वर्कपीस सेट करना - मोड़ना। भागों को मोड़ते समय केंद्रों में जकड़ना
खराद पर पुर्जे बनाने की तकनीक। |
किसी भी भाग का निर्माण सामग्री के चयन से शुरू होता है। चयनित सामग्री को रिक्त स्थान में काट दिया जाता है। वर्कपीस का आकार हमेशा एक निश्चित राशि (भत्ते) से तैयार भाग के आयामों से अधिक होता है। भत्ते का आकार और आकार भाग के आकार, इसके निर्माण की तकनीक पर निर्भर करता है। |
बनावट में एक समान लकड़ी मोड़ने के लिए सबसे उपयुक्त है। ये सन्टी, लिंडेन, एस्पेन, बीच, एल्म, अखरोट हैं। केंद्र मशीनों पर भागों को चालू करना
|
चावल। 1. भाग मोड़ का क्रम ए - वर्कपीस को ठीक करना; बी - वर्कपीस चीरा फिक्सिंग; सी- एक रेयर के साथ खुरदरापन; जी - मीसेल के साथ परिष्करण; वर्कपीस का ई-ट्रिमिंग (सामना करना)। आंतरिक गुहाओं को मोड़ना आंतरिक सतहों को मोड़ने के लिए, वर्कपीस को केवल मशीन के हेडस्टॉक में कैम चक, फेसप्लेट या ट्यूबलर चक के साथ तय किया जाता है।
|
|
चावल। 2. खोखले मोड़ ए - फेसप्लेट पर; b- एक ट्यूबलर कार्ट्रिज में। कैलिपर के साथ खराद पर काम करें एक कैलिपर के साथ खराद पर, मशीन के चल कैलीपर पर लगे टूल होल्डर में लगे कटर के साथ प्रसंस्करण किया जाता है। ऐसी मशीनों में, एक नियम के रूप में, मशीन के साथ और उसके पार मैनुअल और मैकेनिकल फीड होते हैं। टर्निंग कटर। सिर के आकार के अनुसार, कृन्तकों को एक सीधी छड़ (चित्र 3 ए) के साथ सीधे में विभाजित किया जाता है और दाईं या बाईं ओर मुड़ी हुई छड़ के साथ मुड़ा हुआ होता है। काटने के किनारे के स्थान के अनुसार, दाएं (छवि 3 डी) और बाएं (छवि 3 सी) कृन्तकों को प्रतिष्ठित किया जाता है। दाएँ टेलस्टॉक से आगे की ओर अनुदैर्ध्य दिशा में चलते हैं, बाएँ आगे से पीछे की ओर। कटर के माध्यम से (छवि 3 एसी) चरण के गठित अंत को मोड़ने और संसाधित करने के लिए जोर कटर (छवि 3 डी) के माध्यम से मोड़ने, चम्फरिंग के लिए डिज़ाइन किया गया है। स्कोरिंग कटर (चित्र 3 ई) अंत के विमान को संसाधित करने के लिए संसाधित किए जा रहे वर्कपीस के अंत में एक कदम बनाने के लिए काम करते हैं। बाहरी पर खांचे और भीतरी सतहग्रूविंग कटर (चित्र 3 एफ, एच) का उपयोग करके विवरण प्राप्त किया जा सकता है। कटिंग कटर का उपयोग काटने के लिए किया जाता है (चित्र 3 जी)। थ्रेडिंग के लिए, थ्रेडेड कटर का उपयोग किया जाता है (चित्र 3i)। आकार के कटर को वर्कपीस के आकार के अनुसार तेज किया जाता है (चित्र 3 जे)। |
![]() |
चावल। 3. मुख्य प्रकार के मोड़ उपकरण कटर सेट किए जाते हैं ताकि कटर का शीर्ष टेलस्टॉक के केंद्र के साथ मेल खाता हो। धुरी की गति 1200 आरपीएम होनी चाहिए। बेलनाकार रिक्त स्थान को मोड़ना। |
|
चावल। 4. बेलनाकार रिक्त स्थान को संसाधित करने की तकनीक कटर को धीरे-धीरे आगे बढ़ाया जाता है जब तक कि यह घूमने वाले वर्कपीस को नहीं छूता है, और इस स्थिति में इसे दाईं ओर वापस ले लिया जाता है। कटर को लिंबस के साथ 2-3 मिमी आगे खिलाया जाता है और वर्कपीस के साथ पहला वर्किंग पास बनाया जाता है। एक चिकनी बेलनाकार आकृति प्राप्त होने तक पैसेज किए जाते हैं (चित्र 4 ए)। अनुप्रस्थ फ़ीड डायल के संकेतों के अनुसार कटर को वांछित आकार में स्थानांतरित करने के बाद, एक छोटा परीक्षण क्षेत्र बदल दिया जाता है। यदि माप से पता चलता है कि कटर वांछित आकार पर सेट है, तो सतह को पूरी लंबाई के साथ दाएं से बाएं (छवि 4 बी) के साथ संसाधित किया जाता है। मोड़ने के बाद, कटर को वापस ले लिया जाता है। और वे अपनी मूल स्थिति में लौट आते हैं। वही कटर सिरों और किनारों को काटता है। अंतिम चेहरा तब तक काटा जाता है जब तक कटर भाग के केंद्र तक नहीं पहुंच जाता (चित्र 4 सी)। आयताकार खांचे और किनारों को मोड़ने के लिए, एक परिष्करण (ब्लेड) कटर का उपयोग किया जाता है (चित्र 4 डी)। इसे अनुप्रस्थ दिशा में ले जाकर और कैलीपर को अनुदैर्ध्य रूप से घुमाकर, विभिन्न व्यास के साथ एक बेलनाकार सतह को मशीन बनाना संभव है। बोरिंग का उपयोग भागों के छिद्रों और आंतरिक गुहाओं का चयन करने के लिए किया जाता है। बोरिंग बोरिंग द्वारा किया जाता है कठोर कटर(चित्र। 4e)। कटर का अत्याधुनिक स्पिंडल अक्ष के स्तर पर सेट किया गया है। उबाऊ होने पर, कटर के अनुदैर्ध्य फ़ीड को इसके अनुप्रस्थ विस्थापन के साथ भाग के किनारे से उसके केंद्र तक वैकल्पिक किया जाता है, गुहा की दीवार से परत द्वारा सामग्री परत को हटाकर और उसके तल को समतल किया जाता है। जटिल आकार के टर्निंग भागों को आकार के कटर से किया जाता है |
|
चावल। 5. आकार के कटरों को तेज करने और स्थापित करने के विकल्प आकार के कटर स्वतंत्र रूप से कार्बन या उच्च गति वाले स्टील 3-5 मिमी मोटी, 10-20 मिमी चौड़े और 100-120 मिमी लंबे स्ट्रिप्स से बने होते हैं। कटर को लागू समोच्च के साथ घुमाया जाता है, कठोर और तेज किया जाता है (चित्र 5 ए)। कटर के पास आवश्यक रूप से साइड फेस का बैकिंग होना चाहिए ताकि वे प्रसंस्करण के दौरान भाग के संपर्क में न आएं (चित्र 5 बी)। डायरेक्ट और रिवर्स टर्निंग के लिए आकार के कटर (चित्र 5c) को स्थापित करने के लिए दो विकल्प हैं; रिवर्स टर्निंग के दौरान, कटर को पलट दिया जाता है और रिवर्स प्रोफाइल वाला एक हिस्सा प्राप्त किया जाता है। आकार के कटर को अनुप्रस्थ, अनुदैर्ध्य दिशा में और भाग की धुरी के कोण पर (चित्र 5d) भाग में खिलाया जा सकता है। विभिन्न जटिल प्रोफाइल के कुछ हिस्सों को प्राप्त करने के लिए, आप अलग-अलग शार्पनिंग के साथ, 4-8 मिमी की मोटाई के साथ कटर से इकट्ठे हुए एक समग्र कटर का उपयोग कर सकते हैं। उनका अलग संयोजन आपको विभिन्न प्रोफाइल प्राप्त करने की अनुमति देता है (चित्र 5e)। बाहर और अंदर दोनों तरफ से चिकनी आकृतियाँ प्राप्त करने के लिए, कटिंग डिस्क वाले कटर का उपयोग किया जा सकता है। एक डिस्क 4-8 मिमी मोटी, 12-20 मिमी व्यास, 2-3 मिमी की त्रिज्या के साथ एक नाली डिस्क के किनारे पर मशीनी होती है। सख्त होने के बाद, डिस्क को खराद का धुरा पर बोल्ट के साथ लगाया जाता है और तेज किया जाता है (चित्र 5 एफ)। एक कापियर पर एक भाग की मशीनिंग। एक कापियर का उपयोग करके बड़ी मात्रा में समान भागों का उत्पादन करना सुविधाजनक है। काटने के उपकरण के रूप में, मशीन के डिजाइन के आधार पर, आप मशीन के समर्थन में स्थापित टर्निंग टूल्स, जोर के साथ छेनी या डिस्क कटर का उपयोग कर सकते हैं। |
|
चावल। 6. एक छेनी और छेनी के साथ एक कापियर पर प्रसंस्करण |
![]() |
चावल। 7. एक कापियर पर डिस्क कटर के साथ प्रसंस्करण।
सपोर्ट मशीन पर कॉपियर चालू करना
चावल। 8. कापियर के अनुसार भाग को संसाधित करना
एक कापियर बनाने के लिए, एक भाग मॉडल को मशीनीकृत किया जाता है और धुरी के साथ देखा जाता है। प्रोफ़ाइल के परिणामी खंड को प्लाईवुड 4-5 मिमी मोटी और कट आउट (छवि 8 ए) में स्थानांतरित किया जाता है। लेजर कटिंग का उपयोग करके धातु से कॉपियर बनाए जा सकते हैं।
भविष्य के भागों की रूपरेखा मशीन के बिस्तर पर तय की गई है। कैलिपर के क्रॉस स्लाइड से जुड़ा हुआ है धातु धारकएक जांच के साथ। जांच की नोक और कटर का एक ही प्रोफाइल होना चाहिए (चित्र 8 बी)।
पहले रिक्त स्थान को प्रारंभिक रूप से एक सिलेंडर में आकार दिया गया है जिसका व्यास रिक्त के सबसे बड़े व्यास के बराबर है, बाद के रिक्त स्थान को एक छोटे से भत्ते के साथ बनाया जा सकता है। सबसे पहले, वर्कपीस और कॉपियर की सापेक्ष स्थिति को समायोजित किया जाता है (चित्र 8 सी), फिर मशीन कैलीपर को बाईं ओर स्थानांतरित कर दिया जाता है जब तक कि जांच के शीर्ष को लाइन के साथ संरेखित नहीं किया जाता है। सबसे बड़ा व्यासविवरण (चित्र। 8d)। कटर को तब तक आगे बढ़ाया जाता है जब तक कि यह वर्कपीस की सतह के खिलाफ बंद न हो जाए, और जांच सबसे बड़े व्यास के बिंदु पर कॉपियर के खिलाफ टिकी हुई है और इस स्थिति में तय हो गई है। प्रसंस्करण दाएं से बाएं किया जाता है। कटर को अनुप्रस्थ दिशा में भाग में तब तक खिलाया जाता है जब तक कि कॉपियर के समोच्च में जांच बंद न हो जाए (चित्र 8। ई)। एक अनुप्रस्थ स्ट्रोक प्रति कटर के अनुदैर्ध्य विस्थापन का मान 1-2 मिमी है। सैंडपेपर से कट के निशान हटा दिए जाते हैं। एक ही कॉपियर का उपयोग एक ही प्रोफ़ाइल के भागों को मोड़ने के लिए किया जा सकता है, लेकिन विभिन्न व्यास (चित्र। 8 च)। कापियर के कोण में थोड़ा सा परिवर्तन भाग के सिल्हूट को संकुचित कर देता है। कापियर पर लंबे भागों को भागों में नुकीला किया जाता है। सममित आकृतियों को किनारे से मध्य तक संसाधित किया जाता है, फिर वर्कपीस को पलट दिया जाता है और दूसरे भाग को संसाधित किया जाता है (चित्र 8 जी)।
कटिंग मोड चयन
खराद पर मुख्य काटने की गति के लिए विभिन्न बिंदुकटिंग एज अलग है और वर्कपीस के रोटेशन की धुरी की दूरी पर निर्भर करता है। औसत गतिके लिये मध्य बिंदुसूत्र द्वारा निर्धारित किया जाता है:
वी सीपी \u003d πडी सीपी एन / (60 1000)
जहां डी सीपी - वर्कपीस का औसत व्यास, मिमी;
एन- धुरी गति, आरपीएम;
वर्कपीस के व्यास के आधार पर स्पिंडल गति का चयन किया जाता है, 400 मिमी से अधिक के व्यास के साथ एक फेसप्लेट स्थापित करते समय, स्पिंडल की गति 800 आरपीएम से अधिक नहीं होनी चाहिए।
लकड़ी के लिए मुख्य काटने की गति नरम चट्टानें 10-12 मी/से, दृढ़ लकड़ी के लिए 0.5-3 मी/से।
0.8 मिमी से अधिक नहीं परिष्करण के लिए 1.6-2 मिमी मोटे तौर पर प्रति धुरी क्रांति के लिए अनुदैर्ध्य फ़ीड। प्रति स्पिंडल क्रांति क्रॉस फीड 1.2 मिमी से अधिक नहीं होनी चाहिए।
सीएनसी खराद पर मशीनिंग भागों
सीएनसी खराद में काटने के उपकरण के रूप में अंत मिल होते हैं या अंत मिलों और डिस्क कटर के साथ संयुक्त होते हैं।
एंड मिल के साथ एक भाग को संसाधित करते समय, आप वर्कपीस पर एक अलग आकृति वाला प्रोफ़ाइल प्राप्त कर सकते हैं। भविष्य के हिस्से के आकार के आधार पर, कटर की गति और वर्कपीस के रोटेशन की गति सॉफ्टवेयर का उपयोग करके निर्धारित की जाती है।
चावल। 9. एक सीएनसी खराद पर एक मूर्तिकला बनाना
एंड और डिस्क कटर वाली मशीनें आपको वर्कपीस को मोड़ने की प्रक्रिया को तेज करने की अनुमति देती हैं। डिस्क कटर प्रारंभिक खुरदरापन करता है, एंड मिलपरिष्करण।
चावल। 10. डिस्क कटर के साथ वर्कपीस को संसाधित करना
चावल। 11. वर्कपीस को एंड मिल के साथ प्रोसेस करना
वर्कपीस को मोड़ने के बाद, अंतिम परिष्करण और काटने के निशान को हटाने के लिए, इसे सैंडपेपर से उपचारित किया जाता है, आमतौर पर छोटी चौड़ाई के एक टुकड़े का उपयोग किया जाता है, जिसे पूरे वर्कपीस में एक तना हुआ अवस्था में ले जाया जाता है।
चावल। 12. सैंडपेपर के साथ वर्कपीस को संसाधित करना
साहित्य:
1. बुरिकोव वी.जी., व्लासोव वी.एन. हाउस नक्काशी - एम।: यूरेशियन रीजन कंपनी के साथ रूस का निवा, 1993-352 पी।
2. वेतोश्किन यू.आई., स्टार्टसेव वी.एम., ज़ादिमिदको वी.टी.
लकड़ी की कला: पाठ्यपुस्तक। भत्ता। येकातेरिनबर्ग: यूराल। राज्य वन इंजीनियरिंग अन-टी. 2012.
3. ग्लिकिन एम.एस. मशीन "यूनिवर्सल" पर सजावटी लकड़ी का काम।- एम।: लेसन। प्रोम-सेंट, 1987.-208 पी।
4. कोरोटकोव वी.आई. वुडवर्किंग मशीन: शुरुआत के लिए एक पाठ्यपुस्तक। प्रो शिक्षा। - एम.6 प्रकाशन केंद्र "अकादमी", 203.-304 पी।
5. लर्नर पी.एस., लुक्यानोव पी.एम. टर्निंग और मिलिंग व्यवसाय: प्रो. कक्षा 8-11 में छात्रों के लिए भत्ता। औसत स्कूल - दूसरा संस्करण।, संशोधित - एम।: शिक्षा, 1990। - 208 पी।
प्रति जटिल तरीकेएक खराद पर वर्कपीस सेटिंग्स में शामिल हैं: एक 4-जबड़े गैर-आत्म-केंद्रित चक में स्थापना, एक फेसप्लेट पर, चौकोर, स्थिर आराम में और मशीनिंग सनकी भागों में वर्कपीस की स्थापना। उन सभी को या तो स्थिरता की एक विशेष सेटिंग की आवश्यकता होती है, या रोटेशन की धुरी के सापेक्ष वर्कपीस के संरेखण की आवश्यकता होती है।
§ 1. 4-जबड़े चक में मशीनिंग
गैर-परिपत्र वर्कपीस को ठीक करने के लिए, असमान सतहों के साथ कास्टिंग और फोर्जिंग, और कुछ अन्य काम, जबड़े के स्वतंत्र आंदोलन के साथ 4-जबड़े चक का उपयोग किया जाता है।
कोव (चित्र। 236)। वे एक शरीर 2 से मिलकर बनता है, 3 का समर्थन करता है, शिकंजा 4 और कैम 5. कैम को आगे या पीछे के रूप में इस्तेमाल किया जा सकता है। इस तरह के चक में रिक्त स्थान की क्लैंपिंग और सेंटरिंग अलग से की जाती है। चक को एडेप्टर फ्लैंज का उपयोग करके स्पिंडल के थ्रेडेड सिरे पर लगाया जाता है। फ्लैंग्ड स्पिंडल डिज़ाइन वाली मशीनों के लिए, माउंटिंग होल सीधे चक बॉडी में बनाया जाता है।
4-जबड़े चक के शरीर का उपयोग मशीनी समर्थन सतह के साथ वर्कपीस को माउंट करने और क्लैंप करने के लिए एक फेसप्लेट के रूप में किया जा सकता है। इस प्रयोजन के लिए, यह बढ़ते बोल्टों को स्थापित करने के लिए लम्बी खांचे के माध्यम से प्रदान करता है। कार्ट्रिज बनते हैं कई आकार* बाहरी व्यास 160 से 1000 मिमी तक।
इस तरह के चक में वर्कपीस के प्रसंस्करण की एक विशेषता चक (धुरी) की धुरी के साथ मशीनीकृत होने वाली सतह की धुरी को संरेखित करने की आवश्यकता है। यह चाक जोखिम के अनुसार या मार्कअप के अनुसार रिक्त स्थान का मिलान करके किया जाता है,
पहले मामले में (चित्र 237, ए), चाक का एक टुकड़ा धीरे-धीरे घूमने वाले वर्कपीस की सत्यापित सतह पर लाया जाता है और रोटेशन की धुरी के साथ इसकी सांद्रता चाक जोखिम के प्रकार से निर्धारित होती है। हाथों को नुकसान न पहुंचाने के लिए, चाक बार को वर्कपीस के अक्ष के स्तर पर थोड़ा नीचे की ओर ढलान के साथ रखा जाता है, और अधिक स्थिरता के लिए दायाँ हाथसमर्थन छोड़ दिया। यदि जोखिम का निशान पूरी परिधि के साथ स्थित है, जो पहली जांच के दौरान बहुत दुर्लभ है, तो वर्कपीस की स्थिति
सही।
जब जांच की जा रही सतह के केवल एक छोटे से क्षेत्र पर जोखिम रहता है, तो जोखिम के विपरीत कैम को स्थानांतरित करके वर्कपीस की स्थिति को समायोजित किया जाता है।
यदि वर्कपीस में अपेक्षाकृत सपाट या पूर्व-उपचारित सतह है, तो एक समान संरेखण एक बेंच मोटाई गेज के साथ किया जाता है, जैसा कि अंजीर में दिखाया गया है। 237बी. एक विशेष प्लेट या क्रॉस स्लाइड के ऊपरी तल पर स्थापित मोटाई गेज सुई को एक छोटे से अंतराल के साथ जांचने के लिए सतह पर लाया जाता है और, धुरी की कम गति को चालू करके, परिधि के चारों ओर इसकी एकरूपता निर्धारित करता है। संबंधित कैम को शिफ्ट करके चक में वर्कपीस की स्थिति को बदलकर, वे इसे छोटा कर देते हैं। फिर शीर्षक अंत में तय हो जाता है।
दूसरी विधि के अनुसार, रियर सेंटर या मोटाई गेज का उपयोग करके वर्कपीस के अंत में अंकन करके संरेखण किया जाता है।
पीछे के केंद्र के शीर्ष को केंद्र अंकन लाइनों (छवि 237, सी) के चौराहे बिंदु पर छिद्रित अवकाश में डाला जाता है, वर्कपीस को केंद्र के साथ चक बॉडी के अंत तक दबाया जाता है और इस स्थिति में कैम के साथ तय किया जाता है। .
मोटाई गेज (छवि 237, डी) के साथ मिलान करते समय, इसे स्थापित किया जाता है। कैलीपर या एक विशेष प्लेट के क्रॉस स्लाइड का तल। मोटाई गेज सुई, पीछे के केंद्र के शीर्ष की ऊंचाई पर सेट की जाती है, वर्कपीस के अंतिम चेहरे की केंद्र रेखाओं पर लाई जाती है और प्रत्येक पंक्ति की स्थिति को अनुप्रस्थ आंदोलन द्वारा वैकल्पिक रूप से सत्यापित किया जाता है। इस मामले में, केंद्र रेखा, जब वर्कपीस को 180 ° घुमाया जाता है, को पूरी लंबाई में मोटाई गेज सुई के शीर्ष के साथ जोड़ा जाना चाहिए।
ये सुलह बैच से पहले भाग के निर्माण के दौरान ही की जाती है। शेष भागों को 4-जबड़े चक में दो आसन्न जबड़ों के खिलाफ दबाकर सही ढंग से उन्मुख किया जाता है जो वर्कपीस को अलग करते समय हिलते नहीं हैं।
§ 2. एक फेसप्लेट और एक वर्ग पर प्रसंस्करण
लीवर या केस जैसे फ्री-फॉर्म वाले हिस्से जिन्हें 4-जबड़े चक में सही ढंग से स्थापित नहीं किया जा सकता है, उन्हें फेसप्लेट पर लगाया जाता है। स्थापना की इस पद्धति का भी सहारा लिया जाता है, यदि सतह के अक्ष की एक सख्त लंबवतता को अंत तक, या भाग के आधार तक बनाए रखने की आवश्यकता होती है।
फेसप्लेट 1 (चित्र। 238) एक हब के साथ एक कच्चा लोहा डिस्क है, जो स्टिफ़नर के साथ रिवर्स साइड पर प्रबलित है,
हब होल स्पिंडल के सामने के छोर के आकार के अनुसार बनाए जाते हैं, जिस पर फेसप्लेट स्थापित और तय होता है।
फ़ेसप्लेट का अगला सिरा अपनी धुरी पर सख्ती से लंबवत है। इसमें टी-आकार और बढ़ते बोल्ट के लिए खांचे हैं। फेसप्लेट 4-जबड़े चक के शरीर जैसा दिखता है, जिसे कभी-कभी उसी उद्देश्य के लिए उपयोग किया जाता है।
वर्कपीस को क्लैम्प और बोल्ट के साथ फेसप्लेट के अंत के खिलाफ दबाया जाता है, और प्रसंस्करण के दौरान विस्थापन को रोकने के लिए, इसे अतिरिक्त रूप से साइड सपोर्ट के साथ दबाया जाता है। यह बन्धन अंजीर में दिखाया गया है। 238. भाग 4 को दो क्लैंप 2 और बोल्ट के साथ फेसप्लेट के खिलाफ दबाया जाता है। क्लैम्प का अगला सिरा भाग पर टिका होता है, पिछला सिरा स्टैंड पर टिका होता है। 8. साइड सपोर्ट यहां स्क्रू 6 हैं, जो 5 में खराब हो गए हैं। फेसप्लेट से जुड़े वर्ग।
फेसप्लेट पर लगे वर्कपीस में साफ-सुथरा मशीनी सपोर्ट (फेसप्लेट के सामने) होना चाहिए। उन्हें ठीक करते समय, आपको निम्नलिखित नियमों का पालन करना होगा।
1. मजबूत पकड़ बनाने के लिए क्लैंप बोल्ट को यथासंभव भाग के करीब रखा जाना चाहिए।
2. नट्स को पहले कमजोर रूप से कस लें, फिर अंत में।
3. क्लैम्प्स को, यदि संभव हो, फेसप्लेट पर समर्थित हिस्से के स्थानों पर माउंट करें।
4. यदि तीसरे नियम का पालन नहीं किया जा सकता है, तो भाग को झुकने से बचने के लिए नट्स को बहुत अधिक कसने न दें।
5. समर्थन को इतनी ऊंचाई पर उठाएं कि क्लैंप
फेसप्लेट के वर्किंग प्लेन के समानांतर स्थित है।
बैच के पहले ब्लैंक को फेसप्लेट पर उसी तरह से सत्यापित किया जाता है जैसे 4-जबड़े चक में। मेवों को थोड़ा दबा कर, इसे किसी भी जगह ले जाया जा सकता है साइड लाइटहथौड़े से वार। शेष रिक्त स्थान साइड सपोर्ट द्वारा सही ढंग से उन्मुख हैं।
यदि वर्कपीस के गुरुत्वाकर्षण के केंद्र को रोटेशन की धुरी से विस्थापित किया जाता है, तो काउंटरवेट बैलेंसिंग 7 का उपयोग किया जाता है (चित्र 238)। इस क्रम में संतुलन किया जाता है। काउंटरवेट को पहले वर्कपीस के गुरुत्वाकर्षण के केंद्र के विपरीत, अपनी धुरी से कुछ दूरी पर फेसप्लेट पर तय किया जाता है। फिर, गियरबॉक्स तंत्र से स्पिंडल को डिस्कनेक्ट करने के बाद, मैन्युअल रूप से फेसप्लेट को चालू करें। यदि उत्तरार्द्ध अलग-अलग स्थितियों में रुकता है, तो संतुलन सही है। अन्यथा, काउंटरवेट को रोटेशन की धुरी से वांछित दिशा में स्थानांतरित कर दिया जाता है और संतुलन को फिर से दोहराया जाता है।
सतह की धुरी के समानांतर या कोणीय व्यवस्था के साथ भागों को आधार पर मशीनीकृत किया जाता है, जो वर्ग 4 (छवि 239) पर स्थापित होते हैं, जो बोल्ट और नट्स के साथ फेसप्लेट से जुड़ा होता है। भाग 3 (इस मामले में, असर आवास), बदले में, वर्ग के क्षैतिज शेल्फ पर क्लैंप 2 के साथ तय किया गया है और काउंटरवेट 1 द्वारा संतुलित किया गया है।
वर्ग के साथ बैच से पहले वर्कपीस का संरेखण चाक जोखिम या अंकन के अनुसार उपरोक्त विधियों में से एक द्वारा किया जाता है।
इन कार्यों के लिए भी इस्तेमाल किया जा सकता है। 4-जबड़े चक, जिनमें से एक जबड़े को एक वर्ग से बदल दिया जाता है।
3. स्थिर अवस्था में प्रसंस्करण
स्थिर रेस्ट गैर-कठोर शाफ्ट के प्रसंस्करण में उपयोग किए जाने वाले अतिरिक्त समर्थन उपकरण कहलाते हैं।
जिन शाफ्टों की लंबाई 12-15 व्यास से अधिक होती है, उन्हें आमतौर पर गैर-कठोर माना जाता है। इस तरह के हिस्से झुकते हैं, काटने वाले बल की कार्रवाई के तहत कंपन करते हैं और उनका अपना वजन होता है, जो कटर के छिलने का कारण बनता है, प्रसंस्करण की गुणवत्ता को कम करता है और काटने के मोड में कमी को मजबूर करता है। उत्पादकता में वृद्धि, लंबे शाफ्ट स्थिर आराम द्वारा समर्थित हैं।
खराद स्थिर आराम से सुसज्जित हैं सामान्य उद्देश्यदो प्रकार - फिक्स्ड और मोबाइल।
स्थिर आराम (चित्र। 240, ए) में एक आधार 7, एक टिका हुआ कवर 3 और तीन कैम 2 स्वतंत्र आंदोलन के साथ होते हैं। लुनेट को फ्रेम 10 के मध्य गाइड पर स्थापित किया गया है और एक ब्रैकेट 9 के साथ तय किया गया है, जिसे बोल्ट और नट के साथ गाइड के किनारों के खिलाफ दबाया जाता है। क्लैंप 5 द्वारा आवश्यक स्थिति में तय किया गया। कवर 3, अक्ष 1 द्वारा आधार से जुड़ा हुआ है, जब जारी क्लैंप 6 को स्थिर आराम में भाग स्थापित करने के लिए त्याग दिया जा सकता है। कैम की युक्तियाँ विनिमेय हैं। वो हैं
कच्चा लोहा या कांस्य से बना। उच्च काटने की गति के साथ काम करने के लिए, इसके बजाय रोलिंग बीयरिंग स्थापित किए जाते हैं।
चल स्थिर आराम (चित्र। 240, बी) में एक शरीर 5 होता है, जिसका ऊपरी भाग दाईं ओर मुड़ा हुआ होता है, और दो समायोज्य कैम 2 स्वतंत्र आंदोलन के साथ होते हैं। उत्तरार्द्ध को 4 और 3 हैंडल के साथ आवश्यक स्थिति में स्थानांतरित और तय किया जा सकता है। कैलीपर कैरिज 1 के बाईं ओर स्क्रू 6 के साथ स्थापित और तय किया गया है।
चंद्रकला के माध्यम से भागों के प्रसंस्करण पर विचार करें (चित्र 241)।
वर्कपीस को फिक्स्ड लनेट में स्थापित करने से पहले, उस पर एक उथला खांचा (लगभग बीच में) मशीनीकृत किया जाता है।
सतह के इस क्षेत्र के अपवाह को खत्म करने के लिए स्थिर आराम के कैमरों की तुलना में व्यापक। वर्कपीस के विक्षेपण से बचने के लिए, खांचे को थ्रू-थ्रस्ट कटर से मुख्य कटिंग एज के झुकाव के नकारात्मक कोण के साथ मशीनीकृत किया जाता है। कट और फीड की गहराई छोटी होनी चाहिए।
एक बहुत लंबा शाफ्ट सावधानीपूर्वक खांचे के साथ भी झुक सकता है। इस मामले में, खांचे को पहले हेडस्टॉक के थोड़ा करीब घुमाया जाता है, इस जगह पर एक स्थिर आराम स्थापित किया जाता है, और फिर भाग के बीच में एक दूसरा खांचा बनाया जाता है।
उसके बाद, स्थिर आराम स्थापित किया जाता है और फ्रेम पर तय किया जाता है ताकि यह शाफ्ट के खांचे के खिलाफ स्थित हो। इसके कैम समान रूप से, बिना मजबूत दबाव के, खांचे की सतह पर लाए जाते हैं और स्थिर होते हैं। इन क्रियाओं को करते समय, असमान कैम क्लैम्पिंग के मामले में भाग के विक्षेपण की संभावना को ध्यान में रखना चाहिए। इससे बचने के लिए, स्थिर कैमरों को पहले एक छोटी गर्दन पर लगाया जा सकता है, जिसे पीछे के केंद्र में शाफ्ट के अंत में मशीनीकृत किया जाता है। इस तरह की एक अतिरिक्त गर्दन का व्यास ल्युनेट कैम के लिए खांचे के व्यास के अनुसार बनाया गया है।
भागों के एक बैच का निर्माण करते समय, एक छोटे कठोर खराद पर काम करने से पहले एक बार स्थिर आराम कैम स्थापित करना सुविधाजनक होता है।
मशीन पर वर्कपीस को ठीक करने के बाद, शाफ्ट के पहले आधे हिस्से को (लूनेट में) घुमाया जाता है, और फिर, शेष भाग को फिर से स्थापित करने के बाद। शाफ्ट की मशीनी सतह के साथ ल्युनेट को दूसरी बार स्थापित किया गया है। घर्षण को कम करने के लिए, लूनेट कैम के खांचे को तेल से चिकनाई की जाती है।
लंबे शाफ्ट के अंत में फेसिंग, सेंटरिंग और होल-मेकिंग के लिए स्थिर स्थिर रेस्ट का भी उपयोग किया जाता है, यदि बाद वाला स्पिंडल बोर में फिट नहीं होता है। इस मामले में, शाफ्ट
एक छोर चक में तय किया गया है, और दूसरा सिरा लुनेट के कैमरों में स्थापित किया गया है।
लंबी बेलनाकार सतहों को संसाधित करते समय जंगम आराम का उपयोग किया जाता है। उसकी मुट्ठी निपटाने कृन्तक के दायीं ओर 10-15 मिमी की दूरी पर। आवश्यक कटर ऑफ़सेट किया जाता है शीर्ष स्लाइडकैलिपर
बैच से पहले भाग की मशीनी सतह पर स्थिर आराम कैम स्थापित किए जाते हैं। ऐसा करने के लिए सबसे पहले इसके सिरे को पीस लें छोटा प्लॉटआवश्यक व्यास के लिए 20-25 मिमी लंबा, जिसके लिए स्थिर कैम को करीब लाया जाता है। यदि काम बिना शीतलन के किया जाता है, तो समय-समय पर उपचारित सतह को लुनेट कैम के सामने तेल से चाटना आवश्यक है।
गैर-कठोर लंबे शाफ्ट, यहां तक कि स्थिर आराम में संसाधित होने पर भी, एक विक्षेपण के साथ प्राप्त किए जाते हैं। इसलिए, मोड़ खत्म करने से पहले उन्हें सही किया जाता है। संपादन निम्न प्रकार से सही कोष्ठक (चित्र 242) के साथ किया जाता है। केंद्रों में घूमते हुए शाफ्ट की सतह पर विभिन्न स्थानोंलंबाई के साथ चाक का एक टुकड़ा लाया जाता है, जबकि उस पर चाक के निशान बने रहते हैं, जो विक्षेपण के स्थान को दर्शाते हैं। यदि सभी निशान शाफ्ट के एक तरफ हैं, तो विक्षेपण एकतरफा है।
सबसे बड़े विक्षेपण का स्थान चाक ट्रेस के चाप के परिमाण से निर्धारित होता है। जहां विक्षेपण सबसे अधिक होता है, चाप की लंबाई सबसे कम होती है। इस जगह पर, सही ब्रैकेट 2 का स्क्रू 1 स्थापित किया गया है, जैसा कि अंजीर में दिखाया गया है। 242. चूंकि ड्रेसिंग के दौरान शाफ्ट थोड़ा लंबा हो जाता है, इससे पहले पिछला केंद्र निम्नानुसार होता है
थोड़ा ढीला।
अक्सर शाफ्ट में विभिन्न दिशाओं में एक जटिल विक्षेपण होता है। इस मामले में, विक्षेपण की प्रमुख दिशा चाक के निशान से पाई जाती है। सबसे पहले, वर्गों को ठीक किया जाता है जहां विक्षेपण की दिशा प्रचलित एक के विपरीत होती है, ताकि सामान्य एकतरफा विक्षेपण प्राप्त किया जा सके। फिर शाफ्ट को सीधा किया जाता है, जैसा कि ऊपर बताया गया है।
§ 4. सनकी भागों की मशीनिंग
इन भागों में सनकी, सनकी और क्रैंकशाफ्ट शामिल हैं (चित्र। 243)। उन्हें समानांतर स्थानांतरित कुल्हाड़ियों के साथ सतहों की उपस्थिति की विशेषता है। कुल्हाड़ियों के विस्थापन की मात्रा को उत्केंद्रता कहा जाता है।
खराद पर सनकी भागों का प्रसंस्करण किया जा सकता है: 1) सी। 3-जबड़े चक; 2) एक खराद का धुरा पर; 3) 4-जबड़े की चक में या फेसप्लेट पर; 4) कापियर द्वारा; 5) विस्थापित केंद्रों में; 6)। सेंट्रीफ्यूज का उपयोग करना।
सनकी प्रसंस्करण। पहले चार तरीकों में से एक में छोटी लंबाई के सनकी को मशीनीकृत किया जा सकता है।
3-जबड़े की चक में, मशीनीकृत सनकी सतह की धुरी को कार्ट्रिज के जबड़े में से एक के नीचे एक अस्तर स्थापित करके रोटेशन की धुरी के साथ संरेखित किया जाता है (चित्र 244, ए)। अभ्यास के लिए पर्याप्त सटीकता के साथ इसकी मोटाई सूत्र द्वारा निर्धारित की जा सकती है
स्थापना त्रुटि को कम करने के लिए, रिंग से अस्तर को काटने की सिफारिश की जाती है, जिसका छेद वर्कपीस के व्यास के अनुसार बनाया जाता है। अस्तर के उत्तल पक्ष पर, कोनों को काट दिया जाता है ताकि असर प्लेटफॉर्म बी कैम की कामकाजी सतह की चौड़ाई से कम हो।
यदि सनकी वर्कपीस में पहले से बना हुआ छेद है, तो इसे मैंड्रेल (चित्र। 244, बी) पर स्थापना के साथ संसाधित किया जाता है। उत्तरार्द्ध के सिरों पर दो जोड़ी केंद्र छेद होते हैं, जो कि विलक्षणता की मात्रा से ऑफसेट होते हैं। केंद्रों में दो प्रतिष्ठानों के लिए प्रसंस्करण किया जाता है। पहली सेटिंग में, छेद एए के सापेक्ष, सतह जी को दूसरे में बदल दिया जाता है
छेद B-B के संबंध में, सतह C को घुमाया जाता है।
सनकी की ऑफसेट सतह को 4-जबड़े चक या फेसप्लेट में भी बनाया जा सकता है। इस मामले में, मशीनी सतह की स्थिति को अंकन द्वारा वर्कपीस के अंत में पाया जाता है, और फिर इसकी धुरी को अंजीर में वर्णित विधियों में से एक द्वारा धुरी अक्ष के साथ जोड़ा जाता है। 237, विग.
कापियर के साथ सनकी मोड़ते समय (चित्र। 244, सी), एक कापियर 3, एक मध्यवर्ती आस्तीन 4, एक वर्कपीस 5, एक वॉशर 6, एक नट 7 के साथ तय किया गया, मैंड्रेल 2 पर स्थापित किया गया है। मैंड्रेल के साथ स्थापित किया गया है स्पिंडल छेद में एक पतला टांग और एक लंबे पेंच के साथ कड़ा या पीछे के केंद्र द्वारा दबाया जाता है। टूल होल्डर में एक चौड़ा रोलर 1 और एक कटर 8 लगाया गया है। क्रॉस फीड स्क्रू के बजाय कैलीपर में स्थापित स्प्रिंग द्वारा रोलर को कापियर के खिलाफ कसकर दबाया जाता है। जब आप कैलीपर के अनुदैर्ध्य आंदोलन को चालू करते हैं, तो कटर भाग को कॉपियर के प्रोफाइल के साथ मोड़ देगा।
सनकी और क्रैंकशाफ्ट की मशीनिंग। ऐसे शाफ्ट की सतहों को ऑफसेट केंद्रों में संसाधित किया जाता है, अगर उन्हें सिरों पर रखा जाता है - भागों, या केंद्र शिफ्टर्स की मदद से।
पहला तरीका अंजीर में दिखाया गया है। 245 क. ऐसा करने के लिए, वर्कपीस को पहले सामान्य में बदल दिया जाता है केंद्र ए-एव्यास डी तक। केंद्र छेद की दूसरी जोड़ी बी-बी को वर्कपीस के सिरों पर चिह्नित और छिद्रित किया जाता है, जिसके बाद इसे ड्रिल किया जाता है। छोटे वर्कपीस के लिए, यह एक खराद पर केंद्रित करके मैन्युअल रूप से किया जा सकता है। इस मामले में, ड्रिलिंग चक का उपयोग करके मशीन स्पिंडल में केंद्र ड्रिल स्थापित किया जाता है, और वर्कपीस, बाएं हाथ में क्लैंप किया जाता है, पीछे के केंद्र पर एक छिद्रित अवकाश द्वारा समर्थित होता है और टेलस्टॉक क्विल को स्थानांतरित करके ड्रिल को आगे बढ़ाया जाता है।
बड़े आकार के वर्कपीस के लिए, ऑफसेट सेंटर होल को सेंटरिंग मशीनों पर या एक विशेष उपकरण के माध्यम से बनाया जाता है - एक जिग ऑन ड्रिलिंग मशीन.
यदि सनकीपन बड़ा है और भाग के अंत में विस्थापित केंद्र छिद्रों को रखने की अनुमति नहीं देता है, तो उन्हें हटाने योग्य सेंट्रीफ्यूज में बनाया जाता है, जो शाफ्ट के पूर्व-मोड़ अंत पत्रिकाओं के लिए तय किए जाते हैं। इस मामले में, केंद्र छिद्रों की ऑफसेट जोड़ी को एक ही व्यास वाले विमान में सख्ती से स्थित होना चाहिए। ऐसी क्रैंकशाफ्ट प्रसंस्करण विधि का एक उदाहरण अंजीर में दिखाया गया है। 245बी. केंद्र के साथ वर्कपीस स्थापित करते समय स्वदेशी गर्दन 3 मुड़ जाती है छेद ए-एकेंद्र शिफ्टर्स 7, ऑफसेट सेंटर में क्रमशः रॉड जर्नल 2 और 5 को जोड़ना छेद बी-बीऔर वी-वी।
असंतुलित भागों का संतुलन एक काउंटरवेट 7 के साथ किया जाता है, जो ड्राइविंग फेसप्लेट 8 पर तय होता है, और शाफ्ट की कठोरता को स्पेसर रॉड्स 4 और 6 द्वारा बढ़ाया जाता है।
मुख्य करने के लिए
खंड पांच
बुनियादी संचालन और कार्य,
खराद पर प्रदर्शन किया
अध्याय XI
बाहरी बेलनाकार सतहों को मोड़ना
खराद पर, उन हिस्सों को संसाधित करना संभव है जिनकी सतहों में क्रांति के निकायों का रूप होता है। मैकेनिकल इंजीनियरिंग में उपयोग किए जाने वाले अधिकांश हिस्सों में बेलनाकार सतह होती है, जैसे रोलर्स, बुशिंग इत्यादि।
1. अनुदैर्ध्य मोड़ के लिए कटर
अनुदैर्ध्य मोड़ के लिए, कटर के माध्यम से उपयोग किया जाता है। पासिंग कटर में विभाजित हैं प्रारूपऔर परिष्करण.
रफ कटर (चित्र। 99) को किसी न किसी मोड़ के लिए डिज़ाइन किया गया है - छीलने, अतिरिक्त धातु को जल्दी से हटाने के लिए किया जाता है; उन्हें अक्सर खुरदरा कहा जाता है। इस तरह के कटर आमतौर पर एक वेल्डेड या सोल्डर, या यंत्रवत् संलग्न प्लेट के साथ बनाए जाते हैं और एक लंबे . के साथ प्रदान किए जाते हैं अग्रणी. कटर का शीर्ष त्रिज्या r = 1-2 मिमी के साथ गोल होता है। अंजीर पर। 99, लेकिन किसी न किसी सीधी रेखा के कटर को दिखाता है, और अंजीर में। 99, बी - मुड़ा हुआ। कारतूस के जबड़े के पास स्थित भागों की सतहों को मोड़ते समय और सिरों को ट्रिम करने के लिए कटर का मुड़ा हुआ आकार बहुत सुविधाजनक होता है। खुरदुरे कटर से मुड़ने के बाद, भाग की सतह पर बड़े जोखिम होते हैं; मशीनी सतह की गुणवत्ता इसलिए कम है।
फिनिशिंग कटर का उपयोग भागों के अंतिम मोड़ के लिए किया जाता है, यानी सटीक आयाम और प्रसंस्करण की एक साफ, यहां तक कि सतह प्राप्त करने के लिए। मौजूद विभिन्न प्रकारसाफ कटर।
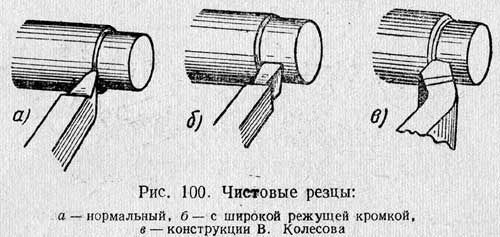
अंजीर पर। 100, एक परिष्करण कटर दिखाता है, जो मुख्य रूप से 2-5 मिमी के बराबर वक्रता के बड़े दायरे में ड्राफ्ट से भिन्न होता है। इस प्रकार के कटर का उपयोग के लिए किया जाता है मछली पकड़ने का काम, जो कट की छोटी गहराई और कम फ़ीड के साथ उत्पादित होते हैं। अंजीर पर। 100b वर्कपीस की धुरी के समानांतर एक विस्तृत कटिंग एज के साथ एक फिनिशिंग कटर दिखाता है। यह कटर उच्च फ़ीड दरों पर ठीक चिप हटाने की अनुमति देता है और एक साफ और चिकनी सतह खत्म करता है। अंजीर पर। 100, सी वी। कोलेसोव के कटर को दिखाता है, जो आपको 1-2 मिमी की गहराई के साथ बड़े फ़ीड (1.5-3 मिमी / रेव) के साथ काम करते समय एक साफ और सुचारू रूप से मशीनी सतह प्राप्त करने की अनुमति देता है (चित्र देखें। 62) )
2. कटर को स्थापित करना और ठीक करना
मोड़ने से पहले, उपकरण धारक में कटर को सही ढंग से स्थापित करना आवश्यक है, यह सुनिश्चित कर लें कि इससे निकलने वाले कटर का हिस्सा जितना संभव हो उतना छोटा है - इसके कोर की ऊंचाई 1.5 से अधिक नहीं।
लंबे समय तक ओवरहैंग के साथ, कटर ऑपरेशन के दौरान कांप जाएगा, परिणामस्वरूप, कुचलने के निशान के साथ मशीन की सतह असमान, लहरदार हो जाएगी।
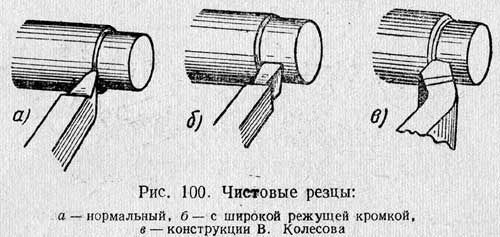
अंजीर पर। 101 टूल होल्डर में कटर की सही और गलत स्थापना को दर्शाता है।
ज्यादातर मामलों में, टूल टिप को मशीन केंद्रों की ऊंचाई पर सेट करने की अनुशंसा की जाती है। ऐसा करने के लिए, अस्तर का उपयोग किया जाता है (दो से अधिक नहीं), उन्हें कटर की पूरी सहायक सतह के नीचे रखकर। परतएक फ्लैट स्टील शासक 150-200 मिमी लंबा है, जिसमें सख्ती से समानांतर ऊपरी और निचली सतह होती है। कटर को स्थापित करने के लिए आवश्यक ऊंचाई प्राप्त करने के लिए टर्नर में विभिन्न मोटाई के ऐसे अस्तर का एक सेट होना चाहिए। इस उद्देश्य के लिए यादृच्छिक प्लेटों का उपयोग नहीं किया जाना चाहिए।
अंजीर में दिखाए गए अनुसार अस्तर को कटर के नीचे रखा जाना चाहिए। शीर्ष पर 102।
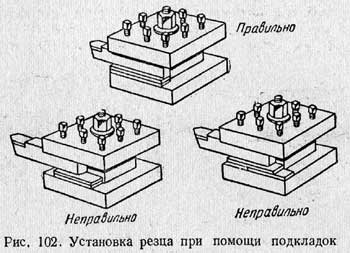
कृन्तक के शीर्ष की ऊंचाई की स्थिति की जांच करने के लिए, इसके शीर्ष को पूर्व-कैलिब्रेटेड केंद्रों में से एक पर लाएं, जैसा कि अंजीर में दिखाया गया है। 103. इसी उद्देश्य के लिए, आप केंद्र की ऊंचाई पर, टेलस्टॉक की क्विल पर खींचे गए जोखिम का उपयोग कर सकते हैं।
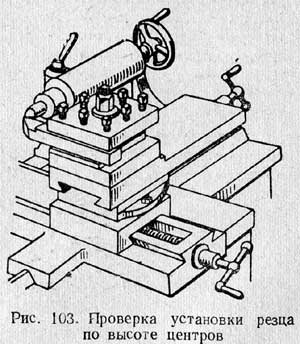
उपकरण धारक में कटर की फिक्सिंग विश्वसनीय और टिकाऊ होनी चाहिए: कटर को कम से कम दो बोल्ट के साथ तय किया जाना चाहिए। कटर को सुरक्षित करने वाले बोल्ट समान रूप से और कसकर कड़े होने चाहिए।
3. केंद्रों में भागों को स्थापित करना और ठीक करना
खराद पर भागों को संसाधित करने का एक सामान्य तरीका है केंद्रों में प्रसंस्करण(चित्र। 104)। इस विधि से वर्कपीस के सिरों पर सेंटर होल्स को प्री-ड्रिल किया जाता है - केंद्रविवरण। मशीन पर स्थापित होने पर, मशीन के फ्रंट और टेलस्टॉक्स के केंद्रों के बिंदु इन छेदों में प्रवेश करते हैं। हेडस्टॉक स्पिंडल से वर्कपीस में रोटेशन को स्थानांतरित करने के लिए, ड्राइवर चक 1 (अंजीर। 104), मशीन स्पिंडल पर खराब हो गया है, और क्लैंप 2, वर्कपीस पर स्क्रू 3 के साथ तय किया गया।
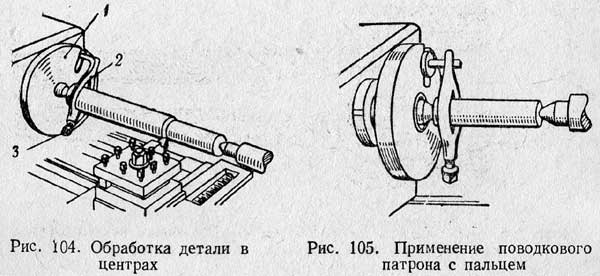
क्लैंप के मुक्त सिरे को कार्ट्रिज के खांचे (चित्र 104) या उंगली (चित्र 105) द्वारा पकड़ लिया जाता है और भाग को घुमाने का कारण बनता है। पहले मामले में, क्लैंप को मुड़ा हुआ बनाया जाता है (चित्र 104), दूसरे में - सीधा (चित्र। 105)। अंजीर में दिखाया गया पिन चक। 105, कार्यकर्ता के लिए खतरा बन गया है; सुरक्षा कवर के साथ ड्राइवर चक सुरक्षित है (चित्र 106)।
आवश्यक सामान खरादहैं केन्द्रों. आमतौर पर अंजीर में दिखाया गया केंद्र। 107, ए.
इसमें एक शंकु 1 होता है, जिस पर भाग लगा होता है, और एक पतला टांग 2 होता है। टांग को मशीन के हेडस्टॉक स्पिंडल और टेलस्टॉक क्विल के पतला बोर में बिल्कुल फिट होना चाहिए।
सामने का केंद्र स्पिंडल और वर्कपीस के साथ घूमता है, जबकि टेलस्टॉक केंद्र ज्यादातर मामलों में स्थिर होता है और घूमने वाले हिस्से के खिलाफ रगड़ता है। घर्षण गर्म हो जाता है और केंद्र की शंक्वाकार सतह और भाग के केंद्र छेद की सतह दोनों को खराब कर देता है। घर्षण को कम करने के लिए, पीछे के केंद्र को लुब्रिकेट करना आवश्यक है।
उच्च गति पर भागों को मोड़ते समय, साथ ही भारी भागों को संसाधित करते समय, केंद्र के तेजी से पहनने और केंद्र छेद के विकास के कारण टेलस्टॉक के निश्चित केंद्र पर काम करना असंभव है।
इन मामलों में करें आवेदन घूर्णन केंद्र. अंजीर पर। 108 टेलस्टॉक क्विल के पतला छेद में डाले गए घूर्णन केंद्र के डिजाइनों में से एक को दिखाता है। केंद्र 1 बॉल बेयरिंग 2 और 4 में घूमता है। अक्षीय दबाव को थ्रस्ट बॉल बेयरिंग द्वारा माना जाता है। केंद्र निकाय का पतला टांग 3 क्विल के पतला छेद से मेल खाता है।
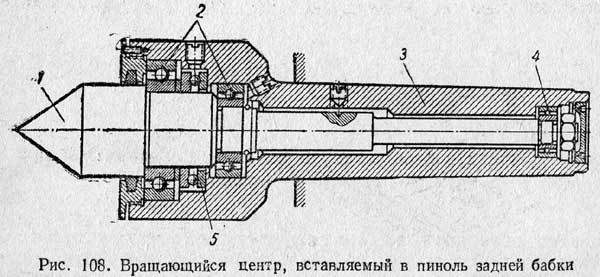
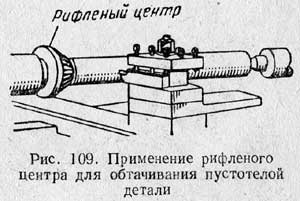
भागों को ठीक करने में लगने वाले समय को कम करने के लिए, क्लैम्प के बजाय अक्सर मैन्युअल क्लैम्पिंग वाले क्लैम्प का उपयोग किया जाता है। घुमावदार सामने केंद्र(चित्र। 109), जो न केवल भाग को केंद्र में रखता है, बल्कि एक पट्टा के रूप में भी कार्य करता है। जब पीछे के केंद्र द्वारा दबाया जाता है, तो गलियारों को वर्कपीस में काट दिया जाता है और इस तरह इसे घुमाया जाता है। खोखले भागों के लिए, बाहरी (चित्र। 110, ए) का उपयोग किया जाता है, और रोलर्स के लिए, आंतरिक (रिवर्स) नालीदार केंद्र (चित्र। 110, बी)।
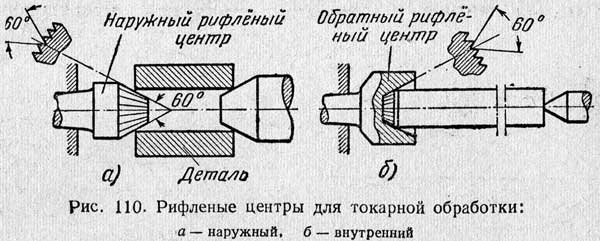
बन्धन की यह विधि आपको एक सेटिंग में पूरी लंबाई के साथ भाग को मोड़ने की अनुमति देती है। पारंपरिक केंद्र और कॉलर के साथ समान भागों को मोड़ना केवल दो सेटिंग्स में किया जा सकता है, जिससे प्रसंस्करण समय में काफी वृद्धि होती है।
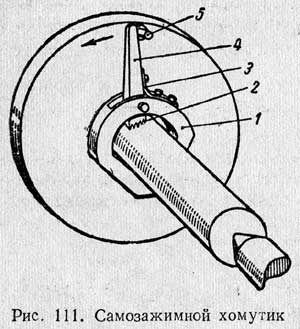
लाइट और मीडियम टर्निंग वर्क के लिए स्व-लॉकिंग क्लैंप. इनमें से एक कॉलर अंजीर में दिखाया गया है। 111. इस तरह के कॉलर के शरीर 1 में, धुरी पर एक कैम 4 स्थापित होता है, जिसके अंत में एक नालीदार सतह होती है। भाग पर कॉलर स्थापित करने के बाद, कैम की नालीदार सतह को नीचे के हिस्से के खिलाफ दबाया जाता है। वसंत की क्रिया 3. केंद्रों में स्थापना और मशीन शुरू करने के बाद, ड्राइविंग चक का पिन 5, कैम 4 को दबाकर, भाग को जाम कर देता है और इसे रोटेशन में सेट करता है। ये सेल्फ-लॉकिंग क्लैम्प्स गैर-उत्पादक समय को काफी कम कर देते हैं।
4. केंद्रों में प्रसंस्करण के लिए मशीन की स्थापना
केंद्रों में वर्कपीस को मोड़ते समय एक बेलनाकार सतह प्राप्त करने के लिए, यह आवश्यक है कि सामने और संदर्भ केंद्र धुरी के रोटेशन की धुरी पर हों, और कटर इस अक्ष के समानांतर चलता है। केंद्रों के सही स्थान की जांच करने के लिए, आपको पीछे के केंद्र को सामने की ओर ले जाना होगा (चित्र 112)। यदि केंद्र बिंदु संरेखित नहीं होते हैं, तो प्लेटिन पर टेलस्टॉक आवास की स्थिति को पृष्ठ 127 पर बताए अनुसार समायोजित किया जाना चाहिए।
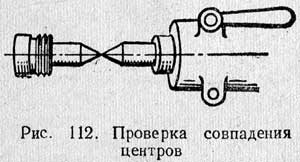
सेंटर मिसलिग्न्मेंट गंदगी या चिप्स के स्पिंडल या पाई-जीरो के टेंपर होल में जाने के कारण भी हो सकता है। इससे बचने के लिए, केंद्रों को स्थापित करने से पहले, धुरी के छेद और क्विल, साथ ही केंद्रों के शंक्वाकार भाग को सावधानीपूर्वक पोंछना आवश्यक है। यदि उसके बाद हेडस्टॉक का केंद्र, जैसा कि वे कहते हैं, "धड़कता है", तो यह दोषपूर्ण है और इसे दूसरे के साथ बदला जाना चाहिए।
मोड़ते समय, भाग गर्म हो जाता है और बढ़ जाता है, जबकि केंद्रों पर दबाव बढ़ जाता है। भाग को संभावित झुकने से रोकने के लिए, और पीछे के केंद्र को जाम होने से बचाने के लिए, समय-समय पर पीछे के केंद्र को छोड़ने की सिफारिश की जाती है, और फिर इसे फिर से सामान्य करने के लिए कस दिया जाता है। समय-समय पर भाग के पीछे के केंद्र छेद को अतिरिक्त रूप से चिकनाई करना भी आवश्यक है।
5. चक में भागों को स्थापित करना और सुरक्षित करना
छोटे हिस्से आमतौर पर चक में स्थापित और सुरक्षित होते हैं, जिन्हें सरल और आत्म-केंद्रित में विभाजित किया जाता है।
साधारण कारतूस आमतौर पर चार जबड़े (चित्र। 113) के साथ बनाए जाते हैं। ऐसे कारतूसों में, प्रत्येक कैम 1, 2, 3 और 4 को अपने स्क्रू 5 द्वारा दूसरों से स्वतंत्र रूप से स्थानांतरित किया जाता है। यह आपको बेलनाकार और गैर-बेलनाकार दोनों आकारों के विभिन्न भागों को स्थापित और ठीक करने की अनुमति देता है। चार-जबड़े चक में एक भाग स्थापित करते समय, इसे सावधानीपूर्वक संरेखित किया जाना चाहिए ताकि यह रोटेशन के दौरान हिट न हो।
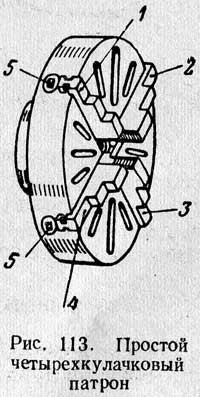
इसकी स्थापना के दौरान भाग का संरेखण एक मोटाई गेज का उपयोग करके किया जा सकता है। गहराई नापने वाले यंत्र को जांचने के लिए सतह पर लाया जाता है, जिससे उनके बीच 0.3-0.5 मिमी का अंतर रह जाता है; धुरी को घुमाते हुए, निगरानी करें कि यह अंतर कैसे बदलता है। अवलोकन के परिणामों के आधार पर, कुछ कैमरों को निचोड़ा जाता है और अन्य को तब तक दबाया जाता है जब तक कि भाग की पूरी परिधि के चारों ओर अंतर एक समान न हो जाए। उसके बाद, अंत में हिस्सा तय हो गया है।
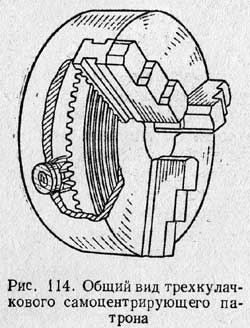
आत्म केंद्रित चक(चित्र। 114 और 115) ज्यादातर मामलों में, तीन-कैम का उपयोग किया जाता है, बहुत कम बार - दो-कैम। ये चक उपयोग करने के लिए बहुत सुविधाजनक हैं, क्योंकि उनमें सभी कैम एक साथ चलते हैं, जिससे कि एक बेलनाकार सतह (बाहरी या आंतरिक) वाला हिस्सा स्थापित हो और धुरी की धुरी के साथ ठीक हो; इसके अलावा, भाग की स्थापना और फिक्सिंग का समय काफी कम हो जाता है।
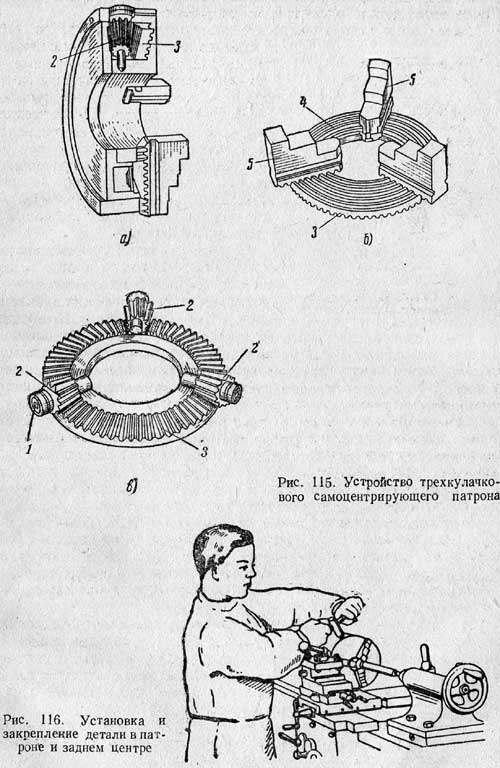
इसमें, कैम को एक कुंजी का उपयोग करके स्थानांतरित किया जाता है, जिसे तीन बेवल गियर 2 (छवि 115, सी) में से एक के टेट्राहेड्रल छेद 1 में डाला जाता है। इन पहियों को एक बड़े शंक्वाकार पहिया 3 (चित्र 115, बी) के साथ जोड़ा गया है। इस पहिए के पिछले फ्लैट की तरफ, एक मल्टी-टर्न सर्पिल ग्रूव 4 काटा जाता है (चित्र 115, बी)। सभी तीन कैम 5 अपने निचले प्रोट्रूशियंस के साथ इस खांचे के अलग-अलग घुमावों में प्रवेश करते हैं। जब गियर 2 में से एक को एक कुंजी के साथ घुमाया जाता है, तो रोटेशन को पहिया 3 में स्थानांतरित कर दिया जाता है, जो घूमता है, सर्पिल खांचे के माध्यम से 4 खांचे के साथ चलता है कारतूस के शरीर का एक साथ और समान रूप से तीनों कैम। जब एक सर्पिल खांचे के साथ डिस्क एक दिशा या किसी अन्य में घूमती है, तो कैम क्रमशः भाग को जकड़ते या छोड़ते हुए केंद्र से दूर जाते हैं या दूर जाते हैं।
यह सुनिश्चित करना आवश्यक है कि भाग चक के जबड़े में मजबूती से टिका हो। अगर कारतूस है अच्छी हालत, फिर एक छोटे हैंडल (चित्र। 116) के साथ एक कुंजी का उपयोग करके भाग की एक मजबूत क्लैंपिंग सुनिश्चित की जाती है। क्लैंपिंग के अन्य तरीके, जैसे कि एक कुंजी के साथ क्लैंपिंग और हैंडल के ऊपर जाने वाला एक लंबा पाइप, किसी भी स्थिति में अनुमति नहीं दी जानी चाहिए।
चक जबड़े. कैम कठोर और कच्चे उपयोग किए जाते हैं। कठोर कैम आमतौर पर उनके कम पहनने के कारण उपयोग किए जाते हैं। लेकिन जब इस तरह के कैम के साथ साफ-सुथरी मशीनी सतहों के साथ भागों को क्लैंप किया जाता है, तो कैम से डेंट के रूप में निशान भागों पर बने रहते हैं। इससे बचने के लिए कच्चे (गैर-कठोर) जबड़ों का इस्तेमाल करने की भी सलाह दी जाती है।
कच्चे कैम इस मायने में भी सुविधाजनक हैं कि वे समय-समय पर एक कटर से ऊब सकते हैं और कारतूस की धड़कन को खत्म कर सकते हैं, जो अनिवार्य रूप से इसके लंबे संचालन के दौरान दिखाई देता है।
रियर सेंटर सपोर्ट वाले चक में पुर्जे लगाना और दबाना. इस पद्धति का उपयोग लंबे और अपेक्षाकृत पतले भागों (चित्र। 116) को संसाधित करते समय किया जाता है, जो केवल चक में तय होने के लिए पर्याप्त नहीं हैं, क्योंकि कटर से बल और उभरे हुए हिस्से का वजन भाग को मोड़ सकता है और इसे फाड़ सकता है चक के।
कोलेट चक. छोटे व्यास के छोटे भागों को बाहरी मशीनी सतह पर जल्दी से जकड़ने के लिए, उनका उपयोग किया जाता है कोलेट चक. ऐसा कारतूस अंजीर में दिखाया गया है। 117. हेडस्टॉक स्पिंडल के टेपर्ड बोर में टेपर्ड शैंक 1 कार्ट्रिज लगाया जाता है। एक शंकु के साथ एक विभाजित स्प्रिंग स्लीव 2, जिसे कोलेट कहा जाता है, कारतूस के अवकाश में स्थापित किया गया है। वर्कपीस कोलेट के छेद 4 में डाला जाता है। फिर वे एक रिंच के साथ चक बॉडी पर अखरोट 3 को पेंच करते हैं। अखरोट को पेंच करते समय, स्प्रिंग कोलेट संपीड़ित होता है और भाग को सुरक्षित करता है।
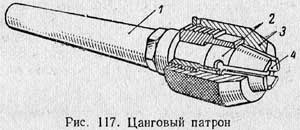
वायवीय चक. अंजीर पर। 118 एक वायवीय चक का आरेख दिखाता है जो भागों का तेज़ और विश्वसनीय बन्धन प्रदान करता है।
स्पिंडल के बायें सिरे पर एक एयर सिलेंडर लगा होता है, जिसके अंदर एक पिस्टन होता है। ट्यूबों के माध्यम से संपीड़ित हवा केंद्रीय चैनल 1 और 2 में प्रवेश करती है, जहां से इसे सिलेंडर के दाएं या बाएं गुहा में निर्देशित किया जाता है। यदि हवा चैनल 1 के माध्यम से सिलेंडर की बाईं गुहा में प्रवेश करती है, तो पिस्टन चैनल 2 के माध्यम से सिलेंडर की दाहिनी गुहा से हवा को विस्थापित करता है और इसके विपरीत। पिस्टन रॉड 4 और स्लाइडर 5 से जुड़ी रॉड 3 से जुड़ा है, जो क्रैंक लीवर की लंबी भुजाओं 6 पर कार्य करता है, जिनमें से छोटी भुजाएं 7 कार्ट्रिज के क्लैंपिंग जबड़े 8 को घुमाती हैं।
कैम की स्ट्रोक लंबाई 3-5 मिमी है। हवा का दबाव आमतौर पर सुबह 4-5 बजे होता है। वायवीय सिलेंडर को सक्रिय करने के लिए, गियरबॉक्स आवास पर एक वितरण वाल्व 9 स्थापित किया गया है, जिसे हैंडल 10 द्वारा घुमाया जाता है।
6. जबड़े की चक में अंदर और बाहर पेंच करना
चक को स्पिंडल पर पेंच करने से पहले, स्पिंडल के अंत में धागों को सावधानी से पोंछ लें और चक बोर में एक कपड़े से पोंछ लें और फिर उन्हें तेल से चिकनाई दें। एक हल्का कारतूस दोनों हाथों से सीधे धुरी के अंत तक लाया जाता है और खराब होने पर खराब हो जाता है (चित्र 119)। बोर्ड पर एक भारी कारतूस लगाने की सिफारिश की जाती है (चित्र 120), इसके छेद को धुरी के अंत तक लाते हुए, कारतूस को विफलता के लिए पेंच करें, जैसा कि पहले मामले में, हाथ से। चक पर पेंच लगाते समय, सुनिश्चित करें कि चक और धुरी की कुल्हाड़ियाँ बिल्कुल समान हैं।
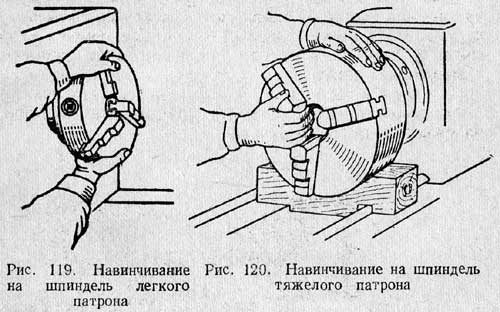
उच्च गति काटने के लिए मशीनों में कारतूस के स्व-अनस्क्रूइंग के मामलों को रोकने के लिए, विभिन्न उपकरणों का उपयोग करके स्पिंडल पर कारतूस के अतिरिक्त बन्धन का उपयोग किया जाता है।
(एक अतिरिक्त अखरोट को पेंच करना, आकार के पटाखे के साथ कारतूस को सुरक्षित करना, आदि)।
कारतूस का पेंच निम्नानुसार किया जाता है। कार्ट्रिज में एक चाबी डालें और दोनों हाथों से अपनी ओर एक झटका लगाएं (चित्र 121)।
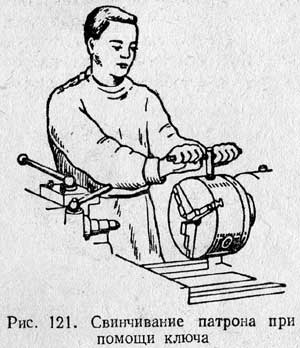
चक या जबड़े पर तेज प्रहार से जुड़े मेकअप के अन्य तरीके अस्वीकार्य हैं: चक क्षतिग्रस्त है, इसके शरीर में कैम ढीले हैं।
एक सहायक कार्यकर्ता की मदद से एक भारी कारतूस को पेंच करना और पेंच करना सबसे अच्छा है।
7. चिकनी बेलनाकार सतहों को मोड़ने की तकनीक
बेलनाकार सतहों का मोड़ आमतौर पर दो चरणों में किया जाता है: पहले, भत्ता का एक बड़ा हिस्सा (3-5 मिमी प्रति व्यास) मोटा हो जाता है, और फिर शेष भाग (1-2 मिमी प्रति व्यास)।
भाग के दिए गए व्यास को प्राप्त करने के लिए, कटर को कट की आवश्यक गहराई पर सेट करना आवश्यक है। कटर को कट की गहराई तक सेट करने के लिए, आप परीक्षण चिप्स विधि का उपयोग कर सकते हैं या अनुप्रस्थ फ़ीड डायल का उपयोग कर सकते हैं।
टेस्ट चिप्स विधि का उपयोग करके कटर को कट की गहराई (प्रति आकार) पर सेट करने के लिए, आपको यह करना होगा:
1. घूर्णी गति के विवरण की रिपोर्ट करें।
2. अनुदैर्ध्य फ़ीड हैंडव्हील और क्रॉस फीड स्क्रू हैंडल को मोड़कर, मैन्युअल रूप से कटर को भाग के दाहिने छोर पर लाएं ताकि इसका शीर्ष भाग की सतह को छू सके।
3. टचिंग मोमेंट सेट करने के बाद, कटर को मैन्युअल रूप से भाग के दाईं ओर ले जाएं और क्रॉस फीड स्क्रू हैंडल को घुमाकर कटर को वांछित कटिंग गहराई तक ले जाएं। उसके बाद, भाग को बदल दिया जाता है हस्त प्रविष्टि 3-5 मिमी की लंबाई पर, मशीन को रोकें और कैलीपर के साथ मुड़ी हुई सतह के व्यास को मापें (चित्र। 122)। यदि व्यास आवश्यकता से अधिक हो जाता है, तो कटर को दाईं ओर वापस ले लिया जाता है और थोड़ी अधिक गहराई पर सेट किया जाता है, करधनी को फिर से मशीनीकृत किया जाता है और माप फिर से लिया जाता है। वांछित आकार प्राप्त होने तक यह सब दोहराया जाता है। फिर यांत्रिक फ़ीड चालू करें और पूरी निर्दिष्ट लंबाई के साथ भाग को पीस लें। अंत में, मैकेनिकल फीड को बंद कर दें, कटर को वापस ले लें और मशीन को बंद कर दें।
फिनिशिंग उसी क्रम में की जाती है।
क्रॉस फीड स्क्रू डायल का उपयोग करना. कटर की स्थापना को कट की गहराई तक तेज करने के लिए, अधिकांश खराद में एक विशेष उपकरण होता है। यह क्रॉस फीड स्क्रू के हैंडल पर स्थित होता है और एक स्लीव या रिंग होता है, जिसकी परिधि पर डिवीजनों को चिह्नित किया जाता है (चित्र 123)। विभाजनों वाली इस आस्तीन को अंग कहा जाता है। डिवीजनों को निश्चित स्क्रू स्लीव पर जोखिम के अनुसार गिना जाता है (चित्र 123 में यह जोखिम लिम्बस के 30 वें स्ट्रोक के साथ मेल खाता है)।
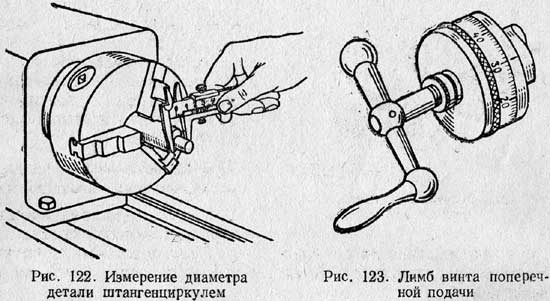
डायल पर डिवीजनों की संख्या और पेंच की पिच अलग-अलग हो सकती है, इसलिए, जब डायल को एक डिवीजन द्वारा घुमाया जाता है तो कटर के अनुप्रस्थ आंदोलन की मात्रा भी भिन्न होगी। मान लें कि डायल को 100 बराबर भागों में विभाजित किया गया है और क्रॉस फीड स्क्रू को 5 मिमी पिच में पिरोया गया है। स्क्रू हैंडल के एक पूर्ण मोड़ के साथ, यानी, अंग के 100 डिवीजन, कटर अनुप्रस्थ दिशा में 5 मिमी आगे बढ़ेगा। यदि आप हैंडल को एक भाग से घुमाते हैं, तो कटर की गति 5:100 = 0.05 मिमी होगी।
यह ध्यान में रखा जाना चाहिए कि जब कटर को अनुप्रस्थ दिशा में ले जाया जाता है, तो कटर पास होने के बाद भाग की त्रिज्या उतनी ही कम हो जाएगी, और भाग का व्यास दोगुना हो जाएगा। इस प्रकार, भाग के व्यास को कम करने के लिए, उदाहरण के लिए, 50.2 से 48.4 मिमी, यानी 50.2 - 48.4 = 1.8 मिमी, कटर को आधा, यानी 0.9 मिमी से आगे बढ़ाना आवश्यक है।
अनुप्रस्थ फ़ीड स्क्रू डायल की मदद से कटर को काटने की गहराई तक सेट करते समय, यह आवश्यक है, हालांकि, पेंच और अखरोट के बीच की खाई को ध्यान में रखना चाहिए, जो तथाकथित "मृत स्ट्रोक" बनाता है। यदि आप इस पर दृष्टि खो देते हैं, तो मशीनी भाग का व्यास निर्दिष्ट एक से भिन्न होगा।
इसलिए, डायल का उपयोग करके कटर को कट की गहराई तक सेट करते समय, यह देखना आवश्यक है अगला नियम. हमेशा स्क्रू हैंडल को धीरे-धीरे दाईं ओर घुमाते हुए डायल के साथ आवश्यक सेटिंग तक पहुंचें (चित्र 124, ए; आवश्यक सेटिंग डायल का 30 वां भाग है)।
यदि आप क्रॉस फीड स्क्रू के हैंडल को आवश्यक मान (चित्र 124, बी) से अधिक मात्रा में घुमाते हैं, तो त्रुटि को ठीक करने के लिए, किसी भी स्थिति में त्रुटि की मात्रा से हैंडल को वापस न खिलाएं, लेकिन आपको विपरीत दिशा में लगभग पूर्ण मोड़ बनाने की जरूरत है, और फिर लिंबस के साथ आवश्यक विभाजन के लिए हैंडल को फिर से दाईं ओर घुमाएं (चित्र 124, सी)। वे वही करते हैं जब कटर को वापस लेना आवश्यक होता है; हैंडल को बाईं ओर मोड़ते हुए, कटर को आवश्यकता से अधिक वापस ले लिया जाता है, और फिर, दाएं घुमाव द्वारा, इसे लिंबस के आवश्यक विभाजन में लाया जाता है।
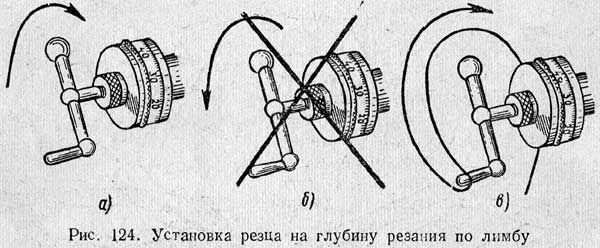
अंग के एक भाग के अनुरूप कटर की गति विभिन्न मशीनों पर भिन्न होती है। इसलिए, काम शुरू करते समय, इसके अनुरूप विस्थापन की मात्रा निर्धारित करना आवश्यक है यह मशीनअंग का एक विभाजन।
अंगों का उपयोग करके, हमारे हाई-स्पीड टर्नर बिना टेस्ट चिप्स के दिए गए आकार को प्राप्त करते हैं।
8. स्थिर भागों में प्रसंस्करण भागों
लंबे और पतले हिस्से, जिनकी लंबाई उनके व्यास से 10-12 गुना है, मोड़ के दौरान अपने स्वयं के वजन से और काटने वाले बल से झुकते हैं। नतीजतन, आइटम हो जाता है अनियमित आकार- बीच में यह मोटा हो जाता है, और सिरों पर - पतला। इसे एक विशेष सहायक उपकरण का उपयोग करके टाला जा सकता है जिसे कहा जाता है पागल मनुष्य. स्थिर आराम का उपयोग करते समय, उच्च परिशुद्धता वाले भागों को पीसना और चिप्स निकालना संभव है बड़ा खंडभाग झुकने के डर के बिना। लुनेट्स बी, गतिहीन और मोबाइल चलते हैं।
स्टैडि रेस्ट(अंजीर। 125) में एक कच्चा लोहा शरीर 1 होता है, जिसके साथ एक टिका हुआ कवर 6 एक टिका हुआ बोल्ट 7 के साथ बांधा जाता है, जो भाग की स्थापना की सुविधा प्रदान करता है। स्थिर आराम के शरीर को फ्रेम गाइड के आकार के अनुसार नीचे संसाधित किया जाता है, जिस पर इसे बार 9 और बोल्ट 8 के माध्यम से तय किया जाता है। दो कैम 4 शरीर के छिद्रों में किसकी मदद से चलते हैं बोल्ट 3 को समायोजित करना, और एक कैम 5 छत पर चलता है। स्क्रू 2 का उपयोग कैम को आवश्यक स्थिति में ठीक करने के लिए किया जाता है ऐसा उपकरण आपको स्थिर आराम में विभिन्न व्यास के शाफ्ट स्थापित करने की अनुमति देता है।
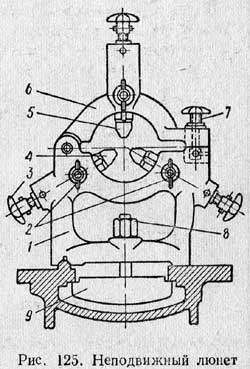
फिक्स्ड रेस्ट में एक अनटर्न्ड वर्कपीस को स्थापित करने से पहले, कैम के लिए इसके बीच में एक खांचे को मशीन करना आवश्यक है, जिसकी चौड़ाई कैम की चौड़ाई से थोड़ी अधिक हो (चित्र। 126)। यदि वर्कपीस की लंबाई बड़ी और छोटा व्यास है, तो इसका विक्षेपण अपरिहार्य है। इससे बचने के लिए, वर्कपीस के अंत के करीब एक अतिरिक्त नाली को मशीनीकृत किया जाता है और इसमें एक स्थिर आराम स्थापित करने के बाद, मुख्य नाली को बीच में मशीनीकृत किया जाता है।
स्थिर स्थिर आरामों का उपयोग सिरों को काटने और सिरों को ट्रिम करने के लिए भी किया जाता है लंबे हिस्से. अंजीर पर। 127 अंत को काटते समय एक निश्चित आराम का उपयोग दिखाता है: भाग एक छोर पर तीन-जबड़े चक में तय किया गया है, और दूसरा बाकी में स्थापित है।
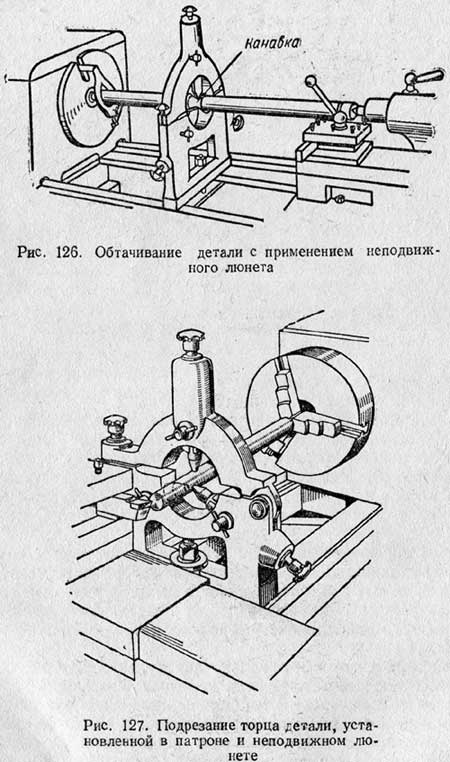
उसी तरह, आप एक लंबे हिस्से के अंत से एक सटीक छेद को मशीन कर सकते हैं, उदाहरण के लिए, एक खराद तकला में एक पतला छेद बोर कर सकते हैं या इसकी पूरी लंबाई के साथ इस तरह के हिस्से को ड्रिल कर सकते हैं।
चल स्थिर आराम(चित्र 128) का उपयोग लंबे भागों को बारीक मोड़ने के लिए किया जाता है। कैलीपर कैरिज पर कैलीपर को फिक्स किया जाता है ताकि वह कटर का अनुसरण करते हुए वर्कपीस के साथ-साथ चलता रहे। इस प्रकार, यह बल के आवेदन के बिंदु पर सीधे भाग का समर्थन करता है और भाग को विक्षेपित होने से रोकता है।
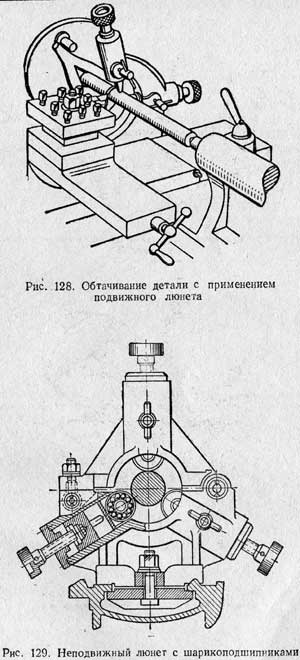
स्थिर विश्राम में केवल दो कैमरे हैं। उन्हें उसी तरह बढ़ाया और तय किया जाता है जैसे कि एक निश्चित लूनेट के कैम।
जबड़े के तेजी से पहनने के कारण पारंपरिक जबड़े के साथ स्थिर आराम उच्च गति मशीनिंग के लिए उपयुक्त नहीं हैं। ऐसे में करें अप्लाई रोलर या बॉल बेयरिंग के साथ स्थिर टिकी हुई है(अंजीर। 129) पारंपरिक कैम के बजाय, जो रोलर्स के संचालन की सुविधा देता है और वर्कपीस के हीटिंग को कम करता है।
9. बेलनाकार सतहों को किनारों से मोड़ने की तकनीक
व्यक्तिगत चरणों के सभी भागों के लिए समान लंबाई के साथ चरणबद्ध भागों (स्टेप्ड रोलर्स) के एक बैच पर प्रसंस्करण करते समय, नवोन्मेषक एक अनुदैर्ध्य स्टॉप का उपयोग करते हैं जो मापने के लिए समय को कम करने के लिए कटर और एक अनुदैर्ध्य फ़ीड अंग की गति को सीमित करता है। लंबाई।
अनुदैर्ध्य स्टॉप का उपयोग करना. अंजीर पर। 130 अनुदैर्ध्य विराम को दर्शाता है। जैसा कि अंजीर में दिखाया गया है, इसे फ्रंट बेड रेल पर बोल्ट किया गया है। 131; स्टॉप को ठीक करने का स्थान चालू किए जाने वाले भाग की लंबाई पर निर्भर करता है।
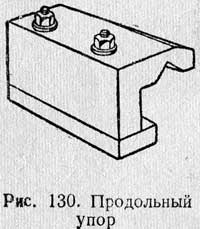
यदि मशीन पर एक अनुदैर्ध्य रोक है, तो प्रारंभिक अंकन के बिना किनारों के साथ बेलनाकार सतहों को संसाधित करना संभव है, उदाहरण के लिए, चरणबद्ध रोलर्स को एक सेटिंग में बिना स्टॉप के बहुत तेजी से चालू किया जाता है। यह रोलर स्टेप की लंबाई के अनुरूप स्टॉप और सपोर्ट के बीच एक लंबाई सीमक (मापने वाली टाइल) बिछाकर हासिल किया जाता है।
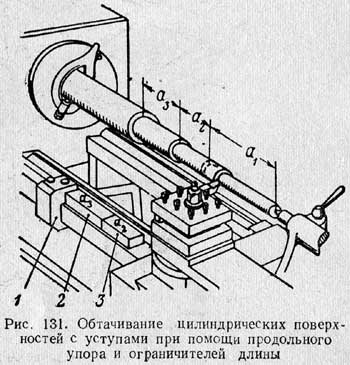
स्टॉप 1 के साथ स्टेप्ड रोलर को मोड़ने और टाइल्स 2 और 3 को मापने का एक उदाहरण चित्र 131 में दिखाया गया है। टर्निंग स्टेप ए 1 तब तक किया जाता है जब तक कैलीपर मापने वाली टाइल के खिलाफ आराम नहीं करता है। इस टाइल को हटाकर, आप रोलर के अगले चरण को 2 की लंबाई के साथ पीस सकते हैं जब तक कि कैलीपर टाइल 2 के खिलाफ आराम न करे। अंत में, हटा दें टाइल 2, चरण 3 पीसें। जैसे ही कैलीपर स्टॉप पर पहुंचता है, यांत्रिक फ़ीड को बंद करना आवश्यक है। मापने वाली टाइल 2 की लंबाई कगार a 3 की लंबाई के बराबर है, और टाइल 3 की लंबाई कगार a 2 की लंबाई के बराबर है।
हार्ड स्टॉप का उपयोग केवल मशीनों पर किया जा सकता है स्वचालित शटडाउनअधिभार फ़ीड (उदाहरण के लिए, 1A62 और अन्य नए मशीन टूल सिस्टम)। यदि मशीन में ऐसा कोई उपकरण नहीं है, तो स्टॉप के साथ मुड़ना तभी संभव है जब यांत्रिक फ़ीड को पहले से बंद कर दिया जाए और कैलीपर को मैन्युअल रूप से स्टॉप पर लाया जाए, अन्यथा मशीन टूट जाएगी।
अनुदैर्ध्य फ़ीड डायल का उपयोग करना अनुदैर्ध्य फ़ीड डायल का उपयोग करना. वर्कपीस की लंबाई को मापने में लगने वाले समय को कम करने के लिए, आधुनिक खराद किससे सुसज्जित हैं? अनुदैर्ध्य फ़ीड डायल. यह अंग बड़े व्यास (चित्र 132) की घूर्णन डिस्क का प्रतिनिधित्व करता है, जो एप्रन की सामने की दीवार पर और अनुदैर्ध्य फ़ीड हैंडव्हील के पीछे स्थित होता है। डिस्क की परिधि पर समान विभाजन लागू होते हैं। जब हैंडव्हील घूमता है, तो अनुदैर्ध्य फीड व्हील से गियरिंग से जुड़ा अंग भी घूमता है। इस प्रकार, एक कटर के साथ कैलीपर का एक निश्चित अनुदैर्ध्य आंदोलन अंग के रोटेशन से मेल खाता है निश्चित संख्यानिश्चित जोखिमों के सापेक्ष विभाजन।
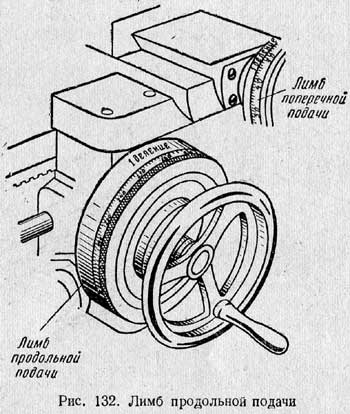
चरणबद्ध भागों को संसाधित करते समय, अनुदैर्ध्य फ़ीड डायल का उपयोग बहुत तर्कसंगत है। इस मामले में, टर्नर, बैच से पहले भाग को संसाधित करने से पहले, कैलीपर का उपयोग करके कटर के साथ चरणों की लंबाई को पहले से चिह्नित करता है, और फिर उन्हें पीसना शुरू कर देता है। पहले चरण को मोड़ने के बाद, वह अनुदैर्ध्य अंग को निश्चित जोखिम के सापेक्ष शून्य स्थिति में सेट करता है। अगले चरणों की ओर मुड़ते हुए, वह उसी जोखिम के संबंध में अंग के संबंधित संकेतों को याद करता है (या लिखता है)। बाद के हिस्सों को मोड़ते समय, टर्नर पहले भाग को मोड़ते समय सेट किए गए संकेतों का उपयोग करता है।
क्रॉस स्टॉप का उपयोग करना. चरणबद्ध भागों की मशीनिंग करते समय व्यास को मापने में लगने वाले समय को कम करने के लिए, कई खरादों पर क्रॉस स्टॉप का उपयोग करना संभव है।
इनमें से एक स्टॉप अंजीर में दिखाया गया है। 133. जोर में दो भाग होते हैं। निश्चित भाग 1 को गाड़ी पर स्थापित किया गया है और बोल्ट 2 के साथ तय किया गया है; जोर पिन 6 तय हो गया है। चल स्टॉप 3 कैलीपर के निचले हिस्से पर बोल्ट 4 के साथ स्थापित और तय किया गया है। स्क्रू 5 को भाग के आवश्यक आकार के लिए बिल्कुल सेट किया गया है। पेंच 5 का अंत, पिन 6 के खिलाफ आराम करते हुए, भाग के आवश्यक आकार को पूर्व निर्धारित करता है। पिन 6 और स्क्रू 5 के बीच मापक टाइलें रखकर, विभिन्न व्यास के चरणों के साथ एक भाग को पीसना संभव है।
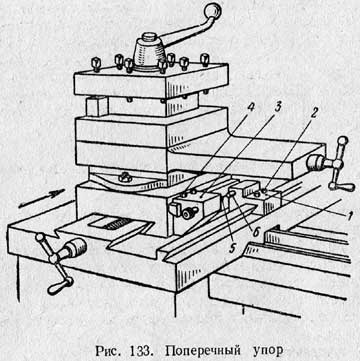
10. मोड़ के लिए काटने की स्थिति
गहराई काटने का विकल्प. मोड़ के दौरान कट की गहराई को मशीनिंग भत्ता और मशीनिंग के प्रकार के आधार पर चुना जाता है - रफिंग या फिनिशिंग (पृष्ठ 101-102 देखें)।
फ़ीड दर चयन. प्रसंस्करण के प्रकार के आधार पर फ़ीड को भी चुना जाता है। आम तौर पर, फ़ीड 0.3 से 1.5 मिमी / रेव से मोटे मोड़ के लिए लिया जाता है, और सेमी-फिनिशिंग और सामान्य कटर के साथ काम करते समय 0.1 से 0.3 मिमी / रेव के लिए और वी द्वारा कटर डिजाइन के साथ काम करते समय 1.5-3 मिमी / रेव के लिए लिया जाता है। कोलेसोव।
काटने की गति का विकल्प. काटने की गति आमतौर पर उपकरण जीवन, संसाधित की जा रही सामग्री की गुणवत्ता, कटर की सामग्री, कट की गहराई, फ़ीड, शीतलन के प्रकार आदि के आधार पर विशेष रूप से डिज़ाइन की गई तालिकाओं के अनुसार चुनी जाती है। (देखें, के लिए उदाहरण, तालिका 6, पृष्ठ 106)।
11. बेलनाकार सतहों को मोड़ते समय विवाह और इसे रोकने के उपाय
बेलनाकार सतहों को मोड़ते समय, निम्न प्रकार के विवाह संभव हैं:
1) भाग की सतह का हिस्सा अनुपचारित रहा;
2) मुड़ी हुई सतह के आयाम गलत हैं;
3) मुड़ी हुई सतह शंक्वाकार निकली;
4) मुड़ी हुई सतह अंडाकार निकली;
5) मशीनी सतह की सफाई ड्राइंग में दिए गए निर्देशों के अनुरूप नहीं है;
6) पीछे के केंद्र का दहन;
7) दोनों तरफ के केंद्रों में रोलर के प्रसंस्करण के दौरान सतहों का गैर-संयोग।
1. पहले प्रकार का विवाह वर्कपीस के अपर्याप्त आयामों (अपर्याप्त मशीनिंग भत्ता), वर्कपीस के खराब स्ट्रेटनिंग (वक्रता), भाग की अनुचित स्थापना और गलत संरेखण, केंद्र छिद्रों के गलत स्थान और विस्थापन के कारण प्राप्त होता है। पिछला केंद्र।
2. टेस्ट चिप्स को हटाते समय कट की गहराई में कटर की गलत सेटिंग या भाग की गलत माप के कारण मुड़ी हुई सतह के गलत आयाम संभव हैं। यह संभव है और प्रदर्शन किए गए कार्य पर टर्नर का ध्यान बढ़ाकर इस प्रकार के विवाह के कारणों को समाप्त करना चाहिए।
3. मुड़ी हुई सतह का टेपर आमतौर पर सामने के सापेक्ष पीछे के केंद्र के विस्थापन के परिणामस्वरूप प्राप्त होता है। इस प्रकार के विवाह के कारण को समाप्त करने के लिए, रियर सेंटर को सही ढंग से स्थापित करना आवश्यक है। रियर सेंटर मिसलिग्न्मेंट का एक सामान्य कारण गंदगी या छोटे चिप्स हैं जो क्विल के पतला बोर में जा रहे हैं। चोंच के बीच और शंक्वाकार छिद्र की सफाई करके भी विवाह के इस कारण को समाप्त किया जा सकता है। यदि सफाई के बाद भी, आगे और पीछे के केंद्रों के सिरे मेल नहीं खाते हैं, तो टेलस्टॉक के शरीर को उसी के अनुसार उसकी प्लेट पर ले जाना आवश्यक है।
4. मुड़े हुए हिस्से की अंडाकारता तब प्राप्त होती है जब स्पिंडल इसके बेयरिंग के असमान पहनने या इसकी गर्दन के असमान पहनने के कारण धड़कता है।
5. मोड़ के दौरान अपर्याप्त सतह खत्म होने के कई कारण हो सकते हैं: कटर की बड़ी फीड, अनियमित कोणों वाले कटर का उपयोग, कटर का खराब शार्पनिंग, कटर टिप की वक्रता की छोटी त्रिज्या, भाग की उच्च चिपचिपाहट सामग्री, एक बड़े ओवरहैंग के कारण कटर का घबराना, उपकरण धारक में कटर का अपर्याप्त रूप से मजबूत लगाव, कैलीपर के अलग-अलग हिस्सों के बीच अंतराल में वृद्धि, इसके ढीले बन्धन के कारण भाग का कांपना या बीयरिंग के पहनने के कारण और धुरी गर्दन।
विवाह के उपरोक्त सभी कारणों को समय पर समाप्त किया जा सकता है।
6. टेलस्टॉक के कठोर केंद्र का जलना निम्नलिखित कारणों से हो सकता है: केंद्र के बीच का हिस्सा बहुत कसकर तय किया गया है; केंद्र छेद का खराब स्नेहन; वर्कपीस का गलत केंद्रीकरण; उच्च काटने की गति।
7. केंद्रों में दोनों तरफ मुड़ने पर प्रसंस्करण सतहों का बेमेल मुख्य रूप से सामने के केंद्र की धड़कन या वर्कपीस में केंद्र छेद के विकास के परिणामस्वरूप प्राप्त होता है। विवाह को रोकने के लिए, परिष्करण के दौरान वर्कपीस के केंद्र छिद्रों की स्थिति की जांच करना आवश्यक है, और यह भी सुनिश्चित करना है कि हेडस्टॉक के केंद्र का कोई अपवाह न हो।
12. बेलनाकार सतहों को मोड़ते समय सुरक्षा सावधानियां
खराद पर प्रसंस्करण के सभी मामलों में, भाग और कटर के मजबूत बन्धन पर ध्यान देना आवश्यक है।
केंद्रों में संसाधित वर्कपीस के बन्धन की विश्वसनीयता काफी हद तक केंद्रों की स्थिति पर निर्भर करती है। पहना केंद्रों के साथ काम करना असंभव है, क्योंकि काटने वाले बल की कार्रवाई के तहत भाग को केंद्रों से फाड़ा जा सकता है, तरफ उड़ सकता है और टर्नर को घायल कर सकता है।
केंद्रों और चकों में भागों को संसाधित करते समय, क्लैंप के उभरे हुए हिस्से और चक के कैम अक्सर कार्यकर्ता के कपड़ों पर कब्जा कर लेते हैं। चलते-फिरते किसी हिस्से को नापते और मशीन की सफाई करते समय यही हिस्से हाथों को नुकसान पहुंचा सकते हैं। दुर्घटनाओं को रोकने के लिए, क्लैम्प पर सुरक्षात्मक ढाल की व्यवस्था की जानी चाहिए या सुरक्षा क्लैंप का उपयोग किया जाना चाहिए, और कैम चक्स को संरक्षित किया जाना चाहिए। सुरक्षा कॉलर का सही प्रकार अंजीर में दिखाया गया है। 134. रिम 3 न केवल बोल्ट 2 के सिर को कवर करता है, बल्कि ड्राइविंग चक के पिन 1 को भी कवर करता है।

टर्नर के हाथों और कपड़ों को आधुनिक खराद पर चक या फेसप्लेट के उभरे हुए हिस्सों से बचाने के लिए, एक विशेष बाड़ का उपयोग किया जाता है (चित्र 135)। डिवाइस का केसिंग 1 मुख्य रूप से हेडस्टॉक की बॉडी पर लगे पिन 2 से जुड़ा होता है।
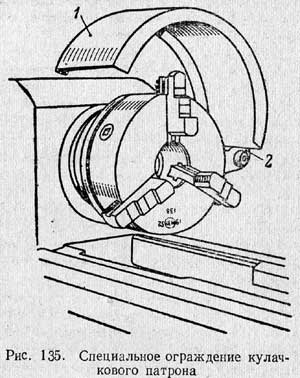
केंद्रों में भागों को स्थापित करते समय, आपको केंद्र के छिद्रों की शुद्धता पर ध्यान देने की आवश्यकता होती है। यदि उनकी गहराई अपर्याप्त है, तो रोटेशन के दौरान भाग केंद्रों को तोड़ सकता है, जो बहुत खतरनाक है। उसी तरह, चक में भाग को ठीक करने के बाद, आपको यह जांचना होगा कि कुंजी हटा दी गई है या नहीं। यदि चाभी चक में रहती है, तो जब स्पिंडल घूमता है, तो वह बिस्तर से टकराएगा और किनारे की ओर उड़ जाएगा। ऐसे में मशीन का खराब होना और कर्मचारी को चोट लगना दोनों ही संभव है।
दुर्घटनाओं का कारण अक्सर चिप्स होते हैं, विशेष रूप से ड्रेन चिप्स, जो, जब उच्च गतिकाटने से एक सतत टेप निकलता है। किसी भी स्थिति में ऐसे चिप्स को हाथ से हटाया या काटा नहीं जाना चाहिए, वे गंभीर कटौती और जलन पैदा कर सकते हैं। जब भी संभव हो चिप ब्रेकर का प्रयोग करना चाहिए। में अखिरी सहाराजब चिप ब्रेकिंग हासिल नहीं की जाती है, तो इसे एक विशेष हुक के साथ हटा दिया जाना चाहिए।
शॉर्ट बाउंसिंग चिप्स देने वाली सामग्री को संसाधित करते समय, काले चश्मे का उपयोग करना या सुरक्षा ग्लास या सेल्युलाइड (चित्र। 136) से बने सुरक्षा कवच का उपयोग करना आवश्यक है, जो एक हिंग वाले रैक पर गाड़ी से जुड़ा होता है। भंगुर धातुओं (कच्चा लोहा, कठोर कांस्य) के प्रसंस्करण से उत्पन्न छोटे चिप्स को हाथों से नहीं, बल्कि ब्रश से साफ करना आवश्यक है।
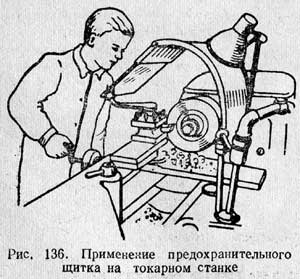
उपकरण धारक के फिक्सिंग बोल्ट के सिर से रिंच फटने के परिणामस्वरूप कटर को स्थापित और ठीक करते समय हाथों में चोट लग सकती है। चाबी को तोड़ना तब होता है जब चाबी के जबड़े और बोल्ट के सिर खराब हो जाते हैं। अक्सर, हालांकि, एक ब्रेकडाउन इस तथ्य से भी होता है कि टर्नर एक कुंजी का उपयोग करता है जिसका आकार बोल्ट के आकार से मेल नहीं खाता है।
केंद्र की ऊंचाई के साथ कटर को किसी भी प्रकार के अस्तर की मदद से स्थापित करना जो इसके लिए अनुकूलित नहीं हैं (धातु स्क्रैप, हैकसॉ के टुकड़े, आदि) इसके संचालन के दौरान कटर की एक स्थिर स्थिति प्रदान नहीं करते हैं। चिप्स के दबाव में, ऐसे अस्तर विस्थापित हो जाते हैं, और कटर की स्थापना गलत हो जाती है। साथ ही कटर का बन्धन भी कमजोर हो जाता है। नतीजतन, पैड और कटर उपकरण धारक से बाहर कूद सकते हैं और टर्नर को घायल कर सकते हैं। इसके अलावा, कटर की स्थापना के दौरान और मशीन पर काम करते समय, धातु के अस्तर के तेज किनारों पर हाथों में चोट लग सकती है। इसलिए, यह अनुशंसा की जाती है कि प्रत्येक टर्नर में अच्छी तरह से तैयार सहायक विमानों और किनारों के साथ विभिन्न मोटाई के अस्तर का एक सेट हो।
परीक्षण प्रश्न 1. कटर होल्डर में कटर कैसे लगाएं?
2. केंद्र रेखा के सापेक्ष कटर की नोक की स्थिति की जांच कैसे करें?
3. बेलनाकार सतहों को मोड़ते समय भागों को कैसे स्थापित और स्थिर किया जाता है?
4. आगे और पीछे के केंद्रों की कामकाजी परिस्थितियों में क्या अंतर है?
5. घूर्णन केंद्र की व्यवस्था कैसे की जाती है और इसका उपयोग किन मामलों में किया जाता है?
6. नुकीला मोर्चा केंद्र क्या है और इसके क्या फायदे हैं?
7. बेलनाकार सतह को मोड़ने के लिए केंद्रों की सही स्थापना की जांच कैसे करें?
8. आत्म-केंद्रित चक कैसे काम करता है? इसके विवरण, इसे स्थापित करने और काम के लिए तैयार करने के नियमों को नाम दें।
9. चार-जबड़े चक में स्थापित करते समय किसी भाग को कैसे संरेखित करें?
10. क्रॉस फीड स्क्रू डायल का उद्देश्य क्या है?
11. अनुदैर्ध्य फ़ीड डायल किसके लिए प्रयोग किया जाता है? इसकी व्यवस्था कैसे की जाती है?
12. स्थिर विराम किसके लिए होते हैं और उनका उपयोग किन मामलों में किया जाता है?
13. स्थिर विश्राम की व्यवस्था कैसे की जाती है?
14. चल स्थिर विश्राम की व्यवस्था कैसे की जाती है?
15. स्थिर विश्राम में स्थापना के लिए शाफ्ट ब्लैंक कैसे तैयार किया जाता है?
16. एक अनुदैर्ध्य स्टॉप के उपयोग का एक उदाहरण दें; क्रॉस स्टॉप।
17. बेलनाकार सतहों को मोड़ने पर किस प्रकार के विवाह संभव हैं? विवाह के कारणों को कैसे दूर करें?
18. बेलनाकार सतहों को मोड़ने के लिए बुनियादी सुरक्षा नियमों की सूची बनाएं।
खराद पर किन भागों को मशीनीकृत और मशीनीकृत किया जा सकता है
हम छोटे और टुकड़े के आदेश के साथ काम करते हैं। हम सशर्त श्रृंखला में कुछ चीजें करते हैं, जैसे शॉक एब्जॉर्बर में इंसर्ट, व्हील एक्सल के लिए एडेप्टर विभिन्न मानक. ऑफ सीजन (नवंबर-फरवरी) में आप बड़ा खेल खेल सकते हैं।
तुलनात्मक रूप से कहें तो हम घूर्णन के किसी भी भाग को बेलनाकार आकार का बना सकते हैं। सबसे अधिक मांग पहियों के लिए विभिन्न प्रकार के एडेप्टर और एक्सल थे। या तो मूल स्पेयर पार्ट बिक्री पर नहीं है, या प्रतीक्षा करने में लंबा समय लगता है, या यह प्रकृति में मौजूद नहीं है। उदाहरण के लिए, कुछ 20 मिमी माविक फ्रंट व्हील में 15 मिमी, 10 मिमी और नियमित 5 मिमी त्वरित रिलीज के लिए एडाप्टर नहीं है। और क्रॉसमैक्स के पिछले पहियों के लिए, लंबे समय तक बिक्री के लिए कोई धुरी नहीं है।
बड़ी संख्या में शॉक एब्जॉर्बर को बैशिंग में इंसर्ट की आवश्यकता होती है। इन्सर्ट को कैप्रोलॉन, पॉलीएसेटल या ड्यूरालुमिन से मशीनीकृत किया जा सकता है। सदमे अवशोषक के शाश्वत रूप से विकृत और चंचल कुल्हाड़ियों को टाइटेनियम मिश्र धातु VT16 से बदला जा सकता है।
कम बार नहीं, बीयरिंगों के बीच झाड़ियों में विकृत स्पेसर आते हैं। निर्माता ने पैसे की बचत की और बहुत नरम मिश्र धातु की आपूर्ति की।
कभी-कभी आपको मास्टर सिलेंडर और ब्रेक कैलिपर के लिए पिस्टन को तेज करना पड़ता है।
अक्सर मौजूदा हिस्से को वांछित आयामों में ठीक करने की आवश्यकता होती है।
हम मोटरसाइकिल और साइकिल के लिए रिप्लेसमेंट स्टीयरिंग पाइप को तेज करते हैं। हम साइकिल के लिए स्टीयरिंग ट्यूब एक्सटेंशन भी बनाते हैं।
कभी-कभी RC मॉडेलर विशेष रूप से मजबूत टाइटेनियम एक्सल और किसी प्रकार के जेट के लिए गनस्मिथ के लिए आते हैं।
मोड़ने के लिए किस सामग्री का उपयोग किया जाता है
मेरे घर में एल्यूमीनियम मिश्र धातु है डी16टी, बी95, 7075 . मूल रूप से, D16t के काम में - यह काफी टिकाऊ है। उन हिस्सों पर जो बहुत अधिक तनाव में हैं, आप मिश्र धातु B95 या 7075 लगा सकते हैं (यह वही है भौतिक गुण) हम एएमजी श्रृंखला मिश्र धातुओं का उपयोग नहीं करते हैं - वे बल्कि कमजोर हैं।
टाइटेनियम मिश्र धातु बीटी6, बीटी16. साइकिल और मोटरसाइकिल के प्रयोजनों के लिए ताकत के मामले में ये दो मिश्र धातु सबसे अधिक मांग में हैं।
कैप्रोलोनऔर पॉलीएसेटल. यह अच्छाई घर्षण इकाइयों में सम्मिलित करने के लिए जाती है। फुल सस्पेंशन असेंबलियों की गणना करते समय अधिकांश फ्रेम बिल्डर्स भी कैप्रोलोन पर स्विच कर रहे हैं।
फ्लोरोप्लास्ट. हम इसका उपयोग मिश्रित भागों के निर्माण में करते हैं।
पोलीयूरीथेन. कभी-कभी आपको कुछ अजीब कफ या आस्तीन बनाने की आवश्यकता होती है।
पीतल के पुर्जे किसी तरह उपयोग नहीं किए जाते हैं, इसलिए पीतल और कांस्य स्टॉक में नहीं हैं - अपना खुद का लाओ।
यदि आप चाहें, तो मैं केवल सामग्री का एक टुकड़ा बेच सकता हूं - हो सकता है कि आप स्वयं एक फ़ाइल लहराना चाहें? =)
हम काम को चालू करने के आदेश कैसे स्वीकार करते हैं
आदेश किसी भी रूप में स्वीकार किया जाता है। यह एक नमूना हो सकता है जिसकी आप प्रतिलिपि बनाना चाहते हैं। चित्रकारी। योजना। रेखाचित्र। फोटो। उंगली की व्याख्या। लेकिन पिछले दो मामलों में, हम एक साथ आयामों के साथ एक स्केच बनाएंगे।
आप समकक्ष पर एक विवरण बना सकते हैं। और हमारे पास रिवर्स इंजीनियरिंग के लिए एक राक्षसी मार्कअप नहीं है।
मुझे इस बात का काफी अच्छा अंदाजा है कि भागों के विभिन्न इंटरफेस कैसे बनाए जाने चाहिए, इसलिए ज्यादातर मामलों में "उंगलियों पर" स्पष्टीकरण के साथ भी कोई समस्या नहीं है। लेकिन कभी-कभी उनके आकार को सटीक रूप से निर्धारित करने के लिए जीवित संभोग भागों की आवश्यकता होती है।
विनिर्माण सटीकता और भाग आयाम
समझदार पैसे के लिए एक टुकड़ा उत्पाद पर मौलिक रूप से प्राप्त करने योग्य सटीकता बाहरी व्यास के लिए 0.01 मिमी है। लेकिन इसकी आवश्यकता शायद ही किसी को होती है, आमतौर पर 0.05 मिमी की सटीकता पर्याप्त होती है (यह वास्तव में, एक प्रेस फिट है)। आंतरिक व्यास- 0.02 मिमी से अधिक नहीं।
खुरदरापन वर्गों को मापने के लिए कुछ भी नहीं है, इसलिए मैं यहां कुछ भी सार्थक नहीं कह सकता। मैं पॉलिशिंग के नमूने दिखा सकता हूं। 14वीं कक्षा के लिए आदर्श दर्पण बनाना कभी भी कोई कार्य नहीं था, और हम बीयरिंग (शंकु) की रोलिंग सतहों को कम से कम 10वीं कक्षा तक पीसते हैं।
तैयारी की अधिकतम लंबाई - 350 मिमी। अधिकतम वर्कपीस व्यास 62 मिमी है।
उत्पादन समय और कीमतें
0.05 मिमी से कम की सटीकता के साथ छोटी चीजें और सरल विवरण या तो तुरंत या उसी दिन किए जाते हैं। अधिक सटीक और जटिल विवरण - अगले दिन या हर दूसरे दिन।
संदर्भ के लिए, कोसने में एक कैप्रोलॉन शॉक एब्जॉर्बर डालना 150 रूबल है। एक 15 मिमी एक्सल से एक नियमित सनकी के लिए एडाप्टर - 500r। किनारों पर असर वाली सीटों और थ्रेड्स के साथ फ्रंट हब के लिए एक्सिस - 2000r (बहुत सटीक कचरा)। कॉल करना आसान है, मोटे तौर पर कार्य की व्याख्या करें, फिर यह स्पष्ट हो जाएगा कि इसकी लागत कितनी है।
शेष प्रश्न फोन द्वारा पूछे जा सकते हैं या व्यक्तिगत रूप से ओगोरोड्नी तक ड्राइव कर सकते हैं।
कार्य उदाहरण
निलंबन कांटे (केप्रोलोन) में तेल सील और परागकोशों को दबाने के लिए उपकरणों का एक सेट:
एंटी-जंग उपचार (D16t) के साथ 15 मिमी एक्सल से सनकी तक एडाप्टर:
बदली PTFE डालने के साथ 7075 मिश्र धातु झाड़ी (प्रक्रिया):
संरचनात्मक प्रसंस्करण के साथ एक निलंबन कांटा कारतूस का उत्पादन:
बुश टेपर पीस:
20 वें अक्ष से एक मानक सनकी के लिए एक एडेप्टर बनाना:
Marzocchi कांटा कारतूस में कस्टम कफ बनाना:
Marzocchi कांटा में कारतूस के कुछ हिस्सों का निर्माण:
शॉक एब्जॉर्बर झाड़ियों में ड्यूरालुमिन इंसर्ट का उत्पादन:
बेलनाकार भागों को मोड़ना
एक खराद पर, उत्पादों को मशीनीकृत किया जाता है, जिसके समोच्च में कई वॉल्यूमेट्रिक शामिल हो सकते हैं ज्यामितीय आकार, जिन्हें कहा जाता है क्रांति के शरीर . ये आंकड़े हैं गेंद, शंकु, सिलेंडर और टोरस(अंजीर देखें। बाईं ओर)।
मशीन पर पुर्जों को मोड़ना विशेष के साथ किया जाता है कृन्तक - छेनी मोड़ना
. पारंपरिक बढ़ईगीरी छेनी के विपरीत, उनके पास लंबे हैंडल होते हैं जो आपको उपकरण को सुरक्षित रूप से पकड़ने और इसे नियंत्रित करने में आसान बनाते हैं।
प्रसंस्करण की गुणवत्ता प्रतिष्ठित है प्रारूपऔर परिष्करणमोड़, उपकरण की पसंद इस पर निर्भर करती है।
के लिये प्रारूप प्रसंस्करण लागू अर्धवृत्ताकार छेनी(अंजीर देखें। लेकिन), के लिये परिष्करण मोड़, ट्रिमिंग समाप्त होता है और भागों को काटना - तिरछी छेनी(अंजीर देखें। 6 ).
पर रफ टर्निंगरिक्त स्थान (अंजीर देखें। लेकिन) एक अर्धवृत्ताकार छेनी को हैंडपीस के साथ ले जाया जाता है। पहले पास के दौरान, चिप्स 1 ... 2 मिमी मोटी छेनी ब्लेड के बीच से हटा दी जाती है (चित्र देखें। 6 , बाएं)। ब्लेड के किनारे के हिस्सों द्वारा आगे की ओर मोड़ किया जाता है जब कटर बाईं और दाईं ओर चलता है (चित्र देखें। 6 , दायी ओर)। छेनी ब्लेड के विभिन्न वर्गों के साथ काम करने के परिणामस्वरूप, भाग की सतह कम लहराती है। 2 ... 3 मिनट के काम के बाद, वे वर्कपीस को ठीक करने की विश्वसनीयता की जांच करते हैं - वे इसे टेलस्टॉक के केंद्र से दबाते हैं। परिष्करण के लिए, 3 ... 4 मिमी (व्यास में) का भत्ता छोड़ा जाना चाहिए।
पर ठीक मोड़(अंजीर देखें।) एक तिरछी छेनी को नीचे की ओर अधिक कोण के साथ किनारे पर रखा गया है। ब्लेड के मध्य और निचले हिस्सों से छीलन काट दी जाती है।
मोड़ते समय टर्निंग छेनी दो हाथों से पकड़ी जाती है: एक हैंडल के लिए, दूसरा रॉड के लिए। रॉड के लिए छेनी को ऊपर या नीचे चारों ओर लपेटा जाता है। किसी न किसी मोड़ के लिए, सबसे विश्वसनीय के रूप में पहली विधि का अधिक बार उपयोग किया जाता है। छेनी पर दबाव एक समान और चिकना होना चाहिए।
उत्पादों के आंतरिक अवकाश को चालू करने के लिए संरक्षकया फेसप्लेट(विभिन्न कंटेनर, ताबूत, नमक शेकर, आदि) - पहले एक ड्रिल के साथ वर्कपीस के केंद्र में एक छेद ड्रिल करें। फिर, अर्धवृत्ताकार सिरे वाली छेनी के साथ, अतिरिक्त लकड़ी का चयन किया जाता है। अंत में, दीवारों को संरेखित करने के लिए, घुमावदार सिरे वाली छेनी का उपयोग करें (बाईं ओर की आकृति देखें)।
उत्पादों को मोड़ने के लिए फेसप्लेटसबसे पहले एक वर्ग के रूप में एक रिक्त स्थान बनाएं। इस वर्कपीस पर विकर्ण खींचे जाते हैं और एक सर्कल को इच्छित उत्पाद के व्यास से थोड़ा बड़ा खींचा जाता है। एक आरा के साथ, एक ऑक्टाहेड्रोन प्राप्त करने के लिए अतिरिक्त कोनों को काट दिया जाता है, जिसे शिकंजा के साथ फेसप्लेट पर खराब कर दिया जाता है। फेसप्लेट को स्पिंडल पर घाव किया जाता है और यह देखने के लिए जाँच की जाती है कि वर्कपीस हैंडपीस से चिपकता है या नहीं। उसके बाद, मशीन को चालू किया जाता है और ऑक्टाहेड्रोन को वांछित व्यास में बदल दिया जाता है। फिर हैंडपीस को वर्कपीस के प्लेन के समानांतर स्थापित किया जाता है और इसके अंदरूनी हिस्से को मशीनी किया जाता है। हैंडपीस को हिलाना, पीसना बाहरउत्पाद।
उत्पाद के व्यास की जाँच की जाती है कैलिपर
या कैलिपर
. वर्कपीस की लंबाई के साथ कई जगहों पर मापन किया जाना चाहिए। स्ट्रेटनेस को रूलर या लाइट में स्क्वायर से चेक किया जा सकता है।
मोड़ने के तुरंत बाद, भाग की सतह को से जुड़े सैंडपेपर से साफ किया जाता है लड़की का ब्लॉक(अंजीर देखें।) लकड़ी की बनावट को उज्ज्वल करने के लिए, उत्पाद की सतह को सख्त लकड़ी की पट्टी से पॉलिश किया जा सकता है। यह ऑपरेशन भाग को घुमाने के साथ-साथ पीसते समय भी किया जाता है।
भाग के सिरों को काटते समय, तिरछी छेनी को नीचे एक तीव्र कोण के साथ किनारे पर रखा जाता है और एक उथला कट बनाया जाता है (बाईं ओर की आकृति देखें)।
फिर, दाएं या बाएं थोड़ा पीछे हटें (जिस पर निर्भर करता है कि अंत काटा जाता है), छेनी को झुकाएं और वर्कपीस के हिस्से को शंकु में काट लें (दाईं ओर की आकृति देखें)। यह ऑपरेशन कई बार दोहराया जाता है जब तक कि 8 ... 10 मिमी के व्यास वाली गर्दन न रह जाए। फिर भाग को मशीन से हटा दिया जाता है, इसके सिरों को हैकसॉ से काट दिया जाता है। सिरे साफ किए जाते हैं।
के निर्माण के लिए एक लंबी संख्यासमान भागखराद पर प्रयोग किया जाता है कंडक्टर(सीमाएं) छेनी या . के लिए कापियर मशीनें . कंडक्टरों को स्वयं बनाना आसान है और टर्निंग छेनी और हैंडपीस दोनों पर स्थापित करना आसान है (बाईं ओर की आकृति देखें)।
संख्याएँ इंगित करती हैं:
1. - जोर;
2. - अनुदैर्ध्य गति का सीमक;
3. - अनुप्रस्थ गति सीमक;
4. - छेनी मोड़ना।
निर्मित भागों पर वांछित आकृति प्राप्त करने के लिए, कभी-कभी विशिष्ट छेनी का उपयोग किया जाता है (दाईं ओर की आकृति देखें)।
वे कभी-कभी विशेष रूप से किसी विशेष उत्पाद या वांछित समोच्च के लिए बनाए जाते हैं।
नीचे एक उत्पाद और इसे बनाने के लिए उपयोग की जाने वाली छेनी का उदाहरण दिया गया है।
उदाहरण के लिए, लकड़ी की गेंद के निर्माण के लिए, छेनी का उपयोग किया जाता है, जो एक विशिष्ट व्यास के बने होते हैं (बाईं ओर की आकृति देखें)।
विशेष छेनी के बिना, एक ही गेंद को साधारण छेनी से बनाया जा सकता है, लेकिन सटीक निर्माण के लिए एक स्टैंसिल (टेम्पलेट) बनाना आवश्यक है जिसके साथ आप गोलाकार सतह की शुद्धता को माप सकते हैं।
स्टैंसिल बनाने और मोड़ने के चरणों को दाईं ओर की आकृति में दिखाया गया है।
मोड़ के लिए लकड़ी न केवल सलाखों या बोर्डों के टुकड़ों को काटकर तैयार की जाती है, बल्कि सूखे पेड़ की शाखाओं का भी उपयोग किया जाता है, साथ ही सलाखों या बोर्डों के गोंद के टुकड़े (अर्थात खंडों से) (नीचे चित्र देखें)। अक्सर ऐसे "ब्लॉक" को मोड़ने के लिए उत्पाद विभिन्न प्रजातियों की लकड़ी का उपयोग करते हैं।
इसके लिए धन्यवाद, ऐसे उत्पाद प्राप्त होते हैं जो रंग और बनावट में बहुत ही असामान्य होते हैं।
काम करते समय, इन नियमों का पालन करें:
कम सुरक्षात्मक स्क्रीन(चश्मा लगाओ)
निष्क्रिय में मशीन के संचालन की जाँच करें;
वर्कपीस को संसाधित करते समय, कटर को सुचारू रूप से लाएं;
सुनिश्चित करें कि वर्कपीस और हैंडपीस के बीच का अंतर 5 मिमी से अधिक नहीं है;
अक्षीय ड्रिलिंग करते समय, टेलस्टॉक को सावधानी से सुरक्षित करें;
भीतरी छेद को खोदते समय, कटर को क्षैतिज तल में सुरक्षित रूप से पकड़ें;
पूरी तरह से बंद वर्कपीस के साथ प्रसंस्करण के आयाम और गुणवत्ता को नियंत्रित करें;
एक हिस्सा खत्म करते समय सैंडपेपरइसे एक विशेष धारक पर ठीक करें।
सभी खराबी की सूचना तुरंत शिक्षक को दें, मशीन बंद करने के बाद!
काम पूरा होने पर:
मशीन से तैयार भाग निकालें;
विशेष रूप से निर्दिष्ट स्थानों में उपकरण और जुड़नार रखना;
कार्यस्थल को साफ करें;
काम पूरा होने पर परिचारक को रिपोर्ट करें।
ऑपरेशन के दौरान, मशीन पर देखने की स्क्रीन को नीचे किया जाना चाहिए।
यदि मशीन में ऐसी स्क्रीन नहीं है, तो सुरक्षात्मक चश्मे में काम करना आवश्यक है।
काटने का उपकरणस्पिंडल के पूर्ण गति प्राप्त करने के बाद ही वर्कपीस में लाएं।
जब मशीन चालू होती है, तो वर्कपीस को ठीक करने और उसके आयामों को मापने, मशीन के घटकों को स्थानांतरित करने के लिए मना किया जाता है।
मशीन को बंद करने के बाद, अपने हाथों से वर्कपीस, चक या फेसप्लेट को ब्रेक न करें।
एक चालू मशीन को लावारिस न छोड़ें।
काम के अंत में, उपकरण को निर्दिष्ट स्थानों पर रखें, चिप्स को ब्रश से साफ़ करें।
यह निषिद्ध है:
शिक्षक की अनुमति के बिना मशीन चालू करें;
बेल्ट ड्राइव गार्ड की अनुपस्थिति में काम करें;
एक अप्रस्तुत वर्कपीस का उपयोग करें;
चिप्स, दरारें, गीला या सड़ा हुआ वर्कपीस का उपयोग करें;
खराद के कुछ हिस्सों पर झुकें;
मशीन पर उपकरण और अन्य सामान रखो;
वर्कपीस को हाथ से रोकें;
मशीन को बंद किए बिना उससे दूर हट जाएं।