načini rezanja. Pomiki med grobim struženjem so postali rezalniki iz karbida brez dodatnega rezalnega roba. Velika enciklopedija nafte in plina
Struženje se lahko izvede z mehanskim pomikom, saj je generatrika obdelanega stožca vzporedna s smerjo vzdolžnega pomika rezalnika.
Tehnološki cikel kopiranja se uporablja za obdelavo stopničastih, stožčastih in ukrivljenih površin, ki zahtevajo vzdolžni pomik rezalnika. Na koncu površinske obdelave se rezalnik umakne iz dela, čeljust pa se vrne v prvotni položaj.
Splošno kazalo stroja za rezanje navojev. |
Vzdolžna podpora 7, nameščena na vodilih ležišča, se premika vzdolž njih in zagotavlja vzdolžni pomik rezalnika. Prečni nosilec zagotavlja navzkrižno podajanje rezalnika. Zgornji rotacijski nosilec se lahko nastavi pod katerim koli kotom glede na os vrtenja obdelovanca, kar je potrebno pri obdelavi stožčastih površin obdelovancev.
Shema obračanja oblikovanega obdelovanca. |
Po prečnem premikanju telesa zadnjega droga za količino h do 15 - 20 mm) je tvornica obdelanega stožca vzporedna s smerjo vzdolžnega pomika rezalnika, tako da se lahko obračanje izvaja z mehanskim pomikom. .
Shema obračanja kuhanja. |
Po prečnem pomiku telesa zadnjega nosilca za vrednost h (do 15 - 20 mm) je tvornica obdelanega stožca vzporedna s smerjo vzdolžnega podajanja rezalnika, zato je mogoče obračanje izvajati z mehanskim krmo.
Za vrezovanje navojev na stružnici je potrebno, da je hitrost vrtenja vretena strogo povezana s hitrostjo gibanja čeljusti, saj se mora vzdolžni pomik rezila v enem obratu vretena natančno ujemati z nagibom navoja. se reže.
Debelina rezanega kovinskega sloja močno vpliva na velikost nepravilnosti. Debelina rezanega sloja je določena z vzdolžnim pomikom rezalnika. Če med postopkom rezanja ni bilo elastično-plastičnih deformacij, bi lahko višino nepravilnosti zlahka izračunali iz geometrijska oblika vrh rezalnika.
Po 1 minuti od začetka dela izklopite vzdolžni pomik rezila, odmaknite rezalnik od obdelovanca in hitro obrnite držalo orodja za 90 ali 180, dokler se konica rezila ne dotakne konice indikatorja.
Pri diamantih v okvirju naj bodo vzdolžni podaji manjši kot pri svinčnikih, pri rezanih diamantih pa še manj. Na primer, pri obdelavi večnitnih navojev za brušenje z diamantnimi rezalniki ne sme biti vzdolžni pomik rezila največ 0,05 m / min. Na koncu postopka oblačenja je priporočljivo narediti en ali dva prehoda brez prečnega podajanja, kar zmanjša količino vzdolžnega podajanja.
Naprava je zasnovana za vrtanje stožčastih lukenj s konstantnim kotom a. Naprava je pritrjena na radialni nosilec sprednje plošče stroja. Z vrtenjem vijaka 3 se rezalnik pomika vzdolžno. Na drugem koncu vijaka je nameščena zvezdica 1, ki s skokom z zobom pri vsakem obratu čeljusti na nastavljeno zaustavitev izvaja samodejno vzdolžno podajanje.
Za obdelavo obdelovanca z rezanjem in s tem pridobitev obdelanih površin določenega dela, obdelovanca in uporabljenega rezalno orodje bi moral narediti določenih gibov. Ti premiki so razdeljeni na glavne (služijo za izvedbo postopka rezanja) in pomožne (služijo za pripravo na postopek rezanja in za dokončanje operacije). Obstajata dve glavni premiki:
- rezalno gibanje (ali glavno gibanje);
- gibanje krme.
Pri obdelavi na stružnici rezalno gibanje - rotacijsko - izvede obdelovanec, ki je tako ali drugače pritrjen na vreteno stroja, pomik - translacijsko - prejme rezalno orodje (rezalnik), togo pritrjeno v orodju. nosilec. Gibanje omogoča proces rezanja (nastajanje odrezkov), premikanje podajalnika omogoča izvajanje tega postopka (obdelave) po celotni dolžini obdelovanca (slika 16. del).
Globina reza (t)- vrednost rezanega sloja v enem prehodu, merjeno v smeri, pravokotni na obdelano površino. Globina reza je vedno pravokotna na smer podajanja (glej tudi sliko 11-14). Pri zunanjem vzdolžnem struženju (slika 16) je polovična razlika med premerom obdelovanca in premerom obdelane površine, pridobljene po enem prehodu:
Hitrost rezanjaυ - količina premika točke rezalni rob glede na površino na enoto časa med izvajanjem rezalnega gibanja *.
Pri struženju, ko se obdelovanec vrti s frekvenco n vrt/min, bo hitrost rezanja na točkah MK rezalnega roba spremenljiva vrednost. Najvišja hitrost:
kjer je D največji premer površine v mm.
* Hitrost rezanja je funkcija vrtilne hitrosti obdelovanca in hitrosti pomika orodja.
Če je hitrost znana, je pogostost vrtenja enostavno določiti:
Pri vzdolžnem struženju ima hitrost rezanja konstantno vrednost skozi celoten čas rezanja (če je premer obdelovanca vzdolž celotne dolžine enak in je hitrost vrtenja nespremenjena). Pri obrezovanju konca, ko se rezalnik premika od oboda obdelovanca proti sredini, je hitrost rezanja pri konstantni hitrosti spremenljiva. Ima najvišja vrednost na obrobju in je v središču enak nič (slika 17). Hitrost rezanja bo med odrezovanjem spremenljiva tudi vzdolž obdelane površine (glej sliko 14). Vendar v teh primerih upoštevajte najvišja hitrost rezanje.
Oddaja s(natančneje, pomik) - količina premika rezalnega roba glede na obdelano površino na enoto časa v smeri premikanja. Pri obračanju je lahko vzdolžna krma ko se rezalnik premika v smeri, vzporedni z osjo obdelovanca (glej sliko 16); navzkrižno krmljenje ko se rezalnik premika v smeri, pravokotni na os obdelovanca (glej sliko 17), in poševno krmo- pod kotom na os obdelovanca (na primer pri obračanju stožčaste površine).
Razločite smolo v enem zavoju obdelovanec, to je količina relativnega premika rezila med enim obratom obdelovanca (iz položaja I se je rezalnik premaknil v položaj II, slika 16), in minutno hranjenje, to je vrednost relativnega premika rezalnika za 1 min. Minutni pomik je označen s S m (mm / min), pomik na obrat - s (mm / vrt). Med njima je naslednje razmerje.
domov
tretji del
Osnove teorije rezanja kovin.
Izbira podatkov za rezanje
Poglavje VI
Osnove teorije rezanja kovin
Ustanovitelji teorije rezanja kovin so bili izjemni ruski znanstveniki I. A. Time (1838-1920), K. A. Zvorykin (1861-1928), Ya. G. Usachev (1873-1941) in drugi. Dela teh znanstvenikov, ki so prejela svetovno priznanje še niso izgubile vrednosti. Vendar pa v razmerah zaostale carske Rusije vsa ta dela niso našla praktična uporaba ker je bila industrija nerazvita.
Znanost o rezanju kovin je dobila širok obseg šele po veliki oktobrski socialistični revoluciji, zlasti v času sovjetskih petletk, ko je bila znanost postavljena v službo socialistične industrije.
Sovjetski znanstveniki V. D. Kuznetsov, V. A. Krivoukhov, I. M. Bezprozvanny, A. M. Rozenberg, M. N. Larin, P. P. Trudov, M. I. Klushin in drugi so ustvarili nacionalno šolo rezanja kovin, posebnost ki je tesno sodelovanje znanosti s proizvodnjo, znanstvenikov z inovatorji proizvodnje.
Pomembno vlogo pri razvoju znanosti o rezanju kovin je imelo gibanje inovatorjev v proizvodnji. V prizadevanju za povečanje produktivnosti dela so vodje proizvodnje začeli iskati nove načine za izboljšanje rezalnih pogojev: ustvarili so novo geometrijo rezalnega orodja, spremenili pogoje rezanja, obvladali nove materiali za rezanje. Vsak delovno mesto Turner-inovator je postal kot majhen laboratorij za preučevanje postopka rezanja.
Široka izmenjava izkušenj, mogoča le v pogojih socialističnega gospodarstva, ter tesno sodelovanje med vodilnimi delavci v proizvodnji in znanosti so zagotovili hiter razvoj znanosti o rezanju kovin.
1. Delo rezalnika
Wedge in njegovo delo. Delovni del katerega koli rezalnega orodja je klin(slika 44). Pod delovanjem uporabljene sile se konica klina zareže v kovino.
Čim ostrejši je klin, to je manjši kot, ki ga tvorijo njegove stranice, manj sile je potrebno, da ga zarežemo v kovino. Kot, ki ga tvorijo stranice klina, se imenuje konusni kot in je označena z grško črko β ( beta). Zato je manjši kot stožca β, lažje klin prodre v kovino, in nasprotno, večji kot je konus β, večja je sila za rezanje kovine. Pri določanju kota zoženja je treba upoštevati mehanske lastnosti kovine, ki se obdeluje. Če trdo kovino režete z rezilom z majhnim kotom ostrenja β, tanko rezilo ne bo vzdržalo in se bo drobilo ali zlomilo. Zato je glede na trdoto kovine, ki se obdeluje, dodeljen ustrezen kot ostrenja klina.
Plast kovine, ki se obdeluje, ki se nahaja neposredno pred rezalnikom, je neprekinjeno stisnjena s svojo sprednjo površino. Ko sila rezalnika preseže sile oprijema kovinskih delcev, se stisnjen element striže in premakne s sprednjo površino klina navzgor. Rezalnik, ki se pod delovanjem uporabljene sile premika naprej, se bo še naprej stiskal, sekal in premikal posamezne elemente iz katerih nastanejo čipi.
Osnovni gibi pri obračanju. Pri obdelavi na stružnicah se obdelovanec vrti, rezalnik pa se premika v vzdolžni ali prečni smeri. Vrtenje obdelovanca se imenuje glavno gibanje in gibanje rezila glede na del - gibanje krme(slika 45).
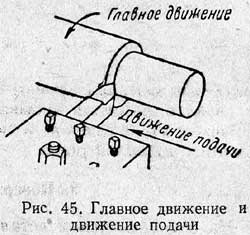
2. Glavni deli in elementi stružnega orodja
Rezalnik je sestavljen iz dveh glavnih delov: glave in telesa (palica) (slika 46). Glava je delovni (rezalni) del rezalnika; telo služi za pritrditev rezila v držalo orodja.

Glava je sestavljena iz naslednjih elementov: sprednja površina, vzdolž katerega se čipi snamejo, in zadnje površine obrnjen proti obdelovancu. Ena od zadnjih površin, obrnjenih proti rezalni površini, se imenuje glavni; drugi, obrnjen proti obdelani površini, - pomožni.
Rezalni robovi so pridobljeni iz presečišča sprednje in zadnje površine. Razlikovati doma in pomožni rezalni rob. Večino rezalnega dela opravi glavni rezalni rob.
Imenuje se presečišče glavnega in sekundarnega rezalnega roba konica sekalca.
3. Površinska obdelava
Na obdelovancu ločimo tri vrste površin (slika 47): obdelana, obdelana in rezalna površina.

obdelano površina je površina obdelovanca, s katerega se odstranijo odrezki.
Površinsko obdelana imenujemo površina dela, pridobljenega po odstranitvi odrezka.
rezalna površina imenujemo površina, ki jo na obdelovancu tvori glavni rezalni rob rezalnika.
Prav tako je treba razlikovati med rezalno ravnino in osnovno ravnino.
rezalna ravnina imenujemo tangenta ravnine na rezalno površino in poteka skozi rezalni rob rezalnika.
Glavna ravnina imenujemo ravnina, vzporedna z vzdolžnim in prečnim pomikom rezalnika. Pri stružnicah sovpada z vodoravno podporno površino držala orodja.
4. Rezalni koti in njihov namen
Koti delovnega dela rezalnika močno vplivajo na potek postopka rezanja.
Z izbiro pravih kotov rezalnika lahko znatno povečate trajanje njegovega neprekinjenega delovanja do otopenja (vzdržljivost) in obdelave na enoto časa (na minuto ali uro) velika količina podrobnosti.
Od izbire kotov rezalnika so odvisni tudi rezalna sila, ki deluje na rezilo, zahtevana moč, kakovost obdelane površine itd. Zato mora vsak strugar dobro preučiti namen vsakega od kotov ostrenja. rezalnik in znajo pravilno izbrati njihovo najugodnejšo vrednost.
Kote rezalnika (slika 48) lahko razdelimo na glavne kote, kote rezalnika v načrtu in kot naklona glavnega rezalnega roba.
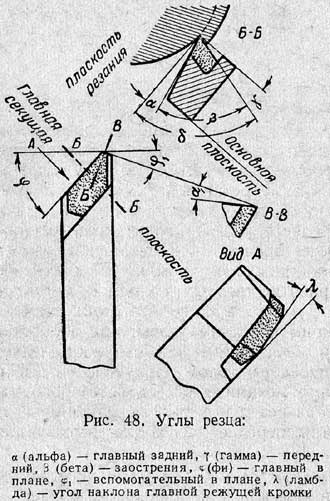
Glavni koti vključujejo: zadnji kot, sprednji kot in kot zoženja; koti rezalnika v načrtu vključujejo glavni in pomožni.
Glavne kote rezalnika je treba izmeriti v glavni rezalni ravnini, ki je pravokotna na rezalno ravnino in glavno ravnino.
Delovni del rezalnika je klin (osenčen na sliki 48), katerega oblika je značilna kot med sprednjo in glavno zadnjo površino rezalnika. Ta kotiček se imenuje konusni kot in je označena z grško črko β (beta).
zadnji kot α ( alfa) je kot med glavnim bokom in rezalno ravnino.
Varnostni kot α služi za zmanjšanje trenja med zadnjo površino rezalnika in obdelovancem. Z zmanjšanjem trenja s tem zmanjšamo segrevanje rezila, ki se zaradi tega manj obrabi. Če pa se reliefni kot močno poveča, je sekalec oslabljen in hitro uničen.
sprednji kot γ ( gama) je kot med sprednjo površino rezalnika in ravnino, pravokotno na rezalno ravnino, potegnjeno skozi glavni rezalni rob.
Nagibni kot γ igra pomembno vlogo pri procesu tvorbe odrezkov. S povečanjem nagibnega kota je lažje rezati rezalnik v kovino, zmanjša se deformacija rezanega sloja, izboljša se pretok odrezkov, zmanjšata rezalna sila in poraba energije ter kakovost obdelane površine. je izboljšan. Po drugi strani pa prekomerno povečanje nagibnega kota vodi do oslabitve rezalnega roba in zmanjšanja njegove trdnosti, do povečanja obrabe rezila zaradi lomljenja rezalnega roba in do poslabšanja odvajanja toplote. . Zato je treba pri obdelavi trdih in krhkih kovin, da bi povečali trdnost orodja, pa tudi njegovo vzdržljivost, uporabiti rezila z manjšim nagibnim kotom; pri obdelavi mehkih in duktilnih kovin je treba uporabiti rezila z velikim nagibnim kotom za lažje odstranjevanje odrezkov. V praksi je izbira sprednjega kota odvisna, poleg mehanske lastnosti material, ki se obdeluje, od materiala rezalnika in oblike sprednje površine. Priporočeni nagibni koti za rezila iz karbidne trdine so navedeni v tabeli. eno.
Načrtujte kote. Vodilni kot φ ( fi) se imenuje kot med glavnim rezalnim robom in smerjo podajanja.
Kot φ običajno izberemo v območju 30-90°, odvisno od vrste obdelave, vrste rezalnika, togosti obdelovanca in rezalnika ter načina njihove pritrditve. Pri obdelavi večine kovin s pretočnimi rezalniki za luščenje je mogoče vzeti kot φ = 45°; pri obdelavi tanke dolgi deli v središčih je treba uporabiti rezila s kotom vodnega kota 60, 75 ali celo 90 °, da se deli ne upognejo ali tresejo.
Pomožni kot v tlorisuφ 1 je kot med sekundarnim rezalnim robom in smerjo podajanja.

Kot λ ( lambda) naklon glavnega rezalnega roba(slika 49) je kot med glavnim rezalnim robom in črto, ki poteka skozi vrh rezalnika vzporedno z glavno ravnino.
Tabela 1
Priporočeni nagibni in zračni koti za karbidna orodja
Opomba. Mehanske lastnosti kovin se določajo na posebnih strojih in instrumentih, vsaka lastnost pa ima svojo oznako. Oznaka σ b v tej in naslednjih tabelah izraža natezno trdnost kovine; vrednost te meje se meri v kg/mm2. Črke HB označujejo trdoto kovine, ki jo na Brinellovi napravi določimo tako, da v površino kovine pritisnemo kaljeno jekleno kroglo. Vrednost trdote se meri v kg / mm 2.
Rezalniki, katerih vrh je najnižja točka rezalnega roba, to je kot λ pozitivno(slika 49, c), so bolj trpežne in odporne; s takšnimi rezalniki je dobro obdelovati trde kovine, pa tudi presihajoče površine, ki ustvarjajo udarno obremenitev. Pri obdelavi takšnih površin rezalniki iz karbida kot naklona glavnega rezalnega roba je nastavljen na 20-30°. Rezalniki, katerih vrh je najvišja točka rezalnega roba, to je kot λ negativno(slika 49, a), je priporočljivo uporabiti za obdelavo delov iz mehkih kovin.
5. Materiali, uporabljeni za izdelavo sekalcev
Pri delu na rezalnih robovih rezalnika se pojavi visok tlak, pa tudi visoka temperatura (600-800 ° in več). Trenje zadnje površine rezalnika o rezalni površini in odrezki na sprednji površini rezalnika povzročajo bolj ali manj hitro obrabo njegovih delovnih površin. Zaradi obrabe se oblika rezalnega dela spremeni in rezalnik čez nekaj časa postane neuporaben za nadaljnje delo; tak rezalnik je treba odstraniti s stroja in ga ponovno nabrusiti. Za podaljšanje življenjske dobe orodja brez ponovnega brušenja je potrebno, da je njegov material dobro odporen proti obrabi pri visokih temperaturah. Poleg tega mora biti material rezalnika dovolj močan, da zdrži visoki tlaki ki nastanejo med rezanjem. Zato so za material rezalnikov postavljene naslednje osnovne zahteve - trdota pri visoki temperaturi, dobra odpornost proti obrabi in trdnost.
Trenutno obstaja veliko orodnih jekel in zlitin, ki izpolnjujejo te zahteve. Sem spadajo: ogljikova orodna jekla, hitrorezna jekla, trde zlitine in keramičnih materialov.
Ogljikovo orodno jeklo. Za izdelavo rezalnih orodij se uporablja jeklo z vsebnostjo ogljika od 0,9 do 1,4%. Po kaljenju in kaljenju rezalno orodje iz tega jekla pridobi visoko trdoto. Če pa med postopkom rezanja temperatura rezalnega roba doseže 200-250 °, se trdota jekla močno zmanjša.
Zaradi tega je ogljikovo orodno jeklo trenutno v omejeni uporabi: uporablja se za izdelavo rezalnih orodij, ki delujejo pri relativno nizki hitrosti rezanja, ko temperatura v območju rezanja doseže majhno vrednost. Takšna orodja vključujejo: matrice, povrtala, pipe, pile, strgala itd. Rezalniki trenutno niso izdelani iz ogljikovega orodnega jekla.
Hitrorezna jekla. Hitrorezna jekla vsebujejo veliko število posebni, tako imenovani legirni elementi - volfram, krom, vanadij in kobalt, ki dajejo jeklu visoke rezalne lastnosti - sposobnost ohranjanja trdote in odpornosti proti obrabi pri segrevanju med rezanjem na 600-700 °. HSS rezalniki omogočajo 2-3 krat višje hitrosti rezanja kot karbonske rezalke.
Trenutno se v ZSSR proizvajajo naslednje vrste hitroreznega jekla (GOST 9373-60): R18, R9, R9F5, R14F14, R18F2, R9K5, R9KYU, R10K5F5 in R18K5F2.
Rezalniki, izdelani v celoti iz hitroreznega jekla, so dragi, zato se za prihranek hitroreznega jekla uporabljajo predvsem rezila z varjenimi ploščami.
Trde zlitine. Za karbidne zlitine je značilna zelo visoka trdota in dobra odpornost proti obrabi.
Trde zlitine so izdelane v obliki plošč iz volframovega in titanovega prahu v kombinaciji z ogljikom. Kombinacija ogljika in volframa se imenuje volframov karbid, s titanom pa titanov karbid. Kot vezivo je dodan kobalt. To praškasto zmes stisnemo pod visokim tlakom, da dobimo majhne plošče, ki jih nato sintramo pri temperaturi okoli 1500°. Končne plošče ne potrebujejo nobenih toplotna obdelava. Plošča je spajkana z bakrom na držalo rezalnika iz ogljikovo jeklo ali nanjo pritrjen s pomočjo nastavitev in vijakov (mehansko pritrditev plošč).
Glavna prednost trdih zlitin je v tem, da se dobro upirajo odrgnini zaradi padajočih sekancev in obdelovanca ter ne izgubijo svojih rezalnih lastnosti tudi pri segrevanju na 900-1000 °. Zahvaljujoč tem lastnostim so rezila, opremljena s karbidnimi vložki, najbolj primerna za obdelavo trdne kovine(trda jekla, vključno s kaljenimi) in nekovinski materiali (steklo, porcelan, plastika) pri hitrostih rezanja, ki so 4-6 krat ali več višje od hitrosti rezanja, ki jih dovoljujejo hitri rezkarji.
Pomanjkljivost trdih zlitin je povečana krhkost.
Trenutno se v ZSSR proizvajata dve skupini trdih zlitin. Glavni so - volfram(VK2, VKZ, VK4, VK6M, VK6, VK8 in VK8M) in titan-volfram(T30K4, T15K6, T14K8, T5K10). Vsaka od teh skupin ima poseben obseg (tabela 2).
Vse volframove zlitine so namenjene za obdelavo litega železa, barvnih kovin in njihovih zlitin, kaljenih jekel, nerjavnih jekel in nekovinskih materialov (ebonit, porcelan, steklo itd.). Za obdelavo jekel se uporabljajo trde zlitine skupine titan-volfram.
Keramični materiali. V zadnjem času so sovjetski metalurgi ustvarili poceni materiale z visokimi rezalnimi lastnostmi, ki v mnogih primerih nadomeščajo trde zlitine. To so keramični materiali termokorund), proizvedeno v obliki plošč bela barva, ki spominja na marmor, ki so tako kot trde zlitine bodisi spajkani na držala rezalnika bodisi nanje mehansko pritrjeni. Te plošče ne vsebujejo tako dragih in redkih elementov, kot so volfram, titan itd. Hkrati imajo keramične plošče večjo trdoto kot trde zlitine in ohranijo trdoto pri segrevanju do 1200 °, kar omogoča rezanje kovin z jih z visoke hitrosti rezanje.
Pomanjkljivost keramičnih plošč je njihova nezadostna viskoznost. Rezalniki, opremljeni s keramičnimi vložki, se lahko uporabljajo za dodelavo ali delno obdelavo litega železa, brona, aluminijevih zlitin in mehkih jekel.
6. Ostrenje in končna obdelava rezalnikov
V tovarnah se ostrenje rezil običajno izvaja centralizirano pri brusilni stroji posebni delavci. Toda strugar mora biti sposoben izostriti in dokončati rezila.
tabela 2
Lastnosti in namen nekaterih vrst trdih zlitin

Brušenje in končna obdelava hitrih rezalnikov se izvaja v skladu z naslednjimi pravili:
1. Brusilno kolo ne sme premagati, njegova površina mora biti enakomerna; če se je delovna površina kroga razvila, jo je treba popraviti.
2. Med ostrenjem morate uporabiti ročnik in ne držite rezalnika na teži. Ročnik naj bo nameščen čim bližje brusilnemu kolu, pod zahtevanim kotom in zagotavlja zanesljivo oporo rezalniku (slika 50, a-d).
3. Rezalnik, ki ga je treba ostriti, je treba premikati vzdolž delovne površine kroga, sicer se bo neenakomerno obrabil.
4. Da ne bi pregreli rezalnika in se s tem izognili pojavu razpok v njem, rezalnika ne pritiskajte močno na krog.
5. Brušenje je treba izvajati s stalnim in obilnim hlajenjem rezila z vodo. Kapljično hlajenje, pa tudi občasno potapljanje močno segretega rezalnika v vodo ni dovoljeno. Če stalno hlajenje ni mogoče, je bolje preiti na suho ostrenje.
6. Brušenje rezil iz hitroreznega jekla je treba opraviti z elektrokorundnimi kolesi srednje trdote in zrnatosti 25-16.
Vrstni red brušenja rezil je nastavljen na naslednji način. Najprej se izostri glavna hrbtna površina (slika 50, a). Nato pomožna zadnja površina (slika 50, b), nato sprednja površina (slika 50, c) in končno polmer vrha (slika 50, d).
7. Strogo je prepovedano brušenje rezil na strojih z odstranjenim zaščitnim pokrovom.
8. Pri brušenju obvezno nosite zaščitna očala.
Po ostrenju rezalnika na njegovih rezalnih robovih ostanejo majhne zareze, zareze in nevarnosti. Odpravljamo jih z dodelavo na posebnih končnih strojih. Končna obdelava se izvaja tudi ročno z uporabo drobnozrnatega brusilnega kamna, navlaženega z mineralnim oljem. Najprej se z lahkimi gibi preizkusnega kamna prilagodijo zadnje površine, nato sprednja in polmer vrha.
Brušenje in končna obdelava rezil, opremljenih s karbidnimi vložki. Ostrenje rezil s ploščami iz trdih zlitin se izvaja na brusilnih strojih s krogi zelenega silicijevega karbida. Ostrenje se izvaja tako ročno (slika 50, a-d), kot s pritrjevanjem sekalcev v držala orodja. Vrstni red brušenja teh rezalnikov je enak kot pri rezkarjih iz hitroreznega jekla, to pomeni, da se rezalnik najprej naostri vzdolž glavne hrbtne strani (slika 50, a), nato pa vzdolž pomožnih hrbtnih površin (slika 50, b). ), nato vzdolž sprednje površine (slika 50, c) in na koncu zaokrožimo vrh sekalca (slika 50, d).
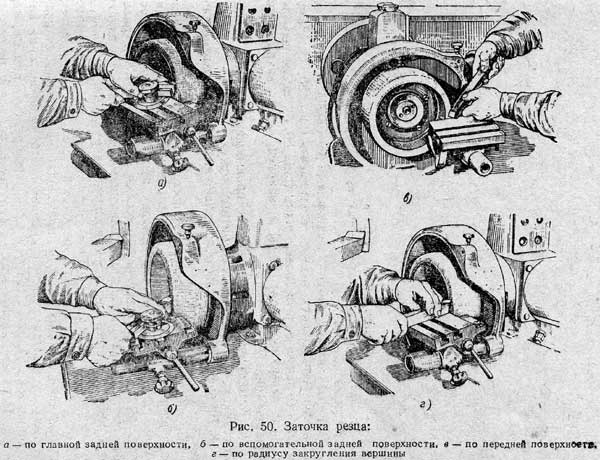
Predhodno ostrenje se izvaja z zelenimi kolesi iz silicijevega karbida z zrnatostjo 50-40, končno ostrenje pa z zrnatostjo 25-16.
Rezalnik ne sme biti močno pritisnjen na delovno površino kroga, da se izognemo pregrevanju in razpokanju plošče iz trde zlitine. Poleg tega ga je treba nenehno premikati glede na krog; to je potrebno za enakomerno obrabo kroga.
Brušenje se lahko izvaja tako na suho kot z obilnim hlajenjem rezalnika z vodo.
Po ostrenju rezalnika iz karbidne trdine je treba njegovo površino nujno dokončati. Končna obdelava se izvaja ročno ali na stroju za končno obdelavo. Ročna končna obdelava se izvaja z litoželezno ali bakreno plastjo, katere delovno površino podrgnemo s posebno pasto ali pa se na površino enakomerno nanese prah borovega karbida, pomešan s strojnim oljem ali kerozinom. Dodelava se izvede na širino 2-4 mm od rezalnega roba.
Bolj produktivna končna obdelava na posebnem stroju za končno obdelavo z uporabo diska iz litega železa s premerom 250-300 mm, ki se vrti s hitrostjo 1,5-2 m / s; na površino tega diska se nanese pasta ali prah borovega karbida, pomešan s strojnim oljem ali kerozinom.
7. Nastajanje čipov
Vrste ostružkov. Odstranjeni odrezek pod pritiskom rezalnika močno spremeni svojo obliko ali, kot pravijo, se deformira: skrajša dolžino in poveča debelino. Ta pojav je prvi odkril prof. I. A. Čas in imenovan krčenje čipov.
Videz odrezka je odvisen od mehanskih lastnosti kovine in pogojev, pod katerimi pride do rezanja. Če se obdelujejo viskozne kovine (svinec, kositer, baker, blago jeklo, aluminij itd.), potem posamezni elementi sekancev, ki se tesno oprimejo drug drugega, tvorijo neprekinjen odrezek, ki se zvija v trak (slika 51, a ). Takšen pramen se imenuje odtok. Pri obdelavi manj viskoznih kovin, kot je trdo jeklo, nastanejo odrezki iz posameznih elementov (slika 51, b), ki so med seboj šibko povezani. Takšen pramen se imenuje čipiranje čipov.
Če je kovina, ki se obdeluje, krhka, na primer lito železo ali bron, se posamezni elementi odrezkov zlomijo in ločijo od obdelovanca in drug od drugega (slika 51, c). Takšen čip, sestavljen iz posameznih lestvic nepravilne oblike, se imenuje zlomljeni čipi.
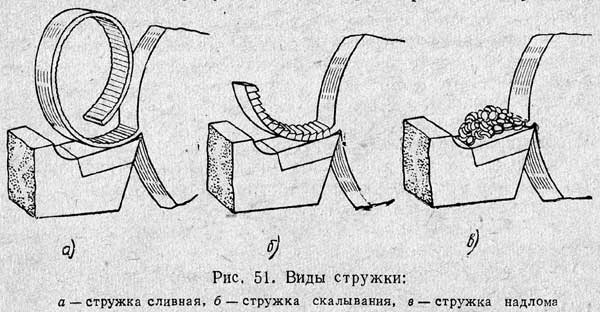
Obravnavane vrste sekancev ne ostanejo konstantne, lahko se spreminjajo s spreminjanjem pogojev rezanja. Čim mehkejša je kovina, ki se obdeluje, in manjša je debelina odrezka in kot rezanja, tem bolj se oblika odrezka približuje odtoku. Enako bo opaženo, ko se poveča hitrost rezanja in uporabi hlajenje. Z zmanjšanjem hitrosti rezanja se namesto odtočnega odrezka dobijo sekanci.
Izrastek. Če pregledate sprednjo površino rezalnika, ki je bil uporabljen za rezanje, lahko na rezalnem robu včasih najdete majhno kepo kovine, privarjeno na rezalnik pod visoko temperaturo in pritiskom. To je t.i izrastek(slika 52). Pojavi se pri določenih pogojih rezanja nodularnih kovin, vendar ga pri obdelavi krhkih kovin ne opazimo. Trdota tvorbe je 2,5-3 krat višja od trdote kovine, ki se obdeluje; zahvaljujoč temu ima rast sama možnost rezanja kovine, iz katere je nastala.
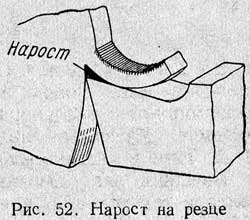
Pozitivna vloga obloge je, da pokriva rezilo, ga ščiti pred obrabo s padajočimi odrezki in delovanjem toplote, kar nekoliko poveča vzdržljivost rezila. Prisotnost nabiranja je koristna pri luščenju, saj se rezilo manj segreje in zmanjša se njegova obraba. Vendar pa se z nastankom nanosa poslabšata natančnost in čistoča obdelane površine, saj nabiranje izkrivlja obliko rezila. Zato je nastanek tvorbe neugoden za zaključna dela.
8. Koncept elementov načina rezanja
Za učinkovitejšo izvedbo obdelave v vsakem posameznem primeru mora strugar poznati osnovne elemente načina rezanja; ti elementi so globina reza, podajanje in hitrost rezanja.
Globina reza imenujemo razdalja med obdelano in obdelano površino, merjeno pravokotno na slednjo. Globina reza je označena s črko t in se meri v milimetrih (slika 53).
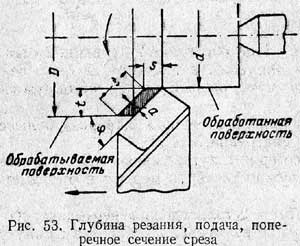
Pri obračanju obdelovanca na stružnici se obdelovalni dodatek odreže v enem ali več prehodih.
Za določitev globine reza t je potrebno izmeriti premer obdelovanca pred in po prehodu rezalnika, polovica razlike v premerih bo dala globino reza, z drugimi besedami,
pri čemer je D premer dela v mm pred prehodom rezalnika; d je premer dela v mm po prehodu rezalnika. Gibanje rezila v enem obratu obdelovanca (slika 53) se imenuje vložitev. Pomik je označen s črko s in se meri v milimetrih na obrat dela; za kratkost je običajno pisati mm / rev. Glede na smer, v kateri se rezalnik premika glede na vodila okvirja, obstajajo:
a) vzdolžna krma- po vodilih ležišča;
b) navzkrižno krmljenje- pravokotno na vodila ležišča;
v) poševno krmo- pod kotom na vodila ležišča (na primer pri obračanju stožčaste površine).
Območje prereza označen s črko f (eff) in je opredeljen kot zmnožek globine reza s podajanjem (glej sliko 53):
Poleg globine reza in podajanja ločijo tudi širino in debelino rezanega sloja (slika 53).
Rezanje širine plasti, oz širina čipa, - razdalja med obdelano in obdelano površino, merjeno vzdolž rezalne površine. Meri se v milimetrih in je označena s črko b (be).
Debelina reza, oz debelina čipov, je razdalja med dvema zaporednima položajema rezalnega roba v enem obratu dela, merjeno pravokotno na širino odrezka. Debelina odrezka se meri v milimetrih in je označena s črko a.
Z enakim podajanjem in globino reza, ko se glavni kot φ zmanjša, se debelina odrezka zmanjša, njegova širina pa se poveča. To izboljša odvajanje toplote z rezalnega roba in podaljša življenjsko dobo orodja, kar vam posledično omogoča znatno povečanje hitrosti rezanja in obdelavo več delov na enoto časa. Vendar pa zmanjšanje glavnega kota v načrtu φ povzroči povečanje radialne (odbojne) sile, ki lahko pri obdelavi premalo togih delov povzroči njihovo upogibanje, izgubo natančnosti in tudi močne tresljaje. Pojav tresljajev pa vodi do poslabšanja čistosti obdelane površine in pogosto povzroči sekanje rezalnega roba rezalnika.
Hitrost rezanja. Pri obdelavi na stružnici točka A, ki se nahaja na krogu s premerom D (slika 54), v enem obratu dela prepotuje pot, ki je enaka dolžini tega kroga.
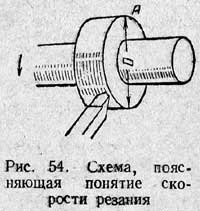
Dolžina katerega koli kroga je približno 3,14-kratnik njegovega premera, zato je enaka 3,14 D.
Število 3.14, ki kaže, kolikokrat je dolžina kroga večja od njegovega premera, je običajno označena z grško črko π (pi).
Točka A v enem obratu naredi pot enako πD. Premer D dela, kot tudi njegov obseg πD, se meri v milimetrih.
Predpostavimo, da bo obdelovanec naredil več vrtljajev na minuto. Označimo njihovo število s črko n vrtljajev na minuto ali skrajšano rpm. Pot, ki jo bo v tem primeru prehodila točka A, bo enaka zmnožku obsega in števila vrtljajev na minuto, to je πDn milimetrov na minuto ali skrajšano mm / min, in se imenuje obodna hitrost.
način, prehodna točka se imenuje površina, ki jo je treba obdelati pri obračanju glede na rezalni rob rezalnika v eni minuti hitrost rezanja.
Ker je premer dela običajno izražen v milimetrih, da bi našli hitrost rezanja v metrih na minuto, delimo πDn s 1000. To lahko zapišemo kot naslednjo formulo:
kjer je v hitrost rezanja v m/min;
D je premer obdelovanca v mm;
n je število vrtljajev na minuto.
Primer 3 Premer obdelanega valja D = 100 = 150 vrt./min. Določite hitrost rezanja.
Odločitev: Štetje hitrosti vretena. Pri struženju dela znanega premera je morda potrebno, da strugar prilagodi stroj na tolikšno število vrtljajev vretena, da doseže zahtevano hitrost rezanja. Za to se uporablja naslednja formula: kjer je D premer obdelovanca v mm;
Primer 4 Kakšno število vrtljajev na minuto mora imeti valj s premerom D = 50 mm pri hitrosti rezanja v = 25 m / min?
Odločitev:
9. Osnovni podatki o silah, ki delujejo na rezalnik, in rezalni moči
Sile, ki delujejo na rezalnik. Pri odstranjevanju odrezkov iz obdelovanca mora rezalnik premagati silo oprijema kovinskih delcev drug na drugega. Ko rezalni rob rezalnika zareže v material, ki se obdeluje, in se odrezek loči, rezalnik doživi pritisk kovine, ki se ločuje (slika 55).

Od zgoraj navzdol sila P z pritisne na rezalnik, ki teži, da pritisne rezalnik navzdol in upogne del navzgor. Ta sila se imenuje rezalna sila.
V vodoravni ravnini v smeri, nasprotni gibanju podajanja, rezalnik pritisne s silo P x, ki se imenuje aksialna sila, oz krmna sila. Ta sila med vzdolžnim obračanjem nagiba k pritisku rezalnika proti zadnji drogi.
V vodoravni ravnini, pravokotno na smer podajanja, rezalnik pritisne s silo P y, ki ji pravimo radialna sila. Ta sila nagiba rezalnik potisniti stran od obdelovanca in ga upogniti v vodoravni smeri.
Vse naštete sile se merijo v kilogramih.
Največja od treh sil je navpična rezalna sila: približno 4-kratna sila podajanja in 2,5-kratna radialna sila. Rezalna sila obremenjuje dele mehanizma vzglavja; obremeni tudi rezalnik, del, kar pogosto povzroči velike napetosti v njih.
Poskusi so ugotovili, da je rezalna sila odvisna od lastnosti materiala, ki se obdeluje, velikosti in oblike odstranjenega odrezka, oblike rezalnika, hitrosti rezanja in hlajenja.
Za karakterizacijo odpornosti različni materiali cutting vzpostavil koncept rezalnega koeficienta. Faktor rezanja K je rezalni tlak v kilogramih na kvadratni milimeter rezanega odseka, merjen pri določenih pogojih rezanja:
Globina reza t......................5 mm
Pomik s......................1 mm/vr
Pregibni kot γ......................15°
Vodilni kot φ.......45°
Rezalni rob rezalnika - pravokoten, vodoravni
Konica rezalnika je zaobljena s polmerom r = 1 mm
Delo poteka brez hlajenja
V tabeli. 3 prikazuje povprečne vrednosti rezalnega faktorja za nekatere kovine.
Tabela 3
Povprečne vrednosti rezalnega faktorja K pri struženju
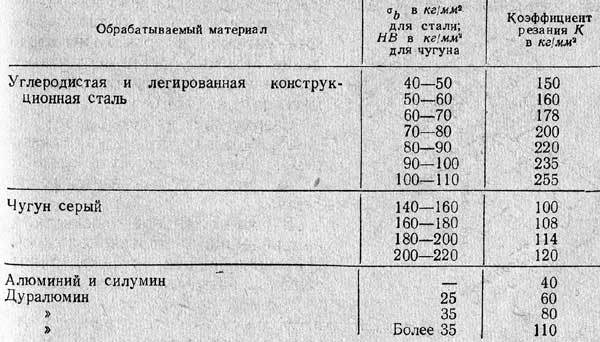
Če je faktor rezanja K znan, lahko z množenjem s površino prečnega prereza reza f v mm 2 po formuli najdete približno vrednost rezalne sile
P z \u003d Kf kg. (osem)
Primer 5 Gred iz strojno izdelanega jekla z σ b = 60 kg / mm 2 je stružena na stružnici. Določite rezalno silo, če je globina reza t = 5 mm in pomik s = 0,5 mm/vrt.
Odločitev. V skladu s formulo (8) rezalna sila P z \u003d Kf kg. (osem) Določimo vrednost f: f \u003d ts \u003d 5x0,5 \u003d 2,5 mm2. Glede na tabelo 3 najdemo vrednost K za strojno izdelano jeklo z σ b \u003d 60 kg / mm 2: K = 160 kg / mm 2. Zato je z = Kf = 160x2,5 = 400 kg. moč rezanja. Če poznate rezalno silo in hitrost rezanja, lahko ugotovite, koliko moči je potrebno za rezanje sekancev določenega odseka.
Moč rezanja je določena s formulo (9) kjer je N res - rezalna moč v hp;
P z - rezalna sila v kg;
v - hitrost rezanja v m/min.
Moč elektromotorja obdelovalnega stroja mora biti nekoliko večja od moči rezanja, saj se del moči elektromotorja porabi za premagovanje trenja v mehanizmih, ki prenašajo gibanje z elektromotorja na vreteno stroja.
Primer 6 Določite moč rezanja za obračanje gredi, obravnavano v prejšnjem primeru, če obdelava poteka pri hitrosti rezanja υ = 60 m/min. Odločitev . Po formuli (9) rezalna moč
Rezalna moč običajno ni izražena v konjskih moči, ampak v kilovatih (kW). Kilovat je 1,36-kratna konjska moč, zato, da izrazite moč v kilovatih, morate konjske moči deliti z 1,36:
in obratno,
10. Toplota reza in življenjska doba orodja
S povečanjem rezalne sile se poveča sila trenja, zaradi česar se poveča količina toplote, ki se sprosti med postopkom rezanja. Toplota rezanja se s povečanjem hitrosti rezanja še poveča, saj se s tem pospeši celoten proces nastajanja odrezkov.
Ustvarjena toplota rezanja z nezadostnim odvzemom le-te zmehča rezalnik, zaradi česar pride do intenzivnejše obrabe njegovega rezalnega dela. Zaradi tega je potrebno menjati rezalnik ali ga izostriti in ponovno namestiti.
Čas neprekinjenega dela rezalnika pred otopenjem se imenuje življenjska doba orodja (merjeno v minutah). Vzroki pogoste menjave rezila (kratka življenjska doba orodja). dodatni stroški za ostrenje in namestitev rezalnika, kot tudi za dopolnitev obrabljenih rezil.
Zato je življenjska doba orodja pomemben dejavnik pri izbiri rezalnih pogojev, še posebej pri izbiri hitrosti rezanja.
Trajnost rezalnika je odvisna predvsem od kakovosti materiala, iz katerega je izdelan. Najbolj odporen bo rezalnik, ki je izdelan iz materiala, ki omogoča najvišjo temperaturo segrevanja brez občutne izgube trdote. Največjo odpornost imajo rezalniki, opremljeni s ploščami iz trde zlitine, mineralno-keramičnimi ploščami; bistveno manjša odpornost - rezila iz hitroreznega jekla, najmanjša - rezila iz ogljikovega orodnega jekla.
Odpornost rezalnika je odvisna tudi od lastnosti materiala, ki se obdeluje, odrezanega odseka, kotov ostrenja rezila in hitrosti rezanja. Povečanje trdote materiala, ki se obdeluje, zmanjša življenjsko dobo orodja.
S spreminjanjem kotov ostrenja in oblike sprednje površine je mogoče doseči znatno povečanje vzdržljivosti rezalnikov in njihove produktivnosti.
Hitrost rezanja še posebej močno vpliva na življenjsko dobo orodja. Včasih že najmanjše povečanje hitrosti vodi do hitrega otopenja rezila. Na primer, če se pri obdelavi jekla s hitrim rezalnikom hitrost rezanja poveča le za 10%, to je 1,1-krat, bo rezalnik dvakrat hitrejši in obratno.
S povečanjem prečnega prereza reza se življenjska doba orodja zmanjša, vendar ne toliko kot pri enakem povečanju hitrosti rezanja.
Življenjska doba orodja je odvisna tudi od velikosti orodja, oblike reza in hlajenja. Bolj masiven je rezalnik, bolje odvaja toploto z rezalnega roba in posledično večja je njegova vzdržljivost.
Poskusi kažejo, da pri enakem odseku reza velika globina reza in manjši pomik zagotavljata večjo življenjsko dobo orodja kot manjša globina reza z ustrezno večjim pomikom. To je razloženo z dejstvom, da pri večji globini reza sekanci pridejo v stik z večjo dolžino rezalnega roba, zato se toplota rezanja bolje odstrani. Zato je z enakim reznim odsekom bolj donosno delati z večjo globino kot z večjim podajanjem.
Obstojnost rezalnika se znatno poveča, ko se ohladi.
Dovod hladilne tekočine mora biti obilen (emulzija 10-12 l/min, olje in sulfofresol 3-4 l/min); majhna količina tekočine ne samo da ne koristi, ampak celo pokvari rezalnik, zaradi česar se na njegovi površini pojavijo majhne razpoke, ki vodijo do sekanja.
11. Izbira hitrosti rezanja
Produktivnost dela je odvisna od izbire hitrosti rezanja: višja kot je hitrost rezanja, tem manj časa porabili za predelavo. Ko pa se hitrost rezanja poveča, se življenjska doba orodja zmanjša, zato na izbiro hitrosti rezanja vpliva življenjska doba orodja in vsi dejavniki, ki vplivajo na življenjsko dobo orodja. Od tega so najpomembnejše lastnosti materiala, ki se obdeluje, kakovost materiala rezalnika, globina reza, pomik, dimenzije rezila in koti ostrenja ter hlajenje.
1. Daljša kot mora biti življenjska doba orodja, nižjo je treba izbrati hitrost rezanja in obratno.
2. Trši kot je material, ki se obdeluje, manjša je življenjska doba orodja, zato je treba za zagotovitev potrebne odpornosti pri obdelavi trdih materialov zmanjšati hitrost rezanja. Pri obdelavi litih in kovanih obdelovancev, na površini katerih je trda skorja, lupine ali luska, je treba zmanjšati hitrost rezanja v primerjavi s tisto, ki je možna pri obdelavi materialov brez skorje.
3. Lastnosti materiala rezalnika določajo njegovo vzdržljivost, zato je od teh lastnosti odvisna tudi izbira hitrosti rezanja. Pri drugih enakih pogojih rezkarji za hitrorezno jeklo omogočajo bistveno višjo hitrost rezanja kot rezila iz ogljikovega jekla; še višje hitrosti rezanja omogočajo rezila, opremljena s trdimi zlitinami.
4. Za povečanje odpornosti rezalnika pri obdelavi viskoznih kovin je koristno uporabiti hlajenje rezalnikov. V tem primeru je z enako življenjsko dobo orodja možno povečati hitrost rezanja za 15-25 % v primerjavi z obdelavo brez hlajenja.
5. Na dovoljeno hitrost rezanja vplivajo tudi dimenzije rezalnika in koti njegovega ostrenja: bolj masiven je rezalnik, predvsem njegova glava, bolje odvaja toploto, ki nastane med rezanjem. Nepravilno izbrani koti rezila, ki ne ustrezajo materialu, ki se obdeluje, povečajo rezalno silo in prispevajo k hitrejši obrabi rezila.
6. S povečanjem reznega preseka se življenjska doba orodja zmanjša, zato je treba pri večjem preseku izbrati nižjo hitrost rezanja kot pri manjšem preseku.
Ker se majhni odrezki odstranijo med končno obdelavo, je lahko hitrost rezanja med končno obdelavo veliko višja kot pri grobi obdelavi.
Ker povečanje reznega odseka manj vpliva na življenjsko dobo orodja kot povečanje hitrosti rezanja, je zaradi rahlega zmanjšanja rezalne hitrosti koristno povečati rezni odsek. Na tem principu temelji metoda obdelave inovatorja strugarja Kuibyshevskega strojnega obrata V. Kolesova. S hitrostjo rezanja 150 m/min T. Kolesov končuje jeklene dele s pomikom do 3 mm/vrt namesto 0,3 mm/vrt, kar vodi do skrajšanja strojnega časa za 8-10-krat.
Postavlja se vprašanje: zakaj napredni stružniki pogosto povečajo produktivnost dela s povečanjem hitrosti rezanja? Ali ni to v nasprotju z osnovnimi zakoni rezanja? Ne, ni v nasprotju. Hitrost rezanja povečajo le v primerih, ko so možnosti za povečanje preseka reza v celoti izkoriščene.
Ko se izvaja polfina ali končna obdelava, kjer je globina reza omejena z majhnim dovoljenjem za obdelavo, pomik pa je omejen z zahtevami visoke čistosti obdelave, je možno povečanje načina rezanja s povečanjem hitrosti rezanja. . To počnejo napredni strugarji, ki delajo pri delni obdelavi in končni obdelavi. Če je mogoče delati z velike odseke rez (z velikimi dodatki), potem je treba najprej izbrati največjo možno globino reza, nato največji možni tehnološko dovoljen podatek in na koncu ustrezno hitrost rezanja.
V primerih, ko je dodatek za obdelavo majhen in ni posebnih zahtev za površinsko obdelavo, je treba način rezanja povečati z uporabo največjega možnega podajanja.
12. Čistost obdelane površine
Pri obdelavi z rezalnikom na obdelani površini dela vedno ostanejo nepravilnosti v obliki vdolbinic in pokrovov, tudi pri najbolj skrbni končni obdelavi. Višina hrapavosti je odvisna od načina obdelave.
Praksa je ugotovila, da čistejša ko je površina dela obdelana, manj je podvržena obrabi in koroziji ter je del močnejši.
Skrbna površinska obdelava pri obdelavi dela je vedno dražja od obdelave grobe površine. Zato je treba čistočo obdelane površine dodeliti glede na pogoje delovanja dela.
Označevanje površinske čistosti na risbah. V skladu z GOST 2789-59 je predvidenih 14 razredov površinske čistosti. Za označevanje vseh razredov čistosti se vzpostavi en znak - enakostranični trikotnik, poleg katerega je navedena številka razreda (na primer 7; 8; 14). Najbolj čiste površine so ocenjene z 14, najbolj grobe pa z oceno 1.
Hrapavost površine po GOST 2789-59 je določena z enim od dveh parametrov: a) srednjim aritmetičnim odklonom profila R a in b) višino nepravilnosti R z.
Za merjenje hrapavosti in dodelitev obdelane površine v določen razred, special merilni instrumenti temelji na metodi tipanja površinskega profila s tanko diamantno iglo. Takšne naprave se imenujejo profilometri in profilografi.
Za določitev hrapavosti in razvrstitev obdelane površine v enega ali drugega razreda čistosti v pogojih delavnice se uporabljajo preizkušeni vzorci različnih razredov čistosti - tako imenovani standardi čistosti, s katerimi se primerja obdelana površina dela.
Dejavniki, ki vplivajo na končno obdelavo površine. Praksa je pokazala, da je čistoča obdelane površine odvisna od več razlogov: materiala, ki se obdeluje, materiala rezalnika, kotov ostrenja in stanja rezalnih robov rezalnika, pomika in hitrosti rezanja, mazanja. in hladilne lastnosti tekočine, togost sistema stroj - rezalnik - del itd.
še posebej pomembnosti da dobim površino Visoka kvaliteta pri struženju ima hitrost rezanja, pomik, naklonske kote in polmer ukrivljenosti konice orodja. Manjši kot je podajanje in vstopni kot ter večji kotni polmer, čistejša je obdelana površina. Hitrost rezanja močno vpliva na končno obdelavo površine. Pri struženju jekla pri hitrosti rezanja več kot 100 m/min je obdelana površina čistejša kot pri hitrosti 25-30 m/min.
Za čistejšo obdelano površino je treba paziti na skrbno ostrenje in končno obdelavo rezalnih robov.
testna vprašanja 1. Kakšne oblike nastane odrezek pri obdelavi viskoznih kovin? Pri obdelavi krhkih kovin?
2. Poimenujte glavne elemente glave sekalca.
3. Pokažite sprednjo in zadnjo površino sekalca; sprednji in zadnji vogali; kot ostrenja.
4. Kakšen je namen sprednjega in zadnjega vogala sekalca?
5. Prikaži vodilne kote in vodilne kote.
6. Iz katerih materialov so izdelani rezkarji?
7. Katere stopnje trdih zlitin se uporabljajo pri predelavi jekla? Pri obdelavi litega železa?
8. Navedite elemente načina rezanja.
9. Kakšne sile delujejo na rezalnik?
10. Kateri dejavniki in kako vplivajo na velikost rezalne sile?
11. Kaj določa vzdržljivost rezalnika?
12. Kateri dejavniki vplivajo na izbiro hitrosti rezanja?
Glavna rezalna orodja, ki se uporabljajo v procesu, vključujejo rezalnik, katerega geometrijski parametri določajo njegove tehnične zmogljivosti, natančnost in učinkovitost obdelave. Vsak specialist, ki se odloči posvetiti obračanje poslov, v kolikor prava izbira koti rezalnega roba povečajo življenjsko dobo orodja in produktivnost.
Parametri stružnih orodij
Kaj orodje za struženje oblikujte držalo, potrebno za pritrditev orodja v držalo stružnica, in delovno glavo, ki omogoča rezanje kovine. Za upoštevanje geometrijskih parametrov stružnega orodja je za vzorec bolje vzeti skoznje orodje.
Na rezalnem delu stružnega orodja te vrste obstajajo tri površine:
- sprednji del (na njem se med obdelavo obdelovanca odstranjujejo kovinski odrezki);
- zadnji - glavni in pomožni (oba obrnjena s sprednjim delom na obdelovanec).
Rob orodja, imenovan rezalni rob (in neposredno vključen v obdelavo), nastane s presečiščem njegove sprednje in glavne zadnje površine. V geometriji stružnega orodja se razlikuje tudi pomožni rezalni rob. Nastane s presečiščem sprednje površine s pomožno zadnjo stranjo.
Točka, na kateri se sekata glavni in sekundarni rezalni rob, se imenuje konica rezalnika. Slednji pri rezanju kovine doživlja ogromne obremenitve, kar vodi do njegovega zloma. Za povečanje odpornosti konice rezalnika se med postopkom ostrenja ne izostri, ampak rahlo zaokroži. To zahteva uvedbo parametra, kot je polmer vrha. Obstaja še en način za povečanje odpornosti konice stružnega orodja - oblikovanje prehodnega rezalnega roba, ki ima pravokotno obliko.
Najpomembnejši geometrijski parametri rezalnikov za struženje so njihovi koti, ki določajo medsebojni dogovor površine orodja. Parametri kota se razlikujejo glede na vrsto stružnega orodja in številne druge dejavnike:
- material za orodje;
- njegove delovne razmere;
- značilnosti materiala, ki ga je treba obdelati.
Orodni koti za struženje
Za pravilno določitev kotov orodje za struženje, njim točne vrednosti, se upoštevajo v tako imenovanih začetnih ravninah.
- Glavna ravnina je vzporedna s smermi podajanja stružnega orodja (vzdolžno in prečno) in sovpada z njegovo podporno površino.
- Rezalna ravnina vključuje glavni rezalni rob in je tangencialna na obdelovalno površino. Ta ravnina je pravokotna na glavno.
- Glavna rezalna ravnina seka glavni rezalni rob in je nameščena pravokotno na projekcijo, ki jo ta rob položi na glavno ravnino. Obstaja tudi pomožna ravnina sekantnega tipa, ki je v skladu s tem pravokotna na projekcijo, ki jo na glavno ravnino nanese pomožni rezalni rob.
Kot že omenjeno, se merijo natančno v teh ravninah, tiste, ki se merijo v ravnini, imenovani glavna sekansa, pa so označene kot glavne. To so predvsem glavni sprednji, glavni zadnji koti, pa tudi koti ostrenja in rezanja.
Eden najpomembnejših je glavni zračni kot stružnega orodja, ki zmanjša trenje, ki nastane, ko zadnja površina orodja sodeluje z delom, ki se trenutno obdeluje (in s tem zmanjša segrevanje orodja in podaljša njegovo življenjsko dobo ). Ta kot tvorita rezalna površina (glavni zadnji del) in rezalna ravnina. Pri izbiri tega kota pri ostrenju orodja se upoštevata vrsta obdelave in material obdelovanca. V tem primeru se morate zavedati, da močno povečanje velikosti zračnega kota vodi do hitre okvare orodja za struženje.
Moč in vzdržljivost rezalnega orodja, sile, ki se pojavijo med obdelavo, določajo parametri nagibnega kota. Nahaja se med sprednjo površino stružnega orodja in ravnino, v kateri se nahaja glavni rezalni rob (ta ravnina je pravokotna na rezalno ravnino). Pri ostrenju stružnega orodja se upoštevajo številni dejavniki, ki vplivajo na vrednost tega kota:
- material obdelovanca in samo orodje;
- oblika sprednje površine;
- pogoji, pod katerimi se bo rezalnik uporabljal.
Povečanje vrednosti nagibnega kota po eni strani izboljša končno obdelavo, po drugi strani pa povzroči zmanjšanje trdnosti in vzdržljivosti stružnega orodja. Tak kot, pridobljen kot posledica ostrenja, ima lahko pozitiven in negativni pomen.
Rezalni stroji z nagibnimi koti, ki imajo negativne vrednosti, so zelo trpežni, vendar jih je težko obdelovati s takšnimi orodji. Običajno se ostrenje z nagibnim kotom, ki ima pozitivno vrednost, uporablja, kadar je treba obdelovanec obdelati iz viskoznega materiala in tudi kadar je material orodja zelo trpežen.
Rezalniki z negativnimi nagibnimi koti se uporabljajo pri obdelavi materialov z visoko trdoto in trdnostjo, pri izvajanju prekinjenega rezanja, ko material orodja nima zadostne upogibne trdnosti in slabo absorbira udarne obremenitve.
Parametri, ki označujejo geometrijo rezalnika za struženje, so tudi koti rezanja in kazalca. Kot rezanja, katerega vrednost se lahko spreminja v območju 60–100 0, se nahaja med površino orodja, imenovano sprednja stran, in rezalno ravnino.
Vrednost tega kota je neposredno odvisna od trdote kovine, ki se obdeluje: višja kot je, večja je njena vrednost. Kot konus je popolnoma skladen z njegovim imenom, meri se med glavno sprednjo in glavno zadnjo površino orodja in označuje stopnjo ostrenja njegovega vrha.
Označite orodje za struženje in kote v načrtu. To je glavni, merjen med smerjo vzdolžnega podajanja in projekcijo, ki jo glavni rezalni rob položi na glavno ravnino, in pomožni, ki ga tvori projekcija pomožnega rezalnega roba na glavno ravnino in smer vzdolžni dovod.
Pri ostrenju ti koti niso izbrani poljubno, temveč glede na vrsto struženja in togost, ki jo ima sistem "stroj-orodje-obdelovanec". Torej lahko obdelavo večine kovin izvedemo z orodji z glavnim kotom v načrtu 45 0, tanke in dolge obdelovance pa je treba obdelati z rezalniki, pri katerih je vrednost tega kota v območju 60– 90 0 . To je potrebno za odpravo upogibanja in tresenja dela.
Pomožni kot v vodilu je hkrati koreliran s končno obdelavo in z življenjsko dobo orodja. Z njegovo zmanjšanjem se poveča čistoča obdelave in podaljša življenjska doba orodja.
Poleg zgoraj obravnavanih v geometriji stružnih orodij ločimo kote.
Vzdolžno struženje se imenuje struženje, pri katerem je smer gibanja podajalnika vzporedna z osjo obdelovanca. Na stružnicah je rezalno gibanje - vrtenje - pritrjeno na obdelovanec, gibanje podajanja - translacijsko gibanje - pa na rezalnik. Na strojih z okroglimi palicami se rezalno orodje vrti, pomik pa je pritrjen na obdelovanec. Prava pot rezanja je vijačna črta.
Razlikovati med finim in grobim struženjem.
Fino struženje (slika 2, a) se izvaja z rezalnikom z ravnimi delovnimi površinami in ravnimi rezalnimi robovi - glavnim in pomožnim. Položaj rezalnih robov glede na os vrtenja obdelovanca je značilen z glavnim kotom v vodilu in pomožnim kotom v vodilu. Vrednost pomožnega kota v načrtu določa globino kinematičnih nepravilnosti, zato ne more biti večja. Položaj ploskev, ki tvorijo glavni rezalni rob, je značilen po zračnem kotu, kotu ostrenja in sprednjem kotu.
Glavni rezalni rob omogoča prečno rezanje, za katerega je značilen kot nagiba lesnih vlaken.
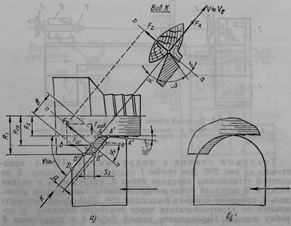
riž. 2. Končna obdelava vzdolžnega struženja (a) in groba obdelava (b)
Kot naklona se meri med smerjo vlaken in normalo.
Grobo struženje (slika 2, b) se izvaja z žlebljenimi rezalniki s polkrožnim rezalnim robom. Prečni prerez odrezki so srpasti, debelina odrezkov na obodu obdelovanca je največja, blizu površine dela pa je zanemarljiva tudi pri velikem podajanju rezalnika. To vam omogoča, da uporabite podajanje na rezilo do 2 mm, medtem ko za fino struženje - ne več kot 0,8 mm.
> Postavitev stružnic
Pri nastavljanju stružnic je potrebno: izbrati rezalnik in ga pritrditi v držalo orodja (za stroje z mehanskim pomikom); namestite prednjo ploščo ali vpenjalno glavo; izberite in pritrdite naslon za roke (za stroje z ročno dovajanje) ali kopirnim ravnilom (za stroje z mehanskim podajanjem); namestite in pritrdite obdelovanec v stroj; preizkusite stroj v prostem teku; nastavite hitrost vretena in pomik; obdelati in pregledati testne kose.
Zahtevani rezalnik je izbran glede na naravo opravljenega dela. Za začetno grobo obdelavo uporabljamo rezalnik za luščenje, za končno pa končni rezalnik z ravnim rezalnim robom. Z mehanskim pomikom je rezalnik pritrjen v držalo orodja z vijaki. Za skrajšanje časa menjave se uporabljajo posebne rotacijske glave, kjer se hkrati krepi več sekalcev za različne namene.
Pri ročno delo je treba preveriti zanesljivost pritrditve rezalnika na leseni ročaj. Ne uporabljajte pokvarjenega rezalnega orodja.
Sredstva za pritrditev obdelovanca so izbrana glede na njegovo obliko in velikost. Za pritrditev dolgih obdelovancev (slika 3, a) se uporabljajo sprednji in zadnji centri. Sprednji center 2 je izdelan v obliki trikrakega povodca s stožčastim steblom, s katerim je vstavljen v stožčasto luknjo vretena 1. Zadnji center 4 ima stožčasti in koničasti del in je pritrjen v pero 5 zadnjega nosilca 6. Za zmanjšanje trenja in povečanje zanesljivosti pritrditve obdelovanca je zadnji center nameščen na ležaju, ki zagotavlja njegovo vrtenje z obdelovancem 3.

riž. 3. Pritrditev obdelovanca v stružnicah: a - v središčih, b - v vpenjalni glavi, c - na čelni plošči; 1 - vreteno, 2 - sprednja sredina, 3 - obdelovanec, 4 - sredina zadaj, 5 - pero, 6 - zadnji del, 7 - vpenjalna glava, 8 - načrt
Glede na dolžino obdelovanca, ki se obdeluje, se zadnji del premakne vzdolž vodil postelje in pritrdi v vnaprej določenem položaju. Obdelovanec fiksiramo tako, da pero potisnemo iz glave, dokler se središča ne vgradijo v konce obdelovanca in ga med vrtenjem varno držijo. Za obračanje konusnih delov je treba telo zadnjega nosilca prečno premakniti z nastavitvenim vijakom in ga pritrditi z blokirno napravo. Vpenjalne glave so namenjene za pritrditev kratkih obdelovancev (slika 3, b). Vpenjalna glava 7 ima navoj, skozi katerega je privit na vreteno. Obdelovanec je pritrjen v vpenjalno glavo tako, da se njegov konec trdno prilega v luknjo vpenjalne glave. Uporabljajo se tudi vpenjalne glave in vpenjalne glave z drsnimi čeljustmi.
Za vpenjanje obdelovancev kratke dolžine in velik premer služijo kot prednje plošče 8 (slika 3, c), privite na vreteno. Obdelovanec je pritrjen na prednjo ploščo z vijaki ali vijaki 9.
Ročnik je nameščen na okvirju tako, da je njegov delovni rob na ravni središč in je blizu generatrike obdelovanca, ki se obdeluje, vendar se ga ne dotika. Z zmanjšanjem premera in pri obdelavi dolgih obdelovancev se ročni del zaporedoma prestavi v nov položaj vzdolž vodil ležišča. Pri obdelavi oblikovanih izdelkov na zadnji strani postelje je na nosilce pritrjeno kopirno ravnilo, katerega oblika je podobna obliki končnega dela. Ko je podajanje vklopljeno, se čeljust premika po ukrivljeni poti in rezalnik reproducira dano obliko dela.
Hitrost vretena je izbrana glede na premer obdelovanca in njegovo moč. Za večje premere je treba nastaviti najmanjšo hitrost vretena. Pri nameščanju prednje plošče s premerom 400 mm hitrost vretena ne sme presegati 800 vrt/min. Hitrost vrtenja se zmanjša s prestavno ročico ali s spreminjanjem vrtilne hitrosti večstopenjskega elektromotorja. hitrost rezanja lesa mehke skale mora biti 10 ... 12 m / s, trdna - 0,5 ... 3 m / s.
Vzdolžni pomik na en obrat vretena mora biti: za grobo obdelavo 1,6 ... 2 mm, za končno obdelavo - ne več kot 0,8 mm. Višje kot so zahteve glede hrapavosti površine, nižji mora biti vzdolžni pomik. Prečni pomik na vrtenje vretena ne sme presegati 1,2 mm. Preden zaženete stroj, se prepričajte zanesljivo pritrditev praznine in namestite ograjo.
Po grobi obdelavi dela se rezalnik zamenja in fino struženje se izvede pri nizkem podajanju. Odrezki v tem primeru morajo biti čim bolj neprekinjeni in enakomerne debeline.
Med obdelavo obliko dela občasno nadzorujemo s šablono ali merilnikom. Pri uporabi kalibra oz merilno orodje s tehtnico se stroj izklopi in šele potem, ko se del popolnoma ustavi, se meri.
Po končani nastavitvi se izvede poskusna obdelava dela in njegove dimenzije se nadzorujejo s kalibrom ali merilnim orodjem z lestvico.