načini rezanja. Dodaci tijekom grubog tokarenja postali su karbidni glodali bez dodatnog reznog ruba. Velika enciklopedija nafte i plina
Tokarenje se može izvesti mehaničkim pomakom, budući da je generatrisa obrađenog konusa paralelna sa smjerom uzdužnog pomaka rezača.
Tehnološki ciklus kopiranja koristi se za obradu stepenastih, konusnih i zakrivljenih površina koje zahtijevaju uzdužni pomak rezača. Na kraju površinske obrade, rezač se povlači iz dijela, a čeljust se vraća u prvobitni položaj.
Opći indeks stroja za rezanje navoja. |
Uzdužni oslonac 7, postavljen na vodilice kreveta, pomiče se duž njih i osigurava uzdužni dovod rezača. Poprečni nosač omogućuje poprečno dovođenje rezaču. Gornji rotirajući oslonac može se postaviti pod bilo kojim kutom u odnosu na os rotacije obratka, što je neophodno kod obrade stožastih površina obratka.
Shema okretanja oblikovanog obratka. |
Nakon poprečnog pomaka tijela stražnjeg dijela za iznos h do 15 - 20 mm), tvornica obrađenog konusa je paralelna sa smjerom uzdužnog pomaka glodala, pa se okretanje može izvesti mehaničkim pomakom. .
Shema okretanja kuhanja. |
Nakon poprečnog pomaka tijela stražnjeg dijela za vrijednost h (do 15 - 20 mm), tvornica obrađenog konusa je paralelna sa smjerom uzdužnog pomaka rezača, pa se okretanje može izvesti mehaničkim hraniti.
Za narezivanje navoja na tokarskom stroju potrebno je da brzina rotacije vretena bude strogo povezana sa brzinom kretanja čeljusti, budući da uzdužni pomak rezača u jednom okretu vretena mora točno odgovarati nagibu navoja biti izrezan.
Debljina sloja rezanog metala uvelike utječe na veličinu nepravilnosti. Debljina rezanog sloja određena je uzdužnim pomakom rezača. Da nije bilo elastično-plastičnih deformacija tijekom procesa rezanja, visina nepravilnosti bi se lako mogla izračunati iz geometrijski oblik vrh rezača.
Nakon 1 minute od početka rada isključite uzdužni pomak rezača, odmaknite rezač od obratka i brzo okrenite držač alata za 90 ili 180 dok vrh rezača ne dodirne vrh indikatora.
Za dijamante u okviru, uzdužni pomaci trebaju biti manji nego za olovke, a za brušene dijamante još manje. Na primjer, kada se diskovi za brušenje navoja s više navoja obrađuju dijamantnim rezačima, uzdužni pomak rezača ne smije biti veći od 0,05 m / min. Na kraju postupka previjanja, preporuča se napraviti jedan ili dva prolaza bez poprečnog dodavanja, smanjujući količinu uzdužnog dodavanja.
Uređaj je dizajniran za bušenje konusnih rupa sa konstantnim kutom a. Uređaj je pričvršćen na radijalnu potporu prednje ploče stroja. Okretanjem vijka 3, rezač se povlači uzdužno. Na drugom kraju vijka ugrađena je zvjezdica 1, koja, skačući zubom pri svakom okretu čeljusti na postavljeni graničnik, vrši automatsko uzdužno pomicanje.
Da bi se izradak obradio rezanjem i time dobile obrađene površine pojedinog dijela, izratka i nanesene alat za rezanje treba napraviti određenim pokretima. Ti se pokreti dijele na glavne (služe za provedbu postupka rezanja) i pomoćne (služe za pripremu za proces rezanja i za završetak operacije). Postoje dva glavna pokreta:
- rezni pokret (ili glavni pokret);
- kretanje hrane.
Prilikom obrade na tokarskom stroju, pokret rezanja - rotacijski - izvodi izradak, koji je na ovaj ili onaj način pričvršćen na vreteno stroja, a pomicanje - translatorno - prima rezni alat (rezač) čvrsto učvršćen u alatu. držač. Pokret omogućuje proces rezanja (formiranje strugotine), kretanje posmaka omogućuje provođenje ovog procesa (obrade) duž cijele duljine obratka (Sl. Dio 16).
Dubina rezanja (t)- vrijednost rezanog sloja u jednom prolazu, mjerena u smjeru okomitom na obrađenu površinu. Dubina reza je uvijek okomita na smjer pomaka (vidi također sliku 11-14). Kod vanjskog uzdužnog tokarenja (slika 16.) to je polurazlika između promjera obratka i promjera obrađene površine dobivene nakon jednog prolaza:
Brzina rezanjaυ - količina pomaka točke sječivo u odnosu na površinu u jedinici vremena tijekom izvođenja pokreta rezanja *.
Prilikom okretanja, kada se radni komad okreće frekvencijom od n o/min, brzina rezanja u MK točkama reznog ruba bit će promjenjiva vrijednost. Maksimalna brzina:
gdje je D najveći promjer površine u mm.
* Brzina rezanja je funkcija brzine rotacije obratka i brzine kretanja alata (posmaka).
Ako je brzina poznata, lako je odrediti frekvenciju vrtnje:
Kod uzdužnog tokarenja, brzina rezanja ima konstantnu vrijednost tijekom cijelog vremena rezanja (ako je promjer obratka po cijeloj dužini isti, a brzina vrtnje je nepromijenjena). Prilikom obrezivanja kraja, kada se rezač pomiče od periferije obratka prema sredini, brzina rezanja pri konstantnoj brzini je promjenjiva. Ona ima najviša vrijednost na periferiji i jednaka je nuli u središtu (slika 17). Brzina rezanja će također biti promjenjiva duž obrađene površine tijekom odvajanja (vidi sliku 14). Međutim, u tim slučajevima razmotrite najveća brzina rezanje.
Podnošenje s(točnije, brzina pomaka) - količina pomaka reznog ruba u odnosu na obrađenu površinu u jedinici vremena u smjeru pomaka. Prilikom okretanja može biti uzdužni dovod kada se rezač pomiče u smjeru paralelnom s osi obratka (vidi sliku 16); križno napajanje kada se rezač pomiče u smjeru okomitom na os obratka (vidi sliku 17), i kosi feed- pod kutom prema osi obratka (na primjer, kod okretanja konične površine).
Razlikovati visinu tona u jednom okretu obradak, tj. količina relativnog pomaka rezača tijekom jednog okretaja obratka (iz položaja I rezač se pomaknuo u položaj II, slika 16), i minutno hranjenje, tj. vrijednost relativnog kretanja rezača za 1 min. Minutni pomak je označen sa S m (mm / min), a pomak po okretaju - s (mm / okret). Između njih postoji sljedeći odnos.
kući
dio tri
Osnove teorije rezanja metala.
Izbor podataka za rezanje
Poglavlje VI
Osnove teorije rezanja metala
Utemeljitelji teorije rezanja metala bili su istaknuti ruski znanstvenici I. A. Time (1838-1920), K. A. Zvorykin (1861-1928), Ya. G. Usachev (1873-1941) i dr. Radovi ovih znanstvenika, koji su primili svjetska priznanja još nisu izgubila na vrijednosti. Međutim, u uvjetima zaostale carske Rusije, sva ta djela nisu pronađena praktična aplikacija jer je industrija bila nerazvijena.
Znanost o rezanju metala dobila je širok opseg tek nakon Velike listopadske socijalističke revolucije, osobito tijekom sovjetskih petogodišnjih planova, kada je znanost stavljena u službu socijalističke industrije.
Sovjetski znanstvenici V. D. Kuznetsov, V. A. Krivoukhov, I. M. Bezprozvanny, A. M. Rozenberg, M. N. Larin, P. P. Trudov, M. I. Klushin i drugi stvorili su nacionalnu školu rezanja metala, razlikovna značajkašto je bliska suradnja znanosti s proizvodnjom, znanstvenika s inovatorima proizvodnje.
Važnu ulogu u razvoju znanosti o rezanju metala odigralo je kretanje inovatora u proizvodnji. U nastojanju da povećaju produktivnost rada, čelnici proizvodnje počeli su tražiti nove načine za poboljšanje uvjeta rezanja: stvorili su novu geometriju reznog alata, promijenili uvjete rezanja, ovladali novim materijala za rezanje. Svaki radno mjesto Tokar-inovator postao je poput malog laboratorija za proučavanje procesa rezanja.
Široka razmjena iskustava, moguća samo u uvjetima socijalističke ekonomije, te bliska suradnja vodećih radnika u proizvodnji i znanosti osigurali su brz razvoj znanosti o rezanju metala.
1. Rad rezača
Wedge i njegovo djelo. Radni dio svakog reznog alata je klin(slika 44). Pod djelovanjem primijenjene sile vrh klina se urezuje u metal.
Što je klin oštriji, odnosno što je manji kut koji formiraju njegove strane, to je manja sila potrebna za njegovo urezivanje u metal. Kut koji čine stranice klina naziva se konusni kut i označava se grčkim slovom β ( beta). Stoga, što je manji kut konusa β, to lakše klin prodire u metal, i, obrnuto, što je veći kut konusa β, to je veća sila koja se mora primijeniti za rezanje metala. Prilikom dodjele kuta konusa potrebno je uzeti u obzir mehanička svojstva metala koji se obrađuje. Ako režete tvrdi metal rezačem s malim kutom oštrenja β, tada tanka oštrica neće izdržati i slomiti će se ili slomiti. Stoga se, ovisno o tvrdoći metala koji se obrađuje, dodjeljuje odgovarajući kut zaoštravanja klina.
Sloj metala koji se obrađuje, smješten neposredno ispred rezača, kontinuirano se komprimira svojom prednjom površinom. Kada sila rezača premašuje sile prianjanja metalnih čestica, komprimirani element se smiče i pomiče prednjom površinom klina prema gore. Rezač, koji se kreće naprijed pod djelovanjem primijenjene sile, nastavit će se komprimirati, lomiti i pomicati pojedinačni elementi od kojih se formira čips.
Osnovni pokreti u okretanju. Prilikom obrade na tokarilicama, izradak se rotira, a rezač prima kretanje u uzdužnom ili poprečnom smjeru. Rotacija obratka naziva se glavni pokret, i pomicanje rezača u odnosu na dio - gibanje hrane(slika 45).
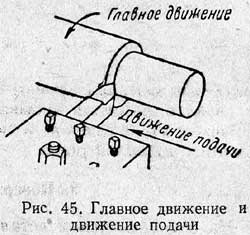
2. Glavni dijelovi i elementi alata za tokarenje
Rezač se sastoji od dva glavna dijela: glave i tijela (šipka) (slika 46). Glava je radni (rezni) dio rezača; tijelo služi za učvršćivanje rezača u držač alata.

Glava se sastoji od sljedećih elemenata: prednja površina, uz koje se čips skida, i stražnje površine okrenut prema obratku. Jedna od stražnjih površina okrenuta prema reznoj površini naziva se glavni; drugi, okrenut prema tretiranoj površini, - pomoćni.
Rezni rubovi dobivaju se od sjecišta prednje i stražnje površine. Razlikovati Dom i pomoćni rezni rub. Većinu reznog posla obavlja glavni rezni rub.
Sjecište glavnog i sekundarnog reznog ruba naziva se vrh sjekutića.
3. Površinska obrada
Na izratku se razlikuju tri vrste površina (slika 47): obrađena, obrađena i rezna površina.

obrađene površina je površina obratka s koje se uklanja strugotina.
Površinski obrađeno naziva se površina dijela dobivenog nakon uklanjanja strugotine.
rezna površina naziva se površina koju na izratku formira glavni rezni rub rezača.
Također je potrebno razlikovati reznu ravninu i osnovnu ravninu.
rezna ravnina naziva se ravnina tangenta na reznu površinu i koja prolazi kroz rezni rub rezača.
Glavna ravnina naziva se ravnina paralelna s uzdužnim i poprečnim posmacima rezača. Kod tokarilica se podudara s vodoravnom potpornom površinom držača alata.
4. Kutovi rezača i njihova namjena
Kutovi radnog dijela rezača uvelike utječu na tijek procesa rezanja.
Odabirom pravih kutova rezača možete značajno produžiti trajanje njegovog neprekidnog rada do otupljenja (trajnost) i obrade u jedinici vremena (po minuti ili satu) velika količina detaljima.
O izboru kutova reza ovise i sila rezanja koja djeluje na rezač, potrebna snaga, kvaliteta obrađene površine itd. Zato svaki tokar mora dobro proučiti namjenu svakog od kutova oštrenja. rezač i moći ispravno odabrati njihovu najpovoljniju vrijednost.
Kutovi rezača (slika 48) mogu se podijeliti na glavne kutove, kutove rezača u planu i kut nagiba glavnog reznog ruba.
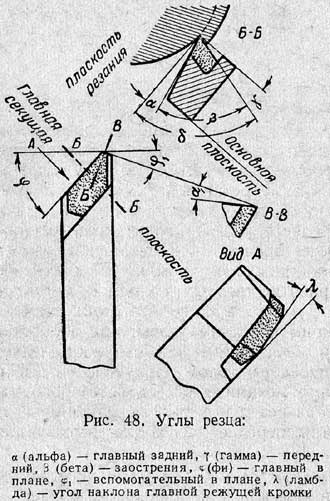
Glavni kutovi uključuju: stražnji kut, prednji kut i kut konusa; kutovi rezača u planu uključuju glavni i pomoćni.
Glavne kutove rezača treba mjeriti u glavnoj reznoj ravnini, koja je okomita na ravninu rezanja i glavnu ravninu.
Radni dio rezača je klin (zasjenjen na slici 48), čiji je oblik karakteriziran kutom između prednje i glavne stražnje površine rezača. Ovaj kutak se zove konusni kut a označava se grčkim slovom β (beta).
stražnji kut α ( alfa) je kut između glavnog boka i rezne ravnine.
Zazorni kut α služi za smanjenje trenja između stražnje površine rezača i obratka. Smanjenjem trenja smanjujemo zagrijavanje rezača koji se zbog toga manje troši. Međutim, ako je kut reljefa jako povećan, sjekutić je oslabljen i brzo uništen.
prednji kut γ ( gama) je kut između prednje površine rezača i ravnine okomite na reznu ravninu, povučenu kroz glavni rezni rub.
Nagibni kut γ igra važnu ulogu u procesu formiranja strugotine. S povećanjem nagibnog kuta, rezač je lakše rezati u metal, smanjuje se deformacija rezanog sloja, poboljšava se protok strugotine, smanjuje se sila rezanja i potrošnja energije, a kvaliteta obrađene površine je poboljšana. S druge strane, prekomjerno povećanje nagibnog kuta dovodi do slabljenja reznog ruba i smanjenja njegove čvrstoće, do povećanja trošenja glodala zbog usitnjavanja reznog ruba i do pogoršanja odvođenja topline. . Stoga pri obradi tvrdih i krhkih metala, kako bi se povećala čvrstoća alata, kao i njegova trajnost, treba koristiti glodala s manjim nagibnim kutom; kod obrade mekih i duktilnih metala treba koristiti glodala s velikim nagibnim kutom kako bi se olakšalo uklanjanje strugotine. U praksi, izbor prednjeg kuta ovisi, pored mehanička svojstva materijal koji se obrađuje, od materijala rezača i oblika prednje površine. Preporučeni nagibni kutovi za glodala od tvrdog metala dati su u tablici. jedan.
Planirajte kutove. Vodeći kut φ ( fi) naziva se kut između glavnog reznog ruba i smjera pomaka.
Kut φ obično se bira u rasponu od 30-90° ovisno o vrsti obrade, vrsti rezača, krutosti obratka i rezača te načinu njihova pričvršćivanja. Kod obrade većine metala prolaznim glodalicama moguće je uzeti kut φ = 45°; pri obradi tanke dugi dijelovi u središtima je potrebno koristiti rezače s kutom od 60, 75 ili čak 90 ° kako se dijelovi ne bi savijali ili drhtali.
Pomoćni kut u planuφ 1 je kut između sekundarnog reznog ruba i smjera pomaka.

Kut λ ( lambda) nagib glavnog reznog ruba(Sl. 49) je kut između glavnog reznog ruba i linije povučene kroz vrh rezača paralelne s glavnom ravninom.
stol 1
Preporučeni nagibni i slobodni kutovi za alate od tvrdog metala
Bilješka. Mehanička svojstva metala određuju se na posebnim strojevima i instrumentima, a svako svojstvo ima svoju oznaku. Oznaka σ b data u ovoj i sljedećim tablicama izražava vlačnu čvrstoću metala; vrijednost ove granice mjeri se u kg/mm2. Slova HB označavaju tvrdoću metala, koja se na Brinellovom uređaju određuje utiskivanjem kaljene čelične kuglice u površinu metala. Vrijednost tvrdoće se mjeri u kg / mm 2.
Rezači čiji je vrh najniža točka reznog ruba, tj. kut λ pozitivan(Sl. 49, c), trajnije su i otpornije; s takvim rezačima dobro je obraditi tvrde metale, kao i isprekidane površine koje stvaraju udarno opterećenje. Prilikom obrade takvih površina karbidne glodalice kut nagiba glavnog reznog ruba podešava se na 20-30°. Rezači čiji je vrh najviša točka reznog ruba, tj. kut λ negativan(Sl. 49, a), preporuča se koristiti za obradu dijelova izrađenih od mekih metala.
5. Materijali koji se koriste za izradu sjekutića
Prilikom rada na reznim rubovima rezača javlja se visoki tlak, kao i visoka temperatura (600-800 ° i više). Trenje stražnje površine rezača o reznu površinu i strugotine na prednjoj površini rezača uzrokuje manje ili više brzo trošenje njegovih radnih površina. Zbog trošenja, oblik reznog dijela se mijenja i rezač nakon nekog vremena postaje neupotrebljiv za daljnji rad; takav rezač se mora skinuti sa stroja i ponovno naoštriti. Kako bi se produžio vijek trajanja alata bez ponovnog brušenja, potrebno je da njegov materijal dobro odolijeva trošenju pri visokim temperaturama. Osim toga, materijal rezača mora biti dovoljno jak da izdrži visoki pritisci koji nastaju tijekom rezanja. Stoga se prema materijalu rezača postavljaju sljedeći osnovni zahtjevi - tvrdoća na visokoj temperaturi, dobra otpornost na habanje i čvrstoća.
Trenutno postoji mnogo alatnih čelika i legura koji zadovoljavaju ove zahtjeve. To uključuje: ugljični alatni čelik, brzorezni čelik, tvrde legure i keramičkih materijala.
Ugljični alatni čelik. Za izradu reznih alata koristi se čelik s udjelom ugljika od 0,9 do 1,4%. Nakon kaljenja i kaljenja, rezni alat izrađen od ovog čelika poprima visoku tvrdoću. Međutim, ako tijekom procesa rezanja temperatura reznog ruba dosegne 200-250 °, tvrdoća čelika naglo pada.
Iz tog razloga, ugljični alatni čelik trenutno ima ograničenu upotrebu: koristi se za izradu reznih alata koji rade pri relativno maloj brzini rezanja kada temperatura u zoni rezanja dosegne malu vrijednost. Takvi alati uključuju: kalupe, razvrtače, slavine, turpije, strugače itd. Rezači se trenutno ne proizvode od ugljičnog alatnog čelika.
Brzorezni čelici. Brzorezni čelici sadrže veliki broj posebni, takozvani legirajući elementi - volfram, krom, vanadij i kobalt, koji čeliku daju visoka svojstva rezanja - sposobnost održavanja tvrdoće i otpornosti na habanje kada se zagrijava tijekom rezanja na 600-700 °. HSS rezači omogućuju 2-3 puta veće brzine rezanja od karbonskih rezača.
Trenutno se u SSSR-u proizvode sljedeće vrste brzoreznog čelika (GOST 9373-60): R18, R9, R9F5, R14F14, R18F2, R9K5, R9KYU, R10K5F5 i R18K5F2.
Rezači u potpunosti izrađeni od brzoreznog čelika su skupi, stoga se, kako bi se uštedio brzorezni čelik, uglavnom koriste rezači sa zavarenim pločama.
Tvrde legure. Karbidne legure karakteriziraju vrlo visoka tvrdoća i dobra otpornost na habanje.
Tvrde legure izrađuju se u obliku ploča od praha volframa i titana u kombinaciji s ugljikom. Kombinacija ugljika i volframa tzv volfram karbida, a kod titana, titanijev karbid. Kobalt se dodaje kao vezivo. Ova praškasta smjesa se preša pod visokim tlakom kako bi se dobile male ploče, koje se zatim sinteriraju na temperaturi od oko 1500°. Gotovi tanjuri ne zahtijevaju nikakve toplinska obrada. Ploča je zalemljena bakrom na držač rezača izrađen od ugljični čelik ili pričvršćen na njega uz pomoć podešavanja i vijaka (mehaničko pričvršćivanje ploča).
Glavna prednost tvrdih legura leži u činjenici da dobro odolijevaju abraziji padajućim strugotinama i izratkom i ne gube svojstva rezanja čak ni kada se zagrije na 900-1000 °. Zahvaljujući tim svojstvima, rezači opremljeni karbidnim umetcima su najprikladniji za obradu čvrsti metali(tvrdi čelici, uključujući otvrdnute) i nemetalni materijali (staklo, porculan, plastika) pri brzinama rezanja koje su 4-6 puta ili više veće od brzina rezanja koje dopuštaju brzi rezači.
Nedostatak tvrdih legura je povećana lomljivost.
Trenutno se u SSSR-u proizvode dvije skupine tvrdih legura. Glavni su - volfram(VK2, VKZ, VK4, VK6M, VK6, VK8 i VK8M) i titan-volfram(T30K4, T15K6, T14K8, T5K10). Svaka od ovih skupina ima specifičan opseg (tablica 2).
Sve legure volframa namijenjene su za obradu lijevanog željeza, obojenih metala i njihovih legura, kaljenih čelika, nehrđajućih čelika i nemetalnih materijala (ebonit, porculan, staklo itd.). Za obradu čelika koriste se tvrde legure titan-volframove skupine.
Keramički materijali. Nedavno su sovjetski metalurzi stvorili jeftine materijale s visokim svojstvima rezanja, koji u mnogim slučajevima zamjenjuju tvrde legure. To su keramički materijali termokorund), proizveden u obliku ploča bijela boja, koji podsjeća na mramor, koji se poput tvrdih legura ili zalemljuje na držače rezača ili se na njih mehanički pričvršćuje. Ove ploče ne sadrže tako skupe i oskudne elemente kao što su volfram, titan, itd. U isto vrijeme, keramičke ploče imaju veću tvrdoću od tvrdih legura i zadržavaju tvrdoću pri zagrijavanju do 1200 °, što omogućuje rezanje metala s njih sa velike brzine rezanje.
Nedostatak keramičkih ploča je njihova nedovoljna viskoznost. Rezači opremljeni keramičkim umetcima mogu se koristiti za doradu ili poluzavršnu obradu lijevanog željeza, bronce, aluminijskih legura i mekih čelika.
6. Oštrenje i dorada rezača
U tvornicama se oštrenje rezača obično provodi centralizirano na strojevi za mljevenje specijalni radnici. Ali sam tokar mora biti u stanju naoštriti i doraditi glodala.
tablica 2
Svojstva i namjena nekih vrsta tvrdih legura

Oštrenje i dorada brzih glodala provodi se u skladu sa sljedećim pravilima:
1. Brusni kotač ne smije tući, njegova površina treba biti ravna; ako se radna površina kruga razvila, treba je ispraviti.
2. Tijekom oštrenja morate koristiti nasadnik, a ne držati rezač na težini. Ručni dio treba postaviti što bliže brusnom kolu, pod potrebnim kutom i pružiti pouzdanu potporu rezaču (Sl. 50, a-d).
3. Rezač koji se izoštrava mora se pomicati duž radne površine kruga, inače će se neravnomjerno istrošiti.
4. Kako ne biste pregrijali rezač i time izbjegli pojavu pukotina u njemu, nemojte snažno pritiskati rezač na krug.
5. Oštrenje se mora provoditi uz kontinuirano i obilno hlađenje rezača vodom. Nije dopušteno hlađenje kapanjem, kao i periodično uranjanje jako zagrijanog rezača u vodu. Ako kontinuirano hlađenje nije moguće, bolje je prijeći na suho oštrenje.
6. Oštrenje glodala od brzoreznog čelika vršiti elektrokorundnim kotačima srednje tvrdoće i zrnatosti 25-16.
Redoslijed oštrenja rezača postavlja se na sljedeći način. Najprije se izoštrava glavna stražnja površina (slika 50, a). Zatim pomoćna stražnja površina (slika 50, b), zatim prednja površina (slika 50, c) i, konačno, polumjer vrha (slika 50, d).
7. Strogo je zabranjeno oštriti noževe na strojevima sa uklonjenim zaštitnim poklopcem.
8. Prilikom oštrenja obavezno nosite zaštitne naočale.
Nakon oštrenja rezača, na njegovim reznim rubovima ostaju mali zarezi, neravnine i rizici. Eliminiraju se doradom na posebnim strojevima za završnu obradu. Završna obrada se također vrši ručno s finozrnatim brusnim kamenom navlaženim mineralnim uljem. Najprije se laganim pomicanjem kamena podese stražnje plohe, a zatim prednja i polumjer vrha.
Oštrenje i dorada rezača opremljenih umetcima od tvrdog metala. Oštrenje rezača s pločama od tvrdih legura provodi se na strojevima za mljevenje s krugovima zelenog silicijevog karbida. Oštrenje se izvodi kako ručno (slika 50, a-d), tako i pričvršćivanjem sjekutića u držače alata. Redoslijed oštrenja ovih glodala je isti kao i kod rezača izrađenih od brzoreznog čelika, tj. prvo se rezač oštri uz glavnu stražnju stranu (slika 50, a), zatim uz pomoćne stražnje površine (slika 50, b ), zatim duž prednje površine (sl. 50, c) i, na kraju, zaokružite vrh sjekutića (slika 50, d).
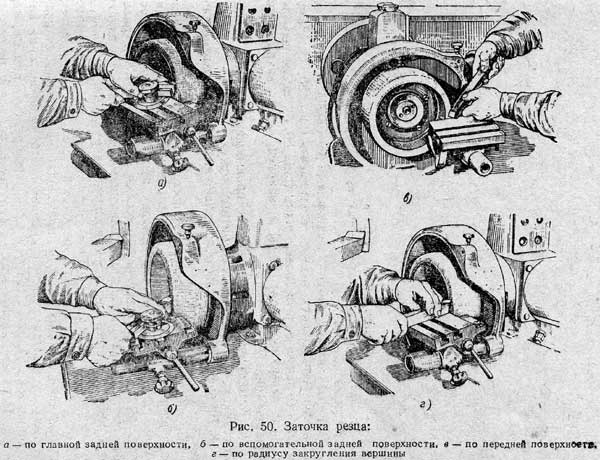
Prethodno oštrenje se izvodi zelenim kotačima od silicij karbida granulacije 50-40, a završno oštrenje granulacije 25-16.
Rezač ne smije biti snažno pritisnut na radnu površinu kruga kako bi se izbjeglo pregrijavanje i pucanje ploče od tvrde legure. Osim toga, mora se stalno pomicati u odnosu na krug; to je neophodno za ravnomjerno trošenje kruga.
Oštrenje se može izvesti i na suho i uz obilno hlađenje rezača vodom.
Nakon oštrenja rezača od tvrdog metala, neophodno je dovršiti njegovu površinu. Završna obrada se vrši ručno ili na stroju za završnu obradu. Ručna završna obrada izvodi se pomoću lijevanog željeza ili bakra, čija se radna površina utrlja posebnom pastom ili prahom borovog karbida pomiješanog sa strojnim uljem ili kerozinom nanosi se na površinu u ravnomjernom sloju. Završna obrada se izvodi na širini od 2-4 mm od reznog ruba.
Produktivnija dorada na posebnom stroju za završnu obradu pomoću diska od lijevanog željeza promjera 250-300 mm, koji se okreće brzinom od 1,5-2 m / s; na površinu ovog diska nanosi se pasta ili prah borovog karbida pomiješan sa strojnim uljem ili kerozinom.
7. Formiranje čipsa
Vrste strugotina. Odvojeni čip pod djelovanjem pritiska rezača uvelike mijenja svoj oblik ili se, kako kažu, deformira: skraćuje duljinu i povećava debljinu. Ovaj fenomen prvi je otkrio prof. I. A. Vrijeme i imenovano skupljanje strugotine.
Izgled strugotine ovisi o mehaničkim svojstvima metala i uvjetima pod kojima dolazi do rezanja. Ako se obrađuju viskozni metali (olovo, kositar, bakar, meki čelik, aluminij, itd.), tada pojedini elementi strugotine, čvrsto prianjajući jedan uz drugi, tvore kontinuiranu strugotinu koja se uvija u traku (Sl. 51, a ). Takav se pramen zove odvod. Prilikom obrade manje viskoznih metala, poput tvrdog čelika, od pojedinačnih elemenata (slika 51, b), slabo povezanih međusobno, nastaju strugotine. Takav se pramen zove usitnjavanje čipsa.
Ako je metal koji se obrađuje krt, kao što je lijevano željezo ili bronca, tada se pojedini elementi strugotine lome i odvajaju od izratka i jedan od drugog (slika 51, c). Takav čip, koji se sastoji od pojedinačnih vage nepravilnog oblika, Zove se slomljeni čips.
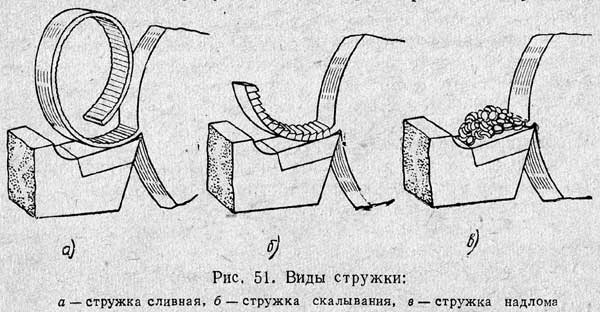
Razmatrane vrste strugotina ne ostaju konstantne, mogu se mijenjati s promjenjivim uvjetima rezanja. Što je metal koji se obrađuje mekši i što je manja debljina strugotine i kut rezanja, oblik strugotine se više približava odvodu. Isto će se primijetiti kada se poveća brzina rezanja i primjenjuje hlađenje. Smanjenjem brzine rezanja, umjesto odvodne strugotine, dobivaju se strugotine.
Izdanak. Ako pregledate prednju površinu rezača koji je korišten za rezanje, tada na reznom rubu ponekad možete pronaći malu grudicu metala zavarenu na rezač pod visokom temperaturom i pritiskom. Ovo je tzv izdanak(Sl. 52). Pojavljuje se pod određenim uvjetima rezanja duktilnih metala, ali se ne opaža pri obradi krhkih metala. Tvrdoća nadogradnje je 2,5-3 puta veća od tvrdoće metala koji se obrađuje; zahvaljujući tome, sama izraslina ima sposobnost rezanja metala od kojeg je nastala.
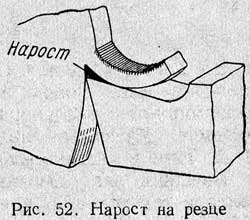
Pozitivna uloga nagomilavanja je u tome što prekriva reznu oštricu, štiteći je od habanja spuštanjem strugotina i djelovanjem topline, a to donekle povećava trajnost rezača. Prisutnost nakupina korisna je pri ljuštenju, budući da se oštrica za rezanje manje zagrijava i njeno trošenje je smanjeno. Međutim, s stvaranjem naslaga, točnost i čistoća obrađene površine se pogoršavaju, budući da nakupljanje iskrivljuje oblik oštrice. Stoga je stvaranje naslaga nepovoljno za završne radove.
8. Koncept elemenata načina rezanja
Za učinkovitije izvođenje obrade u svakom pojedinom slučaju tokar mora poznavati osnovne elemente načina rezanja; ti elementi su dubina rezanja, pomak i brzina rezanja.
Dubina rezanja naziva se udaljenost između obrađene i obrađene površine, mjerena okomito na potonju. Dubina reza je označena slovom t i mjeri se u milimetrima (slika 53).
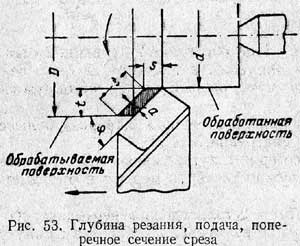
Prilikom okretanja obratka na tokarskom stroju, dodatak za obradu se izrezuje u jednom ili više prolaza.
Za određivanje dubine reza t potrebno je izmjeriti promjer obratka prije i nakon prolaska rezača, pola razlike u promjerima dat će dubinu reza, drugim riječima,
gdje je D promjer dijela u mm prije prolaska rezača; d je promjer dijela u mm nakon prolaska rezača. Kretanje rezača u jednom okretu obratka (slika 53) naziva se podnošenje. Dovod je označen slovom s i mjeri se u milimetrima po okretaju dijela; radi sažetosti uobičajeno je pisati mm / rev. Ovisno o smjeru u kojem se rezač pomiče u odnosu na vodilice okvira, postoje:
a) uzdužni dovod- uz vodilice kreveta;
b) križno napajanje- okomito na vodilice kreveta;
u) kosi feed- pod kutom u odnosu na vodilice kreveta (na primjer, kod okretanja konične površine).
Površina presjeka označen slovom f (eff) i definiran je kao umnožak dubine rezanja pomakom (vidi sliku 53):
Osim dubine rezanja i posmaka, razlikuju i širinu i debljinu rezanog sloja (sl. 53).
Širina sloja rezanja, ili širina čipa, - udaljenost između obrađene i obrađene površine, mjerena duž površine rezanja. Mjeri se u milimetrima i označava se slovom b (be).
Debljina rezanja, ili debljina strugotine, je razmak između dva uzastopna položaja reznog ruba u jednom okretu dijela, mjeren okomito na širinu strugotine. Debljina strugotine mjeri se u milimetrima i označava se slovom a.
S istim posmakom i dubinom reza, kako se glavni kut φ smanjuje, debljina strugotine se smanjuje, a širina joj se povećava. To poboljšava rasipanje topline s reznog ruba i povećava vijek trajanja alata, što zauzvrat omogućuje značajno povećanje brzine rezanja i obradu više dijelova u jedinici vremena. Međutim, smanjenje glavnog kuta u planu φ dovodi do povećanja radijalne (odbojne) sile, koja pri obradi nedovoljno krutih dijelova može uzrokovati njihovo savijanje, gubitak točnosti, ali i jake vibracije. Pojava vibracija, zauzvrat, dovodi do pogoršanja čistoće obrađene površine i često uzrokuje usitnjavanje reznog ruba rezača.
Brzina rezanja. Prilikom obrade na tokarskom stroju, točka A, koja se nalazi na kružnici promjera D (slika 54), u jednom okretu dijela prolazi put jednaku duljini ove kružnice.
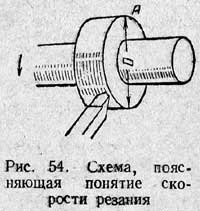
Duljina bilo kojeg kruga je približno 3,14 puta veći od njegovog promjera, stoga je jednaka 3,14 D.
Broj 3.14, koji pokazuje koliko je puta duljina kruga veća od promjera, obično se označava grčkim slovom π (pi).
Točka A u jednom okretu napravit će put jednaku πD. Promjer D dijela, kao i njegov opseg πD, mjeri se u milimetrima.
Pretpostavimo da će radni komad napraviti nekoliko okretaja u minuti. Označimo njihov broj slovom n okretaja u minuti, ili skraćeno o/min. Put koji će proći točka A u ovom slučaju bit će jednak umnošku opsega i broja okretaja u minuti, tj. πDn milimetara u minuti ili skraćeno mm/min, a naziva se obodna brzina.
Put, prohodna točka površina koja se obrađuje pri okretanju u odnosu na rezni rub rezača u jednoj minuti naziva se brzina rezanja.
Budući da se promjer dijela obično izražava u milimetrima, da biste pronašli brzinu rezanja u metrima u minuti, podijelite πDn s 1000. To se može zapisati kao sljedeća formula:
gdje je v brzina rezanja u m/min;
D je promjer obratka u mm;
n je broj okretaja u minuti.
Primjer 3 Promjer obrađenog valjka D = 100 = 150 o/min. Odredite brzinu rezanja.
Odluka: Broj brzina vretena. Prilikom okretanja dijela poznatog promjera može biti potrebno da tokar podesi stroj na toliki broj okretaja vretena kako bi se postigla potrebna brzina rezanja. Za to se koristi sljedeća formula: gdje je D promjer obratka u mm;
Primjer 4 Koliki broj okretaja u minuti treba imati valjak promjera D = 50 mm pri brzini rezanja v = 25 m / min?
Odluka:
9. Osnovni podaci o silama koje djeluju na rezač i snazi rezanja
Sile koje djeluju na rezač. Prilikom uklanjanja strugotina iz obratka, rezač mora prevladati silu prianjanja metalnih čestica jedna na drugu. Kada rezni rub rezača zasiječe u materijal koji se obrađuje i strugotina se odvoji, rezač doživljava pritisak od metala koji se odvaja (Sl. 55).

Od vrha do dna, sila P z pritišće rezač, koji nastoji pritisnuti rezač prema dolje i saviti dio prema gore. Ova sila se zove sila rezanja.
U vodoravnoj ravnini u smjeru suprotnom od pomaka, rezač je pritisnut silom P x, tzv. aksijalna sila, ili sila hrane. Ova sila tijekom uzdužnog okretanja nastoji pritisnuti rezač prema stražnjoj kosi.
U horizontalnoj ravnini, okomito na smjer pomaka, rezač je pritisnut silom P y, koja se naziva radijalna sila. Ova sila teži odgurnuti rezač od obratka i saviti ga u vodoravnom smjeru.
Sve navedene sile mjere se u kilogramima.
Najveća od tri sile je vertikalna sila rezanja: ona je oko 4 puta veća od sile pomaka i 2,5 puta veća od radijalne sile. Sila rezanja opterećuje dijelove mehanizma zaglavlja; također opterećuje rezač, dio, često uzrokujući velika naprezanja u njima.
Eksperimentima je utvrđeno da sila rezanja ovisi o svojstvima materijala koji se obrađuje, veličini i obliku dijela strugotine koja se uklanja, obliku rezača, brzini rezanja i hlađenju.
Za karakterizaciju otpora raznih materijala cutting uspostavio koncept koeficijenta rezanja. Faktor rezanja K je pritisak rezanja u kilogramima po kvadratnom milimetru rezanog dijela, mjeren pod određenim uvjetima rezanja:
Dubina reza t............5 mm
Pomak s......................1 mm/okr
Nagibni kut γ......................15°
Vodeći kut φ.......45°
Rezni rub rezača - pravolinijski, vodoravni
Vrh rezača je zaobljen s polumjerom r = 1 mm
Rad se obavlja bez hlađenja
U tablici. 3 prikazuje prosječne vrijednosti faktora rezanja za neke metale.
Tablica 3
Prosječne vrijednosti faktora rezanja K pri okretanju
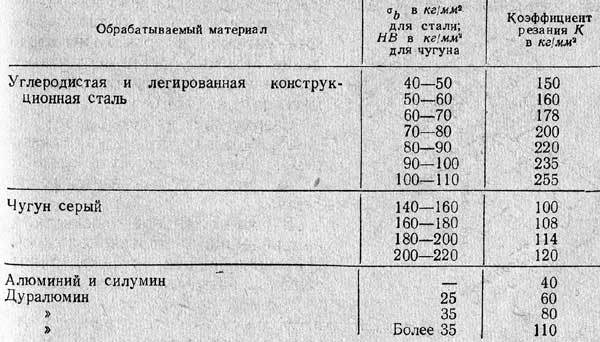
Ako je poznat faktor rezanja K, onda množenjem s površinom poprečnog presjeka f u mm 2, možete pronaći približnu vrijednost sile rezanja pomoću formule
P z \u003d Kf kg. (osam)
Primjer 5 Osovina izrađena od strojno izrađenog čelika s σ b \u003d 60 kg / mm 2 okreće se na tokarskom stroju. Odredite silu rezanja ako je dubina reza t = 5 mm i posmak s = 0,5 mm/obr.
Odluka. Prema formuli (8), sila rezanja P z \u003d Kf kg. (osam) Određujemo vrijednost f: f \u003d ts \u003d 5x0,5 \u003d 2,5 mm 2. Prema tablici 3 nalazimo vrijednost K za strojno izrađen čelik s σ b = 60 kg / mm 2: K = 160 kg / mm 2. Dakle, z = Kf = 160x2,5 = 400 kg. snaga rezanja. Poznavajući silu rezanja i brzinu rezanja, možete saznati koliko je snage potrebno za rezanje strugotina određenog presjeka.
Snaga rezanja određena je formulom (9) gdje je N res - snaga rezanja u KS;
P z - sila rezanja u kg;
v - brzina rezanja u m/min.
Snaga elektromotora alatnog stroja trebala bi biti nešto veća od snage rezanja, jer se dio snage elektromotora troši na prevladavanje trenja u mehanizmima koji prenose kretanje s elektromotora na vreteno stroja.
Primjer 6 Odrediti snagu rezanja za okretanje osovine, razmatranu u prethodnom primjeru, ako se obrada provodi pri brzini rezanja, υ = 60 m/min. Odluka . Prema formuli (9), snaga rezanja
Snaga rezanja obično se ne izražava u konjskim snagama, već u kilovatima (kW). Kilovat je 1,36 konjskih snaga, pa da biste snagu izrazili u kilovatima, trebate podijeliti konjsku snagu s 1,36:
i obrnuto,
10. Toplina rezanja i vijek trajanja alata
S povećanjem sile rezanja raste i sila trenja, zbog čega se povećava količina topline koja se oslobađa tijekom procesa rezanja. Toplina rezanja se još više povećava kako se brzina rezanja povećava, jer se time ubrzava cijeli proces stvaranja strugotine.
Nastala toplina rezanja uz nedovoljno uklanjanje iste omekšava rezač, zbog čega dolazi do intenzivnijeg trošenja njegovog reznog dijela. Zbog toga je potrebno promijeniti rezač ili ga naoštriti i ponovno instalirati.
Vrijeme neprekidnog rada rezača prije otupljenja naziva se vijek trajanja alata (mjereno u minutama). Uzroci česte promjene rezača (kratak vijek trajanja alata). dodatni troškovi za oštrenje i ugradnju rezača, kao i za dopunu istrošenih rezača.
Stoga je vijek trajanja alata važan čimbenik pri odabiru uvjeta rezanja, posebno pri odabiru brzine rezanja.
Trajnost rezača prvenstveno ovisi o kvalitetama materijala od kojeg je izrađen. Najotporniji će biti rezač koji je izrađen od materijala koji omogućuje najvišu temperaturu zagrijavanja bez značajnog gubitka tvrdoće. Rezači opremljeni pločama od tvrde legure, mineralno-keramičkim pločama imaju najveći otpor; znatno manji otpor - rezači od brzoreznog čelika, najmanji - rezači od ugljičnog alatnog čelika.
Otpor rezača također ovisi o svojstvima materijala koji se obrađuje, presjeku reza, kutovima oštrenja rezača i brzini rezanja. Povećanje tvrdoće materijala koji se obrađuje smanjuje vijek trajanja alata.
Promjenom kutova oštrenja i oblika prednje površine moguće je postići značajno povećanje trajnosti rezača i njihove izvedbe.
Brzina rezanja posebno snažno utječe na vijek trajanja alata. Ponekad čak i najmanje povećanje brzine dovodi do brzog otupljivanja rezača. Na primjer, ako se pri obradi čelika brzim rezačem brzina rezanja poveća za samo 10%, tj. 1,1 puta, rezač će postati tup dvostruko brže i obrnuto.
S povećanjem površine poprečnog presjeka reza, vijek trajanja alata se smanjuje, ali ne toliko kao s istim povećanjem brzine rezanja.
Vijek trajanja alata također ovisi o veličini alata, obliku rezanog dijela i hlađenju. Što je rezač masivniji, to bolje uklanja toplinu s oštrice i, posljedično, veća je njegova trajnost.
Eksperimenti pokazuju da s istim presjekom rezanja, velika dubina reza i manji posmak osiguravaju veći vijek trajanja alata nego manja dubina rezanja s odgovarajućim većim posmakom. To se objašnjava činjenicom da s većom dubinom reza, strugotine dolaze u dodir s većom duljinom reznog ruba, pa se toplina rezanja bolje uklanja. Zato je s istim reznim presjekom isplativije raditi s većom dubinom nego s većim posmakom.
Trajnost rezača značajno se povećava kada se ohladi.
Rashladna tekućina mora biti opskrbljena obiljem (emulzija 10-12 l/min, ulje i sulfofresol 3-4 l/min); mala količina tekućine ne samo da nema koristi, već čak i pokvari rezač, uzrokujući pojavu malih pukotina na njegovoj površini, što dovodi do usitnjavanja.
11. Izbor brzine rezanja
Produktivnost rada ovisi o izboru brzine rezanja: što je veća brzina rezanja, to je veća manje vremena potrošeno na obradu. Međutim, s povećanjem brzine rezanja, vijek trajanja alata se smanjuje, stoga na izbor brzine rezanja utječe vijek trajanja alata i svi čimbenici koji utječu na vijek trajanja alata. Od toga su najvažnija svojstva materijala koji se obrađuje, kvaliteta materijala rezača, dubina rezanja, posmak, dimenzije rezača i kutovi oštrenja te hlađenje.
1. Što dulji vijek trajanja alata treba biti, to treba odabrati nižu brzinu rezanja i obrnuto.
2. Što je materijal koji se obrađuje tvrđi, to je kraći vijek trajanja alata, stoga, kako bi se osigurala potrebna otpornost pri obradi tvrdih materijala, treba smanjiti brzinu rezanja. Kod obrade lijevanih i kovanih obradaka, na čijoj se površini nalazi tvrda kora, školjke ili ljuska, potrebno je smanjiti brzinu rezanja u odnosu na onu koja je moguća kod obrade materijala bez kore.
3. Svojstva materijala rezača određuju njegovu trajnost, stoga izbor brzine rezanja također ovisi o tim svojstvima. Pod ostalim jednakim uvjetima, brzorezni čelični rezači omogućuju znatno veću brzinu rezanja od rezača od ugljičnog čelika; čak i veće brzine rezanja omogućuju rezače opremljene tvrdim legurama.
4. Kako bi se povećao otpor rezača pri obradi viskoznih metala, poželjno je koristiti hlađenje rezača. U tom slučaju, uz isti vijek trajanja alata, moguće je povećati brzinu rezanja za 15-25% u odnosu na strojnu obradu bez hlađenja.
5. Dimenzije rezača i kutovi njegovog oštrenja također utječu na dopuštenu brzinu rezanja: što je rezač masivniji, posebno njegova glava, to bolje uklanja toplinu koja nastaje tijekom rezanja. Nepravilno odabrani kutovi rezača koji ne odgovaraju materijalu koji se obrađuje povećavaju silu rezanja i pridonose bržem trošenju rezača.
6. S povećanjem presjeka rezanja smanjuje se vijek trajanja alata, stoga je kod većeg presjeka potrebno odabrati nižu brzinu rezanja nego kod manjeg presjeka.
Budući da se sitna strugotina uklanja tijekom završne obrade, brzina rezanja tijekom dorade može biti mnogo veća nego tijekom grube obrade.
Budući da povećanje presjeka ima manji učinak na vijek trajanja alata nego povećanje brzine rezanja, korisno je povećati rezni dio blagim smanjenjem brzine rezanja. Metoda obrade inovatora tokara Kuibyshevske tvornice alatnih strojeva V. Kolesova temelji se na ovom principu. Radeći pri brzini rezanja od 150 m/min, T. Kolesov dorađuje čelične dijelove s posmakom do 3 mm/okr umjesto 0,3 mm/okr, što dovodi do smanjenja vremena stroja za 8-10 puta.
Postavlja se pitanje: zašto napredni tokari često povećavaju produktivnost rada povećanjem brzine rezanja? Nije li to u suprotnosti s osnovnim zakonima rezanja? Ne, nije u suprotnosti. Oni povećavaju brzinu rezanja samo u slučajevima kada se u potpunosti koriste mogućnosti povećanja presjeka reza.
Kada se izvodi poluzavršna ili završna obrada, gdje je dubina reza ograničena malim dodatkom obrade, a pomak je ograničen zahtjevima visoke završne obrade, povećanje podataka rezanja moguće je povećanjem brzine rezanja. . To rade napredni tokari, radeći na poluzavršnoj i završnoj obradi. Ako je moguće raditi s veliki dijelovi rez (s velikim dopuštenjima), tada je, prije svega, potrebno odabrati najveću moguću dubinu rezanja, zatim najveći mogući tehnološki dopušteni pomak i, na kraju, odgovarajuću brzinu rezanja.
U slučajevima kada je dopuštena obrada mala i ne postoje posebni zahtjevi za završnu obradu površine, način rezanja treba povećati korištenjem najvećeg mogućeg posmaka.
12. Čistoća obrađene površine
Kod obrade rezačem na obrađenoj površini dijela uvijek ostaju nepravilnosti u obliku udubljenja i udubljenja, čak i kod najpažljivije obrade. Visina hrapavosti ovisi o načinu obrade.
Praksa je utvrdila da što je površina dijela čišća obrađena, to je manje podložna habanju i koroziji, a dio je jači.
Pažljiva obrada površine pri strojnoj obradi dijela uvijek je skuplja od grube završne obrade. Stoga, čistoću obrađene površine treba dodijeliti ovisno o radnim uvjetima dijela.
Označavanje čistoće površine na crtežima. Prema GOST 2789-59, predviđeno je 14 klasa čistoće površine. Za označavanje svih razreda čistoće uspostavljen je jedan znak - jednakostranični trokut, pored kojeg je naznačen broj klase (na primjer, 7; 8; 14). Najčišće površine imaju ocjenu 14, a najhrapavije 1.
Hrapavost površine prema GOST 2789-59 određena je jednim od dva parametra: a) srednjim aritmetičkim odstupanjem profila R a i b) visinom neravnina R z.
Za mjerenje hrapavosti i dodjeljivanje obrađene površine određenoj klasi, specijal mjerni instrumenti na temelju metode opipavanja površinskog profila tankom dijamantnom iglom. Takvi uređaji nazivaju se profilometri i profilografi.
Za određivanje hrapavosti i razvrstavanje obrađene površine u jednu ili drugu klasu čistoće u radioničkim uvjetima koriste se ispitani uzorci različitih klasa čistoće - takozvani standardi čistoće, s kojima se uspoređuje obrađena površina dijela.
Čimbenici koji utječu na završnu obradu površine. Praksa je utvrdila da čistoća obrađene površine ovisi o više razloga: materijalu koji se obrađuje, materijalu rezača, kutovima oštrenja i stanju reznih rubova rezača, pomaku i brzini rezanja, podmazivanju i svojstva hlađenja tekućine, krutost sustava stroj - rezač - dio itd.
posebno važnost da dobijete površinu Visoka kvaliteta kod tokarenja ima brzinu rezanja, pomak, nagibe i polumjer zakrivljenosti vrha alata. Što je manji pomak i kut ulaska i veći radijus kuta, to je obrađena površina čišća. Brzina rezanja uvelike utječe na završnu obradu površine. Kod tokarenja čelika brzinom rezanja većom od 100 m/min, obrađena površina je čišća nego pri brzini od 25-30 m/min.
Da bi se dobila čišća obrađena površina, treba obratiti pozornost na pažljivo oštrenje i završnu obradu reznih rubova.
test pitanja 1. Kakvog oblika nastaje strugotina pri strojnoj obradi viskoznih metala? Prilikom obrade krhkih metala?
2. Navedite glavne elemente glave sjekutića.
3. Pokažite prednju i stražnju plohu na sjekutiću; prednji i stražnji kutovi; kut oštrenja.
4. Koja je svrha prednjeg i stražnjeg kuta sjekutića?
5. Prikažite vodeći kut i vodeći kut.
6. Od kojih materijala se izrađuju rezači?
7. Koje se vrste tvrdih legura koriste u preradi čelika? Prilikom obrade lijevanog željeza?
8. Navedite elemente načina rezanja.
9. Koje sile djeluju na rezač?
10. Koji čimbenici i kako utječu na veličinu sile rezanja?
11. Što određuje trajnost rezača?
12. Koji čimbenici utječu na izbor brzine rezanja?
Glavni alati za rezanje koji se koriste u procesu uključuju rezač, čiji geometrijski parametri određuju njegove tehničke mogućnosti, točnost i učinkovitost obrade. Svaki stručnjak koji se odluči posvetiti okretanje poslovanja, Ukoliko pravi izbor kutovi reznog ruba povećavaju vijek trajanja alata i produktivnost.
Parametri alata za tokarenje
Bilo koji alat za tokarenje formiraju držač neophodan za fiksiranje alata u držač tokarilica, te radna glava koja omogućuje rezanje metala. Da bismo uzeli u obzir geometrijske parametre alata za tokarenje, bolje je uzeti prolazni alat kao uzorak.
Na reznom dijelu alata za tokarenje ovog tipa postoje tri površine:
- prednji dio (na njemu se tijekom obrade obratka skidaju metalne strugotine);
- stražnji - glavni i pomoćni (oba okrenuta prednjim dijelom prema izratku).
Rub alata, nazvan rezni rub (i izravno uključen u obradu), nastaje sjecištem njegove prednje i glavne stražnje površine. U geometriji alata za tokarenje izdvaja se i pomoćni rezni rub. On, odnosno, nastaje sjecištem prednje površine s pomoćnim stražnjim.
Točka u kojoj se sijeku glavni i sekundarni rezni rub naziva se vrh rezača. Potonji, prilikom rezanja metala, doživljava ogromna opterećenja, što dovodi do njegovog loma. Da bi se povećao otpor vrha rezača, on se tijekom procesa oštrenja ne oštri, već lagano zaokružuje. To zahtijeva uvođenje parametra kao što je radijus vrha. Postoji još jedan način povećanja otpora vrha alata za tokarenje - formiranje prijelaznog reznog ruba koji ima pravocrtni oblik.
Najvažniji geometrijski parametri glodala za tokarenje su njihovi kutovi koji određuju međusobnog dogovora površine alata. Parametri kuta variraju ovisno o vrsti alata za tokarenje i brojnim drugim čimbenicima:
- materijal alata;
- njegove radne uvjete;
- karakteristike materijala koji se obrađuje.
Kutovi alata za okretanje
Za ispravno određivanje kutova alat za tokarenje, njih točne vrijednosti, oni se razmatraju u tzv. početnim ravninama.
- Glavna ravnina je paralelna sa smjerovima pomaka alata za tokarenje (uzdužno i poprečno) i podudara se s njegovom nosivom površinom.
- Rezna ravnina uključuje glavni rezni rub i tangencijalna je na površinu obrade. Ova je ravnina okomita na glavnu.
- Glavna rezna ravnina siječe glavni rezni rub i nalazi se okomito na projekciju koju ovaj rub polaže na glavnu ravninu. Postoji i pomoćna sekantna ravnina, koja je, prema tome, okomita na projekciju koju na glavnu ravninu nanosi pomoćni rezni rub.
Kao što je gore spomenuto, one se mjere upravo u tim ravninama, a one koje se mjere u ravnini koja se naziva glavna sekanta označavaju se kao glavne. To su, posebno, glavni prednji, glavni stražnji kutovi, kao i kutovi oštrenja i rezanja.
Jedan od najvažnijih je glavni zazorni kut alata za okretanje, koji minimizira trenje koje nastaje kada stražnja površina alata stupi u interakciju s dijelom koji se trenutno obrađuje (i stoga smanjuje zagrijavanje alata i produljuje njegov vijek trajanja ). Ovaj kut tvore površina rezača (glavna stražnja strana) i rezna ravnina. Prilikom odabira ovog kuta prilikom oštrenja alata uzimaju se u obzir vrsta obrade i materijal izratka. U tom slučaju trebate biti svjesni da snažno povećanje veličine kuta zazora dovodi do brzog kvara alata za okretanje.
Čvrstoća i izdržljivost alata za rezanje, sile koje se javljaju tijekom obrade određuju se parametrima nagibnog kuta. Nalazi se između prednje površine alata za tokarenje i ravnine u kojoj se nalazi glavni rezni rub (ova ravnina je okomita na ravninu rezanja). Prilikom oštrenja alata za okretanje uzimaju se u obzir brojni čimbenici koji utječu na vrijednost ovog kuta:
- materijal izratka i sam alat;
- oblik prednje površine;
- uvjetima pod kojima će se rezač koristiti.
Povećanje vrijednosti nagibnog kuta, s jedne strane, poboljšava završetak obrade, a s druge strane izaziva smanjenje čvrstoće i trajnosti alata za tokarenje. Takav kut, dobiven kao rezultat izoštravanja, može imati pozitivan i negativno značenje.
Rezači za tokarenje s nagibnim kutovima koji imaju negativne vrijednosti vrlo su izdržljivi, ali je obrada takvim alatima teška. Obično se oštrenje pod nagibnim kutom, koji ima pozitivnu vrijednost, koristi kada se izradak treba obraditi od viskoznog materijala, a također i kada je materijal alata vrlo izdržljiv.
Rezači s negativnim nagibnim kutovima koriste se pri obradi materijala velike tvrdoće i čvrstoće, kod izvođenja prekinutog rezanja, kada materijal alata nema dovoljnu čvrstoću na savijanje i ne apsorbira dobro udarna opterećenja.
Parametri koji karakteriziraju geometriju glodala za tokarenje su također kutovi rezanja i usmjeravanja. Kut rezanja, čija vrijednost može varirati unutar 60-100 0, nalazi se između površine alata, koja se naziva prednja strana, i ravnine rezanja.
Vrijednost ovog kuta izravno ovisi o tvrdoći metala koji se obrađuje: što je veća, to je veća njegova vrijednost. Kut konusa u potpunosti je u skladu s njegovim imenom, mjeri se između glavne prednje i glavne stražnje površine alata i karakterizira stupanj izoštravanja njegovog vrha.
Okarakterizirajte alat za tokarenje i kutove u planu. Ovo je glavno, mjereno između smjera uzdužnog pomaka i projekcije koju glavni rezni rub polaže na glavnu ravninu, i pomoćno, formirano projekcijom pomoćnog reznog ruba na glavnu ravninu i smjerom uzdužni dovod.
Prilikom oštrenja ovi kutovi se ne biraju proizvoljno, već ovisno o vrsti tokarenja i krutosti koju ima sustav „stroj-alat-obradak”. Dakle, obrada većine metala može se izvesti alatima s glavnim kutom u planu jednakim 45 0, ali tanke i dugačke izratke treba obraditi rezačima, u kojima je vrijednost ovog kuta u rasponu od 60– 90 0 . To je potrebno kako bi se uklonilo otklon i drhtanje dijela.
Pomoćni kut u vodi istovremeno korelira sa završnom obradom i sa vijekom trajanja alata. Njegovim smanjenjem povećava se čistoća obrade i produljuje vijek trajanja alata.
Osim gore navedenih, u geometriji alata za tokarenje razlikuju se kutovi.
Uzdužno tokarenje naziva se tokarenje, u kojem je smjer kretanja posmaka paralelan s osi obratka. Na tokarskim strojevima, gibanje rezanja - rotacija - pričvršćeno je na radni komad, a gibanje pomaka - translacijsko kretanje - na rezač. Na strojevima s okruglim štapićem, alat za rezanje se rotira, a kretanje pomaka je pričvršćeno na radni komad. Prava putanja rezanja je spiralna linija.
Razlikovati fino i grubo tokarenje.
Fino tokarenje (slika 2, a) izvodi se rezačem s ravnim radnim površinama i ravnim reznim rubovima - glavnim i pomoćnim. Položaj reznih rubova u odnosu na os rotacije obratka karakteriziran je glavnim kutom u vodi i pomoćnim kutom u vodi. Vrijednost pomoćnog kuta u planu određuje dubinu kinematičkih nepravilnosti, pa ne može biti veća. Položaj lica koja tvore glavni rezni rub karakteriziraju zazorni kut, kut oštrenja i nagibni kut.
Glavni rezni rub proizvodi poprečno rezanje, karakteriziran kutom nagiba drvenih vlakana.
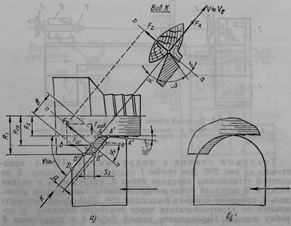
Riža. 2. Završna obrada uzdužnog tokarenja (a) i gruba obrada (b)
Kut nagiba mjeri se između smjera vlakana i normale.
Grubo tokarenje (slika 2, b) izvodi se žljebljenim rezačima s polukružnim reznim rubom. Poprečni presjek strugotine su srpaste, debljina strugotine na periferiji obratka je maksimalna, a blizu površine dijela je neznatna čak i pri velikom pomaku na rezač. To vam omogućuje da primijenite pomak po rezaču do 2 mm, dok za fino tokarenje - ne više od 0,8 mm.
> Postavljanje tokarilica
Prilikom postavljanja tokarilica potrebno je: odabrati rezač i učvrstiti ga u držač alata (kod strojeva s mehaničkim uvlačenjem); ugradite prednju ploču ili steznu glavu; odaberite i pričvrstite naslon za ruke (za strojeve s ručno hranjenje) ili ravnalo za kopiranje (za strojeve s mehaničkim uvlačenjem); ugradite i učvrstite obradak u stroju; testirati stroj u praznom hodu; postavite brzinu vretena i brzinu posmaka; obraditi i pregledati ispitne komade.
Potrebni rezač odabire se ovisno o prirodi obavljenog posla. Za početnu grubu obradu koristi se rezač za ljuštenje, za završno rezač za završnu obradu s ravnim reznim rubom. S mehaničkim pomakom, rezač se učvršćuje u držač alata vijcima. Kako bi se smanjilo vrijeme promjene, koriste se posebne rotacijske glave, gdje se istovremeno ojačava nekoliko sjekutića za različite namjene.
Na ručni rad potrebno je provjeriti pouzdanost pričvršćivanja rezača na drvenu ručku. Nemojte koristiti neispravan alat za rezanje.
Sredstva za pričvršćivanje izratka odabiru se ovisno o njegovom obliku i veličini. Za pričvršćivanje dugih obratka (slika 3, a) koriste se prednji i stražnji centri. Prednji centar 2 izrađen je u obliku trokrakog povodca sa suženim drškom, kojim se uvlači u suženu rupu vretena 1. Stražnji centar 4 ima konusni i šiljasti dio i pričvršćen je u pero 5 stražnjeg nosača 6. Da bi se smanjilo trenje i povećala pouzdanost pričvršćivanja izratka, stražnji centar je postavljen na ležaj, koji osigurava njegovu rotaciju s izratkom 3.

Riža. 3. Pričvršćivanje obratka u tokarilicama: a - u središtima, b - u steznoj glavi, c - na prednjoj ploči; 1 - vreteno, 2 - prednja sredina, 3 - izradak, 4 - stražnja sredina, 5 - pero, 6 - stražnji dio, 7 - stezna glava, 8 - plan
Ovisno o duljini izratka koji se obrađuje, stražnji dio se pomiče duž vodilica ležaja i fiksira u unaprijed određenom položaju. Radni komad se fiksira guranjem pera iz glave sve dok se središta ne ugrade u krajeve izratka i sigurno će ga držati tijekom rotacije. Za okretanje konusnih dijelova, tijelo stražnje letve treba pomaknuti poprečno pomoću vijka za podešavanje i učvrstiti uređajem za zaključavanje. Stezne glave su dizajnirane za pričvršćivanje kratkih obradaka (slika 3, b). Stezna glava 7 ima navoj kroz koji se uvija na vreteno. Radni komad se učvršćuje u steznu glavu tako da se njegov kraj čvrsto uklopi u otvor stezne glave. Također se koriste stezne glave i stezne glave s kliznim čeljustima.
Za stezanje izradaka kratke duljine i veliki promjer služe kao prednje ploče 8 (slika 3, c), pričvršćene na vreteno. Radni komad je pričvršćen na prednju ploču vijcima ili vijcima 9.
Ručni dio je postavljen na okvir tako da je njegov radni rub na razini središta i blizu generatrikse izratka koji se obrađuje, ali ga ne dodiruje. Kako se promjer smanjuje i kada se obrađuju dugi izratci, ručni dio se uzastopno preuređuje u novi položaj duž vodilica ležaja. Prilikom obrade oblikovanih proizvoda na stražnjoj strani kreveta, ravnalo za kopiranje je pričvršćeno na zagrade, čiji je oblik sličan obliku gotovog dijela. Kada je napajanje uključeno, čeljust se pomiče duž zakrivljene staze i rezač reproducira zadani oblik dijela.
Brzina vretena odabire se ovisno o promjeru obratka i njegovoj čvrstoći. Za veće promjere treba postaviti minimalnu brzinu vretena. Prilikom ugradnje prednje ploče promjera 400 mm, brzina vretena ne smije prelaziti 800 o/min. Brzina vrtnje se smanjuje pomoću ručke za prebacivanje para stupnjeva prijenosa ili promjenom brzine vrtnje višebrzinskog elektromotora. brzina rezanja za drvo meke stijene treba biti 10 ... 12 m / s, čvrsta - 0,5 ... 3 m / s.
Uzdužni pomak po okretaju vretena trebao bi biti: za grubu obradu 1,6 ... 2 mm, za završnu obradu - ne više od 0,8 mm. Što su zahtjevi za hrapavošću površine veći, to bi uzdužni pomak trebao biti manji. Poprečni pomak po okretaju vretena ne smije biti veći od 1,2 mm. Prije pokretanja stroja uvjerite se u to pouzdano pričvršćivanje praznine i ugradite ogradu.
Nakon grube obrade dijela, rezač se mijenja i fino tokarenje se izvodi pri malom posmaku. Čipovi u ovom slučaju trebaju biti što je moguće kontinuiraniji i ujednačene debljine.
Tijekom obrade, oblik dijela se povremeno kontrolira šablonom ili mjeračem. Kada koristite kalibar ili mjerni alat s vagom se stroj isključuje i tek nakon što se dio potpuno zaustavi, mjeri se.
Nakon završetka podešavanja, provodi se probna obrada dijela i njegove dimenzije se kontroliraju kalibrom ili mjernim alatom sa skalom.