek. Jeśli przyjrzymy się przedniej powierzchni noża, który był używany do cięcia, to na krawędzi tnącej czasami można znaleźć mały kawałek metalu przyspawany do noża pod wpływem wysokiej temperatury i ciśnienia. To jest tak zwany wyrostek(Rys. 52). Pojawia się w określonych warunkach skrawania metali ciągliwych, ale nie jest obserwowany podczas obróbki metali kruchych. Twardość narostu jest 2,5-3 razy wyższa niż twardość obrabianego metalu; dzięki temu sama narośl ma możliwość cięcia metalu, z którego została uformowana.
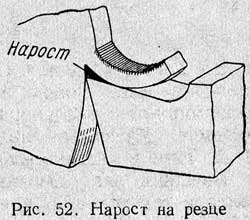
Pozytywną rolą narostu jest to, że zakrywa ostrze tnące, chroniąc je przed zużyciem przez opadające wióry i działanie ciepła, co nieco zwiększa trwałość noża. Obecność narostu jest przydatna podczas obierania, ponieważ ostrze tnące mniej się nagrzewa i zmniejsza się jego zużycie. Jednak wraz z powstawaniem narostu pogarsza się dokładność i czystość obrabianej powierzchni, ponieważ narost zniekształca kształt ostrza. Dlatego tworzenie się narostu jest niekorzystne dla prac wykończeniowych.
8. Pojęcie elementów trybu cięcia
Aby w każdym indywidualnym przypadku wykonać obróbkę bardziej wydajnie, tokarz musi znać podstawowe elementy trybu cięcia; te elementy to głębokość skrawania, posuw i prędkość skrawania.
Głębokość cięcia zwany odległością między obrabianą i obrabianą powierzchnią, mierzoną prostopadle do tej ostatniej. Głębokość cięcia jest oznaczona literą t i mierzona w milimetrach (rys. 53).
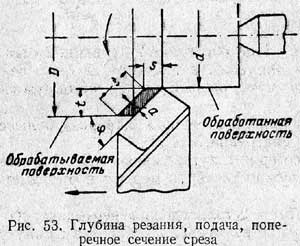
Podczas toczenia przedmiotu na tokarce naddatek na obróbkę jest odcinany w jednym lub kilku przejściach.
Aby określić głębokość skrawania t należy zmierzyć średnicę obrabianego przedmiotu przed i po przejściu frezu, połowa różnicy średnic da głębokość skrawania, czyli innymi słowy
gdzie D jest średnicą części w mm przed przejściem noża; d jest średnicą części w mm po przejściu noża. Nazywa się ruch noża w jednym obrocie przedmiotu obrabianego (ryc. 53) piłowanie. Posuw jest oznaczony literą s i jest mierzony w milimetrach na obrót części; dla zwięzłości zwyczajowo pisze się mm / obr. W zależności od kierunku, w którym nóż porusza się względem prowadnic ramy, występują:
a) posuw wzdłużny- wzdłuż prowadnic łóżka;
b) posuw krzyżowy- prostopadle do prowadnic łóżka;
w) posuw ukośny- pod kątem do prowadnic łóżka (na przykład podczas obracania stożkowej powierzchni).
Pole przekroju cięcia oznaczony literą f (eff) i jest zdefiniowany jako iloczyn głębokości skrawania przez posuw (patrz rys. 53):
Oprócz głębokości cięcia i posuwu rozróżniają również szerokość i grubość ciętej warstwy (ryc. 53).
Szerokość warstwy cięcia, lub szerokość wióra, - odległość pomiędzy obrabianymi i obrabianymi powierzchniami, mierzona wzdłuż powierzchni skrawania. Jest mierzony w milimetrach i oznaczony literą b (be).
Grubość cięcia, lub grubość wióra, to odległość między dwoma kolejnymi pozycjami krawędzi skrawającej w jednym obrocie części, mierzona prostopadle do szerokości wióra. Grubość wióra jest mierzona w milimetrach i oznaczona literą a.
Przy tym samym posuwie i głębokości skrawania, gdy kąt główny φ maleje, grubość wióra maleje, a jego szerokość rośnie. Poprawia to odprowadzanie ciepła z krawędzi skrawającej i zwiększa żywotność narzędzia, co z kolei pozwala znacznie zwiększyć prędkość skrawania i przetwarzać więcej części w jednostce czasu. Jednak zmniejszenie kąta głównego w planie φ prowadzi do wzrostu siły promieniowej (odpychającej), co przy obróbce elementów o niedostatecznej sztywności może powodować ich zginanie, utratę dokładności, a także silne drgania. Pojawienie się drgań z kolei prowadzi do pogorszenia czystości obrabianej powierzchni i często powoduje wykruszanie się krawędzi skrawającej frezu.
Prędkość cięcia. Podczas obróbki na tokarce punkt A, znajdujący się na okręgu o średnicy D (rys. 54), w jednym obrocie część pokonuje drogę równą długości tego okręgu.
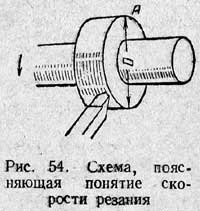
Długość każdego okręgu jest około 3,14 razy większa od jego średnicy, a zatem jest równa 3,14 D.
Liczba 3,14, pokazująca, ile razy długość koła jest większa niż jego średnica, jest zwykle oznaczana grecką literą π (pi).
Punkt A w jednym obrocie utworzy ścieżkę równą πD. Średnica D części oraz jej obwód πD mierzone są w milimetrach.
Załóżmy, że obrabiany przedmiot wykona kilka obrotów na minutę. Oznaczmy ich liczbę literą n obrotów na minutę, czyli w skrócie rpm. Droga, którą zajmie punkt A w tym przypadku będzie równa iloczynowi obwodu i liczby obrotów na minutę, czyli πDn milimetrów na minutę lub w skrócie mm/min i nazywa się prędkość obwodowa.
Sposób, punkt zadowalający nazywana jest powierzchnia do obróbki podczas toczenia względem krawędzi skrawającej frezu w ciągu jednej minuty prędkość cięcia.
Ponieważ średnica części jest zwykle wyrażana w milimetrach, aby obliczyć prędkość skrawania w metrach na minutę, należy podzielić πDn przez 1000. Można to zapisać za pomocą następującego wzoru:
gdzie v jest prędkością skrawania wm/min;
D jest średnicą przedmiotu obrabianego w mm;
n to liczba obrotów na minutę.
Przykład 3Średnica walca obrabianego D = 100 = 150 obr./min. Określ prędkość cięcia.
Decyzja: Liczba obrotów wrzeciona. Podczas toczenia części o znanej średnicy może być konieczne, aby tokarka dostosowała maszynę do takiej liczby obrotów wrzeciona, aby uzyskać wymaganą prędkość skrawania. W tym celu stosuje się następujący wzór: gdzie D jest średnicą przedmiotu obrabianego w mm;
Przykład 4 Jaką liczbę obrotów na minutę powinien mieć walec o średnicy D \u003d 50 mm przy prędkości skrawania v \u003d 25 m / min?
Decyzja:
9. Podstawowe informacje o siłach działających na frez i mocy cięcia
Siły działające na nóż. Podczas usuwania wiórów z przedmiotu obrabianego frez musi pokonać siłę przylegania cząstek metalu do siebie. Gdy krawędź tnąca frezu wcina się w obrabiany materiał i wiór jest oddzielany, frez odczuwa nacisk oddzielonego metalu (rys. 55).

Od góry do dołu siła Pz naciska na frez, który ma tendencję do dociskania frezu w dół i wyginania części do góry. Ta siła nazywa się siła cięcia.
W płaszczyźnie poziomej w kierunku przeciwnym do ruchu posuwu frez dociskany jest siłą P x, zwaną siła osiowa, lub siła posuwu. Ta siła podczas toczenia wzdłużnego ma tendencję do dociskania frezu w kierunku konika.
W płaszczyźnie poziomej, prostopadłej do kierunku posuwu, frez jest dociskany siłą P y, zwaną siłą promieniową. Siła ta ma tendencję do odpychania frezu od przedmiotu obrabianego i wyginania go w kierunku poziomym.
Wszystkie wymienione siły są mierzone w kilogramach.
Największa z tych trzech sił to pionowa siła skrawania: jest to około 4 razy siła posuwu i 2,5 razy siła promieniowa. Siła cięcia obciąża części mechanizmu wrzeciennika; obciąża również frez, część, często powodując w nich duże naprężenia.
Eksperymenty wykazały, że siła skrawania zależy od właściwości obrabianego materiału, wielkości i kształtu usuwanego odcinka wióra, kształtu frezu, prędkości skrawania i chłodzenia.
Aby scharakteryzować opór różne materiały cięcie ustanowiło koncepcję współczynnika cięcia. Współczynnik skrawania K to nacisk skrawania w kilogramach na milimetr kwadratowy skrawanej sekcji, mierzony w określonych warunkach skrawania:
Głębokość cięcia t..............................5 mm
Posuw ......................1 mm/obr
Kąt natarcia γ......................15°
Kąt natarcia φ.......45°
Krawędź tnąca frezu - prostoliniowa, pozioma
Końcówka frezu jest zaokrąglona promieniem r = 1 mm
Praca odbywa się bez chłodzenia
W tabeli. 3 pokazuje średnie wartości współczynnika skrawania dla niektórych metali.
Tabela 3
Średnie wartości współczynnika skrawania K podczas toczenia
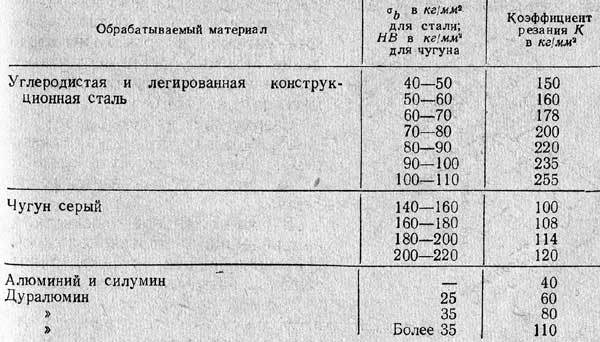
Jeżeli znany jest współczynnik skrawania K, to mnożąc go przez pole przekroju nacięcia f w mm 2, można obliczyć przybliżoną wartość siły skrawania ze wzoru
P z \u003d Kf kg. (osiem)
Przykład 5 Wał wykonany ze stali maszynowej o σ b = 60 kg / mm 2 jest toczony na tokarce. Określ siłę skrawania, jeśli głębokość skrawania t = 5 mm i posuw s = 0,5 mm/obr.
Decyzja. Zgodnie ze wzorem (8) siła cięcia P z \u003d Kf kg. (osiem) Określamy wartość f: f \u003d ts \u003d 5x0,5 \u003d 2,5 mm 2. Zgodnie z tabelą 3 znajdujemy wartość K dla stali maszynowej o σ b \u003d 60 kg / mm 2: K \u003d 160 kg / mm 2. Dlatego z = Kf = 160x2,5 = 400 kg. moc cięcia. Znając siłę skrawania i prędkość skrawania, można dowiedzieć się, jaka moc jest potrzebna do przecięcia wiórów o danym przekroju.
Moc cięcia określa wzór (9) gdzie N res - moc cięcia w KM;
P z - siła cięcia w kg;
v - prędkość skrawania wm/min.
Moc silnika elektrycznego obrabiarki powinna być nieco większa niż moc cięcia, ponieważ część mocy silnika elektrycznego jest zużywana na pokonanie tarcia w mechanizmach przenoszących ruch z silnika elektrycznego na wrzeciono maszyny.
Przykład 6 Wyznacz moc skrawania do obracania wału, rozważaną w poprzednim przykładzie, jeśli obróbka odbywa się z prędkością skrawania υ = 60 m/min. Decyzja . Zgodnie ze wzorem (9) siła cięcia
Moc cięcia jest zwykle wyrażana nie w mocy, ale w kilowatach (kW). Kilowat to 1,36 razy konie mechaniczne, więc aby wyrazić moc w kilowatach, musisz podzielić moc przez 1,36:
i wzajemnie,
10. Ciepło cięcia i żywotność narzędzia
Wraz ze wzrostem siły skrawania wzrasta siła tarcia, w wyniku czego wzrasta ilość ciepła wydzielanego podczas procesu skrawania. Ciepło skrawania wzrasta jeszcze bardziej wraz ze wzrostem prędkości skrawania, ponieważ przyspiesza to cały proces formowania wiórów.
Wytworzone ciepło skrawania przy niewystarczającym jego odprowadzaniu zmiękcza frez, w wyniku czego następuje intensywniejsze zużycie jego części tnącej. Powoduje to konieczność wymiany frezu lub naostrzenia go i ponownej instalacji.
Czas ciągłej pracy frezu przed stępieniem nazywamy trwałością narzędzia (mierzoną w minutach). Częsta zmiana frezu (krótka żywotność narzędzia) powoduje dodatkowe wydatki do ostrzenia i montażu frezu, a także do uzupełniania zużytych frezów.
Dlatego żywotność narzędzia wynosi ważny czynnik przy wyborze warunków skrawania, zwłaszcza przy wyborze prędkości skrawania.
Trwałość noża zależy przede wszystkim od właściwości materiału, z którego jest wykonany. Najbardziej wytrzymały będzie nóż, który wykonany jest z materiału pozwalającego na najwyższą temperaturę nagrzewania bez znacznej utraty twardości. Największą wytrzymałość mają frezy wyposażone w płyty ze stopów twardych, płyty mineralno-ceramiczne; znacznie mniejszy opór - frezy ze stali szybkotnącej, najmniejsze - frezy z węglowej stali narzędziowej.
Opór noża zależy również od właściwości obrabianego materiału, przekroju cięcia, kątów ostrzenia noża i prędkości cięcia. Zwiększenie twardości obrabianego materiału skraca żywotność narzędzia.
Zmieniając kąty ostrzenia oraz kształt powierzchni czołowej, możliwe jest uzyskanie znacznego wzrostu trwałości frezów oraz ich wydajności.
Prędkość skrawania ma szczególnie duży wpływ na trwałość narzędzia. Czasami nawet najmniejszy wzrost prędkości prowadzi do szybkiego stępienia noża. Na przykład, jeśli podczas obróbki stali za pomocą szybkoobrotowego frezu prędkość cięcia zostanie zwiększona tylko o 10%, tj. 1,1 raza, frez stanie się dwukrotnie szybszy i na odwrót.
Wraz ze wzrostem pola przekroju skrawania zmniejsza się żywotność narzędzia, ale nie tak bardzo, jak przy tym samym wzroście prędkości skrawania.
Żywotność narzędzia zależy również od wielkości narzędzia, kształtu skrawanego odcinka i chłodzenia. Im bardziej masywny nóż, tym lepiej odprowadza ciepło z krawędzi tnącej, a co za tym idzie, tym większa jest jego trwałość.
Doświadczenia pokazują, że przy tym samym odcinku skrawania, duża głębokość skrawania i mniejszy posuw zapewniają większą trwałość narzędzia niż mniejsza głębokość skrawania przy odpowiednio większym posuwie. Wyjaśnia to fakt, że przy większej głębokości skrawania wióry stykają się z większą długością krawędzi skrawającej, dzięki czemu ciepło skrawania jest lepiej odprowadzane. Dlatego przy tym samym przekroju bardziej opłaca się pracować na większej głębokości niż z większym posuwem.
Trwałość noża znacznie wzrasta, gdy jest chłodzony.
Chłodziwo musi być dostarczane w dużych ilościach (emulsja 10-12 l/min, olej i sulfofrezol 3-4 l/min); niewielka ilość płynu nie tylko nie przynosi korzyści, ale wręcz psuje frez, powodując pojawianie się na jego powierzchni drobnych pęknięć, prowadzących do odpryskiwania.
11. Wybór prędkości cięcia
Wydajność pracy zależy od wyboru prędkości skrawania: im wyższa prędkość skrawania, tym mniej czasu wydane na przetwarzanie. Jednak wraz ze wzrostem prędkości skrawania żywotność narzędzia maleje, dlatego na wybór prędkości skrawania wpływa trwałość narzędzia i wszystkie czynniki, które wpływają na trwałość narzędzia. Spośród nich najważniejsze są właściwości obrabianego materiału, jakość materiału frezu, głębokość skrawania, posuw, wymiary frezu i kąty ostrzenia oraz chłodzenie.
1. Im dłuższa powinna być żywotność narzędzia, tym mniejsza powinna być prędkość skrawania i odwrotnie.
2. Im twardszy obrabiany materiał, tym mniejsza trwałość narzędzia, dlatego aby zapewnić niezbędną odporność podczas obróbki twardych materiałów, należy zmniejszyć prędkość skrawania. Przy obróbce przedmiotów odlewanych i kutych, na których powierzchni znajduje się twarda skorupa, łupiny lub zgorzelina, konieczne jest zmniejszenie prędkości skrawania w stosunku do możliwej przy obróbce materiałów bez skorupy.
3. Właściwości materiałowe frezu decydują o jego trwałości, dlatego dobór prędkości skrawania również zależy od tych właściwości. Pozostałe parametry są takie same, noże do stali szybkotnącej pozwalają na znacznie wyższą prędkość cięcia niż noże do stali węglowej; jeszcze wyższe prędkości skrawania umożliwiają frezy wyposażone w twarde stopy.
4. W celu zwiększenia wytrzymałości frezu przy obróbce metali lepkich, korzystne jest zastosowanie chłodzenia frezów. W takim przypadku przy tej samej trwałości narzędzia możliwe jest zwiększenie prędkości skrawania o 15-25% w porównaniu z obróbką bez chłodzenia.
5. Na dopuszczalną prędkość cięcia wpływają również gabaryty noża i kąty jego ostrzenia: im bardziej masywny nóż, a zwłaszcza jego głowica, tym lepiej odprowadza ciepło powstałe podczas cięcia. Nieprawidłowo dobrane kąty frezu, które nie odpowiadają obrabianemu materiałowi, zwiększają siłę skrawania i przyczyniają się do szybszego zużycia frezu.
6. Wraz ze wzrostem przekroju zmniejsza się żywotność narzędzia, dlatego przy większym przekroju konieczne jest dobranie mniejszej prędkości skrawania niż przy mniejszym przekroju.
Ponieważ małe wióry są usuwane podczas wykańczania, prędkość skrawania podczas wykańczania może być znacznie wyższa niż podczas obróbki zgrubnej.
Ponieważ zwiększenie przekroju skrawania ma mniejszy wpływ na trwałość narzędzia niż wzrost prędkości skrawania, korzystne jest zwiększenie skrawania ze względu na nieznaczny spadek prędkości skrawania. Na tej zasadzie opiera się metoda przetwarzania innowacyjnego tokarza Kujbyszewskiej Fabryki Obrabiarek V. Kolesov. Pracując z prędkością skrawania 150 m/min, T. Kolesov wykańcza części stalowe z prędkością posuwu do 3 mm/obr. zamiast 0,3 mm/obr., co prowadzi do skrócenia czasu pracy maszyny o 8-10 razy.
Powstaje pytanie: dlaczego zaawansowani tokarze często zwiększają wydajność pracy poprzez zwiększenie prędkości skrawania? Czy to nie jest sprzeczne z podstawowymi prawami cięcia? Nie, to nie jest sprzeczne. Zwiększają prędkość cięcia tylko w przypadku pełnego wykorzystania możliwości zwiększenia przekroju cięcia.
W przypadku wykonywania półwykańczania lub wykańczania, gdzie głębokość skrawania jest ograniczona niewielkim naddatkiem na obróbkę, a posuw jest ograniczony wymaganiami wysokiej czystości obróbki, zwiększenie trybu skrawania jest możliwe poprzez zwiększenie prędkości skrawania . To właśnie robią zaawansowani tokarze, pracując przy półwykańczaniu i wykańczaniu. Jeśli można pracować z duże sekcje skrawania (z dużymi naddatkami), to w pierwszej kolejności należy wybrać możliwie największą głębokość skrawania, następnie możliwie największy technologicznie dopuszczalny posuw, a na końcu odpowiednią prędkość skrawania.
W przypadkach, gdy naddatek na obróbkę jest niewielki i nie ma specjalnych wymagań dotyczących wykończenia powierzchni, tryb skrawania należy zwiększyć stosując możliwie największy posuw.
12. Czystość obrabianej powierzchni
Podczas obróbki frezem nierówności w postaci zagłębień i ząbków zawsze pozostają na obrabianej powierzchni części, nawet przy najstaranniejszym wykańczaniu. Wysokość chropowatości zależy od metody obróbki.
Praktyka wykazała, że im czystsza jest powierzchnia części, tym mniej jest ona podatna na zużycie i korozję, a część jest mocniejsza.
Staranne wykończenie powierzchni podczas obróbki części jest zawsze droższe niż chropowate wykończenie powierzchni. Dlatego czystość obrabianej powierzchni należy przypisać w zależności od warunków pracy części.
Oznaczenie czystości powierzchni na rysunkach. Według GOST 2789-59 zapewnia się 14 klas czystości powierzchni. Aby oznaczyć wszystkie klasy czystości, ustala się jeden znak - trójkąt równoboczny, obok którego wskazany jest numer klasy (na przykład 7; 8; 14). Najczystsze powierzchnie mają stopień 14, a najbardziej chropowaty stopień 1.
Chropowatość powierzchni zgodnie z GOST 2789-59 jest określona przez jeden z dwóch parametrów: a) średnie arytmetyczne odchylenie profilu R a i b) wysokość nierówności R z .
Aby zmierzyć chropowatość i przypisać obrabianą powierzchnię do określonej klasy, specjalny urządzenia pomiarowe oparty na metodzie wyczuwania profilu powierzchni cienką igłą diamentową. Takie urządzenia nazywane są profilometrami i profilografami.
Aby określić chropowatość i zaklasyfikować obrabianą powierzchnię do jednej lub drugiej klasy czystości w warunkach warsztatowych, stosuje się badane próbki różnych klas czystości - tak zwane standardy czystości, z którymi porównywana jest obrabiana powierzchnia części.
Czynniki wpływające na wykończenie powierzchni. Praktyka wykazała, że czystość obrabianej powierzchni zależy od wielu powodów: obrabianego materiału, materiału frezu, kątów ostrzenia i stanu krawędzi tnących frezu, posuwu i prędkości skrawania, smarowania i właściwości chłodzące cieczy, sztywność układu maszyna – frez – część itp.
szczególnie znaczenie zdobyć powierzchnię Wysoka jakość podczas toczenia ma prędkość skrawania, posuw, kąty natarcia oraz promień krzywizny końcówki narzędzia. Im mniejszy posuw i kąt przystawienia oraz większy promień naroża, tym czystsza obrabiana powierzchnia. Szybkość cięcia ma duży wpływ na wykończenie powierzchni. Przy toczeniu stali z prędkością skrawania powyżej 100 m/min obrabiana powierzchnia jest czystsza niż przy prędkości 25-30 m/min.
Aby uzyskać czystszą obrabianą powierzchnię, należy zwrócić uwagę na staranne ostrzenie i wykończenie krawędzi skrawających.
pytania testowe 1. Jaki kształt ma wiór podczas obróbki lepkich metali? Podczas obróbki kruchych metali?
2. Wymień główne elementy głowy siekacza.
3. Pokaż przednią i tylną powierzchnię siekacza; rogi przednie i tylne; kąt ostrzenia.
4. Do czego służą przednie i tylne rogi siekacza?
5. Pokaż kąty natarcia i kąt natarcia.
6. Z jakich materiałów wykonane są frezy?
7. Jakie gatunki stopów twardych stosuje się w obróbce stali? Podczas obróbki żeliwa?
8. Wymień elementy trybu cięcia.
9. Jakie siły działają na nóż?
10. Jakie czynniki i jak wpływają na wielkość siły skrawania?
11. Od czego zależy trwałość noża?
12. Jakie czynniki wpływają na wybór prędkości skrawania?
Do głównych narzędzi skrawających stosowanych w procesie należy frez, którego parametry geometryczne decydują o jego możliwościach technicznych, dokładności i wydajności obróbki. Każdy specjalista, który zdecyduje się poświęcić obracając biznes, o ile właściwy wybór Kąty krawędzi skrawających zwiększają zarówno trwałość, jak i produktywność.
Parametry narzędzi tokarskich
Każdy narzędzie tokarskie tworzą uchwyt niezbędny do zamocowania narzędzia w uchwycie tokarka, oraz głowicę roboczą, która zapewnia cięcie metalu. Aby wziąć pod uwagę parametry geometryczne narzędzia tokarskiego, lepiej jest wziąć za próbkę narzędzie przelotowe.
Na części tnącej noża tokarskiego tego typu istnieją trzy powierzchnie:
- przód (na nim podczas obróbki przedmiotu odpadają wióry metalowe);
- tył - główny i pomocniczy (oba obrócone przednią częścią do przedmiotu obrabianego).
Krawędź narzędzia, zwana krawędzią skrawającą (i bezpośrednio zaangażowaną w obróbkę), jest utworzona przez przecięcie jego przedniej i głównej tylnej powierzchni. W geometrii noża tokarskiego rozróżnia się również pomocniczą krawędź skrawającą. Jest on odpowiednio utworzony przez przecięcie przedniej powierzchni z pomocniczym oparciem.
Punkt, w którym przecinają się główna i pomocnicza krawędź tnąca, nazywany jest końcówką noża. Ten ostatni podczas cięcia metalu podlega ogromnym obciążeniom, prowadzącym do jego pęknięcia. Aby zwiększyć opór końcówki noża, nie jest on ostrzony podczas procesu ostrzenia, ale lekko zaokrąglony. Wymaga to wprowadzenia parametru, takiego jak promień wierzchołka. Istnieje inny sposób na zwiększenie wytrzymałości końcówki noża tokarskiego - utworzenie przejściowej krawędzi skrawającej o prostoliniowym kształcie.
Najważniejszymi parametrami geometrycznymi frezów do toczenia są ich kąty, które określają: wzajemne porozumienie powierzchnie narzędzi. Parametry kąta różnią się w zależności od rodzaju narzędzia tokarskiego i szeregu innych czynników:
- materiał narzędziowy;
- jego warunki pracy;
- właściwości przetwarzanego materiału.
Kąty narzędzi do toczenia
Aby poprawnie określić kąty narzędzie tokarskie, ich dokładne wartości, są one rozpatrywane w tzw. płaszczyznach początkowych.
- Płaszczyzna główna jest równoległa do kierunków posuwu noża tokarskiego (wzdłużnego i poprzecznego) i pokrywa się z jego powierzchnią nośną.
- Płaszczyzna skrawania obejmuje główną krawędź skrawającą i jest styczna do powierzchni obróbki. Ta płaszczyzna jest prostopadła do głównej.
- Główna płaszczyzna skrawająca przecina główną krawędź skrawającą i jest usytuowana prostopadle do rzutu, na który ta krawędź leży na głównej płaszczyźnie. Istnieje również pomocnicza płaszczyzna typu siecznego, która odpowiednio jest prostopadła do rzutu osadzonego na głównej płaszczyźnie przez pomocniczą krawędź skrawającą.
Jak wspomniano powyżej, są one mierzone dokładnie w tych płaszczyznach, a te, które są mierzone w płaszczyźnie zwanej sieczną główną, są oznaczone jako główne. Są to w szczególności kąty główne przednie, główne tylne oraz kąty ostrzenia i cięcia.
Jednym z najważniejszych jest główny kąt przyłożenia noża tokarskiego, który minimalizuje tarcie powstające podczas interakcji tylnej powierzchni narzędzia z obrabianą częścią (a tym samym zmniejsza nagrzewanie się narzędzia i wydłuża jego żywotność ). Kąt ten jest tworzony przez powierzchnię frezu (główny tył) i płaszczyznę cięcia. Przy wyborze tego kąta podczas ostrzenia narzędzia bierze się pod uwagę rodzaj obróbki i materiał przedmiotu obrabianego. W takim przypadku należy mieć świadomość, że silny wzrost wielkości kąta przyłożenia prowadzi do szybkiej awarii narzędzia tokarskiego.
Wytrzymałość i trwałość narzędzia skrawającego, siły występujące podczas obróbki, determinowane są parametrami kąta natarcia. Znajduje się pomiędzy przednią powierzchnią noża tokarskiego a płaszczyzną, w której znajduje się główna krawędź skrawająca (ta płaszczyzna jest prostopadła do płaszczyzny skrawania). Podczas ostrzenia narzędzia tokarskiego bierze się pod uwagę szereg czynników, które wpływają na wartość tego kąta:
- materiał przedmiotu obrabianego i samo narzędzie;
- kształt przedniej powierzchni;
- warunki, w jakich frez będzie używany.
Wzrost wartości kąta natarcia z jednej strony poprawia wykończenie obróbki, az drugiej powoduje spadek wytrzymałości i trwałości noża tokarskiego. Taki kąt, uzyskany w wyniku ostrzenia, może mieć dodatni i negatywne znaczenie.
Frezy tokarskie o kątach natarcia o wartościach ujemnych są bardzo wytrzymałe, ale obróbka takimi narzędziami jest trudna. Zazwyczaj ostrzenie pod kątem natarcia, który ma wartość dodatnią, stosuje się, gdy przedmiot ma być obrabiany z materiału lepkiego, a także gdy materiał narzędzia jest bardzo trwały.
Frezy o ujemnych kątach natarcia stosuje się przy obróbce materiałów o dużej twardości i wytrzymałości, przy wykonywaniu skrawania przerywanego, gdy materiał narzędzia nie ma wystarczającej wytrzymałości na zginanie i nie absorbuje dobrze obciążeń udarowych.
Parametrami charakteryzującymi geometrię frezu do toczenia są również kąty cięcia i nakierowywania. Kąt cięcia, którego wartość może zmieniać się w zakresie 60–100 0, znajduje się pomiędzy powierzchnią narzędzia, zwaną przednią, a płaszczyzną cięcia.
Wartość tego kąta zależy bezpośrednio od twardości obrabianego metalu: im wyższy, tym większa jego wartość. Kąt stożka jest w pełni zgodny z jego nazwą, jest mierzony pomiędzy główną przednią i główną tylną powierzchnią narzędzia i charakteryzuje stopień zaostrzenia jego wierzchu.
Scharakteryzuj narzędzie tokarskie i kąty na planie. Jest to główna, mierzona między kierunkiem posuwu wzdłużnego a rzutem, na który główna krawędź skrawająca leży na płaszczyźnie głównej, oraz pomocnicza, utworzona przez rzut pomocniczej krawędzi skrawającej na główną płaszczyznę i kierunek posuw wzdłużny.
Podczas ostrzenia kąty te nie są wybierane arbitralnie, ale w zależności od rodzaju toczenia i sztywności, jaką ma system „maszyna-narzędzie-przedmiot obrabiany”. Tak więc obróbkę większości metali można prowadzić narzędziami o kącie głównym w planie równym 45 0, ale cienkie i długie detale należy obrabiać frezami, w których wartość tego kąta zawiera się w przedziale 60– 90 0 . Jest to konieczne, aby wyeliminować ugięcie i drżenie części.
Kąt pomocniczy w wyprowadzeniu koreluje jednocześnie z wykończeniem obróbki i trwałością narzędzia. Wraz z jego spadkiem wzrasta czystość obróbki i wzrasta żywotność narzędzia.
Oprócz omówionych powyżej, w geometrii narzędzi tokarskich wyróżnia się kąty.
Toczenie wzdłużne nazywa się toczeniem, w którym kierunek ruchu posuwu jest równoległy do osi przedmiotu obrabianego. Na tokarkach ruch skrawania - obrót - jest przymocowany do przedmiotu obrabianego, a ruch posuwowy - ruch postępowy - do noża. W maszynach z okrągłym prętem narzędzie tnące obraca się, a ruch posuwu jest przymocowany do przedmiotu obrabianego. Prawdziwa ścieżka cięcia to linia śrubowa.
Rozróżnij toczenie precyzyjne i zgrubne.
Toczenie dokładne (ryc. 2, a) wykonuje się za pomocą noża o płaskich powierzchniach roboczych i prostych krawędziach tnących - głównego i pomocniczego. Położenie krawędzi skrawających względem osi obrotu przedmiotu obrabianego charakteryzuje kąt główny w skoku i kąt pomocniczy w skoku. Wartość kąta pomocniczego w planie określa głębokość nierówności kinematycznych, więc nie może być większa. Położenie powierzchni tworzących główną krawędź skrawającą charakteryzuje kąt przyłożenia, kąt zaostrzenia oraz kąt natarcia.
Główna krawędź skrawająca wytwarza cięcie poprzeczne, charakteryzujące się kątem pochylenia włókien drewna.
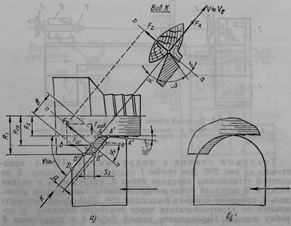
Ryż. 2. Toczenie wzdłużne, wykańczające (a) i zgrubne (b)
Kąt nachylenia mierzy się między kierunkiem włókien a normalną.
Toczenie zgrubne (ryc. 2, b) odbywa się za pomocą frezów rowkowanych z półokrągłą krawędzią tnącą. Przekrój poprzeczny wióry mają kształt sierpa, grubość wiórów na obwodzie przedmiotu obrabianego jest maksymalna, a przy powierzchni części jest nieznaczna nawet przy dużym posuwie do frezu. Pozwala to na zastosowanie posuwu na frez do 2 mm, natomiast przy toczeniu wykańczającym – nie więcej niż 0,8 mm.
> Konfigurowanie tokarek
Podczas ustawiania tokarek należy: dobrać frez i zamocować go w uchwycie narzędziowym (dotyczy maszyn z posuwem mechanicznym); zainstaluj płytę czołową lub uchwyt; wybierz i zamocuj podpórkę na ręce (dla maszyn z ręczne karmienie) lub linijka kopiująca (dla maszyn z posuwem mechanicznym); zainstalować i naprawić obrabiany przedmiot w maszynie; przetestuj maszynę na biegu jałowym; ustawić prędkość wrzeciona i prędkość posuwu; przetwarzać i sprawdzać próbki.
Wymagany nóż jest wybierany w zależności od charakteru wykonywanej pracy. Do wstępnej obróbki zgrubnej używa się frezu do obierania, do ostatecznego frezu wykańczającego z prostą krawędzią tnącą. Przy posuwie mechanicznym frez jest mocowany śrubami w uchwycie narzędzia. Aby skrócić czas wymiany, stosuje się specjalne głowice obrotowe, w których jednocześnie wzmacnia się kilka siekaczy do różnych celów.
Na prace ręczne konieczne jest sprawdzenie niezawodności mocowania noża do drewnianego uchwytu. Nie używaj uszkodzonego narzędzia tnącego.
Sposób mocowania przedmiotu obrabianego dobiera się w zależności od jego kształtu i wielkości. Do mocowania długich przedmiotów obrabianych (ryc. 3, a) stosuje się przednie i tylne środki. Przedni środek 2 wykonany jest w postaci trójzębnej smyczy ze stożkowym trzpieniem, za pomocą którego jest wkładany w zwężający się otwór wrzeciona 1. Tylny środek 4 ma stożkową i spiczastą część i jest zamocowany w pinoli 5 konika 6. Aby zmniejszyć tarcie i zwiększyć niezawodność mocowania przedmiotu obrabianego, tylny środek osadzony jest na łożysku, co zapewnia jego obrót z przedmiotem 3.

Ryż. 3. Mocowanie obrabianego przedmiotu w tokarkach: a - w środkach, b - w uchwycie, c - na płycie czołowej; 1 - wrzeciono, 2 - przedni środkowy, 3 - obrabiany przedmiot, 4 - tylny środkowy, 5 - pióro, 6 - konik, 7 - uchwyt, 8 - plan
W zależności od długości obrabianego przedmiotu konik jest przesuwany wzdłuż prowadnic łoża i ustalany w określonej pozycji. Obrabiany przedmiot jest mocowany przez wypychanie pióra z wrzeciennika, aż środki zostaną osadzone na końcach przedmiotu obrabianego i będą bezpiecznie trzymać go podczas obracania. Aby obrócić części stożkowe, obudowę konika należy przesunąć poprzecznie za pomocą śruby regulacyjnej i zamocować blokadą. Uchwyty są przeznaczone do mocowania krótkich przedmiotów obrabianych (ryc. 3, b). Uchwyt 7 posiada gwint, przez który jest przykręcany do wrzeciona. Obrabiany przedmiot mocuje się w uchwycie, mocno wpasowując jego koniec w otwór uchwytu. Stosowane są również uchwyty zaciskowe i uchwyty ze szczękami przesuwnymi.
Do mocowania detali o krótkiej długości i duża średnica służą jako płyty czołowe 8 (ryc. 3, c), przykręcone do wrzeciona. Obrabiany przedmiot jest mocowany do płyty czołowej za pomocą śrub lub śrub 9.
Rękojeść jest zamontowana na ramie tak, aby jej krawędź robocza znajdowała się na poziomie środków i znajdowała się w pobliżu tworzącej obrabianego przedmiotu, ale go nie dotykała. W miarę zmniejszania się średnicy i obróbki długich elementów rękojeść jest sekwencyjnie ustawiana w nowym położeniu wzdłuż prowadnic łoża. Podczas przetwarzania produktów kształtowych z tyłu łóżka na wspornikach zamocowana jest linijka do kopiowania, której kształt jest podobny do kształtu gotowej części. Gdy posuw jest włączony, suwmiarka porusza się po zakrzywionej ścieżce, a frez odtwarza zadany kształt części.
Prędkość wrzeciona dobierana jest w zależności od średnicy przedmiotu obrabianego i jego wytrzymałości. W przypadku większych średnic należy ustawić minimalną prędkość wrzeciona. Podczas montażu płyty czołowej o średnicy 400 mm prędkość wrzeciona nie powinna przekraczać 800 obr/min. Prędkość obrotową zmniejsza się za pomocą dźwigni zmiany biegów lub poprzez zmianę prędkości obrotowej wielobiegowego silnika elektrycznego. prędkość cięcia drewna miękkie skały powinien wynosić 10 ... 12 m / s, stały - 0,5 ... 3 m / s.
Posuw wzdłużny na jeden obrót wrzeciona powinien wynosić: przy obróbce zgrubnej 1,6...2 mm, przy wykańczaniu - nie więcej niż 0,8 mm. Im wyższe wymagania dotyczące chropowatości powierzchni, tym niższy powinien być posuw wzdłużny. Posuw poprzeczny na obrót wrzeciona nie powinien przekraczać 1,2 mm. Przed uruchomieniem maszyny upewnij się, że: niezawodne mocowanie puste miejsca i zainstaluj ogrodzenie.
Po obróbce zgrubnej części wymienia się frez i wykonuje się toczenie dokładne z niskim posuwem. Wióry w tym przypadku powinny być jak najbardziej ciągłe i jednolitej grubości.
Podczas obróbki kształt części jest okresowo kontrolowany za pomocą szablonu lub miernika. Podczas korzystania z kalibru lub Urządzenie pomiarowe ze skalą maszyna jest wyłączana i dopiero po całkowitym zatrzymaniu części jest mierzona.
Po zakończeniu adiustacji przeprowadzana jest próbna obróbka części, a jej wymiary są kontrolowane kalibrem lub przyrządem pomiarowym ze skalą.