modes de coupe. Les avances lors du tournage grossier sont devenues des fraises en carbure sans arête de coupe supplémentaire. Grande encyclopédie du pétrole et du gaz
Le tournage peut être réalisé avec une avance mécanique, puisque la génératrice du cône usiné est parallèle à la direction de l'avance longitudinale de la fraise.
Le cycle technologique de copie est utilisé pour le traitement de surfaces étagées, coniques et courbes qui nécessitent une avance longitudinale de la fraise. À la fin du traitement de surface, la fraise est retirée de la pièce et l'étrier revient à sa position d'origine.
Index général d'une machine à fileter. |
Le support longitudinal 7, monté sur les guides du lit, se déplace le long de ceux-ci et assure une alimentation longitudinale de la fraise. Le chariot transversal fournit une alimentation transversale à la fraise. Le support rotatif supérieur peut être réglé à n'importe quel angle par rapport à l'axe de rotation de la pièce, ce qui est nécessaire lors de l'usinage de surfaces coniques de pièces.
Schéma de tournage d'une pièce en forme. |
Après le déplacement transversal du corps de la poupée mobile d'une quantité h jusqu'à 15 - 20 mm), la génératrice du cône usiné est parallèle à la direction de l'avance longitudinale de la fraise, de sorte que le tournage peut être effectué avec une avance mécanique .
Schéma de cuisson tournant. |
Après le déplacement transversal du corps de la contrepointe de la valeur h (jusqu'à 15 - 20 mm), la génératrice du cône usiné est parallèle à la direction de l'avance longitudinale de la fraise, de sorte que le tournage peut être effectué avec mécanique nourrir.
Pour le filetage sur un tour, il est nécessaire que la vitesse de rotation de la broche soit strictement liée à la vitesse de déplacement de l'étrier, car l'avance longitudinale de la fraise en un tour de broche doit correspondre exactement au pas du filet être coupé.
L'épaisseur de la couche de métal découpée affecte grandement l'ampleur des irrégularités. L'épaisseur de la couche découpée est déterminée par l'avance longitudinale de la fraise. S'il n'y avait pas de déformations élasto-plastiques pendant le processus de coupe, la hauteur des irrégularités pourrait facilement être calculée à partir de Forme géométrique le haut de la fraise.
Une minute après le début du travail, désactivez l'avance longitudinale de la fraise, éloignez la fraise de la pièce et tournez rapidement le porte-outil de 90 ou 180 jusqu'à ce que la pointe de la fraise touche la pointe indicatrice.
Pour les diamants dans un cadre, les avances longitudinales doivent être inférieures à celles des crayons, et encore moins pour les diamants taillés. Par exemple, lors de l'habillage de meules à filetage multi-filetage avec des fraises diamantées, l'avance longitudinale de la fraise ne doit pas dépasser 0,05 m / min. À la fin du processus de dressage, il est recommandé d'effectuer une ou deux passes sans avance transversale, ce qui réduit la quantité d'avance longitudinale.
Le dispositif est conçu pour percer des trous coniques avec un angle constant a. L'appareil est fixé sur le support radial du plastron de la machine. En faisant tourner la vis 3, la fraise est alimentée longitudinalement. A la deuxième extrémité de la vis, un astérisque 1 est installé, qui, sautant avec sa dent à chaque tour de l'étrier sur la butée de réglage, effectue une avance longitudinale automatique.
Afin de traiter la pièce en coupant et d'obtenir ainsi les surfaces usinées d'une pièce particulière, la pièce et l'application outil de coupe devrait faire certains mouvements. Ces mouvements sont divisés en mouvements principaux (servant à la mise en œuvre du processus de coupe) et auxiliaires (servant à préparer le processus de coupe et à terminer l'opération). Il existe deux mouvements principaux :
- mouvement de coupe (ou mouvement principal);
- mouvement d'alimentation.
Lors du traitement sur un tour, le mouvement de coupe - rotationnel - est effectué par la pièce, qui est fixée d'une manière ou d'une autre à la broche de la machine, et le mouvement d'avance - translationnel - reçoit un outil de coupe (fraise) fixé de manière rigide dans l'outil titulaire. Le mouvement permet le processus de coupe (formation de copeaux), le mouvement de l'avance permet d'effectuer ce processus (usinage) sur toute la longueur de la pièce (Fig. Partie 16).
Profondeur de coupe (t)- la valeur de la couche découpée en une passe, mesurée dans la direction perpendiculaire à la surface usinée. La profondeur de passe est toujours perpendiculaire au sens d'avance (voir aussi fig. 11-14). En tournage longitudinal extérieur (Fig. 16), il s'agit d'une demi-différence entre le diamètre de la pièce et le diamètre de la surface usinée obtenue après une passe :
Vitesse de coupeυ - quantité de mouvement de point en pointe par rapport à la surface par unité de temps lors de la mise en oeuvre du mouvement de coupe*.
En tournage, lorsque la pièce tourne à une fréquence de n tr/min, la vitesse de coupe aux points MK du tranchant sera une valeur variable. Vitesse maximale:
où D est le plus grand diamètre de surface en mm.
* La vitesse de coupe est fonction de la vitesse de rotation de la pièce et de la vitesse de déplacement (avance) de l'outil.
Si la vitesse est connue, il est facile de déterminer la fréquence de rotation :
Avec le tournage longitudinal, la vitesse de coupe a une valeur constante pendant tout le temps de coupe (si le diamètre de la pièce sur toute sa longueur est le même et que la vitesse de rotation est inchangée). Lors de la coupe de l'extrémité, lorsque la fraise se déplace de la périphérie de la pièce vers le centre, la vitesse de coupe à vitesse constante est variable. Elle a valeur la plus élevéeà la périphérie et est égal à zéro au centre (Fig. 17). La vitesse de coupe sera également variable le long de la surface usinée pendant le tronçonnage (voir Fig. 14). Toutefois, dans ces cas, considérez vitesse de pointe Coupe.
Soumission(plus précisément, vitesse d'avance) - la quantité de mouvement de l'arête de coupe par rapport à la surface usinée par unité de temps dans la direction du mouvement d'avance. En tournant, il peut être avance longitudinale lorsque la fraise se déplace dans une direction parallèle à l'axe de la pièce (voir Fig. 16); alimentation croisée lorsque la fraise se déplace dans une direction perpendiculaire à l'axe de la pièce (voir Fig. 17), et alimentation oblique- à un angle par rapport à l'axe de la pièce (par exemple, lors du tournage d'une surface conique).
Distinguer la hauteur en un tour pièce, c'est-à-dire la quantité de mouvement relatif de la fraise pendant un tour de la pièce (de la position I, la fraise est passée à la position II, Fig. 16), et alimentation minute, soit la valeur du mouvement relatif de la fraise pendant 1 min. L'avance minute est indiquée par S m (mm / min) et l'avance par tour - s (mm / tour). Il existe la relation suivante entre eux.
à la maison
section trois
Principes fondamentaux de la théorie de la coupe des métaux.
Choix des conditions de coupe
Chapitre VI
Principes fondamentaux de la théorie de la coupe des métaux
Les fondateurs de la théorie de la coupe des métaux étaient les remarquables scientifiques russes I. A. Time (1838-1920), K. A. Zvorykin (1861-1928), Ya. G. Usachev (1873-1941) et d'autres. Les travaux de ces scientifiques, qui ont reçu reconnaissance mondiale n'ont pas encore perdu leur valeur. Cependant, dans les conditions de la Russie tsariste arriérée, tous ces travaux n'ont pas trouvé application pratique parce que l'industrie était sous-développée.
La science de la coupe des métaux n'a pris une grande ampleur qu'après la Grande Révolution socialiste d'Octobre, en particulier pendant les plans quinquennaux soviétiques, lorsque la science a été mise au service de l'industrie socialiste.
Les scientifiques soviétiques V. D. Kuznetsov, V. A. Krivoukhov, I. M. Bezprozvanny, A. M. Rozenberg, M. N. Larin, P. P. Trudov, M. I. Klushin et d'autres ont créé une école nationale de coupe des métaux, trait distinctif qui est l'étroite collaboration de la science avec la production, des scientifiques avec les innovateurs de la production.
Un rôle important dans le développement de la science de la coupe des métaux a été joué par le mouvement des innovateurs dans la production. Afin d'augmenter la productivité du travail, les responsables de la production ont commencé à chercher de nouvelles façons d'améliorer les conditions de coupe : ils ont créé une nouvelle géométrie d'outil de coupe, changé les conditions de coupe, maîtrisé de nouvelles matériaux de coupe. Chaque lieu de travail Turner-innovator est devenu comme un petit laboratoire pour l'étude du processus de coupe.
Un large échange d'expériences, possible uniquement dans les conditions d'une économie socialiste, et une coopération étroite entre les principaux travailleurs de la production et de la science ont assuré le développement rapide de la science de la coupe des métaux.
1. Travail du coupeur
Wedge et son travail. La partie travaillante de tout outil de coupe est coin(Fig. 44). Sous l'action de la force appliquée, la pointe du coin coupe le métal.
Plus le coin est tranchant, c'est-à-dire plus l'angle formé par ses côtés est petit, moins il faut de force pour le couper dans le métal. L'angle formé par les côtés du coin est appelé angle conique et est noté par la lettre grecque β ( bêta). Par conséquent, plus l'angle de conicité β est petit, plus le coin pénètre facilement dans le métal et, à l'inverse, plus l'angle de conicité β est grand, plus la force doit être appliquée pour couper le métal. Lors de l'attribution de l'angle de conicité, il est nécessaire de prendre en compte les propriétés mécaniques du métal traité. Si vous coupez du métal dur avec un couteau ayant un petit angle d'affûtage β, la lame fine ne résistera pas et s'effritera ou se cassera. Par conséquent, en fonction de la dureté du métal traité, un angle d'affûtage de coin approprié est attribué.
La couche de métal en cours de traitement, située directement devant la fraise, est continuellement comprimée par sa surface avant. Lorsque la force de la fraise dépasse les forces d'adhérence des particules métalliques, l'élément comprimé est cisaillé et déplacé par la surface avant du coin vers le haut. La fraise, avançant sous l'action de la force appliquée, continuera à se comprimer, à s'écailler et à se déplacer éléments individuelsà partir de laquelle les puces sont formées.
Mouvements de base en virage. Lors de l'usinage sur des tours, la pièce tourne et la fraise reçoit un mouvement dans le sens longitudinal ou transversal. La rotation de la pièce est appelée mouvement principal, et le mouvement de la fraise par rapport à la pièce - mouvement d'alimentation(Fig. 45).
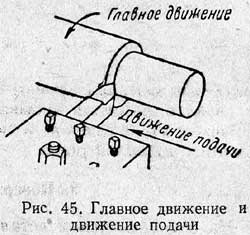
2. Les pièces et éléments principaux de l'outil de tournage
Le couteau se compose de deux parties principales: la tête et le corps (tige) (Fig. 46). Tête est la partie de travail (coupe) du couteau ; corps sert à fixer la fraise dans le porte-outil.

La tête se compose des éléments suivants : face avant, le long duquel les copeaux se détachent, et surfaces arrière face à la pièce. L'une des surfaces arrière faisant face à la surface de coupe est appelée principale; l'autre, tournée vers la surface traitée, - auxiliaire.
Les arêtes de coupe sont obtenues à partir de l'intersection des surfaces avant et arrière. Distinguer domicile et tranchant auxiliaire. La majeure partie du travail de coupe est effectuée par le tranchant principal.
L'intersection des arêtes de coupe principales et secondaires est appelée pointe incisive.
3. Traitement de surface
Trois types de surface sont distingués sur la pièce (Fig. 47) : surface usinée, usinée et coupante.

traité surface est la surface de la pièce dont les copeaux sont retirés.
Surface traitée appelée la surface de la pièce obtenue après enlèvement des copeaux.
surface de coupe appelée la surface formée sur la pièce par le tranchant principal de la fraise.
Il faut également faire la distinction entre le plan de coupe et le plan de base.
plan de coupe appelé le plan tangent à la surface de coupe et passant par le tranchant de la fraise.
Avion principal appelé plan parallèle aux avances longitudinale et transversale de la fraise. Pour les tours, elle coïncide avec la surface d'appui horizontale du porte-outil.
4. Angles de coupe et leur but
Les angles de la partie travaillante de la fraise affectent grandement le déroulement du processus de coupe.
En choisissant les bons angles de la fraise, vous pouvez augmenter considérablement la durée de son fonctionnement continu jusqu'à l'émoussement (durabilité) et le processus par unité de temps (par minute ou par heure) grande quantité des détails.
La force de coupe agissant sur la fraise, la puissance requise, la qualité de la surface usinée... dépendent également du choix des angles de la fraise, c'est pourquoi chaque tourneur doit bien étudier le but de chacun des angles d'affûtage de la fraise et pouvoir sélectionner correctement leur valeur la plus avantageuse.
Les angles de la fraise (Fig. 48) peuvent être divisés en angles principaux, les angles de la fraise dans le plan et l'angle d'inclinaison du tranchant principal.
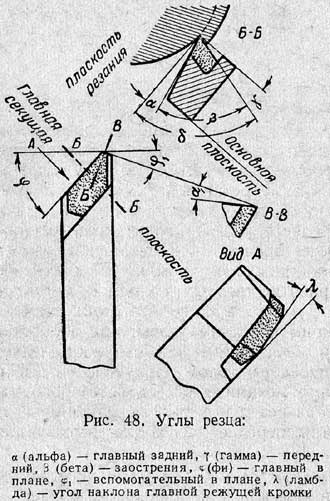
Les principaux angles comprennent : l'angle arrière, l'angle avant et l'angle de cône ; les angles de la fraise dans le plan incluent le principal et l'auxiliaire.
Les angles principaux de la fraise doivent être mesurés dans le plan de coupe principal, qui est perpendiculaire au plan de coupe et au plan principal.
La partie travaillante de la fraise est un coin (ombré sur la Fig. 48), dont la forme est caractérisée par l'angle entre les surfaces avant et arrière principale de la fraise. Ce coin s'appelle angle conique et est désigné par la lettre grecque β (bêta).
angle du dos α ( alpha) est l'angle entre le flanc principal et le plan de coupe.
L'angle de dégagement α sert à réduire le frottement entre la surface arrière de la fraise et la pièce à usiner. En réduisant les frottements, on diminue ainsi l'échauffement de la fraise qui, de ce fait, s'use moins. Cependant, si l'angle de relief est fortement augmenté, l'incisive est affaiblie et rapidement détruite.
angle avant γ ( gamma) est l'angle entre la surface avant de la fraise et le plan perpendiculaire au plan de coupe, passant par l'arête de coupe principale.
L'angle de coupe γ joue un rôle important dans le processus de formation des copeaux. Avec une augmentation de l'angle de coupe, il est plus facile de couper la fraise dans le métal, la déformation de la couche coupée est réduite, le flux de copeaux est amélioré, la force de coupe et la consommation d'énergie sont réduites, et la qualité de la surface usinée est amélioré. D'autre part, une augmentation excessive de l'angle de coupe conduit à un affaiblissement du tranchant et à une diminution de sa résistance, à une augmentation de l'usure de la fraise due à l'écaillage du tranchant, et à une détérioration de l'évacuation de la chaleur . Par conséquent, lors du traitement de métaux durs et cassants, afin d'augmenter la résistance de l'outil, ainsi que sa durabilité, des fraises avec un angle de coupe plus petit doivent être utilisées; lors de l'usinage de métaux tendres et ductiles, des fraises à grand angle de coupe doivent être utilisées pour faciliter l'évacuation des copeaux. En pratique, le choix de l'angle avant dépend, outre propriétés mécaniques matériau en cours de traitement, du matériau de la fraise et de la forme de la surface avant. Les angles de coupe recommandés pour les fraises au carbure sont indiqués dans le tableau. une.
Angles de plan. Angle d'attaque φ ( Fi) est appelé l'angle entre l'arête de coupe principale et la direction d'avance.
L'angle φ est généralement choisi dans la plage de 30 à 90° en fonction du type de traitement, du type de fraise, de la rigidité de la pièce et de la fraise et de la méthode de leur fixation. Lors du traitement de la majorité des métaux avec des fraises à éplucher traversantes, il est possible de prendre l'angle φ = 45° ; lors du traitement mince parties longues dans les centres, il est nécessaire d'utiliser des fraises avec un angle d'attaque de 60, 75 ou même 90 ° pour que les pièces ne se plient pas ou ne tremblent pas.
Angle auxiliaire en planφ 1 est l'angle entre l'arête de coupe secondaire et la direction d'avance.

Angle λ ( lambda) inclinaison du tranchant principal(Fig. 49) est l'angle entre le tranchant principal et la ligne tracée à travers le haut de la fraise parallèle au plan principal.
Tableau 1
Angles de coupe et de dégagement recommandés pour les outils en carbure
Noter. Les propriétés mécaniques des métaux sont déterminées sur des machines et des instruments spéciaux, et chaque propriété reçoit sa propre désignation. La désignation σ b donnée dans ce tableau et les suivants exprime la résistance à la traction du métal ; la valeur de cette limite est mesurée en kg/mm2. Les lettres HB indiquent la dureté du métal, qui est déterminée sur l'appareil Brinell en pressant une bille d'acier trempé dans la surface du métal. La valeur de la dureté est mesurée en kg / mm 2.
Fraises dont le sommet est le point le plus bas de l'arête de coupe, c'est-à-dire l'angle λ positif(Fig. 49, c), sont plus durables et résistants ; avec de telles fraises, il est bon de traiter les métaux durs, ainsi que les surfaces intermittentes qui créent une charge d'impact. Lors du traitement de telles surfaces fraises au carbure l'angle d'inclinaison du tranchant principal est ajusté à 20-30°. Fraises dont le sommet est le point le plus haut de l'arête de coupe, c'est-à-dire l'angle λ négatif(Fig. 49, a), il est recommandé d'utiliser pour le traitement de pièces en métaux mous.
5. Matériaux utilisés pour la fabrication des incisives
Lorsque vous travaillez sur les tranchants de la fraise, une pression élevée se produit, ainsi qu'une température élevée (600-800 ° et plus). Le frottement de la surface arrière de la fraise sur la surface de coupe et des copeaux sur la surface avant de la fraise provoque une usure plus ou moins rapide de ses surfaces de travail. En raison de l'usure, la forme de la partie coupante change et la fraise après un certain temps devient inutilisable pour d'autres travaux ; un tel couteau doit être retiré de la machine et réaffûté. Pour augmenter la durée de vie de l'outil sans réaffûtage, il faut que son matériau résiste bien à l'usure à haute température. De plus, le matériau de la fraise doit être suffisamment solide pour résister hautes pressions survenant lors de la coupe. Par conséquent, les exigences de base suivantes sont imposées au matériau des fraises - dureté à haute température, bonne résistance à l'usure et résistance.
Actuellement, il existe de nombreux aciers à outils et alliages qui répondent à ces exigences. Il s'agit notamment des aciers à outils au carbone, des aciers rapides, des alliages durs et matériaux céramiques.
Acier à outils au carbone. Pour la fabrication d'outils de coupe, on utilise de l'acier à teneur en carbone de 0,9 à 1,4 %. Après trempe et revenu, l'outil de coupe réalisé dans cet acier acquiert une dureté élevée. Cependant, si pendant le processus de coupe, la température du tranchant atteint 200-250 °, la dureté de l'acier chute fortement.
Pour cette raison, l'acier à outils au carbone est actuellement d'une utilisation limitée : il est utilisé pour fabriquer des outils de coupe qui fonctionnent à une vitesse de coupe relativement faible lorsque la température dans la zone de coupe atteint une faible valeur. Ces outils comprennent : les matrices, les alésoirs, les tarauds, les limes, les grattoirs, etc. Les fraises ne sont actuellement pas fabriquées à partir d'acier à outils au carbone.
Aciers rapides. Les aciers rapides contiennent un grand nombre deéléments spéciaux dits d'alliage - tungstène, chrome, vanadium et cobalt, qui confèrent à l'acier des propriétés de coupe élevées - la capacité de maintenir la dureté et la résistance à l'usure lorsqu'ils sont chauffés pendant la coupe à 600-700 °. Les fraises HSS permettent des vitesses de coupe 2 à 3 fois plus élevées que les fraises en carbone.
À l'heure actuelle, les nuances d'acier rapide suivantes (GOST 9373-60) sont produites en URSS: R18, R9, R9F5, R14F14, R18F2, R9K5, R9KYU, R10K5F5 et R18K5F2.
Les fraises entièrement en acier rapide sont chères, par conséquent, afin d'économiser de l'acier rapide, les fraises à plaques soudées sont principalement utilisées.
Alliages durs. Les alliages de carbure se caractérisent par une dureté très élevée et une bonne résistance à l'usure.
Les alliages durs sont fabriqués sous forme de plaques à partir de poudres de tungstène et de titane associées à du carbone. La combinaison de carbone et de tungstène est appelée le carbure de tungstène, et avec le titane, le carbure de titane. Le cobalt est ajouté comme liant. Ce mélange pulvérulent est pressé sous haute pression pour obtenir des plaquettes qui sont ensuite frittées à une température d'environ 1500°. Les plaques finies ne nécessitent aucun traitement thermique. La plaque est soudée avec du cuivre au porte-couteau en Acier Carbone ou fixé à celui-ci à l'aide de réglages et de vis (fixation mécanique des plaques).
Le principal avantage des alliages durs réside dans le fait qu'ils résistent bien à l'abrasion due aux chutes de copeaux et à la pièce et ne perdent pas leurs propriétés de coupe même lorsqu'ils sont chauffés à 900-1000 °. Grâce à ces propriétés, les fraises équipées de plaquettes en carbure conviennent à l'usinage des plus métaux solides(aciers durs, y compris trempés) et matériaux non métalliques (verre, porcelaine, plastiques) à des vitesses de coupe 4 à 6 fois supérieures aux vitesses de coupe autorisées par les coupeuses à grande vitesse.
L'inconvénient des alliages durs est une fragilité accrue.
Actuellement, deux groupes d'alliages durs sont produits en URSS. Les principaux sont - tungstène(VK2, VKZ, VK4, VK6M, VK6, VK8 et VK8M) et titane-tungstène(T30K4, T15K6, T14K8, T5K10). Chacun de ces groupes a un périmètre spécifique (tableau 2).
Tous les alliages de tungstène sont destinés au traitement de la fonte, des métaux non ferreux et leurs alliages, des aciers trempés, des aciers inoxydables et des matériaux non métalliques (ébonite, porcelaine, verre, etc.). Pour le traitement des aciers, des alliages durs du groupe titane-tungstène sont utilisés.
Matériaux céramiques. Récemment, les métallurgistes soviétiques ont créé des matériaux bon marché avec des propriétés de coupe élevées, qui remplacent dans de nombreux cas les alliages durs. Ce sont des matériaux céramiques thermocorindon), réalisé sous forme de plaques couleur blanche, rappelant le marbre, qui, comme les alliages durs, sont soit soudés aux porte-couteaux, soit fixés mécaniquement à ceux-ci. Ces plaques ne contiennent pas d'éléments aussi chers et rares que le tungstène, le titane, etc. Dans le même temps, les plaques en céramique ont une dureté plus élevée que les alliages durs et conservent leur dureté lorsqu'elles sont chauffées jusqu'à 1200 °, ce qui permet de couper des métaux avec eux avec vitesses élevées Coupe.
L'inconvénient des plaques en céramique est leur viscosité insuffisante. Les fraises équipées d'inserts en céramique peuvent être utilisées pour la finition ou la semi-finition de la fonte, du bronze, des alliages d'aluminium et des aciers doux.
6. Affûtage et finition des fraises
Dans les usines, l'affûtage des couteaux est généralement effectué de manière centralisée à Rectifieuses travailleurs spéciaux. Mais le tourneur lui-même doit pouvoir affûter et finir les fraises.
Tableau 2
Propriétés et but de certaines nuances d'alliages durs

L'affûtage et la finition des fraises à grande vitesse sont effectués dans le respect des règles suivantes:
1. La meule ne doit pas battre, sa surface doit être plane ; si la surface de travail du cercle s'est développée, elle doit être corrigée.
2. Pendant l'affûtage, vous devez utiliser une pièce à main et ne pas tenir la fraise sur le poids. La pièce à main doit être installée aussi près que possible de la meule, à l'angle requis et offrir un support fiable à la fraise (Fig. 50, a-d).
3. La fraise à affûter doit être déplacée le long de la surface de travail du cercle, sinon elle s'usera de manière inégale.
4. Afin de ne pas surchauffer le couteau et d'éviter ainsi l'apparition de fissures, n'appuyez pas fortement le couteau sur le cercle.
5. L'affûtage doit être effectué avec un refroidissement continu et abondant de la fraise avec de l'eau. Le refroidissement par goutte à goutte, ainsi que l'immersion périodique d'un couteau hautement chauffé dans l'eau, ne sont pas autorisés. Si le refroidissement continu n'est pas possible, il est préférable de passer à l'affûtage à sec.
6. L'affûtage des fraises en acier rapide doit être effectué à l'aide de meules en électrocorindon de dureté moyenne et de granulométrie 25-16.
L'ordre d'affûtage des couteaux est défini comme suit. Tout d'abord, la surface arrière principale est affûtée (Fig. 50, a). Ensuite, la surface arrière auxiliaire (Fig. 50, b), puis la surface avant (Fig. 50, c) et enfin le rayon du sommet (Fig. 50, d).
7. Il est strictement interdit d'affûter les couteaux sur les machines dont le capot de protection a été retiré.
8. Assurez-vous de porter des lunettes de sécurité lors de l'affûtage.
Après affûtage de la fraise, de petites encoches, bavures et risques subsistent sur ses tranchants. Ils sont éliminés par finition sur des machines de finition spéciales. La finition est également effectuée manuellement à l'aide d'une pierre à aiguiser à grain fin imbibée d'huile minérale. D'abord, avec de légers mouvements de la pierre de touche, les surfaces arrière sont ajustées, puis l'avant et le rayon du dessus.
Affûtage et finition de fraises équipées de plaquettes en carbure. L'affûtage des fraises avec des plaques d'alliages durs est effectué sur des rectifieuses avec des cercles de carbure de silicium vert. L'affûtage est effectué à la fois manuellement (Fig. 50, a-d) et avec la fixation des incisives dans les porte-outils. L'ordre d'affûtage de ces couteaux est le même que pour les couteaux en acier rapide, c'est-à-dire que le couteau est d'abord affûté le long du dos principal (Fig. 50, a), puis le long des surfaces arrière auxiliaires (Fig. 50, b ), puis le long de la face avant (Fig. 50, c) et, enfin, arrondir le sommet de l'incisive (Fig. 50, d).
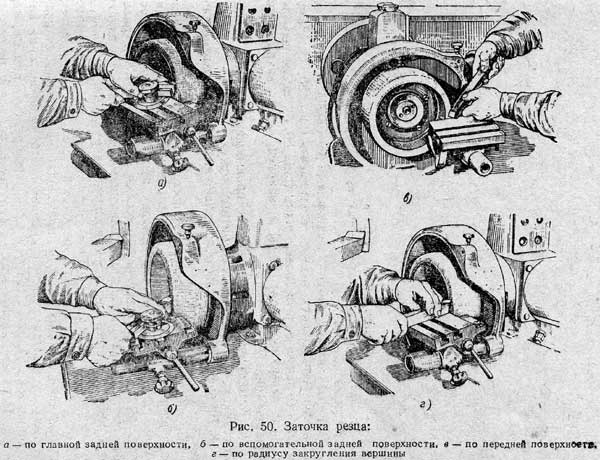
L'affûtage préliminaire est effectué avec des meules vertes en carbure de silicium avec un grain de 50-40 et l'affûtage final avec un grain de 25-16.
La fraise ne doit pas être fortement appuyée contre la surface de travail du cercle afin d'éviter la surchauffe et la fissuration de la plaque en alliage dur. De plus, il doit être constamment déplacé par rapport au cercle ; ceci est nécessaire pour une usure uniforme du cercle.
L'affûtage peut être effectué à la fois à sec et avec un refroidissement abondant de la fraise avec de l'eau.
Après avoir affûté une fraise au carbure, il est impératif de finir sa surface. La finition se fait manuellement ou sur une machine de finition. La finition manuelle est effectuée à l'aide d'un tour en fonte ou en cuivre, dont la surface de travail est frottée avec une pâte spéciale ou une poudre de carbure de bore mélangée à de l'huile de machine ou du kérosène est appliquée sur la surface en une couche uniforme. La finition est effectuée sur une largeur de 2 à 4 mm à partir du bord de coupe.
Finition plus productive sur une machine de finition spéciale utilisant un disque en fonte d'un diamètre de 250-300 mm, tournant à une vitesse de 1,5-2 m/s; une pâte ou une poudre de carbure de bore mélangée à de l'huile de machine ou du kérosène est appliquée à la surface de ce disque.
7. Formation de copeaux
Types de copeaux. La puce détachée sous l'action de la pression de la fraise change considérablement de forme ou, comme on dit, se déforme : elle raccourcit en longueur et augmente en épaisseur. Ce phénomène a été découvert pour la première fois par le Prof. I. A. Temps et nommé retrait des copeaux.
L'aspect du copeau dépend des propriétés mécaniques du métal et des conditions dans lesquelles se produit la coupe. Si des métaux visqueux sont traités (plomb, étain, cuivre, acier doux, aluminium, etc.), les éléments individuels des puces, adhérant étroitement les uns aux autres, forment une puce continue qui s'enroule en une bande (Fig. 51, un ). Un tel brin est appelé drain. Lors du traitement de métaux moins visqueux, tels que l'acier dur, des copeaux sont formés à partir d'éléments individuels (Fig. 51, b), faiblement connectés les uns aux autres. Un tel brin est appelé copeaux d'écaillage.
Si le métal usiné est fragile, comme la fonte ou le bronze, les éléments individuels des copeaux se cassent et se séparent de la pièce et les uns des autres (Fig. 51, c). Une telle puce, composée d'échelles individuelles forme irrégulière, est appelé jetons cassés.
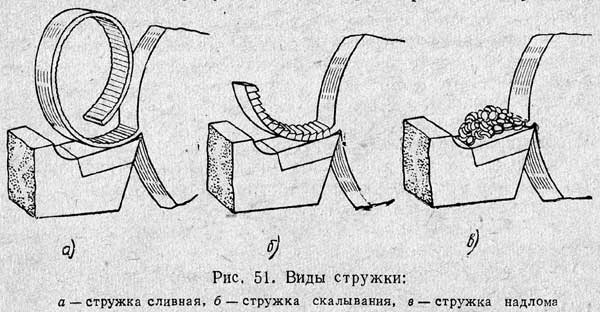
Les types de copeaux considérés ne restent pas constants, ils peuvent changer avec l'évolution des conditions de coupe. Plus le métal traité est tendre et plus l'épaisseur du copeau et l'angle de coupe sont petits, plus la forme du copeau se rapproche du drain. La même chose sera observée lorsque la vitesse de coupe est augmentée et qu'un refroidissement est appliqué. Avec une diminution de la vitesse de coupe, au lieu d'un copeau de drainage, des copeaux de déchiquetage sont obtenus.
Excroissance. Si vous examinez la surface avant de la fraise qui a été utilisée pour la coupe, vous pouvez parfois trouver au bord de la coupe un petit morceau de métal soudé à la fraise sous haute température et pression. C'est ce qu'on appelle excroissance(Fig. 52). Il apparaît dans certaines conditions de coupe des métaux ductiles, mais n'est pas observé lors du traitement des métaux fragiles. La dureté de l'accumulation est 2,5 à 3 fois supérieure à la dureté du métal traité; grâce à cela, la croissance elle-même a la capacité de couper le métal à partir duquel elle a été formée.
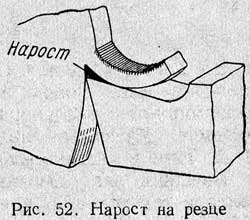
Le rôle positif de l'accumulation est qu'elle recouvre la lame de coupe, la protégeant de l'usure due aux copeaux descendants et à l'action de la chaleur, ce qui augmente quelque peu la durabilité de la fraise. La présence d'une accumulation est utile lors du pelage, car la lame de coupe chauffe moins et son usure est réduite. Cependant, avec la formation d'accumulations, la précision et la propreté de la surface usinée se détériorent, car l'accumulation déforme la forme de la lame. Par conséquent, la formation d'accumulation est défavorable pour les travaux de finition.
8. Le concept des éléments du mode de coupe
Afin d'effectuer un traitement plus efficace dans chaque cas individuel, le tourneur doit connaître les éléments de base du mode de coupe; ces éléments sont la profondeur de coupe, l'avance et la vitesse de coupe.
Profondeur de coupe appelée la distance entre les surfaces usinées et usinées, mesurée perpendiculairement à ces dernières. La profondeur de coupe est indiquée par la lettre t et est mesurée en millimètres (Fig. 53).
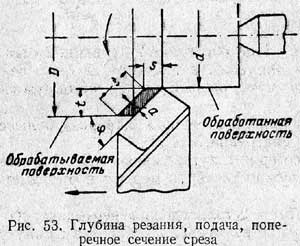
Lors du tournage d'une pièce sur un tour, la surépaisseur d'usinage est coupée en une ou plusieurs passes.
Pour déterminer la profondeur de coupe t, il faut mesurer le diamètre de la pièce avant et après le passage de la fraise, la moitié de la différence de diamètres donnera la profondeur de coupe, autrement dit,
où D est le diamètre de la pièce en mm avant le passage de la fraise ; d est le diamètre de la pièce en mm après passage de la fraise. Le mouvement de la fraise en un tour de la pièce (Fig. 53) est appelé dépôt. L'avance est désignée par la lettre s et est mesurée en millimètres par tour de la pièce ; par souci de brièveté, il est d'usage d'écrire mm/tour. Selon la direction dans laquelle la fraise se déplace par rapport aux guides du cadre, il y a :
un) avance longitudinale- le long des guides de lit ;
b) alimentation croisée- perpendiculaire aux guides du lit ;
dans) alimentation oblique- à un angle par rapport aux guides du lit (par exemple, lors de la rotation d'une surface conique).
Zone de coupe en coupe désignée par la lettre f (eff) et définie comme le produit de la profondeur de passe par l'avance (voir Fig. 53) :
Outre la profondeur de coupe et d'alimentation, ils distinguent également la largeur et l'épaisseur de la couche de coupe (Fig. 53).
Largeur de la couche de coupe, ou alors largeur de copeau, - la distance entre les surfaces usinées et usinées, mesurée le long de la surface de coupe. Il est mesuré en millimètres et est désigné par la lettre b (be).
Épaisseur de coupe, ou alors épaisseur de copeau, est la distance entre deux positions successives de l'arête de coupe dans un tour de pièce, mesurée perpendiculairement à la largeur du copeau. L'épaisseur des copeaux est mesurée en millimètres et est désignée par la lettre a.
Avec la même avance et la même profondeur de coupe, lorsque l'angle principal φ diminue, l'épaisseur du copeau diminue et sa largeur augmente. Cela améliore la dissipation de la chaleur de l'arête de coupe et augmente la durée de vie de l'outil, ce qui vous permet d'augmenter considérablement la vitesse de coupe et de traiter plus de pièces par unité de temps. Cependant, une diminution de l'angle principal dans le plan φ entraîne une augmentation de la force radiale (répulsive) qui, lors du traitement de pièces insuffisamment rigides, peut provoquer leur flexion, une perte de précision et également de fortes vibrations. L'apparition de vibrations, à son tour, entraîne une détérioration de la pureté de la surface usinée et provoque souvent l'écaillage du tranchant de la fraise.
Vitesse de coupe. Lors de l'usinage sur un tour, le point A, situé sur un cercle de diamètre D (Fig. 54), en un tour de pièce parcourt une trajectoire égale à la longueur de ce cercle.
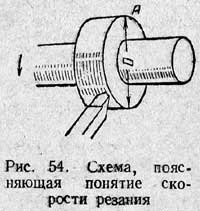
La longueur d'un cercle est d'environ 3,14 fois son diamètre, il est donc égal à 3,14 D.
Le nombre 3,14, indiquant combien de fois la longueur d'un cercle est supérieure à son diamètre, est généralement désigné par la lettre grecque π (pi).
Le point A en un tour fera un chemin égal à πD. Le diamètre D de la pièce, ainsi que sa circonférence πD, se mesurent en millimètres.
Supposons que la pièce fasse plusieurs tours par minute. Désignons leur nombre par la lettre n tours par minute, ou en abrégé rpm. Le chemin que prendra le point A dans ce cas sera égal au produit de la circonférence et du nombre de tours par minute, soit πDn millimètres par minute ou en abrégé mm/min, et s'appelle vitesse circonférentielle.
Chemin, point passable la surface à usiner en tournant par rapport au tranchant de la fraise en une minute est appelée vitesse de coupe.
Le diamètre de la pièce étant généralement exprimé en millimètres, pour trouver la vitesse de coupe en mètres par minute, il faut diviser πDn par 1000. Cela peut s'écrire sous la forme suivante :
où v est la vitesse de coupe en m/min ;
D est le diamètre de la pièce en mm;
n est le nombre de tours par minute.
Exemple 3 Diamètre du rouleau traité D = 100 = 150 tr/min. Déterminez la vitesse de coupe.
Décision: Comptage de la vitesse de la broche. Lors du tournage d'une pièce de diamètre connu, il peut être nécessaire pour un tourneur de régler la machine à un tel nombre de tours de broche afin d'obtenir la vitesse de coupe souhaitée. Pour cela, la formule suivante est utilisée : où D est le diamètre de la pièce en mm;
Exemple 4 Quel nombre de tours par minute un rouleau d'un diamètre de D \u003d 50 mm doit-il avoir à une vitesse de coupe de v \u003d 25 m / min?
Décision:
9. Informations de base sur les forces agissant sur la fraise et la puissance de coupe
Forces agissant sur la fraise. Lors du retrait des copeaux de la pièce, la fraise doit surmonter la force d'adhérence des particules métalliques les unes aux autres. Lorsque le tranchant de la fraise coupe le matériau en cours de traitement et que le copeau est séparé, la fraise subit une pression du métal à séparer (Fig. 55).

De haut en bas, la force P z appuie sur la fraise, ce qui a tendance à presser la fraise vers le bas et à plier la pièce vers le haut. Cette force est appelée force de coupe.
Dans le plan horizontal dans le sens opposé au mouvement d'avance, la fraise est pressée par la force P x, appelée force axiale, ou alors force d'alimentation. Cette force lors du tournage longitudinal a tendance à pousser la fraise vers la poupée mobile.
Dans le plan horizontal, perpendiculaire à la direction d'avance, la fraise est pressée par la force P y, appelée force radiale. Cette force a tendance à éloigner la fraise de la pièce et à la plier dans le sens horizontal.
Toutes les forces répertoriées sont mesurées en kilogrammes.
La plus grande des trois forces est la force de coupe verticale : elle est d'environ 4 fois la force d'avance et 2,5 fois la force radiale. La force de coupe charge les pièces du mécanisme de la poupée ; il charge également la fraise, la pièce, provoquant souvent de fortes contraintes en celles-ci.
Des expériences ont établi que la force de coupe dépend des propriétés du matériau traité, de la taille et de la forme de la section du copeau à enlever, de la forme de la fraise, de la vitesse de coupe et du refroidissement.
Caractériser la résistance divers matériaux coupe a établi le concept de coefficient de coupe. Le facteur de coupe K est la pression de coupe en kilogrammes par millimètre carré de la section coupée, mesurée dans certaines conditions de coupe :
Profondeur de coupe t......................5 mm
Avance s......................1 mm/tr
Angle de coupe γ......................15°
Angle d'attaque φ......45°
Le tranchant de la fraise - rectiligne, horizontal
La pointe de la fraise est arrondie avec un rayon r = 1 mm
Le travail est effectué sans refroidissement
En tableau. 3 montre les valeurs moyennes du facteur de coupe pour certains métaux.
Tableau 3
Valeurs moyennes du facteur de coupe K lors du tournage
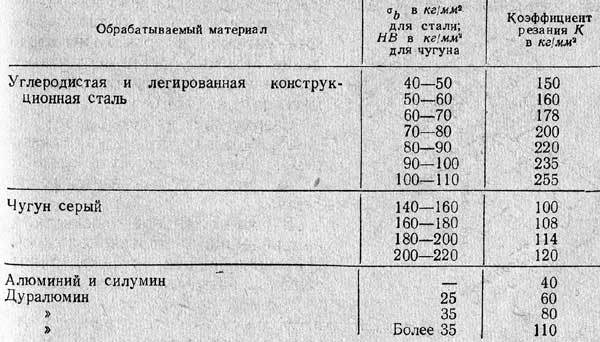
Si le facteur de coupe K est connu, alors en le multipliant par la section transversale de la coupe f en mm 2, vous pouvez trouver la valeur approximative de la force de coupe à l'aide de la formule
P z \u003d Kf kg. (huit)
Exemple 5 Un arbre en acier fabriqué à la machine avec σ b = 60 kg / mm 2 est tourné sur un tour. Déterminer la force de coupe si la profondeur de passe t = 5 mm et l'avance s = 0,5 mm/tr.
Décision. Selon la formule (8), la force de coupe P z \u003d Kf kg. (huit) Nous déterminons la valeur de f: f \u003d ts \u003d 5x0,5 \u003d 2,5 mm 2. D'après le tableau 3 on trouve la valeur de K pour l'acier de fabrication mécanique avec σ b \u003d 60 kg/mm 2 : K \u003d 160 kg/mm 2. Par conséquent, z = Kf = 160x2,5 = 400 kg. puissance de coupe. Connaissant la force de coupe et la vitesse de coupe, vous pouvez connaître la puissance nécessaire pour couper les copeaux d'une section donnée.
La puissance de coupe est déterminée par la formule (9) où N res - puissance de coupe en ch;
P z - force de coupe en kg;
v - vitesse de coupe en m/min.
La puissance du moteur électrique de la machine-outil doit être légèrement supérieure à la puissance de coupe, car une partie de la puissance du moteur électrique est dépensée pour surmonter les frottements dans les mécanismes qui transmettent le mouvement du moteur électrique à la broche de la machine.
Exemple 6 Déterminez la puissance de coupe pour faire tourner l'arbre, considérée dans l'exemple précédent, si le traitement est effectué à une vitesse de coupe, υ = 60 m/min. Décision . Selon la formule (9), le pouvoir de coupe
La puissance de coupe n'est généralement pas exprimée en chevaux-vapeur, mais en kilowatts (kW). Un kilowatt équivaut à 1,36 fois la puissance, donc pour exprimer la puissance en kilowatts, vous devez diviser la puissance par 1,36 :
et vice versa,
10. Chaleur de coupe et durée de vie de l'outil
Avec une augmentation de la force de coupe, la force de frottement augmente, ce qui entraîne une augmentation de la quantité de chaleur dégagée pendant le processus de coupe. La chaleur de coupe augmente encore plus à mesure que la vitesse de coupe augmente, car cela accélère l'ensemble du processus de formation des copeaux.
La chaleur générée par la coupe avec une élimination insuffisante de celle-ci ramollit la fraise, ce qui entraîne une usure plus intense de sa partie coupante. Cela rend nécessaire de changer la fraise ou de l'affûter et de la réinstaller.
Le temps de travail continu de la fraise avant l'émoussage est appelé la durée de vie de l'outil (mesurée en minutes). Changement fréquent de fraise (courte durée de vie de l'outil) dépenses supplémentaires pour affûter et installer la fraise, ainsi que pour réapprovisionner les fraises usées.
Par conséquent, la durée de vie de l'outil est un facteur important lors du choix des conditions de coupe, en particulier lors du choix de la vitesse de coupe.
La durabilité du couteau dépend principalement des qualités du matériau à partir duquel il est fabriqué. Le plus résistant sera le cutter, qui est fait d'un matériau qui permet la température de chauffage la plus élevée sans perte de dureté importante. Les fraises équipées de plaques en alliage dur, les plaques minéralo-céramique ont la plus grande résistance ; beaucoup moins de résistance - fraises en acier rapide, les plus petites - fraises en acier à outils au carbone.
La résistance de la fraise dépend également des propriétés du matériau traité, de la section de coupe, des angles d'affûtage de la fraise et de la vitesse de coupe. L'augmentation de la dureté du matériau usiné réduit la durée de vie de l'outil.
En modifiant les angles d'affûtage et la forme de la surface frontale, il est possible d'obtenir une augmentation significative de la durabilité des fraises et de leur productivité.
La vitesse de coupe a un effet particulièrement important sur la durée de vie de l'outil. Parfois, même la moindre augmentation de vitesse entraîne un émoussement rapide de la fraise. Par exemple, si, lors du traitement de l'acier avec une fraise à grande vitesse, la vitesse de coupe n'est augmentée que de 10%, c'est-à-dire 1,1 fois, la fraise s'émousse deux fois plus vite et vice versa.
Avec une augmentation de la section transversale de la coupe, la durée de vie de l'outil diminue, mais pas autant qu'avec la même augmentation de la vitesse de coupe.
La durée de vie de l'outil dépend également de la taille de l'outil, de la forme de la section coupée et du refroidissement. Plus la fraise est massive, mieux elle évacue la chaleur du tranchant et, par conséquent, plus sa durabilité est grande.
Les expériences montrent qu'avec la même section de coupe, une grande profondeur de coupe et une plus petite avance offrent une plus grande durée de vie qu'une plus petite profondeur de coupe avec une avance correspondante plus grande. Cela s'explique par le fait qu'avec une plus grande profondeur de coupe, les copeaux entrent en contact avec une plus grande longueur du tranchant, donc la chaleur de coupe est mieux évacuée. C'est pourquoi, avec la même section de coupe, il est plus rentable de travailler avec une plus grande profondeur qu'avec une plus grande avance.
La durabilité de la fraise augmente considérablement lorsqu'elle est refroidie.
Le liquide de refroidissement doit être fourni en abondance (émulsion 10-12 l/min, huile et sulfofresol 3-4 l/min) ; une petite quantité de liquide non seulement ne profite pas, mais gâche même le couteau, provoquant l'apparition de petites fissures à sa surface, entraînant un écaillage.
11. Choix de la vitesse de coupe
La productivité du travail dépend du choix de la vitesse de coupe : plus la vitesse de coupe est élevée, moins de temps consacré au traitement. Cependant, à mesure que la vitesse de coupe augmente, la durée de vie de l'outil diminue, de sorte que le choix de la vitesse de coupe est influencé par la durée de vie de l'outil et tous les facteurs qui affectent la durée de vie de l'outil. Parmi celles-ci, les plus importantes sont les propriétés du matériau à usiner, la qualité du matériau de la fraise, la profondeur de coupe, l'avance, les dimensions de la fraise et les angles d'affûtage et le refroidissement.
1. Plus la durée de vie de l'outil doit être longue, plus la vitesse de coupe doit être basse et vice versa.
2. Plus le matériau traité est dur, plus la durée de vie de l'outil est courte. Par conséquent, pour assurer la résistance nécessaire lors de l'usinage de matériaux durs, la vitesse de coupe doit être réduite. Lors de l'usinage de pièces moulées et forgées, à la surface desquelles se trouve une croûte dure, des coquilles ou des écailles, il est nécessaire de réduire la vitesse de coupe par rapport à ce qui est possible lors de l'usinage de matériaux sans croûte.
3. Les propriétés matérielles de la fraise déterminent sa durabilité, par conséquent, le choix de la vitesse de coupe dépend également de ces propriétés. Toutes choses étant égales par ailleurs, les fraises en acier rapide permettent une vitesse de coupe nettement plus élevée que les fraises en acier au carbone; des vitesses de coupe encore plus élevées permettent des fraises équipées d'alliages durs.
4. Afin d'augmenter la résistance de la fraise lors du traitement de métaux visqueux, il est avantageux d'utiliser le refroidissement des fraises. Dans ce cas, avec la même durée de vie d'outil, il est possible d'augmenter la vitesse de coupe de 15 à 25 % par rapport à un usinage sans refroidissement.
5. Les dimensions de la fraise et les angles de son affûtage affectent également la vitesse de coupe admissible : plus la fraise est massive, notamment sa tête, mieux elle évacue la chaleur générée lors de la coupe. Des angles de fraise mal sélectionnés qui ne correspondent pas au matériau traité augmentent la force de coupe et contribuent à une usure plus rapide de la fraise.
6. Avec une augmentation de la section de coupe, la durée de vie de l'outil diminue, par conséquent, avec une section plus grande, il est nécessaire de choisir une vitesse de coupe plus faible qu'avec une section plus petite.
Étant donné que les petits copeaux sont éliminés lors de la finition, la vitesse de coupe lors de la finition peut être beaucoup plus élevée que lors de l'ébauche.
Etant donné qu'une augmentation de la section de coupe a moins d'effet sur la durée de vie de l'outil qu'une augmentation de la vitesse de coupe, il est avantageux d'augmenter la section de coupe en raison d'une légère diminution de la vitesse de coupe. La méthode de traitement du tourneur innovateur de l'usine de machines-outils Kuibyshev V. Kolesov est basée sur ce principe. Travaillant à une vitesse de coupe de 150 m/min, T. Kolesov finit des pièces en acier avec une vitesse d'avance allant jusqu'à 3 mm/tour au lieu de 0,3 mm/tour, ce qui entraîne une réduction du temps machine de 8 à 10 fois.
La question se pose : pourquoi les tourneurs avancés augmentent-ils souvent la productivité du travail en augmentant la vitesse de coupe ? Cela ne contredit-il pas les lois fondamentales de la coupe ? Non, ça ne se contredit pas. Ils n'augmentent la vitesse de coupe que dans les cas où les possibilités d'augmenter la section de coupe sont pleinement exploitées.
Lors de la semi-finition ou de la finition, où la profondeur de coupe est limitée par une petite tolérance d'usinage et l'avance est limitée par les exigences de haute pureté d'usinage, une augmentation du mode de coupe est possible en augmentant la vitesse de coupe . C'est ce que font les tourneurs avancés, travaillant sur la semi-finition et la finition. S'il est possible de travailler avec grandes sections coupe (avec de grandes tolérances), puis, tout d'abord, il faut choisir la plus grande profondeur de coupe possible, puis la plus grande avance possible technologiquement admissible, et, enfin, la vitesse de coupe correspondante.
Dans les cas où la tolérance d'usinage est faible et qu'il n'y a pas d'exigences particulières pour la finition de surface, le mode de coupe doit être augmenté en utilisant la plus grande avance possible.
12. Propreté de la surface usinée
Lors de l'usinage avec une fraise, des irrégularités sous forme de dépressions et de festons restent toujours sur la surface usinée de la pièce, même avec la finition la plus soignée. La hauteur de la rugosité dépend de la méthode de traitement.
La pratique a établi que plus la surface de la pièce est traitée proprement, moins elle est sujette à l'usure et à la corrosion, et la pièce est plus résistante.
Une finition de surface soignée lors de l'usinage d'une pièce est toujours plus coûteuse qu'une finition de surface rugueuse. Par conséquent, la propreté de la surface usinée doit être attribuée en fonction des conditions de fonctionnement de la pièce.
Désignation de la propreté de surface dans les dessins. Selon GOST 2789-59, 14 classes de propreté de surface sont fournies. Pour désigner toutes les classes de pureté, un signe est établi - un triangle équilatéral, à côté duquel le numéro de classe est indiqué (par exemple, 7; 8; 14). Les surfaces les plus propres sont de grade 14 et les plus rugueuses de grade 1.
La rugosité de surface selon GOST 2789-59 est déterminée par l'un des deux paramètres suivants : a) l'écart moyen arithmétique du profil R a et b) la hauteur des irrégularités R z .
Pour mesurer la rugosité et affecter la surface traitée à une classe particulière, instruments de mesure basé sur la méthode de palpage du profil de surface avec une fine aiguille diamantée. Ces appareils sont appelés profilomètres et profilographes.
Pour déterminer la rugosité et classer la surface traitée dans l'une ou l'autre classe de propreté dans des conditions d'atelier, des échantillons testés de différentes classes de propreté sont utilisés - les soi-disant normes de pureté, avec lesquelles la surface usinée de la pièce est comparée.
Facteurs affectant la finition de surface. La pratique a établi que la propreté de la surface usinée dépend d'un certain nombre de raisons : le matériau à usiner, le matériau de la fraise, les angles d'affûtage et l'état des arêtes de coupe de la fraise, la vitesse d'avance et de coupe, la lubrification et les propriétés de refroidissement du liquide, la rigidité du système machine - fraise - pièce, etc.
particulièrement importance obtenir une surface Haute qualité en tournage, il a une vitesse de coupe, une avance, des angles d'avance et un rayon de courbure de la pointe de l'outil. Plus l'angle d'avance et d'attaque est petit et plus le rayon d'angle est grand, plus la surface usinée est propre. La vitesse de coupe affecte grandement la finition de surface. Lors du tournage d'acier à une vitesse de coupe supérieure à 100 m/min, la surface usinée est plus propre qu'à une vitesse de 25-30 m/min.
Pour obtenir une surface usinée plus propre, il faut faire attention à l'affûtage et à la finition soigneuse des arêtes de coupe.
question test 1. Quelle est la forme du copeau lors de l'usinage de métaux visqueux ? Lors du traitement de métaux fragiles ?
2. Nommez les principaux éléments de la tête d'incisive.
3. Montrez les surfaces avant et arrière sur l'incisive; coins avant et arrière; angle d'affûtage.
4. A quoi servent les coins avant et arrière de l'incisive ?
5. Afficher les angles d'avance et l'angle d'avance.
6. De quels matériaux sont faits les cutters ?
7. Quelles qualités d'alliages durs sont utilisées dans le traitement de l'acier ? Lors du traitement de la fonte?
8. Listez les éléments du mode de coupe.
9. Quelles forces agissent sur la fraise ?
10. Quels facteurs et comment affectent-ils l'amplitude de la force de coupe ?
11. Qu'est-ce qui détermine la durabilité de la fraise ?
12. Quels facteurs influencent le choix de la vitesse de coupe ?
Les principaux outils de coupe utilisés dans le processus comprennent une fraise, dont les paramètres géométriques déterminent ses capacités techniques, sa précision et son efficacité de traitement. Tout spécialiste qui décide de se consacrer à transformer les affaires, dans la mesure où bon choix les angles d'arête de coupe augmentent à la fois la durée de vie de l'outil et la productivité.
Paramètres des outils de tournage
Quelconque outil de tournage forment un support nécessaire à la fixation de l'outil dans le support tour, et une tête de travail qui assure la coupe du métal. Pour considérer les paramètres géométriques d'un outil de tournage, il est préférable de prendre un outil traversant comme exemple.
Sur la partie coupante de l'outil de tournage de ce genre il y a trois surface :
- avant (lors du traitement de la pièce, des copeaux de métal se détachent);
- arrière - principal et auxiliaire (tous deux tournés avec leur partie avant vers la pièce).
Le bord de l'outil, appelé tranchant (et directement impliqué dans le traitement), est formé par l'intersection de ses surfaces avant et arrière principale. Dans la géométrie de l'outil de tournage, on distingue également un tranchant auxiliaire. Il est respectivement formé par l'intersection de la surface avant avec le dos auxiliaire.
Le point où les arêtes de coupe principales et secondaires se croisent est appelé la pointe de la fraise. Ce dernier, lors de la coupe du métal, subit des charges énormes, conduisant à sa rupture. Pour augmenter la résistance de la pointe de la fraise, elle n'est pas affûtée pendant le processus d'affûtage, mais légèrement arrondie. Cela nécessite l'introduction d'un paramètre tel que le rayon du sommet. Il existe un autre moyen d'augmenter la résistance de la pointe d'un outil de tournage - la formation d'un tranchant de transition de forme rectiligne.
Les paramètres géométriques les plus importants des fraises pour le tournage sont leurs angles, qui déterminent arrangement mutuel surfaces d'outils. Les paramètres d'angle varient en fonction du type d'outil de tournage et d'un certain nombre d'autres facteurs :
- matériel d'outil;
- ses conditions de travail ;
- caractéristiques du matériau à traiter.
Angles d'outils pour le tournage
Pour déterminer correctement les angles outil de tournage, eux valeurs exactes, ils sont considérés dans les plans dits initiaux.
- Le plan principal est parallèle aux directions d'avance de l'outil de tournage (longitudinal et transversal) et coïncide avec sa surface d'appui.
- Le plan de coupe comprend l'arête de coupe principale et est tangent à la surface d'usinage. Ce plan est perpendiculaire au plan principal.
- Le plan de coupe principal coupe l'arête de coupe principale et est situé perpendiculairement à la projection que cette arête repose sur le plan principal. Il existe également un plan auxiliaire de type sécant, qui, par conséquent, est perpendiculaire à la projection déposée sur le plan principal par le tranchant auxiliaire.
Comme mentionné ci-dessus, ils sont mesurés précisément dans ces plans, et ceux qui sont mesurés dans un plan appelé la sécante principale sont désignés comme les principaux. Il s'agit notamment des angles principaux avant, principaux arrière, ainsi que des angles d'affûtage et de coupe.
L'un des plus importants est l'angle de dégagement principal de l'outil de tournage, qui minimise le frottement qui se produit lorsque la surface arrière de l'outil interagit avec la pièce en cours de traitement (et donc réduit l'échauffement de l'outil et prolonge sa durée de vie ). Cet angle est formé par la surface de coupe (arrière principal) et le plan de coupe. Lors du choix de cet angle lors de l'affûtage d'un outil, le type de traitement et le matériau de la pièce sont pris en compte. Dans ce cas, vous devez être conscient qu'une forte augmentation de la taille de l'angle de dégagement entraîne une défaillance rapide de l'outil de tournage.
La résistance et la durabilité de l'outil de coupe, les forces qui se produisent pendant le traitement, sont déterminées par les paramètres de l'angle de coupe. Il est situé entre la surface avant de l'outil de tournage et le plan dans lequel se trouve le tranchant principal (ce plan est perpendiculaire au plan de coupe). Lors de l'affûtage d'un outil de tournage, un certain nombre de facteurs sont pris en compte qui affectent la valeur de cet angle :
- matériau de la pièce et l'outil lui-même ;
- la forme de la surface avant;
- conditions d'utilisation de la fraise.
Une augmentation de la valeur de l'angle de coupe, d'une part, améliore la finition du traitement et, d'autre part, provoque une diminution de la résistance et de la durabilité de l'outil de tournage. Un tel angle, obtenu à la suite d'un affûtage, peut avoir un effet positif et Sens négatif.
Les fraises tournantes avec des angles de coupe qui ont des valeurs négatives sont très durables, mais il est difficile d'usiner avec de tels outils. Habituellement, l'affûtage avec un angle de coupe, qui a une valeur positive, est utilisé lorsque la pièce doit être traitée à partir d'un matériau visqueux, ainsi que lorsque le matériau de l'outil est très durable.
Les fraises à angles de coupe négatifs sont utilisées lors de l'usinage de matériaux de dureté et de résistance élevées, lors d'une coupe interrompue, lorsque le matériau de l'outil n'a pas une résistance à la flexion suffisante et n'absorbe pas bien les charges de choc.
Les paramètres qui caractérisent la géométrie de la fraise pour le tournage sont également les angles de coupe et de pointage. L'angle de coupe, dont la valeur peut varier entre 60 et 100 0, est situé entre la surface de l'outil, appelée avant, et le plan de coupe.
La valeur de cet angle dépend directement de la dureté du métal traité : plus il est élevé, plus sa valeur est élevée. L'angle de conicité est parfaitement cohérent avec son nom, il est mesuré entre les surfaces principales avant et arrière de l'outil et caractérise le degré d'affûtage de son sommet.
Caractériser l'outil de tournage et les angles dans le plan. C'est le principal, mesuré entre la direction de l'avance longitudinale et la projection que le tranchant principal pose sur le plan principal, et l'auxiliaire, formé par la projection du tranchant auxiliaire sur le plan principal et la direction de l'avance longitudinale.
Lors de l'affûtage, ces angles ne sont pas choisis arbitrairement, mais en fonction du type de tournage et de la rigidité du système «machine-outil-pièce». Ainsi, le traitement de la plupart des métaux peut être effectué avec des outils avec un angle principal dans le plan égal à 45 0, mais les pièces minces et longues doivent être traitées avec des fraises, dans lesquelles la valeur de cet angle est de l'ordre de 60– 90 0 . Ceci est nécessaire pour éliminer la déflexion et le tremblement de la pièce.
L'angle auxiliaire en avance est corrélé à la fois à la finition de l'usinage et à la durée de vie de l'outil. Avec sa diminution, la propreté du traitement augmente et la durée de vie de l'outil augmente.
En plus de ceux discutés ci-dessus, dans la géométrie des outils de tournage, les angles sont distingués.
Le tournage longitudinal est appelé tournage, dans lequel la direction du mouvement de l'alimentation est parallèle à l'axe de la pièce. Sur les tours, le mouvement de coupe - rotation - est attaché à la pièce et le mouvement d'avance - mouvement de translation - à la fraise. Sur les machines à bâtons ronds, l'outil de coupe tourne et le mouvement d'avance est attaché à la pièce. Le véritable chemin de coupe est une ligne hélicoïdale.
Faire la distinction entre tournage fin et grossier.
Le tournage fin (Fig. 2, a) est effectué avec une fraise avec des surfaces de travail plates et des tranchants droits - le principal et l'auxiliaire. La position des arêtes de coupe par rapport à l'axe de rotation de la pièce est caractérisée par l'angle principal en avance et l'angle auxiliaire en avance. La valeur de l'angle auxiliaire dans le plan détermine la profondeur des irrégularités cinématiques, elle ne peut donc pas être plus grande. La position des faces formant le tranchant principal est caractérisée par l'angle de dépouille, l'angle d'affûtage et l'angle de front.
Le tranchant principal produit une coupe en travers, caractérisée par l'angle d'inclinaison des fibres de bois.
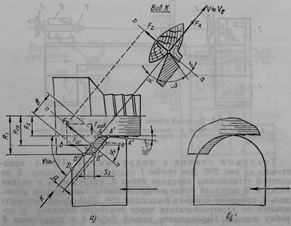
Riz. 2. Tournage longitudinal finition (a) et ébauche (b)
L'angle d'inclinaison est mesuré entre la direction des fibres et la normale.
Le tournage grossier (Fig. 2, b) est effectué avec des fraises rainurées à tranchant semi-circulaire. Section transversale les copeaux sont en forme de faucille, l'épaisseur des copeaux à la périphérie de la pièce est maximale et près de la surface de la pièce, elle est insignifiante même à grande avance de la fraise. Cela vous permet d'appliquer l'avance par fraise jusqu'à 2 mm, tandis que pour le tournage fin - pas plus de 0,8 mm.
> Réglage des tours
Lors de la configuration des tours, il est nécessaire de: sélectionner une fraise et la fixer dans le porte-outil (pour les machines à avance mécanique); installer une plaque frontale ou un mandrin ; sélectionner et fixer le repose-main (pour les machines avec alimentation manuelle) ou une règle de copie (pour les machines à avance mécanique) ; installer et fixer la pièce dans la machine ; tester la machine au ralenti ; régler la vitesse de la broche et l'avance ; traiter et inspecter les éprouvettes.
Le couteau requis est sélectionné en fonction de la nature du travail effectué. Pour l'ébauche initiale, une fraise à éplucher est utilisée, pour la finale, une fraise de finition à tranchant droit. Avec l'avance mécanique, la fraise est fixée dans le porte-outil avec des vis. Pour réduire le temps de changement, des têtes rotatives spéciales sont utilisées, où plusieurs incisives à des fins diverses sont simultanément renforcées.
À travail manuel il est nécessaire de vérifier la fiabilité de la fixation du couteau au manche en bois. N'utilisez pas un outil de coupe défectueux.
Les moyens de fixation de la pièce sont choisis en fonction de sa forme et de sa taille. Pour la fixation de pièces longues (Fig. 3, a), des centres avant et arrière sont utilisés. Le centre avant 2 est réalisé sous la forme d'une laisse à trois dents avec une tige conique, avec laquelle il est inséré dans le trou conique de la broche 1. Le centre arrière 4 a une partie conique et pointue et est fixé dans la plume 5 de la contrepointe 6. Pour réduire les frottements et augmenter la fiabilité de la fixation de la pièce, la pointe arrière est montée sur roulement, ce qui assure sa rotation avec la pièce 3.

Riz. 3. Fixation de la pièce dans les tours: a - dans les centres, b - dans le mandrin, c - sur la plaque frontale; 1 - broche, 2 - centre avant, 3 - pièce, 4 - centre arrière, 5 - fourreau, 6 - poupée mobile, 7 - mandrin, 8 - plan
En fonction de la longueur de la pièce à usiner, la poupée mobile est déplacée le long des guides du lit et fixée dans une position prédéterminée. La pièce est fixée en poussant la douille hors de la poupée jusqu'à ce que les pointes soient encastrées dans les extrémités de la pièce et la maintiennent solidement pendant la rotation. Pour tourner des pièces coniques, le corps de la poupée mobile doit être déplacé transversalement avec une vis de réglage et fixé avec un dispositif de verrouillage. Les mandrins sont conçus pour fixer des pièces courtes (Fig. 3, b). Le mandrin 7 a un filetage à travers lequel il est vissé sur la broche. La pièce est fixée dans le mandrin en insérant fermement son extrémité dans le trou du mandrin. Des mandrins à pinces et des mandrins à mors coulissants sont également utilisés.
Pour le serrage de pièces de petite longueur et grand diamètre servent de plastrons 8 (Fig. 3, c), vissés sur la broche. La pièce est fixée à la plaque frontale avec des vis ou des boulons 9.
La pièce à main est installée sur le châssis de sorte que son bord de travail soit au niveau des centres et soit proche de la génératrice de la pièce en cours de traitement, mais ne la touche pas. Au fur et à mesure que le diamètre diminue et lors du traitement de pièces longues, la pièce à main est réarrangée séquentiellement dans une nouvelle position le long des guides du lit. Lors du traitement de produits façonnés à l'arrière du lit, une règle de copie est fixée sur les supports, dont la forme est similaire à la forme de la pièce finie. Lorsque l'alimentation est activée, l'étrier se déplace le long d'une trajectoire courbe et la fraise reproduit la forme donnée de la pièce.
La vitesse de la broche est sélectionnée en fonction du diamètre de la pièce et de sa résistance. Pour les diamètres plus grands, la vitesse de broche minimale doit être réglée. Lors de l'installation d'une plaque frontale d'un diamètre de 400 mm, la vitesse de la broche ne doit pas dépasser 800 tr/min. La vitesse de rotation est réduite par le levier de changement de vitesse ou en modifiant la vitesse de rotation du moteur électrique à plusieurs vitesses. vitesse de coupe pour le bois roches tendres devrait être de 10 ... 12 m / s, solide - 0,5 ... 3 m / s.
L'avance longitudinale par tour de broche doit être de: pour l'ébauche 1,6 ... 2 mm, pour la finition - pas plus de 0,8 mm. Plus les exigences de rugosité de surface sont élevées, plus l'avance longitudinale doit être faible. L'avance transversale par tour de broche ne doit pas dépasser 1,2 mm. Avant de démarrer la machine, assurez-vous que fixation fiable flans et installez une clôture.
Après l'ébauche de la pièce, la fraise est remplacée et le tournage fin est effectué à faible avance. Les copeaux dans ce cas doivent être aussi continus que possible et d'épaisseur uniforme.
Pendant le traitement, la forme de la pièce est périodiquement contrôlée par un gabarit ou une jauge. Lorsque vous utilisez un calibre ou outil de mesure avec une balance, la machine est éteinte et seulement après l'arrêt complet de la pièce, elle est mesurée.
Une fois le réglage terminé, un traitement d'essai de la pièce est effectué et ses dimensions sont contrôlées avec un calibre ou un outil de mesure avec une échelle.