vágási módok. Az előtolás a durva esztergálás során keményfém vágóké vált, további vágóél nélkül. Olaj és gáz nagy enciklopédiája
Az esztergálás mechanikus előtolással is végezhető, mivel a megmunkált kúp generátora párhuzamos a maró hosszirányú előtolásának irányával.
A másolási technológiai ciklus lépcsős, kúpos és íves felületek feldolgozására szolgál, amelyeknél a vágó hosszirányú előtolása szükséges. A felületkezelés végén a vágó visszahúzódik az alkatrészből, és a féknyereg visszaáll eredeti helyzetébe.
A cérnavágó gép általános mutatója. |
A 7 hosszirányú támaszték, amely az ágy vezetőire van felszerelve, ezek mentén mozog, és biztosítja a vágó hosszirányú előtolását. A keresztkocsi keresztirányú előtolást biztosít a vágó számára. A felső forgótámasz a munkadarab forgástengelyéhez képest tetszőleges szögben beállítható, ami a munkadarabok kúpos felületeinek megmunkálásakor szükséges.
Formált munkadarab esztergálásának sémája. |
A farok törzsének h mértékű keresztirányú elmozdulása után 15 - 20 mm-ig) a megmunkált kúp generátora párhuzamos a maró hosszirányú előtolási irányával, így az esztergálás mechanikus előtolással végezhető. .
A főzés forgatásának sémája. |
A farokrész testének h értékkel történő keresztirányú elmozdulása után (15 - 20 mm-ig) a megmunkált kúp generátora párhuzamos a maró hosszirányú előtolási irányával, így az esztergálás mechanikusan végezhető. takarmány.
Esztergagépen történő menetvágáshoz szükséges, hogy az orsó forgási sebessége szigorúan kapcsolódjon a féknyereg mozgási sebességéhez, mivel a maró hosszirányú előtolása az orsó egy fordulatában pontosan meg kell egyezzen a menetemelkedéssel vágva.
A levágott fémréteg vastagsága nagyban befolyásolja az egyenetlenségek nagyságát. A vágott réteg vastagságát a vágó hosszirányú előtolása határozza meg. Ha a forgácsolás során nem lennének rugalmas-képlékeny alakváltozások, akkor az egyenetlenségek magassága könnyen kiszámítható lenne geometriai alakzat a vágó tetejét.
A munka megkezdésétől számított 1 perc elteltével kapcsolja ki a maró hosszirányú előtolását, távolítsa el a marót a munkadarabtól, és gyorsan forgassa el a szerszámtartót 90 vagy 180 fokkal, amíg a maró hegye hozzá nem ér a jelzőcsúcshoz.
A keretben lévő gyémántok esetében a hosszirányú előtolásnak kisebbnek kell lennie, mint a ceruzáknál, a csiszolt gyémántoknál pedig még kevesebbnek kell lennie. Például, ha többmenetes menetcsiszoló korongokat gyémánt marókkal dolgozunk fel, a maró hosszirányú előtolása nem lehet nagyobb, mint 0 05 m/min. A csávázó folyamat végén ajánlott egy-két áthúzás keresztetetés nélkül, csökkentve a hosszanti adagolás mennyiségét.
A szerelvényt állandó szögű kúpos furatok fúrására tervezték a. A készülék a gép előlapjának radiális támasztékára van rögzítve. A 3 csavar elforgatásával a maró hosszirányban betáplálásra kerül. A csavar második végén egy csillag 1 van felszerelve, amely a féknyereg minden egyes fordulatánál fogával a beállított ütközőre ugrál, és automatikus hosszirányú előtolást hajt végre.
A munkadarab vágással történő megmunkálása és ennek eredményeként egy adott alkatrész megmunkált felületeinek, a munkadarab és az alkalmazott vágóeszköz kellene csinálni bizonyos mozdulatokat. Ezeket a mozgásokat fő (a vágási folyamat végrehajtására szolgáló) és segédmozgásokra (a vágási folyamat előkészítésére és a művelet befejezésére szolgálják) osztják. Két fő mozgás létezik:
- vágómozgás (vagy főmozgás);
- takarmány mozgás.
Esztergagépen történő megmunkáláskor a forgácsoló mozgást - forgó - a munkadarab végzi, amely így vagy úgy van a gép orsójához rögzítve, és az előtolás - transzlációs - a szerszámba mereven rögzített vágószerszámot (vágót) kap. tartó. A mozgás lehetővé teszi a vágási folyamatot (forgácsképződés), az előtolás mozgása lehetővé teszi ennek a folyamatnak (feldolgozásnak) a munkadarab teljes hosszában történő lefolytatását (16. ábra).
Vágási mélység (t)- az egy menetben levágott réteg értéke, a megmunkált felületre merőleges irányban mérve. A fogásmélység mindig merőleges az előtolás irányára (lásd még 11-14. ábra). Külső hosszesztergálással (16. ábra) a munkadarab átmérője és a megmunkált felület egy menet után kapott átmérője közötti különbség fele:
Vágási sebességυ - a pontmozgás mennyisége élvonalbeli a felülethez viszonyítva egységnyi idő alatt a vágási mozgás végrehajtása során *.
Esztergáláskor, amikor a munkadarab n ford./perc frekvenciával forog, a forgácsolási sebesség a vágóél MK pontjain változó érték lesz. Teljes sebesség:
ahol D a legnagyobb felületátmérő mm-ben.
* A vágási sebesség a munkadarab forgási sebességének és a szerszám mozgási (előtolási) sebességének a függvénye.
Ha a sebesség ismert, akkor könnyű meghatározni a forgási frekvenciát:
Hosszirányú esztergálással a vágási sebesség állandó értékű a teljes vágási idő alatt (ha a munkadarab átmérője teljes hosszában azonos, és a forgási sebesség változatlan). A vég vágásánál, amikor a maró a munkadarab pereméről a középpont felé mozog, a vágási sebesség állandó fordulatszámon változó. Neki van legmagasabb érték a periférián, középen pedig nullával egyenlő (17. ábra). A vágási sebesség a megmunkált felület mentén is változó lesz a leszúrás során (lásd 14. ábra). Ezekben az esetekben azonban fontolja meg csúcssebesség vágás.
Előterjesztés s(pontosabban előtolási sebesség) - a forgácsolóél mozgásának mértéke a megmunkált felülethez viszonyítva egységnyi idő alatt az előtolás mozgásának irányában. Fordulásnál lehet hosszanti előtolás amikor a maró a munkadarab tengelyével párhuzamos irányban mozog (lásd 16. ábra); kereszttáplálás amikor a maró a munkadarab tengelyére merőleges irányban mozog (lásd 17. ábra), és ferde takarmány- a munkadarab tengelyéhez képest szögben (például kúpos felület esztergálásakor).
Hangmagasság megkülönböztetése egy körben munkadarab, azaz a maró relatív mozgásának mértéke a munkadarab egy fordulata alatt (16. ábra I. pozícióból a maró a II. pozícióba mozdult), ill. perc takarmány, azaz a vágó relatív mozgásának értéke 1 percre. A percelőtolást S m (mm/min), a fordulatonkénti előtolást pedig - s (mm/ford). A következő kapcsolat van köztük.
haza
harmadik szakasz
A fémforgácsolás elméletének alapjai.
Vágási adatok kiválasztása
fejezet VI
A fémforgácsolás elméletének alapjai
A fémvágás elméletének megalapítói a kiváló orosz tudósok, I. A. Time (1838-1920), K. A. Zvorykin (1861-1928), Ya. G. Usachev (1873-1941) és mások voltak. a világ elismerése még nem veszített értékéből. Az elmaradott cári Oroszország körülményei között azonban mindezek a munkák nem találtak praktikus alkalmazás mert az ipar fejletlen volt.
A fémforgácsolás tudománya csak a Nagy Októberi Szocialista Forradalom után kapott szélesebb kört, különösen a szovjet ötéves tervek idején, amikor a tudomány a szocialista ipar szolgálatába állt.
Szovjet tudósok V. D. Kuznyecov, V. A. Krivoukhov, I. M. fémek, jellegzetes tulajdonsága ami a tudomány és a termelés, a tudósok és a termelés megújítói közötti szoros együttműködés.
A fémvágás tudományának fejlődésében fontos szerepet játszott az innovátorok mozgása a termelésben. A munka termelékenységének növelése érdekében a termelési vezetők új utakat kerestek a forgácsolási feltételek javítására: új forgácsolószerszám-geometriát hoztak létre, megváltoztatták a forgácsolási feltételeket, újat sajátítottak el. vágó anyagok. Minden egyes munkahely A Turner-Innovator olyan lett, mint egy kis laboratórium a vágási folyamat tanulmányozására.
A csak a szocialista gazdaság körülményei között lehetséges széles körű tapasztalatcsere, valamint a termelés és a tudomány vezető munkásai közötti szoros együttműködés biztosította a fémforgácsolás tudományának gyors fejlődését.
1. A vágó munkája
Wedge és munkája. Bármely vágószerszám működő része az ék(44. ábra). Az alkalmazott erő hatására az ék hegye belevág a fémbe.
Minél élesebb az ék, vagyis minél kisebb az oldalai által bezárt szög, annál kisebb erő szükséges a fémbe vágásához. Az ék oldalai által alkotott szöget ún kúpos szögés a görög β betűvel jelöljük ( béta). Ezért minél kisebb a β kúposszög, annál könnyebben hatol be az ék a fémbe, és fordítva, minél nagyobb a β kúposszög, annál nagyobb erőt kell kifejteni a fém vágásához. A kúpos szög hozzárendelésénél figyelembe kell venni a feldolgozandó fém mechanikai tulajdonságait. Ha a kemény fémet kis β élezési szögű maróval vágja, akkor a vékony penge nem fog ellenállni, és összeomlik vagy eltörik. Ezért a megmunkálandó fém keménységétől függően megfelelő ékélezési szöget rendelnek hozzá.
A közvetlenül a vágóeszköz előtt elhelyezkedő megmunkálás alatt álló fémréteget az elülső felülete folyamatosan összenyomja. Ha a vágó ereje meghaladja a fémrészecskék tapadási erejét, az összenyomott elem elnyíródik, és az ék elülső felülete felfelé tolja. A kifejtett erő hatására előrehaladó vágó továbbra is összenyom, forgácsol és eltolódik egyedi elemek amelyből forgács keletkezik.
Alapmozgások a fordulásban. Esztergagépen történő megmunkáláskor a munkadarab forog, és a maró hossz- vagy keresztirányú mozgást kap. A munkadarab forgását ún fő mozgás, és a vágó mozgása az alkatrészhez képest - előtolás mozgását(45. ábra).
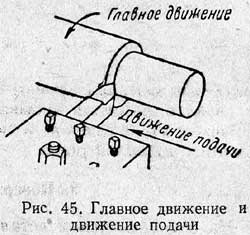
2. Az esztergaszerszám főbb részei, elemei
A vágó két fő részből áll: a fejből és a testből (rúdból) (46. ábra). Fej a vágó munka (vágó) része; test a vágó rögzítésére szolgál a szerszámtartóban.

A fej a következő elemekből áll: elülső felület, amely mentén leválik a forgács, és hátsó felületek a munkadarab felé nézzen. A vágási felület felé néző egyik hátsó felület ún fő-; a másik a kezelt felület felé néz, - kiegészítő.
A vágóélek az elülső és a hátsó felületek metszéspontjából származnak. Megkülönböztetni itthonés segédvágóél. A vágási munka nagy részét a fő vágóél végzi.
A fő és a másodlagos vágóél metszéspontját ún metszőfog hegye.
3. Felületkezelés
A munkadarabon háromféle felületet különböztetünk meg (47. ábra): megmunkált, megmunkált és vágófelület.

feldolgozott A felület a munkadarab azon felülete, amelyről a forgácsot eltávolítják.
Felület kezelt a forgácseltávolítás után kapott alkatrész felületét nevezzük.
vágási felület a vágó fő vágóéle által a munkadarabon kialakított felületnek nevezzük.
Különbséget kell tenni a vágási sík és az alapsík között is.
vágósík a vágófelületet érintő és a vágóélen áthaladó síkot nevezzük.
Fő sík a vágó hossz- és keresztirányú előtolásával párhuzamos síknak nevezzük. Esztergagépeknél egybeesik a szerszámtartó vízszintes tartófelületével.
4. Vágószögek és rendeltetésük
A vágó munkarészének szögei nagymértékben befolyásolják a vágási folyamat menetét.
A maró megfelelő szögeinek megválasztásával jelentősen megnövelheti a folyamatos működésének időtartamát a tompulásig (tartósság) és az időegységenkénti feldolgozást (perc vagy óra) nagy mennyiség részletek.
A maró szögeinek megválasztásától is függ a maróra ható forgácsolóerő, a szükséges teljesítmény, a megmunkált felület minősége stb.. Éppen ezért minden esztergályosnak alaposan tanulmányoznia kell az egyes élezési szögek rendeltetését. a vágót, és képesek legyenek helyesen kiválasztani a legelőnyösebb értéküket.
A maró szögei (48. ábra) feloszthatók a főszögekre, a maró szögeire a tervben és a fő vágóél dőlésszögére.
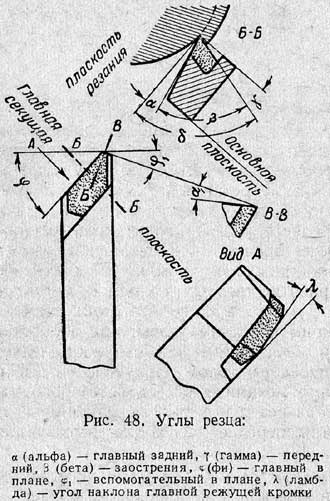
A főbb szögek a következők: hátsó szög, elülső szög és kúpos szög; a vágó szögei a tervben tartalmazzák a fő és a segéd.
A vágó fő szögeit a fő vágási síkban kell mérni, amely merőleges a vágási síkra és a fősíkra.
A vágó munkarésze egy ék (a 48. ábrán árnyékolva), amelynek alakját a maró elülső és fő hátsó felülete közötti szög jellemzi. Ezt a sarkot hívják kúpos szögés a görög β (béta) betűvel jelöljük.
hátszög α ( alfa) a főszárny és a vágási sík közötti szög.
Az α hézagszög a maró hátlapja és a munkadarab közötti súrlódás csökkentését szolgálja. A súrlódás csökkentésével ezáltal csökkentjük a maró felmelegedését, ami emiatt kevésbé kopik. Ha azonban a domborítási szög jelentősen megnő, a metszőfog gyengül és gyorsan megsemmisül.
elülső szög γ ( gamma) a maró elülső felülete és a vágósíkra merőleges sík közötti szög, amely a fő vágóélen keresztül van behúzva.
A γ dőlésszög fontos szerepet játszik a forgácsképzési folyamatban. A dőlésszög növekedésével könnyebben vágható a vágó a fémbe, csökken a vágott réteg deformációja, javul a forgácsáramlás, csökken a forgácsolóerő és az energiafogyasztás, valamint a megmunkált felület minősége javítva van. Másrészt a dőlésszög túlzott megnövekedése a vágóél gyengüléséhez és szilárdságának csökkenéséhez, a vágóél leforgácsolódása miatti maró kopásának növekedéséhez, valamint a hőelvonás romlásához vezet. . Ezért a kemény és törékeny fémek megmunkálásakor a szerszám szilárdságának és tartósságának növelése érdekében kisebb dőlésszögű marókat kell használni; lágy és képlékeny fémek megmunkálásakor nagy dőlésszögű marókat kell használni a forgácseltávolítás megkönnyítésére. A gyakorlatban az elülső szög megválasztása attól is függ, hogy mechanikai tulajdonságok feldolgozandó anyag, a vágó anyagától és az elülső felület alakjától. A keményfém marógépekhez javasolt dőlésszögeket a táblázat tartalmazza. egy.
Tervezési szögek. Vezető szög φ ( fi) a fő vágóél és az előtolás iránya közötti szögnek nevezzük.
A φ szöget általában a 30-90°-os tartományban választják meg a megmunkálás módjától, a maró típusától, a munkadarab és a maró merevségétől és a rögzítés módjától függően. A fémek többségének áteresztő hámozóvágókkal történő megmunkálásakor lehetséges a φ = 45° szög; feldolgozáskor vékony hosszú részek a központokban 60, 75 vagy akár 90 ° szögű vágószerszámokat kell használni, hogy az alkatrészek ne hajoljanak vagy remegjenek.
Segédszög a tervbenφ 1 a másodlagos vágóél és az előtolás iránya közötti szög.

Szög λ ( lambda) a fő vágóél dőlése(49. ábra) a fő vágóél és a maró tetején a fősíkkal párhuzamosan húzott vonal közötti szög.
Asztal 1
A keményfém szerszámokhoz javasolt dőlésszögek és hézagszögek
Jegyzet. A fémek mechanikai tulajdonságait speciális gépeken, műszereken határozzák meg, és minden tulajdonságnak saját jelölést kap. Az ebben és a következő táblázatokban megadott σ b jelölés a fém szakítószilárdságát fejezi ki; ennek a határértéknek az értékét kg/mm2-ben mérik. A HB betűk a fém keménységét jelölik, amelyet a Brinell készüléken úgy határoznak meg, hogy egy edzett acélgolyót a fém felületébe nyomnak. A keménység értékét kg / mm 2 -ben mérik.
Olyan marók, amelyek csúcsa a vágóél legalacsonyabb pontja, azaz λ szög pozitív(49. ábra, c), tartósabbak és ellenállóbbak; ilyen marókkal jó keményfémeket, valamint ütőterhelést okozó szakaszos felületeket megmunkálni. Az ilyen felületek feldolgozásakor keményfém vágógépek a fő vágóél dőlésszöge 20-30°-ra van állítva. Olyan marók, amelyek csúcsa a vágóél legmagasabb pontja, azaz λ szög negatív(49. ábra, a)) lágyfémekből készült alkatrészek megmunkálásához ajánlott használni.
5. A metszőfogak gyártásához használt anyagok
A vágó vágóélein végzett munka során nagy nyomás, valamint magas hőmérséklet (600-800 ° és felette) lép fel. A maró hátsó felületének súrlódása a vágófelületen és a forgács a maró elülső felületén a munkafelületek többé-kevésbé gyors kopását okozza. A kopás miatt a vágórész alakja megváltozik, és a vágó egy idő után használhatatlanná válik a további munkákhoz; az ilyen vágót ki kell venni a gépből és újra kell élezni. Az újraköszörülés nélküli szerszám élettartamának növeléséhez szükséges, hogy az anyag jól ellenálljon a magas hőmérsékleten történő kopásnak. Ezenkívül a vágó anyagának elég erősnek kell lennie ahhoz, hogy ellenálljon magas nyomások vágás során keletkezik. Ezért a következő alapvető követelményeket támasztják a marók anyagával szemben - keménység magas hőmérsékleten, jó kopásállóság és szilárdság.
Jelenleg számos szerszámacél és ötvözet létezik, amely megfelel ezeknek a követelményeknek. Ide tartoznak: szén szerszámacélok, gyorsacélok, keményötvözetek és kerámia anyagok.
Karbon szerszámacél. A vágószerszámok gyártásához 0,9-1,4% széntartalmú acélt használnak. Edzés és temperálás után az ebből az acélból készült vágószerszám nagy keménységet kap. Ha azonban a vágási folyamat során a vágóél hőmérséklete eléri a 200-250 ° -ot, az acél keménysége meredeken csökken.
Emiatt a szén-szerszámacél jelenleg korlátozottan használható: olyan forgácsolószerszámokat készítenek belőle, amelyek viszonylag kis forgácsolási sebességgel működnek, amikor a vágási zóna hőmérséklete kis értéket ér el. Ilyen szerszámok a következők: matricák, dörzsárak, menetfúrók, reszelők, kaparók stb. A vágószerszámok jelenleg nem szénacélból készülnek.
Gyorsacélok. A gyorsacélok tartalmaznak nagyszámú speciális, úgynevezett ötvöző elemek - wolfram, króm, vanádium és kobalt, amelyek magas vágási tulajdonságokat adnak az acélnak - képesek megőrizni a keménységet és a kopásállóságot, amikor a vágás során 600-700 ° -ra hevítik. A HSS marók 2-3-szor nagyobb vágási sebességet tesznek lehetővé, mint a szénvágóké.
Jelenleg a következő típusú gyorsacélt (GOST 9373-60) gyártják a Szovjetunióban: R18, R9, R9F5, R14F14, R18F2, R9K5, R9KYU, R10K5F5 és R18K5F2.
A teljes egészében gyorsacélból készült marók drágák, ezért a gyorsacél megtakarítása érdekében elsősorban hegesztett lemezes marókat használnak.
Kemény ötvözetek. A keményfém ötvözeteket nagyon nagy keménység és jó kopásállóság jellemzi.
A keményötvözetek lemezek formájában készülnek szénnel kombinált volfrám- és titánporokból. A szén és a wolfram kombinációját ún keményfém, és titánnal, titán-karbiddal. Kötőanyagként kobaltot adnak hozzá. Ezt a porszerű keveréket nagy nyomáson sajtolják, hogy kis lemezeket kapjanak, amelyeket ezután körülbelül 1500 °C-on szinterezünk. A kész lemezek nem igényelnek semmit hőkezelés. A lemezt rézzel forrasztják az anyagból készült vágótartóhoz szénacél vagy állítások és csavarok segítségével rögzítik hozzá (a lemezek mechanikus rögzítése).
A keményötvözetek fő előnye abban rejlik, hogy jól ellenállnak a lehulló forgácsok és a munkadarab által okozott kopásnak, és nem veszítik el vágási tulajdonságaikat még 900-1000 °C-ra melegítve sem. Ezeknek a tulajdonságoknak köszönhetően a keményfém lapkákkal felszerelt marók alkalmasak leginkább megmunkálásra szilárd fémek(kemény acélok, beleértve az edzetteket is) és nem fémes anyagok (üveg, porcelán, műanyagok) 4-6-szor nagyobb vágási sebességgel, mint a nagysebességű marók által megengedett vágási sebesség.
A kemény ötvözetek hátránya a fokozott ridegség.
Jelenleg a Szovjetunióban két keményötvözet-csoportot gyártanak. A főbbek - volfrám(VK2, VKZ, VK4, VK6M, VK6, VK8 és VK8M) és titán-volfrám(T30K4, T15K6, T14K8, T5K10). Ezen csoportok mindegyikének sajátos hatóköre van (2. táblázat).
Minden volfrámötvözet öntöttvas, színesfémek és ötvözeteik, edzett acélok, rozsdamentes acélok és nemfémes anyagok (ebonit, porcelán, üveg stb.) feldolgozására szolgál. Az acélok feldolgozásához a titán-volfrám csoport kemény ötvözeteit használják.
Kerámia anyagok. A közelmúltban a szovjet kohászok olcsó, magas forgácsolási tulajdonságokkal rendelkező anyagokat hoztak létre, amelyek sok esetben helyettesítik a keményötvözeteket. Ezek kerámia anyagok termokorund), lemezek formájában gyártják fehér szín, márványra emlékeztető, amelyeket a keményötvözetekhez hasonlóan vagy a vágótartókra forrasztanak, vagy mechanikusan rögzítenek hozzájuk. Ezek a lemezek nem tartalmaznak olyan drága és ritka elemeket, mint a volfrám, titán stb. Ugyanakkor a kerámia lemezek keményebbek, mint a keményötvözetek, és megtartják keménységüket 1200 °C-ra melegítve, ami lehetővé teszi a fémek vágását velük nagy sebességek vágás.
A kerámia lemezek hátránya az elégtelen viszkozitás. A kerámiabetétes vágószerszámok öntöttvas, bronz, alumíniumötvözetek és lágyacélok megmunkálására vagy félkészítésére használhatók.
6. Vágók élezése és kikészítése
A gyárakban a marók élezése általában központosított módon történik köszörűgépek speciális munkások. De magának az esztergályosnak is tudnia kell élezni és megmunkálni a marókat.
2. táblázat
Egyes keményötvözetfajták tulajdonságai és rendeltetése

A nagy sebességű marók élezése és simítása az alábbi szabályok betartásával történik:
1. A csiszolókorong ne üssön, felülete egyenletes legyen; ha a kör munkafelülete kialakult, akkor azt korrigálni kell.
2. Az élezés során kézidarabot kell használni, és nem szabad súlyon tartani a vágót. A kézidarabot a lehető legközelebb kell felszerelni a csiszolókoronghoz, a kívánt szögben, és megbízhatóan támasztja meg a vágót (50. ábra, a-d).
3. Az élezendő vágót a kör munkafelülete mentén kell mozgatni, különben egyenetlenül kopik.
4. Annak érdekében, hogy ne melegítse túl a vágót, és ezáltal elkerülje a repedések megjelenését, ne nyomja erősen a vágót a körhöz.
5. Az élezést a vágó folyamatos és bőséges vízzel történő hűtésével kell végezni. Nem megengedett a csepegtető hűtés, valamint az erősen felhevített vágógép időszakos vízbe merítése. Ha a folyamatos hűtés nem lehetséges, érdemes száraz élezésre váltani.
6. A gyorsacélból készült marók élezését közepes keménységű, 25-16 szemcseméretű elektrokorund kerekekkel kell elvégezni.
Az élezővágók sorrendjét a következőképpen állítjuk be. Először a fő hátsó felületet élesítik (50. ábra, a). Ezután a kiegészítő hátsó felület (50. ábra, b), majd az elülső felület (50. ábra, c) és végül a tetejének sugara (50. ábra, d).
7. Szigorúan tilos a vágóélek élezése eltávolított védőburkolatú gépeken.
8. Az élezés során feltétlenül viseljen védőszemüveget.
A vágó élezése után apró bevágások, sorja és kockázatok maradnak a vágóéleken. Speciális simítógépeken végzett kikészítéssel küszöbölhetők ki. A simítást manuálisan is végezzük ásványolajjal megnedvesített finomszemcsés fenőkő segítségével. Először a próbakő enyhe mozdulataival a hátsó felületeket, majd az elejét és a felső sugarát állítják be.
Keményfém lapkákkal felszerelt marók élezése és simítása. A keményötvözet lemezekkel ellátott marók élezését zöld szilícium-karbid körökkel ellátott csiszológépeken végzik. Az élezés mind kézzel (50. ábra, a-d), mind a metszőfogak szerszámtartókban történő rögzítésével történik. Ezeknek a maróknak az élezési sorrendje megegyezik a gyorsacélból készült marókéval, azaz először a marót a fő hátlap mentén (50. ábra, a), majd a kiegészítő hátsó felületeken (50. ábra, b) élesítjük. ), majd az elülső felület mentén (50. ábra, c), végül kerekítsük le a metszőfog tetejét (50. ábra, d).
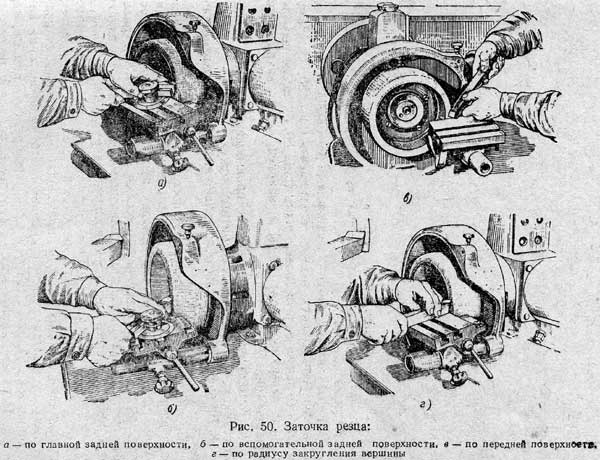
Az előélezést 50-40-es szemcseméretű zöld szilícium-karbid kerekekkel, a végső élezést 25-16-os szemcsefinomsággal végezzük.
A vágót nem szabad erősen a kör munkafelületéhez nyomni, hogy elkerüljük a keményötvözet lemez túlmelegedését és megrepedését. Ezenkívül folyamatosan mozgatni kell a körhöz képest; ez szükséges a kör egyenletes kopásához.
Az élezés szárazon és a vágó bőséges vízzel történő hűtésével is elvégezhető.
A keményfém vágó élezése után feltétlenül ki kell fejezni a felületét. A kikészítés manuálisan vagy simítógépen történik. A kézi simítást öntöttvas vagy rézlappal végezzük, amelynek munkafelületét speciális pasztával dörzsöljük, vagy gépolajjal kevert bór-karbidport vagy kerozint egyenletes rétegben hordunk fel a felületre. A simítást a vágóéltől számított 2-4 mm szélességben végezzük.
Termelékenyebb megmunkálás speciális befejező gépen 250-300 mm átmérőjű, 1,5-2 m / s sebességgel forgó öntöttvas tárcsával; gépolajjal vagy kerozinnal kevert bór-karbid pasztát vagy port alkalmaznak ennek a korongnak a felületére.
7. Forgácsképződés
Forgácsfajták. A levált forgács a vágónyomás hatására nagymértékben megváltoztatja alakját, vagy ahogy mondják, deformálódik: hosszában lerövidül és vastagsága megnő. Ezt a jelenséget először Prof. I. A. Idő és név forgácszsugorodás.
A forgács megjelenése a fém mechanikai tulajdonságaitól és a vágás körülményeitől függ. Ha viszkózus fémeket dolgozunk fel (ólom, ón, réz, lágyacél, alumínium stb.), akkor a forgácsok egyes elemei egymáshoz szorosan tapadva folyamatos forgácsot alkotnak, amely szalaggá tekered (51. ábra, a ). Az ilyen szálat ún csatorna. Kevésbé viszkózus fémek, például keményacél feldolgozásakor az egyes elemekből forgács keletkezik (51. ábra, b), amelyek gyengén kapcsolódnak egymáshoz. Az ilyen szálat ún forgács aprítása.
Ha a megmunkálandó fém rideg, például öntöttvas vagy bronz, akkor a forgácsok egyes elemei eltörnek és elválnak a munkadarabtól és egymástól (51. ábra, c). Egy ilyen chip, amely egyedi mérlegekből áll szabálytalan alakú, nak, nek hívják törött chipek.
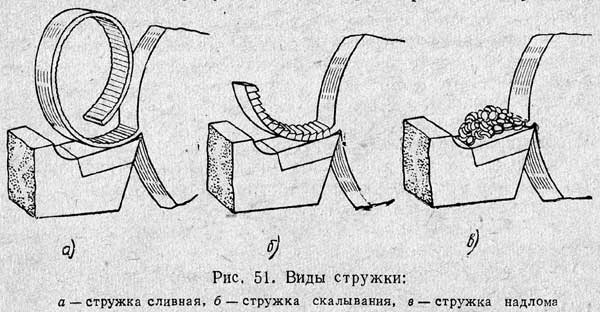
A figyelembe vett forgácstípusok nem maradnak állandóak, a változó forgácsolási körülményekkel változhatnak. Minél lágyabb a megmunkálandó fém, és minél kisebb a forgácsvastagság és a vágási szög, annál jobban megközelíti a forgács alakja a lefolyót. Ugyanez figyelhető meg a vágási sebesség növelésekor és a hűtés alkalmazásakor. A vágási sebesség csökkenésével a leeresztő forgács helyett forgácsot kapunk.
Kinövés. Ha megvizsgáljuk a vágáshoz használt maró elülső felületét, akkor a vágóélen néha egy kis fémcsomót találhatunk, amely magas hőmérsékleten és nyomáson van a maróhoz hegesztett. Ez az ún kinövés(52. ábra). Megjelenik a képlékeny fémek bizonyos forgácsolási körülményei között, de nem figyelhető meg rideg fémek feldolgozása során. A felhalmozódás keménysége 2,5-3-szor nagyobb, mint a feldolgozandó fém keménysége; ennek köszönhetően maga a növekedés képes levágni a fémet, amelyből kialakult.
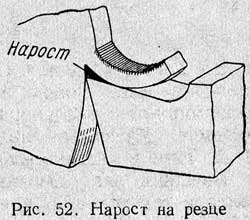
A felhalmozódás pozitív szerepe, hogy befedi a vágópengét, megóvja a leereszkedő forgácsok és a hőhatások által okozott kopástól, és ez némileg növeli a vágó tartósságát. Hámozáskor hasznos a lerakódás jelenléte, mivel a vágópenge kevésbé melegszik fel, és csökken a kopása is. A felrakódások kialakulásával azonban a megmunkált felület pontossága és tisztasága romlik, mivel a felrakódás torzítja a penge alakját. Ezért a felhalmozódás kialakulása kedvezőtlen a befejező munkákhoz.
8. A vágási mód elemeinek fogalma
A feldolgozás minden egyes esetben hatékonyabb elvégzése érdekében az esztergályosnak ismernie kell a vágási mód alapelemeit; ezek az elemek a vágásmélység, az előtolás és a vágási sebesség.
Vágásmélység a megmunkált és megmunkált felületek távolságának nevezzük, az utóbbira merőlegesen mérve. A fogásmélységet t betű jelzi, és milliméterben mérjük (53. ábra).
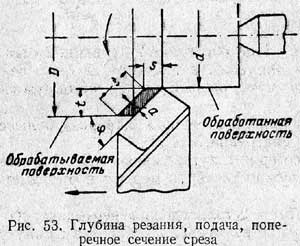
A munkadarab esztergagépen történő esztergálásakor a megmunkálási ráhagyás egy vagy több menetben levágásra kerül.
A t fogásmélység meghatározásához meg kell mérni a munkadarab átmérőjét a maró áthaladása előtt és után, az átmérők különbségének fele megadja a fogásmélységet, más szóval,
ahol D az alkatrész átmérője mm-ben, mielőtt a maró áthaladna; d az alkatrész átmérője mm-ben, miután a maró áthaladt. A marónak a munkadarab egy fordulat alatti mozgását (53. ábra) ún iktatás. Az előtolást s betű jelöli, és milliméterben mérik az alkatrész fordulatszámánként; a rövidség kedvéért mm / fordulatszámot szokás írni. Attól függően, hogy a vágó milyen irányban mozog a keretvezetőkhöz képest, vannak:
a) hosszanti előtolás- az ágyvezetők mentén;
b) kereszttáplálás- merőleges az ágyvezetőkre;
ban ben) ferde takarmány- az ágy vezetőihez képest szögben (például kúpos felület forgatásakor).
Metszeti vágási terület f betűvel (eff) jelöljük, és az előtolás fogásmélységének szorzataként definiáljuk (lásd 53. ábra):
A vágási és előtolási mélység mellett megkülönböztetik a vágott réteg szélességét és vastagságát is (53. ábra).
Vágási réteg szélessége, vagy forgácsszélesség, - a megmunkált és megmunkált felületek távolsága, a vágási felület mentén mérve. Mérése milliméterben történik, és b (be) betűvel jelöljük.
Vágási vastagság, vagy forgácsvastagság, a forgácsolóél két egymást követő helyzete közötti távolság az alkatrész egy fordulatában, a forgácsszélességre merőlegesen mérve. A forgácsvastagságot milliméterben mérik, és a betűvel jelölik.
Azonos előtolás és fogásmélység mellett a φ főszög csökkenésével a forgácsvastagság csökken, a szélessége pedig nő. Ez javítja a hőleadást a vágóélről és növeli a szerszám élettartamát, ami viszont lehetővé teszi a vágási sebesség jelentős növelését és több alkatrész feldolgozását egységnyi idő alatt. A φ terv fő szögének csökkenése azonban a sugárirányú (taszító) erő növekedéséhez vezet, ami a nem kellően merev részek feldolgozásakor hajlítást, pontosságvesztést és erős rezgéseket is okozhat. A rezgések megjelenése pedig a megmunkált felület tisztaságának romlásához vezet, és gyakran a maró vágóélének letöredezését okozza.
Vágási sebesség. Esztergagépen történő megmunkáláskor a D átmérőjű körön elhelyezkedő A pont (54. ábra) az alkatrész egy fordulata alatt ennek a körnek a hosszával megegyező utat tesz meg.
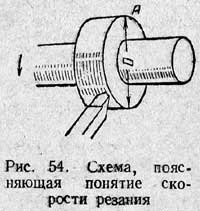
Bármely kör hossza körülbelül 3,14-szerese az átmérőjének, tehát egyenlő 3,14 D-vel.
A 3,14-es számot, amely azt mutatja, hogy a kör hossza hányszor nagyobb, mint az átmérője, általában a görög π (pi) betűvel jelölik.
Az A pont egy fordulat alatt πD-vel egyenlő utat tesz meg. Az alkatrész D átmérőjét, valamint kerületét πD milliméterben mérjük.
Tegyük fel, hogy a munkadarab percenként több fordulatot fog megtenni. Jelöljük számukat n fordulat/perc betűvel, vagy rövidítve rpm. Ebben az esetben az A pont által megtett út egyenlő a kerület és a percenkénti fordulatok számának szorzatával, azaz πDn milliméter per perc vagy rövidítve mm / perc, és az ún. kerületi sebesség.
Út, átjárható pont a maró vágóéléhez képest egy perc alatti elforduláskor megmunkálandó felületet ún vágási sebesség.
Mivel az alkatrész átmérőjét általában milliméterben adják meg, a vágási sebesség méter/percben kifejezett meghatározásához πDn-t el kell osztani 1000-el. Ez a következő képlettel írható fel:
ahol v a vágási sebesség m/percben;
D a munkadarab átmérője mm-ben;
n a percenkénti fordulatok száma.
3. példa Megmunkált görgő átmérője D = 100 = 150 ford./perc. Határozza meg a vágási sebességet.
Döntés: Orsó fordulatszám számlálás. Ismert átmérőjű alkatrész esztergálásakor előfordulhat, hogy egy esztergagépnek ilyen számú orsófordulatra kell beállítania a gépet a kívánt forgácsolási sebesség elérése érdekében. Ehhez a következő képletet használják: ahol D a munkadarab átmérője mm-ben;
4. példa Hány fordulatszámot kell percenként egy D \u003d 50 mm átmérőjű görgőnek v \u003d 25 m / perc vágási sebesség mellett?
Döntés:
9. Alapvető tudnivalók a maróra ható erőkről és a vágóerőről
A vágóra ható erők. Amikor eltávolítja a forgácsot a munkadarabról, a vágónak le kell győznie a fémrészecskék egymáshoz tapadásának erejét. Amikor a maró vágóéle belevág a megmunkálás alatt álló anyagba, és a forgácsot leválasztják, a maró nyomást gyakorol a leválasztandó fémre (55. ábra).

Felülről lefelé a P z erő rányomja a marót, ami hajlamos lenyomni a marót és felhajlítani az alkatrészt. Ezt az erőt ún vágóerő.
Vízszintes síkban az előtolási mozgással ellentétes irányban a marót P x erő nyomja, ún axiális erő, vagy tápláló erő. Ez az erő a hosszirányú esztergálás során a vágót a farokrész felé nyomja.
A vízszintes síkban, az előtolás irányára merőlegesen a marót a P y erő nyomja, amit radiális erőnek nevezünk. Ez az erő arra törekszik, hogy a marót eltolja a munkadarabtól és vízszintes irányba hajlítsa.
Az összes felsorolt erőt kilogrammban mérik.
A három erő közül a legnagyobb a függőleges forgácsolóerő: körülbelül 4-szerese az előtolási erőnek és 2,5-szerese a radiális erőnek. A vágóerő megterheli a támasztószerkezet alkatrészeit; a vágót, alkatrészt is terheli, sokszor nagy feszültségeket okozva bennük.
Kísérletek során bebizonyosodott, hogy a forgácsolóerő függ a megmunkálandó anyag tulajdonságaitól, az eltávolítandó forgácsszakasz méretétől és alakjától, a vágó alakjától, a vágási sebességtől és a hűtéstől.
Az ellenállás jellemzésére különféle anyagok vágás létrehozta a vágási együttható fogalmát. A K vágási tényező a vágási nyomás kilogramm/négyzetmilliméterben a vágott szakaszon, bizonyos vágási körülmények között mérve:
Vágásmélység t......................5 mm
Előtolás s......................1 mm/ford
A dőlésszög γ................................15°
Vezetési szög φ.......45°
A vágó éle egyenes, vízszintes
A vágó hegye r = 1 mm sugárral lekerekített
A munka hűtés nélkül történik
táblázatban. A 3. ábra egyes fémek forgácsolási tényezőjének átlagos értékeit mutatja.
3. táblázat
A K vágási tényező átlagértékei esztergáláskor
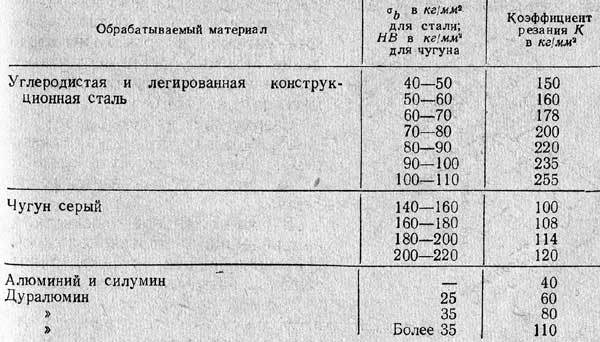
Ha ismert a K forgácsolási tényező, akkor ezt megszorozva az f vágás keresztmetszeti területével mm 2 -ben, a képlet segítségével megkaphatja a forgácsolóerő hozzávetőleges értékét.
P z \u003d Kf kg. (nyolc)
5. példa Esztergagépen egy gépi acélból készült tengelyt forgatunk, amelynek σ b = 60 kg / mm 2. Határozza meg a forgácsolóerőt, ha a fogásmélység t = 5 mm és az előtolás s = 0,5 mm/ford.
Döntés. A (8) képlet szerint vágóerő P z \u003d Kf kg. (nyolc) Meghatározzuk f értékét: f \u003d ts \u003d 5x0,5 \u003d 2,5 mm 2. táblázat szerint A 3. ábrán megtaláljuk a K értékét gépi acélnál, amelynek σ b \u003d 60 kg / mm 2: K = 160 kg / mm 2. Ezért z = Kf = 160x2,5 = 400 kg. vágóerő. A vágási erő és vágási sebesség ismeretében megtudhatja, mekkora teljesítmény szükséges egy adott szakasz forgácsának vágásához.
A vágási teljesítményt a képlet határozza meg (9) ahol N res – vágási teljesítmény LE-ben;
P z - vágóerő kg-ban;
v - vágási sebesség m/percben.
A szerszámgép villanymotorjának teljesítményének valamivel nagyobbnak kell lennie, mint a vágóteljesítménynek, mivel az elektromos motor erejének egy részét a súrlódás leküzdésére fordítják azokban a mechanizmusokban, amelyek az elektromos motorról a gép orsójára továbbítják a mozgást.
6. példa Határozza meg az előző példában figyelembe vett tengely forgatásához szükséges forgácsolási teljesítményt, ha a feldolgozást υ = 60 m/min forgácsolási sebességgel végezzük. határozat . A (9) képlet szerint vágási teljesítmény
A vágási teljesítményt általában nem lóerőben, hanem kilowattban (kW) fejezik ki. A kilowatt 1,36-szoros lóerő, tehát a teljesítmény kilowattban történő kifejezéséhez el kell osztani a lóerőt 1,36-tal:
és fordítva,
10. Vágási hő és a szerszám élettartama
A forgácsolóerő növekedésével a súrlódási erő növekszik, aminek következtében megnő a vágási folyamat során felszabaduló hőmennyiség. A vágási hő a vágási sebesség növekedésével még jobban megnő, mivel ez felgyorsítja a forgácsképződés teljes folyamatát.
Az elégtelen eltávolítása esetén keletkező vágáshő meglágyítja a marót, aminek következtében a vágórészének kopása intenzívebben következik be. Emiatt ki kell cserélni a vágót, vagy meg kell élezni és vissza kell szerelni.
A maró tompítás előtti folyamatos munkájának idejét szerszámélettartamnak nevezzük (percben mérve). A maró gyakori cseréje (a szerszám rövid élettartama) oka további kiadások a vágó élezéséhez és beszereléséhez, valamint az elhasználódott marók utánpótlásához.
Ezért a szerszám élettartama az fontos tényező a vágási feltételek megválasztásakor, különösen a vágási sebesség kiválasztásakor.
A vágó tartóssága elsősorban az anyag minőségétől függ, amelyből készült. A legellenállóbb a vágó lesz, amely olyan anyagból készül, amely lehetővé teszi a legmagasabb fűtési hőmérsékletet jelentős keménységveszteség nélkül. A keményötvözet lemezekkel, ásványi-kerámia lapokkal felszerelt marók a legnagyobb ellenállással rendelkeznek; lényegesen kisebb ellenállás - gyorsacélból készült marók, a legkisebbek - karbon szerszámacélból készült marók.
A vágó ellenállása függ a megmunkálandó anyag tulajdonságaitól, a vágási szakasztól, a vágó élezési szögeitől és a vágási sebességtől is. A megmunkálandó anyag keménységének növelése csökkenti a szerszám élettartamát.
Az élezési szögek és az elülső felület alakjának változtatásával a marók tartósságának és termelékenységének jelentős növelése érhető el.
A vágási sebesség különösen erősen befolyásolja a szerszám élettartamát. Néha még a legkisebb sebességnövekedés is a vágó gyors eltompulásához vezet. Például, ha az acél nagy sebességű maróval történő megmunkálásakor a vágási sebességet csak 10%-kal, azaz 1,1-szeresére növelik, akkor a vágószerszám kétszer olyan gyorsan eltompul, és fordítva.
A vágás keresztmetszeti területének növekedésével a szerszám élettartama csökken, de nem annyira, mint a vágási sebesség azonos növekedése esetén.
A szerszám élettartama a szerszám méretétől, a vágási szakasz alakjától és a hűtéstől is függ. Minél masszívabb a vágó, annál jobban távolítja el a hőt a vágóélről, és ennek következtében annál tartósabb.
A kísérletek azt mutatják, hogy ugyanazon vágási szakasz mellett a nagy fogásmélység és a kisebb előtolás nagyobb szerszámélettartamot biztosít, mint a kisebb fogásmélység megfelelően nagyobb előtolással. Ez azzal magyarázható, hogy nagyobb vágásmélység esetén a forgács a vágóél nagyobb hosszával érintkezik, így a vágási hő jobban eltávolítható. Éppen ezért ugyanazzal a vágási résszel kifizetődőbb nagyobb mélységgel dolgozni, mint nagyobb előtolással.
A vágó tartóssága jelentősen megnő, ha lehűtjük.
A hűtőfolyadékot bőségesen kell adagolni (emulzió 10-12 l/perc, olaj és szulfofrezol 3-4 l/perc); egy kis mennyiségű folyadék nemhogy nem tesz jót, de még meg is rontja a vágót, aminek következtében apró repedések jelennek meg a felületén, ami csorbuláshoz vezet.
11. Vágási sebesség kiválasztása
A munka termelékenysége a vágási sebesség megválasztásától függ: minél nagyobb a vágási sebesség, az kevesebb idő feldolgozásra költött. A vágási sebesség növekedésével azonban a szerszám élettartama csökken, ezért a vágási sebesség megválasztását befolyásolja a szerszám élettartama és minden olyan tényező, amely befolyásolja a szerszám élettartamát. Ezek közül a legfontosabbak a megmunkálandó anyag tulajdonságai, a maró anyagának minősége, a fogásmélység, az előtolás, a maró méretei és az élezési szögek, valamint a hűtés.
1. Minél hosszabb a szerszám élettartama, annál kisebb vágási sebességet kell választani, és fordítva.
2. Minél keményebb a megmunkálandó anyag, annál kisebb a szerszám élettartama, ezért a kemény anyagok megmunkálásakor a szükséges ellenállás biztosításához csökkenteni kell a forgácsolási sebességet. Öntött és kovácsolt munkadarabok megmunkálásakor, amelyek felületén kemény kéreg, héjak vagy pikkely található, a forgácsolási sebességet csökkenteni kell a kéreg nélküli anyagok megmunkálásakor lehetségeshez képest.
3. A maró anyagtulajdonságai meghatározzák a tartósságát, ezért a vágási sebesség megválasztása is ezektől a tulajdonságoktól függ. Ha egyéb dolgok nem változnak, a nagysebességű acélvágók lényegesen nagyobb vágási sebességet tesznek lehetővé, mint a szénacél marók; a még nagyobb vágási sebesség lehetővé teszi a kemény ötvözetekkel felszerelt marókat.
4. A vágó ellenállásának növelése érdekében viszkózus fémek megmunkálásánál előnyös a marók hűtése. Ilyenkor azonos szerszámélettartam mellett 15-25%-kal lehet növelni a forgácsolási sebességet a hűtés nélküli megmunkáláshoz képest.
5. A maró méretei és élezési szögei is befolyásolják a megengedett vágási sebességet: minél masszívabb a vágó, különösen a feje, annál jobban elvezeti a vágás során keletkező hőt. A rosszul megválasztott vágószögek, amelyek nem felelnek meg a megmunkált anyagnak, növelik a vágóerőt és hozzájárulnak a vágó gyorsabb kopásához.
6. A vágási szakasz növekedésével a szerszám élettartama csökken, ezért nagyobb metszetnél kisebb vágási sebességet kell választani, mint kisebb szakasznál.
Mivel a simítás során kis forgácsot távolítanak el, a simítás során a vágási sebesség sokkal nagyobb lehet, mint a nagyolásnál.
Mivel a vágási szakasz növelése kevésbé befolyásolja a szerszám élettartamát, mint a vágási sebesség növelése, a vágási sebesség enyhe csökkenése miatt előnyös a vágási szakasz növelése. A Kuibisev Szerszámgépgyár V. Koleszov újító esztergályos feldolgozási módszere ezen az elven alapul. A 150 m/perc forgácsolási sebességgel dolgozó T. Kolesov acél alkatrészeket 0,3 mm/fordulat helyett akár 3 mm/ford előtolási sebességgel fejezi be, és ez a gépi idő 8-10-szeres csökkenéséhez vezet.
Felmerül a kérdés: miért növelik a fejlett esztergák gyakran a munka termelékenységét a vágási sebesség növelésével? Ez nem mond ellent a vágás alaptörvényeinek? Nem, ez nem mond ellent. Csak olyan esetekben növelik a vágási sebességet, amikor a vágási szakasz növelésének lehetőségeit teljes mértékben kihasználják.
Félsimítás vagy simítás során, ahol a fogásmélységet egy kis megmunkálási ráhagyás korlátozza, és az előtolást a nagy megmunkálási tisztaság követelményei korlátozzák, a forgácsolási mód növelése a vágási sebesség növelésével lehetséges. . Ezt teszik a haladó esztergályosok, akik fél- és simításon dolgoznak. Ha lehet vele dolgozni nagy szakaszok vágás (nagy ráhagyással), akkor mindenekelőtt a lehető legnagyobb fogásmélységet, majd a lehető legnagyobb technológiailag megengedett előtolást és végül a megfelelő vágási sebességet kell kiválasztani.
Azokban az esetekben, amikor a megmunkálási ráhagyás kicsi, és nincs speciális felületi követelmény, a forgácsolási módot a lehető legnagyobb előtolás alkalmazásával kell növelni.
12. A megmunkált felület tisztasága
Maróval történő megmunkáláskor az alkatrész megmunkált felületén a leggondosabb megmunkálás mellett is mindig maradnak egyenetlenségek bemélyedések, kagylók formájában. Az érdesség magassága a feldolgozási módtól függ.
A gyakorlat bebizonyította, hogy minél tisztábban kezelik az alkatrész felületét, annál kevésbé van kitéve a kopásnak, korróziónak, és annál erősebb az alkatrész.
A gondos felületkezelés egy alkatrész megmunkálásakor mindig drágább, mint a durva felületkezelés. Ezért a megmunkált felület tisztaságát az alkatrész üzemi körülményeitől függően kell hozzárendelni.
Felületi tisztaság jelölése rajzokon. A GOST 2789-59 szerint 14 felületi tisztasági osztályt biztosítanak. Az összes tisztasági osztály megjelölésére egy jelet hoznak létre - egy egyenlő oldalú háromszöget, amely mellett az osztályszám szerepel (például 7; 8; 14). A legtisztább felületek 14-es, a legdurvábbak pedig 1-es fokozatúak.
A GOST 2789-59 szerinti felületi érdességet két paraméter egyike határozza meg: a) az R a profil számtani átlagos eltérése és b) az R z egyenetlenségek magassága.
Az érdesség mérésére és a kezelt felület egy adott osztályhoz rendeléséhez speciális mérőműszerek a felületi profil vékony gyémánttűvel történő tapintásának módszere alapján. Az ilyen eszközöket profilométereknek és profilográfoknak nevezik.
Az érdesség meghatározásához és a kezelt felület besorolásához egy vagy másik tisztasági osztályba műhelyi körülmények között különböző tisztasági osztályok tesztelt mintáit használják - az úgynevezett tisztasági szabványokat, amelyekkel összehasonlítják az alkatrész megmunkált felületét.
A felületkezelést befolyásoló tényezők. A gyakorlatban bebizonyosodott, hogy a megmunkált felület tisztasága számos októl függ: a megmunkált anyagtól, a maró anyagától, az élezési szögektől és a maró vágóéleinek állapotától, az előtolástól és a vágási sebességtől. , a folyadék kenési és hűtési tulajdonságai, a rendszer gép - vágó - alkatrész merevsége stb.
Különösen fontosságát felületet szerezni Jó minőség esztergálásnál van vágási sebessége, előtolása, vezetési szögei és a szerszám hegyének görbületi sugara. Minél kisebb az előtolás és a belépési szög, és minél nagyobb a saroksugár, annál tisztább a megmunkált felület. A vágási sebesség nagymértékben befolyásolja a felület minőségét. Acél 100 m/perc-nél nagyobb forgácsolási sebességgel történő esztergálásakor a megmunkált felület tisztább, mint 25-30 m/perc sebességnél.
A tisztább megmunkált felület elérése érdekében ügyelni kell a vágóélek gondos élezésére és befejezésére.
tesztkérdések 1. Milyen alakú a forgács viszkózus fémek megmunkálásakor? Törékeny fémek feldolgozásakor?
2. Nevezze meg a metszőfogfej fő elemeit!
3. Mutasd meg a metszőfog elülső és hátsó felületét; első és hátsó sarkok; élezési szög.
4. Mi a célja a metszőfog első és hátsó sarkának?
5. Az elvezetési szögek és az elvezetési szögek megjelenítése.
6. Milyen anyagokból készülnek a vágók?
7. Milyen minőségű keményötvözeteket használnak az acélfeldolgozásban? Öntöttvas feldolgozásakor?
8. Sorolja fel a vágási mód elemeit!
9. Milyen erők hatnak a vágóra?
10. Milyen tényezők és hogyan befolyásolják a vágóerő nagyságát?
11. Mi határozza meg a vágó tartósságát?
12. Milyen tényezők befolyásolják a vágási sebesség megválasztását?
Az eljárás során használt fő forgácsolószerszámok közé tartozik a maró, amelynek geometriai paraméterei határozzák meg műszaki képességeit, pontosságát és feldolgozási hatékonyságát. Bármely szakember, aki úgy dönt, hogy rászánja magát forgó üzlet, Amennyiben jó választás A vágóélszögek növelik a szerszám élettartamát és a termelékenységet.
Esztergaszerszámok paraméterei
Bármi esztergaszerszám képezzen egy tartót, amely a szerszám rögzítéséhez szükséges a tartóban esztergapad, és fémvágást biztosító munkafej. Az esztergaszerszám geometriai paramétereinek figyelembevételéhez jobb, ha egy átmenő szerszámot veszünk mintaként.
Az esztergaszerszám vágórészén ebből a típusból három felület van:
- elülső (a munkadarab feldolgozása során fémforgácsok válnak le róla);
- hátsó - fő és segéd (mindkettő elülső részével a munkadarabhoz fordult).
A szerszám éle, az úgynevezett vágóél (és közvetlenül részt vesz a feldolgozásban), az elülső és a fő hátsó felületek metszéspontjából alakul ki. Az esztergaszerszám geometriájában egy segédvágóél is megkülönböztethető. Ez rendre az elülső felület és a kiegészítő hátlap metszéspontjából jön létre.
Azt a pontot, ahol a fő és a másodlagos vágóél metszik, a maró csúcsának nevezzük. Ez utóbbi a fém vágásakor hatalmas terhelést szenved, ami annak töréséhez vezet. A vágócsúcs ellenállásának növelése érdekében az élezési folyamat során nem élesítik, hanem kissé lekerekítik. Ehhez egy olyan paraméter bevezetésére van szükség, mint például a csúcssugár. Van egy másik módja az esztergaszerszám csúcsának ellenállásának növelésére - egy egyenes vonalú átmeneti vágóél kialakítása.
Az esztergáláshoz használt marók legfontosabb geometriai paraméterei a szögeik, amelyek meghatározzák kölcsönös megegyezés szerszámfelületek. A szögparaméterek az esztergaszerszám típusától és számos egyéb tényezőtől függően változnak:
- szerszám anyaga;
- munkakörülményei;
- a feldolgozandó anyag jellemzői.
Szerszámszögek esztergáláshoz
A szögek helyes meghatározásához esztergaszerszám, őket pontos értékeket, ezeket az úgynevezett kezdeti síkokban veszik figyelembe.
- A fősík párhuzamos az esztergaszerszám előtolási irányaival (hosszirányú és keresztirányú), és egybeesik a tartófelületével.
- A forgácsolási sík tartalmazza a fő vágóélt, és érintőlegesen érinti a megmunkálási felületet. Ez a sík merőleges a fő síkra.
- A fő vágósík metszi a fő vágóélt, és merőlegesen helyezkedik el arra a vetületre, amelyet ez az él a fősíkon fekszik. Létezik egy segédmetsző típusú sík is, amely ennek megfelelően merőleges a segédvágóél által a fősíkra lerakott vetületre.
Mint fentebb említettük, pontosan ezekben a síkokban mérik, és azokat, amelyeket a fő szekánsnak nevezett síkban mérnek, főként jelölik ki. Ezek különösen a fő első, a fő hátsó szögek, valamint az élezés és a vágás szögei.
Az egyik legfontosabb az esztergaszerszám fő hézagszöge, amely minimálisra csökkenti a súrlódást, amely akkor keletkezik, amikor a szerszám hátsó felülete kölcsönhatásba lép az éppen megmunkált alkatrészsel (és ezáltal csökkenti a szerszám felmelegedését és meghosszabbítja az élettartamát ). Ezt a szöget a vágófelület (fő hátsó) és a vágási sík alkotja. A szerszám élezésekor ennek a szögnek a kiválasztásakor figyelembe veszik a megmunkálás típusát és a munkadarab anyagát. Ebben az esetben tudnia kell, hogy a hézagszög nagyságának erős növekedése az esztergaszerszám gyors meghibásodásához vezet.
A vágószerszám szilárdságát és tartósságát, a feldolgozás során fellépő erőket a dőlésszög paraméterei határozzák meg. Az esztergaszerszám elülső felülete és az a sík között helyezkedik el, amelyben a fő vágóél található (ez a sík merőleges a vágósíkra). Az esztergaszerszám élezésekor számos olyan tényezőt veszünk figyelembe, amelyek befolyásolják ennek a szögnek az értékét:
- a munkadarab anyaga és maga a szerszám;
- az elülső felület alakja;
- feltételek, amelyek mellett a vágót használni fogják.
A dőlésszög értékének növekedése egyrészt javítja a feldolgozás minőségét, másrészt az esztergaszerszám szilárdságának és tartósságának csökkenését idézi elő. Az élezés eredményeként kapott ilyen szögnek pozitív és negatív jelentése.
A negatív értékű dőlésszögű esztergavágók rendkívül tartósak, de az ilyen szerszámokkal történő megmunkálás nehézkes. Általában a pozitív értékű dőlésszöggel történő élezést akkor alkalmazzák, ha a munkadarabot viszkózus anyagból kell megmunkálni, és akkor is, ha a szerszám anyaga nagyon tartós.
A negatív hajlítási szögű marókat nagy keménységű és szilárdságú anyagok megmunkálásakor, megszakított forgácsolásakor alkalmazzák, amikor a szerszám anyagának nincs megfelelő hajlítószilárdsága és nem veszi fel jól az ütési terhelést.
Az esztergáláshoz használt maró geometriáját jellemző paraméterek a vágási és a mutatószögek is. A vágási szög, amelynek értéke 60-100 0 között változhat, a szerszám felülete, az úgynevezett front és a vágási sík között helyezkedik el.
Ennek a szögnek az értéke közvetlenül függ a feldolgozandó fém keménységétől: minél nagyobb, annál nagyobb az értéke. A kúpos szög teljes mértékben megfelel a nevének, a szerszám fő elülső és fő hátulsó felülete között mérik, és jellemzi a tetejének élezési fokát.
Jellemezze az esztergaszerszámot és a szögeket a tervben! Ez a fő, a hosszirányú előtolás iránya és a fő vágóél fősíkra eső vetülete között mérve, valamint a segédvágóél fősíkra való vetülete és a vágóél iránya által alkotott segéd. a hosszanti előtolás.
Élezéskor ezeket a szögeket nem önkényesen választják meg, hanem az esztergálás típusától és a „szerszámgép-munkadarab” rendszer merevségétől függően. Tehát a legtöbb fém megmunkálása elvégezhető olyan szerszámokkal, amelyek főszöge a tervben 45 0, de a vékony és hosszú munkadarabokat maróval kell megmunkálni, ahol ennek a szögnek az értéke a 60-os tartományban van. 90 0 . Erre azért van szükség, hogy kiküszöböljük az alkatrész elhajlását és remegését.
A vezetés segédszöge egyidejűleg korrelál a megmunkálás befejezésével és a szerszám élettartamával. Csökkenésével nő a feldolgozás tisztasága és nő a szerszám élettartama.
Az esztergaszerszámok geometriájában a fent tárgyaltakon kívül megkülönböztetnek szögeket.
A hosszanti esztergálást esztergálásnak nevezzük, melynél az előtolás mozgási iránya párhuzamos a munkadarab tengelyével. Esztergagépeken a forgácsoló mozgás - forgás - a munkadarabhoz, az előtolás - transzlációs mozgás - a maróhoz van rögzítve. A körpálcás gépeken a vágószerszám forog, és az előtoló mozgás a munkadarabhoz kapcsolódik. A valódi vágási útvonal egy csavarvonal.
Tegyen különbséget a finom és durva esztergálás között.
A finom esztergálást (2. ábra, a) lapos munkafelületű és egyenes vágóélekkel rendelkező maróval végezzük - a fő és a kiegészítő. A forgácsolóélek helyzetét a munkadarab forgástengelyéhez viszonyítva a vezetőben lévő főszög és a vezetőben lévő segédszög jellemzi. A segédszög értéke a tervben meghatározza a kinematikai egyenetlenségek mélységét, így nem lehet nagyobb. A fő vágóélt alkotó lapok helyzetét a hézagszög, az élezési szög és az elülső szög jellemzi.
A fő vágóél keresztirányú vágást eredményez, amelyet a farostok dőlésszöge jellemez.
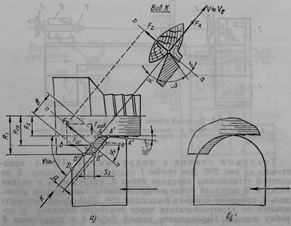
Rizs. 2. Hosszirányú esztergálás simítás (a) és nagyolás (b)
A dőlésszöget a szálak iránya és a normál között mérik.
A durva esztergálást (2. ábra, b) félkör alakú vágóélű hornyos marókkal végezzük. Keresztmetszet a forgácsok félhold alakúak, a forgács vastagsága a munkadarab perifériáján maximális, az alkatrész felülete közelében még a maró nagy előtolása esetén is jelentéktelen. Ez lehetővé teszi, hogy marónként legfeljebb 2 mm-t, finom esztergálásnál pedig legfeljebb 0,8 mm-t alkalmazzon.
> Esztergagépek beállítása
Az esztergagépek beállításánál szükséges: egy marószerszám kiválasztása és a szerszámtartóban rögzítése (mechanikus előtolású gépeknél); szereljen fel előlapot vagy tokmányt; válassza ki és rögzítse a kéztámaszt (olyan gépeknél, amelyek kézi adagolás) vagy másolóvonalzót (mechanikus adagolású gépekhez); telepítse és rögzítse a munkadarabot a gépben; tesztelje a gépet alapjáraton; állítsa be az orsó fordulatszámát és előtolási sebességét; dolgozza fel és ellenőrizze a próbadarabokat.
A szükséges vágót az elvégzett munka jellegétől függően választják ki. A kezdeti nagyoláshoz hámozó vágót, az utolsóhoz egy egyenes vágóélű befejező marót használunk. Mechanikus előtolásnál a vágót csavarokkal rögzítik a szerszámtartóba. Az átállási idő csökkentése érdekében speciális forgófejeket használnak, ahol egyszerre több különböző célú metszőfogat erősítenek meg.
Nál nél kézi munka ellenőrizni kell a vágó fa fogantyúhoz való rögzítésének megbízhatóságát. Ne használjon hibás vágószerszámot.
A munkadarab rögzítésének módjait annak alakjától és méretétől függően választják ki. Hosszú munkadarabok rögzítéséhez (3. ábra, a) az elülső és a hátsó középpontokat használják. Az elülső középső 2 háromágú, elkeskenyedő szárú póráz formájában készül, amellyel az 1 orsó kúpos furatába kerül. A hátsó 4 középrésznek kúpos és hegyes része van, és a tollba van rögzítve. A súrlódás csökkentése és a munkadarab rögzítésének megbízhatóságának növelése érdekében a hátsó középpont csapágyra van felszerelve, amely biztosítja annak forgását a 3 munkadarabbal.

Rizs. 3. A munkadarab rögzítése esztergagépekben: a - a központokban, b - a tokmányban, c - az előlapon; 1 - orsó, 2 - első középső, 3 - munkadarab, 4 - hátsó középső, 5 - toll, 6 - farokszár, 7 - tokmány, 8 - terv
A megmunkálandó munkadarab hosszától függően a faroktámaszt az ágy vezetői mentén mozgatják és egy előre meghatározott helyzetben rögzítik. A munkadarab rögzítése úgy történik, hogy a tolltollat ki kell nyomni a fejtartóból, amíg a középpontok be nem ágyazódnak a munkadarab végeibe, és biztonságosan tartják azt forgás közben. A kúpos alkatrészek esztergálásához a faroktestet keresztirányban kell mozgatni egy beállító csavarral, és rögzíteni kell egy reteszelő szerkezettel. A tokmányokat rövid munkadarabok rögzítésére tervezték (3. ábra, b). A 7-es tokmánynak van egy menete, amelyen keresztül az orsóra van csavarozva. A munkadarabot úgy rögzítjük a tokmányban, hogy a végét szorosan beillesztjük a tokmány furatába. Befogótokmányok és csúszópofás tokmányok is használatosak.
Rövid hosszúságú munkadarabok befogására és nagy átmérőjű előlapként szolgálnak 8 (3. ábra, c), az orsóra csavarozva. A munkadarabot csavarokkal vagy csavarokkal 9 rögzítik az előlaphoz.
A kézidarabot úgy kell a keretre felszerelni, hogy a munkaéle a középpontok szintjén legyen, és a megmunkálás alatt álló munkadarab generátorához közel legyen, de ne érjen hozzá. Az átmérő csökkenésével és hosszú munkadarabok megmunkálásakor a kézidarab egymás után átrendeződik egy új pozícióba az ágyvezetők mentén. Az ágy hátsó oldalán formázott termékek feldolgozásakor a konzolokra egy másolóvonalzót rögzítenek, amelynek alakja hasonló a kész alkatrész formájához. Az előtolás bekapcsolásakor a féknyereg ívelt pályán mozog, és a maró az alkatrész adott alakját reprodukálja.
Az orsó fordulatszámát a munkadarab átmérőjétől és szilárdságától függően választjuk meg. Nagyobb átmérők esetén a minimális orsófordulatszámot kell beállítani. 400 mm átmérőjű előlap felszerelésekor az orsó fordulatszáma nem haladhatja meg a 800 ford./perc értéket. A fordulatszámot csökkenti a fogantyú pár fokozat kapcsolásához vagy a többsebességes villanymotor fordulatszámának változtatása. vágási sebesség fához puha sziklák 10 ... 12 m / s-nak kell lennie, szilárd - 0,5 ... 3 m / s.
A hosszirányú előtolás orsófordulatonként legyen: nagyolásnál 1,6 ... 2 mm, simításnál - legfeljebb 0,8 mm. Minél magasabb a felületi érdesség követelménye, annál kisebbnek kell lennie a hosszirányú előtolásnak. Az orsófordulatonkénti keresztelőtolás nem haladhatja meg az 1,2 mm-t. A gép elindítása előtt győződjön meg arról megbízható rögzítés nyersdarabokat és szereljen fel egy kerítést.
Az alkatrész nagyolása után a marószerszámot kicserélik, és kis előtolás mellett finomesztergálást végeznek. A forgácsnak ebben az esetben a lehető legfolyékonyabbnak és egyenletes vastagságúnak kell lennie.
A feldolgozás során az alkatrész formáját időszakonként egy sablon vagy mérőeszköz szabályozza. Kaliber használatakor ill mérőeszköz mérleggel a gépet kikapcsolják és csak az alkatrész teljes leállása után mérik le.
A beállítás végeztével az alkatrész próbafeldolgozása megtörténik, és a méreteit kaliberrel vagy skálás mérőeszközzel ellenőrizzük.