Hemlagad cnc maskinritning. Hur man gör en hemmagjord cnc-router för metall
Att göra en tredimensionell ritning på träyta fabriks CNC-fräsmaskiner för trä används. Det är svårt att göra en liknande minimodell med egna händer hemma, men det är möjligt med en detaljerad studie av designen. För att göra detta måste du förstå detaljerna, välja rätt komponenter och konfigurera dem.
Funktionsprincipen för fräsmaskinen
Modern träbearbetningsutrustning med ett numeriskt block programstyrning designad för att bilda ett komplext mönster på trä. Konstruktionen ska innehålla en mekanisk elektronisk del. I kombination kommer de att automatisera arbetsprocessen så mycket som möjligt.
För att göra ett skrivbord på trä med dina egna händer, bör du bekanta dig med huvudkomponenterna. Skärelementet är en skärare, som är installerad i en spindel placerad på motoraxeln. Denna design är fäst vid sängen. Den kan röra sig längs två koordinataxlar - x; y. För att fixa arbetsstycket är det nödvändigt att göra ett stödbord.
Den elektroniska styrenheten är ansluten till stegmotorerna. De ger förskjutning av vagnen i förhållande till delen. Med denna teknik kan du göra 3D-ritningar på en träyta.
Driftsekvensen för miniutrustning med CNC, som du kan göra själv.
- Att skriva ett program enligt vilket sekvensen av rörelser för skärdelen kommer att utföras. För att göra detta är det bäst att använda speciella mjukvarusystem utformade för anpassning i hemgjorda modeller.
- Ställa arbetsstycket på bordet.
- Programutgång till CNC.
- Slå på utrustning, övervaka implementeringen av automatiska åtgärder.
För att uppnå maximal automatisering av arbetet i 3D-läge måste du rita ett diagram korrekt och välja lämpliga komponenter. Experter rekommenderar att man studerar fabriksmodeller innan man gör en mini- fräsmaskin med dina egna händer.
För att skapa komplexa mönster och mönster på en träyta behöver du flera typer av fräsar. Vissa av dem kan du göra själv, men för fint arbete bör du köpa fabriks.
Schema för en hemmagjord fräsmaskin med numerisk kontroll
Det svåraste steget är valet av det optimala tillverkningsschemat. Det beror på arbetsstyckets dimensioner och graden av dess bearbetning. För hemmabruk det är tillrådligt att göra ett gör-det-själv-skrivbord, som kommer att ha det optimala antalet funktioner.
Det bästa alternativetär tillverkning av två vagnar som kommer att röra sig längs x-koordinataxlarna; y. Det är bäst att använda slipade stålstänger som bas. Vagnar kommer att monteras på dem. För att skapa en transmission behövs stegmotorer och skruvar med rullningslager.
För maximal automatisering av processen vid konstruktionen av en gör-det-själv mini CNC träfräsmaskin är det nödvändigt att tänka över den elektroniska delen i detalj. Konventionellt består den av följande komponenter:
- kraftenhet. Det är nödvändigt att tillföra elektricitet till stegmotorer och styrkrets. Använd ofta modellen 12v 3A;
- kontroller. Den är utformad för att ge kommandon till elmotorer. För driften av en gör-det-själv mini CNC-fräsmaskin räcker det med en enkel krets för att styra funktionen hos tre motorer;
- förare. Det är också ett element av reglering av driften av den rörliga delen av strukturen.
Fördelen med detta komplex är möjligheten att importera körbara filer av de vanligaste formaten. Med hjälp av en speciell applikation kan du skapa en tredimensionell ritning av delen för preliminär analys. Stegmotorer kommer att köras med en viss slaghastighet. Men för detta måste du göra tekniska specifikationer till kontrollprogrammet.
Val av tillbehör till CNC-fräsmaskin
Nästa steg är att välja komponenter för montering av hemgjord utrustning. Det bästa alternativet är att använda improviserade medel. Som grund för skrivbordsmodeller av en 3D-maskin kan du använda trä, aluminium eller plexiglas.
För korrekt funktion av hela komplexet är det nödvändigt att utveckla utformningen av bromsok. Under deras rörelse bör det inte finnas några vibrationer, detta kan leda till felaktig fräsning. Därför, före montering, kontrolleras alla komponenter för kompatibilitet med varandra.
- guider. Polerade stålstänger med en diameter på 12 mm används. Längden för x-axeln är 200 mm, för y-axeln är den 90 mm;
- bromsok. Textolite är det bästa alternativet. Den vanliga storleken på plattformen är 25*100*45 mm;
- stegmotorer. Experter rekommenderar att du använder modeller från en 24v, 5A skrivare. Till skillnad från diskenheter har de mer kraft;
- kutterblock. Den kan också tillverkas av textolit. Konfigurationen beror direkt på det tillgängliga verktyget.
Strömförsörjningen monteras bäst från fabrik. På egentillverkning fel är möjliga, som sedan påverkar driften av all utrustning.
Proceduren för att tillverka en CNC-fräsmaskin
Efter att ha valt alla komponenter kan du göra en stationär mini CNC trärouter själv med dina egna händer. Alla element kontrolleras preliminärt igen, deras dimensioner och kvalitet kontrolleras.
För att fixera elementen i utrustningen är det nödvändigt att använda speciella fästelement. Deras konfiguration och form beror på det valda schemat.
Proceduren för att montera stationär mini CNC-utrustning för trä med en 3D-bearbetningsfunktion.
- Installation av bromsokstyrningar, deras fixering på strukturens sidodelar. Dessa block är inte installerade på basen än.
- Lappning av bromsok. De måste flyttas längs styrningarna tills en smidig gång erhålls.
- Dra åt bultarna för att fixera bromsoken.
- Fästa komponenter till basen av utrustningen.
- Montering av ledarskruvar tillsammans med kopplingar.
- Installation av drivmotorer. De är fästa på kopplingsskruvarna.
Den elektroniska delen är placerad i ett separat block. Detta hjälper till att minska sannolikheten för felfunktion under driften av routern. Också viktig poängär valet av arbetsyta för installation av utrustning. Det måste vara plant, eftersom nivåjusteringsbultarna inte ingår i designen.
Ett villkor för utförandet av professionell träbearbetning är närvaron av en CNC-fräsmaskin. Kommersiellt tillgängliga vägar och inte alla har råd. Därför gör många dem med sina egna händer, sparar pengar och njuter av den kreativa processen.
Det finns två alternativ för tillverkning av minimaskiner för fräsning av trä:
- köp av en uppsättning delar och dess tillverkning (Modelist-kit som kostar från 40 till 110 tusen rubel);
- gör det med dina egna händer.
Överväg tillverkningen av mini CNC-fräsmaskiner med dina egna händer.
Val av designfunktioner
Listan över åtgärder vid utveckling, tillverkning av en minienhet för träfräsning är som följer:
- Inledningsvis måste du bestämma vilken typ av arbete vi pratar om. Detta kommer att berätta vilka dimensioner och tjocklekar av delar som kan bearbetas på den.
- Gör layouten och den föreslagna listan över delar för en hemmagjord skrivbordsmaskin för DIY-tillverkning.
- Välj programvara genom att ta in den fungerande skick så att det fungerar enligt det givna programmet.
- Köp nödvändiga komponenter, delar, produkter.
- Med ritningar, gör de saknade elementen med dina egna händer, montera och felsöka den färdiga produkten.
Design
En hemmagjord maskin består av följande huvuddelar:
- säng med ett bord placerat på den;
- bromsok med förmågan att flytta skäret i tre koordinater;
- spindel med fräs;
- guider för att flytta bromsok och portal;
- en strömförsörjningsenhet som tillhandahåller elektricitet till motorerna, en styrenhet eller ett kopplingskort med hjälp av mikrokretsar;
- förare för att stabilisera arbetet;
- sågspån dammsugare.
Styrningar är installerade på ramen för att flytta portalen längs Y-axeln. Styrningar placeras på portalen för att flytta bromsoket längs X-axeln. Spindeln med fräsen är monterad på bromsoket. Den rör sig längs sina guider (Z-axeln).
Styrenheten och drivrutinerna tillhandahåller automatisering av CNC-maskinen genom att överföra kommandon till elmotorerna. Genom att använda Kcams mjukvarupaket kan du använda vilken styrenhet som helst och ger motorstyrning i enlighet med delritningen som lagts in i programmet.
Konstruktionen måste göras styv för att motstå de arbetskrafter som uppstår under drift och inte leda till vibrationer. Vibrationer kommer att leda till en minskning av kvaliteten på den resulterande produkten, verktygsbrott. Därför måste fästelementens dimensioner säkerställa strukturens soliditet.
En hemmagjord CNC-fräsmaskin används för att få en tredimensionell 3D-bild på trädetalj. Den är fixerad på bordet denna apparat. Den kan även användas som gravör. Konstruktionen säkerställer rörelsen av arbetskroppen - spindeln med skäraren installerad i enlighet med det specificerade handlingsprogrammet. Bromsokets rörelse längs X- och Y-axlarna sker längs polerade styrningar med hjälp av stegmotorer.
Genom att flytta spindeln längs den vertikala Z-axeln kan du ändra bearbetningsdjupet på den skapade ritningen på trädet. För att få en 3D-reliefritning måste du göra ritningar. Det är tillrådligt att använda olika sorter fräsar som gör att du kan få bästa alternativen bildvisning.
Urval av komponenter
För styrningar används stålstänger D = 12 mm. För bättre rörelse av vagnarna är de slipade. Deras längd beror på storleken på bordet. Du kan använda härdade stålstänger från en matrisskrivare.
Stegmotorer kan användas därifrån. Deras parametrar: 24 V, 5 A.
Det är önskvärt att tillhandahålla fixering av skärare med en spännhylsa.
Det är bättre att använda en fabrikstillverkad strömförsörjning för en hemmagjord minifräsmaskin, eftersom prestanda beror på det.
Regulatorn behöver använda kondensatorer och motstånd i SMD-paket för ytmontering.
hopsättning
För att montera en hemmagjord maskin för fräsning av 3D trädelar med dina egna händer måste du göra ritningar, förbereda viktigt verktyg, tillbehör, gör de saknade delarna. Efter det kan du börja montera.
Gör-det-själv-monteringssekvensen för en mini CNC-maskin med 3D-bearbetning består av:
- bromsokstyrningar installeras i sidoväggarna tillsammans med vagnen (utan skruvar).
- vagnarna flyttas längs styrningarna tills deras rörelse blir jämn. Således är hålen i bromsoket överlappade.
- åtdragningsbultar på bromsok.
- fixering av monteringsenheter på maskinen och montering av skruvar.
- installation av stegmotorer och deras anslutning med skruvar med hjälp av kopplingar.
- regulatorn är tilldelad i ett separat block för att minska påverkan av manövermekanismer på den.
En hemmagjord CNC-maskin efter montering måste testas! Testning av 3D-bearbetning utförs genom att använda sparlägen för att identifiera alla problem och åtgärda dem.
Drift i automatiskt läge tillhandahålls av programvara. Avancerade datoranvändare kan använda nätaggregat och drivrutiner för styrenheter, stegmotorer. Strömförsörjningen omvandlar den inkommande AC (220 V, 50 Hz) till D.C. behövs för att driva styrenheten och stegmotorerna. För dem går maskinstyrning från en persondator genom LPT-porten. Arbetsprogram är Turbo CNC och VRI-CNC. CorelDRAW- och ArtCAM-grafikredigeringsprogram används för att förbereda de ritningar som krävs för implementering i ett träd.
Resultat
Hemmagjord mini CNC-fräsmaskin för 3D-delar är lätt att använda, säkerställer noggrannhet och kvalitet på bearbetningen. Om du behöver göra mer komplext arbete måste du använda stegmotorer med större effekt (till exempel: 57BYGH-401A). I det här fallet, för att flytta bromsoken, måste du använda kuggremmar för att rotera skruvarna, och inte en koppling.
Installationen av strömförsörjningen (S-250-24), växelkort, drivrutiner kan göras i det gamla fallet från datorn, modifiera det. Den kan förses med en röd "stopp"-knapp för nödavstängning av utrustning.
Om du hittar ett fel, markera en text och klicka Ctrl+Enter.
Ett set med vilket du kan montera din CNC-fräs.
Färdiga verktygsmaskiner säljs i Kina, en recension av en av dem har redan publicerats på Muska. Vi monterar själva maskinen. Välkommen…
UPD: fillänkar
Jag kommer ändå att ge en länk till en recension av den färdiga maskinen från AndyBig. Jag kommer inte att upprepa mig, jag kommer inte att citera hans text, vi kommer att skriva allt från grunden. Titeln listar bara en uppsättning med motorer och en drivrutin, det kommer fler delar, jag ska försöka ge länkar till allt.
Och det här ... jag ber om ursäkt på förhand till läsarna, jag tog inte specifikt bilder under processen, eftersom. i det ögonblicket tänkte jag inte göra en recension, men jag kommer att ta upp maximalt med bilder av processen och försöka ge detaljerad beskrivning alla noder.
Syftet med recensionen är inte så mycket att skryta som att visa möjligheten att göra en assistent åt dig själv. Jag hoppas att denna recension kommer att ge någon en idé, och det är möjligt att inte bara upprepa, utan också göra det ännu bättre. Gå…
Hur idén föddes:
Det blev så att jag har förknippats med teckningar länge. De där. min yrkesverksamhet nära förknippad med dem. Men det är en sak när man gör en ritning, och då väcker helt andra människor designobjektet till liv, och det är en helt annan när man själv ger liv till designobjektet. Och om jag tycks klara mig bra med att bygga saker, så med modellering och annan brukskonst, inte riktigt.
Så länge fanns det en dröm från en bild ritad i AutoCAD, att göra en smäll - och den är in natura framför dig, du kan använda den. Denna idé halkade då och då, men kunde inte ta form i något konkret, förrän ...
Tills jag såg REP-RAP för tre eller fyra år sedan. Tja, 3D-skrivaren var en mycket intressant sak, och idén att sätta ihop mig själv tog lång tid att ta form, jag samlade information om olika modeller om för- och nackdelar olika alternativ. Vid ett tillfälle, genom att klicka på en av länkarna, kom jag till ett forum där folk satt och diskuterade inte 3D-skrivare, utan CNC-fräsmaskiner. Och härifrån kanske hobbyn börjar sin resa.
Istället för teori
I ett nötskal om CNC-fräsmaskiner (jag skriver med mina egna ord avsiktligt, utan att kopiera artiklar, läroböcker och manualer).
En fräsmaskin fungerar precis motsatsen till en 3D-skrivare. I skrivaren, steg för steg, lager för lager, byggs modellen upp genom att smälta polymerer, i en fräsmaskin, med hjälp av en fräs, avlägsnas "allt överflödigt" från arbetsstycket och den önskade modellen erhålls.
För att använda en sådan maskin behöver du det nödvändiga minimumet.
1. Bas (kropp) med linjära styrningar och transmissionsmekanism (kan vara skruv eller rem)
2. Spindel (jag ser att någon log, men det är vad den heter) - själva motorn med en spännhylsa i vilken ett arbetsverktyg är installerat - en fräs.
3. Stegmotorer - motorer som tillåter kontrollerade vinkelrörelser.
4. Styrenhet - ett styrkort som överför spänning till motorerna i enlighet med de signaler som tas emot från styrprogrammet.
5. Dator med installerat kontrollprogram.
6. Grundläggande ritfärdigheter, tålamod, lust och gott humör.))
Punkterna:
1. Bas.
genom konfiguration:
Jag kommer att dela upp i 2 typer, det finns mer exotiska alternativ, men de två huvudsakliga:
Med flyttbar portal:
Egentligen, designen jag har valt, har den en bas på vilken guider är fixerade längs X-axeln. En portal rör sig längs X-axelguiderna, på vilka Y-axelguiderna är placerade, och Z-axelnoden rör sig längs Det.
Med statisk portal
Denna design representerar också sig själv som en kropp, som också är en portal på vilken Y-axelguiderna är placerade, och Z-axelnoden rör sig längs den, och X-axeln rör sig redan i förhållande till portalen.
Efter material:
kroppen kan göras av olika material, den vanligaste:
- duralumin - har ett bra förhållande mellan massa, styvhet, men priset (bara för en hemmagjord hobbyprodukt) är fortfarande deprimerande, men om det finns synpunkter på maskinen för att tjäna seriösa pengar, så finns det inga alternativ.
- plywood - bra styvhet med tillräcklig tjocklek, låg vikt, förmågan att bearbeta med vad som helst :), och själva priset, ett ark av plywood 17 är nu ganska billigt.
- stål - används ofta på maskiner med stor bearbetningsyta. En sådan maskin måste naturligtvis vara statisk (inte mobil) och tung.
- MFD, plexiglas och monolitiskt polykarbonat, även spånskiva - såg också sådana alternativ.
Som du kan se är själva maskinens design väldigt lik både en 3D-skrivare och lasergravörer.
Jag skriver medvetet inte om designen av 4-, 5- och 6-axliga fräsmaskiner, eftersom. på agendan står en hemmagjord hobbymaskin.
2. Spindel.
Egentligen kommer spindlar med luft- och vattenkylning.
Luftkylda är billigare i slutändan, eftersom. för dem är det inte nödvändigt att blockera en extra vattenkrets, de fungerar lite högre än vatten. Kylning tillhandahålls av en baksidan ett pumphjul, som vid höga varvtal skapar ett påtagligt luftflöde som kyler motorhuset. Ju mer kraftfull motor, desto allvarligare kylning och desto större luftflöde, som mycket väl kan blåsa upp i alla riktningar
damm (spån, sågspån) av arbetsstycket.
Vattenkyld. En sådan spindel fungerar nästan tyst, men i slutändan kan skillnaden mellan dem i arbetet inte höras, eftersom ljudet från materialet som bearbetas av skäraren kommer att blockera det. Det finns inget drag från pumphjulet, i det här fallet förstås, men det finns en extra hydraulkrets. I en sådan krets måste det finnas rörledningar, en pump för att pumpa vätska, samt en plats för kylning (radiator med luftflöde). Vanligtvis hälls inte vatten i denna krets, utan antingen TOSOL eller etylenglykol.
Det finns också spindlar med olika kapacitet, och om lågeffekts sådana kan anslutas direkt till styrkortet, måste motorer med en effekt på 1 kW eller mer kopplas via styrenheten, men det handlar inte om oss.))
Ja, ofta i hemmagjorda maskiner installerar de direktslipmaskiner eller fräsar med en avtagbar bas. Ett sådant beslut kan motiveras, särskilt när man utför arbete av kort varaktighet.
I mitt fall valdes en 300W luftkyld spindel.
3. Stegmotorer.
De mest använda motorerna är 3 storlekar
NEMA17, NEMA23, NEMA 32
de skiljer sig åt i storlek, kraft och arbetsmoment
NEMA17 används vanligtvis i 3D-skrivare, de är för små för en fräsmaskin, eftersom. du måste bära en tung portal, på vilken en sidobelastning dessutom appliceras under bearbetningen.
NEMA32 för ett sådant farkost är onödigt, dessutom skulle du behöva ta ett annat styrkort.
mitt val föll på NEMA23 med en maximal effekt för detta kort - 3A.
Även människor använder steppers från skrivare, men sedan. Jag hade dem inte heller och var fortfarande tvungen att köpa, jag valde allt i satsen.
4. Styrenhet
Ett styrkort som tar emot signaler från datorn och överför spänning till stegmotorer som förflyttar maskinens axlar.
5. Dator
Du behöver en separat dator (möjligen mycket gammal) och det finns kanske två anledningar till detta:
1. Det är osannolikt att du bestämmer dig för att placera en fräs i närheten av den plats där du är van att läsa internet, leka leksaker, hålla konton osv. Helt enkelt för att fräsen är högljudd och dammig. Vanligtvis står maskinen antingen i verkstaden eller i garaget (bättre uppvärmd). Min maskin står i garaget, den går mest på tomgång på vintern, pga. ingen uppvärmning.
2. Av ekonomiska skäl brukar man använda datorer som inte längre är relevanta för hemlivet - hårt använda :)
Krav på bilen i stort sett ingenting:
- från Pentium 4
- förekomsten av ett diskret grafikkort
- RAM från 512MB
- närvaron av en LPT-kontakt (jag kommer inte att säga något om USB, jag har inte studerat nyheterna ännu på grund av drivrutinen som fungerar på LPT)
en sådan dator tas antingen ur skafferiet, eller, som i mitt fall, köps den för nästan ingenting.
På grund av maskinens låga effekt försöker vi att inte installera ytterligare programvara, dvs. endast axel och kontrollprogram.
Nästa är två alternativ:
- installera Windows XP (det är en svag dator, minns du väl?) och kontrollprogrammet MATCH3 (det finns andra, men det här är det mest populära)
- vi lägger niks och Linux CNC (de säger att allt också är väldigt bra, men jag behärskade inte niks)
Jag kommer kanske att tillägga, för att inte förolämpa alltför rika människor, att det är fullt möjligt att sätta inte en fjärde stubbe, utan någon form av ai7 - snälla, om du gillar det och har råd.
6. Grundläggande ritfärdigheter, tålamod, lust och gott humör.
Här i ett nötskal.
För att manövrera maskinen behöver du ett kontrollprogram (i huvudsak en textfil som innehåller koordinaterna för rörelser, rörelsehastighet och acceleration), som i sin tur är förberedd i en CAM-applikation - vanligtvis ArtCam, i denna applikation är själva modellen förberedd, dess mått ställs in och ett skärverktyg väljs.
Jag brukar ta en lite längre väg, göra en ritning och sedan AutoCad, spara den *.dxf, ladda upp den till ArtCam och förbereda UE där.
Nåväl, låt oss börja processen att skapa din egen.
Innan vi designar en maskin tar vi utgångspunkt i flera punkter:
- Axelaxlar kommer att tillverkas av konstruktionsbultar med M10-gänga. Naturligtvis finns det utan tvekan fler tekniska alternativ: en axel med trapetsgänga, en kulskruv (kulskruv), men du måste förstå att priset på frågan lämnar mycket att önska, och för en hobbymaskin, priset är i allmänhet utrymme. Men med tiden ska jag uppgradera och byta ut hårnålen mot en trapets.
- Materialet i maskinkroppen är 16 mm plywood. Varför plywood? Tillgänglig, billig, glad. Det finns faktiskt många alternativ, någon gör av duralumin, någon från plexiglas. Jag föredrar plywood.
Göra en 3D-modell:
Brotsch:
Sen gjorde jag så här, det fanns ingen bild kvar, men jag tror att det blir tydligt. Jag skrev ut en skanning på genomskinliga ark, klippte ut dem och klistrade in dem på en plywoodskiva.
Sågade bitar och borrade hål. Av verktygen - en sticksåg och en skruvmejsel.
Det finns ytterligare ett litet knep som kommer att göra livet enklare i framtiden: innan du borrar hål, klämma ihop alla parade delar med en klämma och borra igenom, så får du hål som är lika placerade på varje del. Även om en liten avvikelse uppstår under borrningen kommer de inre delarna av de anslutna delarna att matcha och hålet kan brotschas lite.
Parallellt gör vi en specifikation och börjar beställa allt.
vad hände med mig:
1. Uppsättningen som specificeras i denna recension inkluderar: styrkort för stegmotor (drivrutin), NEMA23 stegmotorer - 3 st, 12V strömförsörjning, LPT-sladd och kylare.
2. Spindel (detta är det enklaste, men gör ändå sitt jobb), fästelement och en 12V strömförsörjning.
3. Begagnad dator Pentium 4, viktigast av allt, moderkortet har LPT och ett diskret grafikkort + CRT-skärm. Jag tog den till Avito för 1000 rubel.
4. Stålaxel: Ф20mm - L=500mm - 2st, Ф16mm - L=500mm - 2st, Ф12mm - L=300mm - 2st.
Jag tog den hit, på den tiden i St Petersburg visade den sig vara dyrare att ta. Kom inom 2 veckor.
5. Linjära lager: f20 - 4 st., f16 - 4 st., f12 - 4 st.
20
16
12
6. Infästningar för axlar: f20 - 4 st, f16 - 4 st, f12 - 2 st.
20
16
12
7. Caprolonmuttrar med M10 gänga - 3 st.
Jag tog tillsammans med skaften på duxe.ru
8. Rotationslager, stängda - 6 st.
På samma plats, men kineserna har också många av dem
9. PVA-tråd 4x2,5
det är offline
10. Kuggar, pluggar, muttrar, klämmor - ett gäng.
Detta är också offline, i hårdvara.
11. En uppsättning fräsar köptes också
Så vi beställer, väntar, klipper och hämtar.
Ursprungligen installerades drivrutinen och strömförsörjningen för den i fodralet med datorn tillsammans.
Senare beslutades att placera föraren i ett separat ärende, det bara dök upp.
Tja, den gamla bildskärmen ändrades på något sätt till en mer modern.
Som jag sa i början trodde jag aldrig att jag skulle skriva en recension, så jag bifogar bilder på noderna, och jag ska försöka förklara monteringsprocessen.
Först monterar vi tre axlar utan skruvar för att rikta in axlarna så exakt som möjligt.
Vi tar de främre och bakre väggarna på huset, fäster flänsarna för axlarna. Vi stränger 2 linjära lager på X-axeln och sätter in dem i flänsarna.
Vi fäster botten av portalen till de linjära lagren, vi försöker rulla basen av portalen fram och tillbaka. Vi är övertygade om våra händers krökning, vi demonterar allt och borrar hål lite.
Därmed får vi en viss rörelsefrihet för axlarna. Nu betar vi flänsarna, sätter in axlarna i dem och flyttar basen av portalen fram och tillbaka för att uppnå en jämn glidning. Vi drar åt flänsarna.
I detta skede är det nödvändigt att kontrollera axlarnas horisontellitet, såväl som deras inriktning längs Z-axeln (kort sagt så att avståndet från monteringsbordet till axlarna är detsamma) för att inte fylla upp framtida arbetsplan senare.
Vi räknade ut X-axeln.
Vi fäster portalställen i basen, för detta använde jag möbelfat.
Fäst flänsarna för Y-axeln på stolparna, denna gång från utsidan:
Vi sätter in axlar med linjära lager.
Vi fixar Z-axelns bakvägg.
Vi upprepar processen med att justera axlarnas parallellitet och fixera flänsarna.
Vi upprepar samma process med Z-axeln.
Vi får en ganska rolig design som kan flyttas med en hand längs tre koordinater.
En viktig punkt: alla axlar ska röra sig lätt, d.v.s. lutar strukturen något, själva portalen bör röra sig fritt, utan gnisslande och motstånd.
Fäst sedan ledarskruvarna.
Vi skär av M10-konstruktionsbulten i önskad längd, skruvar caprolonmuttern ungefär i mitten och 2 M10-muttrar på varje sida. Det är bekvämt för detta, efter att ha dragit åt muttrarna lite, klämma fast tappen i skruvmejseln och dra åt muttrarna.
Vi sätter in lagren i uttagen och trycker dubbarna in i dem från insidan. Efter det fixerar vi dubbarna i lagret med muttrar på varje sida och kontrar med den andra så att de inte lossnar.
Vi fäster kaprolonmuttern vid basen av axeln.
Vi klämmer fast änden av tappen i skruvmejseln och försöker flytta axeln från början till slut och återvända.
Här har vi ytterligare ett par glädjeämnen som väntar på oss:
1. Avståndet från mutterns axel till basen i mitten (och troligen vid monteringstillfället kommer basen att vara i mitten) kanske inte sammanfaller med avståndet i extrema positioner, därför att axlar under vikten av strukturen kan böjas. Jag var tvungen att lägga kartong längs X-axeln.
2. Axelvägen kan vara mycket snäv. Om du har eliminerat alla snedvridningar, kan spänningen spela en roll, här är det nödvändigt att fånga spänningsmomentet för fixering med muttrar till det installerade lagret.
Efter att ha hanterat problemen och fått fri rotation från början till slut, fortsätter vi att installera de återstående skruvarna.
Vi fäster stegmotorer på skruvarna:
I allmänhet, när du använder specialskruvar, oavsett om det är en trapets eller en kulskruv, bearbetas ändarna på dem och sedan görs anslutningen till motorn mycket bekvämt med en speciell koppling.
Men vi har en byggdubb och fick fundera på hur vi skulle fixa den. I det ögonblicket stötte jag på ett snitt gasledning och tillämpade det. Den "vindar" direkt på hårnålen på motorn, går in i slipningen, drar åt den med klämmor - den håller väldigt bra.
För att fixa motorerna tog jag ett aluminiumrör och kapade det. Justeras med brickor.
För att ansluta motorerna tog jag följande kontakter:
Förlåt, jag kommer inte ihåg vad de heter, jag hoppas att någon i kommentarerna kommer att berätta för dig.
GX16-4-kontakt (tack Jager). Jag bad en kollega att köpa i en elektronikaffär, han bor bara i närheten, men det visade sig vara väldigt obekvämt för mig att ta mig dit. Jag är mycket nöjd med dem: de håller dem säkert, de är designade för en högre ström, du kan alltid koppla bort dem.
Vi lägger arbetsfältet, det är också ett offerbord.
Vi ansluter alla motorer till styrkortet från recensionen, ansluter det till en 12V PSU, ansluter till datorn med en LPT-kabel.
Installera MACH3 på PC, gör inställningar och försök!
Om inställningen separat kanske jag inte kommer att skriva. Det kan fortsätta i ett par sidor till.
Jag har en hel glädje, videon från den första lanseringen av maskinen har bevarats:
Ja, när den här videon rörde sig längs X-axeln blev det en fruktansvärd studs, tyvärr minns jag inte exakt, men till slut fann jag att antingen brickan dinglade eller något annat, i allmänhet löstes det utan problem.
Därefter måste du sätta spindeln, samtidigt som du säkerställer dess vinkelräthet (samtidigt i X och Y) mot arbetsplanet. Kärnan i proceduren är detta, vi fäster en penna på spindeln med elektrisk tejp, så att indragning från axeln erhålls. Med en mjuk sänkning av pennan börjar han rita en cirkel på tavlan. Om spindeln är nedsmutsad, visar det sig inte en cirkel, utan en båge. Följaktligen är det nödvändigt att uppnå inriktning genom att rita en cirkel. Ett foto från processen har bevarats, pennan är ur fokus och vinkeln är inte densamma, men jag tror att kärnan är tydlig:
Vi hittar en färdig modell (i mitt fall Ryska federationens vapensköld), förbereder UE, matar den till MACH och går!
Maskindrift:
bild pågår:
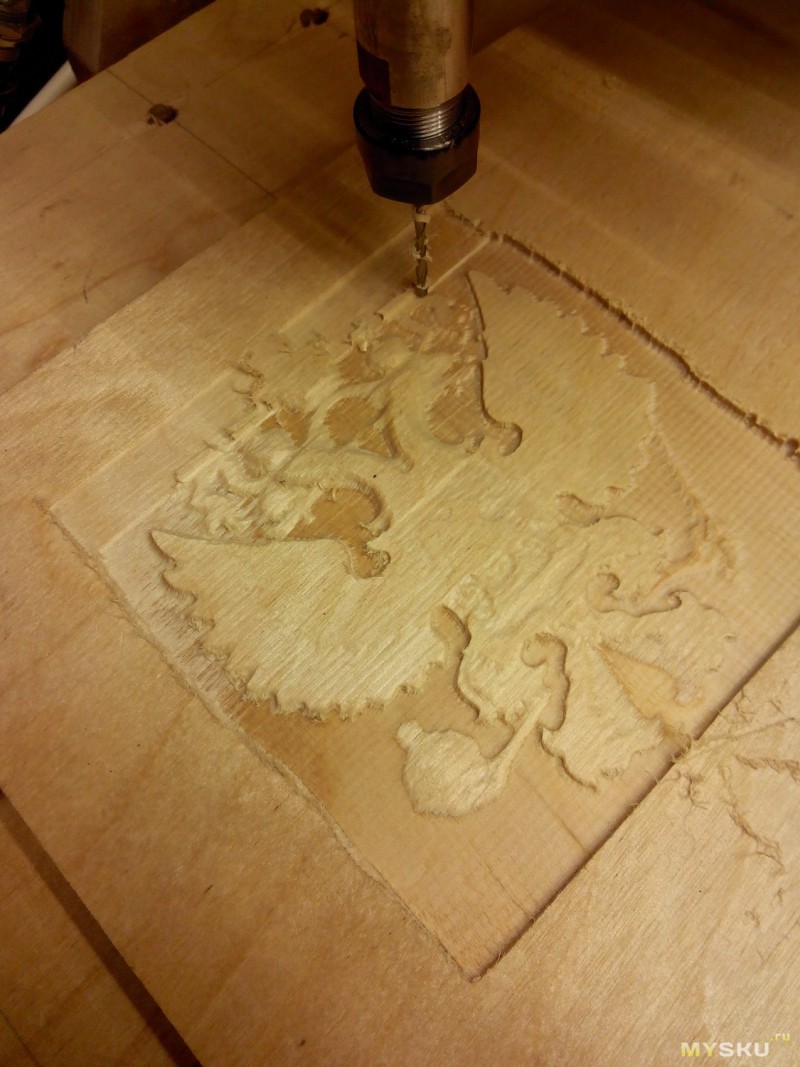
Jo, självklart går vi igenom initieringen))
Situationen är både rolig och allmänt förståelig. Vi drömmer om att bygga en maskin och genast såga något supercoolt, men i slutändan förstår vi att den här gången bara kommer att ta mycket tid.
I ett nötskal:
Med 2D-bearbetning (enbart utsågning) sätts en kontur som skärs ut i flera omgångar.
Med 3D-bearbetning (här kan du fördjupa dig i en holivar, vissa hävdar att detta inte är 3D utan 2,5D, eftersom arbetsstycket endast bearbetas ovanifrån), är en komplex yta satt. Och ju högre noggrannhet det önskade resultatet är, desto tunnare skärmaskinen används, desto fler pass av denna skärare behövs.
För att påskynda processen används grovbearbetning. De där. först provtas huvudvolymen med en stor fräs, sedan påbörjas efterbehandling med en tunn fräs.
Därefter provar vi, ställer in, experimenterar osv. 10 000 timmars regeln fungerar även här ;)
Kanske kommer jag inte längre att tråka ut dig med en berättelse om konstruktion, inställning etc. Det är dags att visa resultatet av att använda maskinen - produkten.
Som du kan se är det mest sågade konturer eller 2D-bearbetning. Det tar mycket tid att bearbeta tredimensionella figurer, maskinen står i garaget och jag stannar förbi där en kort stund.
Här kommer de med rätta att lägga märke till mig - men på ... att bygga en sådan bandura, om du kan skära en figur med en U-formad sticksåg eller en elektrisk sticksåg?
Det är möjligt, men detta är inte vår metod. Som ni minns skrev jag i början av texten att det var idén att göra en teckning på en dator och förvandla denna teckning till en produkt som fungerade som drivkraften till skapandet av detta odjur.
Att skriva en recension fick mig till slut att uppgradera maskinen. De där. uppgraderingen var planerad tidigare, men "händer nådde inte." Sista ändring innan dess fanns det en organisation av ett hus för maskinen:
I garaget, när maskinen är igång, har det alltså blivit mycket tystare och mycket mindre dammflugor.
Den senaste uppgraderingen var installationen av en ny spindel, mer exakt, nu har jag två utbytbara baser:
1. Med kinesisk 300W spindel för fint arbete:
2. Med en inhemsk, men inte mindre kinesisk fräs "Enkor" ...
Med den nya routern kom nya möjligheter.
Snabbare bearbetning, mer damm.
Här är resultatet av att använda en halvcirkulär spårfräs:
Tja, speciellt för MYSKU
Enkel rak spårfräs:
Bearbeta video:
På detta kommer jag att begränsa, men enligt reglerna skulle det vara nödvändigt att göra en inventering.
Minus:
- Dyrt.
- Under en lång tid.
- Då och då måste man lösa nya problem (de släckte lampan, pickuper, något som lösts upp, etc.)
Fördelar:
– Skapandeprocessen. Bara detta motiverar redan skapandet av maskinen. Sökandet efter lösningar på uppkommande problem och genomförande är vad man istället för att sitta på prästen reser sig upp och går för att göra något.
- Glädje i ögonblicket av att ge gåvor gjorda med dina egna händer. Här ska tilläggas att maskinen inte gör allt arbete själv :) förutom fräsning är det fortfarande nödvändigt att bearbeta den, slipa den, måla den osv.
Tack så mycket om du fortfarande läser. Jag hoppas att mitt inlägg, även om det inte uppmuntrar dig att skapa en sådan (eller annan) maskin, på något sätt kommer att vidga dina vyer och ge stof till eftertanke. Jag vill också säga tack till dem som övertalade mig att skriva detta opus, utan det hade jag tydligen ingen uppgradering, så allt är i svart.
Jag ber om ursäkt för felaktigheter i formuleringen och eventuella lyriska utvikningar. Mycket behövde skäras, annars hade texten blivit helt enkelt enorm. Förtydliganden och kompletteringar är naturligtvis möjliga, skriv i kommentarerna – jag ska försöka svara alla.
Lycka till i dina ansträngningar!
Utlovade fillänkar:
- maskinritning,
- sopa,
formatet är dxf. Det betyder att du kan öppna filen med vilken vektorredigerare som helst.
3D-modellen är detaljerad med 85-90 procent, jag gjorde många saker, antingen när jag förberedde skanningen eller på plats. Förstå och förlåt.)
En CNC-router kan vara en stor hjälpreda vid småskalig produktion eller hem reparation. Kostnaden för fabriks CNC-fräsmaskiner (cnc) är ganska hög, så vissa hantverkare skapar dem framgångsrikt med sina egna händer enligt unika ritningar.
Att göra en hemmagjord cnc-maskin med egna händer är inte lätt, ibland tar det flera månader.
Maskindesign
Det enklaste sättet att göra en ram för en hemmagjord fräsmaskin för metall är från ett rör kvadratisk sektion 80 x 80 mm, ganska låg. Den låga höjden gör enheten ganska stabil och förhindrar vibrationer. Stativet för att fästa skenorna är också gjort av rektangulärt metallrör 60 x 20 mm. Sängen är bultad, eftersom svetsfogar deformerar strukturen. Bultade fästelement gör att du kan ställa in enheten exakt på nivån, kontaktytan är stor, fästet är pålitligt och ganska styvt, utan glapp.
Arbetsytans storlek hemmagjord maskin måste göras från 32 x 35 cm Längden på styraxlarna längs Y och X är 1,6 cm, längs Z - 1 cm.
Styrningar görs bäst profil, annars kommer de att hänga längs X-axeln.
Glidlager är bättre att välja industriella, om än det billigaste. Deras användning kommer att minska sannolikheten för bakslag.
Z-axeln är monterad på ett skruvdrev, då den är ganska tung. För att överföra vridning till ledskruven från Z-axeln används en kuggrem med en bredd på 10 mm. Ett sådant schema låter dig minska slaget och underlätta placeringen av stegmotorn i förhållande till färdskruven. Minskar maskinvikten och sparar vertikalt utrymme.
Själva axeln är gjord av en aluminiumplatta och två stegmotorer är installerade bakom den. Deras syfte är att överföra vridning till Z-axelskruven med hjälp av en kuggrem, en annan motor överför rörelse längs X-axeln med en rem Z-axelns ledskruv kan tillverkas av en konstruktionsbult.
Om istället för en rem görs en skruvväxel på ritningen kommer hastigheten att öka till 850 rpm och noggrannheten hos en hemmagjord cnc-maskin. Men den här designen är mycket dyrare.
Om du planerar att vattenkyla spindeln bör du också tillhandahålla en vattenpump, samt en uppsättning gummirör.
Motor och mjukvara
För en hemmagjord CNC-fräsmaskin (de kallas även cnc) är en stegmotor med ett vridmoment på 18 kg / cm lämplig. En sådan motor är tillräcklig för en spindel med en effekt på 1,5 kilowatt. Det kommer att visa sig att bearbeta delar gjorda av mjuka metaller och enkla jobb på kolstål.
Styrenheten, frekvenskonvektorn och moderkortet kan installeras i en enda skyddslåda. Även om många är rädda för störningar är de ganska sällsynta. En sådan kontrollcentral är benägen att överhettas i varmt väder!
CNC-fräsmaskiner, monterade för hand enligt ritningar, arbetar under ledning av Linux. Vissa drivrutiner måste skrivas för hand, till exempel för en stegmotor med mikrostepping. Styrenheter med USB-utgång fungerar inte under Linux, detta bör beaktas när du väljer dem. Du måste köpa en fyraxlig styrenhet och göra lämpliga inställningar.
Färdigt set för maskinmontering
De flesta hantverkare som monterar maskinen med sina egna händer står inför behovet av att köpa många färdiga delar. Som ett resultat, priset hemgjord enhet kan vara högre än fabriken. Bearbeta självmontering mycket lång, och resultatet är ofta en besvikelse. Ofta gör hantverkare flera gånger om maskiner monterade utan ritningar och beräkningar, vilket för deras arbete till önskad standard.
Det är möjligt att göra en CNC-router med dina egna händer med en skiftnyckel och en skruvmejsel på en arbetsdag, med ett färdigt kit - en slags enkel konstruktör för vuxna, som innehåller absolut alla detaljer och ritningar. Setet är en garanti Hög kvalitet framtida maskin.
Enheten och testning av en hemmagjord fräs:
17
En guide för att skapa en CNC-fräs CNC-maskin. Kapitel 1 Maskinelektronik
God dag till alla! Och här är jag med en ny del av min berättelse om CNC - verktygsmaskin. När jag började skriva artikeln trodde jag inte ens att den skulle visa sig vara så omfattande. När jag skrev om maskinens elektronik tittade jag och blev rädd – A4-arket stod skrivet på båda sidor, och det fanns fortfarande mycket att berätta.
Till slut blev det så här manual för att skapa en CNC-maskin, fungerande maskin, från grunden. Det kommer att finnas tre delar av artikeln om en maskin: 1-elektronisk fyllning, 2-mekanik av maskinen, 3-alla detaljer om att ställa in elektroniken, själva maskinen och maskinstyrningsprogrammet.
I allmänhet kommer jag att försöka kombinera i ett material allt användbart och nödvändigt för varje nybörjare i denna intressanta verksamhet, vad jag själv läste på olika internetresurser och gick igenom mig själv. Förresten, i den artikeln glömde jag att visa bilder på hantverk gjorda. Jag fixar det här. Frigolitbjörn och plywoodväxt.
Förord
Efter att jag satt ihop min lilla maskin utan betydande utgifter för ansträngning, tid och pengar, var jag seriöst intresserad av detta ämne. Jag tittade på YouTube, om inte alla, så nästan alla videor relaterade till amatörmaskiner. Särskilt imponerande var fotografierna av produkter som människor gör på sina " Hem CNC". Jag tittade och bestämde mig - jag ska montera min stora maskin! Så, på en våg av känslor, tänkte jag inte över det, jag kastade mig in i en ny och okänd värld för mig själv CNC.Visste inte var jag skulle börja. Först och främst beställde jag en vanlig stegmotor Vexta 12 kg/cm, bland annat med den stolta inskriptionen "made in Japan".
Medan han körde genom hela Ryssland satt han på kvällarna på olika CNC-forum och försökte göra ett val STEP/DIR-kontroller och stegmotorförare. Jag övervägde tre alternativ: på en mikrokrets L298, på fältarbetare, eller köp färdig kinesiska TB6560 som det fanns mycket motstridiga recensioner om.
För vissa fungerade det utan problem under lång tid, för andra brann det ut vid minsta användarfel. Någon skrev till och med att han brann ut när han vred lätt på axeln på motorn som då var kopplad till styrenheten. Förmodligen det faktum att kinesernas opålitlighet och spelade till förmån för att välja ett system L297+ diskuteras aktivt på forumet. Upplägget är förmodligen verkligen omöjligt. fältdrivkrafterna för föraren med ampere är flera gånger högre än vad som behöver matas till motorerna. Även om du behöver löda dig själv (detta är bara ett plus), och kostnaden för delarna kom ut lite mer än den kinesiska kontrollern, men den är pålitlig, vilket är viktigare.
Jag avviker lite från ämnet. När allt detta var klart tänkte jag inte ens på att jag en dag skulle skriva om det. Därför finns det inga bilder på monteringsprocessen av mekanik och elektronik, bara några få bilder tagna på en mobiltelefonkamera. Allt annat klickade jag specifikt för artikeln, redan monterat.
Fallet med lödkolven är rädd
Jag börjar med strömförsörjningen. Jag planerade att göra en impuls, jag pillade med det i säkert en vecka, men jag kunde inte besegra spänningen, som kom från ingenstans. Jag lindar transen på 12v - allt är OK, jag lindar den på 30 - en fullständig röra. Jag kom fram till att någon sorts skitsnack klättrar på feedback från 30v till TL494 och riva hennes torn. Så jag övergav denna impuls, eftersom det fanns flera TS-180, varav en gick för att tjäna fosterlandet som en krafttrans. Och vad du än säger, kommer en bit järn och koppar att vara mer pålitlig än en massa smula. Transformatorn lindades tillbaka till de erforderliga spänningarna, men det var nödvändigt + 30V för att driva motorerna, + 15V för att driva IR2104, +5v på L297, och en fläkt. Du kan applicera 10 eller 70 på motorerna, det viktigaste är att inte överskrida strömmen, men om du gör mindre minskar den maximala hastigheten och effekten, men transformatorn tillät det inte längre. Jag behövde 6-7A. Stabiliserade spänningar 5 och 15v, lämnade 30 "flytande" enligt vårt elnäts bedömning.Hela den här tiden satt jag varje kväll vid datorn och läste, läste, läste. Ställa in styrenheten, välja program: vilket man ska rita, vilket man ska använda maskinen, hur man gör mekanik osv. etc. I allmänhet, ju mer jag läser, desto mer hemskt blev det, och allt oftare uppstod frågan "för vad behöver jag det här?!". Men det var för sent att dra sig tillbaka, motorn låg på bordet, detaljerna var någonstans på vägen – vi måste fortsätta.
Det är dags att löda brädan. Tillgänglig på Internet passade inte mig av tre anledningar:
1 - Butiken som beställde delarna var inte där IR2104 i DIP-paket, och de skickade mig 8-SOICN. De är lödda på brädet på andra sidan, upp och ner, och därför var det nödvändigt att spegla spåren, och dem ( IR2104) 12 stycken.
2 - Motstånd och kondensatorer togs också i SMD-paket för att minska antalet hål som behövde borras.
3 - Kylaren jag hade var mindre och de extrema transistorerna var utanför sitt område. Det var nödvändigt att flytta fältarbetarna på en bräda till höger och på den andra till vänster, så jag gjorde två typer av brädor.
Maskinstyrningsdiagram
För säkerheten för LPT-porten är styrenheten och datorn anslutna via ett optokopplarkort. Jag tog schemat och signet från en välkänd sida, men återigen var jag tvungen att göra om det lite för mig själv och ta bort onödiga detaljer.
Ena sidan av kortet strömförsörjs via USB-porten, den andra, ansluten till styrenheten, drivs av en + 5V-källa. Signaler överförs via optokopplare. Jag kommer att skriva alla detaljer om att ställa in kontrollern och frikopplingen i det tredje kapitlet, men här kommer jag bara att nämna huvudpunkterna. Detta frånkopplingskort är utformat för säker anslutning av stegmotorstyrningen till datorns LPT-port. Helt elektriskt isolerar datorporten från maskinens elektronik, och låter dig styra en 4-axlig CNC-maskin. Om maskinen bara har tre axlar, som i vårt fall, kan onödiga delar lämnas hängande i luften, eller inte lödas alls. Det är möjligt att ansluta ändsensorer, en tvångsstoppknapp, ett spindelaktiveringsrelä och en annan anordning, såsom en dammsugare.
Det var ett foto på optokopplarkortet taget från Internet, och så här ser min trädgård ut efter installation i fodralet. Två brädor och ett gäng trådar. Men det verkar inte finnas några störningar, och allt fungerar utan fel.
Det första styrkortet är klart, jag kontrollerade allt och testade det steg för steg, som i instruktionerna. Jag ställde in en liten ström som en trimmer (detta är möjligt på grund av närvaron av PWM) och kopplade strömmen (motorerna) genom en kedja av 12 + 24v glödlampor så att det var "ingenting om ingenting". Jag har fältarbetare utan radiator.
Motorn väsnade. Goda nyheter, så PWM fungerar som det ska. Jag trycker på en tangent och den snurrar! Jag glömde nämna att denna kontroller är designad för att styra en bipolär stegmotor d.v.s. en med 4 trådar. Spelas med steg/halvstegslägen, aktuell. I halvstegsläge beter sig motorn mer stabilt och utvecklar höga varvtal + noggrannhetsökningar. Så jag lämnade bygeln i "halva steget". Med den maximala säkra strömmen för motorn vid en spänning på ca 30V, visade det sig snurra motorn upp till 2500 rpm! Min första maskin utan PWM drömde aldrig om något sådant.))
De följande två motorerna beställde mer kraftfulla, Nema vid 18 kg/s, men redan "made in China".
De är sämre i kvalitet Vexta Kina och Japan är trots allt två olika saker. När man roterar skaftet med handen gör japanerna det på något sätt mjukt, men kineserna har en annan känsla, men hittills har det inte påverkat arbetet. Det finns inga kommentarer för dem.
Jag lödde de återstående två korten, kollade igenom "LED-stegmotorsimulatorn", allt verkar vara bra. Jag kopplar in en motor - den fungerar bra, men inte 2500 rpm, utan ca 3000! Enligt det redan utarbetade schemat ansluter jag den tredje motorn till det tredje kortet, snurrar i ett par sekunder och reser mig upp ... Jag tittar på oscilloskopet - det finns inga pulser på en utgång. Jag kallar avgiften - en av IR2104 genomborrade.
Tja, jag kanske har en defekt, jag läste att det ofta händer med denna mikruha. Jag löder en ny (jag tog 2 stycken med marginal), samma nonsens - det vänder STOPP i ett par sekunder! Här ansträngde jag mig, och låt oss kolla fältarbetarna. Det har min styrelse förresten IRF530(100V / 17A) mot (50V / 49A), som i originalet. Maximalt 3A kommer att gå till motorn, så en reserv på 14A kommer att vara mer än tillräckligt, men skillnaden i pris är nästan 2 gånger till fördel för 530-talet.
Så jag kollar fältarbetarna och vad jag ser ... jag lödde inte ett ben! Och alla 30V från fältarbetaren flög till utgången av denna "irka". Jag lödde benet, undersökte noggrant allt igen, satte ett till IR2104, jag är själv orolig - det här är den sista. Jag slog på den och blev väldigt glad när motorn inte stannade efter två sekunders drift. Lägen kvar enligt följande: motor Vexta- 1,5A, motor NEMA 2,5A. Vid denna ström uppnås varv på cirka 2000, men det är bättre att begränsa dem programmatiskt för att undvika att hoppa över steg, och motorernas temperatur kl. långt arbeteöverskrider inte säkra för motorer. Krafttransformatorn klarar sig utan problem, eftersom vanligtvis bara 2 motorer snurrar samtidigt, men ytterligare luftkylning är önskvärt för kylaren.
Nu om installationen av fältarbetare på kylaren, och det finns 24 av dem, om någon inte har märkt det. I denna version av brädan ligger de liggande, d.v.s. kylaren bara lägger sig på dem och attraheras av något.
Naturligtvis är det önskvärt att sätta en solid bit glimmer för att isolera kylflänsen från transistorerna, men jag hade ingen. Hittade en väg ut. Därför att i hälften av transistorerna går höljet till pluseffekt, de kan monteras utan isolering, bara på termisk pasta. Och under resten lägger jag bitar av glimmer som blivit över från sovjetiska transistorer. Jag borrade radiatorn och skivan på tre ställen genom och igenom och spände med bultar. Jag fick en stor bräda genom att löda tre separata brädor runt kanterna, samtidigt som jag lödde en 1 mm koppartråd runt omkretsen för styrka. Jag placerade all elektronisk stoppning och strömförsörjningen på något slags järnchassi, jag vet inte ens varför.
Jag skar ut sido- och topplocket från plywood och satte en fläkt ovanpå.
Jag borrade hål i frontpanelen för många lysdioder för att indikera driftlägen.
För att snabbt koppla/avkoppla motorer och styrenheten använde jag kontakter från förra årtusendet. Och bra kontakt önskad ström hålla utan några konsekvenser för dem själva.