Impostazione del pezzo - tornitura. Bloccaggio nei centri durante la tornitura di parti
Tecnologia di produzione di parti su un tornio. |
La produzione di qualsiasi parte inizia con la selezione del materiale. Il materiale selezionato viene tagliato in spazi vuoti. La dimensione del pezzo supera sempre le dimensioni del pezzo finito di una certa quantità (indennità). La dimensione e la forma dell'indennità dipendono dalla forma della parte, dalla tecnologia della sua fabbricazione. |
Il legno di consistenza uniforme è più adatto per la tornitura. Questi sono betulla, tiglio, pioppo tremulo, faggio, olmo, noce. Parti di tornitura su macchine centrali
|
Riso. 1. Sequenza di tornitura del pezzo a - fissaggio del pezzo; b - fissaggio dell'incisione del pezzo; c- sgrossatura con reyer; g - finire con Meisel; e-rifilatura (sfacciatura) del pezzo. Tornitura di cavità interne Per la tornitura di superfici interne, il pezzo viene fissato solo nella testa della macchina, con un mandrino a camme, una piastra frontale o un mandrino tubolare.
|
|
Riso. 2. Tornitura cava a - sul frontalino; b- in una cartuccia tubolare. Lavorare su torni con una pinza Sui torni dotati di calibro, la lavorazione viene effettuata con frese fissate in un portautensili montato su un calibro mobile della macchina. Tali macchine, di regola, hanno un'alimentazione manuale e meccanica lungo e attraverso la macchina. Frese per tornitura. A seconda della forma della testa, gli incisivi sono divisi in dritti con asta dritta (Fig. 3 a) e piegati con asta piegata a destra oa sinistra. In base alla posizione del tagliente, si distinguono gli incisivi destro (Fig. 3d) e sinistro (Fig. 3c). Quelle destre si muovono in direzione longitudinale dalla contropunta in avanti, quelle sinistre dall'avanti al dietro. Le frese passanti (Fig. 3 a-c) sono progettate per tornire, smussare, le frese a spinta (Fig. 3 d) per girare e lavorare l'estremità formata del gradino. Le frese per cordonatura (Fig. 3 e) servono a formare un gradino all'estremità del pezzo in lavorazione, per elaborare il piano dell'estremità. Scanalature sulla parte esterna e superficie interna i dettagli possono essere ottenuti utilizzando frese per scanalare (Fig. 3 f, h). Le taglierine vengono utilizzate per il taglio (Fig. 3 g). Per la filettatura viene utilizzata una fresa filettata (Fig. 3i). Le frese sagomate vengono affilate in base alla forma del pezzo (Fig. 3 j). |
![]() |
Riso. 3. Principali tipologie di utensili per tornitura Le frese sono impostate in modo che la parte superiore della fresa coincida con il centro della contropunta. La velocità del mandrino dovrebbe essere di 1200 giri/min. Tornitura di grezzi cilindrici. |
|
Riso. 4. Tecniche di lavorazione dei grezzi cilindrici La fresa viene fatta avanzare gradualmente fino a toccare il pezzo in rotazione e in questa posizione viene retratta a destra. La fresa viene fatta avanzare di 2-3 mm lungo il limbus e la prima passata di lavoro viene eseguita lungo il pezzo. I passaggi vengono eseguiti fino ad ottenere una forma cilindrica liscia (Fig. 4 a). Dopo aver spostato la taglierina in base alle indicazioni del quadrante di alimentazione trasversale alla dimensione desiderata, viene ruotata una piccola area di prova. Se la misurazione ha mostrato che la taglierina è impostata sulla dimensione desiderata, la superficie viene lavorata per l'intera lunghezza da destra a sinistra (Fig. 4 b). Dopo la rotazione, la taglierina viene retratta. E tornano alla loro posizione originale. La stessa taglierina taglia l'estremità e le sporgenze. La faccia terminale viene tagliata finché la fresa non si avvicina al centro del pezzo (Fig. 4 c). Per la tornitura di scanalature e sporgenze rettangolari, viene utilizzata una fresa di finitura (a lama) (Fig. 4 d). Spostandola in direzione trasversale e spostando la pinza longitudinalmente, è possibile lavorare una superficie cilindrica con diametri differenti. L'alesatura viene utilizzata per selezionare i fori e le cavità interne delle parti. Il noioso è eseguito da noioso taglierina dura(Fig. 4e). Il tagliente della fresa si trova a livello dell'asse del mandrino. Durante la foratura, l'avanzamento longitudinale della fresa viene alternato ai suoi spostamenti trasversali dal bordo del pezzo al suo centro, asportando strato per strato il materiale dalla parete della cavità da ritagliare e livellandone il fondo. La tornitura di pezzi di forma complessa viene eseguita con frese sagomate |
|
Riso. 5. Opzioni per l'affilatura e l'installazione di frese sagomate Le frese sagomate sono realizzate indipendentemente da strisce di carbonio o acciaio rapido di 3-5 mm di spessore, 10-20 mm di larghezza e 100-120 mm di lunghezza. La fresa viene ruotata lungo il contorno applicato, temprata e affilata (Fig. 5 a). Le frese devono necessariamente avere un dorso delle facce laterali in modo che non vengano a contatto con il pezzo durante la lavorazione (Fig. 5 b). Ci sono due opzioni per l'installazione di una fresa sagomata (Fig. 5c) per la tornitura diretta e inversa: durante la tornitura inversa, la fresa viene capovolta e si ottiene un pezzo con un profilo inverso. Le frese sagomate possono essere alimentate al pezzo in direzione trasversale, longitudinale e ad angolo rispetto all'asse del pezzo (Fig. 5d). Per ottenere parti di vari profili complessi, è possibile utilizzare una fresa composita assemblata da frese con uno spessore di 4-8 mm, con affilatura diversa. La loro diversa combinazione permette di ottenere vari profili (Fig. 5e). Per ottenere forme lisce sia dall'esterno che dall'interno del pezzo, è possibile utilizzare una taglierina con disco da taglio. Lungo il bordo del disco viene lavorato un disco di 4-8 mm di spessore, 12-20 mm di diametro, una scanalatura con un raggio di 2-3 mm. Dopo l'indurimento, il disco viene montato con un bullone sul mandrino e affilato (Fig. 5 f). Lavorazione di una parte su una fotocopiatrice. È conveniente produrre un grande volume di parti identiche utilizzando una fotocopiatrice. Come utensile da taglio, a seconda del design della macchina, è possibile utilizzare utensili di tornitura installati nel supporto della macchina, scalpelli con enfasi o tronchesi a disco. |
|
Riso. 6. Elaborazione su una fotocopiatrice con scalpello e scalpello |
![]() |
Riso. 7. Elaborazione con una taglierina a disco su una fotocopiatrice.
Accensione di una fotocopiatrice su una macchina di supporto
Riso. 8. Elaborazione della parte secondo la fotocopiatrice
Per realizzare una fotocopiatrice, un modello di parte viene lavorato e segato lungo l'asse. La sezione risultante del profilo viene trasferita su compensato di 4-5 mm di spessore e ritagliata (Fig. 8 a). Le fotocopiatrici possono essere realizzate in metallo utilizzando il taglio laser.
Il profilo delle parti future è fissato sul basamento della macchina. Attaccato alla slitta trasversale della pinza supporto in metallo con una sonda. La punta della sonda e la fresa devono avere lo stesso profilo (Fig. 8 b).
Il primo grezzo viene preliminarmente sagomato in un cilindro con un diametro pari al diametro più grande del grezzo, gli sbozzati successivi possono essere realizzati con una piccola tolleranza. Innanzitutto, viene regolata la posizione relativa del pezzo e della fotocopiatrice (Fig. 8 c), quindi il calibro della macchina viene spostato a sinistra finché la parte superiore della sonda non è allineata con la linea diametro maggiore dettagli (Fig. 8d). La taglierina viene fatta avanzare fino a quando non si ferma contro la superficie del pezzo e la sonda poggia contro la fotocopiatrice nel punto del diametro maggiore e viene fissata in questa posizione. L'elaborazione viene eseguita da destra a sinistra. La taglierina viene alimentata al pezzo in direzione trasversale finché la sonda non si ferma nel contorno della fotocopiatrice (Fig. 8. e). Il valore dello spostamento longitudinale della fresa per una corsa trasversale è di 1-2 mm. I segni di taglio vengono rimossi con carta vetrata. La stessa fotocopiatrice può essere utilizzata per tornire pezzi dello stesso profilo, ma di diametri diversi (Fig. 8 f). Un leggero cambiamento nell'angolo della fotocopiatrice dà un restringimento della sagoma della parte. Le parti lunghe sono affilate in parti sulla fotocopiatrice. Le figure simmetriche vengono elaborate dal bordo al centro, quindi il pezzo viene capovolto e la seconda parte viene elaborata (Fig. 8g).
Selezione della modalità di taglio
La velocità del movimento di taglio principale sui torni per vari punti il tagliente è diverso e dipende dalla distanza dall'asse di rotazione del pezzo. velocità media per punto medioè determinato dalla formula:
V cp \u003d πD cp n / (60 1000)
dove D cp - il diametro medio del pezzo, mm;
N-velocità del mandrino, giri/min;
La velocità del mandrino viene selezionata in base al diametro del pezzo; quando si installa un frontalino con un diametro superiore a 400 mm, la velocità del mandrino non deve superare gli 800 giri/min.
Velocità di taglio principale per legno rocce morbide 10-12 m/s, per legno duro 0,5-3 m/s.
Avanzamento longitudinale per giro mandrino per sgrossatura 1,6-2 mm, per finitura non superiore a 0,8 mm. L'avanzamento incrociato per giro del mandrino non deve superare 1,2 mm.
Lavorazione di pezzi su torni CNC
I torni CNC hanno frese a candela come utensile da taglio o sono combinati con frese a candela e frese a disco.
Quando si lavora un pezzo con una fresa a candela, è possibile ottenere un profilo figurato diverso sul pezzo. Il movimento della fresa e la velocità di rotazione del pezzo sono impostati tramite software, a seconda della forma del pezzo futuro.
Riso. 9. Creazione di una scultura su un tornio CNC
Le macchine con tronchese e tronchesi consentono di velocizzare il processo di tornitura dei pezzi. La fresa a disco esegue la sgrossatura preliminare, fresa finitura.
Riso. 10. Lavorazione del pezzo con una taglierina a disco
Riso. 11. Lavorazione del pezzo con una fresa a candela
Dopo aver tornito il pezzo, per la finitura finale e la rimozione dei segni di taglio, viene trattato con carta vetrata, di solito viene utilizzato un pezzo di piccola larghezza, che viene spostato in uno stato teso su tutto il pezzo.
Riso. 12. Lavorazione del pezzo con carta vetrata
Letteratura:
1. Burikov V.G., Vlasov V.N. Intaglio della casa - M .: Niva della Russia insieme alla Compagnia della regione eurasiatica, 1993-352 p.
2. Vetoshkin Yu.I., Startsev V.M., Zadimidko V.T.
Arti del legno: libro di testo. indennità. Ekaterinburg: Urali. stato ingegneria forestale un-t. 2012.
3. Glikin MS Falegnameria decorativa sulla macchina "Universale" .- M.: Lesn. prom-st, 1987.-208 p.
4. Korotkov VI macchine per la lavorazione del legno: un libro di testo per cominciare. prof. Formazione scolastica. - M.6 Centro editoriale "Accademia", 203.-304 p.
5. Lerner PS, Lukyanov P.M. Attività di tornitura e fresatura: Proc. Indennità per gli studenti delle classi 8-11. media scuola - 2a ed., rivista - M.: Education, 1990. - 208 p.
A modi complicati le impostazioni del pezzo su un tornio includono: installazione in un mandrino non autocentrante a 4 griffe, su una piastra frontale, a squadra, in lune fisse e installazione di pezzi durante la lavorazione di parti eccentriche. Tutti richiedono un'impostazione speciale dell'attrezzatura o l'allineamento del pezzo rispetto all'asse di rotazione.
§ 1. Lavorazione in mandrini a 4 griffe
Per bloccare pezzi non rotondi, pezzi fusi e forgiati con superfici irregolari e altri lavori, vengono utilizzati mandrini a 4 griffe con movimento indipendente della ganascia.
Kov (fig. 236). Sono costituiti da corpo 2, supporti 3, viti 4 e camme 5. Le camme possono essere utilizzate come avanti o indietro. Il bloccaggio e il centraggio dei pezzi grezzi in tali mandrini vengono eseguiti separatamente. Il mandrino è montato sull'estremità filettata del mandrino utilizzando una flangia di adattamento 1. Per le macchine con un design mandrino flangiato, il foro di montaggio è realizzato direttamente nel corpo del mandrino.
Il corpo del mandrino a 4 griffe può essere utilizzato come piastra frontale per il montaggio e il bloccaggio di pezzi con superficie di appoggio lavorata. A tale scopo, fornisce scanalature allungate per l'installazione dei bulloni di montaggio. Le cartucce sono fatte varie dimensioni*con diametro esterno da 160 a 1000 mm.
Una caratteristica della lavorazione di pezzi in tali mandrini è la necessità di allineare l'asse della superficie da lavorare con l'asse del mandrino (mandrino). Questo viene fatto riconciliando gli spazi vuoti in base al rischio gesso o in base al markup,
Nel primo caso (Fig. 237, a), un pezzo di gesso viene portato sulla superficie verificata di un pezzo in lenta rotazione e la sua concentricità con l'asse di rotazione è determinata dal tipo di rischio gesso. Per non danneggiare le mani, la barra di gesso è posta all'incirca a livello dell'asse del pezzo con una leggera pendenza verso il basso, e per una maggiore stabilità mano destra supporto sinistro. Se la traccia del rischio si trova lungo l'intera circonferenza, cosa molto rara al primo controllo, allora la posizione del pezzo
Corretta.
Quando il rischio rimane solo su una piccola area della superficie da controllare, la posizione del pezzo viene regolata spostando le camme opposte al rischio.
Se il pezzo ha una superficie relativamente piana o pretrattata, un allineamento simile viene eseguito con uno spessimetro da banco, come mostrato in fig. 237b. L'ago spessimetro, installato su un'apposita piastra o sul piano superiore della slitta a croce, viene portato in superficie da controllare con un piccolo spazio vuoto e, attivando la bassa velocità del mandrino, se ne determina l'uniformità attorno alla circonferenza. .Quindi il titolo è finalmente corretto.
Secondo il secondo metodo, l'allineamento viene eseguito segnando all'estremità del pezzo utilizzando il centro posteriore o uno spessimetro.
La parte superiore del centro posteriore viene inserita nell'incavo punzonato nel punto di intersezione delle linee di marcatura del centro (Fig. 237, c), il pezzo viene premuto con il centro all'estremità del corpo del mandrino e fissato con camme in questa posizione .
Quando si riconcilia con uno spessimetro (Fig. 237, d), viene installato. il piano della slitta a croce della pinza o una piastra speciale. L'ago spessimetro, posto all'altezza della sommità del centro posteriore, viene portato alle linee centrali della faccia terminale del pezzo e la posizione di ciascuna linea viene verificata alternativamente mediante movimento trasversale. In questo caso, la linea centrale, quando il pezzo viene ruotato di 180°, deve essere abbinata alla parte superiore dell'ago spessimetro per l'intera lunghezza.
Queste riconciliazioni vengono eseguite solo durante la fabbricazione della prima parte del lotto. Le parti rimanenti sono orientate correttamente in un mandrino a 4 griffe premendo contro due griffe adiacenti che non si muovono quando si staccano i pezzi.
§ 2. Lavorazione su un frontalino e un quadrato
Le parti a forma libera come leve o custodie che non possono essere installate correttamente in un mandrino a 4 griffe sono fissate su un frontalino. A questo metodo di installazione si ricorre anche se si vuole mantenere una rigorosa perpendicolarità dell'asse della superficie da lavorare all'estremità, o base del pezzo.
La piastra frontale 1 (Fig. 238) è un disco in ghisa con un mozzo, rinforzato sul retro con rinforzi,
I fori del mozzo sono realizzati in base alla forma dell'estremità anteriore del mandrino, su cui è installato e fissato il frontalino.
L'estremità anteriore del frontalino è rigorosamente perpendicolare al suo asse. Ha scanalature a T e passanti per il montaggio dei bulloni. Il frontalino ricorda il corpo di un mandrino a 4 griffe, che a volte viene utilizzato per lo stesso scopo.
Il pezzo viene premuto contro l'estremità del frontalino con morsetti e bulloni e, per evitare spostamenti durante la lavorazione, viene ulteriormente premuto con supporti laterali. Questo fissaggio è mostrato in Fig. 238. La parte 4 viene premuta contro il frontalino con due morsetti 2 e bulloni 3. L'estremità anteriore del morsetto poggia sulla parte, l'estremità posteriore poggia sul supporto 8. I supporti laterali qui sono le viti 6, che sono avvitate nel 5 quadrati attaccati al frontalino.
I pezzi montati sul frontalino devono avere un'estremità di supporto (rivolta verso il frontalino) lavorata in modo pulito. Quando li risolvi, devi rispettare le seguenti regole.
1. I bulloni di fissaggio devono essere posizionati il più vicino possibile alla parte per creare una presa più forte.
2. Serrare i dadi in diagonale prima debolmente, poi infine.
3. Montare i morsetti, se possibile, nei punti della parte che sono supportati sul frontalino.
4. Se non è possibile seguire la terza regola, non serrare troppo i dadi per evitare di piegare il pezzo.
5. Sollevare i supporti di supporto ad un'altezza tale che i morsetti
posizionato parallelamente al piano di lavoro del frontalino.
Il primo pezzo grezzo del lotto viene verificato sul frontalino allo stesso modo del mandrino a 4 griffe. Con i dadi leggermente premuti, può essere spostato in qualsiasi luce laterale colpi di martello. Il resto degli spazi vuoti è orientato correttamente dai supporti laterali.
Se il baricentro del pezzo viene spostato dall'asse di rotazione, viene utilizzata la bilanciatura a contrappeso 7 (Fig. 238). Il bilanciamento viene eseguito in questo ordine. Il contrappeso viene prima fissato sul frontalino a una certa distanza dal suo asse, opposto al baricentro del pezzo. Quindi, dopo aver scollegato il mandrino dal meccanismo del cambio, ruotare manualmente il frontalino. Se quest'ultimo si ferma in posizioni diverse, il bilanciamento è corretto. In caso contrario, il contrappeso viene spostato nella direzione desiderata dall'asse di rotazione e l'equilibratura viene ripetuta nuovamente.
Le parti con una disposizione parallela o angolare dell'asse della superficie da lavorare alla base sono installate sul quadrato 4 (Fig. 239), che è fissato al frontalino con bulloni e dadi 5. Parte 3 (in questo caso, la sede del cuscinetto), a sua volta, è fissata sul ripiano orizzontale della squadra con i morsetti 2 e bilanciata dal contrappeso 1.
L'allineamento del primo pezzo del lotto insieme al quadrato viene eseguito con uno dei metodi sopra indicati in base al rischio di gesso o alla marcatura.
Per questi lavori possono essere utilizzati anche. Mandrino a 4 griffe, una delle quali è sostituita da una squadra.
§ 3. Lavorazione in stazionari
Le pause fisse sono chiamate dispositivi di supporto aggiuntivi utilizzati nella lavorazione di alberi non rigidi.
Gli alberi la cui lunghezza supera i 12-15 diametri sono generalmente considerati non rigidi. Tali parti si piegano, vibrano sotto l'azione della forza di taglio e del proprio peso, che provoca la scheggiatura della fresa, degrada la qualità della lavorazione e costringe a una riduzione della modalità di taglio, aumenta la produttività, gli alberi lunghi sono supportati da lunghe fisse.
I torni sono dotati di lunette scopo generale due tipi: fisso e mobile.
Il supporto fisso (Fig. 240, a) è costituito da una base 7, un coperchio incernierato 3 e tre camme 2 con movimento indipendente. La lunetta è installata sulle guide centrali del telaio 10 ed è fissata con una staffa 9, che viene premuta contro le battute delle guide con un bullone e un dado 8. Le camme possono essere spostate radialmente mediante viti ruotando le maniglie 4 e fissato nella posizione richiesta dai morsetti 5. Il coperchio 3, collegato alla base dall'asse 1, quando rilasciato il morsetto 6 può essere scartato per installare il pezzo nella lunetta. Le punte delle camme sono intercambiabili. Loro sono
in ghisa o bronzo. Per lavorare con velocità di taglio elevate, vengono invece installati cuscinetti volventi.
La lunetta mobile (Fig. 240, b) è costituita da un corpo 5, la cui parte superiore è piegata a destra, e due camme regolabili 2 con movimento indipendente. Quest'ultimo può essere spostato e fissato nella posizione desiderata con le maniglie 4 e 3. La lunetta è installata e fissata con viti 6 sul lato sinistro del carrello pinza 1.
Si consideri la lavorazione di parti mediante lunette (Fig. 241).
Prima di installare il pezzo in una lunetta fissa, viene lavorata una scanalatura poco profonda (circa al centro)
più largo delle camme della lunetta per eliminare l'eccentricità di questa zona della superficie. Per evitare la flessione del pezzo, la scanalatura viene lavorata con una fresa a spinta passante con un angolo di inclinazione negativo del tagliente principale. La profondità di taglio e avanzamento deve essere ridotta.
Un albero molto lungo può piegarsi anche con un'attenta scanalatura. In questo caso, la scanalatura viene prima ruotata un po' più vicino alla paletta, in questo punto viene installata una lunetta, quindi viene realizzata una seconda scanalatura nel mezzo della parte.
Successivamente, la lunetta viene installata e fissata sul telaio in modo che si trovi contro la scanalatura dell'albero. Le sue camme sono uniformemente, senza forte pressione, portate sulla superficie della scanalatura e fissate. Quando si eseguono queste azioni, si dovrebbe tenere conto della possibilità di flessione della parte in caso di bloccaggio irregolare della camma. Per evitare ciò, le camme fisse possono essere prima montate su un collo corto, che viene lavorato all'estremità dell'albero al centro posteriore. Il diametro di un tale collo aggiuntivo è realizzato in base al diametro della scanalatura per le camme della lunetta.
Quando si fabbrica un lotto di parti, è conveniente installare le camme di arresto fisso una volta, prima del lavoro, su un mandrino rigido corto.
Dopo aver fissato il pezzo sulla macchina, viene girata prima una metà dell'albero (verso la lunetta), quindi, dopo la reinstallazione, la parte rimanente. La lunetta è installata secondariamente lungo la superficie lavorata dell'asta. Per ridurre l'attrito, la scanalatura per le camme della lunetta è lubrificata con olio.
Le lunghe fisse vengono utilizzate anche per spianare, centrare e forare all'estremità di un albero lungo se quest'ultimo non si adatta al foro del mandrino. In questo caso, l'albero
un'estremità è fissata nel mandrino e l'altra estremità è installata nelle camme della lunetta.
La lunetta mobile viene utilizzata durante la lavorazione di lunghe superfici cilindriche. I suoi pugni si sbarazzano a destra dell'incisivo a una distanza di 10-15 mm. Viene eseguito lo spostamento tagliente richiesto diapositiva superiore calibro.
Le camme di lunetta sono installate sulla superficie lavorata della prima parte del lotto. Per fare ciò, macina prima alla fine piccola trama 20-25 mm di lunghezza al diametro richiesto, al quale si avvicinano le camme fisse. Se il lavoro viene eseguito senza raffreddamento, è necessario leccare periodicamente con olio la superficie trattata davanti alle camme della lunetta.
Gli alberi lunghi non rigidi, anche se lavorati in lunetta, sono ottenuti con una deflessione. Pertanto, vengono corretti prima di terminare la tornitura. La modifica viene eseguita con la parentesi corretta (Fig. 242) come segue. Alla superficie di un albero rotante al centro in vari posti un pezzo di gesso viene portato lungo la lunghezza, mentre su di esso rimangono segni di gesso, che mostrano il luogo della deviazione. Se tutte le tracce sono su un lato dell'albero, la deflessione è unilaterale.
Il luogo della massima deviazione è determinato dall'ampiezza dell'arco della traccia di gesso. Dove la deflessione è maggiore, la lunghezza dell'arco è più breve. In questo punto è installata la vite 1 della staffa 2 corretta, come mostrato in fig. 242. Poiché lo stelo si allunga leggermente durante la medicazione, il centro posteriore segue prima di questo
allentare leggermente.
Spesso l'albero ha una deflessione complessa in diverse direzioni. In questo caso, la direzione di deflessione predominante si trova dalle tracce di gesso. In primo luogo, vengono corretti i tratti in cui la direzione della deflessione è opposta a quella prevalente, in modo da ottenere una deflessione unilaterale generale. Quindi l'albero viene raddrizzato, come indicato sopra.
§ 4. Lavorazione di parti eccentriche
Queste parti includono eccentrici, eccentrici e alberi a gomiti (Fig. 243). Sono caratterizzati dalla presenza di superfici con assi paralleli spostati. La quantità di spostamento degli assi è chiamata eccentricità.
La lavorazione di particolari eccentrici su tornio può essere effettuata: 1) c. mandrino a 3 griffe; 2) su un mandrino; 3) in un mandrino a 4 griffe o su piastra frontale; 4) tramite fotocopiatrice; 5) nei centri sfollati; 6). utilizzando centrifughe.
Elaborazione eccentrica. Gli eccentrici di piccola lunghezza possono essere lavorati in uno dei primi quattro modi.
In un mandrino a 3 griffe, l'asse della superficie eccentrica lavorata è allineato con l'asse di rotazione installando un rivestimento sotto una delle ganasce della cartuccia (Fig. 244, a). Il suo spessore con una precisione sufficiente per la pratica può essere determinato dalla formula
Per ridurre l'errore di installazione, si consiglia di tagliare il rivestimento dall'anello, il cui foro è realizzato in base al diametro del pezzo. Sul lato convesso del rivestimento, gli angoli sono tagliati in modo che la piattaforma di supporto b sia inferiore alla larghezza della superficie di lavoro della camma.
Se il pezzo eccentrico ha un foro precedentemente realizzato, viene lavorato con l'installazione sul mandrino (Fig. 244, b). Alle estremità di quest'ultimo ci sono due coppie di fori centrali, sfalsati dalla quantità di eccentricità. La lavorazione viene effettuata per due installazioni nei centri. Nella prima impostazione, rispetto ai fori A-A, la superficie G è tornita, nella seconda
Per quanto riguarda i fori B-B, la superficie C è tornita.
La superficie sfalsata dell'eccentrico può anche essere lavorata in un mandrino a 4 griffe o piastra frontale. In questo caso, la posizione della superficie lavorata viene rilevata all'estremità del pezzo mediante marcatura, quindi il suo asse viene combinato con l'asse del mandrino con uno dei metodi descritti in Fig. 237, Vig.
Quando si ruota l'eccentrico lungo la fotocopiatrice (Fig. 244, c), sul mandrino 2 sono installati una fotocopiatrice 3, un manicotto intermedio 4, un pezzo 5, una rondella 6, fissata con un dado 7. Il mandrino è installato con un gambo conico nel foro del mandrino e serrato con una vite lunga o premuto dal centro posteriore. Nel portautensili sono fissati un rullo largo 1 e una taglierina 8. Il rullo è premuto saldamente contro la fotocopiatrice da una molla installata nella pinza al posto della vite di alimentazione a croce. Quando si attiva il movimento longitudinale della pinza, la taglierina girerà la parte lungo il profilo della fotocopiatrice.
Lavorazione di eccentrici e alberi a gomiti. Le superfici di tali alberi vengono lavorate in centri sfalsati, se posizionate sulle estremità - parti o con l'aiuto di traslatori centrali.
Il primo modo è mostrato in Fig. 245 a. Per fare ciò, il pezzo viene prima girato in modo normale centri A-A fino al diametro D. La seconda coppia di fori centrali B-B viene contrassegnata e punzonata alle estremità del pezzo, dopodiché viene perforata. Per piccoli pezzi, questo può essere fatto manualmente centrando su un tornio. In questo caso, la punta centrale viene installata nel mandrino della macchina mediante un mandrino di perforazione e il pezzo, bloccato nella mano sinistra, è supportato da un incavo punzonato sul centro posteriore e fatto avanzare verso la punta spostando la punta della contropunta.
Per pezzi di grandi dimensioni, i fori centrali sfalsati vengono realizzati su macchine di centraggio o mediante un dispositivo speciale - una maschera su macchine di perforazione.
Se l'eccentricità è grande e non consente di posizionare fori centrali sfalsati all'estremità del pezzo, vengono realizzati in centrifughe rimovibili, che sono fissate ai perni di estremità pre-torniti dell'albero. In questo caso, la coppia di fori centrali sfalsati deve trovarsi rigorosamente sullo stesso piano diametrale. Un esempio di tale metodo di lavorazione dell'albero a gomiti è mostrato in Fig. 245b. I colli indigeni 3 vengono ruotati durante l'installazione del pezzo lungo il centro fori A-A i traslatori centrali 7, i perni di biella 2 e 5, rispettivamente, nel centro sfalsato fori B-B e V-V.
Il bilanciamento delle parti sbilanciate viene effettuato con un contrappeso 7, che è fissato sulla piastra di guida 8, e la rigidità dell'albero è aumentata dalle aste distanziatrici 4 e 6.
Al principale
sezione cinque
Operazioni di base e lavoro,
eseguita al tornio
Capitolo XI
Tornitura di superfici cilindriche esterne
Sui torni è possibile lavorare pezzi le cui superfici hanno la forma di corpi di rivoluzione. La maggior parte delle parti utilizzate nell'ingegneria meccanica ha superfici cilindriche, come rulli, boccole, ecc.
1. Frese per tornitura longitudinale
Per la tornitura longitudinale vengono utilizzate frese passanti. Le taglierine di passaggio sono divise in bozza e finitura.
Le frese per sgrossatura (Fig. 99) sono progettate per la sgrossatura - pelatura, eseguita per rimuovere rapidamente il metallo in eccesso; sono spesso chiamati ruvidi. Tali frese sono solitamente realizzate con una piastra saldata o saldata o fissata meccanicamente e sono dotate di un lungo bordo tagliente. La parte superiore della fresa è arrotondata lungo il raggio r = 1-2 mm. Sulla fig. 99, ma mostra la fresa della retta grossolana, e in fig. 99, b - piegato. La forma piegata della taglierina è molto comoda quando si girano le superfici di parti situate vicino alle ganasce della cartuccia e per tagliare le estremità. Dopo la tornitura con una sgrossatrice, la superficie del pezzo presenta grossi rischi; la qualità della superficie lavorata è quindi bassa.
Le frese di finitura vengono utilizzate per la tornitura finale dei pezzi, ovvero per ottenere dimensioni precise e una superficie di lavorazione pulita e uniforme. Esistere diversi tipi taglierine pulite.
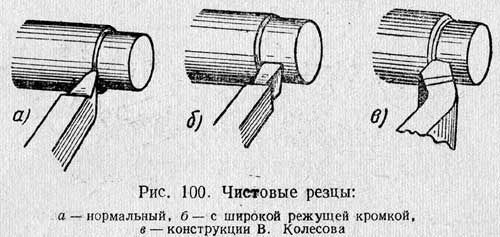
Sulla fig. 100, a mostra una fresa di finitura, che si differenzia da quella di sformo principalmente per un ampio raggio di curvatura pari a 2-5 mm. Questo tipo di taglierina è usata per finendo il lavoro, che vengono prodotti con una piccola profondità di taglio e un basso avanzamento. Sulla fig. 100b mostra una fresa di finitura con un ampio tagliente parallelo all'asse del pezzo. Questa fresa consente una rimozione fine dei trucioli ad elevate velocità di avanzamento e produce una finitura superficiale pulita e liscia. Sulla fig. 100, c mostra la fresa di V. Kolesov, che consente di ottenere una superficie pulita e levigata quando si lavora con un avanzamento elevato (1,5-3 mm / giro) con una profondità di taglio di 1-2 mm (vedere Fig. 62 ).
2. Installazione e fissaggio della taglierina
Prima di girare, è necessario installare correttamente la fresa nel portautensile, assicurandosi che la parte della fresa che sporge da essa sia il più corta possibile - non più di 1,5 dell'altezza del suo nucleo.
Con una sporgenza più lunga, la fresa tremerà durante il funzionamento, di conseguenza la superficie lavorata risulterà irregolare, ondulata, con tracce di schiacciamento.
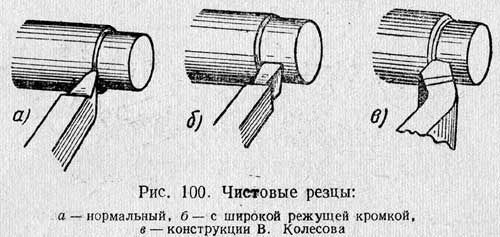
Sulla fig. 101 mostra la corretta e non corretta installazione della fresa nel portautensile.
Nella maggior parte dei casi, si consiglia di impostare la punta dell'utensile all'altezza dei centri della macchina. Per questo vengono utilizzate fodere (non più di due), posizionandole sotto l'intera superficie di appoggio della taglierina. Linerè un righello piatto in acciaio lungo 150-200 mm, con superfici superiore e inferiore rigorosamente parallele. Il tornitore deve disporre di una serie di tali rivestimenti di diversi spessori in modo da ottenere l'altezza necessaria per l'installazione della fresa. Le piastre casuali non dovrebbero essere utilizzate per questo scopo.
Le fodere devono essere posizionate sotto la taglierina come mostrato in Fig. 102 in alto.
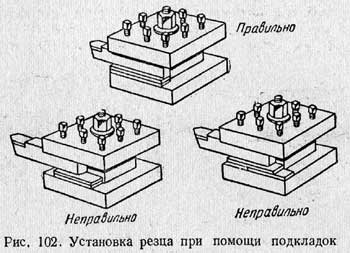
Per verificare la posizione della sommità dell'incisivo in altezza, portare la sommità dello stesso in uno dei centri precalibrati, come mostrato in Fig. 103. Allo stesso scopo si può utilizzare il rischio disegnato sulla penna della contropunta, all'altezza del centro.
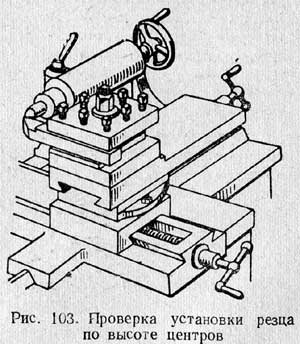
Il fissaggio della fresa nel portautensile deve essere affidabile e durevole: la fresa deve essere fissata con almeno due bulloni. I bulloni che fissano la taglierina devono essere serrati in modo uniforme e stretto.
3. Installazione e fissaggio delle parti nei centri
Un modo comune per elaborare le parti sui torni è lavorazione nei centri(Fig. 104). Con questo metodo, i fori centrali sono preforati alle estremità del pezzo - centro dettaglio. Una volta installato sulla macchina, i punti dei centri della parte anteriore e delle contropunte della macchina entrano in questi fori. Per trasferire la rotazione dal mandrino della paletta al pezzo, mandrino del conducente 1 (Fig. 104), avvitato al mandrino della macchina, e morsetto 2, fissata con la vite 3 sul pezzo.
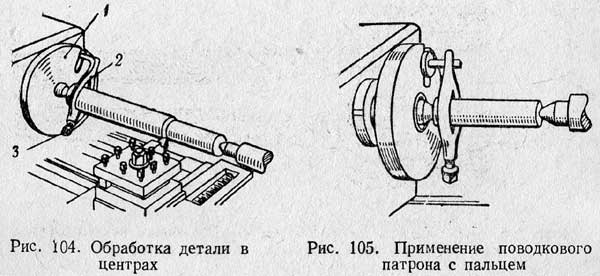
L'estremità libera del morsetto viene catturata dalla scanalatura (Fig. 104) o dal dito (Fig. 105) della cartuccia e fa ruotare la parte. Nel primo caso, il morsetto viene piegato (Fig. 104), nel secondo dritto (Fig. 105). Il mandrino a perno mostrato in fig. 105, costituisce un pericolo per il lavoratore; più sicuro è un mandrino guida con coperchio di sicurezza (Fig. 106).
accessori essenziali tornio sono centri. Di solito il centro mostrato in Fig. 107, a.
È costituito da un cono 1, su cui è montato il pezzo, e da un gambo conico 2. Il gambo deve adattarsi esattamente al foro conico del mandrino della paletta e del cannotto della contropunta della macchina.
Il centro anteriore ruota con il mandrino e il pezzo, mentre il centro della contropunta è nella maggior parte dei casi fermo e sfrega contro la parte rotante. L'attrito si riscalda e consuma sia la superficie conica del centro che la superficie del foro centrale della parte. Per ridurre l'attrito, è necessario lubrificare il centro posteriore.
Quando si girano pezzi ad alta velocità, così come quando si lavorano pezzi pesanti, è impossibile lavorare su un centro fisso della contropunta a causa della rapida usura del centro stesso e dello sviluppo di un foro centrale.
In questi casi, fare domanda centri rotanti. Sulla fig. 108 mostra uno dei disegni del centro rotante inserito nel foro rastremato del cannotto della contropunta. Il centro 1 ruota nei cuscinetti a sfere 2 e 4. La pressione assiale è percepita dal cuscinetto a sfere reggispinta 5. Il gambo conico 3 del corpo centrale corrisponde al foro conico del cannotto.
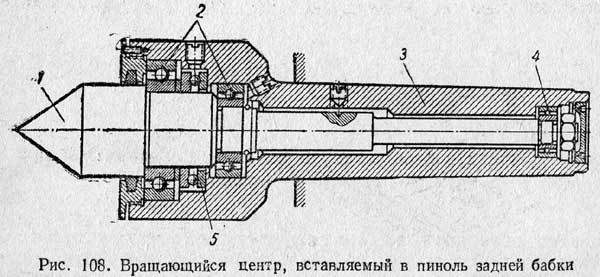
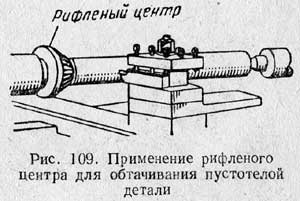
Per ridurre i tempi di fissaggio delle parti, al posto dei morsetti vengono spesso utilizzati morsetti con bloccaggio manuale. centri anteriori scanalati(Fig. 109), che oltre a centrare la parte, fungono anche da guinzaglio. Quando vengono premute dal centro posteriore, le corrugazioni tagliano il pezzo e quindi gli trasmettono la rotazione. Per le parti cave vengono utilizzati esterni (Fig. 110, a) e per i rulli centri ondulati interni (inversi) (Fig. 110, b).
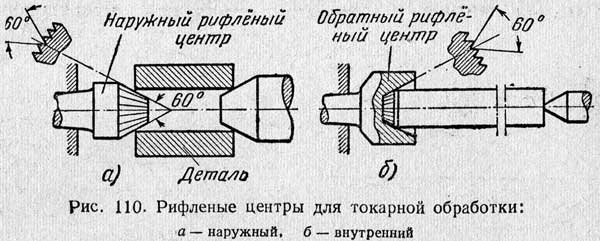
Questo metodo di fissaggio consente di ruotare la parte per l'intera lunghezza in un'unica impostazione. La tornitura degli stessi pezzi con un centro e un colletto convenzionali può essere eseguita in due sole impostazioni, il che aumenta notevolmente il tempo di lavorazione.
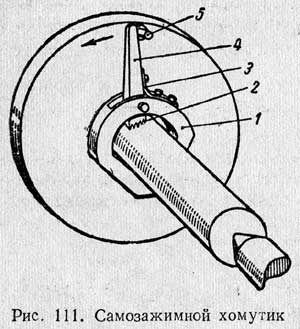
Per lavori di tornitura leggera e media morsetti autobloccanti. Uno di questi collari è mostrato in Fig. 111. Nel corpo 1 di tale collare, una camma 4 è installata sull'asse, la cui estremità ha una superficie ondulata 2. Dopo aver installato il collare sulla parte, la superficie corrugata della camma viene premuta contro la parte sottostante l'azione della primavera 3. Dopo l'installazione nei centri e l'avviamento della macchina, il perno 5 del mandrino di trascinamento, premendo la camma 4, blocca il pezzo e lo mette in rotazione. Questi morsetti autobloccanti riducono notevolmente i tempi non produttivi.
4. Predisposizione della macchina per la lavorazione nei centri
Per ottenere una superficie cilindrica quando si gira il pezzo nei centri, è necessario che i centri anteriore e di riferimento si trovino sull'asse di rotazione del mandrino e la fresa si muova parallelamente a questo asse. Per verificare la corretta posizione dei centri, è necessario spostare il centro posteriore in avanti (Fig. 112). Se i punti centrali non si allineano, la posizione dell'alloggiamento della contropunta sulla piastra deve essere regolata come indicato a pagina 127.
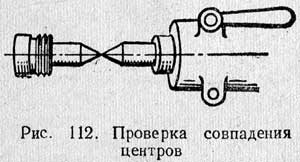
Il disallineamento centrale può anche essere causato da sporco o trucioli che entrano nei fori conici del mandrino o nei pi-zeri. Per evitare ciò, è necessario pulire accuratamente i fori del mandrino e gli aculei, nonché la parte conica dei centri, prima di installare i centri. Se il centro della paletta, come si suol dire, "batte", allora è difettoso e deve essere sostituito con un altro.
Durante la rotazione, la parte si riscalda e si allunga, creando al contempo una maggiore pressione sui centri. Per evitare che la parte si pieghi e che il centro posteriore si inceppi, si consiglia di rilasciare di tanto in tanto il centro posteriore, quindi serrarlo nuovamente alla normalità. È inoltre necessario lubrificare periodicamente il foro centrale posteriore del pezzo.
5. Installazione e fissaggio delle parti nei mandrini
Le parti corte vengono solitamente installate e fissate in mandrini, che sono suddivisi in semplici e autocentranti.
Le cartucce semplici sono solitamente realizzate con quattro ganasce (Fig. 113). In tali cartucce, ciascuna camma 1, 2, 3 e 4 è mossa dalla propria vite 5 indipendentemente dalle altre. Ciò consente di installare e fissare al loro interno varie parti di forme sia cilindriche che non. Quando si installa una parte in un mandrino a quattro griffe, deve essere accuratamente allineata in modo che non colpisca durante la rotazione.
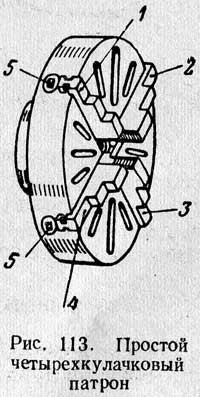
L'allineamento della parte durante la sua installazione può essere effettuato utilizzando uno spessimetro. Il incisore di profondità viene portato in superficie da controllare, lasciando uno spazio di 0,3-0,5 mm tra di loro; ruotando il mandrino, monitorare come cambia questa distanza. In base ai risultati dell'osservazione, alcune camme vengono estratte e altre vengono premute fino a quando lo spazio non diventa uniforme attorno all'intera circonferenza del pezzo. Dopodiché, la parte è finalmente riparata.
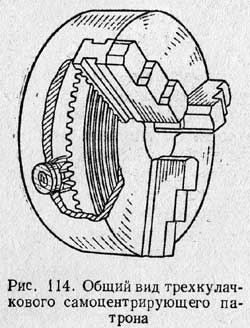
Mandrini autocentranti(Fig. 114 e 115) nella maggior parte dei casi vengono utilizzate tre camme, molto meno spesso: due camme. Questi mandrini sono molto comodi da usare, poiché tutte le camme in essi contenute si muovono contemporaneamente, in modo che una parte che ha una superficie cilindrica (esterna o interna) sia installata e bloccata esattamente lungo l'asse del mandrino; inoltre si riducono notevolmente i tempi di installazione e fissaggio del pezzo.
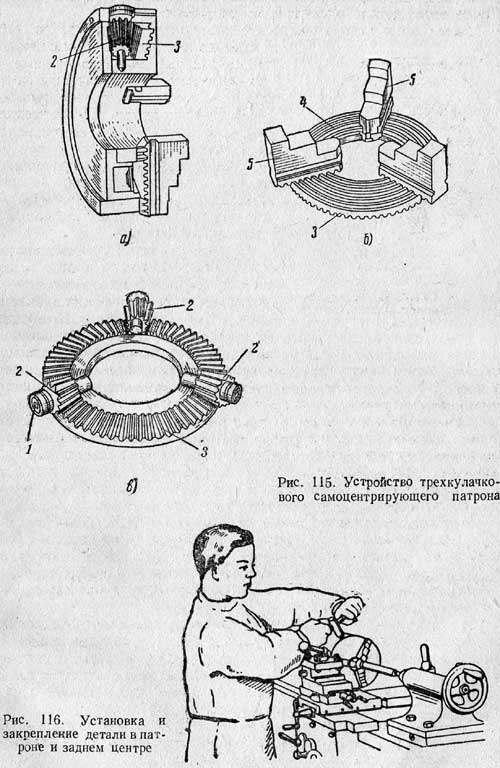
In esso, le camme vengono spostate tramite una chiave, che viene inserita nel foro tetraedrico 1 di uno dei tre ingranaggi conici 2 (Fig. 115, c). Queste ruote sono accoppiate con una grande ruota conica 3 (Fig. 115, b). Sul lato piatto inverso di questa ruota, viene tagliata una scanalatura a spirale multigiro 4 (Fig. 115, b). Tutte e tre le camme 5 entrano nelle singole spire di questa scanalatura con le loro sporgenze inferiori.Quando uno degli ingranaggi 2 viene ruotato con una chiave, la rotazione viene trasferita alla ruota 3 che, ruotando, attraverso la scanalatura a spirale 4 si sposta lungo le scanalature del corpo della cartuccia contemporaneamente e in modo uniforme tutte e tre le camme. Quando il disco con una scanalatura a spirale ruota in una direzione o nell'altra, le camme si avvicinano o si allontanano dal centro, rispettivamente bloccando o rilasciando il pezzo.
È necessario assicurarsi che la parte sia saldamente fissata nelle ganasce del mandrino. Se la cartuccia è buone condizioni, quindi si assicura un forte bloccaggio del pezzo utilizzando una chiave con impugnatura corta (Fig. 116). In nessun caso dovrebbero essere consentiti altri metodi di bloccaggio, come il bloccaggio con una chiave e un lungo tubo che passa sopra la maniglia.
Mandibole di Chuck. Le camme vengono utilizzate temprate e grezze. Le camme temprate vengono solitamente utilizzate a causa della loro bassa usura. Ma quando si fissano parti con superfici lavorate in modo pulito con tali camme, sulle parti rimangono tracce sotto forma di ammaccature dalle camme. Per evitare ciò, si consiglia inoltre di utilizzare ganasce grezze (non temprate).
Le camme grezze sono anche convenienti in quanto possono essere periodicamente annoiate con una taglierina ed eliminano il battito della cartuccia, che inevitabilmente compare durante il suo lungo funzionamento.
Inserimento e bloccaggio di parti in un mandrino con supporto centrale posteriore. Questo metodo viene utilizzato durante la lavorazione di parti lunghe e relativamente sottili (Fig. 116), che non sono sufficienti per essere fissate solo nel mandrino, poiché la forza della fresa e il peso della parte sporgente possono piegare la parte e strapparla del mandrino.
Mandrini a pinza. Per fissare rapidamente pezzi corti di piccolo diametro alla superficie esterna lavorata, vengono utilizzati mandrini a pinza. Tale cartuccia è mostrata in Fig. 117. La cartuccia con gambo conico 1 è installata nel foro conico del mandrino della paletta. Un manicotto a molla diviso 2 con un cono, chiamato colletto, è installato nell'incavo della cartuccia. Il pezzo viene inserito nel foro 4 della pinza. Quindi avvitano il dado 3 sul corpo del mandrino con una chiave.Quando si avvita il dado, il colletto a molla viene compresso e fissa la parte.
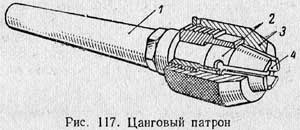
Mandrini pneumatici. Sulla fig. 118 mostra uno schema di un mandrino pneumatico che fornisce un fissaggio rapido e affidabile delle parti.
All'estremità sinistra del mandrino è fissato un cilindro pneumatico, all'interno del quale è presente un pistone. L'aria compressa attraverso i tubi entra nei canali centrali 1 e 2, da dove viene diretta alla cavità destra o sinistra del cilindro. Se l'aria entra attraverso il canale 1 nella cavità sinistra del cilindro, il pistone sposta l'aria dalla cavità destra del cilindro attraverso il canale 2 e viceversa. Il pistone è collegato ad uno stelo 3 collegato ad uno stelo 4 e ad un cursore 5, che agisce sui bracci lunghi 6 delle manovelle, i cui bracci corti 7 muovono le ganasce di bloccaggio 8 della cartuccia.
La lunghezza della corsa delle camme è di 3-5 mm. La pressione dell'aria è solitamente dalle 4 alle 5 del mattino. Per azionare il cilindro pneumatico, sulla scatola del cambio è installata una valvola di distribuzione 9, che viene ruotata dalla maniglia 10.
6. Avvitamento e svitamento dei mandrini a ganasce
Prima di avvitare il mandrino sul mandrino, pulire accuratamente i filetti all'estremità del mandrino e nel foro del mandrino con uno straccio e quindi lubrificarli con olio. Una cartuccia leggera viene portata con entrambe le mani direttamente all'estremità del mandrino e avvitata fino alla rottura (Fig. 119). Si consiglia di mettere una cartuccia pesante sulla scheda (Fig. 120), portando il suo foro all'estremità del mandrino, avvitare la cartuccia a rotture, come nel primo caso, a mano. Quando si avvita il mandrino, assicurarsi che gli assi del mandrino e del mandrino siano esattamente gli stessi.
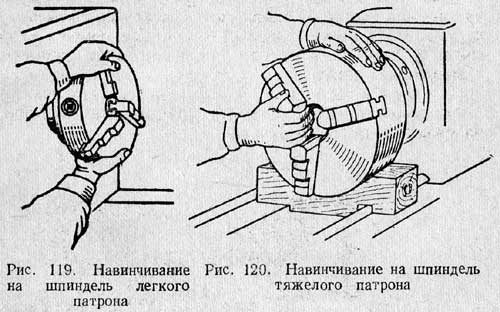
Per evitare casi di svitamento automatico delle cartucce nelle macchine per il taglio ad alta velocità, viene utilizzato un fissaggio aggiuntivo della cartuccia sul mandrino utilizzando vari dispositivi.
(avvitando un dado aggiuntivo, fissando la cartuccia con cracker sagomati, ecc.).
L'avvitamento della cartuccia si effettua come segue. Inserite una chiave nella cartuccia e con entrambe le mani fate uno scatto verso di voi (fig. 121).
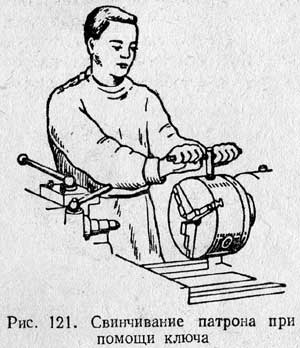
Altri metodi di trucco, associati a colpi acuti al mandrino o alle mascelle, sono inaccettabili: il mandrino è danneggiato, le camme nel suo corpo sono allentate.
Avvitare e svitare una cartuccia pesante è meglio farlo con l'aiuto di un lavoratore ausiliario.
7. Tecniche per la tornitura di superfici cilindriche lisce
La tornitura delle superfici cilindriche viene solitamente eseguita in due fasi: prima viene sgrossata gran parte del sovrametallo (3-5 mm per diametro), quindi la parte rimanente (1-2 mm per diametro).
Per ottenere un determinato diametro del pezzo, è necessario impostare la fresa alla profondità di taglio richiesta. Per impostare la taglierina alla profondità di taglio, è possibile utilizzare il metodo dei chip di prova o utilizzare il selettore di avanzamento trasversale.
Per impostare la taglierina alla profondità di taglio (per dimensione) utilizzando il metodo dei chip di prova, è necessario:
1. Riportare i dettagli del movimento rotatorio.
2. Ruotando il volantino di avanzamento longitudinale e la maniglia della coclea di avanzamento trasversale, portare manualmente la taglierina all'estremità destra del pezzo in modo che la sua sommità tocchi la superficie del pezzo.
3. Dopo aver impostato il momento di contatto, spostare manualmente la taglierina a destra del pezzo e, ruotando la maniglia della vite di avanzamento trasversale, spostare la taglierina alla profondità di taglio desiderata. Successivamente, la parte viene girata con alimentazione manuale ad una lunghezza di 3-5 mm, fermare la macchina e misurare il diametro del piano tornito con un calibro (Fig. 122). Se il diametro risulta essere superiore a quello richiesto, la fresa viene retratta a destra e impostata a una profondità leggermente maggiore, la cintura viene nuovamente lavorata e la misurazione viene ripetuta. Tutto questo viene ripetuto fino ad ottenere la dimensione desiderata. Quindi attivare l'avanzamento meccanico e rettificare la parte per l'intera lunghezza specificata. Al termine, spegnere l'avanzamento meccanico, riprendere la taglierina e fermare la macchina.
La finitura viene eseguita nello stesso ordine.
Usando il quadrante della vite di alimentazione incrociata. Per accelerare l'installazione della fresa alla profondità di taglio, la maggior parte dei torni dispone di uno strumento speciale. Si trova sull'impugnatura della coclea a croce ed è un manicotto o anello, sulla cui circonferenza sono contrassegnate le divisioni (Fig. 123). Questa manica con divisioni è chiamata arto. Le divisioni sono contate in base al rischio sul manicotto a vite fisso (in Fig. 123 questo rischio coincide con il 30° colpo del limbus).
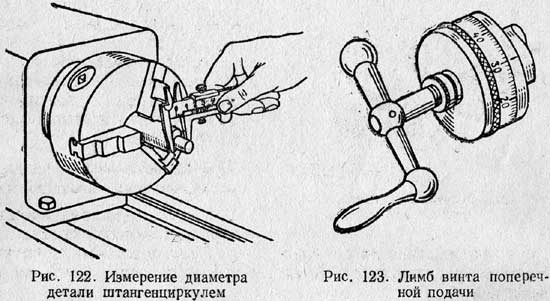
Il numero di divisioni sul quadrante e il passo della vite possono essere diversi, quindi anche la quantità di movimento trasversale della fresa quando il quadrante viene ruotato di una divisione sarà diverso. Si supponga che il quadrante sia diviso in 100 parti uguali e che la vite di alimentazione a croce sia filettata con un passo di 5 mm. Con un giro completo dell'impugnatura a vite, ovvero 100 divisioni dell'arto, il cutter si muoverà in direzione trasversale di 5 mm. Se si ruota la maniglia di una divisione, il movimento della taglierina sarà 5:100 = 0,05 mm.
Va tenuto presente che quando la fresa viene spostata nella direzione trasversale, il raggio della parte dopo il passaggio della fresa diminuirà della stessa quantità e il diametro della parte raddoppierà. Pertanto, per ridurre il diametro del pezzo, ad esempio da 50,2 a 48,4 mm, cioè di 50,2 - 48,4 = 1,8 mm, è necessario spostare la fresa in avanti della metà, cioè di 0,9 mm.
Quando si imposta la fresa alla profondità di taglio con l'aiuto del quadrante della vite di avanzamento trasversale, è tuttavia necessario tenere conto dello spazio tra la vite e il dado, che forma il cosiddetto "corsa morta". Se lo perdi di vista, il diametro della parte lavorata sarà diverso da quello specificato.
Pertanto, quando si imposta la fresa alla profondità di taglio utilizzando un quadrante, è necessario osservare prossima regola. Avvicinarsi sempre all'impostazione richiesta lungo il quadrante ruotando lentamente la maniglia a vite verso destra (Fig. 124, a; l'impostazione richiesta è la 30a divisione del quadrante).
Se si ruota la maniglia della vite senza fine di una quantità maggiore del valore richiesto (Fig. 124, b), per correggere l'errore, in nessun caso non riportare indietro la maniglia della quantità dell'errore, ma è necessario fare un giro quasi completo nella direzione opposta, quindi ruotare nuovamente la maniglia verso destra fino alla divisione richiesta lungo il limbus (Fig. 124, c). Lo stesso fanno quando è necessario riprendere la taglierina; ruotando l'impugnatura verso sinistra, il cutter viene retratto più del necessario, quindi, mediante rotazione a destra, viene portato alla necessaria divisione del limbus.
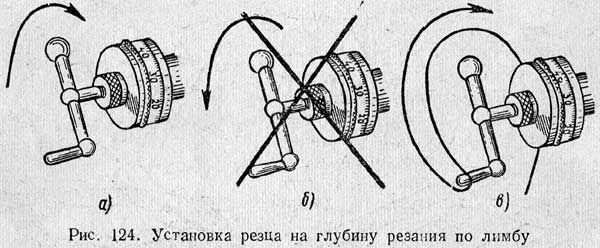
Il movimento del cutter, corrispondente a una divisione dell'arto, è diverso su macchine diverse. Pertanto, quando si inizia il lavoro, è necessario determinare la quantità di spostamento corrispondente a questa macchina una divisione del limbus.
Utilizzando gli arti, i nostri tornitori ad alta velocità raggiungono una determinata dimensione senza chip di prova.
8. Lavorare parti in lunetta
Le parti lunghe e sottili, la cui lunghezza è 10-12 volte il loro diametro, si piegano durante la tornitura sia dal proprio peso che dalla forza di taglio. Di conseguenza, l'oggetto ottiene forma irregolare- nel mezzo risulta essere più spesso e alle estremità - più sottile. Questo può essere evitato utilizzando uno speciale dispositivo di supporto chiamato lunetta. Utilizzando le lunette è possibile rettificare i pezzi con alta precisione e rimuovere i trucioli sezione più grande senza timore di piegare il pezzo. Le lunette b, si muovono immobili e mobili.
riposo costante(Fig. 125) ha un corpo in ghisa 1, con il quale è fissato un coperchio incernierato 6 con un bullone incernierato 7, che facilita l'installazione del pezzo. Il corpo della lunetta viene lavorato nella parte inferiore secondo la forma delle guide del telaio, su cui è fissato mediante una barra 9 e un bullone 8. Due camme 4 si muovono nei fori del corpo con l'aiuto di bulloni di regolazione 3 e una camma 5 si muove sul tetto.Per fissare le camme nella posizione richiesta, vengono utilizzate le viti 2. Tale dispositivo consente di installare alberi di vari diametri nella lunetta.
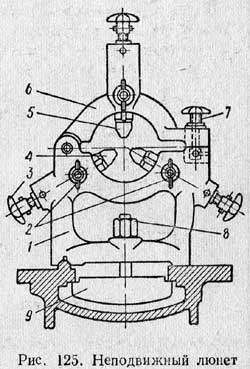
Prima di installare un pezzo grezzo in un supporto fisso, è necessario eseguire una scanalatura al centro di esso per le camme con una larghezza leggermente superiore alla larghezza della camma (Fig. 126). Se il pezzo ha una grande lunghezza e un piccolo diametro, la sua flessione è inevitabile. Per evitare ciò, viene lavorata una scanalatura aggiuntiva più vicino all'estremità del pezzo e, dopo aver installato una lunetta, la scanalatura principale viene lavorata al centro.
Le lunghe fisse fisse vengono utilizzate anche per tagliare le estremità e rifilare le estremità parti lunghe. Sulla fig. 127 mostra l'uso di un supporto fisso durante il taglio dell'estremità: la parte è fissata a un'estremità in un mandrino a tre griffe e l'altra estremità è installata nel resto.
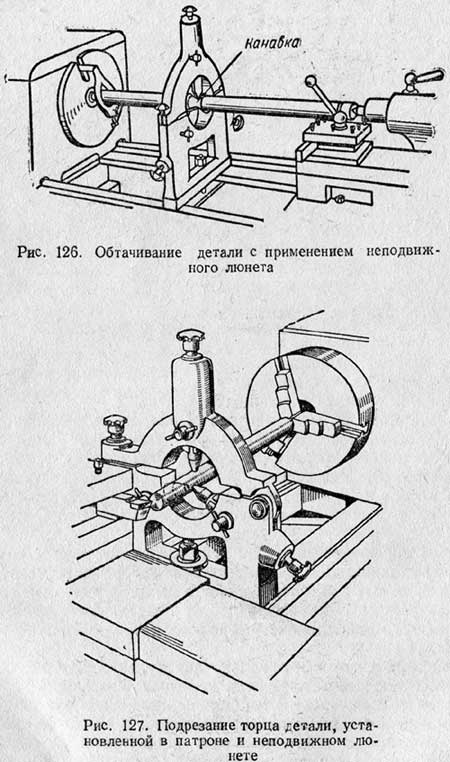
Allo stesso modo, è possibile eseguire un foro preciso dall'estremità di un pezzo lungo, ad esempio praticare un foro conico in un mandrino del tornio o eseguire un trapano di tale pezzo per tutta la sua lunghezza.
Lunetta mobile(Fig. 128) viene utilizzato per la tornitura fine di pezzi lunghi. La lunetta è fissata sul carro pinza in modo che si muova con essa lungo il pezzo, seguendo la fresa. Pertanto, sostiene la parte direttamente nel punto di applicazione della forza e impedisce la deflessione della parte.
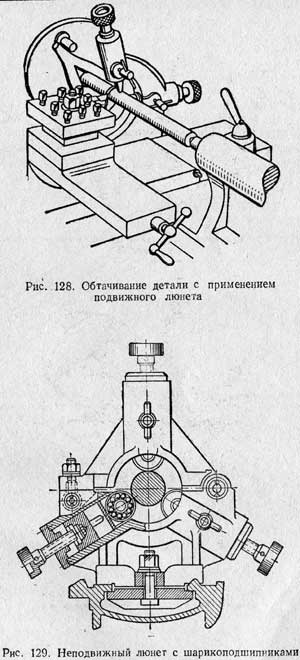
La lunetta ha solo due camme. Si allungano e si fissano allo stesso modo delle camme di una lunetta fissa.
Le lunette con ganasce convenzionali non sono adatte per la lavorazione ad alta velocità a causa della rapida usura delle ganasce. In questi casi, applicare lunette con cuscinetti a rulli oa sfere(Fig. 129) al posto delle camme convenzionali, che facilita il funzionamento dei rulli e riduce il riscaldamento del pezzo.
9. Tecniche di tornitura di superfici cilindriche con sporgenze
Quando si lavora su tornio un lotto di pezzi a gradini (rulli a gradini) con la stessa lunghezza per tutte le parti dei singoli gradini, gli innovatori utilizzano un fermo longitudinale che limita il movimento della fresa e un braccio longitudinale di avanzamento per ridurre i tempi di misurazione del lunghezza.
Utilizzo della battuta longitudinale. Sulla fig. 130 mostra la battuta longitudinale. È imbullonato alla sponda anteriore del letto come mostrato in fig. 131; il luogo di fissaggio della battuta dipende dalla lunghezza della parte da girare.
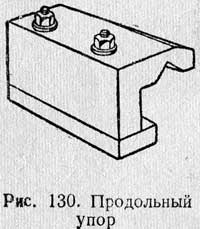
Se è presente un arresto longitudinale sulla macchina, è possibile lavorare superfici cilindriche con sporgenze senza marcatura preliminare, mentre, ad esempio, i rulli a gradini vengono ruotati in un'unica posizione molto più velocemente che senza arresto. Ciò si ottiene interponendo tra la battuta e il supporto un limitatore di lunghezza (piastrella di misurazione), corrispondente alla lunghezza del gradino del rullo.
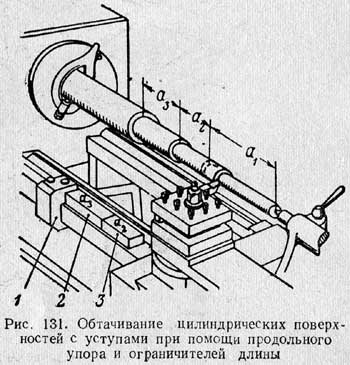
Un esempio di rotazione di un rullo a gradini con fermo 1 e di misurazione delle piastrelle 2 e 3 è mostrato in Fig. 131. Si esegue la rotazione della fase a 1 fino a quando la pinza si appoggia contro la piastrella di misurazione 3. Rimuovendo questa piastrella, è possibile rettificare il passaggio successivo del rullo con una lunghezza di 2 fino a quando la pinza si appoggia contro la piastrella 2. Infine, rimuovendo il piastrella 2, macinare il passaggio a 3 . Non appena la pinza raggiunge la battuta, è necessario disattivare l'avanzamento meccanico. La lunghezza della piastrella di misura 2 è uguale alla lunghezza della battuta a 3 e la lunghezza della piastrella 3 è uguale alla lunghezza della battuta a 2 .
Gli arresti duri possono essere utilizzati solo su macchine con spegnimento automatico alimentazione in sovraccarico (ad esempio, 1A62 e altri nuovi sistemi di macchine utensili). Se la macchina non dispone di un tale dispositivo, è possibile girare lungo l'arresto solo se l'avanzamento meccanico viene disattivato in anticipo e la pinza viene arrestata manualmente, altrimenti la macchina si romperà.
Utilizzando la manopola di avanzamento longitudinale Utilizzando la manopola di avanzamento longitudinale. Per ridurre il tempo impiegato per misurare le lunghezze dei pezzi, i moderni torni sono dotati di quadrante di alimentazione longitudinale. Questo arto rappresenta un disco rotante di grande diametro (Fig. 132), posto sulla parete frontale del grembiule e dietro il volantino di avanzamento longitudinale. Divisioni uguali vengono applicate alla circonferenza del disco. Quando il volantino ruota, ruota anche l'arto collegato mediante ingranaggio alla ruota di alimentazione longitudinale. Pertanto, un certo movimento longitudinale della pinza con un cutter corrisponde alla rotazione dell'arto di un certo numero divisioni relative ai rischi fissi.
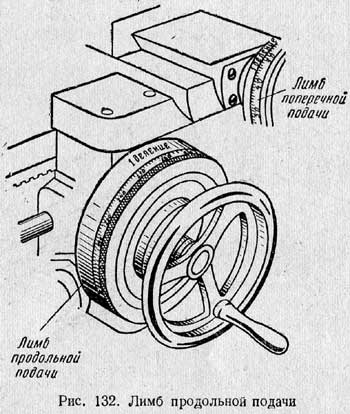
Quando si elaborano parti a gradini, l'uso di un quadrante di alimentazione longitudinale è molto razionale. In questo caso, il tornitore, prima di elaborare la prima parte del lotto, segna preliminarmente la lunghezza dei gradini con una fresa utilizzando un calibro, quindi inizia a macinarli. Dopo aver girato il primo stadio, pone l'arto longitudinale in posizione zero rispetto al rischio fisso. Girando i passi successivi, memorizza (o annota) le corrispondenti indicazioni dell'arto relative allo stesso rischio. Quando si girano le parti successive, il tornitore utilizza le indicazioni impostate quando si gira la prima parte.
Usando il fermo incrociato. Per ridurre il tempo impiegato per misurare i diametri durante la lavorazione di parti a gradini, è possibile utilizzare un arresto a croce su un certo numero di torni.
Una di queste fermate è mostrata in Fig. 133. Il corsivo si compone di due parti. La parte fissa 1 è installata sul carrello e fissata con bulloni 2; il perno di spinta 6 è fisso. Il fermo mobile 3 è installato e fissato con bulloni 4 sulla parte inferiore della pinza. La vite 5 è impostata esattamente sulla dimensione richiesta della parte. L'estremità della vite 5, appoggiata al perno 6, predetermina la dimensione richiesta del pezzo. Posizionando piastrelle di misurazione tra il perno 6 e la vite 5, è possibile rettificare un pezzo con gradini di vari diametri.
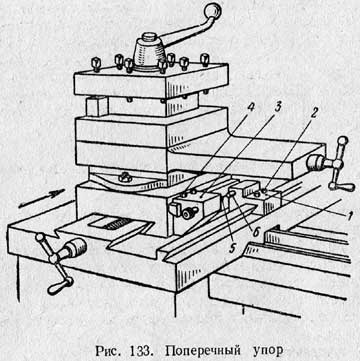
10. Condizioni di taglio per la tornitura
Scelta della profondità di taglio. La profondità di taglio durante la tornitura viene selezionata in base al sovrametallo di lavorazione e al tipo di lavorazione - sgrossatura o finitura (vedi pagine 101-102).
Selezione della velocità di avanzamento. Anche il mangime viene scelto in base al tipo di lavorazione. Di solito, l'avanzamento viene preso per la sgrossatura da 0,3 a 1,5 mm/giro e per la semifinitura e la finitura da 0,1 a 0,3 mm/giro quando si lavora con frese normali e 1,5-3 mm/giro quando si lavora con frese disegni di V. Kolesov.
Scelta della velocità di taglio. La velocità di taglio viene solitamente scelta secondo tabelle appositamente studiate in funzione della vita utensile, della qualità del materiale in lavorazione, del materiale della fresa, della profondità di taglio, dell'avanzamento, del tipo di raffreddamento, ecc. (vedi, per esempio, Tabella 6, pagina 106).
11. Matrimonio quando si girano superfici cilindriche e misure per prevenirlo
Quando si girano superfici cilindriche, sono possibili i seguenti tipi di unione:
1) parte della superficie del pezzo è rimasta non trattata;
2) le dimensioni della superficie tornita non sono corrette;
3) la superficie tornita risultava conica;
4) la superficie tornita è risultata ovale;
5) la pulizia della superficie lavorata non corrisponde alle indicazioni del disegno;
6) combustione del centro posteriore;
7) non coincidenza delle superfici durante la lavorazione del rullo nei centri su entrambi i lati.
1. Il matrimonio del primo tipo si ottiene a causa di dimensioni insufficienti del pezzo (sovrametallo di lavorazione insufficiente), scarso raddrizzamento (curvatura) del pezzo, installazione impropria e allineamento impreciso della parte, posizione imprecisa dei fori centrali e spostamento del centro posteriore.
2. Sono possibili dimensioni errate della superficie tornita a causa di un'impostazione imprecisa della fresa alla profondità di taglio o di una misurazione errata del pezzo durante la rimozione dei trucioli di prova. È possibile e dovrebbe eliminare le cause di questo tipo di matrimonio aumentando l'attenzione del tornitore sul lavoro svolto.
3. La conicità della superficie tornita si ottiene solitamente come risultato dello spostamento del centro posteriore rispetto all'anteriore. Per eliminare la causa di questo tipo di matrimonio, è necessario installare correttamente il centro posteriore. Una causa comune del disallineamento del centro posteriore è lo sporco o piccoli trucioli che entrano nel foro conico della penna. Pulindo il centro e il foro conico della penna, si può eliminare anche questa causa del matrimonio. Se, anche dopo la pulizia, le punte dei centri anteriore e posteriore non coincidono, è necessario spostare di conseguenza il corpo della contropunta sulla sua piastra.
4. L'ovalità della parte tornita si ottiene quando il mandrino batte per usura irregolare dei suoi cuscinetti o usura irregolare dei suoi colli.
5. Una finitura superficiale insufficiente durante la tornitura può essere dovuta a una serie di motivi: grande avanzamento della fresa, uso di una fresa con angoli irregolari, scarsa affilatura della fresa, piccolo raggio di curvatura della punta della fresa, alta viscosità del pezzo materiale, tremolio della fresa a causa di una grande sporgenza, fissaggio non sufficientemente forte della fresa nel portautensile, maggiore spazio tra le singole parti della pinza, tremore del pezzo a causa del suo fissaggio allentato o a causa dell'usura dei cuscinetti e colli di fuso.
Tutte le suddette cause di matrimonio possono essere eliminate in modo tempestivo.
6. La bruciatura del centro rigido della contropunta può essere causata dai seguenti motivi: la parte è troppo stretta tra i centri; scarsa lubrificazione del foro centrale; centraggio errato del pezzo; alta velocità di taglio.
7. La mancata corrispondenza delle superfici di lavorazione quando si gira su entrambi i lati nei centri si ottiene principalmente a causa del battito del centro anteriore o dello sviluppo di fori centrali nel pezzo. Per prevenire il matrimonio, è necessario controllare le condizioni dei fori centrali del pezzo durante la finitura e anche assicurarsi che non vi sia eccentricità del centro della paletta.
12. Precauzioni di sicurezza durante la tornitura di superfici cilindriche
In tutti i casi di lavorazione su tornio è necessario prestare attenzione al forte fissaggio del pezzo e della fresa.
L'affidabilità del fissaggio del pezzo lavorato nei centri dipende in gran parte dallo stato dei centri. È impossibile lavorare con centri usurati, poiché la parte sotto l'azione della forza di taglio può essere strappata dai centri, volare di lato e ferire il tornitore.
Durante la lavorazione di parti in centri e mandrini, le parti sporgenti del morsetto e le camme del mandrino spesso catturano i vestiti del lavoratore. Queste stesse parti possono causare danni alle mani durante la misurazione di un pezzo e la pulizia della macchina in movimento. Per prevenire incidenti, è necessario disporre protezioni di sicurezza in corrispondenza dei morsetti o utilizzare morsetti di sicurezza e proteggere i mandrini a camme. Il tipo perfetto di collare di sicurezza è mostrato in fig. 134. Il bordo 3 copre non solo la testa del bullone 2, ma anche il perno 1 del mandrino di trascinamento.

Per proteggere le mani e gli indumenti del tornitore dalle parti sporgenti del mandrino o del frontalino sui torni moderni, viene utilizzata una recinzione speciale (Fig. 135). L'involucro 1 del dispositivo è articolato al perno 2 fissato sul corpo della paletta.
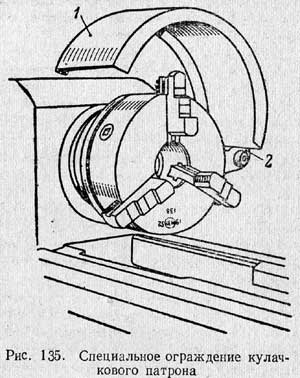
Quando si installano parti al centro, è necessario prestare attenzione alla correttezza dei fori centrali. Se la loro profondità è insufficiente, la parte può staccarsi dai centri durante la rotazione, il che è molto pericoloso. Allo stesso modo, dopo aver fissato la parte nel mandrino, è necessario verificare se la chiave è stata rimossa. Se la chiave rimane nel mandrino, quando il mandrino ruota, colpirà il letto e volerà via di lato. In questo caso sono possibili sia il guasto della macchina che il danno al lavoratore.
La causa degli incidenti sono spesso i trucioli, in particolare i trucioli di scarico, che, quando alte velocità il taglio si stacca da un nastro continuo. In nessun caso tali trucioli devono essere rimossi o tagliati a mano, possono causare gravi tagli e ustioni. Quando possibile, dovrebbero essere usati rompitrucioli. IN ultima risorsa quando la rottura del truciolo non è raggiunta, va rimossa con un apposito gancio.
Durante la lavorazione di materiali che emettono brevi schegge rimbalzanti, è necessario utilizzare occhiali protettivi o utilizzare schermi di sicurezza in vetro di sicurezza o celluloide (Fig. 136), fissati al carrello su una cremagliera incernierata. È necessario spazzare via i piccoli trucioli derivanti dalla lavorazione dei metalli fragili (ghisa, bronzo duro) non con le mani, ma con un pennello.
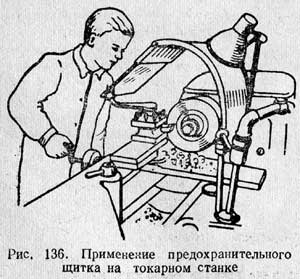
Potrebbero esserci lesioni alle mani durante l'installazione e il fissaggio delle lame a causa della rottura della chiave dalle teste dei bulloni di fissaggio del portautensili. La rottura della chiave si verifica quando le ganasce della chiave e le teste dei bulloni sono usurate. Spesso, però, si verifica un guasto anche per il fatto che il tornitore utilizza una chiave la cui dimensione non corrisponde a quella del chiavistello.
L'installazione della fresa lungo l'altezza dei centri con l'ausilio di qualsiasi tipo di rivestimento non adatto a questo (rottami di metallo, pezzi di seghetti, ecc.) non fornisce una posizione stabile della fresa durante il suo funzionamento. Sotto la pressione dei trucioli, tali rivestimenti vengono spostati e l'installazione della taglierina va storta. Allo stesso tempo, anche il fissaggio della taglierina si indebolisce. Di conseguenza, le pastiglie e la taglierina possono saltare fuori dal portautensili e ferire il tornitore. Inoltre, durante l'installazione della taglierina e quando si lavora sulla macchina, sono possibili lesioni alle mani sugli spigoli vivi dei rivestimenti metallici. Pertanto, si raccomanda che ogni tornitore abbia una serie di rivestimenti di vari spessori, con piani di appoggio e bordi ben rifiniti.
domande di prova 1. Come installare la taglierina nel supporto taglierina?
2. Come controllare la posizione della punta della taglierina rispetto alla linea centrale?
3. Come vengono installate e fissate le parti durante la tornitura di superfici cilindriche?
4. Qual è la differenza tra le condizioni di lavoro dei centri anteriori e posteriori?
5. Come è disposto il centro rotante e in quali casi viene utilizzato?
6. Cos'è il centro anteriore zigrinato e quali sono i suoi vantaggi?
7. Come verificare la corretta installazione dei centri per la tornitura di una superficie cilindrica?
8. Come funziona un mandrino autocentrante? Nomina i suoi dettagli, le regole per installarlo e prepararlo per il lavoro.
9. Come allineare una parte durante l'installazione in un mandrino a quattro griffe?
10. Qual è lo scopo del quadrante della vite a croce?
11. A cosa serve la manopola di alimentazione longitudinale? Come è organizzato?
12. A cosa servono le lune fisse e in quali casi vengono utilizzate?
13. Come è organizzata la lunetta?
14. Come si dispone una lunetta mobile?
15. Come viene preparato un pezzo grezzo per l'installazione in una lunetta?
16. Fornire un esempio dell'uso di una battuta longitudinale; fermata incrociata.
17. Quali tipi di matrimonio sono possibili quando si tornino superfici cilindriche? Come eliminare le cause del matrimonio?
18. Elencare le regole di sicurezza di base per la tornitura di superfici cilindriche.
Quali parti possono essere lavorate e lavorate su un tornio
Lavoriamo con piccoli ordini e pezzi. Facciamo alcune cose in serie condizionale, come inserti negli ammortizzatori, adattatori per assi delle ruote standard diversi. In bassa stagione (novembre-febbraio) puoi affrontare un gioco più grande.
Relativamente parlando, possiamo fare qualsiasi parte della rotazione di una forma cilindrica. I più richiesti erano una varietà di adattatori e assali per ruote. O il pezzo di ricambio originale non è in vendita, o ci vuole molto tempo per aspettare, oppure non esiste in natura. Ad esempio, alcune ruote anteriori Mavic da 20 mm non dispongono di un adattatore per 15 mm, 10 mm e il normale sgancio rapido da 5 mm. E per le ruote posteriori di Crossmax, non ci sono assali in vendita da molto tempo.
Un numero enorme di ammortizzatori richiede inserti nei colpi. Gli inserti possono essere lavorati da caprolon, poliacetale o duralluminio. Gli assi degli ammortizzatori eternamente deformabili e giocosi possono essere sostituiti con la lega di titanio VT16.
Non meno spesso, le boccole sono dotate di distanziali deformati tra i cuscinetti. Il produttore ha risparmiato denaro e ha fornito una lega troppo morbida.
A volte devi affilare i pistoni per le pompe freno e le pinze dei freni.
Spesso è necessario mettere a punto la parte esistente alle dimensioni desiderate.
Affiliamo tubi sterzo di ricambio per moto e biciclette. Realizziamo anche prolunghe tubo sterzo per biciclette.
A volte i modellisti RC vengono per assali in titanio particolarmente robusti e armaioli per alcuni tipi di jet.
Quali materiali vengono utilizzati per la tornitura
Ho leghe di alluminio in casa D16T, B95, 7075 . Fondamentalmente, nel lavoro di D16t, è abbastanza resistente. Su parti troppo sollecitate, puoi mettere la lega B95 o 7075 (questo è lo stesso Proprietà fisiche). Non utilizziamo leghe della serie AMG: sono piuttosto deboli.
leghe di titanio BT6, BT16. Queste sono le due leghe più richieste in termini di resistenza ai fini del ciclismo e della moto.
Kaprolon e poliacetale. Questo bene va agli inserti nelle unità di attrito. La maggior parte dei costruttori di telai passa anche al kaprolon per il calcolo degli assemblaggi a sospensione completa.
Fluoroplasto. Lo usiamo nella produzione di parti composite.
poliuretano. Di tanto in tanto è necessario creare un polsino o una manica strani.
Le parti in ottone in qualche modo non vengono utilizzate, quindi ottone e bronzo non sono in stock: porta il tuo.
Se lo desideri, posso semplicemente vendere un pezzo di materiale - forse tu stesso vuoi sventolare un file? =)
Come accettiamo ordini per lavori di tornitura
L'ordine è accettato in qualsiasi forma. Questo potrebbe essere un campione di cui vuoi fare una copia. Disegno. Schema. Schizzo. La foto. Spiegazione del dito. Ma negli ultimi due casi, insieme faremo uno schizzo con le dimensioni.
Puoi fare un dettaglio sulla controparte. E non abbiamo un markup mostruoso per il reverse engineering.
Ho un'idea abbastanza chiara di come dovrebbero essere realizzate le varie interfacce dei pezzi, quindi nella maggior parte dei casi non ci sono problemi nemmeno con la spiegazione "sulle dita". Ma a volte sono necessarie parti di accoppiamento vive per determinarne con precisione le dimensioni.
Precisione di fabbricazione e dimensioni delle parti
La precisione fondamentalmente ottenibile su un prodotto a pezzo per soldi sani è di 0,01 mm per i diametri esterni. Ma questo è raramente necessario a qualcuno, di solito è sufficiente una precisione di 0,05 mm (questo è, infatti, un adattamento a pressione). Diametri interni- non più di 0,02 mm.
Non c'è nulla per misurare le classi di rugosità, quindi non posso dire nulla di significativo qui. Posso mostrare campioni di lucidatura. Non è mai stato un compito realizzare uno specchio ideale come 14° grado, e noi maciniamo le superfici di rotolamento dei cuscinetti (coni) almeno fino al 10° grado.
La lunghezza massima di preparazione - 350 mm. Il diametro massimo del pezzo è 62 mm.
Tempi di produzione e prezzi
Piccole cose e dettagli semplici con una precisione inferiore a 0,05 mm vengono eseguiti immediatamente o nello stesso giorno. Dettagli più accurati e complessi: il giorno successivo o a giorni alterni.
Per riferimento, l'inserimento di un ammortizzatore caprolon nel bashing è di 150 rubli. Adattatore da un perno da 15 mm a un normale eccentrico - 500r. Asse per il mozzo anteriore con sedi dei cuscinetti e filettature sui bordi - 2000r (spazzatura molto precisa). È più facile chiamare, spiegare approssimativamente l'attività, quindi diventerà chiaro quanto costa.
Le restanti domande possono essere poste per telefono o guidare personalmente a Ogorodny.
Esempi di lavoro
Un set di strumenti per premere i paraolio e le antere nelle forcelle di sospensione (kaprolon):
Adattatore da perno 15mm a eccentrico con trattamento anticorrosione (D16t):
Boccola in lega 7075 con inserto sostituibile in PTFE (processo):
Produzione di una cartuccia a forcella ammortizzata con lavorazione strutturale:
Rettifica conica della boccola:
Realizzazione di un adattatore dal 20° asse a un eccentrico standard:
Realizzazione di polsini personalizzati nella cartuccia della forcella Marzocchi:
Fabbricazione di parti della cartuccia nella forcella Marzocchi:
Produzione di inserti in duralluminio nelle boccole degli ammortizzatori:
Tornitura di pezzi cilindrici
Al tornio vengono lavorati prodotti il cui contorno può essere costituito da più volumi forme geometriche, che sono chiamati corpi di rivoluzione . Queste cifre sono sfera, cono, cilindro e toro(vedi fig. a sinistra).
La tornitura dei pezzi a bordo macchina viene eseguita con appositi incisivi - scalpelli torniti
. A differenza dei tradizionali scalpelli da carpenteria, hanno impugnature allungate che consentono di tenere saldamente lo strumento e facilitarne il controllo.
Si distingue la qualità della lavorazione bozza e finitura tornitura, la scelta dell'utensile dipende da questo.
Per bozza si applica il trattamento scalpello semicircolare(vedi fig. ma), per finitura tornitura, rifilatura estremità e taglio di parti - scalpello obliquo(vedi fig. 6 ).
In tornitura grossolana spazi vuoti (vedi fig. ma) uno scalpello semicircolare viene spostato lungo il manipolo. Durante il primo passaggio, i trucioli di 1 ... 2 mm di spessore vengono rimossi dal centro della lama dello scalpello (vedi Fig. 6 , sinistra). L'ulteriore rotazione viene eseguita dalle parti laterali della lama quando la taglierina si sposta sia a sinistra che a destra (vedi Fig. 6 , sulla destra). Come risultato del lavoro con diverse sezioni della lama dello scalpello, la superficie della parte è meno ondulata. Dopo 2 ... 3 minuti di lavoro, controllano l'affidabilità del fissaggio del pezzo: lo premono con il centro della contropunta. Per la finitura, è necessario lasciare un margine di 3 ... 4 mm (di diametro).
In tornitura fine(vedi Fig.) Uno scalpello obliquo è posizionato sul bordo con un angolo ottuso verso il basso. I trucioli vengono tagliati dalla parte centrale e inferiore della lama.
Lo scalpello rotante si tiene con due mani durante la rotazione: una per il manico, l'altra per l'asta. Per l'asta, lo scalpello è avvolto intorno alla parte superiore o inferiore. Per la tornitura di sgrossatura, viene utilizzato più spesso il primo metodo, in quanto il più affidabile. La pressione sullo scalpello dovrebbe essere uniforme e liscia.
Per girare gli incavi interni dei prodotti utilizzando patrono o frontalini(vari contenitori, cofanetti, saliere, ecc.) - praticare prima un foro al centro del pezzo con un trapano. Quindi, con uno scalpello con un'estremità semicircolare, viene selezionato il legno in eccesso. Infine, per allineare le pareti, utilizzare uno scalpello con un'estremità curva (vedi figura a sinistra).
Per tornire prodotti con frontalini prima crea uno spazio vuoto a forma di quadrato. Le diagonali sono disegnate su questo pezzo e viene disegnato un cerchio leggermente più grande del diametro del prodotto previsto. Con una sega, gli angoli in eccesso vengono tagliati per ottenere un ottaedro, che viene avvitato al frontalino con viti. Il frontalino viene avvolto sul mandrino e controllato per vedere se il pezzo in lavorazione aderisce al manipolo. Successivamente, la macchina viene accesa e l'ottaedro viene ruotato al diametro desiderato. Quindi il manipolo viene installato parallelamente al piano del pezzo e la sua parte interna viene lavorata. Spostando il manipolo, macinare fuori da prodotti.
Il diametro del prodotto viene controllato calibro
o calibro
. Le misurazioni devono essere effettuate in più punti lungo la lunghezza del pezzo. La rettilineità può essere controllata con un righello o un quadrato alla luce.
Immediatamente dopo la tornitura, la superficie della parte viene pulita con una carta vetrata attaccata Blocco di legno(vedi fig.). Per ravvivare la struttura del legno, la superficie del prodotto può essere lucidata con una barra di legno più duro. Questa operazione viene eseguita durante la rotazione del pezzo e la rettifica.
Quando si tagliano le estremità della parte, lo scalpello obliquo viene posizionato sul bordo con un angolo acuto verso il basso e viene eseguito un taglio poco profondo (vedere la figura a sinistra).
Quindi, facendo un piccolo passo indietro a destra o a sinistra (a seconda dell'estremità tagliata), inclinare lo scalpello e tagliare parte del pezzo in un cono (vedere la figura a destra). Questa operazione viene ripetuta più volte fino a quando rimane un collo con un diametro di 8 ... 10 mm. Quindi la parte viene rimossa dalla macchina, le sue estremità vengono tagliate con un seghetto. Le estremità vengono pulite.
Per la fabbricazione di un largo numero parti identiche usato su un tornio conduttori(limitatori) per scalpelli o macchine fotocopiatrici . I conduttori sono facili da realizzare da soli e facili da installare sia su scalpello rotante che su manipolo (vedi figura a sinistra).
I numeri indicano:
1. - enfasi;
2. - limitatore di movimento longitudinale;
3. - limitatore di movimento trasversale;
4. - scalpello rotante.
Per ottenere i contorni desiderati sui manufatti, a volte vengono utilizzati scalpelli specifici (vedi figura a destra).
A volte sono realizzati appositamente per un prodotto particolare o per il contorno desiderato.
Di seguito è riportato un esempio di un prodotto e degli scalpelli utilizzati per realizzarlo.
Ad esempio, per la fabbricazione di una palla di legno vengono utilizzati scalpelli, realizzati con un diametro specifico (vedi figura a sinistra).
Senza scalpelli speciali, la stessa sfera può essere lavorata con semplici scalpelli, ma per una lavorazione precisa è necessario realizzare uno stampino (dima) con il quale poter misurare la correttezza della superficie sferica.
I passaggi per realizzare uno stencil e girare sono mostrati nella figura a destra.
Il legno per la tornitura viene preparato non solo ritagliando barre o pezzi di assi, ma anche utilizzando rami di alberi essiccati, nonché incollando pezzi di barre o tavole (cioè da segmenti) (vedi figura sotto). Spesso per girare tale "blocco " i prodotti utilizzano legno di specie diverse.
Grazie a ciò, si ottengono prodotti molto insoliti per colore e consistenza.
Quando lavori, segui queste regole:
Inferiore schermo protettivo(indossare gli occhiali)
Verificare il funzionamento della macchina al minimo;
Durante la lavorazione del pezzo, portare senza problemi la taglierina;
Assicurarsi che lo spazio tra il pezzo e il manipolo non superi i 5 mm;
Quando si esegue la foratura assiale, fissare accuratamente la contropunta;
Mentre si pratica il foro interno, tenere saldamente la taglierina su un piano orizzontale;
Controllare le dimensioni e la qualità della lavorazione a pezzo completamente fermo;
Quando si finisce una parte carta vetrata fissarlo su un supporto speciale.
Segnalare tutti i malfunzionamenti all'insegnante subito dopo aver spento la macchina!
Al termine dei lavori:
Rimuovere il pezzo finito dalla macchina;
Disporre strumenti e attrezzature in luoghi appositamente designati;
Ripulire il posto di lavoro;
Riferire all'addetto al termine dei lavori.
Durante il funzionamento, lo schermo di visualizzazione della macchina deve essere abbassato.
Se la macchina non dispone di tale schermo, è necessario lavorare con occhiali protettivi.
Strumento per tagliare portare al pezzo solo dopo che il mandrino ha raggiunto la velocità massima.
All'accensione della macchina è vietato correggere il pezzo e misurarne le dimensioni, spostare i componenti della macchina.
Dopo aver spento la macchina, non rallentare il pezzo, il mandrino o il frontalino con le mani.
Non lasciare una macchina in funzione incustodita.
Alla fine del lavoro, metti gli strumenti nei punti designati, spazza le patatine con un pennello.
È vietato:
Accendere la macchina senza il permesso dell'insegnante;
Lavorare in assenza di protezione della trasmissione a cinghia;
Utilizzare un pezzo non preparato;
Utilizzare un pezzo con scheggiature, crepe, bagnato o marcio;
Appoggiati a parti di un tornio;
Mettere strumenti e altri oggetti sulla macchina;
Fermare il pezzo a mano;
Allontanarsi dalla macchina senza spegnerla.