Disegno a macchina cnc fatto in casa. Come realizzare un router cnc fatto in casa per metallo
Per realizzare un disegno tridimensionale superficie in legno vengono utilizzate fresatrici CNC di fabbrica per legno. È difficile realizzare un mini modello simile con le tue mani a casa, ma è possibile con uno studio dettagliato del design. Per fare ciò, è necessario comprendere le specifiche, scegliere i componenti giusti e configurarli.
Il principio di funzionamento della fresatrice
Moderna attrezzatura per la lavorazione del legno con blocco numerico controllo del programma progettato per formare un motivo complesso su legno. Il progetto deve contenere una parte elettronica meccanica. In combinazione, automatizzano il più possibile il processo di lavoro.
Per realizzare un desktop su legno con le tue mani, dovresti familiarizzare con i componenti principali. L'elemento di taglio è una fresa, che è installata in un mandrino posizionato sull'albero del motore. Questo disegno è attaccato al letto. Può muoversi lungo due assi di coordinate - x; y. Per riparare il pezzo, è necessario realizzare un tavolo di supporto.
La centralina elettronica è collegata ai motori passo passo. Forniscono lo spostamento del carrello rispetto alla parte. Usando questa tecnologia, puoi realizzare disegni 3D su una superficie di legno.
La sequenza di funzionamento della mini-attrezzatura con CNC, che puoi realizzare tu stesso.
- Scrivere un programma in base al quale verrà eseguita la sequenza di movimenti della parte tagliente. Per fare ciò, è meglio utilizzare sistemi software speciali progettati per l'adattamento in modelli fatti in casa.
- Posizionamento del pezzo sul tavolo.
- Output del programma al CNC.
- Accensione delle apparecchiature, monitoraggio dell'implementazione di azioni automatiche.
Per ottenere la massima automazione del lavoro in modalità 3D, dovrai redigere correttamente un diagramma e selezionare i componenti appropriati. Gli esperti consigliano di studiare i modelli di fabbrica prima di realizzare un mini- fresatrice con le tue stesse mani.
Per creare motivi e motivi complessi su una superficie di legno, avrai bisogno di diversi tipi di taglierine. Alcuni di loro puoi farli da solo, ma per un buon lavoro, dovresti acquistare quelli di fabbrica.
Schema di una fresatrice artigianale a controllo numerico
La fase più difficile è la scelta dello schema di produzione ottimale. Dipende dalle dimensioni del pezzo e dal grado della sua lavorazione. Per uso domesticoè consigliabile realizzare un desktop fai-da-te, che avrà il numero ottimale di funzioni.
L'opzione miglioreè la fabbricazione di due carrelli che si muoveranno lungo gli assi delle coordinate x; y. È meglio usare barre d'acciaio rettificate come base. I carrelli saranno montati su di loro. Per creare una trasmissione sono necessari motori passo-passo e viti con cuscinetti volventi.
Per la massima automazione del processo nella progettazione di una mini fresatrice per legno CNC fai-da-te, è necessario pensare in dettaglio alla parte elettronica. Convenzionalmente, è costituito dai seguenti componenti:
- alimentatore. È necessario fornire elettricità ai motori passo-passo e al chip del controller. Utilizzare spesso il modello 12v 3A;
- controllore. È progettato per dare comandi a motori elettrici. Per il funzionamento di una mini fresatrice CNC fai-da-te è sufficiente un semplice circuito per controllare il funzionamento di tre motori;
- autista. Costituisce inoltre un elemento di regolazione del funzionamento della parte mobile della struttura.
Il vantaggio di questo complesso è la possibilità di importare file eseguibili dei formati più comuni. Utilizzando un'applicazione speciale, è possibile creare un disegno tridimensionale della parte per l'analisi preliminare. I motori passo-passo funzioneranno a una certa frequenza di corsa. Ma per questo devi fare specifiche tecniche al programma di controllo.
Scelta di accessori per fresatrice CNC
Il prossimo passo è selezionare i componenti per l'assemblaggio di apparecchiature fatte in casa. L'opzione migliore è usare mezzi improvvisati. Come base per i modelli desktop di una macchina 3D, puoi utilizzare legno, alluminio o plexiglass.
Per corretto funzionamento dell'intero complesso, è necessario sviluppare il design delle pinze. Durante il loro movimento non dovrebbero esserci vibrazioni, questo può portare a una fresatura imprecisa. Pertanto, prima del montaggio, tutti i componenti vengono verificati per verificarne la compatibilità tra loro.
- guide. Vengono utilizzate barre di acciaio lucido con un diametro di 12 mm. La lunghezza per l'asse x è 200 mm, per l'asse y è 90 mm;
- calibro. Textolite è l'opzione migliore. La dimensione normale della piattaforma è 25*100*45 mm;
- motori passo passo. Gli esperti consigliano di utilizzare modelli da una stampante 24v, 5A. A differenza delle unità disco, hanno più potenza;
- blocco tagliente. Può anche essere fatto da textolite. La configurazione dipende direttamente dallo strumento disponibile.
L'alimentatore è assemblato al meglio dalla fabbrica. In autoproduzione sono possibili errori che influiscono successivamente sul funzionamento di tutte le apparecchiature.
La procedura per la produzione di una fresatrice CNC
Dopo aver selezionato tutti i componenti, puoi realizzare tu stesso un mini router per legno CNC desktop con le tue mani. Tutti gli elementi vengono preliminarmente ricontrollati, ne vengono controllate le dimensioni e la qualità.
Per riparare gli elementi dell'attrezzatura, è necessario utilizzare elementi di fissaggio speciali. La loro configurazione e forma dipendono dallo schema scelto.
La procedura per l'assemblaggio di apparecchiature desktop mini CNC per legno con funzione di elaborazione 3D.
- Installazione di guide pinza, loro fissaggio sulle parti laterali della struttura. Questi blocchi non sono ancora installati sulla base.
- Lappatura delle pinze. Devono essere spostati lungo le guide fino ad ottenere una guida fluida.
- Serrare i bulloni per fissare le pinze.
- Fissaggio di componenti alla base dell'apparecchiatura.
- Installazione di madreviti insieme ai giunti.
- Installazione di motori di azionamento. Sono fissati alle viti di accoppiamento.
La parte elettronica si trova in un blocco separato. Ciò aiuta a ridurre la probabilità di malfunzionamento durante il funzionamento del router. Anche punto importanteè la scelta del piano di lavoro per l'installazione delle apparecchiature. Deve essere a livello, poiché i bulloni di regolazione del livello non sono forniti nel progetto.
Una condizione per le prestazioni della lavorazione professionale del legno è la presenza di una fresatrice CNC. Strade disponibili in commercio e non tutti possono permetterselo. Pertanto, molti li realizzano con le proprie mani, risparmiando denaro e godendosi il processo creativo.
Esistono due opzioni per la produzione di mini macchine per la fresatura del legno:
- acquisto di un set di parti e sua fabbricazione (kit per modellisti che costano da 40 a 110 mila rubli);
- fallo con le tue mani.
Considera la produzione di mini fresatrici CNC con le tue mani.
Scelta delle caratteristiche del design
L'elenco delle azioni nello sviluppo e nella produzione di un mini dispositivo per la fresatura del legno è il seguente:
- Inizialmente, devi decidere di che tipo di lavoro stiamo parlando. Questo ti dirà quali dimensioni e spessori delle parti possono essere elaborati su di esso.
- Crea un layout e un elenco stimato di parti per una macchina desktop fatta in casa per la produzione fai-da-te.
- Scegli il software portandolo dentro condizioni di lavoro in modo che funzioni secondo il programma indicato.
- Acquista i componenti, le parti, i prodotti necessari.
- Avere disegni, creare gli elementi mancanti con le tue mani, assemblare ed eseguire il debug del prodotto finito.
Design
Una macchina fatta in casa è composta dalle seguenti parti principali:
- letto con un tavolo posizionato su di esso;
- calibri con la possibilità di muovere la taglierina in tre coordinate;
- mandrino con fresa;
- guide per lo spostamento di pinze e portale;
- un alimentatore che fornisce elettricità ai motori, un controller o una scheda di commutazione tramite microcircuiti;
- autisti per stabilizzare il lavoro;
- aspirapolvere per segatura.
Le guide sono installate sul telaio per spostare il portale lungo l'asse Y. Le guide sono posizionate sul portale per spostare la pinza lungo l'asse X. Il mandrino con la fresa è montato sulla pinza. Si muove lungo le sue guide (asse Z).
Il controller e i driver forniscono l'automazione della macchina CNC trasmettendo comandi ai motori elettrici. L'utilizzo del pacchetto software Kcam consente di utilizzare qualsiasi controller e fornisce il controllo del motore in base al disegno del pezzo inserito nel programma.
Il design deve essere reso rigido per resistere alle forze di lavoro che si verificano durante il funzionamento e non provocare vibrazioni. Le vibrazioni porteranno a una diminuzione della qualità del prodotto risultante, alla rottura dell'utensile. Pertanto, le dimensioni degli elementi di fissaggio devono garantire la solidità della struttura.
Una fresatrice CNC fatta in casa viene utilizzata per ottenere un'immagine 3D tridimensionale dettaglio in legno. È fissato sul tavolo questo dispositivo. Può essere utilizzato anche come incisore. Il design garantisce il movimento del corpo di lavoro: il mandrino con la fresa installata secondo il programma di azioni specificato. Il movimento della pinza lungo gli assi X e Y avviene lungo guide lucidate mediante motori passo-passo.
Spostando il mandrino lungo l'asse Z verticale è possibile modificare la profondità di lavorazione sul disegno creato sull'albero. Per ottenere un disegno in rilievo 3D, è necessario realizzare dei disegni. Si consiglia di utilizzare diversi tipi frese che ti permetteranno di ottenere migliori parametri visualizzazione delle immagini.
Selezione dei componenti
Per le guide si utilizzano aste in acciaio D = 12 mm. Per una migliore movimentazione dei carrelli, sono rettificati. La loro lunghezza dipende dalle dimensioni del tavolo. È possibile utilizzare barre di acciaio temprato da una stampante ad aghi.
I motori passo-passo possono essere utilizzati da lì. I loro parametri: 24 V, 5 A.
È desiderabile fornire il fissaggio delle frese con una pinza.
È meglio utilizzare un alimentatore fabbricato in fabbrica per una mini fresatrice fatta in casa, poiché le prestazioni dipendono da esso.
Il controller deve utilizzare condensatori e resistori nei pacchetti SMD per il montaggio su superficie.
Assemblea
Per assemblare una macchina fatta in casa per la fresatura di parti in legno 3D con le tue mani, devi fare disegni, prepararti strumento essenziale, accessori, realizzare le parti mancanti. Dopodiché, puoi iniziare a montare.
La sequenza di montaggio fai da te di una mini macchina CNC con lavorazione 3D è composta da:
- le guide della pinza sono installate nelle pareti laterali insieme al carrello (senza viti).
- i carrelli vengono spostati lungo le guide fino a quando il loro movimento non diventa regolare. Pertanto, i fori nella pinza sono lappati.
- bulloni di serraggio sulle pinze.
- fissaggio delle unità di montaggio sulla macchina e installazione di viti.
- installazione di motori passo-passo e loro collegamento con viti mediante giunti.
- il controller è allocato in un blocco separato per ridurre l'influenza dei meccanismi operativi su di esso.
Una macchina CNC fatta in casa dopo il montaggio deve essere testata! Il test dell'elaborazione 3D viene eseguito utilizzando le modalità di risparmio per identificare tutti i problemi e risolverli.
Il funzionamento in modalità automatica è fornito dal software. Gli utenti avanzati di computer possono utilizzare alimentatori e driver per controller, motori passo-passo. L'alimentatore converte la corrente alternata in ingresso (220 V, 50 Hz). DC necessario per alimentare il controller e i motori passo-passo. Per loro, il controllo della macchina da un personal computer passa attraverso la porta LPT. I programmi di lavoro sono Turbo CNC e VRI-CNC. I programmi di editor grafico CorelDRAW e ArtCAM vengono utilizzati per preparare i disegni necessari per l'implementazione in un albero.
Risultati
La mini fresatrice CNC fatta in casa per parti 3D è facile da usare, garantisce precisione e qualità della lavorazione. Se devi eseguire lavori più complessi, devi utilizzare motori passo-passo di maggiore potenza (ad esempio: 57BYGH-401A). In questo caso, per muovere le pinze, è necessario utilizzare delle cinghie dentate per ruotare le viti, e non una frizione.
L'installazione dell'alimentatore (S-250-24), della scheda di commutazione, dei driver può essere eseguita nel vecchio case dal computer, modificandolo. Può essere dotato di un pulsante rosso "stop" per l'arresto di emergenza dell'apparecchiatura.
Se trovi un errore, evidenzia un pezzo di testo e fai clic Ctrl+Invio.
Un set con cui puoi assemblare la tua fresatrice CNC.
Le macchine utensili già pronte sono vendute in Cina, una recensione di una di esse è già stata pubblicata su Muska. Montiamo noi stessi la macchina. Benvenuto…
UPD: collegamenti ai file
Darò comunque un collegamento a una recensione della macchina finita di AndyBig. Non mi ripeterò, non citerò il suo testo, scriveremo tutto da zero. Il titolo elenca solo un set con motori e un pilota, ci saranno più parti, cercherò di dare collegamenti a tutto.
E questo... Mi scuso in anticipo con i lettori, non ho fatto foto in modo specifico nel processo, perché. in quel momento non avevo intenzione di fare una recensione, ma alzerò un massimo di foto del processo e proverò a dare descrizione dettagliata tutti i nodi.
Lo scopo della recensione non è tanto quello di vantarsi quanto di mostrare l'opportunità di creare un assistente per te stesso. Spero che questa recensione possa dare un'idea a qualcuno, ed è possibile non solo ripeterla, ma anche renderla ancora migliore. Andare…
Come è nata l'idea:
È successo che sono stato associato ai disegni per molto tempo. Quelli. mio attività professionale strettamente legati ad essi. Ma una cosa è quando si crea un disegno, e poi persone completamente diverse danno vita all'oggetto di design, ed è un'altra cosa quando si dà vita all'oggetto di design da soli. E se con la costruzione mi sembra che vada bene, allora con la modellazione e altre arti applicate, non proprio.
Quindi per molto tempo c'è stato un sogno da un'immagine disegnata in AutoCAD, per fare un colpo - ed è in natura davanti a te, puoi usarlo. Questa idea scivolava di tanto in tanto, ma non poteva prendere forma in nulla di concreto, finché...
Fino a quando non ho visto REP-RAP tre o quattro anni fa. Ebbene, la stampante 3D è stata una cosa molto interessante, e l'idea di assemblarmi ha richiesto molto tempo per prendere forma, ho raccolto informazioni su diversi modelli sui pro e i contro diverse opzioni. A un certo punto, facendo clic su uno dei collegamenti, sono arrivato a un forum in cui le persone erano sedute e discutevano non di stampanti 3D, ma di fresatrici CNC. E da qui, forse, l'hobby inizia il suo viaggio.
Invece di teoria
In poche parole sulle fresatrici a controllo numerico (scrivo con parole mie intenzionalmente, senza copiare articoli, libri di testo e manuali).
Una fresatrice funziona esattamente al contrario di una stampante 3D. Nella stampante, passo dopo passo, strato dopo strato, si costruisce il modello fondendo i polimeri, in una fresatrice, con l'ausilio di una taglierina, si rimuove dal pezzo “tutto ciò che è superfluo” e si ottiene il modello richiesto.
Per far funzionare una macchina del genere, è necessario il minimo necessario.
1. Base (corpo) con guide lineari e meccanismo di trasmissione (può essere a vite oa cinghia)
2. Mandrino (vedo qualcuno sorridere, ma è così che si chiama) - il vero motore con una pinza in cui è installato uno strumento di lavoro - una fresa.
3. Motori passo-passo - motori che consentono movimenti angolari controllati.
4. Controller: una scheda di controllo che trasmette la tensione ai motori in base ai segnali ricevuti dal programma di controllo.
5. Computer con programma di controllo installato.
6. Abilità di disegno di base, pazienza, desiderio e buon umore.))
I punti:
1. Base.
per configurazione:
Mi dividerò in 2 tipi, ci sono opzioni più esotiche, ma le 2 principali:
Con portale mobile:
In realtà, il design che ho scelto, ha una base su cui sono fissate le guide lungo l'asse X. Un portale si muove lungo le guide dell'asse X, su cui si trovano le guide dell'asse Y, e il nodo dell'asse Z si muove lungo esso.
Con portale statico
Questo disegno si rappresenta come un corpo, è anche un portale su cui si trovano le guide dell'asse Y e il nodo dell'asse Z si muove lungo di esso e l'asse X si sta già muovendo rispetto al portale.
Per materiale:
il corpo può essere fatto da materiali diversi, il più comune:
- duralluminio - ha un buon rapporto tra massa e rigidità, ma il prezzo (solo per un prodotto fatto in casa per hobby) è ancora deprimente, anche se se ci sono opinioni sulla macchina per fare soldi seri, non ci sono opzioni.
- compensato - buona rigidità con spessore sufficiente, peso ridotto, capacità di lavorare con qualsiasi cosa :) e il prezzo stesso, un foglio di compensato 17 ora è piuttosto economico.
- acciaio - spesso utilizzato su macchine con un'ampia area di lavorazione. Una macchina del genere, ovviamente, deve essere statica (non mobile) e pesante.
- MFD, plexiglass e policarbonato monolitico, anche truciolare - ha visto anche tali opzioni.
Come puoi vedere, il design della macchina stessa è molto simile sia a una stampante 3D che a un incisore laser.
Non scrivo deliberatamente sui progetti di fresatrici a 4, 5 e 6 assi, perché. all'ordine del giorno c'è una macchina per hobby fatta in casa.
2. Mandrino.
In realtà, i mandrini sono dotati di raffreddamento ad aria e ad acqua.
I raffreddati ad aria sono alla fine più economici, perché. per loro non è necessario bloccare un circuito dell'acqua aggiuntivo, funzionano un po' più rumorosamente di quelli dell'acqua. Il raffreddamento è fornito da a lato posteriore una girante, che alle alte velocità crea un flusso d'aria tangibile che raffredda l'alloggiamento del motore. Più potente è il motore, più serio è il raffreddamento e maggiore è il flusso d'aria, che può ben gonfiarsi in tutte le direzioni
polvere (trucioli, segatura) del pezzo.
Acqua raffreddata. Un tale mandrino funziona quasi in silenzio, ma alla fine, comunque, non si sente la differenza tra loro nel processo di lavoro, poiché il suono del materiale in lavorazione dalla taglierina lo bloccherà. Non c'è tiraggio dalla girante, in questo caso, ovviamente, ma c'è un circuito idraulico aggiuntivo. In un tale circuito devono essere presenti tubazioni, una pompa per il pompaggio del liquido e un luogo per il raffreddamento (radiatore con flusso d'aria). Di solito non viene versata acqua in questo circuito, ma TOSOL o glicole etilenico.
Esistono anche mandrini di varie capacità, e se quelli a bassa potenza possono essere collegati direttamente alla scheda di controllo, allora i motori con una potenza di 1 kW o più devono essere collegati tramite l'unità di controllo, ma non si tratta di noi.))
Sì, spesso nelle macchine casalinghe si installano smerigliatrici dirette, o frese con base smontabile. Tale decisione può essere giustificata, soprattutto quando si eseguono lavori di breve durata.
Nel mio caso è stato scelto un mandrino raffreddato ad aria da 300 W.
3. Motori passo-passo.
I motori più utilizzati sono di 3 taglie
NEMA17, NEMA23, NEMA 32
differiscono per dimensioni, potenza e momento di lavoro
I NEMA17 sono solitamente utilizzati nelle stampanti 3D, sono troppo piccoli per una fresatrice, perché. è necessario trasportare un portale pesante, a cui viene applicato anche un carico laterale durante la lavorazione.
NEMA32 per un tale mestiere non è necessario, inoltre, dovresti prendere un'altra scheda di controllo.
la mia scelta è caduta su NEMA23 con una potenza massima per questa scheda - 3A.
Inoltre, le persone usano gli stepper dalle stampanti, ma da allora. Non li avevo nemmeno io e dovevo ancora comprare, ho scelto tutto nel kit.
4. Controllore
Una scheda di controllo che riceve i segnali dal computer e trasmette la tensione ai motori passo-passo che muovono gli assi della macchina.
5. Computer
Hai bisogno di un computer separato (possibilmente molto vecchio) e ci sono, forse, due ragioni per questo:
1. È improbabile che tu decida di posizionare una fresatrice vicino al luogo in cui sei abituato a leggere Internet, giocare a giocattoli, fare contabilità, ecc. Semplicemente perché la fresatrice è rumorosa e polverosa. Di solito la macchina è in officina o in garage (meglio riscaldata). La mia macchina è in garage, è per lo più inattiva in inverno, perché. nessun riscaldamento.
2. Per motivi economici, di solito vengono utilizzati computer che non sono più rilevanti per la vita domestica - molto utilizzati :)
Requisiti per l'auto in generale per nulla:
- dal Pentium 4
- la presenza di una scheda video discreta
- RAM da 512 MB
- la presenza di un connettore LPT (su USB non dico nulla, non ho ancora studiato le novità per via del driver che funziona su LPT)
un computer del genere o viene preso dalla dispensa o, come nel mio caso, viene acquistato quasi per niente.
A causa della bassa potenza della macchina, si cerca di non installare software aggiuntivo, ad es. solo asse e programma di controllo.
Poi ci sono due opzioni:
- installa Windows XP (è un computer debole, ricordi giusto?) e il programma di controllo MATCH3 (ce ne sono altri, ma questo è il più popolare)
- mettiamo niks e Linux CNC (dicono che anche tutto è molto buono, ma non ho imparato i niks)
Aggiungerò, forse, per non offendere persone eccessivamente ricche, che è del tutto possibile non mettere un quarto moncone, ma una specie di ai7 - per favore, se ti piace e te lo puoi permettere.
6. Abilità di disegno di base, pazienza, desiderio e buon umore.
Qui in poche parole.
Per far funzionare la macchina è necessario un programma di controllo (essenzialmente un file di testo contenente le coordinate dei movimenti, velocità di movimento e accelerazione), che a sua volta viene preparato in un'applicazione CAM - solitamente ArtCam, in questa applicazione viene preparato il modello stesso, la sua vengono impostate le dimensioni e viene selezionato un utensile da taglio.
Di solito prendo un percorso leggermente più lungo, faccio un disegno, quindi AutoCad, salvandolo *.dxf, lo carico su ArtCam e preparo l'UE lì.
Bene, iniziamo il processo di creazione del tuo.
Prima di progettare una macchina, prendiamo come punti di partenza diversi punti:
- I semiassi saranno realizzati con prigionieri di costruzione con filettatura M10. Certo, ci sono senza dubbio più opzioni tecnologiche: un albero con filettatura trapezoidale, una vite a ricircolo di sfere (vite a ricircolo di sfere), ma bisogna capire che il prezzo della questione lascia molto a desiderare, e per una macchina da hobby, il prezzo è generalmente lo spazio. Tuttavia, nel tempo, aggiornerò e sostituirò la forcina con un trapezio.
- Il materiale del corpo macchina è compensato da 16 mm. Perché compensato? Disponibile, economico, allegro. In realtà ci sono molte opzioni, qualcuno fa da duralluminio, qualcuno da plexiglass. Preferisco il compensato.
Realizzazione di un modello 3D:
Alesatore:
Poi ho fatto questo, non c'era più immagine, ma penso che sarà chiaro. Ho stampato una scansione su fogli trasparenti, li ho ritagliati e incollati su un foglio di compensato.
Pezzi segati e fori praticati. Degli strumenti: un seghetto alternativo e un cacciavite.
C'è un altro piccolo trucco che renderà la vita più facile in futuro: prima di praticare i fori, stringi tutte le parti accoppiate con un morsetto e fora attraverso, in modo da ottenere fori che si trovano ugualmente su ciascuna parte. Anche se si verifica una leggera deviazione durante la perforazione, le parti interne delle parti collegate combaciano e il foro può essere leggermente alesato.
Parallelamente, facciamo una specifica e iniziamo a ordinare tutto.
cosa mi è successo:
1. Il set specificato in questa recensione include: scheda di controllo del motore passo-passo (driver), motori passo-passo NEMA23 - 3 pezzi, alimentazione 12V, cavo LPT e dispositivo di raffreddamento.
2. Mandrino (questo è il più semplice, ma fa comunque il suo lavoro), elementi di fissaggio e un'alimentazione a 12V.
3. Computer usato Pentium 4, soprattutto, la scheda madre ha LPT e una scheda video discreta + monitor CRT. L'ho portato ad Avito per 1000 rubli.
4. Albero in acciaio: Ф20mm - L=500mm - 2pz, Ф16mm - L=500mm - 2pz, Ф12mm - L=300mm - 2pz.
L'ho preso qui, a quel tempo a San Pietroburgo si è rivelato più costoso da prendere. È arrivato in 2 settimane.
5. Cuscinetti lineari: f20 - 4 pz., f16 - 4 pz., f12 - 4 pz.
20
16
12
6. Fissaggi per alberi: f20 - 4 pz., f16 - 4 pz., f12 - 2 pz.
20
16
12
7. Dadi Caprolon con filettatura M10 - 3 pz.
Ho portato con me gli alberi su duxe.ru
8. Cuscinetti di rotazione, chiusi - 6 pz.
Nello stesso posto, ma anche i cinesi ne hanno molti
9. Filo PVA 4x2,5
è offline
10. Ingranaggi, tasselli, dadi, morsetti: un mucchio.
Questo è anche offline, nell'hardware.
11. È stato anche acquistato un set di frese
Quindi ordiniamo, aspettiamo, tagliamo e raccogliamo.
Inizialmente, il driver e l'alimentatore sono stati installati nella custodia insieme al computer.
Successivamente è stato deciso di posizionare l'autista in una custodia separata, è appena apparso.
Bene, il vecchio monitor in qualche modo è cambiato in uno più moderno.
Come dicevo all'inizio, non avrei mai pensato di scrivere una recensione, quindi allego le foto dei nodi, e cercherò di spiegare il processo di assemblaggio.
Innanzitutto, assembliamo tre assi senza viti per allineare gli alberi nel modo più accurato possibile.
Prendiamo le pareti anteriore e posteriore dell'alloggiamento, fissiamo le flange per gli alberi. Incordiamo 2 cuscinetti lineari sull'asse X e li inseriamo nelle flange.
Fissiamo la parte inferiore del portale ai cuscinetti lineari, proviamo a far rotolare la base del portale avanti e indietro. Siamo convinti della curvatura delle nostre mani, smontiamo tutto e foriamo un po'.
Pertanto, otteniamo una certa libertà di movimento degli alberi. Ora inseriamo le flange, inseriamo gli alberi al loro interno e spostiamo la base del portale avanti e indietro per ottenere una scorrevolezza regolare. Stringiamo le flange.
In questa fase è necessario verificare l'orizzontalità degli alberi, nonché il loro allineamento lungo l'asse Z (in breve, in modo che la distanza dal tavolo di montaggio agli alberi sia la stessa) per non riempire il futuro piano di lavoro più tardi.
Abbiamo scoperto l'asse X.
Fissiamo gli scaffali del portale alla base, per questo ho usato botti per mobili.
Fissare le flange per l'asse Y ai montanti, questa volta dall'esterno:
Inseriamo alberi con cuscinetti lineari.
Ripariamo la parete posteriore dell'asse Z.
Ripetiamo il processo di regolazione del parallelismo degli alberi e fissiamo le flange.
Ripetiamo lo stesso processo con l'asse Z.
Otteniamo un design piuttosto divertente che può essere spostato con una mano lungo tre coordinate.
Un punto importante: tutti gli assi dovrebbero muoversi facilmente, ad es. inclinando leggermente la struttura, il portale stesso dovrebbe muoversi liberamente, senza scricchiolii e resistenze.
Quindi, fissare le viti di comando.
Tagliamo il prigioniero di costruzione M10 della lunghezza richiesta, avvitiamo il dado caprolon approssimativamente al centro e 2 dadi M10 su ciascun lato. È conveniente per questo, dopo aver serrato leggermente i dadi, bloccare il prigioniero nel cacciavite e, tenendo i dadi, serrare.
Inseriamo i cuscinetti nelle prese e spingiamo i prigionieri dall'interno. Successivamente, fissiamo i prigionieri al cuscinetto con dadi su ciascun lato e contrastiamo con il secondo in modo che non si allentino.
Fissiamo il dado caprolon alla base dell'asse.
Fissiamo l'estremità del prigioniero nel cacciavite e proviamo a spostare l'asse dall'inizio alla fine e tornare.
Qui abbiamo un altro paio di gioie che ci aspettano:
1. La distanza dall'asse del dado alla base al centro (e molto probabilmente al momento del montaggio la base sarà al centro) potrebbe non coincidere con la distanza in posizioni estreme, perché gli alberi sotto il peso della struttura possono piegarsi. Ho dovuto mettere il cartone lungo l'asse X.
2. La corsa dell'albero può essere molto stretta. Se hai eliminato tutte le distorsioni, la tensione può avere un ruolo, qui è necessario cogliere il momento di tensione del fissaggio con dadi al cuscinetto installato.
Dopo aver affrontato i problemi e aver ricevuto la rotazione libera dall'inizio alla fine, procediamo all'installazione delle restanti viti.
Attacchiamo i motori passo-passo alle viti:
In generale, quando si utilizzano viti speciali, siano esse trapezoidali o a ricircolo di sfere, su di esse vengono lavorate le estremità e quindi il collegamento al motore viene realizzato molto convenientemente con un apposito giunto.
Ma abbiamo un perno di costruzione e abbiamo dovuto pensare a come risolverlo. In quel momento mi sono imbattuto in un taglio tubo del gas, e l'ha applicato. Si "avvolge" direttamente sulla forcina del motore, entra nella macinazione, l'ha stretto con i morsetti - tiene molto bene.
Per riparare i motori, ho preso un tubo di alluminio e l'ho tagliato. Regolato con rondelle.
Per collegare i motori ho preso i seguenti connettori:
Scusa, non ricordo come si chiamano, spero che qualcuno nei commenti te lo dica.
Connettore GX16-4 (grazie Jager). Ho chiesto a un collega di acquistare in un negozio di elettronica, vive solo nelle vicinanze, ma si è rivelato molto scomodo per me arrivarci. Sono molto contento di loro: li tengono saldamente, sono progettati per una corrente più alta, puoi sempre scollegarli.
Mettiamo il campo di lavoro, è anche un tavolo sacrificale.
Colleghiamo tutti i motori alla scheda di controllo dalla recensione, lo colleghiamo a un alimentatore da 12V, colleghiamo al computer con un cavo LPT.
Installa MACH3 sul PC, effettua le impostazioni e prova!
Per quanto riguarda l'impostazione separatamente, forse, non scriverò. Potrebbe andare avanti per un altro paio di pagine.
Ho tutta una gioia, il video del primo lancio della macchina è stato conservato:
Sì, quando questo video si muoveva lungo l'asse X, c'era un terribile rimbalzo, purtroppo non ricordo esattamente, ma alla fine ho trovato o la rondella penzolante, o qualcos'altro, in generale si è risolto senza problemi.
Successivamente, è necessario posizionare il mandrino, garantendone la perpendicolarità (contemporaneamente in X e Y) al piano di lavoro. L'essenza della procedura è questa, attacciamo una matita al fuso con del nastro isolante, ottenendo così un rientro dall'asse. Con un leggero abbassamento della matita, inizia a disegnare un cerchio sulla lavagna. Se il mandrino è disseminato, non risulta un cerchio, ma un arco. Di conseguenza, è necessario ottenere l'allineamento disegnando un cerchio. Una foto del processo è stata conservata, la matita è sfocata e l'angolazione non è la stessa, ma penso che l'essenza sia chiara:
Troviamo un modello finito (nel mio caso, lo stemma della Federazione Russa), prepariamo la UE, la diamo in pasto al MACH e via!
Funzionamento della macchina:
foto in corso:
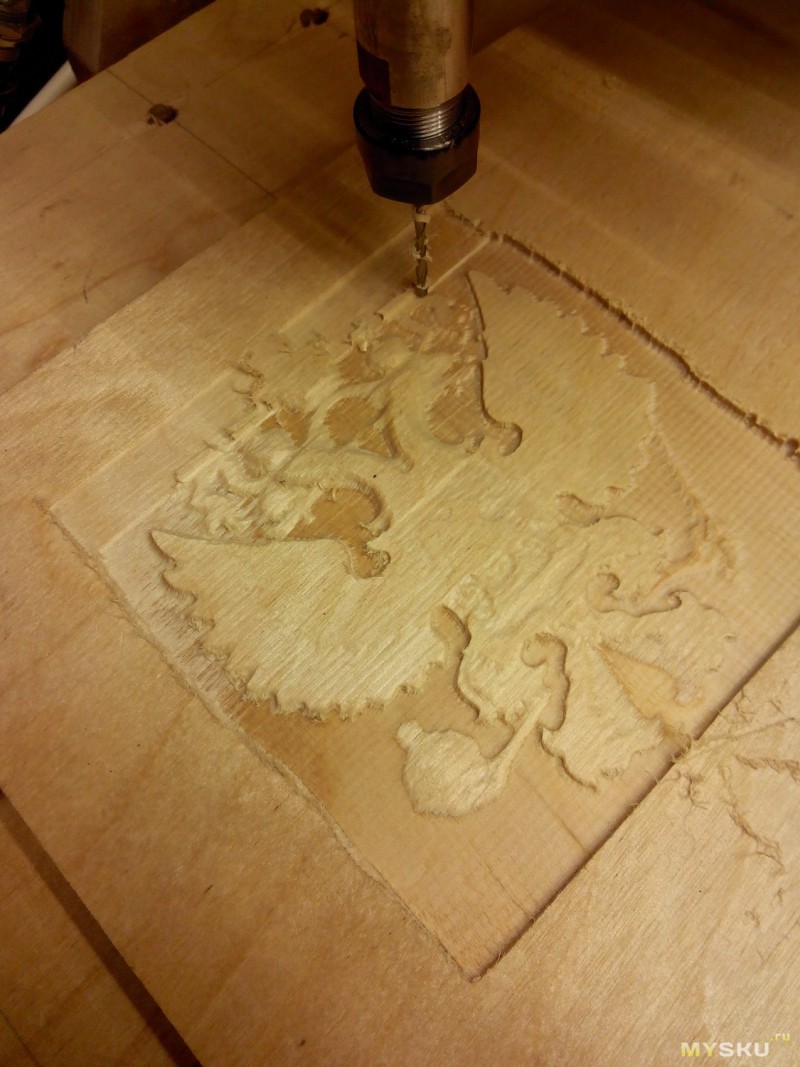
Bene, ovviamente passiamo attraverso l'iniziazione))
La situazione è divertente e generalmente comprensibile. Sogniamo di costruire una macchina e di segare subito qualcosa di super cool, ma alla fine capiamo che questa volta ci vorrà solo molto tempo.
In poche parole:
Con l'elaborazione 2D (semplice segatura) viene impostato un contorno che viene ritagliato in più passaggi.
Con l'elaborazione 3D (qui puoi immergerti in un holivar, alcuni sostengono che questo non è 3D ma 2.5D, poiché il pezzo viene elaborato solo dall'alto), viene impostata una superficie complessa. E maggiore è la precisione del risultato desiderato, più sottile viene utilizzata la taglierina, più passaggi sono necessari per questa taglierina.
Per accelerare il processo, viene utilizzata la sgrossatura. Quelli. prima si campiona il volume principale con una taglierina grande, quindi si inizia la rifinitura con una taglierina sottile.
Successivamente, proviamo, configuriamo, sperimentiamo, ecc. La regola delle 10000 ore funziona anche qui ;)
Forse non ti annoierò più con una storia sulla costruzione, la messa a punto, ecc. È ora di mostrare i risultati dell'utilizzo della macchina: il prodotto.
Come puoi vedere, si tratta principalmente di contorni segati o di elaborazione 2D. Ci vuole molto tempo per elaborare figure tridimensionali, la macchina è in garage e mi fermo lì per un po'.
Qui mi noteranno giustamente - ma su ... per costruire una tale bandura, se riesci a ritagliare una figura con un seghetto alternativo a forma di U o un seghetto alternativo elettrico?
È possibile, ma questo non è il nostro metodo. Come ricorderete, all'inizio del testo, ho scritto che è stata l'idea di fare un disegno su un computer e trasformare questo disegno in un prodotto che è servito da slancio per la creazione di questa bestia.
Scrivere una recensione alla fine mi ha spinto ad aggiornare la macchina. Quelli. l'aggiornamento era stato pianificato in precedenza, ma "le mani non sono arrivate". Ultima modifica prima c'era un'organizzazione di una casa per la macchina:
Così, in garage, quando la macchina è in funzione, è diventata molto più silenziosa e molto meno polvere vola.
L'ultimo aggiornamento è stato l'installazione di un nuovo mandrino, più precisamente, ora ho due basi intercambiabili:
1. Con mandrino cinese da 300 W per un ottimo lavoro:
2. Con una fresa domestica, ma non meno cinese "Enkor" ...
Con il nuovo router sono arrivate nuove possibilità.
Elaborazione più veloce, più polvere.
Ecco il risultato dell'utilizzo di una fresa per scanalature semicircolare:
Bene, soprattutto per MYSKU
Fresa per scanalature diritte semplice:
Video di processo:
Su questo ridurrò, ma secondo le regole bisognerebbe fare un bilancio.
Svantaggi:
- Costoso.
- Per molto tempo.
- Di tanto in tanto devi risolvere nuovi problemi (hanno spento la luce, pickup, qualcosa di sbrogliato, ecc.)
Professionisti:
- Il processo di creazione. Solo questo giustifica già la creazione della macchina. La ricerca di soluzioni ai problemi emergenti e all'attuazione è ciò che, invece di sederti sul sedere, ti alzi e vai a fare qualcosa.
- Gioia nel momento di fare regali fatti con le tue mani. Qui c'è da aggiungere che la macchina non fa tutto il lavoro da sola :) oltre alla fresatura, è comunque necessario lavorarla, carteggiarla, dipingerla, ecc.
Grazie mille se stai ancora leggendo. Spero che il mio post, anche se non vi incita a creare tale (o un'altra) macchina, allarghi i vostri orizzonti e dia spunti di riflessione. Voglio anche ringraziare coloro che mi hanno convinto a scrivere quest'opera, senza di essa non avrei avuto un aggiornamento, a quanto pare, quindi è tutto in nero.
Mi scuso per le imprecisioni nella formulazione e per eventuali digressioni liriche. Molto doveva essere tagliato, altrimenti il testo si sarebbe rivelato semplicemente immenso. Chiarimenti e integrazioni sono naturalmente possibili, scrivi nei commenti - cercherò di rispondere a tutti.
Buona fortuna per il tuo impegno!
Collegamenti ai file promessi:
- disegno a macchina,
- spazzare,
il formato è dxf. Ciò significa che puoi aprire il file con qualsiasi editor vettoriale.
Il modello 3D è dettagliato dell'85-90 percento, ho fatto molte cose, al momento della preparazione della scansione o sul posto. Per favore, capisci e perdona.)
Un router CNC può essere un grande aiuto nella produzione su piccola scala o riparazione a casa. Il costo delle fresatrici CNC di fabbrica (cnc) è piuttosto elevato, quindi alcuni artigiani le creano con successo con le proprie mani secondo disegni unici.
Realizzare una macchina cnc fatta in casa con le proprie mani non è facile, a volte ci vogliono diversi mesi.
Progettazione della macchina
Il modo più semplice per realizzare un telaio per una fresatrice fatta in casa per metallo è da un tubo sezione quadrata 80 x 80 mm, abbastanza basso. L'altezza ridotta rende il dispositivo abbastanza stabile e previene le vibrazioni. Anche il supporto per il fissaggio delle guide è di forma rettangolare tubo di metallo 60 x 20 mm. Il letto è imbullonato, poiché i giunti saldati deformano la struttura. Gli elementi di fissaggio imbullonati consentono di posizionare il dispositivo esattamente sul livello, l'area di contatto è ampia, il fissaggio è affidabile e abbastanza rigido, senza gioco.
Dimensioni dell'area di lavoro macchina fatta in casa deve essere realizzato da 32 x 35 cm La lunghezza degli alberi di guida lungo Y e X è di 1,6 cm, lungo Z - 1 cm.
Le guide sono di profilo migliore, altrimenti si incurveranno lungo l'asse X.
È meglio scegliere cuscinetti a strisciamento industriali, anche se i più economici. Il loro utilizzo ridurrà la probabilità di contraccolpo.
L'asse Z è montato su un ingranaggio a vite, in quanto è piuttosto pesante. Per trasmettere la torsione alla vite di comando dall'asse Z, viene utilizzata una cinghia dentata con una larghezza di 10 mm. Tale schema consente di ridurre il battito e facilitare il posizionamento del motore passo-passo rispetto alla vite di traslazione. Riduce il peso della macchina e consente di risparmiare spazio verticale.
L'asse stesso è costituito da una piastra di alluminio e dietro di esso sono installati due motori passo-passo. Il loro scopo è trasferire la torsione alla vite dell'asse Z per mezzo di una cinghia dentata, un altro motore trasmette il movimento lungo l'asse X con una cinghia. La vite di comando dell'asse Z può essere ricavata da un perno di costruzione.
Se invece di una cinghia viene realizzato un ingranaggio a vite nel disegno, la velocità aumenterà a 850 giri/min e la precisione di una macchina cnc fatta in casa. Ma questo design è molto più costoso.
Se prevedi di raffreddare ad acqua il mandrino, dovresti anche fornire una pompa dell'acqua e un set di tubi di gomma.
Motore e software
Per una fresatrice CNC fatta in casa (chiamata anche cnc), è adatto un motore passo-passo con una coppia di 18 kg / cm. Un tale motore è sufficiente per un mandrino con una potenza di 1,5 kilowatt. Risulterà elaborare parti in metalli teneri e lavori semplici su acciaio al carbonio.
Il controller, il convettore di frequenza e la scheda madre possono essere installati in un'unica scatola protettiva. Sebbene molti abbiano paura delle interferenze, sono piuttosto rari. Un tale centro di controllo è soggetto a surriscaldamento quando fa caldo!
Le fresatrici CNC, assemblate a mano secondo disegni, lavorano sotto la guida di Linux. Alcuni driver dovranno essere scritti a mano, ad esempio per un motore passo-passo con microstepping. I controller con uscita USB non funzionano sotto Linux, questo dovrebbe essere preso in considerazione quando li si sceglie. È necessario acquistare un controller a quattro assi ed effettuare le impostazioni appropriate.
Set pronto per il montaggio della macchina
La maggior parte degli artigiani che assemblano la macchina con le proprie mani si trovano ad affrontare la necessità di acquistare molte parti finite. Di conseguenza, il prezzo dispositivo fatto in casa potrebbe essere superiore a quello di fabbrica. Processi autoassemblaggio molto lungo, e il risultato è spesso deludente. Spesso gli artigiani rifanno più volte macchine assemblate senza disegni e calcoli, portando il loro lavoro allo standard desiderato.
È possibile realizzare un router CNC con le proprie mani usando una chiave inglese e un cacciavite in un giorno lavorativo, utilizzando un kit già pronto, una sorta di semplice costruttore per adulti, contenente assolutamente tutti i dettagli e i disegni. Il set è una garanzia Alta qualità macchina futura.
Il dispositivo e il test di una fresa fatta in casa:
17
Una guida alla creazione di una fresatrice CNC. Capitolo 1 Elettronica della macchina
Buongiorno a tutti! Ed eccomi qui con una nuova parte della mia storia su CNC - macchina utensile. Quando ho iniziato a scrivere l'articolo, non pensavo nemmeno che si sarebbe rivelato così voluminoso. Quando ho scritto dell'elettronica della macchina, ho guardato e mi sono spaventato: il foglio A4 era scritto su entrambi i lati e c'era ancora molto da raccontare.
Alla fine è andata così manuale per la creazione di una macchina CNC, macchina funzionante, da zero. Ci saranno tre parti dell'articolo su una macchina: 1-riempimento elettronico, 2-meccanica della macchina, 3-tutti i dettagli della configurazione dell'elettronica, della macchina stessa e del programma di controllo della macchina.
In generale, cercherò di combinare in un unico materiale tutto ciò che è utile e necessario per ogni principiante in questo interessante business, ciò che io stesso ho letto su varie risorse Internet e sono passato attraverso me stesso. A proposito, in quell'articolo mi sono dimenticato di mostrare le foto dei mestieri realizzati. Sto aggiustando questo. Orso di polistirolo e pianta di compensato.
Prefazione
Dopo aver assemblato la mia piccola macchina senza un dispendio significativo di sforzi, tempo e denaro, ero seriamente interessato a questo argomento. Ho guardato su YouTube, se non tutti, quindi quasi tutti i video relativi alle macchine amatoriali. Particolarmente impressionanti sono state le fotografie dei prodotti che le persone realizzano sui loro “ CNC di casa". Ho guardato e deciso: assemblerò la mia grande macchina! Quindi, su un'ondata di emozioni, non ci ho pensato bene, mi sono tuffato in un mondo nuovo e sconosciuto per me stesso CNC.Non sapevo da dove cominciare. Prima di tutto, ho ordinato un normale motore passo-passo Vexta 12 kg/cm, tra l'altro con l'orgogliosa scritta "made in Japan".
Mentre guidava per tutta la Russia, la sera si sedeva in vari forum CNC e cercava di fare una scelta Controllore STEP/DIR e driver per motori passo-passo. Ho considerato tre opzioni: su un microcircuito L298, sui lavoratori sul campo o acquista il cinese già pronto TB6560 su cui c'erano recensioni molto contrastanti.
Per alcuni ha funzionato a lungo senza problemi, per altri si è bruciato al minimo errore dell'utente. Qualcuno ha persino scritto che si è bruciato quando ha girato leggermente l'albero del motore collegato in quel momento al controller. Probabilmente il fatto dell'inaffidabilità dei cinesi ha giocato a favore della scelta di uno schema L297+ discusso attivamente sul forum. Lo schema è probabilmente davvero immortale. i driver di campo del driver per ampere sono molte volte superiori a quelli che devono essere alimentati ai motori. Anche se hai bisogno di saldarti (questo è solo un vantaggio), e il costo delle parti è uscito un po 'più del controller cinese, ma è affidabile, il che è più importante.
Divago un po' dall'argomento. Quando tutto questo è stato fatto, non ho nemmeno pensato che un giorno ne avrei scritto. Pertanto, non ci sono foto del processo di assemblaggio di meccanica ed elettronica, solo alcune foto scattate con la fotocamera di un cellulare. Tutto il resto l'ho cliccato apposta per l'articolo, già assemblato.
Il caso del saldatore ha paura
Comincio dall'alimentatore. Avevo programmato di dare un impulso, ci ho giocherellato probabilmente per una settimana, ma non sono riuscito a sconfiggere l'eccitazione, che veniva dal nulla. Avvolgo la trance a 12v - tutto è a posto, lo avvolgo a 30 - un pasticcio completo. Sono giunto alla conclusione che una specie di stronzata sale sul feedback da 30v a TL494 e abbattere la sua torre. Quindi ho abbandonato questo impulso, poiché c'erano diversi TS-180, uno dei quali è andato a servire la madrepatria come trance di potere. E qualunque cosa tu dica, un pezzo di ferro e rame sarà più affidabile di un mucchio di sgretolamento. Il trasformatore si riavvolge alle tensioni richieste, ma occorreva + 30V per alimentare i motori, + 15V per alimentare IR2104, +5v acceso L297, e un fan. Puoi applicare 10 o 70 ai motori, l'importante è non superare la corrente, ma se fai di meno la velocità massima e la potenza diminuiscono, ma il trasformatore non lo permetteva più. Avevo bisogno di 6-7A. Tensioni stabilizzate 5 e 15v, lasciate 30 “flottanti” a discrezione della nostra rete elettrica.Per tutto questo tempo, ogni notte mi sono seduto al computer e ho letto, letto, letto. Impostare il controller, scegliere i programmi: quale disegnare, quale azionare la macchina, come fare la meccanica, ecc. eccetera. In generale, più leggevo, più diventava terribile e sempre più spesso sorgeva la domanda "perché ne ho bisogno?!". Ma era troppo tardi per ritirarsi, il motore era sul tavolo, i dettagli erano da qualche parte lungo la strada - dobbiamo continuare.
È ora di saldare la scheda. Disponibile su Internet non mi andava bene per tre motivi:
1 - Il negozio che ha ordinato i pezzi non c'era IR2104 nei pacchetti DIP e mi hanno inviato 8-SOICN. Sono saldati alla scheda sull'altro lato, capovolti, e di conseguenza è stato necessario rispecchiare le tracce e loro ( IR2104) 12 pezzi.
2 - Anche i resistori ei condensatori vengono inseriti in pacchetti SMD per ridurre il numero di fori da praticare.
3 - Il radiatore che avevo era più piccolo ei transistor estremi erano fuori dalla sua zona. Era necessario spostare i lavoratori sul campo su una tavola a destra e sull'altra a sinistra, quindi ho realizzato due tipi di tavola.
Schema del controllore della macchina
Per la sicurezza della porta LPT, il controller e il computer sono collegati tramite una scheda fotoaccoppiatore. Ho preso lo schema e il sigillo da un noto sito, ma ancora una volta ho dovuto rifarlo un po' per me stesso e rimuovere i dettagli non necessari.
Un lato della scheda è alimentato tramite la porta USB, l'altro, collegato al controller, è alimentato da una sorgente +5V. I segnali vengono trasmessi tramite fotoaccoppiatori. Scriverò tutti i dettagli sulla configurazione del controller e sul disaccoppiamento nel terzo capitolo, ma qui menzionerò solo i punti principali. Questa scheda di disaccoppiamento è progettata per il collegamento sicuro del controller del motore passo-passo alla porta LPT del computer. Isola completamente elettricamente la porta del computer dall'elettronica della macchina e consente di controllare una macchina CNC a 4 assi. Se la macchina ha solo tre assi, come nel nostro caso, le parti non necessarie possono essere lasciate sospese in aria o non saldate affatto. È possibile collegare sensori di fine corsa, un pulsante di arresto forzato, un relè di abilitazione mandrino e un altro dispositivo, come un aspirapolvere.
Era una foto della scheda dell'accoppiatore ottico presa da Internet, ed è così che appare il mio giardino dopo l'installazione nella custodia. Due assi e un mucchio di fili. Ma sembra che non ci siano interferenze e tutto funziona senza errori.
La prima scheda controller è pronta, ho controllato tutto e testato passo dopo passo, come nelle istruzioni. Ho impostato una piccola corrente come trimmer (questo è possibile grazie alla presenza del PWM) e ho collegato l'alimentazione (motori) tramite una catena di lampadine 12 + 24v in modo che fosse "niente se niente". Ho lavoratori sul campo senza radiatore.
Il motore sibilò. Buone notizie, quindi PWM funziona come dovrebbe. Premo un tasto e gira! Ho dimenticato di dire che questo controller è progettato per controllare un motore passo-passo bipolare, ad es. uno a 4 fili. Giocato con modalità passo / mezzo passo, corrente. In modalità mezzo passo, il motore si comporta in modo più stabile e sviluppa velocità elevate + aumenti di precisione. Quindi ho lasciato il ponticello nel "mezzo passo". Con la massima corrente di sicurezza per il motore a una tensione di circa 30 V, si è scoperto che faceva girare il motore fino a 2500 giri / min! La mia prima macchina senza PWM non ha mai sognato una cosa del genere.))
I successivi due motori ordinati più potenti, Nema a 18kg/s, ma già “made in China”.
Sono di qualità inferiore Vexta Dopotutto, Cina e Giappone sono due cose diverse. Quando si ruota l'asta con la mano, i giapponesi lo fanno in qualche modo dolcemente, ma i cinesi hanno una sensazione diversa, ma finora questo non ha influito sul lavoro. Non ci sono commenti per loro.
Ho saldato le restanti due schede, controllato tramite il "simulatore di motori passo-passo a LED", tutto sembra andare bene. Collego un motore - funziona bene, ma non a 2500 giri/min, ma a circa 3000! Secondo lo schema già elaborato, collego il terzo motore alla terza scheda, giro per un paio di secondi e mi alzo ... Guardo l'oscilloscopio: non ci sono impulsi su un'uscita. Chiamo il canone - uno di IR2104 trafitto.
Beh, forse ne ho uno difettoso, ho letto che succede spesso con questo mikruha. Ne saldo uno nuovo (ho preso 2 pezzi con un margine), la stessa sciocchezza: si FERMA per un paio di secondi! Qui mi sono sforzato e controlliamo i lavoratori sul campo. A proposito, la mia tavola ce l'ha IRF530(100V / 17A) vs. (50V / 49A), come nell'originale. Al motore andranno al massimo 3A, quindi un'alimentazione da 14A sarà più che sufficiente, ma la differenza di prezzo è quasi 2 volte a favore dei 530.
Quindi, controllo i lavoratori sul campo e quello che vedo ... non ho saldato una gamba! E tutti i 30 V del lavoratore sul campo sono volati all'uscita di questo "irka". Ho saldato la gamba, esaminato di nuovo tutto attentamente, ne ho messo un altro IR2104, anch'io sono preoccupato - questo è l'ultimo. L'ho acceso ed ero molto contento quando il motore non si è spento dopo due secondi di funzionamento. Modalità lasciate come segue: motore Vexta- 1,5 A, motore NEMA 2.5A. Con questa corrente si raggiungono circa 2000 giri, ma è meglio limitarli programmaticamente per evitare di saltare passi, e la temperatura dei motori a lungo lavoro non supera la cassaforte per motori. Il trasformatore di alimentazione funziona senza problemi, perché di solito solo 2 motori girano contemporaneamente, ma è auspicabile un raffreddamento ad aria aggiuntivo per il radiatore.
Ora sull'installazione di operatori sul campo sul radiatore, e ce ne sono 24, se qualcuno non se ne è accorto. In questa versione della tavola, si trovano sdraiati, ad es. il radiatore si adagia su di loro ed è attratto da qualcosa.
Certo, è desiderabile mettere un solido pezzo di mica per isolare il dissipatore di calore dai transistor, ma non ne avevo uno. Ho trovato una via d'uscita. Perché in metà dei transistor il case va a più potenza, possono essere montati senza isolamento, solo su pasta termica. E sotto il resto, ho messo pezzi di mica lasciati dai transistor sovietici. Ho perforato il radiatore e la scheda in tre punti in tutto e per tutto e l'ho serrato con i bulloni. Ho ottenuto una scheda grande saldando tre schede separate lungo i bordi, mentre ho saldato un filo di rame da 1 mm attorno al perimetro per maggiore resistenza. Ho posizionato tutta l'imbottitura elettronica e l'alimentatore su una specie di telaio di ferro, non so nemmeno perché.
Ho ritagliato la copertura laterale e superiore dal compensato e ci ho messo un ventaglio sopra.
Ho praticato dei fori nel pannello frontale per numerosi LED per indicare le modalità di funzionamento.
Per collegare/scollegare velocemente motori e centralina ho utilizzato connettori dell'ultimo millennio. E buon contatto corrente desiderata conservare senza alcuna conseguenza per se stessi.