Настройка на детайла - завъртане. Захващане в центрове при завъртане на детайли
Технология на производство на детайли на струг. |
Производството на всяка част започва с избора на материал. Избраният материал се нарязва на заготовки. Размерът на детайла винаги надвишава размерите на готовата част с определено количество (припуск). Размерът и формата на надбавката зависят от формата на детайла, технологията на неговото производство. |
Дървесината с еднаква текстура е най-подходяща за струговане. Това са бреза, липа, трепетлика, бук, бряст, орех. Завъртане на части на централни машини
|
Ориз. 1. Последователност на завъртане на детайла а - фиксиране на детайла; b - фиксиране на разреза на детайла; в- груба обработка с райер; g - завършване с Meisel; e- подрязване (облицовка) на детайла. Завъртане на вътрешни кухини За струговане на вътрешни повърхности детайлът се фиксира само в главната баба на машината с гърбичен патронник, лицева плоча или тръбен патронник.
|
|
Ориз. 2. Кухо струговане а - на лицевата плоча; b- в тръбен патрон. Работете на стругове с шублер На стругове с шублер обработката се извършва с фрези, фиксирани в държач за инструменти, монтиран върху подвижен шублер на машината. Такива машини като правило имат ръчно и механично подаване по протежение на и напречно на машината. Стругащи фрези. Според формата на главата резците се делят на прави с прав прът (фиг. 3 а) и огънати с пръчката, извита надясно или наляво. Според местоположението на режещия ръб се разграничават десни (фиг. 3г) и леви (фиг. 3в) резци. Десните се движат в надлъжна посока от задната баба към предната част, левите отпред към задната. Проходните фрези (фиг. 3 а-в) са предназначени за струговане, скосяване, през упорни фрези (фиг. 3 г) за струговане и обработка на оформения край на стъпалото. Режещи фрези (фиг. 3 д) служат за оформяне на стъпало в края на обработвания детайл, за обработка на равнината на края. Жлебове на външната и вътрешна повърхностдетайлите могат да бъдат получени с помощта на фрези за жлебове (фиг. 3 е, з). За рязане се използват режещи фрези (фиг. 3 g). За нарязване на резба се използва резбова резба (фиг. 3i). Оформените фрези се заточват според формата на детайла (фиг. 3 к). |
![]() |
Ориз. 3. Основни видове стругарски инструменти Фрезите са настроени така, че горната част на фрезата да съвпада с центъра на задната баба. Скоростта на шпиндела трябва да бъде 1200 rpm. Обработване на цилиндрични заготовки. |
|
Ориз. 4. Техники за обработка на цилиндрични заготовки Фрезата се подава постепенно напред, докато докосне въртящия се детайл и в това положение се прибира надясно. Резачката се подава напред 2-3 мм по лимба и първият работен проход се прави по протежение на детайла. Пасажите се извършват до получаване на гладка цилиндрична форма (фиг. 4 а). След като преместите фреза според показанията на диска за напречно подаване до желания размер, се завърта малка тестова зона. Ако измерването показа, че фрезата е настроена на желания размер, тогава повърхността се обработва по цялата дължина от дясно на ляво (фиг. 4 б). След завъртане ножът се прибира. И се връщат в първоначалното си положение. Същият нож изрязва края и первазите. Крайната повърхност се изрязва, докато фрезата се приближи до центъра на детайла (фиг. 4 в). За струговане на правоъгълни канали и первази се използва довършителен (острие) фрез (фиг. 4 г). Чрез преместването му в напречна посока и преместването на шублера надлъжно е възможно да се обработва цилиндрична повърхност с различни диаметри. Пробиването се използва за избор на отвори и вътрешни кухини на частите. Скуката се извършва чрез скука твърд резец(фиг. 4д). Режещият ръб на фреза е настроен на нивото на оста на шпиндела. При пробиване надлъжното подаване на фреза се редува с напречните му измествания от ръба на детайла към центъра му, като се отстранява слой по слой материал от стената на изрязваната кухина и се изравнява дъното му. Завъртането на части със сложна форма се извършва с фасонни фрези |
|
Ориз. 5. Опции за заточване и монтаж на фасонни фрези Оформените фрези се изработват независимо от ленти от въглеродна или бързорежеща стомана с дебелина 3-5 мм, ширина 10-20 мм и дължина 100-120 мм. Резачката се завърта по нанесения контур, закалява се и се заточва (фиг. 5 а). Фрезите трябва задължително да имат подложка на страничните повърхности, така че да не влизат в контакт с детайла по време на обработка (фиг. 5 б). Има два варианта за монтиране на фасонен фрез (фиг. 5в) за директно и обратно струговане, като при обратно завъртане фрезата се обръща и се получава детайл с обратен профил. Оформените фрези могат да се подават към детайла в напречна, надлъжна посока и под ъгъл спрямо оста на детайла (фиг. 5г). За да получите части от различни сложни профили, можете да използвате композитен нож, сглобен от фрези с дебелина 4-8 мм, с различно заточване. Различната им комбинация позволява получаването на различни профили (фиг. 5д). За получаване на гладки форми както отвън, така и отвътре на детайла може да се използва фреза с режещ диск. По ръба на диска се обработва диск с дебелина 4-8 мм, диаметър 12-20 мм, жлеб с радиус 2-3 мм. След втвърдяване дискът се монтира с болт върху дорника и се заточва (фиг. 5 е). Обработка на детайл на копирна машина. Удобно е да се произвежда голям обем от идентични части с помощта на копирна машина. Като режещ инструмент, в зависимост от конструкцията на машината, можете да използвате стругови инструменти, монтирани в опората на машината, длета с упор или дискови фрези. |
|
Ориз. 6. Обработка на копирна машина с длето и длето |
![]() |
Ориз. 7. Обработка с дискова резачка на копирна машина.
Включване на копирна машина на поддържаща машина
Ориз. 8. Обработка на детайла според копирната машина
За да се направи копирна машина, модел на част се обработва и изрязва по оста. Полученият участък от профила се прехвърля върху шперплат с дебелина 4-5 мм и се изрязва (фиг. 8 а). Копирните машини могат да бъдат направени от метал с лазерно рязане.
Профилът на бъдещите части е фиксиран върху леглото на машината. Прикрепен към напречния плъзгач на шублера метален държачсъс сонда. Върхът на сондата и фрезата трябва да имат еднакъв профил (фиг. 8 б).
Първата заготовка предварително се оформя в цилиндър с диаметър, равен на най-големия диаметър на заготовката, следващите заготовки могат да бъдат направени с малък припуск. Първо се регулира относителното положение на детайла и копирната машина (фиг. 8 в), след това шублерът на машината се измества наляво, докато горната част на сондата се изравни с линията най-голям диаметърдетайли (фиг. 8г). Фрезата се подава напред, докато спре към повърхността на детайла, а сондата се опира в копирната машина в точката с най-голям диаметър и е фиксирана в това положение. Обработката се извършва от дясно на ляво. Фрезата се подава към детайла в напречна посока, докато сондата спре в контура на копирната машина (фиг. 8. д). Стойността на надлъжното изместване на фреза за един напречен ход е 1-2 mm. Следите от рязане се отстраняват с шкурка. Една и съща копирна машина може да се използва за струговане на части от същия профил, но с различни диаметри (фиг. 8 е). Лека промяна в ъгъла на копирната машина дава стесняване на силуета на детайла. Дългите части се заточват на копирната машина на части. Симетричните фигури се обработват от ръба до средата, след което детайлът се обръща и се обработва втората част (фиг. 8g).
Избор на режим на рязане
Скоростта на основното рязане на стругове за различни точкирежещият ръб е различен и зависи от разстоянието до оста на въртене на детайла. Средната скоростза средна точкасе определя по формулата:
V cp \u003d πD cp n / (60 1000)
където D cp - средният диаметър на детайла, mm;
N- скорост на шпиндела, об/мин;
Скоростта на шпиндела се избира в зависимост от диаметъра на детайла; при монтиране на лицева плоча с диаметър повече от 400 mm скоростта на шпиндела не трябва да надвишава 800 rpm.
Основна скорост на рязане на дърво меки скали 10-12 m/s, за твърда дървесина 0,5-3 m/s.
Надлъжно подаване на оборот на шпиндела за груба обработка 1,6-2 mm, за довършителни работи не повече от 0,8 mm. Напречно подаване на оборот на шпиндела не трябва да надвишава 1,2 mm.
Механична обработка на части на стругове с ЦПУ
CNC струговете имат крайни фрези като режещ инструмент или се комбинират с крайни фрези и дискови фрези.
Когато обработвате детайл с крайна фреза, можете да получите различен фигурен профил върху детайла. Движението на фреза и скоростта на въртене на детайла се задават с помощта на софтуер, в зависимост от формата на бъдещата част.
Ориз. 9. Създаване на скулптура на струг с ЦПУ
Машините с крайни и дискови фрези ви позволяват да ускорите процеса на завъртане на детайли. Дисковата фреза извършва предварителна груба обработка, крайна мелницадовършителни работи.
Ориз. 10. Обработка на детайла с дискова фреза
Ориз. 11. Обработка на детайла с крайна фреза
След завъртане на детайла, за окончателно довършване и отстраняване на следи от рязане, той се обработва с шкурка, обикновено се използва парче с малка ширина, което се премества в опънато състояние по целия детайл.
Ориз. 12. Обработка на детайла с шкурка
литература:
1. Буриков В.Г., Власов В.Н. Къща резба - М .: Нива на Русия заедно с Компанията на Евразийския регион, 1993-352 стр.
2. Ветошкин Ю.И., Старцев В.М., Задимидко В.Т.
Дървесни изкуства: учеб. надбавка. Екатеринбург: Урал. състояние горско инженерство не-т. 2012 г.
3. Гликин М.С. Декоративна дограма на машина "Universal" .- M .: Lesn. пром-ст, 1987.-208 с.
4. Коротков В.И. дървообработващи машини: Учебник за нач. проф. Образование. - М.6 Издателски център "Академия", 203.-304 с.
5. Лернер П.С., Лукянов П.М. Стругарска и фрезова дейност: Proc. Помощ за ученици от 8-11 клас. средно училище - 2-ро изд., преработено - М .: Образование, 1990. - 208 с.
Да се сложни начиниНастройките на детайла на струг включват: монтаж в 4-челюст несамоцентриращ се патронник, на лицева плоча, квадрат, в стабилни опори и монтаж на детайли при обработка на ексцентрични части. Всички те се нуждаят или от специална настройка на приспособлението, или от подравняване на детайла спрямо оста на въртене.
§ 1. Механична обработка в 4-челюстни патронници
За фиксиране на некръгли заготовки, отливки и изковки с неравни повърхности и някои други работи се използват 4-челюстни патронници с независимо движение на челюстта.
Ков (фиг. 236). Те се състоят от тяло 2, опори 3, винтове 4 и гърбици 5. Гърбиците могат да се използват като предни или задни. Затягането и центрирането на заготовките в такива патронници се извършват отделно. Патронникът се монтира върху резбовия край на шпиндела с помощта на адаптерен фланец 1. При машини с фланцова конструкция на шпиндела монтажният отвор се прави директно в тялото на патронника.
Тялото на 4-челюстния патронник може да се използва като лицева плоча за монтаж и затягане на детайли с обработена опорна повърхност. За тази цел той осигурява чрез удължени канали за монтаж на монтажни болтове. Изработват се патрони различни размери*с външен диаметър от 160 до 1000 мм.
Характеристика на обработката на детайли в такива патронници е необходимостта от подравняване на оста на обработваната повърхност с оста на патронника (шпиндела). Това се прави чрез съгласуване на заготовките според риска от тебешир или според маркировката,
В първия случай (фиг. 237, а) парче тебешир се довежда до проверената повърхност на бавно въртящ се детайл и неговата концентричност с оста на въртене се определя от вида на риска от тебешир. За да не се повредят ръцете, тебеширът се поставя приблизително на нивото на оста на детайла с лек наклон надолу и за по-голяма стабилност дясна ръкаподкрепа лява. Ако следата от риска е разположена по цялата обиколка, което е много рядко при първата проверка, тогава позицията на детайла
вярно.
Когато рискът остава само на малка площ от проверяваната повърхност, позицията на детайла се регулира чрез изместване на гърбиците, противоположни на риска.
Ако детайлът има относително плоска или предварително обработена повърхност, тогава подобно подравняване се извършва с уред за дебелина на стенда, както е показано на фиг. 237b. Иглата за измерване на дебелината, монтирана върху специална плоча или горната равнина на напречния плъзгач, се извежда на повърхността за проверка с малка междина и чрез включване на ниската скорост на шпиндела се определя нейната равномерност по обиколката. Чрез промяна на позицията на детайла в патронника чрез изместване на съответните гърбици, те го правят възможно по-малък. Тогава заглавието е окончателно фиксирано.
Съгласно втория метод подравняването се извършва чрез маркиране в края на детайла с помощта на задния център или уреда за дебелина.
Горната част на задния център се вкарва в пробитата вдлъбнатина в пресечната точка на централните маркировъчни линии (фиг. 237, в), детайлът се притиска с центъра към края на тялото на патронника и се фиксира с гърбици в това положение .
При съгласуване с дебеломер (фиг. 237, г), той се монтира на. равнината на напречния плъзгач на шублера или специална плоча. Иглата за измерване, поставена на височината на горната част на задния център, се довежда до централните линии на крайната повърхност на детайла и позицията на всяка линия се проверява последователно чрез напречно движение. В този случай средната линия, когато детайлът се завърти на 180 °, трябва да се комбинира с горната част на иглата за измерване на дебелината по цялата дължина.
Тези съгласувания се извършват само по време на производството на първата част от партидата. Останалите части са правилно ориентирани в 4-челюстния патронник чрез притискане към две съседни челюсти, които не се движат при отделяне на детайлите.
§ 2. Обработка върху лицева плоча и квадрат
Части със свободна форма, като лостове или калъфи, които не могат да бъдат правилно монтирани в 4-челюстния патронник, са фиксирани върху лицева плоча. Към този метод на монтаж се прибягва и ако се изисква да се поддържа стриктна перпендикулярност на оста на обработваната повърхност до края или основата на детайла.
Лицева плоча 1 (фиг. 238) е чугунен диск с главина, подсилен от обратната страна с усилватели,
Отворите на главината са направени според формата на предния край на шпиндела, върху който е монтирана и фиксирана лицевата плоча.
Предният край на лицевата плоча е строго перпендикулярен на оста си. Има Т-образни и проходни канали за монтажни болтове. Лицевата плоча наподобява тялото на 4-челюстния патронник, който понякога се използва за същата цел.
Заготовката се притиска към края на лицевата плоча със скоби и болтове, като за предотвратяване на изместване по време на обработка се притиска допълнително със странични опори. Това закрепване е показано на фиг. 238. Част 4 се притиска към лицевата плоча с две скоби 2 и болтове 3. Предният край на скобата лежи върху детайла, задният край лежи на стойката 8. Страничните опори тук са винтове 6, които се завинтват в 5 квадрати, прикрепени към лицевата плоча.
Заготовките, монтирани на лицевата плоча, трябва да имат чисто обработена опора (с лице към лицевата плоча) край. Когато ги поправяте, трябва да се придържате към следните правила.
1. Стягащите болтове трябва да бъдат поставени възможно най-близо до детайла, за да се създаде по-здраво захващане.
2. Затегнете гайките диагонално отначало слабо, след това накрая.
3. Монтирайте скобите, ако е възможно, на местата на частта, които се поддържат върху лицевата плоча.
4. Ако третото правило не може да се спазва, не затягайте много гайките, за да избегнете огъване на частта.
5. Вдигнете опорните стойки на такава височина, че скобите
разположен успоредно на работната равнина на лицевата плоча.
Първата заготовка от партидата се проверява на лицевата плоча по същия начин, както при 4-челюстния патронник. С леко притиснати гайки може да се премести на всяка странична светлинаудари с чук. Останалите заготовки са правилно ориентирани от страничните опори.
Ако центърът на тежестта на детайла е изместен от оста на въртене, се използва балансиране на противотежестта 7 (фиг. 238). Балансирането се извършва в този ред. Противотежестта първо се фиксира върху лицевата плоча на известно разстояние от оста й, противоположно на центъра на тежестта на детайла. След това, след като изключите шпиндела от механизма на скоростната кутия, завъртете ръчно предната плоча. Ако последният спре в различни позиции, тогава балансирането е правилно. В противен случай противотежестта се измества в желаната посока от оста на въртене и балансирането се повтаря отново.
Части с успоредно или ъглово разположение на оста на обработваната повърхност към основата се монтират върху квадрата 4 (фиг. 239), който е прикрепен към лицевата плоча с болтове и гайки 5. Част 3 (в този случай, корпусът на лагера), от своя страна, е фиксиран върху хоризонталния рафт на квадрата със скоби 2 и балансиран от противотежест 1.
Подравняването на първия детайл от партидата заедно с квадрата се извършва по един от горните методи според риска от тебешир или маркировка.
За тези произведения също може да се използва. 4-челюстен патронник, една от челюстите на който е заменена с квадрат.
§ 3. Обработка в постоянни почивки
Постоянните опори се наричат допълнителни опорни устройства, използвани при обработката на нетвърди валове.
Валовете, чиято дължина надвишава 12-15 диаметъра, обикновено се считат за нетвърди. Такива части се огъват, вибрират под действието на силата на рязане и собственото си тегло, което причинява раздробяване на фрезата, влошава качеството на обработка и принуждава намаляване на режима на рязане.Повишава производителността, дългите валове се поддържат от стабилни опори.
Струговете са оборудвани със стабилни опори с общо предназначениедва вида - фиксирани и мобилни.
Фиксираната опора (фиг. 240, а) се състои от основа 7, шарнирен капак 3 и три гърбици 2 с независимо движение. Люнетът е монтиран върху средните водачи на рамката 10 и е фиксиран със скоба 9, която се притиска към первазите на водачите с болт и гайка 8. Гърбиците могат да се преместват радиално чрез винтове чрез завъртане на дръжките 4 и фиксиран в желаната позиция чрез скоби 5. Капак 3, свързан към основата чрез ос 1, когато се освободи скоба 6, може да се изхвърли, за да се монтира частта в стабилна опора. Върховете на гърбиците са взаимозаменяеми. Те са
изработени от чугун или бронз. За работа с високи скорости на рязане вместо тях се монтират търкалящи лагери.
Подвижната стабилна опора (фиг. 240, б) се състои от тяло 5, чиято горна част е огъната надясно, и две регулируеми гърбици 2 с независимо движение. Последният може да се премести и фиксира в желаното положение с дръжки 4 и 3. Люнетът е монтиран и фиксиран с винтове 6 от лявата страна на носача на шублера 1.
Помислете за обработката на части с помощта на люнети (фиг. 241).
Преди да монтирате детайла във фиксиран люнет, върху него се обработва плитък жлеб (приблизително в средата)
по-широки от гърбиците на стабилната опора, за да се елиминира изтичането на тази област от повърхността. За да се избегне отклонение на детайла, жлебът се обработва с проходна фреза с отрицателен ъгъл на наклон на основния режещ ръб. Дълбочината на рязане и подаване трябва да са малки.
Много дълъг вал може да се огъне дори при внимателно нарязване. В този случай жлебът първо се завърта малко по-близо до главата, на това място се монтира стабилна опора и след това се прави втори жлеб в средата на детайла.
След това стабилната опора се монтира и фиксира върху рамката, така че да е разположена срещу жлеба на вала. Неговите гърбици са равномерно, без силен натиск, изведени до повърхността на жлеба и фиксирани. При извършване на тези действия трябва да се има предвид възможността за отклонение на частта в случай на неравномерно захващане на гърбица. За да се избегне това, стабилните гърбици могат първо да се монтират на късо гърло, което се обработва в края на вала в задния център. Диаметърът на такава допълнителна шийка се прави според диаметъра на жлеба за гърбиците на люнета.
Когато произвеждате партида от части, е удобно да монтирате стабилните гърбици за почивка веднъж, преди работа, върху къс твърд дорник.
След фиксиране на детайла върху машината, първо се обръща едната половина на вала (към люнета), а след това, след преинсталиране, останалата част. Люнетът се монтира вторично по обработената повърхност на вала. За да се намали триенето, жлебът за люнетните гърбици се смазва с масло.
Неподвижните подпори се използват и за облицовка, центриране и пробиване на дупки в края на дълъг вал, ако последният не се вписва в отвора на шпиндела. В този случай валът
единият край е фиксиран в патронника, а другият край е монтиран в гърбиците на люнета.
Подвижната опора се използва при обработка на дълги цилиндрични повърхности. Юмруците му се разпореждат вдясно от резецана разстояние 10-15 мм. Извършва се необходимото отместване на фреза горен слайдшублер.
Устойчивите гърбици се монтират върху обработената повърхност на първата част от партидата. За да направите това, първо смилайте края му малък парцелДължина 20-25 мм до необходимия диаметър, до който се доближават стабилните гърбици. Ако работата се извършва без охлаждане, е необходимо периодично да се облизва обработената повърхност с масло пред гърбиците на люнета.
Нетвърдите дълги валове, дори когато се обработват в стабилни почивки, се получават с отклонение. Следователно те се коригират преди завършване на завъртане. Редактирането се извършва с правилната скоба (фиг. 242), както следва. Към повърхността на вал, въртящ се в центровете в различни местапо дължината се донася парче тебешир, като върху него остават знаци от тебешир, които показват мястото на отклонението. Ако всички следи са от едната страна на вала, тогава отклонението е едностранно.
Мястото на най-голямото отклонение се определя от големината на дъгата на тебеширената следа. Там, където отклонението е най-голямо, дължината на дъгата е най-къса. На това място е монтиран винт 1 на правилната скоба 2, както е показано на фиг. 242. Тъй като валът се удължава леко по време на обличане, задният център следва преди това
разхлабете леко.
Често валът има сложно отклонение в различни посоки. В този случай преобладаващата посока на отклонение се установява от следите от тебешир. Първо се коригират участъци, където посоката на отклонението е противоположна на преобладаващата, за да се получи общо едностранно отклонение. След това валът се изправя, както е посочено по-горе.
§ 4. Механична обработка на ексцентрични части
Тези части включват ексцентрици, ексцентрици и колянови валове (фиг. 243). Характеризират се с наличието на повърхности с успоредно изместени оси. Размерът на изместване на осите се нарича ексцентриситет.
Обработката на ексцентрични части на стругове може да се извърши: 1) в. 3-челюстен патронник; 2) на дорник; 3) в 4-челюстен патронник или на лицева плоча; 4) чрез копирна машина; 5) в разселени центрове; 6). с помощта на центрофуги.
Ексцентрична обработка. Ексцентриците с малка дължина могат да бъдат обработени по един от първите четири начина.
В 3-челюстния патронник оста на обработената ексцентрична повърхност е подравнена с оста на въртене чрез инсталиране на облицовка под една от челюстите на патрона (фиг. 244, а). Дебелината му с достатъчна точност за практика може да се определи по формулата
За да се намали грешката при монтажа, се препоръчва да се изреже облицовката от пръстена, чийто отвор е направен според диаметъра на детайла. От изпъкналата страна на облицовката ъглите се изрязват така, че лагерната платформа b да е по-малка от ширината на работната повърхност на гърбицата.
Ако ексцентричният детайл има предварително направен отвор, той се обработва с монтаж върху дорника (фиг. 244, б). В краищата на последния има две двойки централни отвори, компенсирани от размера на ексцентриситета. Обработката се извършва за две инсталации в центровете. При първата настройка, спрямо отворите A-A, повърхността G е обърната, във втората
По отношение на отворите B-B, повърхност C е обърната.
Изместената повърхност на ексцентрика може също да се обработва в 4-челюст патронник или лицева плоча. В този случай позицията на обработваната повърхност се намира в края на детайла чрез маркиране и след това оста му се комбинира с оста на шпиндела по един от методите, описани на фиг. 237, Виг.
При завъртане на ексцентрика по протежение на копирната машина (фиг. 244, в), на дорника 2 се монтират копирна машина 3, междинна втулка 4, детайл 5, шайба 6, фиксирани с гайка 7. Донникът се монтира с заострен остов в отвора на шпиндела и се затяга с дълъг винт или се притиска от задния център. В държача на инструмента са фиксирани широк валяк 1 и фреза 8. Ролката се притиска плътно към копирната машина от пружина, монтирана в шублер вместо винта за кръстосано подаване. Когато включите надлъжното движение на шублера, резачката ще завърти частта по профила на копирната машина.
Механична обработка на ексцентрични и колянови валове. Повърхностите на такива валове се обработват в офсетни центрове, ако са поставени на краищата - части, или с помощта на централни превключватели.
Първият начин е показан на фиг. 245 а. За да направите това, детайлът първо се обръща в нормално състояние центрове А-Адо диаметър D. Втората двойка централни отвори B-B се маркира и пробива в краищата на детайла, след което се пробива. За малки детайли това може да се направи ръчно чрез центриране на струг. В този случай централното свредло се монтира в шпиндела на машината с помощта на патронник за пробиване, а детайлът, захванат в лявата ръка, се поддържа от перфорирана вдлъбнатина в задния център и се подава напред към свредлото чрез преместване на перото на задната баба.
За детайли с големи размери се правят изместени централни отвори на центриращи машини или с помощта на специално устройство - приспособление за пробивни машини.
Ако ексцентриситетът е голям и не позволява поставяне на изместени централни отвори в края на детайла, те се правят в подвижни центрофуги, които се фиксират към предварително обърнатите крайни цапи на вала. В този случай изместената двойка централни отвори трябва да бъде разположена стриктно в една и съща диаметрална равнина. Пример за такъв метод за обработка на коляновия вал е показан на фиг. 245б. Местните шийки 3 се обръщат при монтиране на детайла по средата дупки A-Aцентрални превключватели 7, шейни на свързващия прът 2 и 5, съответно, в изместен център дупки B-Bи V-V.
Балансирането на небалансираните части се извършва с противотежест 7, който е фиксиран върху задвижващата лицева плоча 8, а твърдостта на вала се увеличава с дистанционни пръти 4 и 6.
към вкъщи
раздел пет
Основни операции и работа,
изпълнена на струг
Глава XI
Обръщане на външни цилиндрични повърхности
На стругове е възможно да се обработват части, чиито повърхности имат формата на тела на въртене. Повечето от частите, използвани в машиностроенето, имат цилиндрични повърхности, като ролки, втулки и др.
1. Фрези за надлъжно струговане
За надлъжно завъртане се използват проходни фрези. Преминаващите фрези са разделени на черноваи довършителни работи.
Грубото фрези (фиг. 99) са предназначени за грубо струговане - лющене, извършвано с цел бързо отстраняване на излишния метал; често се наричат груби. Такива фрези обикновено се изработват със заварена или запоена, или механично закрепена плоча и са снабдени с дълга режещ ръб. Горната част на фрезата е заоблена по радиуса r = 1-2 mm. На фиг. 99, но показва фрезата на грубата права линия, а на фиг. 99, b - огънат. Огънатата форма на резачката е много удобна при завъртане на повърхностите на части, разположени близо до челюстите на касетата, и за подрязване на краищата. След завъртане с груб резец, повърхността на детайла има големи рискове; следователно качеството на обработваната повърхност е ниско.
Довършителните фрези се използват за окончателно струговане на детайли, тоест за получаване на точни размери и чиста, равна повърхност на обработка. Съществуват различни видовечисти фрези.
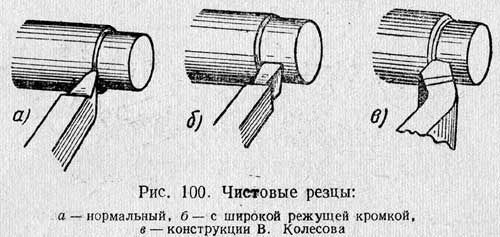
На фиг. 100, а показва довършителна фреза, която се различава от черновата основно по голям радиус на кривина, равен на 2-5 mm. Този тип фреза се използва за довършителни работи, които се произвеждат с малка дълбочина на рязане и ниско подаване. На фиг. 100b показва довършителна фреза с широк режещ ръб, успореден на оста на детайла. Този нож позволява фино отстраняване на стърготини при високи скорости на подаване и произвежда чиста и гладка повърхност. На фиг. 100, c показва фрезата на В. Колесов, която ви позволява да получите чиста и гладко обработена повърхност при работа с голям подаване (1,5-3 mm / оборот) с дълбочина на рязане 1-2 mm (виж фиг. 62 ).
2. Монтаж и фиксиране на фреза
Преди завъртане е необходимо правилно да монтирате ножа в държача на инструмента, като се уверите, че частта на ножа, излизаща от него, е възможно най-къса - не повече от 1,5 от височината на сърцевината му.
При по-дълъг надвес, фрезата ще трепери по време на работа, в резултат на това обработената повърхност ще се окаже неравна, вълнообразна, със следи от смачкване.
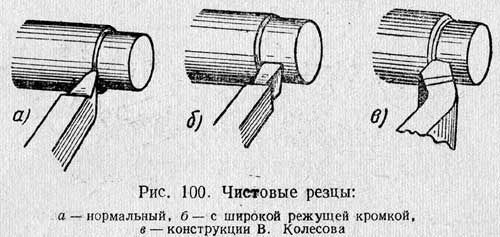
На фиг. 101 показва правилната и неправилната инсталация на ножа в държача на инструмента.
В повечето случаи се препоръчва да поставите върха на инструмента на височината на центровете на машината. За това се използват облицовки (не повече от две), като се поставят под цялата носеща повърхност на фрезата. Подплатае плоска стоманена линийка с дължина 150-200 мм, имаща строго успоредни горна и долна повърхност. Стругачът трябва да има набор от такива облицовки с различна дебелина, за да получи височината, необходима за монтиране на фреза. За тази цел не трябва да се използват произволни плочи.
Подложките трябва да се поставят под фреза, както е показано на фиг. 102 отгоре.
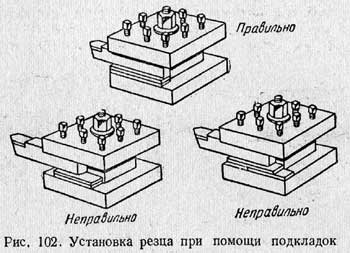
За да проверите позицията на горната част на резеца по височина, донесете горната му част до един от предварително калибрираните центрове, както е показано на фиг. 103. За същата цел можете да използвате риска, начертан върху перото на задната баба, на височината на центъра.
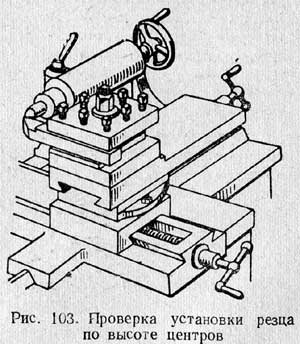
Фиксирането на ножа в държача на инструмента трябва да бъде надеждно и издръжливо: ножът трябва да бъде фиксиран с най-малко два болта. Болтовете, закрепващи фрезата, трябва да бъдат равномерно и плътно затегнати.
3. Монтаж и фиксиране на части в центрове
Често срещан начин за обработка на части на стругове е обработка в центрове(фиг. 104). С този метод централните отвори се пробиват предварително в краищата на детайла - центърдетайл. Когато се монтират на машината, точките на центровете на предната и задната част на машината влизат в тези отвори. За да прехвърлите въртене от шпиндела на главата към детайла, водач патронник 1 (фиг. 104), завинтени към шпиндела на машината, и скоба 2, фиксиран с винт 3 върху детайла.
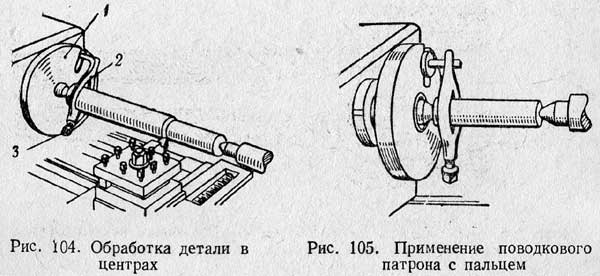
Свободният край на скобата се улавя от жлеба (фиг. 104) или пръста (фиг. 105) на патрона и кара частта да се върти. В първия случай скобата е направена огъната (фиг. 104), във втория - права (фиг. 105). Щифтовият патронник, показан на фиг. 105, представлява опасност за работника; по-безопасен е задвижващ патронник с предпазен капак (фиг. 106).
основни аксесоари стругса центрове. Обикновено центърът, показан на фиг. 107, а.
Състои се от конус 1, върху който е монтирана частта, и заострен остов 2. Дръжката трябва да пасва точно на конусния отвор на шпиндела на главната баба и на задна баба на машината.
Предният център се върти с шпиндела и детайла, докато центъра на задната баба в повечето случаи е неподвижен и се трие във въртящата се част. Триенето се нагрява и износва както коничната повърхност на центъра, така и повърхността на централния отвор на детайла. За да намалите триенето, е необходимо да смажете задния център.
При въртене на детайли с високи скорости, както и при обработка на тежки детайли, работата върху фиксиран център на задната баба е невъзможна поради бързото износване на самия център и развитието на централен отвор.
В тези случаи прилагайте въртящи се центрове. На фиг. 108 показва един от дизайните на въртящия се център, вмъкнат в заострения отвор на перото на задната баба. Център 1 се върти в сачмените лагери 2 и 4. Аксиалното налягане се възприема от упорния сачмен лагер 5. Конусният остов 3 на централното тяло съответства на конусния отвор на перото.
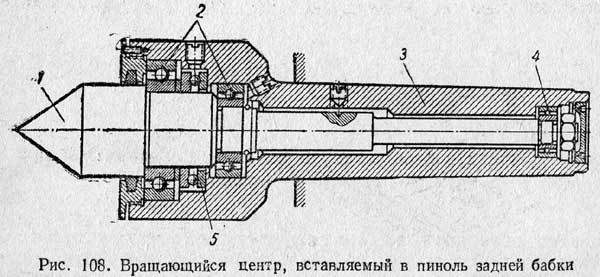
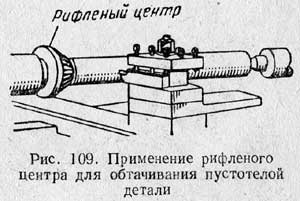
За да се намали времето за фиксиране на части, често вместо скоби се използват скоби с ръчно затягане. набраздени предни центрове(фиг. 109), които не само центрират частта, но действат и като каишка. Когато се притиснат от задния център, гофрите се врязват в детайла и по този начин предават въртене към него. За кухи части се използват външни (фиг. 110, а), а за ролки - вътрешни (обратни) гофрирани центрове (фиг. 110, б).
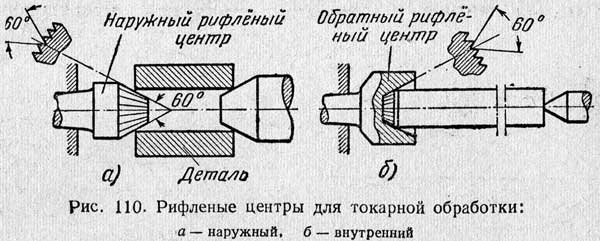
Този метод на закрепване ви позволява да завъртите частта по цялата дължина в една настройка. Завъртането на едни и същи части с конвенционален център и яка може да се извърши само в две настройки, което значително увеличава времето за обработка.
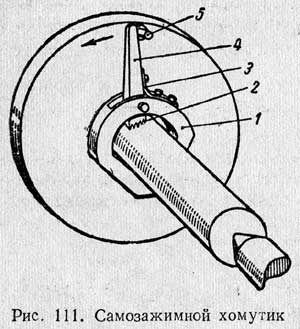
За лека и средна стругова работа самозаключващи се скоби. Една от тези яки е показана на фиг. 111. В тялото 1 на такава яка, върху оста е монтирана гърбица 4, чийто край има гофрирана повърхност 2. След монтиране на яката върху детайла, гофрираната повърхност на гърбицата се притиска към детайла под действието на пружината 3. След монтаж в центровете и стартиране на машината, щифтът 5 на задвижващия патронник, натискайки гърбицата 4, заклинва детайла и го върти. Тези самозаключващи се скоби значително намаляват непроизводителното време.
4. Настройка на машината за обработка в центрове
За да се получи цилиндрична повърхност при завъртане на детайла в центровете, е необходимо предният и референтният центрове да са върху оста на въртене на шпиндела, а фрезата да се движи успоредно на тази ос. За да проверите правилното разположение на центровете, трябва да преместите задния център напред (фиг. 112). Ако централните точки не са подравнени, позицията на корпуса на задната баба върху валиката трябва да се регулира, както е посочено на страница 127.
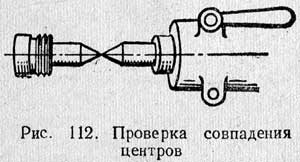
Несъответствието в центъра може също да бъде причинено от попадане на мръсотия или стърготини в конусните отвори на шпиндела или пи-нулите. За да избегнете това, е необходимо внимателно да избършете отворите на шпиндела и перлите, както и конусната част на центровете, преди да монтирате центровете. Ако центърът на главичката след това, както се казва, "бие", тогава той е дефектен и трябва да бъде заменен с друг.
При завъртане частта се нагрява и удължава, като същевременно създава повишен натиск върху центровете. За да предотвратите възможно огъване на частта и заклинване на задния център, се препоръчва от време на време да освобождавате задния център и след това да го затегнете отново до нормалното. Също така е необходимо периодично допълнително да смазвате задния централен отвор на детайла.
5. Монтаж и закрепване на части в патронници
Късите части обикновено се монтират и закрепват в патронници, които са разделени на прости и самоцентриращи се.
Простите патрони обикновено се правят с четири челюсти (фиг. 113). В такива патрони всяка гърбица 1, 2, 3 и 4 се движи от своя винт 5 независимо от другите. Това ви позволява да инсталирате и фиксирате в тях различни части както с цилиндрична, така и с нецилиндрична форма. Когато монтирате детайл в патронник с четири челюсти, той трябва да бъде внимателно подравнен, така че да не се удари по време на въртене.
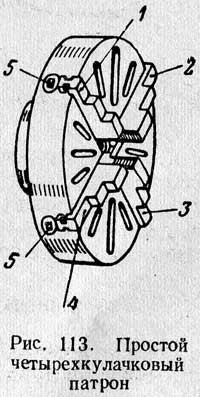
Подравняването на детайла по време на монтажа му може да се извърши с помощта на уред за дебелина. Дълбокомерът се извежда на повърхността за проверка, като се оставя празнина от 0,3-0,5 mm между тях; завъртайки шпиндела, наблюдавайте как се променя тази междина. Въз основа на резултатите от наблюдението някои гърбици се изстискват, а други се притискат, докато междината стане еднаква по цялата обиколка на детайла. След това частта е окончателно фиксирана.
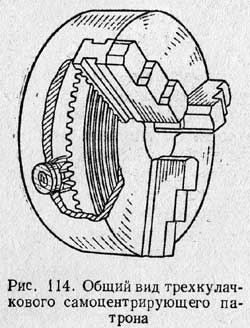
Самоцентриращи се патронници(фиг. 114 и 115) в повечето случаи се използват три гърбици, много по-рядко - двукамерни. Тези патронници са много удобни за използване, тъй като всички гърбици в тях се движат едновременно, така че част, която има цилиндрична повърхност (външна или вътрешна), се монтира и захваща точно по оста на шпиндела; освен това времето за монтаж и фиксиране на частта е значително намалено.
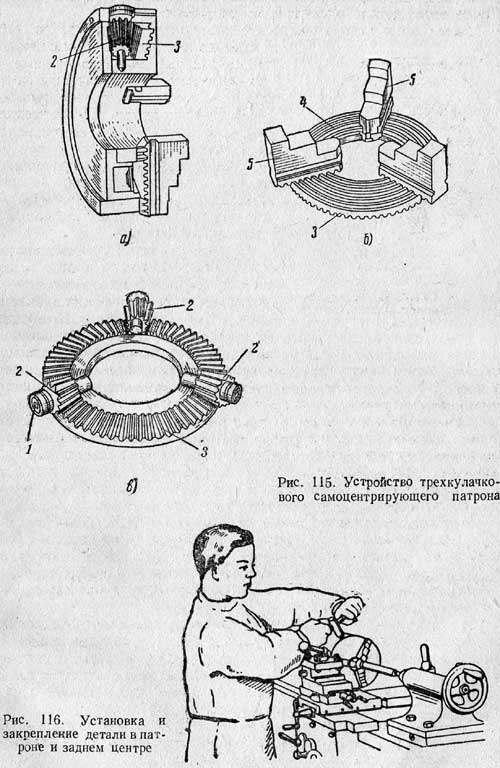
При него гърбиците се преместват с помощта на ключ, който се вкарва в тетраедричния отвор 1 на едно от трите конусни зъбни колела 2 (фиг. 115, в). Тези колела са свързани с голямо конично колело 3 (фиг. 115, б). На обратната плоска страна на това колело се изрязва многооборотен спирален жлеб 4 (фиг. 115, б). И трите гърбици 5 влизат в отделни завои на този жлеб с долните си издатини. Когато едно от зъбните колела 2 се завърти с ключ, въртенето се прехвърля към колелото 3, което, въртейки се, през спиралния жлеб 4 се движи по жлебовете на тялото на патрона едновременно и равномерно и трите гърбици. Когато дискът със спираловиден жлеб се върти в една или друга посока, гърбиците се приближават или отдалечават от центъра, съответно захващайки или освобождавайки детайла.
Необходимо е да се гарантира, че частта е здраво фиксирана в челюстите на патронника. Ако касетата е добро състояние, тогава се осигурява силно захващане на детайла с помощта на ключ с къса дръжка (фиг. 116). Други методи за захващане, като затягане с ключ и дълга тръба, която минава над дръжката, в никакъв случай не трябва да се допускат.
Патронни челюсти. Гърбиците се използват втвърдени и сурови. Обикновено се използват закалени гърбици поради ниското им износване. Но при затягане на части с чисто обработени повърхности с такива гърбици, върху частите остават следи под формата на вдлъбнатини от гърбиците. За да се избегне това, също се препоръчва използването на сурови (незакалени) челюсти.
Необработените гърбици също са удобни с това, че могат периодично да се отегчават с резачка и да елиминират биенето на патрона, което неизбежно се появява при продължителната му работа.
Вмъкване и затягане на части в патронник със задна централна опора. Този метод се използва при обработка на дълги и относително тънки части (фиг. 116), които не са достатъчни, за да бъдат фиксирани само в патронника, тъй като силата от фреза и тежестта на изпъкналата част могат да огънат детайла и да го разкъсат на патронника.
Цангови патронници. За бързо закрепване на къси части с малък диаметър към външната обработена повърхност се използват цангови патронници. Такава касета е показана на фиг. 117. Заострен остов 1 патрон е монтиран в конусния отвор на шпиндела на главната баба. Раздвоена пружинна втулка 2 с конус, наречена цанга, е монтирана във вдлъбнатината на патрона. Заготовката се вкарва в отвора 4 на цангата. След това с гаечен ключ завинтват гайка 3 към тялото на патронника.При завинтване на гайката пружинната цанга се притиска и закрепва детайла.
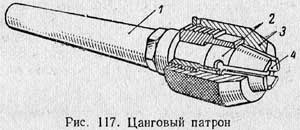
Пневматични патронници. На фиг. 118 показва диаграма на пневматичен патронник, който осигурява бързо и надеждно закрепване на частите.
В левия край на шпиндела е фиксиран въздушен цилиндър, вътре в който има бутало. Сгъстен въздух през тръбите навлиза в централните канали 1 и 2, откъдето се насочва към дясната или лявата кухина на цилиндъра. Ако въздухът влезе през канал 1 в лявата кухина на цилиндъра, тогава буталото измества въздуха от дясната кухина на цилиндъра през канал 2 и обратно. Буталото е свързано с прът 3, свързан към прът 4 и плъзгач 5, който действа върху дългите рамена 6 на манивелата, късите рамена 7 на които движат затягащите челюсти 8 на патрона.
Дължината на хода на гърбиците е 3-5 мм. Въздушното налягане обикновено е 4-5 сутринта. За задействане на пневматичния цилиндър на корпуса на скоростната кутия е монтиран разпределителен клапан 9, който се завърта от дръжката 10.
6. Завинтване и изваждане на челюстни патронници
Преди да завиете патронника към шпиндела, внимателно избършете резбите в края на шпиндела и в отвора на патронника с парцал и след това ги смажете с масло. Лек патрон се довежда с две ръце директно до края на шпиндела и се завинтва до повреда (фиг. 119). Препоръчително е да поставите тежък патрон върху дъската (фиг. 120), като донесете дупката му до края на шпиндела, завийте касетата до повреда, както в първия случай, на ръка. При завинтване на патронника се уверете, че осите на патронника и шпиндела са абсолютно еднакви.
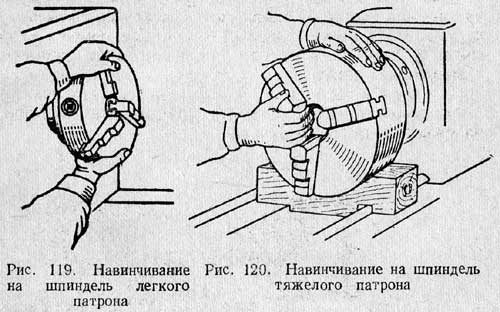
За да се предотвратят случаи на самоотвинтване на патрони в машини за високоскоростно рязане, се използва допълнително закрепване на патрона върху шпиндела с помощта на различни устройства.
(завиване на допълнителна гайка, закрепване на патрона с оформени бисквити и др.).
Завинтването на патрона се извършва по следния начин. Поставете ключ в патрона и с двете ръце направете рязко движение към себе си (фиг. 121).
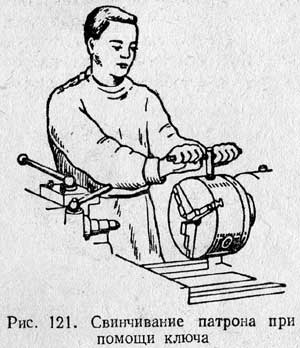
Други методи за гримиране, свързани с остри удари по патронника или челюстите, са неприемливи: патронникът е повреден, гърбиците в тялото му са разхлабени.
Завинтването и завинтването на тежък патрон се извършва най-добре с помощта на помощен работник.
7. Техники за струговане на гладки цилиндрични повърхности
Обработването на цилиндрични повърхности обикновено се извършва на два етапа: първо се изпилява голяма част от припуските (3-5 mm на диаметър), а след това останалата част (1-2 mm на диаметър).
За да получите даден диаметър на детайла, е необходимо да настроите фреза на необходимата дълбочина на рязане. За да настроите ножа на дълбочината на рязане, можете да използвате метода за тестови чипове или да използвате диска за напречно подаване.
За да настроите ножа на дълбочината на рязане (по размер) с помощта на метода за тестови чипове, трябва:
1. Докладвайте подробности за ротационното движение.
2. Чрез завъртане на ръчното колело за надлъжно подаване и дръжката на винта за напречно подаване, ръчно приведете ножа към десния край на детайла, така че горната му част да докосне повърхността на детайла.
3. След като зададете момента на докосване, преместете ръчно ножа вдясно от детайла и, като завъртите дръжката на винта за кръстосано подаване, преместете ножа до желаната дълбочина на рязане. След това частта се обръща с ръчно подаванена дължина 3-5 мм спрете машината и измерете диаметъра на струговата повърхност с шублер (фиг. 122). Ако диаметърът се окаже повече от необходимия, фрезата се прибира надясно и се настройва на малко по-голяма дълбочина, поясът отново се обработва и измерването се извършва отново. Всичко това се повтаря, докато се получи желаният размер. След това включете механичното подаване и смилайте детайла по цялата посочена дължина. В края изключете механичното подаване, върнете ножа обратно и спрете машината.
Завършването се извършва в същия ред.
Използване на винтовия диск за кръстосано подаване. За да се ускори монтирането на фреза до дълбочината на рязане, повечето стругове имат специален инструмент. Намира се при дръжката на винта за кръстосано подаване и представлява втулка или пръстен, по обиколката на който са отбелязани деления (фиг. 123). Този ръкав с деления се нарича крайник. Разделенията се броят според риска върху фиксираната винтова втулка (на фиг. 123 този риск съвпада с 30-ия ход на лимба).
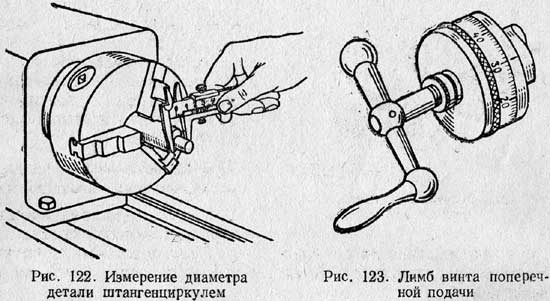
Броят на деленията на циферблата и стъпката на винта могат да бъдат различни, следователно размерът на напречното движение на ножа, когато циферблатът се завърти с едно деление, също ще бъде различен. Да приемем, че циферблатът е разделен на 100 равни части и винтът за кръстосано подаване е с резба с 5 мм стъпка. С едно пълно завъртане на дръжката на винта, т.е. 100 деления на крайника, фрезата ще се движи в напречна посока с 5 mm. Ако завъртите дръжката с едно деление, тогава движението на фреза ще бъде 5:100 = 0,05 mm.
Трябва да се има предвид, че когато фрезата се премести в напречна посока, радиусът на детайла след преминаване на фреза ще намалее със същото количество, а диаметърът на детайла ще се удвои. По този начин, за да се намали диаметърът на детайла, например, от 50,2 на 48,4 mm, тоест с 50,2 - 48,4 = 1,8 mm, е необходимо да се премести фрезата наполовина, т.е. с 0,9 mm.
При настройване на фреза на дълбочината на рязане с помощта на винтовия диск за напречно подаване е необходимо обаче да се вземе предвид пролуката между винта и гайката, която образува така наречения "мъртъв ход". Ако изгубите това от поглед, тогава диаметърът на обработваната част ще се различава от посочения.
Следователно, когато настройвате фреза на дълбочината на рязане с помощта на циферблат, е необходимо да се спазва следващото правило. Винаги се приближавайте до необходимата настройка по протежение на циферблата, като бавно завъртате дръжката на винта надясно (фиг. 124, а; необходимата настройка е 30-тото деление на циферблата).
Ако завъртите дръжката на винта за кръстосано подаване с количество, по-голямо от необходимата стойност (фиг. 124, b), тогава, за да коригирате грешката, в никакъв случай не подавайте дръжката обратно с размера на грешката, но трябва да направите почти пълен завой в обратна посока и след това да завъртите дръжката отново надясно до необходимото разделение по лимба (фиг. 124, в). Те правят същото, когато е необходимо да се върне фрезата; завъртайки дръжката наляво, ножът се прибира повече от необходимото и след това, чрез дясно завъртане, се привежда до необходимото разделение на лимба.
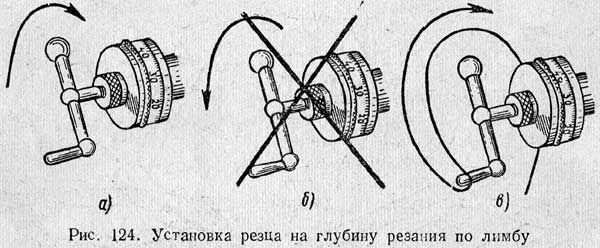
Движението на фреза, съответстващо на едно деление на крайника, е различно при различните машини. Следователно, при започване на работа е необходимо да се определи размера на изместването, съответстващо на тази машинаедно деление на лимба.
Използвайки крайници, нашите високоскоростни стругари постигат даден размер без тестови чипове.
8. Обработка на части в стабилни почивки
Дългите и тънки части, чиято дължина е 10-12 пъти диаметъра им, се огъват по време на въртене както от собственото си тегло, така и от силата на рязане. В резултат на това артикулът получава неправилна форма- в средата се оказва по-дебел, а в краищата - по-тънък. Това може да се избегне чрез използване на специално поддържащо устройство, наречено люнетка. При използване на стабилни почивки е възможно детайлите да се шлайфат с висока точност и да се отстраняват стърготини по-голям разделбез страх от огъване на частта. Люнетите б, се движат неподвижни и подвижни.
постоянна почивка(фиг. 125) има корпус от чугун 1, с който шарнирният капак 6 е закрепен с шарнирен болт 7, което улеснява монтажа на детайла. Тялото на стабилната опора е обработено отдолу според формата на водачите на рамката, върху които се закрепва с помощта на прът 9 и болт 8. Две гърбици 4 се движат в отворите на тялото с помощта на регулиращи болтове 3, а по покрива се движи една гърбица 5. За фиксиране на гърбиците в необходимото положение се използват винтове 2. Такова устройство ви позволява да монтирате валове с различни диаметри в стабилната опора.
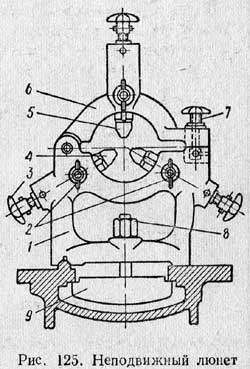
Преди да монтирате необработен детайл във фиксирана опора, е необходимо да се обработи жлеб в средата му за гърбиците с ширина малко по-голяма от ширината на гърбицата (фиг. 126). Ако детайлът има голяма дължина и малък диаметър, тогава неговото отклонение е неизбежно. За да се избегне това, допълнителен жлеб се обработва по-близо до края на детайла и след като се монтира стабилна опора в него, основният жлеб се обработва в средата.
Фиксирани стабилни опори също се използват за отрязване на краищата и подрязване на краищата на дълги части. На фиг. 127 показва използването на фиксирана опора при рязане на края: частта е фиксирана в единия край в патронник с три челюсти, а другият край е монтиран в останалата част.
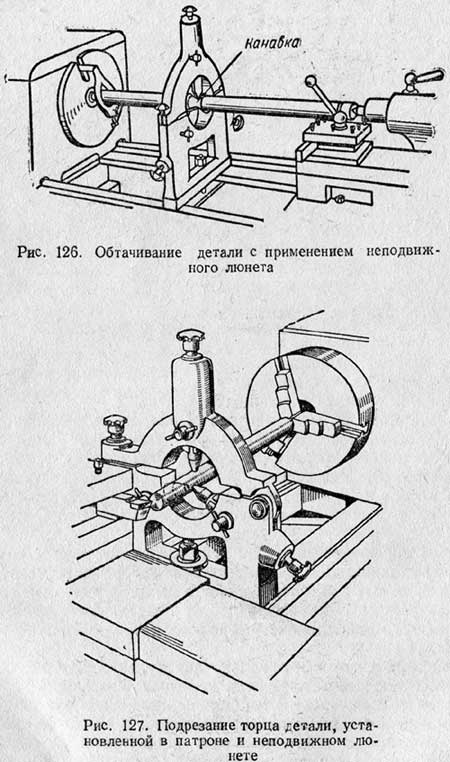
По същия начин можете да обработите прецизен отвор от края на дълга част, например да пробиете заострен отвор в шпиндела на струг или да пробиете такава част по цялата й дължина.
Подвижна стабилна почивка(фиг. 128) се използва за фино струговане на дълги части. Люнетът е фиксиран върху шейната на шублера, така че да се движи заедно с него по протежение на детайла, следвайки фреза. По този начин тя поддържа детайла директно в точката на приложение на силата и предотвратява отклоняването на частта.
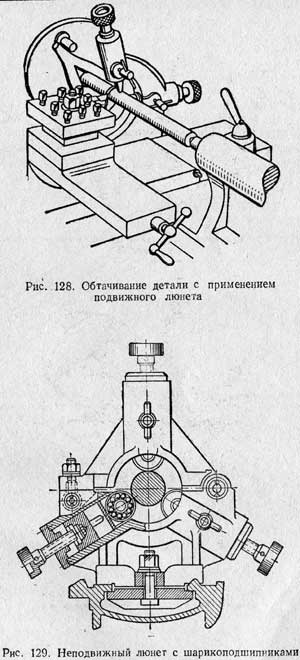
Стабилната опора има само две гърбици. Те са удължени и фиксирани по същия начин, както гърбиците на фиксиран люнет.
Стабилните опори с конвенционални челюсти не са подходящи за високоскоростна обработка поради бързото износване на челюстите. В такива случаи прилагайте стабилни опори с ролкови или сачмени лагери(фиг. 129) вместо конвенционални гърбици, което улеснява работата на ролките и намалява нагряването на детайла.
9. Техники за струговане на цилиндрични повърхности с первази
Когато обработват на стругове партида от стъпаловидни части (стъпаловидни ролки) с еднаква дължина за всички части на отделните стъпала, иноваторите използват надлъжен ограничител, който ограничава движението на фреза и надлъжно подаващо крайче, за да намалят времето за измерване на дължина.
Използване на надлъжен ограничител. На фиг. 130 показва надлъжния ограничител. Той е закрепен с болтове към релсата на предното легло, както е показано на фиг. 131; мястото на фиксиране на ограничителя зависи от дължината на детайла, който ще се обърне.
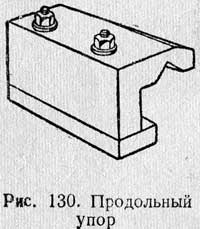
Ако на машината има надлъжен ограничител, е възможно да се обработват цилиндрични повърхности с первази без предварителна маркировка, докато, например, стъпаловидни ролки се завъртат в една настройка много по-бързо, отколкото без упор. Това се постига чрез полагане на ограничител на дължината (мерителна плочка) между ограничителя и опората, съответстващ на дължината на стъпалото на ролката.
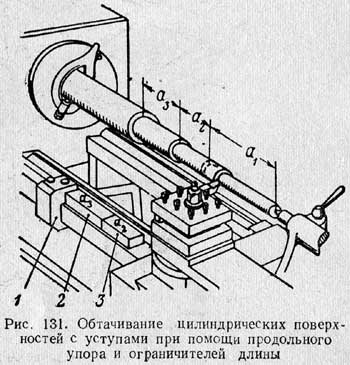
Пример за завъртане на стъпаловиден валяк със стоп 1 и измервателни плочки 2 и 3 е показан на фиг. 131. Стъпка на завъртане a 1 се извършва, докато шублерът се опря в измервателната плочка 3. Като премахнете тази плочка, можете да смилате следващата стъпка на ролката с дължина 2, докато шублерът се опря в плочката 2. Накрая, премахването на плочка 2, смилайте стъпка a 3 . Веднага след като шублерът достигне ограничителя, е необходимо да изключите механичното подаване. Дължината на измервателната плочка 2 е равна на дължината на перваза a 3 , а дължината на плочката 3 е равна на дължината на перваза a 2 .
Твърдите ограничители могат да се използват само на машини с автоматично изключванеподаване на претоварване (например 1A62 и други нови машинни инструменти). Ако машината няма такова устройство, тогава завъртането покрай ограничителя е възможно само ако механичното подаване е изключено предварително и шублерът е спрян ръчно, в противен случай машината ще се счупи.
Използване на диска за надлъжно подаване Използване на диска за надлъжно подаване. За да се намали времето, прекарано за измерване на дължините на детайлите, съвременните стругове са оборудвани с циферблат за надлъжно подаване. Този крайник представлява въртящ се диск с голям диаметър (фиг. 132), разположен на предната стена на престилката и зад ръчното колело за надлъжно подаване. На обиколката на диска се прилагат равни деления. Когато ръчното колело се върти, крайникът, свързан чрез зъбно колело към надлъжното захранващо колело, също се върти. По този начин, определено надлъжно движение на шублера с фреза съответства на въртенето на крайника чрез определен бройразделения спрямо фиксираните рискове.
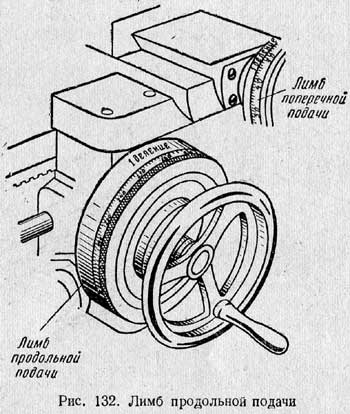
При обработката на стъпаловидни части използването на циферблат за надлъжно подаване е много рационално. В този случай стругарът, преди да обработи първата част от партидата, предварително маркира дължината на стъпалата с резачка с помощта на шублер и след това започва да ги смила. След като завърта първия етап, той настройва надлъжния крайник в нулева позиция спрямо фиксирания риск. Завъртайки следващите стъпки, той запаметява (или записва) съответните индикации на крайника относно същия риск. При завъртане на следващите части стругарът използва показанията, зададени при завъртане на първата част.
Използване на кръстосания ограничител. За да се намали времето, прекарано за измерване на диаметри при обработка на стъпаловидни части, е възможно да се използва напречен ограничител на редица стругове.
Една от тези спирки е показана на фиг. 133. Ударението се състои от две части. Фиксираната част 1 е монтирана върху каретката и фиксирана с болтове 2; упорният щифт 6 е фиксиран. Подвижният ограничител 3 е монтиран и фиксиран с болтове 4 в долната част на шублера. Винт 5 е настроен точно на необходимия размер на детайла. Краят на винта 5, опрян в щифта 6, предопределя необходимия размер на детайла. Чрез поставяне на измервателни плочки между щифт 6 и винт 5 е възможно да се шлайфат детайл със стъпки с различни диаметри.
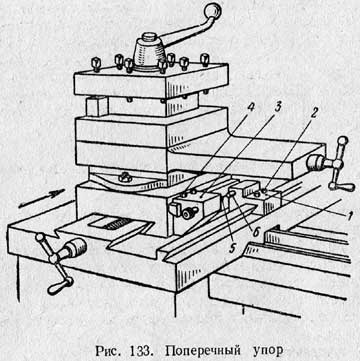
10. Условия на рязане при струговане
Избор на дълбочина на рязане. Дълбочината на рязане по време на струговане се избира в зависимост от надбавката за обработка и вида на обработка - груба или довършителна (виж страници 101-102).
Избор на скорост на подаване. Фуражът също се избира в зависимост от вида на обработката. Обикновено подаването се взема за грубо струговане от 0,3 до 1,5 mm / оборот, а за полудовършителни и довършителни работи от 0,1 до 0,3 mm / оборот при работа с нормални фрези и 1,5-3 mm / оборот при работа с фрези по дизайн на V. Колесов.
Избор на скорост на рязане. Скоростта на рязане обикновено се избира според специално разработени таблици в зависимост от живота на инструмента, качеството на обработвания материал, материала на фреза, дълбочината на рязане, подаването, вида на охлаждане и т.н. (вижте за например, Таблица 6, страница 106).
11. Брак при струговане на цилиндрични повърхности и мерки за предотвратяването му
При завъртане на цилиндрични повърхности са възможни следните видове брак:
1) част от повърхността на детайла остава необработена;
2) размерите на обърнатата повърхност са неправилни;
3) обърнатата повърхност се оказа конична;
4) обърнатата повърхност се оказа овална;
5) чистотата на обработваната повърхност не съответства на инструкциите в чертежа;
6) изгаряне на задния център;
7) несъвпадение на повърхностите при обработката на ролката в центровете от двете страни.
1. Бракът от първия тип се получава поради недостатъчни размери на детайла (недостатъчен припуск за обработка), лошо изправяне (кривина) на детайла, неправилен монтаж и неточно подравняване на детайла, неточно разположение на централните отвори и изместване на детайла. заден център.
2. Възможни са неправилни размери на струганата повърхност поради неточна настройка на фреза към дълбочината на рязане или неправилно измерване на детайла при отстраняване на тестови стружки. Възможно е и трябва да се премахнат причините за този вид брак чрез повишаване на вниманието на стругара към извършената работа.
3. Конусността на обърнатата повърхност обикновено се получава в резултат на изместването на задния център спрямо предния. За да премахнете причината за този тип брак, е необходимо правилно да инсталирате задния център. Честа причина за несъответствие на задния център е мръсотия или малки стърготини, попадащи в конусния отвор на перото. Чрез почистване на центъра и коничния отвор на перото тази причина за брак също може да бъде елиминирана. Ако дори след почистване върховете на предния и задния център не съвпадат, е необходимо съответно да преместите тялото на задната баба върху нейната плоча.
4. Овалността на струганата част се получава при биене на шпиндела поради неравномерно износване на лагерите му или неравномерно износване на шийките му.
5. Недостатъчната обработка на повърхността по време на струговане може да се дължи на редица причини: голямо подаване на фреза, използване на фреза с неправилни ъгли, лошо заточване на фреза, малък радиус на кривина на върха на фреза, висок вискозитет на детайла материал, треперене на фреза поради голям надвес, недостатъчно здраво закрепване на фреза в държача на инструмента, увеличени празнини между отделните части на шублера, треперене на детайла поради хлабавото му закрепване или поради износване на лагерите и вратове на шпиндела.
Всички горепосочени причини за брак могат да бъдат елиминирани своевременно.
6. Изгаряне на твърдия център на задната баба може да бъде причинено от следните причини: частта е твърде плътно фиксирана между центровете; лошо смазване на централния отвор; неправилно центриране на детайла; висока скорост на рязане.
7. Несъответствието на обработващите повърхности при двустранно завъртане в центровете се получава главно в резултат на биене на предния център или развитие на централни отвори в детайла. За да се предотврати брак, е необходимо да се провери състоянието на централните отвори на детайла по време на довършителните работи, както и да се гарантира, че няма изтичане на центъра на главната баба.
12. Мерки за безопасност при струговане на цилиндрични повърхности
При всички случаи на обработка на стругове е необходимо да се обърне внимание на здравото закрепване на детайла и фреза.
Надеждността на закрепването на обработвания детайл в центровете зависи до голяма степен от състоянието на центровете. Невъзможно е да се работи с износени центрове, тъй като частта под действието на силата на рязане може да се изтръгне от центровете, да отлети настрани и да нарани стругара.
При обработка на детайли в центрове и патронници, изпъкналите части на скобата и гърбиците на патронника често улавят дрехите на работника. Същите тези части могат да причинят повреда на ръцете при измерване на част и почистване на машината в движение. За да се предотвратят злополуки, трябва да се поставят защитни щитове на скобите или да се използват предпазни скоби, а гърбичните патронници трябва да бъдат защитени. Перфектният тип предпазна яка е показан на фиг. 134. Джантата 3 покрива не само главата на болта 2, но и щифта 1 на задвижващия патронник.

За предпазване на ръцете и облеклото на стругара от изпъкналите части на патронника или лицевата плоча на съвременните стругове се използва специална ограда (фиг. 135). Корпусът 1 на устройството е шарнирно свързан към щифта 2, фиксиран върху тялото на главната баба.
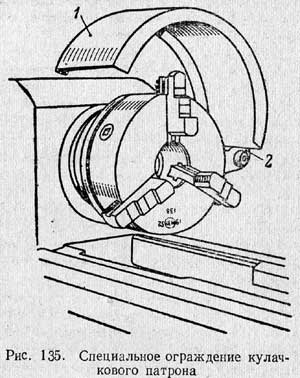
Когато инсталирате части в центровете, трябва да обърнете внимание на правилността на централните отвори. Ако дълбочината им е недостатъчна, частта може да отчупи центровете по време на въртене, което е много опасно. По същия начин, след като фиксирате частта в патронника, трябва да проверите дали ключът е изваден. Ако ключът остане в патронника, тогава, когато шпинделът се върти, той ще удари леглото и ще отлети настрани. В този случай е възможна както повреда на машината, така и нараняване на работника.
Причината за злополуките често са стружки, особено дренажни стружки, които, когато високи скоростирязането идва от непрекъсната лента. В никакъв случай такива чипове не трябва да се отстраняват или отрязват на ръка, те могат да причинят тежки порязвания и изгаряния. Стружкоразбивачите трябва да се използват, когато е възможно. AT последна инстанциякогато не се постигне разбиване на стружки, трябва да се отстрани със специална кука.
При обработка на материали, които дават къси подскачащи стружки, е необходимо да се използват очила или да се използват предпазни щитове от безопасно стъкло или целулоид (фиг. 136), прикрепени към каретата върху шарнирна стойка. Необходимо е да се отстранят малки стърготини, получени от обработката на крехки метали (чугун, твърд бронз) не с ръце, а с четка.
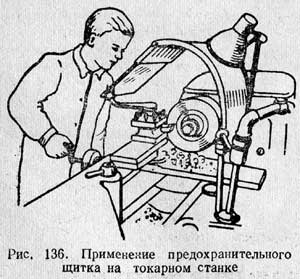
Възможно е да има наранявания на ръцете при монтиране и фиксиране на ножовете в резултат на откъсване на гаечния ключ от главите на фиксиращите болтове на държача на инструмента. Счупването на ключа става, когато челюстите на ключа и главите на болтовете са износени. Често обаче повреда възниква и от факта, че стругарът използва ключ, чийто размер не съответства на размера на болта.
Монтирането на фреза по височината на центровете с помощта на всякакъв вид облицовки, които не са пригодени за това (метални отпадъци, парчета ножовки и др.), не осигурява стабилно положение на фреза по време на неговата работа. Под натиска на чиповете такива облицовки се изместват и инсталирането на фреза се обърка. В същото време закрепването на фреза също отслабва. В резултат на това подложките и фрезата могат да изскочат от държача на инструмента и да наранят стругара. Освен това по време на монтажа на фреза и при работа на машината са възможни наранявания на ръцете по острите ръбове на металните облицовки. Затова се препоръчва всеки стругар да има набор от облицовки с различна дебелина, с добре обработени носещи равнини и ръбове.
тестови въпроси 1. Как да инсталирам ножа в държача на фреза?
2. Как да проверите положението на върха на фреза спрямо централната линия?
3. Как се монтират и фиксират части при струговане на цилиндрични повърхности?
4. Каква е разликата между условията на работа на предния и задния центрове?
5. Как е устроен въртящият се център и в какви случаи се използва?
6. Какво представлява набраздения преден център и какви са неговите предимства?
7. Как да проверите правилната инсталация на центрове за струговане на цилиндрична повърхност?
8. Как работи самоцентриращият се патронник? Назовете неговите подробности, правилата за инсталиране и подготовка за работа.
9. Как да подравните част, когато я монтирате в патронник с четири челюсти?
10. Каква е целта на винтовия диск за кръстосано подаване?
11. За какво се използва циферблатът за надлъжно подаване? Как е подредено?
12. За какво служат постоянните почивки и в какви случаи се използват?
13. Как е подредена постоянната почивка?
14. Как е подредена подвижна стабилна поставка?
15. Как се подготвя заготовка за вал за монтаж в стабилен покой?
16. Дайте пример за използване на надлъжен ограничител; кръстосано спиране.
17. Какви видове брак са възможни при струговане на цилиндрични повърхности? Как да премахнем причините за брака?
18. Избройте основните правила за безопасност при струговане на цилиндрични повърхности.
Какви части могат да се обработват и обработват на струг
Работим с малки и на брой поръчки. Правим някои неща в условни серии, като вложки в амортисьори, адаптери за оси на колелата различни стандарти. В извън сезона (ноември-февруари) можете да се заемете с по-голяма игра.
Относително казано, можем да направим всяка част от въртенето с цилиндрична форма. Най-търсените бяха разнообразието от адаптери и оси за колела. Или оригиналната резервна част не се продава, или се чака много време, или не съществува в природата. Например, някои 20 мм предни колела на Mavic нямат адаптер за 15 мм, 10 мм и обикновените 5 мм бързо освобождаване. А за задните колела на Crossmax няма оси за продажба от доста време.
Огромен брой амортисьори изискват вложки в ударите. Вложките могат да бъдат обработени от капролон, полиацетал или дуралуминий. Вечно деформируеми и игриви оси на амортисьори могат да бъдат заменени с титанова сплав VT16.
Не по-рядко втулките се предлагат с деформирани дистанционни елементи между лагерите. Производителят спести пари и достави твърде мека сплав.
Понякога трябва да заточвате бутала за главни цилиндри и спирачни апарати.
Често се изисква фина настройка на съществуващата част до желаните размери.
Заточваме резервни кормилни тръби за мотоциклети и велосипеди. Изработваме и удължители на кормилната тръба за велосипеди.
Понякога RC моделисти идват за особено здрави титаниеви оси и оръжейници за някакъв вид джетове.
Какви материали се използват за струговане
Имам алуминиеви сплави в домакинството си D16T, B95, 7075 . По принцип в работата на D16t - той е доста издръжлив. На части, които са подложени на твърде голямо напрежение, можете да поставите сплав B95 или 7075 (това е същото физични свойства). Ние не използваме сплави от серия AMG - те са доста слаби.
титаниеви сплави BT6, BT16. Това са двете сплави, които са най-търсени по отношение на якост за целите на колоездене и мотоциклети.
Капролони полиацетал. Това добро се отнася за вложките в фрикционните възли. Повечето производители на рамки също преминават към капролон, когато изчисляват комплектите с пълно окачване.
Флуоропласт. Използваме го при производството на композитни части.
полиуретан. Понякога трябва да направите някакъв странен маншет или ръкав.
Частите от месинг някак си не са използвани, така че месинг и бронз не са на склад - донесете свои.
Ако желаете, мога просто да продам парче материал - може би вие сами искате да размахате файл? =)
Как приемаме поръчки за стругарски работи
Поръчката се приема под всякаква форма. Това може да е извадка, на която искате да направите копие. Рисуване. Схема. Скица. Снимка. Обяснение с пръсти. Но в последните два случая заедно ще направим скица с размери.
Можете да направите детайл върху контрагента. И ние нямаме чудовищна надценка за обратно инженерство.
Имам доста добра представа как трябва да бъдат направени различните интерфейси на части, така че в повечето случаи няма проблеми дори с обяснението "на пръсти". Но понякога се изискват живи части за чифтосване, за да се определи точно техния размер.
Точност на изработка и размери на частите
Принципно постижимата точност на единичен продукт за разумни пари е 0,01 mm за външни диаметри. Но това рядко е необходимо на някого, обикновено точността от 0,05 мм е достатъчна (това всъщност е пресоване). Вътрешни диаметри- не повече от 0,02 мм.
Няма какво да се измерват класовете на грапавост, така че не мога да кажа нищо смислено тук. Мога да покажа образци на полиране. Никога не е било задача да направим идеално огледало а ла 14-ти клас, а търкалящите се повърхности на лагери (конуси) шлифоваме до поне 10-ти клас.
Максимална дължина на подготовка - 350 мм. Максималният диаметър на детайла е 62 мм.
Време за производство и цени
Малките неща и простите детайли с точност под 0,05 мм се правят веднага или в същия ден. По-точни и сложни детайли - на следващия ден или през ден.
За справка, поставянето на капролонов амортисьор в удара е 150 рубли. Адаптер от 15мм ос към обикновен ексцентрик - 500р. Ос за предна главина с лагерни седалки и резби по ръбовете - 2000р (много прецизен боклук). По-лесно е да се обадите, да обяснете грубо задачата, тогава ще стане ясно колко струва.
Останалите въпроси можете да зададете по телефона или да отидете лично до Огородни.
Примери за работа
Комплект инструменти за пресоване на маслени уплътнения и прашници в окачващи вилици (капролон):
Адаптер от 15 мм ос към ексцентрик с антикорозионна обработка (D16t):
Втулка от сплав 7075 със сменяема PTFE вложка (процес):
Производство на патрон за окачваща вилица със структурна обработка:
Конусно шлифоване на втулката:
Изработване на адаптер от 20-та ос към стандартен ексцентрик:
Изработка на маншети по поръчка във виличния патрон Marzocchi:
Производство на части от патрона във вилката Marzocchi:
Производство на дуралуминиеви вложки във втулки на амортисьорите:
Завъртане на цилиндрични части
На струг се обработват продукти, чийто контур може да се състои от няколко обемни геометрични фигури, които се наричат тела на революцията . Тези цифри са топка, конус, цилиндър и тор(виж фиг. вляво).
Завъртането на детайли на машината се извършва със специални резци - стругова длета
. За разлика от конвенционалните дърводелски длета, те имат удължени дръжки, които ви позволяват да държите сигурно инструмента и улесняват управлението му.
Отличава се качеството на обработка черноваи довършителни работизавъртане, изборът на инструмент зависи от това.
За чернова се прилага обработка полукръгло длето(виж фиг. а), за довършителни работи завъртане, подрязване на краищата и отрязване на части - наклонено длето(виж фиг. 6 ).
В грубо стругованезаготовки (виж фиг. а) по накрайника се движи полукръгло длето. По време на първото преминаване стружки с дебелина 1 ... 2 mm се отстраняват от средата на острието на длетото (виж фиг. 6 , наляво). По-нататъшното завъртане се извършва от страничните части на острието, когато ножът се движи както наляво, така и надясно (виж фиг. 6 , на дясно). В резултат на работа с различни участъци от острието на длетата, повърхността на детайла е по-малко вълнообразна. След 2 ... 3 минути работа проверяват надеждността на фиксирането на детайла - притискат го с центъра на задната баба. За довършителни работи трябва да се остави припуск от 3 ... 4 mm (в диаметър).
В фино завъртане(виж фиг.) На ръба се поставя наклонено длето с тъп ъгъл надолу. Стружките се отрязват от средната и долната част на острието.
Длетото за завъртане се държи с две ръце при завъртане: едната за дръжката, другата за пръта. За пръта длетото се увива отгоре или отдолу. За грубо струговане по-често се използва първият метод, като най-надежден. Натискът върху длетото трябва да бъде равномерно и гладко.
За завъртане на вътрешни вдлъбнатини на продукти с покровителили лицеви плочи(различни контейнери, ковчежета, солници и др.) - първо пробийте дупка в центъра на детайла с бормашина. След това с длето с полукръг край се избира излишната дървесина. Накрая, за да подравните стените, използвайте длето с извит край (вижте фигурата вляво).
За струговане на продукти с лицеви плочипърво направете заготовка под формата на квадрат. Върху този детайл се изчертават диагонали и се изчертава кръг малко по-голям от диаметъра на предвидения продукт. С трион се изрязват излишните ъгли, за да се получи октаедър, който се завинтва към лицевата плоча с винтове. Лицевата плоча се навива върху шпиндела и се проверява дали детайлът се придържа към накрайника. След това машината се включва и октаедърът се завърта до желания диаметър. След това накрайникът се монтира успоредно на равнината на детайла и вътрешната му част се обработва. Премествайки накрайника, смилайте навънпродукти.
Диаметърът на продукта се проверява шублер
или шублер
. Измерванията трябва да се направят на няколко места по дължината на детайла. Правата може да се провери с линийка или квадрат на светлината.
Веднага след завъртане повърхността на детайла се почиства с прикрепена шкурка дървен блок(виж фиг.). За да се изясни текстурата на дървото, повърхността на продукта може да бъде полирана с пръчка от по-твърдо дърво. Тази операция се извършва при въртене на детайла, както и при смилане.
При изрязване на краищата на детайла наклоненото длето се поставя върху ръба с остър ъгъл надолу и се прави плитък разрез (виж фигурата вляво).
След това, като се отдръпнете малко надясно или наляво (в зависимост от това кой край е отрязан), наклонете длетото и отрежете част от детайла в конус (вижте фигурата вдясно). Тази операция се повтаря няколко пъти, докато остане шийка с диаметър 8 ... 10 mm. След това частта се отстранява от машината, краищата й се отрязват с ножовка. Краищата се почистват.
За производството на Голям бройидентични частиизползван на струг проводници(ограничители) за длета или копирни машини . Проводниците са лесни за изработка сами и лесни за инсталиране както на въртящо длето, така и на накрайник (вижте фигурата вляво).
Цифрите показват:
1. - ударение;
2. - ограничител на надлъжното движение;
3. - ограничител на напречното движение;
4. - стругове длето.
За да се получат желаните контури на произведените части, понякога се използват специфични длета (вижте фигурата вдясно).
Понякога се правят специално за конкретен продукт или желан контур.
По-долу е даден пример за продукт и длетата, които се използват за направата му.
Например, за производството на дървена топка се използват длета, които са направени до определен диаметър (вижте фигурата вляво).
Без специални длета една и съща топка може да се обработва с обикновени длета, но за прецизно изработване е необходимо да се направи шаблон (шаблон), с който да измерите правилността на сферичната повърхност.
Стъпките за изработка на шаблон и завъртане са показани на фигурата вдясно.
Дървото за струговане се приготвя не само чрез изрязване на пръти или парчета дъски, но и чрез използване на изсушени клони на дървета, както и залепване на парчета пръти или дъски (т.е. от сегменти) (виж фигурата по-долу). Често за завъртане на такъв „блок“ продуктите използват дървесина от различни видове.
Благодарение на това се постигат продукти, които са много необичайни по цвят и текстура.
Когато работите, спазвайте следните правила:
Нисък защитен екран(слагам очила)
Проверете работата на машината на празен ход;
Когато обработвате детайла, плавно донесете фреза;
Уверете се, че разстоянието между детайла и накрайника не надвишава 5 мм;
Когато извършвате аксиално пробиване, закрепете внимателно задната баба;
Докато пробивате вътрешния отвор, дръжте фрезата здраво в хоризонтална равнина;
Контролирайте размерите и качеството на обработка с напълно спрян детайл;
При завършване на част шкуркафиксирайте го върху специален държач.
Съобщете за всички неизправности на учителя незабавно, след изключване на машината!
След приключване на работата:
Извадете готовата част от машината;
Поставете инструменти и приспособления на специално определени места;
Почистете работното място;
Докладвайте на придружителя, когато работата приключи.
По време на работа екранът за наблюдение на машината трябва да бъде свален.
Ако машината няма такъв екран, е необходимо да се работи в защитни очила.
Режещ инструментдонесете до детайла само след като шпинделът набере пълна скорост.
Когато машината е включена, е забранено коригирането на детайла и измерването на неговите размери, преместването на компонентите на машината.
След като изключите машината, не счупвайте детайла, патронника или предната плоча с ръце.
Не оставяйте работеща машина без надзор.
В края на работата поставете инструментите на определените места, пометете чиповете с четка.
Забранено е:
Включете машината без разрешението на учителя;
Работете при липса на предпазител на ремъчната предавка;
Използвайте неподготвен детайл;
Използвайте детайл със стружки, пукнатини, мокри или изгнили;
Облегнете се на части от струг;
Поставете инструменти и други предмети върху машината;
Спрете детайла на ръка;
Отдалечете се от машината, без да я изключвате.