Сталь 20 держстандарт 1050 88 механічні властивості
Сталь - рукотворний сплав заліза і вуглецю - користується сьогодні постійним попитом у різних галузях промисловості. Без нього важко зводити міста, монтувати трубопроводи, виробляти транспорт, техніку, різноманітні агрегати та деталі.
Частка заліза в сталевому сплаві має становити щонайменше 45 %. Від вмісту вуглецю та легуючих елементів залежать усі властивості сталі, а в результаті, та отриманих з неї виробів металопрокату.
Одна з найбільш затребуваних марок сировини - сталь 45. Характеристики та властивості визначають її популярність на ринку металопрокату. Належить вона до розряду конструкційних вуглецевих якісних сталей.
Розшифровка та хімічний склад
Наявність числа 45 у назві марки сировини "повідомляє" про вміст близько 0,45% вуглецю (C). Інші «інгредієнти» розподілилися таким чином: кремній (Si) – від 0,17 – до 0,37, хром (Cr) – до 0,25, марганець (Mn) – 0,5 – 0,8, нікель (Ni) - до 0,25, мідь (Cu) – до 0,25, фосфор (P) – до 0,035, сірка (S) – до 0,04, миш'як (As) – 0,08.
Деякі фізичні та технологічні характеристики
- Вага (питома): 7826 кг/м3.
- Твердість сталі 45: HB = 50 HRC (після загартування).
- Температура кування: від 1250 до 700 про З подальшим охолодженням на повітрі (для деталей, переріз яких варіюється до 400 мм).
- Токарна обробка рекомендується у гарячекатаному стані.
- Варіанти зварювання: РДС, КТЗ (при підігріві). Потрібна подальша термообробка.
- Флокеночутливість: низька
- Схильність до крихкості при відпустці: відсутня.
Механічні та Фізичні властивостіможна подивитися у таблиці:
Особливості стали марки 45
Сталь 45 відрізняється підвищеними характеристиками міцності, витривалості, добре обробляється, доступна за вартістю. Знайшла застосування практично у всіх галузях промисловості, там, де мають місце постійні механічні навантаження, складні температурні умови. Вироби із сталі 45, наприклад, вкрай затребуване коло, витримують перепади в діапазоні від 200 до 600 С.
Якщо порівняти деякі характеристики сировини марки 45 і, наприклад, марки 35, стає очевидним вплив частки вуглецю у складі сплаву. Так, 0,42 – 0,5% проти 0,32 – 0,4% (відповідно) вказує на підвищені характеристики твердості сталі 45.
Якщо ст 35 класифікується як обмежена, то сталь 45 (ГОСТ 1050-88) - вариться дуже важко. Це, мабуть, є першим із «недоліків» останньої. Другий - схильність до корозії через присутність нікелю і хрому.
Сортовий прокат, включаючи фасонний, виготовляють за суворими вимогами ГОСТів: 1050-88, 10702-78, 2590-2006 та 2591-2006, 2879-2006, 8509-93 та 8510-86
- Для виготовлення каліброваного прутка необхідно дотримуватися вимог стандартів 1050-88, 8559-75 та 8560-78, 7417-75,
- листового прокату: товстого (ГОСТи 1577-93, 19903-74), тонкого - ГОСТ 16523-97,
- смуги (ГОСТи 103-2006, 1577-93, 82-70),
- шліфованого прутка - ГОСТ 14955-77,
- стрічки із сталі 45 - ГОСТ 2284-79,
- кованих заготовок - ГОСТи 8479-70, 1133-71,
- труб - стандарти 8732-78, 8731-74, 8733-74, 8734-75, а також 21729-76,
- дроту – ГОСТи 17305-91, 5663-79.
Забезпечують тривалу працездатність ланцюгового приводу.
Хімічний склад сталі.
Хоча основною часткою у складі Сталі 45 має залізо (Fe) – до 97%, але визначальним показником марки є вуглець (C), його частка становить 0,42 – 0,5%. Саме це число позначається у маркуванні сталі. Наведемо повний хімічний склад:
- залізо (Fe) – до 97%;
- вуглець (С) – від 0,42 до 0,5%;
- кремній (Si) – від 0,17 до 0,37%;
- хром (Cr) – до 0,25%;
- марганець (Mn) – 0,5 – 0,8%;
- нікель (Ni) – до 0,25%;
- мідь (Cu) – до 0,25%;
- фосфор (P) – до 0,035%;
- сірка (S) – до 0,04%;
- миш'як (As) – 0,08.
Малий процентний вміст хрому та нікелю визначає схильність виробів із Сталі 45 корозії, що необхідно враховувати при технічне обслуговуваннята змащуванні редукторів та ланцюгових зірочок.
Сталь 45 ГОСТ.
Сталь 45 застосовується як заготовка для найрізноманітніших виробів. Залежно від форми весь металопрокат регламентується ГОСТами. Докладніше:
- Сортовий прокат, у тому числі фасонний - ГОСТ 1050-74, ГОСТ 2590-71, ГОСТ 2591-71, ГОСТ 2879-69, ГОСТ 8509-86, ГОСТ 8510-86, ГОСТ 8239-72, ГОСТ 8240 -78.
- Калібрований пруток ГОСТ 1050-74, ГОСТ 7414-75, ГОСТ 8559-75, ГОСТ 8560-78, ГОСТ 10702-78.
- Лист товстий ГОСТ 1577-81, ГОСТ 19903-74.
- Лист тонкий ГОСТ 16523-70.
- Стрічка ГОСТ 2284-79.
- Смуга ГОСТ 1577-81, ГОСТ 103-76, ГОСТ 82-70.
- Дріт ГОСТ 17305-71, ГОСТ 5663-79.
- Кування та ковані заготівлі ГОСТ 8479-70, ГОСТ 1131-71.
- Труби ГОСТ 8732-78, ГОСТ 8733-87, ГОСТ 8734-75, ГОСТ 8731-87, ГОСТ 21729-78.
Сталь 45. Механічні характеристики.
Механічні характеристики при підвищених температурах
t випробування, °C | s0,2, МПа | sB, МПа | d5, % | d, % | y, % | KCU, Дж/м2 |
Нормалізація | ||||||
200 | 340 | 690 | 10 | 36 | 64 | |
300 | 255 | 710 | 22 | 44 | 66 | |
400 | 225 | 560 | 21 | 65 | 55 | |
500 | 175 | 370 | 23 | 67 | 39 | |
600 | 78 | 215 | 33 | 90 | 59 | |
Зразок діаметром 6 мм та довжиною 30 мм, кований та нормалізований. Швидкість деформування 16 мм/хв. Швидкість деформації 0,0091/с. | ||||||
700 | 140 | 170 | 43 | 96 | ||
800 | 64 | 110 | 58 | 98 | ||
900 | 54 | 76 | 62 | 100 | ||
1000 | 34 | 50 | 72 | 100 | ||
1100 | 22 | 34 | 81 | 100 | ||
1200 | 15 | 27 | 90 | 100 |
Механічні властивості прокату
Термообробка, стан постачання | Перетин, мм | sB, МПа | d5, % | d4, % | y, % |
Сталь гарячекатана, кована, калібрована та сріблянка 2-ї категорії після нормалізації | 25 | 600 | 16 | 40 | |
Сталь калібрована 5-ї категорії після нагартовки | 640 | 6 | 30 | ||
Сталь калібрована та калібрована зі спеціальним оздобленням після відпустки або відпалу | <590 | 40 | |||
Листи нормалізовані та гарячекатані | 80 | 590 | 18 | ||
Смуги нормалізовані або гарячекатані | 6-25 | 600 | 16 | 40 | |
Лист гарячекатаний | <2 | 550-690 | 14 | ||
Лист гарячекатаний | 2-3,9 | 550-690 | 15 | ||
Лист холоднокатаний | <2 | 550-690 | 15 | ||
Лист холоднокатаний | 2-3,9 | 550-690 | 16 |
Механічні властивості поковок
Перетин, мм | s0,2, МПа | sB, МПа | d5, % | y, % | HB |
Нормалізація | |||||
100-300 | 245 | 470 | 19 | 42 | 143-179 |
300-500 | 245 | 470 | 17 | 35 | 143-179 |
500-800 | 245 | 470 | 15 | 30 | 143-179 |
<100 | 275 | 530 | 20 | 44 | 156-197 |
100-300 | 275 | 530 | 17 | 34 | 156-197 |
Загартування. Відпустка | |||||
300-500 | 275 | 530 | 15 | 29 | 156-197 |
Нормалізація. Загартування. Відпустка. | |||||
<100 | 315 | 570 | 17 | 39 | 167-207 |
100-300 | 315 | 570 | 14 | 34 | 167-207 |
300-500 | 315 | 570 | 12 | 29 | 167-207 |
<100 | 345 | 590 | 18 | 59 | 174-217 |
100-300 | 345 | 590 | 17 | 54 | 174-217 |
<100 | 395 | 620 | 17 | 59 | 187-229 |
Механічні властивості в залежності від температури відпустки
t відпустки, °С | s0,2, МПа | sB, МПа | d5, % | y, % | KCU, Дж/м2 | HB |
Загартування 850 ° С, вода. Зразки діаметром 15 мм | ||||||
450 | 830 | 980 | 10 | 40 | 59 | |
500 | 730 | 830 | 12 | 45 | 78 | |
550 | 640 | 780 | 16 | 50 | 98 | |
600 | 590 | 730 | 25 | 55 | 118 | |
Загартування 840 ° С, вода. Діаметр заготовки 60 мм | ||||||
400 | 520-590 | 730-840 | 12-14 | 46-50 | 50-70 | 202-234 |
500 | 470-520 | 680-770 | 14-16 | 52-58 | 60-90 | 185-210 |
600 | 410-440 | 610-680 | 18-20 | 61-64 | 90-120 | 168-190 |
Механічні властивості в залежності від перерізу
Перетин, мм | s0,2, МПа | sB, МПа | d5, % | y, % | KCU, Дж/м2 |
Загартування 850 °С, відпустка 550 °С. Зразки вирізалися із центру заготовок. | |||||
15 | 640 | 780 | 16 | 50 | 98 |
30 | 540 | 730 | 15 | 45 | 78 |
75 | 440 | 690 | 14 | 40 | 59 |
100 | 440 | 690 | 13 | 40 | 49 |
Технологічні характеристики стали.
Температура кування:
- Початок – 1250 про С;
- Кінця - 700 про;
- Перетин до 400 мм охолоджується на повітрі.
Зварюваність - важко зварювана, способи зварювання: РДС та КТЗ. Необхідний підігрів та подальша термообробка.
Оброблюваність різанням - у гарячекатаному стані при НВ 170-179 та sB = 640 МПа Ku тв.спл. = 1, Ku б. = 1.
Схильність до відпускної спроможності – не схильна.
Флокеночутливість – малочутлива.
Тим перетура критичних точок
Ударна в'язкість
Ударна в'язкість, KCU, Дж/см2
Стан постачання, термообробка | 20 | -20 | -40 | -60 |
Пруток діаметром 25 мм. Гарячекатаний стан. | 14-15 | 10-14 | 5-14 | 3-8 |
Пруток діаметром 25 мм. Відпал | 42-47 | 27-34 | 27-31 | 13 |
Пруток діаметром 25 мм. Нормалізація | 49-52 | 37-42 | 33-37 | 29 |
Пруток діаметром 25 мм. Загартування. Відпустка | 110-123 | 72-88 | 36-95 | 31-63 |
Пруток діаметром 120 мм. Гарячекатаний стан | 42-47 | 24-26 | 15-33 | 12 |
Пруток діаметром 120 мм. Відпал | 47-52 | 32 | 17-33 | 9 |
Пруток діаметром 120 мм. Нормалізація | 76-80 | 45-55 | 49-56 | 47 |
Пруток діаметром 120 мм. Загартування. Відпустка | 112-164 | 81 | 80 | 70 |
Межа витривалості Стали 45
s-1, МПа | t-1, МПа | sB, МПа | s0,2, МПа |
245 | 157 | 590 | 310 |
421 | 880 | 680 | |
231 | 520 | 270 | |
331 | 660 | 480 |
Прожарюваність сталі
Твердість для смуг прожарюваності HRCе (HRB).
Відстань від торця, мм / HRC е | |||||||||
1.5 | 3 | 4.5 | 6 | 7.5 | 9 | 12 | 16.5 | 24 | 30 |
50.5-59 | 41.5-57 | 29-54 | 25-42.5 | 23-36.5 | 22-33 | 20-31 | (92)-29 | (88)-26 | (86)-24 |
Термообробка | Кількість мартенситу, % | Крит.діам. у воді, мм | Крит.діам. в олії, мм | ||||||
Загартування | 50 | 15-35 | 6-12 |
Фізичні властивості
Температура випробування, °С | 20 | 100 | 200 | 300 | 400 | 500 | 600 | 700 | 800 | 900 |
Модуль нормальної пружності, Е, ДПа | 200 | 201 | 193 | 190 | 172 | |||||
Модуль пружності при зсуві крученням G, ДПа | 78 | 69 | 59 | |||||||
Щільність, pn, кг/см3 | 7826 | 7799 | 7769 | 7735 | 7698 | 7662 | 7625 | 7587 | 7595 | |
Коефіцієнт теплопровідності Вт/(м · ° С) | 48 | 47 | 44 | 41 | 39 | 36 | 31 | 27 | 26 | |
Температура випробування, °С | 20- 100 | 20- 200 | 20- 300 | 20- 400 | 20- 500 | 20- 600 | 20- 700 | 20- 800 | 20- 900 | 20- 1000 |
Коефіцієнт лінійного розширення (a, 10-6 1/°С) | 11.9 | 12.7 | 13.4 | 14.1 | 14.6 | 14.9 | 15.2 | |||
Питома теплоємність (С, Дж/(кг · °С)) | 473 | 498 | 515 | 536 | 583 | 578 | 611 | 720 | 708 |
Сталь - це сплав заліза, що деформується (що піддається ковці) з вуглецем та іншими елементами. Її отримують зі складу, в якому є місце для чавуну та сталевого брухту, обробляють у мартенівських печах, кисневих конвертерах та електричних пічках. Якщо сплаві заліза більше 2,14% вуглецю, тоді це вже чавун.
Класифікація сталі
На ринку 99% всієї сталі представлений конструкційний матеріал у широкому сенсі. До цієї групи відносяться сталі для зведення будівельних споруд, виготовлення деталей машин, пружних елементів, інструментів, а також для особливих умов роботи, що мають певні показники, наприклад, теплостійкі, нержавіючі та інші.
Головними якостями матеріалу є:

Сталь та сплави класифікують:
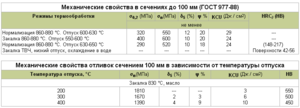
Хімічний склад
Залежно від вмісту вуглецю ділять на групи:
- вуглецю менше 0,3% С - маловуглецеві.
- Середньовуглецеві, коли його від 0,3 до 0,7%.
- Більше 07% - високовуглецеві.
Щоб покращити технологічні властивості матеріалу, сталь легують. Що це означає? Крім звичайних домішок до її складу додають у певних поєднаннях легуючі елементи. Зазвичай найкращі властивості виникають, коли легують комплексно.
У легованих сталях класифікація відбувається завдяки сумарному відсотку домішок, що містяться в ній:

Структурний склад
Леговані сталі поділяються на види структурного аналізу:
- У відтоженому вигляді - ледебуритний, феритний, доевтектоїдний, заевтектоїдний, аустенітний.
- У нормалізованому вигляді – автенітний, мартенситний, перлітний.
Перлітний клас характеризується низьким вмістом легуючих елементів. До нього відносяться леговані та вуглецеві сталі. Мартенситний включає сталі з більш високим відсотком легуючих речовин. До автенітного класу входять матеріали з високим значенням легуючих елементів.
За способом виробництва та вмісту домішок цей матеріал ділиться на 4 групи:
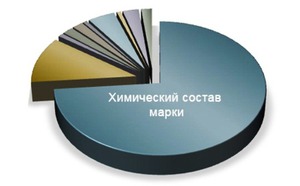
Застосування
Шарикопідшипникові хромисті сталі застосовуються виготовлення підшипників. Цей вид зарекомендував себе як високоміцний, твердий і контактно-витривалий матеріал.
Пружну деформацію мають деякі види сталітому вони застосовуються для пружин, ресор та інших виробів. Багато хто з них повинен витримувати циклічні навантаження. Тому основними вимогами до цих видів стали є високі значення пружності, плинності, витривалості, також необхідна пластичність та опір крихкому руйнуванню.
Високоміцні сталі мають міцність при необхідній пластичності, малу чутливість до надрізів, низькі пороги холодноламкості, відмінну зварюваність, високі показники опору крихкому руйнуванню.
Сталь 45
Цей сплав сталі відрізняється від інших набором особливих характеристик, які притаманні лише цій марці. Вона відрізняється застосуванням та високою функціональністю, унікальним складом хімічних сполук, сукупністю ливарних та інших виробничих параметрів
Застосування
Сталь під номером 45 виготовляється відповідно до всіх вимог ГОСТу. З неї роблять вали всіх видів, бандажі, шпинделі, циліндри різних видів, кулачки різноманітної форми. По суті, застосовується для конструкцій та пристроїв, функціональним призначенням яких є стійкість до величезних навантажень, де потрібно демонструвати підвищені показники зносостійкості, міцності, нечутливості до корозії.
У складі стали марки 45 відповідно до ГОСТузнаходяться такі елементи, як фосфор, миш'як, мідь, нікель, марганець та інші речовини. Дана сталь має великий набір механічних характеристик. Тому вона здатна винести практично всі кліматичні та температурні коливання. Випробовують цей вид сталі при температурному інтервалі від 200 до 600 градусів.
МІЖДЕРЖАВНИЙ СТАНДАРТ
ПРОКАТ СОРТОВИЙ, КАЛІБРОВАНИЙ, ІЗ СПЕЦІАЛЬНОЇ ОСОБЛИВОСТІ ПОВЕРХНІ
ІЗ ВУГЛЕДИНОЇ ЯКІСНОЇ КОНСТРУКЦІЙНОЇ СТАЛІ
Загальні технічні умови
ГОСТ 1050-88
Дата введення 01.01.91
Цей стандарт встановлює загальні технічні умови для гарячекатаного та кованого сортового прокату з вуглецевої якісної конструкційної сталі марок 08, 10, 15, 20, 25, 30, 35, 40, 45, 50, 55, 58 (55пп) та 6 250 мм, а також прокату каліброваного та зі спеціальним оздобленням поверхні всіх марок.
У частині норм хімічного складу стандарт поширюється на інші види прокату, зливки, поковки, штампування зі сталі марок, перерахованих вище, а також зі сталі марок 05кп, 08кп, 08пс, Юкп, Юпс, Пкп, 15кп, 15пс, 18кп, 20 .
1. ОСНОВНІ ПАРАМЕТРИ І РОЗМІРИ
1.1. Марки та хімічний склад сталі по ковшової пробі повинні відповідати наведеним у табл.1.
Таблиця 1
Масова частка елементів, % |
||||
Марка сталі |
||||
вуглецю |
марганцю |
хрому, не більше |
||
Не більше 0,06 |
Не більше 0,03 |
Не більше 0,40 |
||
Не більше 0,03 |
||||
Не більше 0,07 |
||||
Не більше 0,06 |
||||
Не більше 0,07 |
||||
Не більше 0,06 |
||||
Не більше 0,07 |
||||
Примітки:
1. За ступенем розкислення сталь позначають: киплячу – кп. напівспокійну – пс, спокійну – без індексу.
2. Сталь марки 05кп не допускається до застосування у новоствореній та модернізованій техніці.
3. Профіль для косих шайб за ГОСТ 5157 виготовляють із сталі марок 20 та 35.
(Змінена редакція, Змін.№ 1),
1.1.1. Масова частка сірки сталі повинна бути трохи більше 0,040 %, фосфору - трохи більше 0,035 %.
Для сталі марок Пкп і 18кп, що застосовується для плакування, масова частка сірки має бути
трохи більше 0,035 %, фосфору - трохи більше 0,030 %.
1.1.2. Залишкова масова частка нікелю у сталі всіх марок має перевищувати 0,30 %, міді сталі марок Пкп і 18кп - 0,20 %, сталі інших марок - 0,30 %.
1.1.3. У сталі марок 35, 40, 45, 50, 55 і 60, призначеної для виготовлення патентованого дроту, масова частка марганцю повинна бути 0,30-0,60 %, нікелю - не більше 0,15 %, хрому -не більше 0, 15%, міді – не більше 0,20%. Масова частка сірки і фосфору - відповідно до вимог стандартів на дріт, але не перевищує норм, наведених у п. 1.1.1.
1.1.4. У сталі марок 08ПС, ЮПС, 15ПС і 20ПС, призначеної для виготовлення листового прокату для холодного штампування, допускається масова частка марганцю до 0,25% за нижньою межею.
1.1.5. У сталі марок 08пс, Юпс, 15пс і 20пс допускається масова частка кремнію менше 0,05% за умови застосування інших (крім кремнію) розкислювачів у необхідних кількостях.
1.1.6. У сталі допускається масова частка миш'яку трохи більше 0,08 %.
1.1.7. Масова частка азоту в киснево-конвертерної сталі має перевищувати 0,006 % для тонколистового прокату і стрічки і 0,008 % - інших видів прокату.
1.1.8. Відповідно до замовлення в спокійній сталі, виготовленої скрап-процесом і скрап-
рудним процесом, допускається залишкова мас-Таблица2 сова частка нікелю і хрому не більше 0,40% кожного.
(Введено додатково, Змін.№ 1),
1.2. Впрокаті, заготівлях, поковках і виробах подальшого переділу допускаються відхилення за хімічним складом від норм, наведених у табл.1, відповідно до табл.2.
1.3. Сортамент прокату повинен відповідати вимогам:
ГОСТ 2590 - для гарячекатаного круглого;
ГОСТ 2591 або іншої нормативно-технічної документації - для гарячекатаного квадрат-
Найменування елемента
ГОСТ 1133 - для кованого круглого та квадратного;
ГОСТ 2879 – для гарячекатаного шестигранного;
ГОСТ 103 - для гарячекатаного смугового;
ГОСТ 4405 – для кованого смугового;
ГОСТ 5157 – для профілю для косих шайб;
ГОСТ 7417 – для каліброваного круглого;
ГОСТ 8559 – для каліброваного квадратного;
ГОСТ 8560 – для каліброваного шестигранного;
нормативно-технічної документації – для каліброваного смугового;
ГОСТ 14955 - зі спеціальним оздобленням поверхні.
Приклади умовних позначень наведено у додатку 1.
(Змінена редакція, Змін. №1),
2. ТЕХНІЧНІ ВИМОГИ
2,1, Характеристики базового виконання
2.1.1. Прокат сортової немірної довжини (НД) з граничними відхиленнями для звичайної точності розмірів, кривизни, овальності та інших вимог до форми, серповидності та відхилення від площинності класу 2 за ГОСТ 103 (для смуги).
2.1.2. Прокат каліброваної немірної довжини (НД) із граничними відхиленнями для поля допуску – Ы1, овальністю – не більше граничних відхилень по діаметру.
2.1.3. Прокат зі спеціальною обробкою поверхні немірної довжини (НД) з граничними відхиленнями для поля допуску - Ы1, овальністю - трохи більше половини граничних відхилень по діаметру.
2.1.4. Прокат сортовий без термічної обробки, калібрований та зі спеціальною обробкою поверхні нагартований - НГ або термічно оброблений (відпалений, високовідпущений, нормалізований, нормалізований з відпусткою, загартований з відпусткою) - ТО.
2.1.5. Прокат сортової двох груп якості поверхні: 2ГП та ЗГП. Прокат групи якості поверхні 2РП призначений переважно для гарячої обробки тиском групи ЗГП - переважно для холодної механічної обробки.
2.1.6. На поверхні прокату групи якості поверхні 2ГП не повинно бути розкочаних бульбашок, прокатних полон, заходів сонця, тріщин, забруднень, тріщин напруги.
2.1.1-2.1.6. (Змінена редакція,Змін. №1),
2.1.6.1. Дефекти на поверхні повинні бути видалені пологою вирубкою або зачисткою,
ширина якої має бути не менше п'ятикратної глибини.
Глибина зачистки дефектів, рахуючи від фактичного розміру, повинна перевищувати: половини допуску розмір - для прокату розміром менше 80 мм; допуску на розмір – для прокату розміром від 80 до 140 мм;
5% діаметра або товщини – для прокату розміром від 140 до 200 мм;
6% діаметра або товщини – для прокату розміром більше 200 мм.
В одному перерізі прокату розміром (діаметром або товщиною) понад 140 мм допускається не більше двох зачисток максимальної глибини.
2.1.6.2. На поверхні прокату допускаються без зачистки окремі ризики, вм'ятини та
горобина глибиною в межах половини допуску на розмір, а також розкочені бульбашки та
забруднення (волосовини) глибиною, що не перевищує У 4 допуску на розмір, але не більше 0,20 мм,
рахуючи від фактичного розміру.
2.1.7. На поверхні прокату з якістю поверхні групи ЗГП допускаються місцеві
дефекти глибиною, що не перевищує мінусового граничного відхилення на розмір для прокату
розміром не менше 100 мм; допуску на розмір – для прокату розміром 100 мм та більше.
Глибина залягання дефектів рахується від номінального розміру. (Змінена редакція, Зм. № 1),
2.1.8. Прокат сортовий має бути обрізаний.
Допускаються зім'яті кінці та задирки.
Косина різу сортового прокату розміром до 30 мм не регламентується, понад 30 мм не повинна перевищувати 0,1 діаметра або товщини. Прокат сортовий розміром до 40 мм немірної довжини дозволяється виготовляти з необрізними кінцями.
2.1.9. Якість поверхні та вимоги щодо обрізання кінців каліброваного прокату повинні
відповідати - ГОСТ 1051 груп Б та В, зі спеціальним оздобленням поверхні - ГОСТ 14955
груп, Г і Д.
У прокаті зі спеціальним оздобленням поверхні обезуглерожування не допускається.
2.1.10. Твердість (ТВ1) сортового прокату без термічної обробки не повинна перевищувати
255 НВ, каліброваного та зі спеціальною обробкою поверхні нагартованого - 269 НВ.
(Змінена редакція,Змін. №1),
2.1.11. Механічні властивості прокату в нормалізованому стані (М1) повинні відповід-
ти нормам, наведеним у табл.3.
Таблиця 3
Механічні властивості, не менше |
||||
Марка сталі |
Тимчасове |
Відносне |
Відносне |
|
Межа плинності ст т, |
опір |
подовження 5 5 |
звуження у |
|
розриву ст, Н/мм 2 |
||||
Примітай» |
1. Норми механічних властивостей, наведені в табл.3, належать до прокату діаметром або товщиною
до 80 мм. Для прокату діаметром або товщиною понад 80 мм допускається зниження відносного подовження
на 2% (абс.) та відносного звуження на 5% (аба).
Норми механічних властивостей для заготовок, перекованих із прутків діаметром або завтовшки понад 120 до 250 мм на прокат діаметром або завтовшки від 90 до 100 мм, повинні відповідати наведеним у табл.3.
2. За узгодженням виробника зі споживачем для сталі марок 25-60 допускається зниження час-
ного опору на 20 Н/мм 2 (2 кгс/мм 2) порівняно з нормами, вказаними в табл.3, при одночас-
ном підвищенні норм відносного подовження на 2% (абс).
(Змінена редакція, Змін.№ 1),
2.1.12. Макроструктура прокату не повинна мати усадкової раковини, пухкості, пухирів, розшарування, внутрішніх тріщин, шлакових включень та флокінів.
2.2. Характеристики, що встановлюються споживачем
2.2.1. Прокат із сталі марок 20, 25, 30, 35, 40, 45, 50 з масовою часткою бору 0,002-0,006%. І тут наприкінці позначення марки ставиться літера Р.
2.2.2. Прокат із спокійної сталі з масовою часткою кремнію 0,17-0,27 %.
2.2.3. Прокат мірної довжини (МД).
2.2.4. Прокат довжини, кратної мірної (КД).
2.2.5. Прокат калібрований та зі спеціальним оздобленням поверхні з полем допуску Ы2.
2.2.6. Сортовий прокат у термічно обробленому стані (відпалений, високовідпущений, нормалізований, нормалізований з відпусткою) - ТО.
2.2.7. Прокат з якістю поверхні групи 1ГП - без розкочаних бульбашок та забруднень (волосовин) та випробуванням на гаряче осадження (65).
Прокат призначений переважно для гарячої опади, висадки та штампування. Випробування прокату розміром 80 мм виробник може не проводити.
2.2.8. Прокат із сталі марок 25, 30, 35, 40, 45, 50 з контролем ударної в'язкості (КУВ) на
термічно оброблених (загартування + відпустка) зразках.
Норми ударної в'язкості повинні відповідати зазначеним у табл.4.
2.2.9. Прокат калібрований у нагартованому або термічно обробленому стані з нормованими механічними властивостями (М2) відповідно до вимог, зазначених у табл. 5.
Таблиця 5
Механічні властивості прокату, не менше |
||||||
нагартованого |
відпаленого або високовідпущеного |
|||||
Тимчасове |
Тимчасове |
|||||
опір |
Відносне |
Відносне |
опір |
Відносне |
Відносне |
|
подовження 8 5 % |
звуження у, % |
розриву ст, Н/мм 2 (кгс/мм 2) |
подовження 5 5 % |
звуження у, % |
||
2.2.10. Прокат з нормованою в балах мікроструктурою (КМС) відповідно до вимог, зазначених у табл. 6.
Таблиця 6
Макроструктура сталі в балах, не більше
Примітка. Для прокату розміром 70 мм і більше з якістю поверхні групи допускаються підкіркові бульбашки бала 2 на глибину не більше 1 / 2 допуску на діаметр чи товщину.
2.2.11. Прокат з нормованою твердістю (ТВ2) відповідно до вимог, наведених у табл. 7.
Таблиця 7
Число твердості НВ, не більше |
||||
для гарячекатаного та кованого |
для каліброваного прокату та зі спеціальною |
|||
Марка сталі |
обробкою поверхні |
|||
без термічної обробки |
після відпалу або високої відпустки |
нагартованого |
відпаленого або високовідпущеного |
|
2.2.12. Прокат із ультразвуковим контролем (УЗК) внутрішніх дефектів за ГОСТ 21120.
2.2.13. Прокат із забезпеченням зварюваності (ГС).
2.2.14. Прокат із сталі марок 35, 40, 45, 50, 55, 58 (55пп), 60, призначений для поверхневого загартування струмами високої частоти, з обезуглероживанием (ферит+перехідна зона) не більше 1,5% діаметра або товщини на бік (1С ).
2.2.3-2.2.14. (Змінена редакція, Змін.№ 1),
2.2.15. (Виключений, Змін. №1),
2.3. Характеристики, що встановлюються за погодженням споживача з виробником
2.3.1. Прокат із зменшеними порівняно з наведеними в табл.1 межами масової частки вуглецю, але не менше 0,05 %.
2.3.2. Прокат із зменшеними порівняно з наведеними в табл.1 межами за масовою часткою вуглецю, але не менше 0,05 %, без урахування відхилень у готовому прокаті, зазначених у табл.2.
2.3.3. Прокат з масовою часткою сірки 0,020-0,040%.
2.3.4. Прокат з масовою часткою сірки трохи більше 0,025 %.
2.3.5. Прокат з масовою часткою фосфору трохи більше 0,030 %.
2.3.6. Прокат з масовою часткою міді трохи більше 0,25 %.
2.3.7. Сортовий прокат діаметром або товщиною понад 30 до 140 мм з видаленням задирок (УЗ) та зім'ятих кінців.
2.3.8. Нагартований прокат з підвищеною на 15 НВ у порівнянні з наведеними у табл. 7 твердістю (ТВЗ).
2.3.9. Прокат з нормованими механічними властивостями (МОЗ), що визначаються на зразках, вирізаних з термічно оброблених заготовок (загартування + відпустка), зазначеного в замовлення розміру, відповідно до вимог табл. 8.
Таблиця 8
Механічні властивості прокату розміром |
||||||||||||
від 16 до 40 мм |
від 40 до 100 мм |
|||||||||||
Не менше |
Відносне подовження |
Межа текучес-ти а Т; Н/мм 2 (кгс/мм 2) |
Тимчасове опір розриву |
Відносне подовження |
Межа текучес-ти а Т; Н/мм 2 (кгс/мм 2) |
Тимчасове опір розриву |
Відносне подовження |
|||||
850-1000 (87-102) |
Примітки.
1. Норми механічних властивостей до 01.01.92 є браковочними, визначення обов'язково.
2. Механічні властивості сталі 30 поширюються на прокат розміром до 63 мм.
3. Значення механічних властивостей наведено для прокату круглого перерізу. Для прямокутних перерізів діапазони еквівалентних діаметрів наведено у додатку 2.2.3.10. Прокат з нормованою прожарюваністю (ПР) відповідно до додатків 3 і 4.
2.3.11. Прокат зі сталі марок 35, 40, 45, 50, 55, 58 (55пп), 60, призначений для
поверхневого гарту струмами високої частоти, з обезуглероживанием (ферит+перехідна зона)
трохи більше 0,5 % діаметра чи товщини убік (2С).
2.3.12. Прокат у травленому стані (Т). 2.3.6-2.3.12. (Змінена редакція, Изм.№ 1),
2.3.13. Прокат калібрований з полем допуску Ы0.
2.3.14. Прокат сортовий гарячекатаний підвищеної (Б) та високої (А) точності розмірів.
2.3.15. Прокат з якістю поверхні групи
2ГП із випробуванням на гаряче осадку (65). Т а б л я 8а
Випробування прокату розміром св.
тель може не проводити.
2.3.16. Прокат із сталі марок 45, 50, 50А з контролем твердості (ТВ4) на загартованих зразках 50 50А відповідно до вимог, зазначених у табл.8а.
2.3.17. Масова частка азоту не більше 0,008% в киснево-конвертерної сталі для тонколістового прокату.
2.3.13-2.3.17. (Введені додатково, Змін.№ 1),
2.4. Допускається в технічних умовах на конкретну продукцію передбачати доповнення
ні або підвищені характеристики, не передбачені цим стандартом.
Перелік додаткових характеристик наведено у додатку 5.
2.5. Маркування та пакування прокату - за ГОСТ 7566.
2.5.1. Упаковка каліброваного прокату - за ГОСТ 1051, зі спеціальним оздобленням поверхні - за ГОСТ 14955.
2.5.2. Маркування наносять безпосередньо на продукцію, якщо продукція не підлягає упаковці, та на ярлик, якщо продукція упакована у зв'язки, мотки та бухти.
3. ПРАВИЛА ПРИЙМАННЯ
3.1. Прокат приймають партіями, що складаються із сталі однієї плавки, одного розміру та
одного режиму термічної обробки (при виготовленні у термічно обробленому стані).
За погодженням виробника із споживачем партії формуються зі сталі однієї марки декількох плавок одного розміру.
Кожну партію супроводжують документом якості за ГОСТ 7566.
При використанні напівспокійної сталі інших (крім кремнію) розкислювачів робиться відповідна вказівка в документі про якість.
Для прокату, що приймається з характеристиками, що встановлюються споживачем відповідно до пп. 2.2 і 2.3, у документі про якість вказують результати випробувань за показниками, що замовляються.
3.2. Прокат піддають приймально-здавальним випробуванням.
3.3. Для перевірки якості від партії прокату відбирають:
1) для хімічного аналізу – проби за ГОСТ 7565. Контроль залишкових міді, нікелю, хрому, миш'яку та азоту виробник проводить періодично не рідше одного разу на квартал. При виготовленні сталі з урахуванням марганцевого еквівалента контроль залишкових міді, нікелю та хрому проводять на кожній плавці;
2) для контролю якості поверхні та розмірів - всі прутки, смуги та мотки;
3) для контролю макроструктури за зломом або травленням, для випробування на ударний вигин, визначення глибини обезуглероженного шару - два прутки, смуги або мотка;
4) для перевірки твердості – 2 % прутків, смуг або мотків, але не менше 3 штук;
5) для випробування на розтяг - один пруток, смугу або моток для контролю в нормалізованому стані, два прутки, дві смуги або два мотки для контролю в нагартованому, отожженном, високовідпущеному або загартованому з відпусткою стані;
6) для визначення прожарюється TM - один пруток, смугу або моток від плавки-ковша сталі всіх марок, що не містять бор, і два прутки, дві смуги або два мотки від плавки-ковша сталі марок, що містять бор;
7) для визначення величини зерна – один пруток, смугу або моток від плавки-ковша;
8) для випробування на осадку - три дроти, смуги або мотка;
9) Для визначення твердості після гарту - два поздовжні зразки від плавки. (Змінена редакція, Изм.№ 1),
3.4. При отриманні незадовільних результатів випробувань хоча б по одному з показників щодо нього проводять повторні випробування за ГОСТ 7566.
Результати повторних випробувань розповсюджують на всю партію.
4. МЕТОДИ ВИПРОБУВАНЬ
4.1. Хімічний аналіз сталі проводять за ГОСТ 22536.0-ГОСТ 22536.9, ГОСТ 27809, ГОСТ 12359 або іншими методами точності, що не поступаються стандартним. У разі розбіжностей хімічний аналіз проводять за ГОСТ 22536.0-ГОСТ 22536.9, ГОСТ 27809, ГОСТ 12359.
4.2. Якість поверхні перевіряють оглядом прокату без застосування збільшувальних приладів. При необхідності проводять освітлення або травлення поверхні, а для прокату зі спеціальною обробкою поверхні діаметром до 3 мм включно огляд проводять при збільшенні до 10 х. Глибину залягання дефектів на поверхні прокату визначають контрольним зачищенням або запилюванням напилком.
4.3. Геометричні розміри і форму визначають за допомогою вимірювальних інструментів за ГОСТ 26877, ГОСТ 162, ГОСТ 166, ГОСТ 427, ГОСТ 2216, ГОСТ 3749, ГОСТ 5378, ГОСТ 6507, ГОСТ 7502, або інструментів, атестованих Г000.
4.4. Відбір проб від мотків всім видів випробувань проводять з відривом щонайменше 1,5 витка від кінця раската.
4.5. Від кожного відібраного для контролю прутка, смуги або мотка відбирають: для випробування на розтягування та осадку, для визначення величини зерна, прожарюється TM і глибини обезуглеро-женого шару - по одному зразку;
для випробування на ударний вигин - за одним зразком кожного типу; для контролю макроструктури – один темплет.
4.6. Відбір проб для випробувань на осадку – за ГОСТ 7564.
4.7. Відбір проб для випробування механічних властивостей по табл.3 і 5 проводять за ГОСТ 7564 (варіант 1), табл.4 і 8 - по ГОСТ 7564 (варіант 2).
(Змінена редакція, Змін.№ 1),
4.7а. Відбір зразків для визначення твердості після гарту проводять за схемою, наведеною в додатку 8.
Проби для контролю можуть бути вирізані із готового прокату або граничної заготовки (у плавковому контролі).
(Введено додатково, Змін.№ 1),
Зразки нагрівають до температури кування 850-1000°З осаджують на 65% відносно початкової висоти. На осаджених зразках не повинно бути тріщин і занепадів, що розкрилися. (Змінена редакція, Изм.№ 1),
4.9. Твердість за Брінеллем визначають за ГОСТ 9012. Твердість прокату діаметром або
завтовшки менше 5 мм не визначають.
4.9а. Твердість по Роквеллу після гарту визначають за ГОСТ 9013 на майданчику, розташованому на середині довжини зразка. Поверхня площадки для виміру твердості піддається зачистці: у своїй шорсткість поверхні Ка мусить бути трохи більше 1,25 мкм по ГОСТ 2789.
(Введено додатково, Змін.№ 1),
4.10. Випробування на розтяг проводять за ГОСТ 1497 на зразках п'ятикратної довжини
діаметром 5 чи 10 мм.
Для прокату діаметром або товщиною до 25 мм включно випробування допускається проводити на зразках без механічної обробки.
Випробування на ударну в'язкість проводять за ГОСТ 9454 на зразках типу 1. Напрямок осі зразка - вздовж напряму прокатки.
4.11. Зразки для випробувань на розтяг прокату відповідно до вимог табл.
вирізують із нормалізованих заготовок діаметром або стороною квадрата 25 мм.
* На території Російської Федерації діють ПР 50.2.009-94.
Для прутків діаметром менше 25 мм нормалізація проводиться у готовому перерізі прутка (без вирізки заготовки).
Примітка. Від прутків розміром більше 120 мм відбір проб для механічних випробувань може проводитися від перекованих або перекатаних заготовок 90-100 мм.
4.12. Зразки для випробувань на розтяг прокату відповідно до вимог табл.8 вирізають з термічно оброблених заготовок розміром, вказаним споживачем.
4.13. Режими термічної обробки заготовок (зразків) для проведення випробувань механічних властивостей наведені в додатках 6 і 7, для контролю твердості після загартування - у додатку 9.
(Змінена редакція,Змін. №1),
4.14. Контроль макроструктури на злам або протруєних темплетах проводять без застосування.
ня збільшувальних приладів за ГОСТ 10243.
Допускається застосовувати методи ультразвукового контролю (УЗК) та інші методи контролю, що не руйнують, узгоджені в установленому порядку.
4.15. Глибину обезуглероженного шару визначають за ГОСТ 1763.
4.16. Прожарювання визначають методом торцевого гарту за ГОСТ 5657.
4.17. Величину зерна визначають за ГОСТ 5639.
4.18. На сталі однієї плавки, що пройшла випробування на макроструктуру, прожарюваність і механічні властивості на великих профілях прокату, при виготовленні більш дрібних профілів прокату перераховані випробування у виробника допускається не проводити.
4.19. Допускається у виробника застосовувати статистичні та неруйнівні методи контролю за методикою, узгодженою в установленому порядку. При виникненні розбіжностей та періодичних перевірках якості продукції застосовуються методи контролю, передбачені цим стандартом.
5. ТРАНСПОРТУВАННЯ І ЗБЕРІГАННЯ
5.1. Транспортування та зберігання - за ГОСТ 7566 з наступним доповненням.
5.1.1. Транспортування продукції проводиться транспортом всіх видів відповідно до правил перевезення вантажів, що діють на транспорті цього виду. По залізницях перевезення здійснюється залежно від маси та габаритних розмірів у критих чи відкритих вагонах. Маса вантажного місця не повинна перевищувати при механізованому завантаженні у відкриті транспортні засоби 10000 кг, у криті – 1250 кг. Упаковка, засоби та способи формування пакетів – за ГОСТ 7566.
При відправленні двох і більше вантажних місць, розміри яких дозволяють оформити транспортний пакет із габаритними розмірами за ГОСТ 24597, вантажні місця мають бути сформовані у транспортні пакети. Засоби кріплення – за ГОСТ 21650.
(Змінена редакція, Зм. № 1),
Приклади умовних позначень
Прокат сортовий, круглий, звичайної твердості прокатки (В), ІІ класу по кривизні, немірної довжини (НД), діаметром 100 мм за ГОСТ 2590-88, із сталі марки 30, з якістю поверхні групи 2ГП, з механічними властивостями за табл.3 (М1), з твердістю за п.2.1.10 (ТВ1), з контролем ударної в'язкості по табл.4(КУВ), з видаленням задирок (УЗ), з випробуванням на гаряче осадження (65), без термічної обробки:
Коло В-П-НД-100 ГОСТ2590-88/30-2ГП-М1-ТВ1-КУВ-УЗ-66 ГОСТ 1050-88
Прокат сортовий, квадратний, підвищеної точності прокатки (Б), I класу по кривизні, мірної довжини (МД), зі стороною квадрата 25 мм за ГОСТ 2591-88, із сталі марки 35, з якістю поверхні групи 1ГП, з механічними властивостями по табл. .8 (МОЗ), з твердістю по табл.7 (ТВ2), з нормованою в балах макроструктурою (КМС) по табл.6, з обезуглероживанием за п.2.2.14 (1С), термічно оброблений (ТО):
Квадрат Б-1-МД-25 ГОСТ2591-88/35-1ГП-МЗ-ТВ2-КМС-1С-ТО ГОСТ 1050-88
Прокат смугової, звичайної точності прокатки (В), серповидності класу 2, відхилення від площинності класу 2, кратної мірної довжини (КД), товщиною 36 мм, шириною 90 мм за ГОСТ 103-76, зі сталі марки 45, з якістю поверхні групи ЗГП, з механічними властивостями по табл.3 (М1), з твердістю за п.2.1.10 (ТВ1), з нормованим прожарюванням (ПР), без термічної обробки:
Смуга В-2-2-КД-36х90 ГОСТ 103-76/45-ЗГП-М1-ТВ1-ПР ГОСТ 1050-88
Профіль гарячекатаний для косих шайб, мірної довжини (МД), з розмірами 2ВхНх1г = 32x5,8x4 мм за ГОСТ 5157-83, із сталі марки 35, з якістю поверхні групи ЗГП, з механічними властивостями по табл.3 (М1), з твердістю за п.2.1.10 (ТВ1), без термічної обробки:
Профіль для косих шайб МД-32х5, 8х4 ГОСТ5157-83/35-ЗГП-М1-ТВ1
ГОСТ 1050-88
Прокат калібрований, круглий, з полем допуску по Ы1, мірної довжини (МД), діаметром 10 мм за ГОСТ 7417-75, зі сталі марки 45, з якістю поверхні групи по ГОСТ 1051-73, з механічними властивостями по табл5 (М2) , з твердістю по п238 (ТВЗ), з обезуглероживанием по п2311 (2С), нагартований (НГ):
Коло НП-МД-10ГОСТ 7417-75/45-В-М2-ТВЗ-2С-НГ ГОСТ 1050-88
Прокат калібрований, квадратний, з полем допуску Ы1, кратної мірної довжини (КД), зі стороною квадрата 15 мм за ГОСТ 8559-75 зі сталі марки 20, з якістю поверхні групи Б по ГОСТ 1051-73, з механічними властивостями по табл. 8 (МОЗ), з твердістю за табл. 7 (ТВ2), із забезпеченням зварюваності (ГС), нагартований (НГ):
Квадрат НП-КД-15ГОСТ8559-75/20-Б-МЗ-ТВ2-ГС-НГ ГОСТ 1050-88
Прокат калібрований, шестигранний, з полем допуску Ы2, немірної довжини (НД), діаметром вписаного кола 8 мм за ГОСТ 8560-78, із сталі марки 45, з якістю поверхні групи В за ГОСТ 1051-73, з механічними властивостями за табл. .3 (М1), з твердістю по табл.8а (ТВ4), термічно оброблений (ТО):
Шестигранник Н12-НД-8ГОСТ 8560-78/45-В-М1-ТВ4-ТО ГОСТ 1050-88
Прокат зі спеціальною обробкою поверхні, круглий, з полем допуску Ы1, немірної довжини (НД), діаметром 8 мм, з якістю поверхні групи за ГОСТ 14955-77 зі сталі марки 20, з механічними властивостями по табл.5 (М2), з твердістю за табл.7 (ТВЗ) нагартований (НГ):
Коло НП-НД-8ГОСТ 14955-77/20-В-М2-ТВЗ-НГ ГОСТ 1050-88
Приклади умовних позначень, які допускається наводити в конструкторській документації:
Прокат зі спеціальною обробкою поверхні, круглий, з полем допуску Ы1, немірної довжини (НД), діаметром 8 мм, якістю поверхні групи за ГОСТ 14955-77, зі сталі марки 20, з механічними властивостями по табл.5 (М2), з твердістю за табл.7 (ТВЗ), нагартований (НГ):
КтР НП-НД-8 ГОСТ 14955-77
РУ20-В-М2-ТВЗ-НГ ГОСТ 1050-88
(Змінена редакція, Змін.№ 1).
ДОДАТОК 4Обов'язковеПАРАМЕТРИ МАРОЧНИХ СМУГ (МЕЖІ КОЛИВАНЬ ТВЕРДОСТІ НКС (НКС Е) І НКВ ЗА ДОВЖИНОЮ ТОРЦЕВОГО ЗРАЗКУ
Таблиця 9
Твердість для смуг прожарювання сталі марок |
||||||
НКС 56 (НКС Е 57) |
НКС 48(НКС Е 49,5) |
НКС 57(НКС Е 58) |
НКС 49 (НКС Е 50,5) |
НКС 58 (НКС Е 59) |
НКС 49 (НКС Е 50,5) |
|
НКС 54(НКС Е 55) |
НКС 43(НКС Е 44) |
НКС 56 (НКС Е 57) |
НКС 44(НКС Е 45,5) |
НКС 56 (НКС Е 57) |
НКС 44(НКС Е 45,5) |
|
НКС 48(НКС Е 49) |
НКС 25 (НКС Е 27) |
НКС 51(НКС Е 52,5) |
НКС 27(НКС Е 29) |
НКС 53(НКС Е 54) |
НКС 27(НКС Е 29) |
|
НКС 36 (НКС Е 38) |
НКС 21(НКС Е 23) |
НКС 36(НКС Е 37,5) |
НКС 24 (НКС Е 26) |
НКС 41(НКС Е 42,5) |
НКС 24 (НКС Е 26) |
|
НКС29(НКС Е 31) |
НКС 18(НКС Е 20) |
НКС 32(НКС Е 33,5) |
НКС 22 (НКС Е 24) |
НКС 35(НКС Е 36,5) |
НКС 22 (НКС Е 24) |
|
НКС 28(НКС Е 30) |
НКС 30 (НКС Е 32) |
НКС 20 (НКС Е 22) |
НКС 31(НКС Е 33) |
НКС 20 (НКС Е 22) |
||
НКС 27(НКС Е 29) |
НКС 28(НКС Е 30) |
НКС 18(НКС Е 20) |
НКС 30,5 (НКС Е 32,5) |
НКС 19 (НКС Е 21) |
||
НКС 26 (НКС Е 28) |
НКС 27(НКС Е 29) |
НКС29(НКС Е 31) |
НКС 18(НКС Е 20) |
|||
НКС25,5 (НКС Е 27,5) |
НКС 26 (НКС Е 28) |
НКС 28(НКС Е 30) |
||||
НКС 25 (НКС Е 27) |
НКС 25,5 (НКС Е 27,5) |
НКС 27,5 (НКС Е 29,5) |
||||
НКС24,5 (НКС Е 26,5) |
НКС 25 (НКС Е 27) |
НКС 27(НКС Е 29) |
||||
НКС 24 (НКС Е 26) |
НКС 24,5 (НКС Е 26,5) |
НКС 26,5 (НКС Е 28,5) |
||||
НКС23,5 (НКС Е 25,5) |
НКС 24 (НКС Е 26) |
НКС 26 (НКС Е 28) |
||||
НКС 23 (НКС Е 25) |
НКС 23,5 (НКС Е 25,5) |
НКС 25 (НКС Е 27) |
||||
НКС 22 (НКС Е 24) |
НКС 23 (НКС Е 25) |
НКС 24 (НКС Е 26) |
||||
НКС 21(НКС Е 23) |
НКС 22 (НКС Е 24) |
НКС 23 (НКС Е 25) |
||||
НКС 20 (НКС Е 22) |
НКС 21(НКС Е 23) |
НКС 22 (НКС Е 24) |
||||
НКС 20,5 (НКС Е 22,5) |
||||||
НКС 20 (НКС Е 22) |
||||||
ХАРАКТЕРИСТИКИ ПРОКАТУ, ЩО ВСТАНОВЛЮЮТЬСЯ З УГОДИ СПОЖИВАЧА З ІЗГО-ТЕВІТЕЛЕМ В НТД
1. Прокат з нормованою масовою часткою азоту сталі електровиплавки.
2 Прокат з нижньою частковою часткою марганцю, зменшеною проти норм табл. 1 на величину марганцевого еквівалента, що дорівнює:
Е ш = 0,3(Сг %)+0,5 (N1 %) + 0,7 (Сі %), де Сг, N1, Сі - залишкова фактична масова частка хрому, нікелю, міді сталі, не перевищує норм, зазначених у табл.1.
3. Прокат калібрований із сталі марок 08, 55 та 60 у нагартованому або термічно обробленому стані з контролем механічних властивостей.
4. Прокат із нормованою ударною в'язкістю на зразках типу I при температурі мінус 40°С.
5. Прокат із нормованою ударною в'язкістю на зразках типу II при температурі плюс 20°С та мінусових температурах.
6. Прокат без контролю щодо звуження.
7. Прокат калібрований та зі спеціальною обробкою поверхні з нормованою твердістю в нормалізованому з відпусткою та загартованому з відпусткою стані.
8. Прокат сортовий з нормованою твердістю у нормалізованому стані.
9. Прокат із нормованою твердістю в заданих межах.
10. Прокат без контролю жорсткості.
11. Прокат із нормованою величиною аустенітного зерна.
12. Прокат із нормованою чистотою по неметалевих включеннях.
13. Прокат із нормованою чистотою по волосинах, що виявляються на поверхні готових деталей магнітним методом або травленням.
14. Прокат малотоннажних партій.
Режими термічної обробки заготовок для контролю механічних властивостей, наведених у табл.3 та 4
Температура нагрівання, °С |
|||
Марка сталі |
Нормалізація |
||
Випробування під час розтягування |
Випробування на ударний вигин |
||
при нормалізації чи загартуванні - 30 хв;
при відпустці 200 ° С -2 год;
при відпустці 600 ° С -1ч.
Середовище охолодження при загартуванні – вода.
Режими термічної обробки заготовок контролю механічних властивостей, наведених у табл.8
а -для прокату діаметром до 25 мм
б-для прокату діамет-ром понад 25 мм ДОДАТОК 9 РекомендованеРежими термічної обробки зразків для визначення твердості після загартування, наведеної в табл.
Таблиця 2
Примітки:
1 Час витримки при загартуванні (після досягнення температури загартування) 20 хв
2. Температура олії (65±10)°С.
ДОДАТКИ 8 9(Введено додатково Змін.№ 1).
ІНФОРМАЦІЙНІ ДАНІ
1. РОЗРОБЛЕНИЙ І ВНЕСЕН Міністерством чорної металургії СРСР
2. УТВЕР5КДЕН І ВВЕДЕНИЙ У ДІЮ Постановою Державного комітету СРСР за стандартами від 24.11,88 № 3811
3. ВЗАМІН ГОСТ 1050-74
4. ПОСИЛАННІ НОРМАТИВНО-ТЕХНІЧНІ ДОКУМЕНТИ
Номер пункту, підпункту |
Номер пункту, підпункту |
||
ГОСТ 8.001-80 |
ГОСТ 7565-81 |
||
ГОСТ 8.326-89 |
ГОСТ 7566-81 |
2.5, 3.1, 3.4, 5.1, 5.1.1 |
|
1.3, 2.1.1, додаток 1 |
ГОСТ 8559-75 |
||
ГОСТ 8560-78 |
1.3, додаток 1 |
||
ГОСТ 8817-82 |
|||
ГОСТ 9012-59 |
|||
ГОСТ 1050-88 |
Додаток 1 |
ГОСТ 9013-59 |
|
ГОСТ 1051-73 |
2.1.9, 2.5.1, додаток 1 |
ГОСТ 9454-78 |
|
ГОСТ 1133-71 |
ГОСТ 10243-75 |
||
ГОСТ 1497-84 |
ГОСТ 12359-81 |
||
ГОСТ 1763-68 |
ГОСТ 14955-77 |
1.3,2.1.9,2.5.1, додаток 1 |
|
ГОСТ 2216-84 |
ГОСТ 21120-75 |
||
ГОСТ 2590-88 |
1.3, додаток 1 |
ГОСТ 21650-76 |
|
ГОСТ 2591-88 |
1.3, додаток 1 |
ГОСТ 22235-76 |
|
ГОСТ 2879-88 |
ГОСТ 22536.0-87 |
||
ГОСТ 3749-77 |
ГОСТ 22536.1-88 |
||
ГОСТ 4405-75 |
ГОСТ 22536.2-87 |
||
ГОСТ 5157-83 |
1.3, додаток 1 |
ГОСТ 22536.3-88 |
|
ГОСТ 5378-88 |
ГОСТ 22536.4-88 |
||
ГОСТ 5639-82 |
ГОСТ 22536.5-87 |
||
ГОСТ 5657-69 |
ГОСТ 22536.6-88 |
||
ГОСТ 6507-90 |
ГОСТ 22536.7-88 |
||
ГОСТ 7417-75 |
1.3, додаток 1 |
ГОСТ 22536.8-87 |
|
ГОСТ 7502-89 |
ГОСТ 22536.9-88 |
||
ГОСТ 7566-81 |
ГОСТ 24597-81 |
||
ГОСТ 7564-73 |
ГОСТ 26877-91 |
||
ГОСТ 27809-95 |
5. Обмеження терміну дії знято за протоколом № 5-94 Міждержавної Ради зі стандартизації, метрології та сертифікації (ІВС 11-12-94)
6. ПЕРЕВИДАННЯ (квітень 1996 р.) зі Зміною № 1, затвердженим у грудні 1991 р. (ІВС 4-92)