काटने के तरीके। रफ टर्निंग के दौरान फ़ीड बिना किसी अतिरिक्त कटिंग एज के कार्बाइड कटर बन गए। तेल और गैस का बड़ा विश्वकोश
टर्निंग को मैकेनिकल फीड के साथ किया जा सकता है, क्योंकि मशीनी शंकु का जेनरेटर कटर के अनुदैर्ध्य फ़ीड की दिशा के समानांतर है।
प्रतिलिपि तकनीकी चक्र का उपयोग चरणबद्ध, शंक्वाकार और घुमावदार सतहों के प्रसंस्करण के लिए किया जाता है जिसके लिए कटर के अनुदैर्ध्य फ़ीड की आवश्यकता होती है। सतह के उपचार के अंत में, कटर को भाग से हटा दिया जाता है, और कैलीपर अपनी मूल स्थिति में वापस आ जाता है।
धागा काटने वाली मशीन का सामान्य सूचकांक। |
अनुदैर्ध्य समर्थन 7, बिस्तर के गाइड पर घुड़सवार, उनके साथ चलता है और कटर की अनुदैर्ध्य फ़ीड प्रदान करता है। क्रॉस कैरिज कटर को क्रॉस फीड प्रदान करता है। ऊपरी रोटरी समर्थन को किसी भी कोण पर वर्कपीस के रोटेशन की धुरी पर सेट किया जा सकता है, जो कि वर्कपीस की शंक्वाकार सतहों को मशीनिंग करते समय आवश्यक है।
एक आकार के वर्कपीस को मोड़ने की योजना। |
15 - 20 मिमी तक टेलस्टॉक के शरीर के अनुप्रस्थ विस्थापन के बाद, मशीनी शंकु का जेनरेटर कटर के अनुदैर्ध्य फ़ीड की दिशा के समानांतर है, इसलिए यांत्रिक फ़ीड के साथ मोड़ किया जा सकता है .
खाना पकाने की योजना। |
टेलस्टॉक के शरीर के मान एच (15 - 20 मिमी तक) के अनुप्रस्थ विस्थापन के बाद, मशीनी शंकु का जेनरेटर कटर के अनुदैर्ध्य फ़ीड की दिशा के समानांतर है, इसलिए यांत्रिक के साथ मोड़ किया जा सकता है चारा।
खराद पर थ्रेडिंग के लिए, यह आवश्यक है कि स्पिंडल के रोटेशन की गति को कैलीपर की गति से सख्ती से जोड़ा जाए, क्योंकि स्पिंडल की एक क्रांति में कटर की अनुदैर्ध्य फ़ीड बिल्कुल धागे की पिच से मेल खाना चाहिए। काटा जा रहा है।
कट धातु की परत की मोटाई अनियमितताओं के परिमाण को बहुत प्रभावित करती है। कट परत की मोटाई कटर के अनुदैर्ध्य फ़ीड द्वारा निर्धारित की जाती है। यदि काटने की प्रक्रिया के दौरान कोई लोचदार-प्लास्टिक विकृति नहीं थी, तो अनियमितताओं की ऊंचाई की गणना आसानी से की जा सकती है ज्यामितीय आकारकटर के शीर्ष।
काम शुरू होने के 1 मिनट के बाद, कटर के अनुदैर्ध्य फ़ीड को बंद कर दें, कटर को वर्कपीस से दूर ले जाएं और टूल होल्डर को 90 या 180 तक जल्दी से घुमाएं जब तक कि कटर की नोक संकेतक टिप को न छू ले।
एक फ्रेम में हीरे के लिए, अनुदैर्ध्य फ़ीड पेंसिल की तुलना में कम और कटे हुए हीरे के लिए भी कम होनी चाहिए। उदाहरण के लिए, जब डायमंड कटर के साथ मल्टी-थ्रेड थ्रेड-पीस व्हील ड्रेसिंग करते हैं, तो कटर की अनुदैर्ध्य फ़ीड 0 05 मीटर / मिनट से अधिक नहीं होनी चाहिए। ड्रेसिंग प्रक्रिया के अंत में, क्रॉस फीड के बिना एक या दो पास बनाने की सिफारिश की जाती है, जिससे अनुदैर्ध्य फ़ीड की मात्रा कम हो जाती है।
स्थिरता को एक स्थिर कोण के साथ शंक्वाकार छिद्रों को उबाऊ करने के लिए डिज़ाइन किया गया है। डिवाइस को मशीन फेसप्लेट के रेडियल सपोर्ट पर फिक्स किया गया है। स्क्रू 3 को घुमाकर कटर को लंबे समय तक फीड किया जाता है। पेंच के दूसरे छोर पर, एक तारक 1 स्थापित किया गया है, जो कैलीपर के प्रत्येक मोड़ पर सेट स्टॉप पर अपने दाँत के साथ कूदता है, स्वचालित अनुदैर्ध्य फ़ीड करता है।
इसके परिणामस्वरूप किसी विशेष भाग, वर्कपीस और लागू की मशीनी सतहों को काटकर और प्राप्त करके वर्कपीस को संसाधित करने के लिए काटने का उपकरणबनाना चाहिए कुछ आंदोलन. इन आंदोलनों को मुख्य (काटने की प्रक्रिया के कार्यान्वयन के लिए सेवारत) और सहायक (काटने की प्रक्रिया की तैयारी के लिए और ऑपरेशन को पूरा करने के लिए सेवारत) में विभाजित किया गया है। दो मुख्य आंदोलन हैं:
- काटने की गति (या मुख्य गति);
- फ़ीड आंदोलन।
एक खराद पर प्रसंस्करण करते समय, काटने की गति - घूर्णी - वर्कपीस द्वारा की जाती है, जिसे मशीन स्पिंडल में एक तरह से या किसी अन्य में बांधा जाता है, और फ़ीड आंदोलन - ट्रांसलेशनल - उपकरण में कठोरता से तय किया गया एक काटने का उपकरण (कटर) प्राप्त करता है। धारक। आंदोलन काटने की प्रक्रिया (चिप गठन) को सक्षम बनाता है, फ़ीड की गति इस प्रक्रिया (प्रसंस्करण) को वर्कपीस की पूरी लंबाई (चित्र। भाग 16) के साथ करना संभव बनाती है।
कटौती की गहराई (टी)- एक पास में कट परत का मान, मशीनी सतह के लंबवत दिशा में मापा जाता है। कट की गहराई हमेशा फ़ीड दिशा के लंबवत होती है (अंजीर भी देखें। 11-14)। बाहरी अनुदैर्ध्य मोड़ (छवि 16) के साथ, यह वर्कपीस के व्यास और एक पास के बाद प्राप्त मशीनी सतह के व्यास के बीच का आधा अंतर है:
काटने की गतिυ - बिंदु आंदोलन की मात्रा अग्रणीकटिंग मूवमेंट के कार्यान्वयन के दौरान प्रति यूनिट समय सतह के सापेक्ष *।
मोड़ते समय, जब वर्कपीस n आरपीएम की आवृत्ति पर घूमता है, तो कटिंग एज के एमके बिंदुओं पर काटने की गति एक चर मान होगी। अधिकतम चाल:
जहां डी मिमी में सबसे बड़ा सतह व्यास है।
* काटने की गति वर्कपीस घूर्णी गति और उपकरण यात्रा (फ़ीड) गति का एक कार्य है।
यदि गति ज्ञात है, तो घूर्णन की आवृत्ति निर्धारित करना आसान है:
अनुदैर्ध्य मोड़ के साथ, काटने की गति का पूरे काटने के समय में एक स्थिर मूल्य होता है (यदि इसकी पूरी लंबाई के साथ वर्कपीस का व्यास समान है, और घूर्णी गति अपरिवर्तित है)। अंत को ट्रिम करते समय, जब कटर वर्कपीस की परिधि से केंद्र की ओर बढ़ता है, तो स्थिर गति से काटने की गति परिवर्तनशील होती है।उसके पास उच्चतम मूल्यपरिधि पर और केंद्र में शून्य के बराबर है (चित्र 17)। बिदाई के दौरान मशीनी सतह के साथ काटने की गति भी परिवर्तनशील होगी (चित्र 14 देखें)। हालाँकि, इन मामलों में, विचार करें उच्चतम गतिकाट रहा है।
सबमिशन(अधिक सटीक, फ़ीड दर) - फ़ीड आंदोलन की दिशा में प्रति यूनिट समय में मशीनी सतह के सापेक्ष अत्याधुनिक गति की मात्रा। मुड़ते समय, यह हो सकता है अनुदैर्ध्य फ़ीडजब कटर वर्कपीस की धुरी के समानांतर दिशा में चलता है (चित्र 16 देखें); क्रॉस फीडजब कटर वर्कपीस की धुरी के लंबवत दिशा में चलता है (चित्र 17 देखें), और परोक्ष फ़ीड- वर्कपीस की धुरी के कोण पर (उदाहरण के लिए, शंक्वाकार सतह को मोड़ते समय)।
पिच भेद एक बारी मेंवर्कपीस, यानी वर्कपीस की एक क्रांति के दौरान कटर के सापेक्ष आंदोलन की मात्रा (स्थिति I से कटर स्थिति II, चित्र 16 में स्थानांतरित हो गया), और मिनट फ़ीड, यानी 1 मिनट के लिए कटर के सापेक्ष आंदोलन का मूल्य। मिनट फ़ीड एस एम (मिमी / मिनट), और प्रति क्रांति फ़ीड - एस (मिमी / रेव) द्वारा इंगित किया जाता है। उनके बीच निम्नलिखित संबंध है।
मुख्य करने के लिए
खंड तीन
धातु काटने के सिद्धांत की मूल बातें।
डेटा काटने का विकल्प
अध्याय VI
धातु काटने के सिद्धांत की मूल बातें
धातुओं को काटने के सिद्धांत के संस्थापक उत्कृष्ट रूसी वैज्ञानिक आईए टाइम (1838-1920), केए ज़्वोरकिन (1861-1928), हां जी। उसाचेव (1873-1941) और अन्य थे। इन वैज्ञानिकों के कार्य, जिन्हें प्राप्त हुआ विश्व मान्यता ने अभी तक अपना मूल्य नहीं खोया है। हालाँकि, पिछड़े tsarist रूस की स्थितियों में, ये सभी कार्य नहीं पाए गए व्यावहारिक आवेदनक्योंकि उद्योग अविकसित था।
धातु काटने के विज्ञान ने महान अक्टूबर समाजवादी क्रांति के बाद ही व्यापक दायरा प्राप्त किया, विशेषकर सोवियत पंचवर्षीय योजनाओं के दौरान, जब विज्ञान को समाजवादी उद्योग की सेवा में रखा गया था।
सोवियत वैज्ञानिक वी.डी. कुज़नेत्सोव, वी.ए. क्रिवोखोव, आईएम धातु, विशेष फ़ीचरजो उत्पादन के साथ विज्ञान का, उत्पादन के नवप्रवर्तकों के साथ वैज्ञानिकों का घनिष्ठ सहयोग है।
धातु काटने के विज्ञान के विकास में एक महत्वपूर्ण भूमिका उत्पादन में नवप्रवर्तकों के आंदोलन द्वारा निभाई गई थी। श्रम उत्पादकता बढ़ाने के प्रयास में, उत्पादन के नेताओं ने काटने की स्थिति में सुधार के लिए नए तरीकों की तलाश शुरू की: उन्होंने एक नया काटने का उपकरण ज्यामिति बनाया, काटने की स्थिति बदल दी, नई महारत हासिल की काटने की सामग्री. प्रत्येक कार्यस्थलटर्नर-इनोवेटर कटिंग प्रक्रिया के अध्ययन के लिए एक छोटी प्रयोगशाला की तरह हो गया है।
अनुभव का व्यापक आदान-प्रदान, केवल समाजवादी अर्थव्यवस्था की स्थितियों के तहत संभव है, और उत्पादन और विज्ञान में अग्रणी श्रमिकों के बीच घनिष्ठ सहयोग ने धातुओं को काटने के विज्ञान के तेजी से विकास को सुनिश्चित किया।
1. कटर का कार्य
कील और उसका काम. किसी भी काटने के उपकरण का कार्य भाग है कील(चित्र। 44)। लागू बल की कार्रवाई के तहत, कील की नोक धातु में कट जाती है।
कील जितनी तेज होती है, यानी उसकी भुजाओं से बना कोण जितना छोटा होता है, उसे धातु में काटने के लिए उतना ही कम बल लगता है। पच्चर की भुजाओं से बनने वाले कोण को कहते हैं शंकु कोणऔर इसे ग्रीक अक्षर β से निरूपित किया जाता है ( बीटा) इसलिए, टेपर कोण β जितना छोटा होता है, उतना ही आसान कील धातु में प्रवेश करता है, और, इसके विपरीत, टेपर कोण β जितना बड़ा होता है, धातु को काटने के लिए उतना ही अधिक बल लगाया जाना चाहिए। शंकु कोण को निर्दिष्ट करते समय, संसाधित होने वाली धातु के यांत्रिक गुणों को ध्यान में रखना आवश्यक है। यदि आप एक छोटे से शार्पनिंग एंगल वाले कटर से कठोर धातु को काटते हैं, तो पतला ब्लेड टिकेगा नहीं और उखड़ जाएगा या टूट जाएगा। इसलिए, संसाधित की जा रही धातु की कठोरता के आधार पर, एक उपयुक्त वेज शार्पनिंग एंगल असाइन किया जाता है।
संसाधित की जा रही धातु की परत, सीधे कटर के सामने स्थित होती है, इसकी सामने की सतह से लगातार संकुचित होती है। जब कटर का बल धातु के कणों के आसंजन की ताकतों से अधिक हो जाता है, तो संपीड़ित तत्व को कतरनी और कील की सामने की सतह से ऊपर की ओर स्थानांतरित कर दिया जाता है। कटर, लागू बल की कार्रवाई के तहत आगे बढ़ते हुए, संपीड़ित, चिप और शिफ्ट करना जारी रखेगा व्यक्तिगत तत्वजिससे चिप्स बनते हैं।
मोड़ में बुनियादी आंदोलनों. जब खराद पर मशीनिंग होती है, तो वर्कपीस घूमता है, और कटर अनुदैर्ध्य या अनुप्रस्थ दिशा में गति प्राप्त करता है। वर्कपीस के रोटेशन को कहा जाता है मुख्य आंदोलन, और भाग के सापेक्ष कटर की गति - फ़ीड गति(चित्र। 45)।
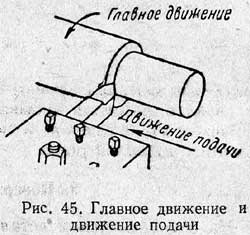
2. टर्निंग टूल के मुख्य भाग और तत्व
कटर में दो मुख्य भाग होते हैं: सिर और शरीर (छड़) (चित्र। 46)। सिरकटर का कामकाजी (काटने) हिस्सा है; तनउपकरण धारक में कटर को सुरक्षित करने का कार्य करता है।

सिर में निम्नलिखित तत्व होते हैं: सामने की सतह, जिसके साथ चिप्स निकलते हैं, और पीछे की सतहवर्कपीस का सामना करना पड़ रहा है। काटने की सतह का सामना करने वाली पिछली सतहों में से एक को कहा जाता है मुख्य; दूसरा, उपचारित सतह का सामना कर रहा है, - सहायक.
कटिंग किनारों को आगे और पीछे की सतहों के चौराहे से प्राप्त किया जाता है। अंतर करना घरऔर सहायक अत्याधुनिक. कटिंग का अधिकांश कार्य मुख्य कटिंग एज द्वारा किया जाता है।
मुख्य और द्वितीयक कटिंग किनारों के चौराहे को कहा जाता है कृन्तक टिप.
3. भूतल उपचार
वर्कपीस पर तीन प्रकार की सतह को प्रतिष्ठित किया जाता है (चित्र 47): मशीनीकृत, मशीनीकृत और काटने की सतह।

संसाधितसतह वर्कपीस की सतह है जिसमें से चिप्स निकाले जाते हैं।
सतह का इलाजचिप हटाने के बाद प्राप्त भाग की सतह कहा जाता है।
काटने की सतहकटर के मुख्य कटिंग एज द्वारा वर्कपीस पर बनी सतह को कहा जाता है।
कटिंग प्लेन और बेस प्लेन के बीच अंतर करना भी आवश्यक है।
काटने वाला विमानविमान को काटने की सतह पर स्पर्शरेखा कहा जाता है और कटर के काटने वाले किनारे से गुजरता है।
मुख्य विमानकटर के अनुदैर्ध्य और अनुप्रस्थ फ़ीड के समानांतर एक विमान कहा जाता है। खराद के लिए, यह उपकरण धारक की क्षैतिज समर्थन सतह के साथ मेल खाता है।
4. कटर कोण और उनका उद्देश्य
कटर के काम करने वाले हिस्से के कोण काटने की प्रक्रिया के प्रवाह को बहुत प्रभावित करते हैं।
कटर के समकोण का चयन करके, आप इसके निरंतर संचालन की अवधि को ब्लंटिंग (स्थायित्व) और प्रति यूनिट समय (प्रति मिनट या घंटे) तक बढ़ा सकते हैं। बड़ी मात्राविवरण।
कटर पर कार्य करने वाली काटने की शक्ति, आवश्यक शक्ति, मशीन की सतह की गुणवत्ता आदि भी कटर के कोणों की पसंद पर निर्भर करती है। यही कारण है कि प्रत्येक टर्नर को प्रत्येक तीक्ष्ण कोण के उद्देश्य का अच्छी तरह से अध्ययन करना चाहिए कटर और सही ढंग से उनके सबसे फायदेमंद मूल्य का चयन करने में सक्षम हो।
कटर के कोण (चित्र। 48) को मुख्य कोणों में विभाजित किया जा सकता है, योजना में कटर के कोण और मुख्य काटने वाले किनारे के झुकाव के कोण।
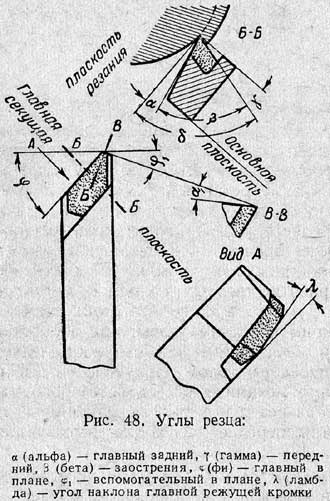
मुख्य कोणों में शामिल हैं: बैक एंगल, फ्रंट एंगल और टेंपर एंगल; योजना में कटर के कोणों में मुख्य और सहायक शामिल हैं।
कटर के मुख्य कोणों को मुख्य कटिंग प्लेन में मापा जाना चाहिए, जो कटिंग प्लेन और मुख्य प्लेन के लंबवत हो।
कटर का काम करने वाला हिस्सा एक पच्चर (चित्र 48 में छायांकित) है, जिसका आकार कटर के सामने और मुख्य पीछे की सतहों के बीच के कोण की विशेषता है। इस कोने को कहा जाता है शंकु कोणऔर ग्रीक अक्षर β (बीटा) द्वारा निरूपित किया जाता है।
पिछला कोण α ( अल्फा) मुख्य फ्लैंक और कटिंग प्लेन के बीच का कोण है।
क्लीयरेंस एंगल α कटर की पिछली सतह और वर्कपीस के बीच घर्षण को कम करने का कार्य करता है। घर्षण को कम करके, हम इस प्रकार कटर के ताप को कम करते हैं, जो इसके कारण कम घिसता है। हालांकि, अगर राहत कोण बहुत बढ़ जाता है, तो इंसुलेटर कमजोर हो जाता है और जल्दी से नष्ट हो जाता है।
सामने का कोण γ ( गामा) कटर की सामने की सतह और काटने वाले विमान के लंबवत विमान के बीच का कोण है, जो मुख्य काटने के किनारे के माध्यम से खींचा जाता है।
रेक कोण चिप बनाने की प्रक्रिया में एक महत्वपूर्ण भूमिका निभाता है। रेक कोण में वृद्धि के साथ, कटर को धातु में काटना आसान होता है, कट परत की विकृति कम हो जाती है, चिप प्रवाह में सुधार होता है, काटने की शक्ति और बिजली की खपत कम हो जाती है, और मशीन की सतह की गुणवत्ता कम हो जाती है। सुधार किया जाता है। दूसरी ओर, रेक एंगल में अत्यधिक वृद्धि से कटिंग एज कमजोर हो जाती है और इसकी ताकत में कमी आती है, कटिंग एज के छिलने के कारण कटर के पहनने में वृद्धि होती है, और गर्मी हटाने में गिरावट आती है। . इसलिए, कठोर और भंगुर धातुओं को संसाधित करते समय, उपकरण की ताकत बढ़ाने के साथ-साथ इसके स्थायित्व को बढ़ाने के लिए, छोटे रेक कोण वाले कटर का उपयोग किया जाना चाहिए; जब नरम और तन्य धातुओं की मशीनिंग की जाती है, तो चिप को हटाने की सुविधा के लिए बड़े रेक कोण वाले कटर का उपयोग किया जाना चाहिए। व्यवहार में, सामने के कोण का चुनाव निर्भर करता है, इसके अलावा यांत्रिक विशेषताएंसंसाधित की जा रही सामग्री, कटर की सामग्री और सामने की सतह के आकार से। कार्बाइड कटर के लिए अनुशंसित रेक कोण तालिका में दिए गए हैं। एक।
योजना कोण। अग्रणी कोण φ ( फाई) को मुख्य कटिंग एज और फीड दिशा के बीच का कोण कहा जाता है।
कोण को आमतौर पर प्रसंस्करण के प्रकार, कटर के प्रकार, वर्कपीस की कठोरता और कटर और उनके लगाव की विधि के आधार पर 30-90 ° की सीमा में चुना जाता है। अधिकांश धातुओं को पास-थ्रू छीलने वाले कटर के साथ संसाधित करते समय, कोण φ = 45 डिग्री लेना संभव है; पतली प्रसंस्करण करते समय लंबे हिस्सेकेंद्रों में 60, 75 या 90 ° के सीसे के कोण के साथ कटर का उपयोग करना आवश्यक है ताकि भागों झुकें या कांपें नहीं।
योजना में सहायक कोणφ 1 सेकेंडरी कटिंग एज और फीड दिशा के बीच का कोण है।

कोण ( लैम्ब्डा) मुख्य अत्याधुनिक का झुकाव(चित्र 49) मुख्य काटने के किनारे और मुख्य विमान के समानांतर कटर के शीर्ष के माध्यम से खींची गई रेखा के बीच का कोण है।
तालिका नंबर एक
कार्बाइड उपकरणों के लिए अनुशंसित रेक और निकासी कोण
ध्यान दें। धातुओं के यांत्रिक गुणों को विशेष मशीनों और उपकरणों पर निर्धारित किया जाता है, और प्रत्येक संपत्ति को अपना पदनाम दिया जाता है। इस और बाद की तालिकाओं में दिया गया पदनाम b धातु की तन्यता शक्ति को व्यक्त करता है; इस सीमा का मान किलो/मिमी 2 में मापा जाता है। एचबी अक्षर धातु की कठोरता को दर्शाता है, जो ब्रिनेल डिवाइस पर धातु की सतह में कठोर स्टील की गेंद को दबाकर निर्धारित किया जाता है। कठोरता का मान किलो / मिमी 2 में मापा जाता है।
कटर जिसका शीर्ष काटने के किनारे का सबसे निचला बिंदु है, यानी कोण λ सकारात्मक(अंजीर। 49, सी), अधिक टिकाऊ और प्रतिरोधी हैं; ऐसे कटरों के साथ कठोर धातुओं के साथ-साथ रुक-रुक कर होने वाली सतहों को संसाधित करना अच्छा होता है जो एक प्रभाव भार पैदा करते हैं। ऐसी सतहों को संसाधित करते समय कार्बाइड कटरमुख्य काटने के किनारे के झुकाव के कोण को 20-30 डिग्री तक समायोजित किया जाता है। कटर जिसका शीर्ष धार का उच्चतम बिंदु है, अर्थात कोण λ नकारात्मक(अंजीर। 49, ए), नरम धातुओं से बने भागों के प्रसंस्करण के लिए उपयोग करने की सिफारिश की जाती है।
5. कृन्तकों के निर्माण के लिए प्रयुक्त सामग्री
कटर के काटने वाले किनारों पर काम करते समय, उच्च दबाव होता है, साथ ही उच्च तापमान (600-800 ° और ऊपर)। काटने की सतह पर कटर की पिछली सतह और कटर की सामने की सतह पर चिप्स के घर्षण से इसकी कार्यशील सतहों का कमोबेश तेजी से क्षरण होता है। पहनने के कारण, काटने वाले भाग का आकार बदल जाता है और कटर कुछ समय बाद आगे के काम के लिए अनुपयोगी हो जाता है; इस तरह के कटर को मशीन से हटा दिया जाना चाहिए और फिर से चालू किया जाना चाहिए। बिना रिग्राइंडिंग के उपकरण के जीवन को बढ़ाने के लिए, यह आवश्यक है कि इसकी सामग्री उच्च तापमान पर अच्छी तरह से पहनने के लिए प्रतिरोधी हो। इसके अलावा, कटर की सामग्री को झेलने के लिए पर्याप्त मजबूत होना चाहिए उच्च दबावकाटने के दौरान उत्पन्न होना। इसलिए, कटर की सामग्री पर निम्नलिखित बुनियादी आवश्यकताएं लगाई जाती हैं - उच्च तापमान पर कठोरता, अच्छा पहनने का प्रतिरोध और ताकत।
वर्तमान में, कई उपकरण स्टील्स और मिश्र धातुएं हैं जो इन आवश्यकताओं को पूरा करती हैं। इनमें शामिल हैं: कार्बन टूल स्टील्स, हाई स्पीड स्टील्स, हार्ड मिश्र और चीनी मिट्टी सामग्री.
कार्बन उपकरण स्टील. काटने के उपकरण के निर्माण के लिए 0.9 से 1.4% कार्बन सामग्री वाले स्टील का उपयोग किया जाता है। शमन और तड़के के बाद, इस स्टील से बने काटने का उपकरण उच्च कठोरता प्राप्त करता है। हालांकि, अगर काटने की प्रक्रिया के दौरान काटने के किनारे का तापमान 200-250 डिग्री तक पहुंच जाता है, तो स्टील की कठोरता तेजी से गिरती है।
इस कारण से, कार्बन टूल स्टील वर्तमान में सीमित उपयोग का है: इसका उपयोग काटने के उपकरण बनाने के लिए किया जाता है जो अपेक्षाकृत कम काटने की गति पर काम करते हैं जब काटने वाले क्षेत्र में तापमान एक छोटे से मूल्य तक पहुंच जाता है। इस तरह के उपकरणों में शामिल हैं: डाई, रीमर, टैप, फाइल, स्क्रेपर्स, आदि। कटर वर्तमान में कार्बन टूल स्टील से निर्मित नहीं होते हैं।
हाई स्पीड स्टील्स. हाई स्पीड स्टील्स में शामिल हैं एक बड़ी संख्या कीविशेष, तथाकथित मिश्र धातु तत्व - टंगस्टन, क्रोमियम, वैनेडियम और कोबाल्ट, जो स्टील को उच्च काटने के गुण देते हैं - 600-700 ° तक काटने के दौरान कठोरता बनाए रखने और प्रतिरोध पहनने की क्षमता। एचएसएस कटर कार्बन कटर की तुलना में 2-3 गुना अधिक काटने की गति की अनुमति देते हैं।
वर्तमान में, यूएसएसआर में हाई-स्पीड स्टील (GOST 9373-60) के निम्न ग्रेड का उत्पादन किया जाता है: R18, R9, R9F5, R14F14, R18F2, R9K5, R9KYU, R10K5F5 और R18K5F2।
पूरी तरह से हाई-स्पीड स्टील से बने कटर महंगे होते हैं, इसलिए हाई-स्पीड स्टील को बचाने के लिए वेल्ड प्लेट वाले कटर का इस्तेमाल मुख्य रूप से किया जाता है।
कठोर मिश्र। कार्बाइड मिश्र धातुओं को बहुत अधिक कठोरता और अच्छे पहनने के प्रतिरोध की विशेषता है।
कार्बन के साथ संयुक्त टंगस्टन और टाइटेनियम पाउडर से प्लेटों के रूप में कठोर मिश्र धातुएं बनाई जाती हैं। कार्बन और टंगस्टन के संयोजन को कहते हैं टंगस्टन कार्बाइड, और टाइटेनियम, टाइटेनियम कार्बाइड के साथ। कोबाल्ट को बाइंडर के रूप में जोड़ा जाता है। इस चूर्ण मिश्रण को छोटी प्लेटों को प्राप्त करने के लिए उच्च दबाव में दबाया जाता है, जिन्हें बाद में लगभग 1500 डिग्री के तापमान पर पाप किया जाता है। तैयार प्लेटों को किसी की आवश्यकता नहीं है उष्मा उपचार. प्लेट को तांबे के साथ कटर धारक को मिलाया जाता है कार्बन स्टीलया समायोजन और शिकंजा (प्लेटों के यांत्रिक बन्धन) की मदद से इससे जुड़ा हुआ है।
कठोर मिश्र धातुओं का मुख्य लाभ यह है कि वे चिप्स और वर्कपीस को अच्छी तरह से गिरने से घर्षण का विरोध करते हैं और 900-1000 ° तक गर्म होने पर भी अपने काटने के गुणों को नहीं खोते हैं। इन गुणों के लिए धन्यवाद, कार्बाइड आवेषण से लैस कटर मशीनिंग के लिए सबसे उपयुक्त हैं ठोस धातु(कठोर स्टील सहित) और गैर-धातु सामग्री (कांच, चीनी मिट्टी के बरतन, प्लास्टिक) काटने की गति पर जो उच्च गति वाले कटर द्वारा अनुमत काटने की गति से 4-6 गुना या अधिक है।
कठोर मिश्र धातुओं का नुकसान भंगुरता में वृद्धि है।
वर्तमान में, यूएसएसआर में कठोर मिश्र धातुओं के दो समूह निर्मित होते हैं। मुख्य हैं - टंगस्टन(वीके2, वीकेजेड, वीके4, वीके6एम, वीके6, वीके8 और वीके8एम) और टाइटेनियम-टंगस्टन(T30K4, T15K6, T14K8, T5K10)। इनमें से प्रत्येक समूह का एक विशिष्ट दायरा होता है (तालिका 2)।
सभी टंगस्टन मिश्र धातु कच्चा लोहा, अलौह धातुओं और उनके मिश्र धातुओं, कठोर स्टील्स, स्टेनलेस स्टील्स और गैर-धातु सामग्री (इबोनाइट, चीनी मिट्टी के बरतन, कांच, आदि) के प्रसंस्करण के लिए अभिप्रेत हैं। स्टील्स के प्रसंस्करण के लिए, टाइटेनियम-टंगस्टन समूह के कठोर मिश्र धातुओं का उपयोग किया जाता है।
सिरेमिक सामग्री. हाल ही में, सोवियत धातुकर्मियों ने उच्च काटने वाले गुणों के साथ सस्ती सामग्री बनाई है, जो कई मामलों में कठोर मिश्र धातुओं की जगह लेती है। ये सिरेमिक सामग्री हैं थर्मोकोरंडम), प्लेटों के रूप में निर्मित सफेद रंग, संगमरमर की याद ताजा करती है, जो कठोर मिश्र धातुओं की तरह या तो कटर धारकों को मिलाप किया जाता है या यंत्रवत् रूप से उनसे जुड़ा होता है। इन प्लेटों में टंगस्टन, टाइटेनियम आदि जैसे महंगे और दुर्लभ तत्व नहीं होते हैं। साथ ही, सिरेमिक प्लेटों में कठोर मिश्र धातुओं की तुलना में अधिक कठोरता होती है और 1200 डिग्री तक गर्म होने पर उनकी कठोरता बरकरार रहती है, जिससे धातुओं को काटना संभव हो जाता है उनके साथ उच्च गतिकाट रहा है।
सिरेमिक प्लेटों का नुकसान उनकी अपर्याप्त चिपचिपाहट है। सिरेमिक आवेषण से लैस कटर का उपयोग कच्चा लोहा, कांस्य, एल्यूमीनियम मिश्र धातु और हल्के स्टील के परिष्करण या अर्ध-परिष्करण के लिए किया जा सकता है।
6. कटर को तेज करना और खत्म करना
कारखानों में, कटरों की शार्पनिंग आमतौर पर केंद्रीकृत तरीके से की जाती है पीसने की मशीनविशेष कार्यकर्ता। लेकिन टर्नर खुद कटर को तेज करने और खत्म करने में सक्षम होना चाहिए।
तालिका 2
हार्ड मिश्र धातु के कुछ ग्रेड के गुण और उद्देश्य

उच्च गति वाले कटरों को तेज और परिष्कृत करना निम्नलिखित नियमों के अनुपालन में किया जाता है:
1. पीसने वाला पहिया हिट नहीं होना चाहिए, इसकी सतह भी होनी चाहिए; यदि सर्कल की कामकाजी सतह विकसित हो गई है, तो इसे ठीक किया जाना चाहिए।
2. शार्पनिंग के दौरान, आपको एक हैंडपीस का उपयोग करने की आवश्यकता होती है, न कि कटर को वजन पर रखने की। हैंडपीस को ग्राइंडिंग व्हील के जितना संभव हो सके, आवश्यक कोण पर स्थापित किया जाना चाहिए और कटर को विश्वसनीय समर्थन देना चाहिए (चित्र 50, ए-डी)।
3. तेज करने वाले कटर को सर्कल की कामकाजी सतह के साथ ले जाना चाहिए, अन्यथा यह असमान रूप से खराब हो जाएगा।
4. कटर को ज़्यादा गरम न करने के लिए और इस तरह उसमें दरारें न दिखने के लिए, कटर को सर्कल में जोर से न दबाएं।
5. कटर को पानी से लगातार और प्रचुर मात्रा में ठंडा करके शार्पनिंग की जानी चाहिए। ड्रिप कूलिंग, साथ ही पानी में अत्यधिक गर्म कटर के आवधिक विसर्जन की अनुमति नहीं है। यदि निरंतर शीतलन संभव नहीं है, तो ड्राई शार्पनिंग पर स्विच करना बेहतर है।
6. उच्च गति वाले स्टील से बने कटरों की शार्पनिंग मध्यम कठोरता और 25-16 दाने के आकार के इलेक्ट्रोकोरंडम पहियों का उपयोग करके की जानी चाहिए।
कटर को तेज करने का क्रम निम्नानुसार निर्धारित किया गया है। सबसे पहले, मुख्य पीछे की सतह को तेज किया जाता है (चित्र 50, ए)। फिर सहायक पीछे की सतह (चित्र। 50, बी), फिर सामने की सतह (चित्र। 50, सी) और, अंत में, शीर्ष की त्रिज्या (चित्र। 50, डी)।
7. सुरक्षात्मक आवरण को हटाकर मशीनों पर कटर को तेज करना सख्त मना है।
8. तेज करते समय सुरक्षा चश्मे पहनना सुनिश्चित करें।
कटर को तेज करने के बाद इसके काटने वाले किनारों पर छोटे-छोटे निशान, गड़गड़ाहट और जोखिम बना रहता है। विशेष परिष्करण मशीनों पर परिष्करण करके उन्हें समाप्त कर दिया जाता है। खनिज तेल से सिक्त महीन दाने वाले मट्ठे का उपयोग करके फिनिशिंग भी मैन्युअल रूप से की जाती है। सबसे पहले, टचस्टोन के हल्के आंदोलनों के साथ, पीछे की सतहों को समायोजित किया जाता है, और फिर सामने और शीर्ष की त्रिज्या।
कार्बाइड इंसर्ट से लैस कटरों की शार्पनिंग और फिनिशिंग. हरी सिलिकॉन कार्बाइड के हलकों के साथ पीसने वाली मशीनों पर कठोर मिश्र धातुओं की प्लेटों के साथ कटर को तेज किया जाता है। शार्पनिंग दोनों को मैन्युअल रूप से किया जाता है (चित्र 50, a-d), और उपकरण धारकों में incenders को ठीक करने के साथ। इन कटरों को तेज करने का क्रम हाई-स्पीड स्टील से बने कटर के समान है, अर्थात, पहले कटर को मुख्य बैक (चित्र 50, ए) के साथ तेज किया जाता है, फिर सहायक बैक सतहों के साथ (चित्र 50, बी) ), फिर सामने की सतह के साथ (चित्र। 50, सी) और, अंत में, चीरा लगाने वाले के ऊपर से गोल (चित्र। 50, डी)।
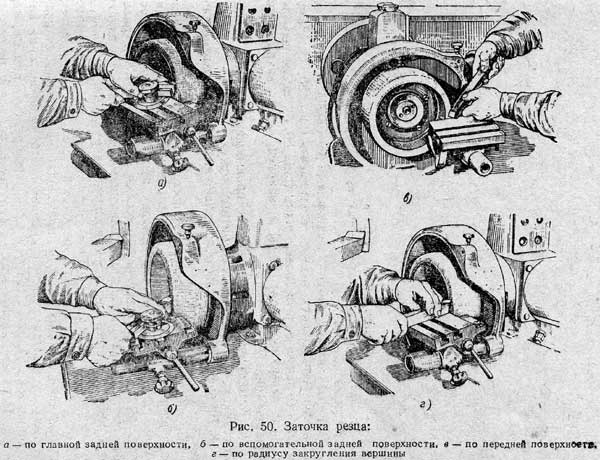
प्रारंभिक शार्पनिंग हरे सिलिकॉन कार्बाइड पहियों के साथ 50-40 की ग्रिट के साथ की जाती है, और अंतिम शार्पनिंग 25-16 की ग्रिट के साथ की जाती है।
कठोर मिश्र धातु प्लेट के अधिक गरम होने और टूटने से बचने के लिए कटर को सर्कल की कामकाजी सतह के खिलाफ जोर से नहीं दबाया जाना चाहिए। इसके अलावा, इसे सर्कल के सापेक्ष लगातार स्थानांतरित किया जाना चाहिए; सर्कल के एक समान पहनने के लिए यह आवश्यक है।
पानी के साथ कटर के सूखे और प्रचुर मात्रा में ठंडा होने पर तेज किया जा सकता है।
कार्बाइड कटर को तेज करने के बाद, इसकी सतह को खत्म करना अनिवार्य है। फिनिशिंग मैन्युअल रूप से या फिनिशिंग मशीन पर की जाती है। मैनुअल फिनिशिंग एक कच्चा लोहा या तांबे की गोद का उपयोग करके किया जाता है, जिसकी कामकाजी सतह को एक विशेष पेस्ट से रगड़ा जाता है या मशीन के तेल या मिट्टी के तेल के साथ मिश्रित बोरान कार्बाइड पाउडर को एक समान परत में सतह पर लगाया जाता है। कटिंग एज से 2-4 मिमी की चौड़ाई तक फिनिशिंग की जाती है।
250-300 मिमी के व्यास के साथ कच्चा लोहा डिस्क का उपयोग करके एक विशेष परिष्करण मशीन पर अधिक उत्पादक परिष्करण, 1.5-2 मीटर / सेकंड की गति से घूमता है; मशीन के तेल या मिट्टी के तेल के साथ मिश्रित बोरान कार्बाइड का पेस्ट या पाउडर इस डिस्क की सतह पर लगाया जाता है।
7. चिप गठन
छीलन के प्रकार। कटर के दबाव की कार्रवाई के तहत अलग की गई चिप अपने आकार को बहुत बदल देती है या, जैसा कि वे कहते हैं, विकृत हो जाती है: यह लंबाई में छोटा हो जाता है और मोटाई में बढ़ जाता है। इस घटना की खोज सबसे पहले प्रो. I. A. समय और नाम चिप संकोचन.
चिप की उपस्थिति धातु के यांत्रिक गुणों और उन परिस्थितियों पर निर्भर करती है जिनके तहत कटाई होती है। यदि चिपचिपी धातुओं को संसाधित किया जाता है (सीसा, टिन, तांबा, हल्के स्टील, एल्यूमीनियम, आदि), तो चिप्स के अलग-अलग तत्व, एक-दूसरे का कसकर पालन करते हुए, एक निरंतर चिप बनाते हैं जो एक टेप में कर्ल करती है (चित्र 51, ए) ) ऐसे स्ट्रैंड को कहा जाता है नाली. कम चिपचिपी धातुओं को संसाधित करते समय, जैसे कि कठोर स्टील, चिप्स अलग-अलग तत्वों (चित्र। 51, बी) से बनते हैं, जो एक दूसरे से कमजोर रूप से जुड़े होते हैं। ऐसे स्ट्रैंड को कहा जाता है चिपिंग चिप्स.
यदि मशीनीकृत धातु भंगुर है, जैसे कच्चा लोहा या कांस्य, तो चिप्स के अलग-अलग तत्व वर्कपीस से और एक दूसरे से टूट जाते हैं और अलग हो जाते हैं (चित्र 51, सी)। ऐसी चिप, जिसमें अलग-अलग तराजू होते हैं अनियमित आकार, कहा जाता है टूटे हुए चिप्स.
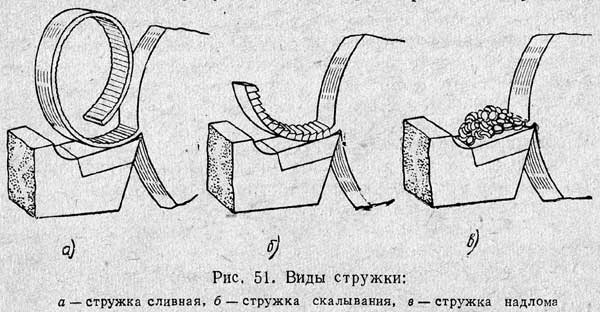
माना जाता है कि चिप्स के प्रकार स्थिर नहीं रहते हैं, वे बदलती परिस्थितियों के साथ बदल सकते हैं। संसाधित होने वाली धातु जितनी नरम होती है और चिप की मोटाई और काटने का कोण जितना छोटा होता है, चिप का आकार उतना ही अधिक होता है। वही देखा जाएगा जब काटने की गति बढ़ाई जाती है और शीतलन लागू किया जाता है। काटने की गति में कमी के साथ, एक नाली चिप के बजाय, चिपिंग चिप्स प्राप्त होते हैं।
बहिर्गमन। यदि आप कटर की सामने की सतह की जांच करते हैं जिसे काटने के लिए इस्तेमाल किया गया था, तो काटने के किनारे पर आप कभी-कभी उच्च तापमान और दबाव में कटर से वेल्डेड धातु की एक छोटी सी गांठ पा सकते हैं। यह तथाकथित है परिणाम(चित्र 52)। यह तन्य धातुओं की कुछ काटने की स्थितियों के तहत प्रकट होता है, लेकिन भंगुर धातुओं को संसाधित करते समय नहीं देखा जाता है। संसाधित होने वाली धातु की कठोरता की तुलना में बिल्ड-अप की कठोरता 2.5-3 गुना अधिक है; इसके लिए धन्यवाद, विकास में ही उस धातु को काटने की क्षमता होती है जिससे इसे बनाया गया था।
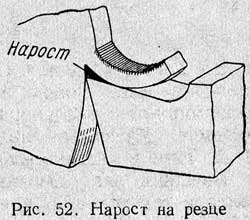
बिल्ड-अप की सकारात्मक भूमिका यह है कि यह काटने वाले ब्लेड को कवर करता है, इसे अवरोही चिप्स और गर्मी की क्रिया से पहनने से बचाता है, और इससे कटर का स्थायित्व कुछ हद तक बढ़ जाता है। छीलते समय बिल्ड-अप की उपस्थिति उपयोगी होती है, क्योंकि काटने वाला ब्लेड कम गर्म होता है और इसका घिसाव कम हो जाता है। हालांकि, बिल्ड-अप के गठन के साथ, मशीनी सतह की सटीकता और सफाई खराब हो जाती है, क्योंकि बिल्ड-अप ब्लेड के आकार को विकृत कर देता है। अतः निर्माण कार्य का निर्माण परिष्करण कार्य के लिए प्रतिकूल है।
8. कटिंग मोड के तत्वों की अवधारणा
प्रत्येक व्यक्तिगत मामले में अधिक कुशलता से प्रसंस्करण करने के लिए, टर्नर को कटिंग मोड के मूल तत्वों को जानना चाहिए; ये तत्व कट, फ़ीड और काटने की गति की गहराई हैं।
कटौती की गहराईमशीनी और मशीनी सतहों के बीच की दूरी को कहा जाता है, जिसे बाद वाले के लंबवत मापा जाता है। कट की गहराई को अक्षर t द्वारा दर्शाया गया है और इसे मिलीमीटर (चित्र 53) में मापा जाता है।
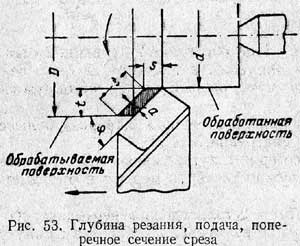
खराद पर वर्कपीस को मोड़ते समय, मशीनिंग भत्ता एक या अधिक पास में काट दिया जाता है।
कट टी की गहराई निर्धारित करने के लिए, कटर के गुजरने से पहले और बाद में वर्कपीस के व्यास को मापना आवश्यक है, व्यास में आधा अंतर कट की गहराई देगा, दूसरे शब्दों में,
जहां डी कटर के गुजरने से पहले मिमी में भाग का व्यास है; d कटर के गुजरने के बाद मिमी में भाग का व्यास है। वर्कपीस के एक चक्कर में कटर की गति (चित्र 53) कहलाती है दाखिल. फ़ीड को अक्षर s द्वारा निरूपित किया जाता है और भाग के प्रति चक्कर मिलीमीटर में मापा जाता है; संक्षिप्तता के लिए, यह मिमी / रेव लिखने की प्रथा है। फ्रेम गाइड के सापेक्ष कटर किस दिशा में चलता है, इस पर निर्भर करता है:
लेकिन) अनुदैर्ध्य फ़ीड- बिस्तर गाइड के साथ;
बी) क्रॉस फीड- बेड गाइड के लंबवत;
में) परोक्ष फ़ीड- बिस्तर के गाइड के कोण पर (उदाहरण के लिए, शंक्वाकार सतह को मोड़ते समय)।
कट . का अनुभागीय क्षेत्रअक्षर f (eff) द्वारा निरूपित और फ़ीड द्वारा कट की गहराई के उत्पाद के रूप में परिभाषित किया गया है (चित्र 53 देखें):
कट और फीड की गहराई के अलावा, वे कट परत की चौड़ाई और मोटाई में भी अंतर करते हैं (चित्र 53)।
परत की चौड़ाई काटना, या चिप की चौड़ाई, - काटने की सतह के साथ मापी गई मशीनी और मशीनी सतहों के बीच की दूरी। इसे मिलीमीटर में मापा जाता है और इसे b (be) अक्षर से दर्शाया जाता है।
कट मोटाई, या चिप मोटाई, चिप की चौड़ाई के लंबवत मापा गया भाग के एक चक्कर में धार की दो क्रमिक स्थितियों के बीच की दूरी है। चिप की मोटाई मिलीमीटर में मापी जाती है और इसे अक्षर a से दर्शाया जाता है।
उसी फ़ीड और कट की गहराई के साथ, के संदर्भ में मुख्य कोण में कमी के साथ, चिप की मोटाई कम हो जाती है, और इसकी चौड़ाई बढ़ जाती है। यह अत्याधुनिक से गर्मी अपव्यय में सुधार करता है और उपकरण जीवन को बढ़ाता है, जो बदले में आपको काटने की गति में काफी वृद्धि करने और प्रति यूनिट समय में अधिक भागों को संसाधित करने की अनुमति देता है। हालांकि, योजना φ में मुख्य कोण में कमी से रेडियल (प्रतिकारक) बल में वृद्धि होती है, जो अपर्याप्त रूप से कठोर भागों को संसाधित करते समय, उन्हें मोड़ने, सटीकता की हानि और मजबूत कंपन का कारण बन सकती है। कंपन की उपस्थिति, बदले में, मशीनी सतह की शुद्धता में गिरावट की ओर ले जाती है और अक्सर कटर के काटने के किनारे को छिलने का कारण बनती है।
काटने की गति. एक खराद पर मशीनिंग करते समय, व्यास D (चित्र 54) के एक वृत्त पर स्थित बिंदु A, भाग के एक चक्कर में इस वृत्त की लंबाई के बराबर पथ की यात्रा करता है।
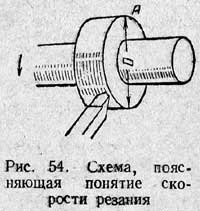
किसी भी वृत्त की लंबाई उसके व्यास का लगभग 3.14 गुना होती है, इसलिए यह 3.14 D के बराबर होता है।
संख्या 3.14, यह दर्शाती है कि किसी वृत्त की लंबाई उसके व्यास से कितनी गुना अधिक है, आमतौर पर ग्रीक अक्षर (pi) द्वारा निरूपित किया जाता है।
बिंदु A एक चक्कर में D के बराबर पथ बनाएगा। भाग का व्यास D, साथ ही इसकी परिधि πD, मिलीमीटर में मापा जाता है।
मान लें कि वर्कपीस प्रति मिनट कई चक्कर लगाएगा। आइए हम उनकी संख्या को अक्षर n क्रांतियों प्रति मिनट, या संक्षिप्त रूप में rpm द्वारा निरूपित करें। इस मामले में बिंदु A जो पथ लेगा वह परिधि के गुणनफल और प्रति मिनट क्रांतियों की संख्या के बराबर होगा, अर्थात Dn मिलीमीटर प्रति मिनट या संक्षिप्त मिमी / मिनट, और कहा जाता है परिधीय गति.
रास्ता, पास करने योग्य बिंदुएक मिनट में कटर की धार के सापेक्ष मुड़ने पर मशीनीकृत होने वाली सतह कहलाती है काटने की गति.
चूंकि भाग व्यास आमतौर पर मिलीमीटर में व्यक्त किया जाता है, मीटर प्रति मिनट में काटने की गति को खोजने के लिए, Dn को 1000 से विभाजित करें। इसे निम्न सूत्र के रूप में लिखा जा सकता है:
जहां v काटने की गति मी/मिनट में है;
डी मिमी में वर्कपीस का व्यास है;
n प्रति मिनट क्रांतियों की संख्या है।
उदाहरण 3संसाधित रोलर व्यास डी = 100 = 150 आरपीएम। काटने की गति निर्धारित करें।
समाधान: स्पिंडल स्पीड काउंट. ज्ञात व्यास के एक हिस्से को मोड़ते समय, आवश्यक काटने की गति प्राप्त करने के लिए टर्नर के लिए मशीन को इतनी संख्या में धुरी क्रांतियों में समायोजित करना आवश्यक हो सकता है। इसके लिए निम्न सूत्र का प्रयोग किया जाता है: जहां डी मिमी में वर्कपीस का व्यास है;
उदाहरण 4डी \u003d 50 मिमी के व्यास वाले रोलर को प्रति मिनट कितने चक्कर लगाने चाहिए, जिसकी काटने की गति v \u003d 25 मीटर / मिनट होनी चाहिए?
समाधान:
9. कटर और काटने की शक्ति पर कार्य करने वाले बलों के बारे में बुनियादी जानकारी
कटर पर अभिनय करने वाले बल. वर्कपीस से चिप्स निकालते समय, कटर को एक दूसरे से धातु के कणों के आसंजन के बल को दूर करना चाहिए। जब कटर का काटने वाला किनारा संसाधित की जा रही सामग्री में कट जाता है और चिप को अलग कर दिया जाता है, तो कटर धातु के अलग होने से दबाव का अनुभव करता है (चित्र 55)।

ऊपर से नीचे तक, P z बल कटर पर दबाता है, जो कटर को नीचे दबाता है और भाग को ऊपर की ओर मोड़ता है। इस बल को कहा जाता है काटने की शक्ति.
क्षैतिज तल में फ़ीड गति के विपरीत दिशा में, कटर को P x बल द्वारा दबाया जाता है, जिसे कहा जाता है अक्षीय ताकत, या फ़ीड बल. अनुदैर्ध्य मोड़ के दौरान यह बल कटर को टेलस्टॉक की ओर दबाता है।
क्षैतिज तल में, फ़ीड दिशा के लंबवत, कटर को बल P y द्वारा दबाया जाता है, जिसे रेडियल बल कहा जाता है। यह बल कटर को वर्कपीस से दूर धकेलता है और उसे क्षैतिज दिशा में मोड़ता है।
सभी सूचीबद्ध बलों को किलोग्राम में मापा जाता है।
तीन बलों में सबसे बड़ा ऊर्ध्वाधर काटने वाला बल है: यह फ़ीड बल का लगभग 4 गुना और रेडियल बल का 2.5 गुना है। काटने का बल हेडस्टॉक तंत्र के कुछ हिस्सों को लोड करता है; यह कटर, भाग को भी लोड करता है, जिससे अक्सर उनमें बड़े तनाव पैदा होते हैं।
प्रयोगों ने स्थापित किया है कि काटने की शक्ति संसाधित की जा रही सामग्री के गुणों, चिप के खंड के आकार और आकार, कटर के आकार, काटने की गति और शीतलन पर निर्भर करती है।
प्रतिरोध को चिह्नित करने के लिए विभिन्न सामग्रीकटिंग ने गुणांक काटने की अवधारणा को स्थापित किया। कटिंग फैक्टर K, कटिंग सेक्शन के किलोग्राम प्रति वर्ग मिलीमीटर में कटिंग प्रेशर है, जिसे कुछ कटिंग स्थितियों के तहत मापा जाता है:
कट टी की गहराई …………….5 मिमी
फ़ीड एस......................1 मिमी/रेव
रेक कोण γ......................15°
अग्रणी कोण φ.......45°
कटर का अत्याधुनिक - सीधा, क्षैतिज
कटर की नोक को त्रिज्या r = 1 मिमी . के साथ गोल किया जाता है
बिना कूलिंग के होता है काम
तालिका में। 3 कुछ धातुओं के लिए काटने के कारक के औसत मूल्यों को दर्शाता है।
टेबल तीन
मोड़ते समय कटिंग फैक्टर K का औसत मान
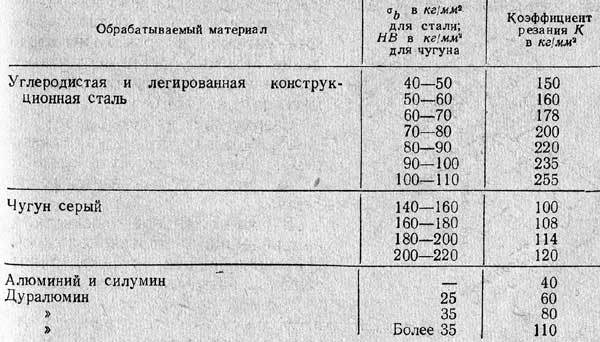
यदि काटने का कारक K ज्ञात है, तो इसे मिमी 2 में कटे हुए f के क्रॉस-सेक्शनल क्षेत्र से गुणा करके, आप सूत्र का उपयोग करके काटने वाले बल का अनुमानित मान ज्ञात कर सकते हैं।
पी जेड \u003d केएफ किलो। (8)
उदाहरण 5 b = 60 किग्रा / मिमी 2 के साथ मशीन से बने स्टील से बने शाफ्ट को एक खराद पर घुमाया जाता है। यदि कट टी = 5 मिमी की गहराई और फ़ीड एस = 0.5 मिमी/रेव की गहराई हो तो काटने के बल का निर्धारण करें।
समाधान। सूत्र (8) के अनुसार, काटने की शक्ति पी जेड \u003d केएफ किलो। (8)हम f: f \u003d ts \u003d 5x0.5 \u003d 2.5 मिमी 2 का मान निर्धारित करते हैं। तालिका के अनुसार 3 हम मशीन-निर्मित स्टील के लिए K का मान b \u003d 60 किग्रा / मिमी 2: K \u003d 160 किग्रा / मिमी 2 के साथ पाते हैं। इसलिए, z = Kf = 160x2.5 = 400 किग्रा। काटने की शक्ति. काटने की शक्ति और काटने की गति को जानकर, आप यह पता लगा सकते हैं कि किसी दिए गए खंड के चिप्स को काटने के लिए कितनी शक्ति की आवश्यकता है।
काटने की शक्ति सूत्र द्वारा निर्धारित की जाती है (9) जहां एन रेस - एचपी में बिजली काटने;
पी जेड - किलो में काटने की शक्ति;
v - मी/मिनट में काटने की गति।
मशीन टूल की इलेक्ट्रिक मोटर की शक्ति काटने की शक्ति से कुछ अधिक होनी चाहिए, क्योंकि इलेक्ट्रिक मोटर की शक्ति का एक हिस्सा इलेक्ट्रिक मोटर से मशीन स्पिंडल तक गति संचारित करने वाले तंत्र में घर्षण पर काबू पाने में खर्च होता है।
उदाहरण 6पिछले उदाहरण में माना जाता है कि शाफ्ट को मोड़ने के लिए काटने की शक्ति का निर्धारण करें, यदि प्रसंस्करण एक काटने की गति से किया जाता है, = 60 मीटर/मिनट। समाधान । सूत्र (9) के अनुसार, काटने की शक्ति
काटने की शक्ति आमतौर पर अश्वशक्ति में नहीं, बल्कि किलोवाट (किलोवाट) में व्यक्त की जाती है। एक किलोवाट 1.36 गुना अश्वशक्ति है, इसलिए किलोवाट में शक्ति व्यक्त करने के लिए, आपको अश्वशक्ति को 1.36 से विभाजित करने की आवश्यकता है:
और इसके विपरीत,
10. कट और उपकरण जीवन की गर्मी
काटने के बल में वृद्धि के साथ, घर्षण बल बढ़ता है, जिसके परिणामस्वरूप काटने की प्रक्रिया के दौरान निकलने वाली गर्मी की मात्रा बढ़ जाती है। काटने की गति बढ़ने के साथ-साथ काटने की गर्मी और भी अधिक बढ़ जाती है, क्योंकि इससे चिप बनने की पूरी प्रक्रिया तेज हो जाती है।
इसे अपर्याप्त हटाने के साथ काटने की उत्पन्न गर्मी कटर को नरम करती है, जिसके परिणामस्वरूप इसके काटने वाले हिस्से का पहनना अधिक तीव्रता से होता है। इससे कटर को बदलना या इसे तेज करना और इसे फिर से स्थापित करना आवश्यक हो जाता है।
ब्लंटिंग से पहले कटर के लगातार काम करने के समय को टूल लाइफ (मिनटों में मापा जाता है) कहा जाता है। कटर का बार-बार परिवर्तन (लघु उपकरण जीवन) का कारण बनता है अतिरिक्त व्ययकटर को तेज करने और स्थापित करने के लिए, साथ ही पहने हुए कटर को फिर से भरने के लिए।
इसलिए, उपकरण जीवन है एक महत्वपूर्ण कारककाटने की स्थिति चुनते समय, खासकर जब काटने की गति चुनते हैं।
कटर का स्थायित्व मुख्य रूप से उस सामग्री के गुणों पर निर्भर करता है जिससे इसे बनाया जाता है। सबसे प्रतिरोधी कटर होगा, जो एक ऐसी सामग्री से बना है जो कठोरता के महत्वपूर्ण नुकसान के बिना उच्चतम ताप तापमान की अनुमति देता है। कठोर मिश्र धातु प्लेटों, खनिज-सिरेमिक प्लेटों से लैस कटरों में सबसे बड़ा प्रतिरोध होता है; काफी कम प्रतिरोध - उच्च गति वाले स्टील से बने कटर, सबसे छोटे - कार्बन टूल स्टील से बने कटर।
कटर का प्रतिरोध संसाधित होने वाली सामग्री के गुणों, कट सेक्शन, कटर के शार्पनिंग एंगल्स और काटने की गति पर भी निर्भर करता है। मशीनीकृत होने वाली सामग्री की कठोरता बढ़ने से उपकरण का जीवन कम हो जाता है।
तीक्ष्ण कोणों और सामने की सतह के आकार को बदलकर, कटर के स्थायित्व और उनकी उत्पादकता में उल्लेखनीय वृद्धि प्राप्त करना संभव है।
उपकरण जीवन पर काटने की गति का विशेष रूप से मजबूत प्रभाव पड़ता है। कभी-कभी गति में थोड़ी सी भी वृद्धि से कटर का तेजी से कुंद हो जाता है। उदाहरण के लिए, यदि उच्च गति वाले कटर से स्टील को संसाधित करते समय, काटने की गति केवल 10% बढ़ जाती है, अर्थात, 1.1 गुना, तो कटर दो बार तेज और इसके विपरीत सुस्त हो जाएगा।
कट के क्रॉस-सेक्शनल क्षेत्र में वृद्धि के साथ, उपकरण का जीवन कम हो जाता है, लेकिन उतना नहीं जितना कि काटने की गति में वृद्धि के साथ।
टूल का जीवन टूल के आकार, कट सेक्शन के आकार और कूलिंग पर भी निर्भर करता है। कटर जितना अधिक विशाल होता है, उतना ही बेहतर यह अत्याधुनिक से गर्मी को दूर करता है और इसके परिणामस्वरूप, इसकी स्थायित्व जितनी अधिक होती है।
प्रयोगों से पता चलता है कि कट के एक ही खंड के साथ, कट की एक बड़ी गहराई और एक छोटी फ़ीड एक समान रूप से बड़े फ़ीड के साथ कट की एक छोटी गहराई की तुलना में अधिक उपकरण जीवन प्रदान करती है। यह इस तथ्य से समझाया गया है कि कटौती की अधिक गहराई के साथ, चिप्स काटने वाले किनारे की अधिक लंबाई के संपर्क में आते हैं, इसलिए गर्मी काटना बेहतर होता है। इसीलिए, एक ही कट सेक्शन के साथ, अधिक से अधिक फीड के साथ अधिक गहराई के साथ काम करना अधिक लाभदायक होता है।
ठंडा होने पर कटर का स्थायित्व काफी बढ़ जाता है।
शीतलक की भरपूर मात्रा में आपूर्ति की जानी चाहिए (इमल्शन 10-12 लीटर/मिनट, तेल और सल्फ़ोफ़्रेसोल 3-4 लीटर/मिनट); तरल की एक छोटी मात्रा न केवल लाभ नहीं देती है, बल्कि कटर को भी खराब कर देती है, जिससे इसकी सतह पर छोटी दरारें दिखाई देती हैं, जिससे छिल जाता है।
11. गति काटने का विकल्प
श्रम उत्पादकता काटने की गति की पसंद पर निर्भर करती है: काटने की गति जितनी अधिक होगी, कम समयप्रसंस्करण पर खर्च किया गया। हालांकि, जैसे-जैसे काटने की गति बढ़ती है, उपकरण का जीवन कम हो जाता है, इसलिए काटने की गति का चुनाव उपकरण के जीवन और उपकरण के जीवन को प्रभावित करने वाले सभी कारकों से प्रभावित होता है। इनमें से सबसे महत्वपूर्ण हैं मशीनीकृत होने वाली सामग्री के गुण, कटर की सामग्री की गुणवत्ता, कट की गहराई, फ़ीड, कटर के आयाम और तीक्ष्ण कोण और शीतलन।
1. उपकरण का जीवन जितना लंबा होना चाहिए, काटने की गति उतनी ही कम होनी चाहिए और इसके विपरीत।
2. कठिन सामग्री संसाधित की जा रही है, कम उपकरण जीवन, इसलिए, कठिन सामग्री को मशीनिंग करते समय आवश्यक प्रतिरोध सुनिश्चित करने के लिए, काटने की गति को कम करना होगा। जब मशीनिंग कास्ट और जाली वर्कपीस, जिसकी सतह पर एक कठोर क्रस्ट, शेल या स्केल होता है, तो उस के खिलाफ काटने की गति को कम करना आवश्यक है जो बिना क्रस्ट के मशीनिंग सामग्री के दौरान संभव है।
3. कटर के भौतिक गुण इसके स्थायित्व को निर्धारित करते हैं, इसलिए, काटने की गति का चुनाव भी इन गुणों पर निर्भर करता है। अन्य चीजें समान होने के कारण, उच्च गति वाले स्टील कटर कार्बन स्टील कटर की तुलना में काफी अधिक काटने की गति की अनुमति देते हैं; यहां तक कि उच्च काटने की गति भी कटर को कठोर मिश्र धातुओं से लैस करने की अनुमति देती है।
4. चिपचिपी धातुओं को संसाधित करते समय कटर के प्रतिरोध को बढ़ाने के लिए, कटर के शीतलन का उपयोग करना फायदेमंद होता है। इस मामले में, एक ही उपकरण जीवन के साथ, बिना शीतलन के मशीनिंग की तुलना में काटने की गति को 15-25% तक बढ़ाना संभव है।
5. कटर के आयाम और इसके तेज करने के कोण भी स्वीकार्य काटने की गति को प्रभावित करते हैं: कटर जितना अधिक विशाल होता है, विशेष रूप से उसका सिर, उतना ही बेहतर यह काटने के दौरान उत्पन्न गर्मी को हटा देता है। गलत तरीके से चुने गए कटर कोण जो संसाधित की जा रही सामग्री के अनुरूप नहीं हैं, काटने की शक्ति को बढ़ाते हैं और कटर के तेजी से पहनने में योगदान करते हैं।
6. कट सेक्शन में वृद्धि के साथ, टूल लाइफ कम हो जाती है, इसलिए, एक बड़े सेक्शन के साथ, एक छोटे सेक्शन की तुलना में कम काटने की गति चुनना आवश्यक है।
चूंकि परिष्करण के दौरान छोटे चिप्स हटा दिए जाते हैं, इसलिए परिष्करण के दौरान काटने की गति खुरदरापन की तुलना में बहुत अधिक हो सकती है।
चूंकि कट सेक्शन में वृद्धि से कटिंग स्पीड में वृद्धि की तुलना में टूल लाइफ पर कम प्रभाव पड़ता है, इसलिए कटिंग स्पीड को थोड़ा कम करके कट सेक्शन को बढ़ाना फायदेमंद होता है। कुइबिशेव मशीन टूल प्लांट वी। कोलेसोव के इनोवेटर टर्नर की प्रसंस्करण विधि इस सिद्धांत पर आधारित है। 150 मीटर/मिनट की कटिंग गति से काम करते हुए, टी. कोलेसोव 0.3 मिमी/रेव के बजाय 3 मिमी/रेव तक की फ़ीड दर के साथ स्टील के पुर्जों को खत्म करता है, और इससे मशीन के समय में 8-10 गुना की कमी आती है।
सवाल उठता है: उन्नत टर्नर अक्सर काटने की गति बढ़ाकर श्रम उत्पादकता क्यों बढ़ाते हैं? क्या यह काटने के बुनियादी नियमों का खंडन नहीं करता है? नहीं, यह विरोधाभास नहीं है। वे केवल उन मामलों में काटने की गति बढ़ाते हैं जहां कटौती के अनुभाग को बढ़ाने के अवसरों का पूरी तरह से उपयोग किया जाता है।
जब अर्ध-परिष्करण या परिष्करण किया जाता है, जहां कटौती की गहराई मशीनिंग के लिए एक छोटे से भत्ते द्वारा सीमित होती है, और फ़ीड मशीनिंग की उच्च शुद्धता की आवश्यकताओं से सीमित होती है, काटने की गति को बढ़ाकर काटने के मोड में वृद्धि संभव है . यह वही है जो उन्नत टर्नर करते हैं, अर्ध-परिष्करण और परिष्करण पर काम करते हैं। के साथ काम करना संभव हो तो बड़े खंडकट (बड़े भत्तों के साथ), फिर, सबसे पहले, कट की सबसे बड़ी संभव गहराई का चयन करना आवश्यक है, फिर सबसे बड़ा संभव तकनीकी रूप से अनुमेय फ़ीड, और अंत में, संबंधित काटने की गति।
ऐसे मामलों में जहां मशीनिंग भत्ता छोटा है और सतह खत्म करने के लिए कोई विशेष आवश्यकताएं नहीं हैं, काटने के मोड को सबसे बड़ा संभव फ़ीड का उपयोग करके बढ़ाया जाना चाहिए।
12. मशीनी सतह की सफाई
जब एक कटर के साथ मशीनिंग करते हैं, तो सबसे सावधानीपूर्वक परिष्करण के साथ, अवसाद और स्कैलप्स के रूप में अनियमितताएं हमेशा भाग की मशीनी सतह पर बनी रहती हैं। खुरदरापन की ऊंचाई प्रसंस्करण विधि पर निर्भर करती है।
अभ्यास ने स्थापित किया है कि जिस हिस्से की सतह को साफ किया जाता है, वह उतना ही कम पहनने और जंग के अधीन होता है, और हिस्सा मजबूत होता है।
सावधानीपूर्वक सतह परिष्करण जब किसी भाग की मशीनिंग हमेशा किसी न किसी सतह खत्म की तुलना में अधिक महंगी होती है। इसलिए, मशीन की सतह की सफाई को भाग की परिचालन स्थितियों के आधार पर सौंपा जाना चाहिए।
चित्र में सतह की सफाई का पदनाम. GOST 2789-59 के अनुसार, सतह की सफाई के 14 वर्ग प्रदान किए जाते हैं। सभी शुद्धता वर्गों को नामित करने के लिए, एक चिन्ह स्थापित किया गया है - एक समबाहु त्रिभुज, जिसके आगे वर्ग संख्या इंगित की गई है (उदाहरण के लिए, 7; 8; 14)। सबसे साफ सतहों को 14 और सबसे खुरदरी ग्रेड 1 ग्रेड दिया गया है।
GOST 2789-59 के अनुसार सतह खुरदरापन दो मापदंडों में से एक द्वारा निर्धारित किया जाता है: a) प्रोफ़ाइल का अंकगणितीय माध्य विचलन R a और b) अनियमितताओं की ऊंचाई R z ।
खुरदरापन मापने और उपचारित सतह को किसी विशेष वर्ग को सौंपने के लिए, विशेष मापन उपकरणपतली हीरे की सुई के साथ सतह प्रोफ़ाइल को महसूस करने की विधि के आधार पर। ऐसे उपकरणों को प्रोफिलोमीटर और प्रोफिलोग्राफ कहा जाता है।
खुरदरापन निर्धारित करने और उपचारित सतह को कार्यशाला की स्थितियों में सफाई के एक या दूसरे वर्ग में वर्गीकृत करने के लिए, स्वच्छता के विभिन्न वर्गों के परीक्षण किए गए नमूनों का उपयोग किया जाता है - तथाकथित शुद्धता मानक, जिसके साथ भाग की मशीनी सतह की तुलना की जाती है।
भूतल खत्म को प्रभावित करने वाले कारक. अभ्यास ने स्थापित किया है कि मशीनी सतह की सफाई कई कारणों पर निर्भर करती है: मशीन की जा रही सामग्री, कटर की सामग्री, तीक्ष्ण कोण और कटर के काटने वाले किनारों की स्थिति, फ़ीड और काटने की गति, चिकनाई और तरल के शीतलन गुण, सिस्टम मशीन की कठोरता - कटर - भाग, आदि।
विशेष रूप से महत्त्वसतह पाने के लिए उच्च गुणवत्तामोड़ते समय, इसमें काटने की गति, फ़ीड, लीड कोण और टूल टिप की वक्रता त्रिज्या होती है। फ़ीड और प्रवेश कोण जितना छोटा होगा और कोने का दायरा जितना बड़ा होगा, मशीन की सतह उतनी ही साफ होगी। काटने की गति सतह खत्म को बहुत प्रभावित करती है। स्टील को 100 मीटर/मिनट से अधिक की कटिंग गति से घुमाते समय, मशीनीकृत सतह 25-30 मीटर/मिनट की गति की तुलना में अधिक साफ होती है।
एक क्लीनर मशीनी सतह प्राप्त करने के लिए, काटने वाले किनारों को सावधानीपूर्वक तेज करने और खत्म करने पर ध्यान देना चाहिए।
परीक्षण प्रश्न 1. चिपचिपी धातुओं की मशीनिंग करते समय चिप किस आकार का होता है? भंगुर धातुओं को संसाधित करते समय?
2. कृन्तक शीर्ष के मुख्य तत्वों के नाम लिखिए।
3. कृन्तक पर आगे और पीछे की सतहों को दिखाएँ; सामने और पीछे के कोने; तीक्ष्ण कोण।
4. कृन्तक के आगे और पीछे के कोनों का उद्देश्य क्या है?
5. लीड कोण और लीड कोण दिखाएं।
6. कटर किस सामग्री से बने होते हैं?
7. इस्पात प्रसंस्करण में किस ग्रेड के कठोर मिश्र धातुओं का उपयोग किया जाता है? कच्चा लोहा प्रसंस्करण करते समय?
8. कटिंग मोड तत्वों की सूची बनाएं।
9. कटर पर कौन से बल कार्य करते हैं?
10. कौन से कारक और वे काटने वाले बल के परिमाण को कैसे प्रभावित करते हैं?
11. कटर का स्थायित्व क्या निर्धारित करता है?
12. काटने की गति की पसंद को कौन से कारक प्रभावित करते हैं?
प्रक्रिया में उपयोग किए जाने वाले मुख्य काटने के उपकरण में एक कटर शामिल होता है, जिसके ज्यामितीय पैरामीटर इसकी तकनीकी क्षमताओं, सटीकता और प्रसंस्करण दक्षता को निर्धारित करते हैं। कोई भी विशेषज्ञ जो खुद को समर्पित करने का फैसला करता है कारोबार मोड़ना, जहां तक कि सही पसंदअत्याधुनिक कोण उपकरण जीवन और उत्पादकता दोनों को बढ़ाते हैं।
टर्निंग टूल्स के पैरामीटर्स
कोई भी टर्निंग टूलधारक में उपकरण को ठीक करने के लिए आवश्यक धारक बनाएं खराद, और एक काम करने वाला सिर जो धातु काटने की सुविधा प्रदान करता है। टर्निंग टूल के ज्यामितीय मापदंडों पर विचार करने के लिए, थ्रू टूल को नमूने के रूप में लेना बेहतर है।
टर्निंग टूल के काटने वाले हिस्से पर इस प्रकार केतीन सतहें हैं:
- सामने (उस पर वर्कपीस के प्रसंस्करण के दौरान, धातु के चिप्स निकल रहे हैं);
- पीछे - मुख्य और सहायक (दोनों अपने सामने के हिस्से के साथ वर्कपीस में बदल गए)।
उपकरण का किनारा, जिसे अत्याधुनिक (और सीधे प्रसंस्करण में शामिल) कहा जाता है, इसके सामने और मुख्य पीछे की सतहों के प्रतिच्छेदन से बनता है। टर्निंग टूल की ज्यामिति में, एक सहायक कटिंग एज भी प्रतिष्ठित है। यह, क्रमशः, सहायक पीठ के साथ सामने की सतह के चौराहे से बनता है।
जिस बिंदु पर मुख्य और द्वितीयक काटने वाले किनारे प्रतिच्छेद करते हैं उसे कटर का सिरा कहा जाता है। उत्तरार्द्ध, जब धातु काटते हैं, तो भारी भार का अनुभव होता है, जिससे यह टूट जाता है। कटर की नोक के प्रतिरोध को बढ़ाने के लिए, इसे तेज करने की प्रक्रिया के दौरान तेज नहीं किया जाता है, लेकिन थोड़ा गोल किया जाता है। इसके लिए शीर्ष त्रिज्या जैसे पैरामीटर की शुरूआत की आवश्यकता होती है। टर्निंग टूल की नोक के प्रतिरोध को बढ़ाने का एक और तरीका है - एक संक्रमणकालीन कटिंग एज का निर्माण जिसमें एक सीधा आकार होता है।
मोड़ने के लिए कटर के सबसे महत्वपूर्ण ज्यामितीय पैरामीटर उनके कोण हैं, जो निर्धारित करते हैं आपसी व्यवस्थाउपकरण सतहों। टर्निंग टूल के प्रकार और कई अन्य कारकों के आधार पर कोण पैरामीटर भिन्न होते हैं:
- उपकरण सामग्री;
- उसकी काम करने की स्थिति;
- संसाधित की जाने वाली सामग्री की विशेषताएं।
मोड़ के लिए उपकरण कोण
कोणों को सही ढंग से निर्धारित करने के लिए टर्निंग टूल, उन्हें सटीक मान, उन्हें तथाकथित प्रारंभिक विमानों में माना जाता है।
- मुख्य विमान टर्निंग टूल (अनुदैर्ध्य और अनुप्रस्थ) की फ़ीड दिशाओं के समानांतर है और इसकी सहायक सतह के साथ मेल खाता है।
- काटने वाले विमान में मुख्य अत्याधुनिक शामिल है और मशीनिंग सतह के लिए स्पर्शरेखा है। यह विमान मुख्य के लंबवत है।
- मुख्य काटने वाला विमान मुख्य काटने के किनारे को काटता है और प्रक्षेपण के लंबवत स्थित होता है कि यह किनारा मुख्य विमान पर रहता है। एक सहायक सेकेंट-प्रकार का विमान भी है, जो तदनुसार, सहायक विमान द्वारा मुख्य विमान पर जमा प्रक्षेपण के लिए लंबवत है।
जैसा कि ऊपर उल्लेख किया गया है, उन्हें इन विमानों में ठीक से मापा जाता है, और जिन्हें एक विमान में मापा जाता है जिन्हें मुख्य छेदक कहा जाता है, उन्हें मुख्य के रूप में नामित किया जाता है। ये, विशेष रूप से, मुख्य सामने, मुख्य पीछे के कोण, साथ ही तीक्ष्ण और काटने के कोण हैं।
सबसे महत्वपूर्ण में से एक टर्निंग टूल का मुख्य क्लीयरेंस एंगल है, जो उस घर्षण को कम करता है जो तब होता है जब टूल की पिछली सतह उस हिस्से के साथ इंटरैक्ट करती है जिसे वर्तमान में संसाधित किया जा रहा है (और इसलिए टूल के हीटिंग को कम करता है और इसके जीवन का विस्तार करता है) ) यह कोण कटर सतह (मुख्य पीछे) और काटने वाले विमान द्वारा बनता है। उपकरण को तेज करते समय इस कोण को चुनते समय, प्रसंस्करण के प्रकार और वर्कपीस की सामग्री को ध्यान में रखा जाता है। इस मामले में, आपको अवगत होना चाहिए कि निकासी कोण के आकार में एक मजबूत वृद्धि टर्निंग टूल की तीव्र विफलता की ओर ले जाती है।
काटने के उपकरण की ताकत और स्थायित्व, प्रसंस्करण के दौरान होने वाली ताकतों को रेक कोण के मापदंडों द्वारा निर्धारित किया जाता है। यह टर्निंग टूल की सामने की सतह और उस प्लेन के बीच स्थित है जिसमें मुख्य कटिंग एज स्थित है (यह प्लेन कटिंग प्लेन के लंबवत है)। टर्निंग टूल को तेज करते समय, कई कारकों को ध्यान में रखा जाता है जो इस कोण के मूल्य को प्रभावित करते हैं:
- वर्कपीस सामग्री और उपकरण ही;
- सामने की सतह का आकार;
- जिन शर्तों के तहत कटर का उपयोग किया जाएगा।
रेक कोण के मूल्य में वृद्धि, एक ओर, प्रसंस्करण की समाप्ति में सुधार करती है, और दूसरी ओर, यह टर्निंग टूल की ताकत और स्थायित्व में कमी को भड़काती है। तीक्ष्णता के परिणामस्वरूप प्राप्त इस तरह के कोण में एक सकारात्मक और हो सकता है नकारात्मक अर्थ.
रेक कोण वाले टर्निंग कटर जिनमें ऋणात्मक मान होते हैं वे अत्यधिक टिकाऊ होते हैं, लेकिन ऐसे उपकरणों के साथ मशीनिंग मुश्किल है। आम तौर पर एक रेक कोण के साथ तेज करना, जिसका सकारात्मक मूल्य होता है, का उपयोग तब किया जाता है जब वर्कपीस को चिपचिपा सामग्री से संसाधित किया जाना होता है, और जब उपकरण सामग्री अत्यधिक टिकाऊ होती है।
नकारात्मक रेक कोण वाले कटर का उपयोग तब किया जाता है जब उच्च कठोरता और ताकत के साथ मशीनिंग सामग्री, बाधित कटिंग करते समय, जब उपकरण सामग्री में पर्याप्त झुकने की शक्ति नहीं होती है और शॉक लोड को अच्छी तरह से अवशोषित नहीं करता है।
टर्निंग के लिए कटर की ज्यामिति को दर्शाने वाले पैरामीटर भी कटिंग और पॉइंटिंग एंगल हैं। काटने का कोण, जिसका मान 60-100 0 के भीतर भिन्न हो सकता है, उपकरण की सतह के बीच स्थित होता है, जिसे सामने कहा जाता है, और काटने वाला विमान।
इस कोण का मूल्य सीधे संसाधित होने वाली धातु की कठोरता पर निर्भर करता है: यह जितना अधिक होगा, इसका मूल्य उतना ही अधिक होगा। टेपर एंगल पूरी तरह से अपने नाम के अनुरूप है, इसे टूल के मुख्य फ्रंट और मेन बैक सतहों के बीच मापा जाता है और इसके टॉप के शार्पनिंग की डिग्री को दर्शाता है।
योजना में टर्निंग टूल और कोणों को चिह्नित करें। यह मुख्य है, जिसे अनुदैर्ध्य फ़ीड की दिशा और प्रक्षेपण के बीच मापा जाता है कि मुख्य काटने वाला किनारा मुख्य विमान पर रहता है, और सहायक एक, मुख्य विमान पर सहायक काटने वाले किनारे के प्रक्षेपण और दिशा की दिशा अनुदैर्ध्य फ़ीड।
तेज करते समय, इन कोणों को मनमाने ढंग से नहीं चुना जाता है, लेकिन मोड़ के प्रकार और कठोरता के आधार पर "मशीन-टूल-वर्कपीस" प्रणाली है। तो, अधिकांश धातुओं का प्रसंस्करण 45 0 के बराबर योजना में मुख्य कोण वाले उपकरणों के साथ किया जा सकता है, लेकिन पतले और लंबे वर्कपीस को कटर से संसाधित किया जाना चाहिए, जिसमें इस कोण का मान 60- की सीमा में हो- 90 0। भाग के विक्षेपण और कंपन को समाप्त करने के लिए यह आवश्यक है।
लीड में सहायक कोण एक साथ मशीनिंग की समाप्ति और उपकरण जीवन के साथ सहसंबद्ध होता है। इसकी कमी के साथ, प्रसंस्करण की सफाई बढ़ती है और उपकरण जीवन बढ़ता है।
ऊपर चर्चा किए गए लोगों के अलावा, टर्निंग टूल्स की ज्यामिति में, कोणों को प्रतिष्ठित किया जाता है।
अनुदैर्ध्य मोड़ को मोड़ कहा जाता है, जिसमें फ़ीड की गति की दिशा वर्कपीस की धुरी के समानांतर होती है। खराद पर, काटने की गति - रोटेशन - वर्कपीस से जुड़ी होती है, और फ़ीड गति - ट्रांसलेशनल मूवमेंट - कटर से जुड़ी होती है। राउंड स्टिक मशीनों पर, काटने का उपकरण घूमता है, और फ़ीड गति वर्कपीस से जुड़ी होती है। असली काटने का रास्ता एक पेचदार रेखा है।
फाइन और रफ टर्निंग में अंतर बताइए।
फाइन टर्निंग (चित्र 2, ए) एक कटर के साथ फ्लैट काम करने वाली सतहों और सीधे काटने वाले किनारों के साथ किया जाता है - मुख्य और सहायक। वर्कपीस के रोटेशन की धुरी के सापेक्ष काटने वाले किनारों की स्थिति को लीड में मुख्य कोण और लीड में सहायक कोण की विशेषता है। योजना में सहायक कोण का मान गतिज अनियमितताओं की गहराई को निर्धारित करता है, इसलिए यह बड़ा नहीं हो सकता। मुख्य कटिंग एज बनाने वाले चेहरों की स्थिति को क्लीयरेंस एंगल, शार्पनिंग एंगल और रेक एंगल की विशेषता है।
मुख्य काटने वाला किनारा क्रॉस-फेस कटिंग का उत्पादन करता है, जो लकड़ी के तंतुओं के झुकाव के कोण की विशेषता है।
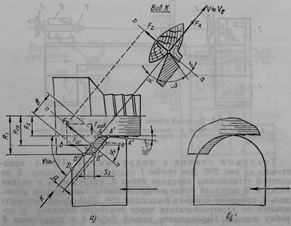
चावल। 2. अनुदैर्ध्य मोड़ परिष्करण (ए) और खुरदरापन (बी)
झुकाव के कोण को तंतुओं की दिशा और सामान्य के बीच मापा जाता है।
रफ टर्निंग (चित्र 2, बी) एक अर्धवृत्ताकार कटिंग एज के साथ ग्रूव्ड कटर के साथ किया जाता है। अनुप्रस्थ अनुभागचिप्स सिकल के आकार के होते हैं, वर्कपीस की परिधि पर चिप्स की मोटाई अधिकतम होती है, और भाग की सतह के पास यह कटर को उच्च फ़ीड पर भी महत्वहीन होता है। यह आपको प्रति कटर फ़ीड को 2 मिमी तक लागू करने की अनुमति देता है, जबकि ठीक मोड़ के लिए - 0.8 मिमी से अधिक नहीं।
> खराद की स्थापना
खराद स्थापित करते समय, यह आवश्यक है: एक कटर का चयन करें और इसे उपकरण धारक (यांत्रिक फ़ीड वाली मशीनों के लिए) में ठीक करें; एक फेसप्लेट या चक स्थापित करें; हाथ आराम का चयन करें और ठीक करें (मशीनों के लिए हस्त प्रविष्टि) या कॉपी रूलर (मैकेनिकल फीड वाली मशीनों के लिए); मशीन में वर्कपीस को स्थापित और ठीक करें; बेकार में मशीन का परीक्षण करें; धुरी की गति और फ़ीड दर निर्धारित करें; परीक्षण टुकड़ों की प्रक्रिया और निरीक्षण करें।
प्रदर्शन किए गए कार्य की प्रकृति के आधार पर आवश्यक कटर का चयन किया जाता है। प्रारंभिक खुरदरापन के लिए, एक छीलने वाले कटर का उपयोग किया जाता है, अंतिम के लिए, एक सीधे काटने वाले किनारे के साथ एक परिष्करण कटर। यांत्रिक फ़ीड के साथ, उपकरण धारक में कटर को शिकंजा के साथ तय किया गया है। बदलाव के समय को कम करने के लिए, विशेष रोटरी हेड्स का उपयोग किया जाता है, जहां विभिन्न प्रयोजनों के लिए कई इंसुलेटर एक साथ मजबूत किए जाते हैं।
पर मैनुअल कामलकड़ी के हैंडल पर कटर को बन्धन की विश्वसनीयता की जांच करना आवश्यक है। दोषपूर्ण काटने के उपकरण का उपयोग न करें।
वर्कपीस को बन्धन के साधनों को उसके आकार और आकार के आधार पर चुना जाता है। लंबी वर्कपीस (छवि 3, ए) को बन्धन के लिए, आगे और पीछे के केंद्रों का उपयोग किया जाता है। सामने का केंद्र 2 एक पतला टांग के साथ तीन-पंख वाले पट्टा के रूप में बनाया गया है, जिसके साथ इसे धुरी के पतला छेद में डाला जाता है। पीछे के केंद्र 4 में एक शंक्वाकार और नुकीला हिस्सा होता है और इसे क्विल में तय किया जाता है। 5 टेलस्टॉक 6. घर्षण को कम करने और वर्कपीस को बन्धन की विश्वसनीयता बढ़ाने के लिए, रियर सेंटर को असर पर रखा गया है, जो वर्कपीस के साथ इसके रोटेशन को सुनिश्चित करता है।

चावल। 3. वर्कपीस को खराद में बन्धन: ए - केंद्रों में, बी - चक में, सी - फेसप्लेट पर; 1 - स्पिंडल, 2 - फ्रंट सेंटर, 3 - वर्कपीस, 4 - रियर सेंटर, 5 - क्विल, 6 - टेलस्टॉक, 7 - चक, 8 - प्लान
संसाधित किए जा रहे वर्कपीस की लंबाई के आधार पर, टेलस्टॉक को बेड के गाइड के साथ ले जाया जाता है और पूर्व निर्धारित स्थिति में तय किया जाता है। वर्कपीस को हेडस्टॉक से बाहर धकेल कर तब तक तय किया जाता है जब तक कि केंद्र वर्कपीस के सिरों में एम्बेडेड नहीं हो जाते हैं और रोटेशन के दौरान इसे सुरक्षित रूप से पकड़ लेंगे। टेपर भागों को चालू करने के लिए, टेलस्टॉक आवास को एक समायोजन पेंच के साथ ट्रांसवर्सली स्थानांतरित किया जाना चाहिए और एक लॉकिंग डिवाइस के साथ तय किया जाना चाहिए। चक को छोटी वर्कपीस (छवि 3, बी) को बन्धन के लिए डिज़ाइन किया गया है। चक 7 में एक धागा होता है जिसके माध्यम से इसे स्पिंडल पर खराब कर दिया जाता है। वर्कपीस को चक के छेद में इसके सिरे को मजबूती से फिट करके चक में तय किया जाता है। स्लाइडिंग जॉ के साथ कोलेट चक और चक का भी उपयोग किया जाता है।
छोटी लंबाई के वर्कपीस को क्लैंप करने के लिए और बड़ा व्यासस्पिंडल पर खराब किए गए फेसप्लेट 8 (चित्र 3, सी) के रूप में कार्य करें। वर्कपीस को फेसप्लेट पर शिकंजा या बोल्ट 9 के साथ तय किया गया है।
हैंडपीस को फ्रेम पर स्थापित किया जाता है ताकि इसका काम करने वाला किनारा केंद्रों के स्तर पर हो और संसाधित किए जा रहे वर्कपीस के जेनरेटर के पास हो, लेकिन इसे छूता नहीं है। जैसे-जैसे व्यास घटता है और लंबी वर्कपीस को संसाधित करते समय, हैंडपीस को क्रमिक रूप से बेड गाइड के साथ एक नई स्थिति में पुनर्व्यवस्थित किया जाता है। बिस्तर के पीछे की तरफ आकार के उत्पादों को संसाधित करते समय, ब्रैकेट पर एक प्रतिलिपि शासक तय किया जाता है, जिसका आकार तैयार भाग के आकार के समान होता है। जब फ़ीड को चालू किया जाता है, तो कैलीपर घुमावदार पथ पर चलता है और कटर भाग के दिए गए आकार को पुन: पेश करता है।
वर्कपीस के व्यास और उसकी ताकत के आधार पर स्पिंडल गति का चयन किया जाता है। बड़े व्यास के लिए, न्यूनतम धुरी गति निर्धारित की जानी चाहिए। 400 मिमी के व्यास के साथ फेसप्लेट स्थापित करते समय, धुरी की गति 800 आरपीएम से अधिक नहीं होनी चाहिए। गियर शिफ्ट लीवर द्वारा या मल्टी-स्पीड इलेक्ट्रिक मोटर की घूर्णी गति को बदलकर घूर्णी गति को कम किया जाता है। लकड़ी के लिए काटने की गति नरम चट्टानें 10 ... 12 मीटर / सेकंड होना चाहिए, ठोस - 0.5 ... 3 मीटर / सेकंड।
धुरी की एक क्रांति के लिए अनुदैर्ध्य फ़ीड होना चाहिए: 1.6 ... 2 मिमी, परिष्करण के लिए - 0.8 मिमी से अधिक नहीं। सतह खुरदरापन के लिए जितनी अधिक आवश्यकताएं होंगी, अनुदैर्ध्य फ़ीड उतनी ही कम होनी चाहिए। प्रति स्पिंडल क्रांति क्रॉस फीड 1.2 मिमी से अधिक नहीं होनी चाहिए। मशीन शुरू करने से पहले, सुनिश्चित करें कि विश्वसनीय बन्धनरिक्त स्थान और एक बाड़ स्थापित करें।
भाग को खुरदरा करने के बाद, कटर को बदल दिया जाता है और कम फ़ीड पर बारीक मोड़ दिया जाता है। इस मामले में चिप्स यथासंभव निरंतर और समान मोटाई के होने चाहिए।
प्रसंस्करण के दौरान, भाग के आकार को समय-समय पर एक टेम्पलेट या गेज द्वारा नियंत्रित किया जाता है। कैलिबर का उपयोग करते समय or मापन यंत्रएक पैमाने के साथ, मशीन को बंद कर दिया जाता है और भाग पूरी तरह से बंद होने के बाद ही इसे मापा जाता है।
समायोजन समाप्त करने के बाद, भाग का एक परीक्षण प्रसंस्करण किया जाता है और इसके आयामों को एक कैलिबर या मापने वाले उपकरण के साथ एक पैमाने के साथ नियंत्रित किया जाता है।